摘 要:作为航空发动机的热端部件之一,涡轮转子占据极其重要的地位。涡轮转子工况恶劣,受力复杂,故要求其材料要具备高拉伸强度,高屈服强度,使其在高温高压下正常稳定运行。低压涡轮转子支撑锥壁是航空发动机上重要的零组件之一,其结构复杂,承受多种机械载荷和热载荷,因此必须保证支撑锥壁零件具备高可靠性,一旦零件失效后果不堪设想。喷丸强化是目前国内外使用最广泛的抗疲劳表面强化技术之一,文章研究低压涡轮转子支撑锥壁的喷丸工艺过程。
关键词:工艺路线;疲劳寿命;数控编程;喷丸工艺
引言
作为航空发动机的热端部件之一,涡轮转子占据极其重要的地位。涡轮转子工况恶劣,受力复杂,故要求其材料要具备高拉伸强度,高屈服强度,从而使其在高温高压下能正常稳定运行。新机的研制,给涡轮部件的材料提出了更高的要求,对其材料机械加工特性的研究也变得日趋迫切。低压涡轮支撑锥壁是航空发动机重要的零部件,承受着十分复杂的热载荷和机械载荷。支撑锥壁联接着涡轮叶盘与涡轮轴,其型面型腔数量众多且难以加工,结构极其复杂,且制造周期较长,因此必须保证零件可靠性避免零件失效,航空零部件80%以上失效是由于疲劳失效造成的。喷丸是一种通过用金属丸粒不停地撞击金属表面从而在其上产生残留压应力层和冷作硬化来改进金属的性能的冷加工过程。这种特种工艺可以提高零件疲劳寿命,增强其可靠性。
1 喷丸工艺原理
喷丸强化工艺是一种表面处理工艺方法,它通过用金属丸粒不停地撞击金属表面从而在其上产生残留压应力层同时又因为冷挤压使零件表面冷作硬化。残余压应力可消除零件因机加、热处理等环节产生的残余拉应力,而冷作硬化使零件的强度有所提高。晶粒晶格的畸变使零件不易产生裂纹扩展,从而能显著提高零件抗疲劳性能和抗应力腐蚀能力,延长零件使用寿命。
喷丸强化是一种冷加工工艺,对于喷丸强化的效能评定来说喷丸强度、表面覆盖率和粗糙度都是较为重要的考察项,在这些技术要求中又以喷丸强度最为关键也最难控制。实际加工中零件的喷丸强度值受到十余种工艺参数的影响,包括压缩空气压力、流量、弹丸材质、喷嘴类型及尺寸、喷射角度等等,这其中细小的变化也会相应的改变喷丸强化的最终效果。对于喷丸强化工艺来说,必须严格监控各参数的变化,为了简化喷丸工艺中过程的控制,在对同一部位进行喷丸强化加工时,可以将喷射角度、弹丸、喷嘴等参数进行固化,而仅通过调整空气压力和弹丸的流量以及加工时间等几个因素来保证喷丸效果的稳定。
2 涡轮转子支撑锥壁的工艺性分析及工艺方法的确定
2.1 零件特点及设计要求
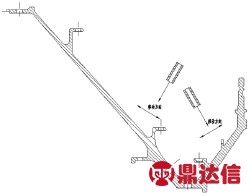
图1 转子支撑锥壁第一面喷丸工艺路线
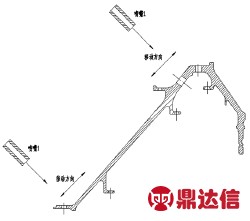
图2 转子支撑锥壁第二面喷丸工艺路线
低压涡轮转子支撑锥壁表面分为喷丸区、任意喷丸区、禁喷区,所涉及零件特征:型腔、型面、内孔、里沿。该零件是一个典型的复杂型面盘型零件,零件的最大外圆大于Φ750mm,型腔浅但是所处位置较深,数量较多,且形状复杂,加工孔数多,对喷丸工艺技术要求较高。
2.2 工艺准备及特种工艺工序的安排
在喷丸工序之前,需完成零件相关尺寸特性等所有机械加工工序,之后根据工厂现有设备条件,采用数控喷丸机对零件进行喷丸。在接收零件后指导现场操作人员按工艺规程对零件进行清理,按规程标注区域对零件上的禁喷区进行保护。通常禁喷区的保护分为两种方式,对于大批量的产品一般通过专用遮挡工装对其进行保护,对于研制件或件数较少的产品一般采用专门的保护胶带对零件进行保护,本次采用的是专用保护胶带对零件进行保护。
2.3 工艺路线的确定
2.3.1 工序路线的安排
转子支撑锥壁喷丸的工艺路线为:
接收零件→零件保护→锥壁定点试片喷丸→锥壁移动试片喷丸→锥壁一面定点喷丸→锥壁一面移动喷丸→锥壁一面补充喷丸→锥壁二面定点喷丸→锥壁二面移动喷丸→锥壁内腔试片喷丸→锥壁内腔喷丸→清理→最终检验
低压涡轮转子支撑锥壁是发动机中的结构支撑部件,其对抗疲劳性能要求较为严格,根据其结构特点对其喷丸工艺路线分为第一面定点喷丸,第一面移动喷丸,第二面定点喷丸,第二面移动喷丸,小孔喷丸,再根据喷丸路线编制对应的试片喷丸工序。
2.3.2 型面型腔喷丸过程
先将喷丸试片通过专用夹具安装在数控喷丸机上,之后通过试片程序对其进行喷丸,根据试片结果进行弧高度曲线的划定并根据图纸要求,确定了喷射角度,弹丸流量,空气压力,喷丸时间或喷丸次数,其余相关参数由数控喷丸机固化,在对应零件部位的试片喷丸之后立即进行对该部位的喷丸工序,转子支撑锥壁的辐板部位面积大,要求喷丸表面覆盖均匀,在本次过程中采用移动式喷丸的方式,通过程序控制喷嘴沿零件型面移动,同时保持各项工艺参数不变,完成对零件大面积、长距离、型面结构简单部位的喷丸。零件的细小型腔部位,采用定点喷丸的方式对其进行喷丸。由于零件内部复杂,存在着相互遮挡问题,腔体里侧丸粒无法触及等问题,本次主要通过编制数控程序与手动操作相结合以示教的方式对难以触及的型腔进行逐次逼近,记录每次的位置点,根据位置点进行程序编制,从而实现对第一面与第二面的喷丸,如图1、2所示。
2.3.3 小孔喷丸过程
根据设计要求需要对支撑锥壁众多加工孔进行喷丸,通常小孔喷丸的方法分为两种情况:第一、在孔外侧用喷嘴直接喷丸,当孔直径大于孔深时,可以从孔的侧面进行喷丸,因每次只能喷到孔的1/4面积,所以要对孔进行4个方向喷丸。当孔直径小于孔深但孔深小于二倍孔直径并且是通孔时,采用外喷嘴喷丸时要从孔的两侧进行喷丸,但也要对孔进行4个方向喷丸,左右方向喷丸,前后也要进行喷丸,才能达到完全覆盖,为提高效率,也可以采用4个喷嘴在孔的4个方向同时进行喷丸。第二、在孔内侧采用反射式喷嘴进行喷丸,在通孔的任一端放置一个反射式喷嘴,将其伸入小孔可以对通孔内径进行喷丸,为了获得均匀的覆盖率有时需要旋转式反射喷嘴。本次采用第一种方式对转子支撑锥壁加工孔进行喷丸。
3 结束语
在10倍放大镜下,对零件的喷丸后表面进行了细致的检查,喷丸后的形貌均匀,覆盖率达到设计要求,通过检查喷丸试片及对应的弧高度曲线,证明喷丸工艺参数满足图纸要求,制定的工艺路线正确合理,顺利完成了低压转子支撑锥壁的喷丸工序,保证零件加工喷丸区域的要求和技术条件。喷丸处理后表面形成残余压应力层和冷作硬化可对零件表面强化,同时也可以破碎机械加工的刀痕,减小缺口敏感性,从而有效提高零件抗疲劳强度,一般可提高疲劳寿命1-3倍,甚至可提高几十倍。