摘要:本文介绍了弧齿锥齿轮接触斑点的应用研究的过程,通过对某型号装载机驱动桥的弧齿锥齿轮副的接触斑点的分析研究,实施小齿轮的加工参数的调整,经整机试验达到了预期要求。重新确认制造过程接触斑点的标准,据此进行制造过程的控制,确保批量生产的齿轮满足使用要求,取得了很好的效果,质量外反馈率大幅改善。
关键词:工程机械;弧齿轮锥齿轮;主传动;接触斑点
弧齿锥齿轮和准双曲面齿轮统称为弧齿锥齿轮,具有重叠系数大、承载能力强、运转平稳、噪声低的特点,因此它被广泛应用于工程机械传动系统中。接触区就是当齿轮旋转进入啮合直至脱离啮合期间,轮齿相互接触的区域,它与齿轮的平稳运转、使用寿命和噪声有直接的影响,是齿轮设计的一个关键特性。接触区的质量要求一般来自齿轮的零件图,但实际上很多零件图是没有齿面接触区具体要求的,即便是有要求,有些也是与具体齿轮的使用特性不一定完全吻合,因此直接选用某个标准中的接触区质量要求也不一定合适,这就需要在标准框架范围内,结合产品使用特性和实践验证综合设计新的合适的接触区质量要求。这个框架就是:“齿轮满负荷时接触区应基本布满整个工作齿面但不出现边缘接触”。这就是判断接触区质量的基本原则。
1 现状分析
某型轮式装载机的弧齿轮锥齿轮副,在保质期内出现了异常的反馈率。从失效件分析中发现,其接触区存在有严重不符合,为了改进这一状况,展开了对接触区的改善研究。
从产品失效件中,对现状接触区进行测量。从测量结果来看 ,满负荷时的斑点 ,无论是接触区的高度值还是长度值都太大,满负荷时接触区均出现边缘接触。
2 改进方案
根据目前该齿轮副的强度情况,小轮的强度较强,决定对小轮进行修形,使接触区优化达到要求。改进试验流程,结合修正方法,分别对齿高方向、齿面节线曲率、齿形曲率、对角接触等进行反复修正,直至接触区及其 V/H检验,均达到满意效果。最终满足强度及噪音的要求。
3 接触区域尺寸及 V/H检验的约定
接触区域尺寸约定:为了描述的方便,无论是凸面还是凹面的接触区域尺寸,进行统一的定义为A、B、C、D。对 V/H检验的约定:V及 H的取值正负符号进行了定义,在滚动检验机上,令大齿轮改变垂直移动,使接触区由正常位置移向齿小端,其垂直移动量记为 V1;为使接触区位于齿高中部,小齿轮的水平位移应相应地改为 H1;再使大齿轮作垂直移动,使接触区移向齿的大端,其垂直位移量为 V2;伴随改变水平位移量为 H2,接触区由小端移向大端所必须的垂直总位移量 ΣV=|V2-V1|,水平总位移量ΣH=|H2-H1|。
4 改进过程
根据上述的斑点测量及 V-H检验方法,进行持续改进,大轮无负荷时接触区数据、大轮满负荷后接触区数据、V/H检验数据、凸凹面加工参数 3次改进调整数据分别如表1、表2、表3及表4。
(1)第 1次改进及问题分析。从表3的 V/H检验数据看出,V、H移动值都比较小,说明斑点在齿长、齿高方向都比较长,斑点位置凹面偏小端,凸面在中部偏小端。改进目标为:凹面:热后齿长斑点由 70%缩短至 35%~ 45%;凸面:热后齿长斑点由 70%缩短至 35%~ 45%左右,齿高 斑点缩短距齿顶 为 2.5~ 3mm。改进方案为第 1次改进的刀盘直径、滚比、偏心角参数值见表4。从试验数据可以看出:第 1次改进后的 V、H移动值明显比现状的大,说明第 1次改进后斑点缩短很多,斑点位置凹面偏小端,凸面在中间。
(2)第 2次改进及存在问题分析。改进目标:热处理后凹面齿高斑点距齿顶 3~ 4mm,凸面齿长 斑 点 缩 短 至 30%左 右, 齿 高 斑 点 距 齿 顶 3.5~4.5mm;改进方案:加工参数改进方案如表4。从第二次改进情况可以看出:凹面对角值较上次试验相同,凸面由于热前内对角较明显,热后内对角较上次试验就更明显。
表1 大轮无负荷时接触区数据
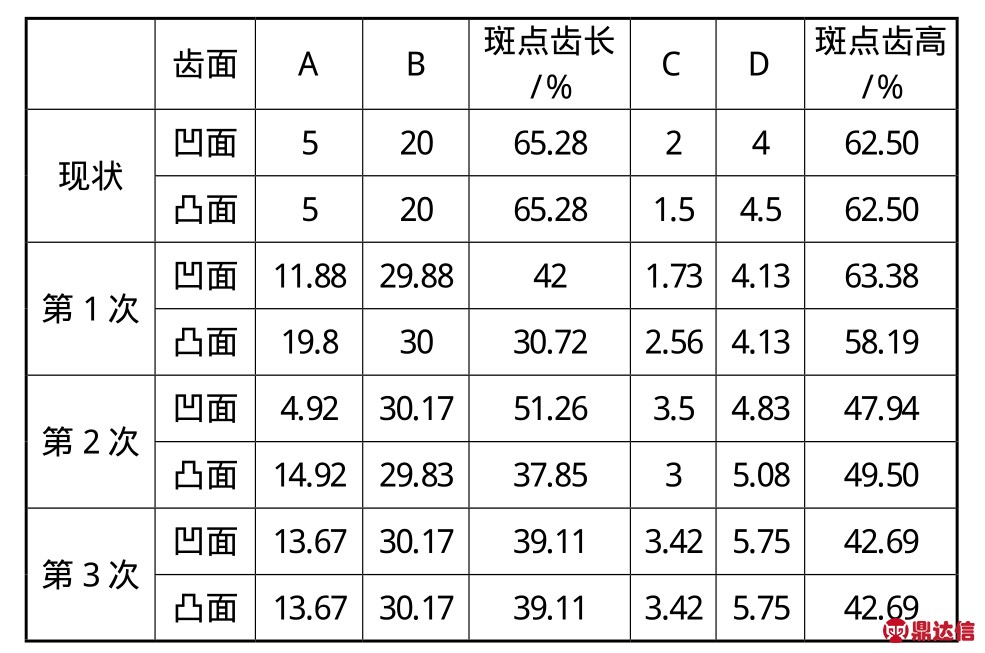
表2 大轮满负荷后接触区数据

(3)第 3次改进及问题分析。凹面:齿长方向调往小端 2mm,齿高方向往齿底挪 0.5mm;凸面:齿长方向调往大端 3mm,齿高方向往齿底挪 0.5mm。改进方案:加工参数改进方案如表4;第 3次改进后 V/H检验数据如表3。
通过3次改进及试验,满负荷时齿面接触斑点达到设计标准要求,其在载荷情况下的接触区及 V/H值作为成品验收的标准。
5 结语
通过3次弧齿锥齿轮接触区改进及试验,接触区域已达到标准要求,取得预期效果。目前已通过超过3年的市场验证 ,外反馈率降至 0.4%以下,接触区完全满足使用要求,试验改进方法有效。
参考文献:
[1]李普华 .对格里森齿锥齿轮接触区的认识与修正 [J].机电工程技术,2010年第 39卷第 08期 .
表3 V/H检验数据
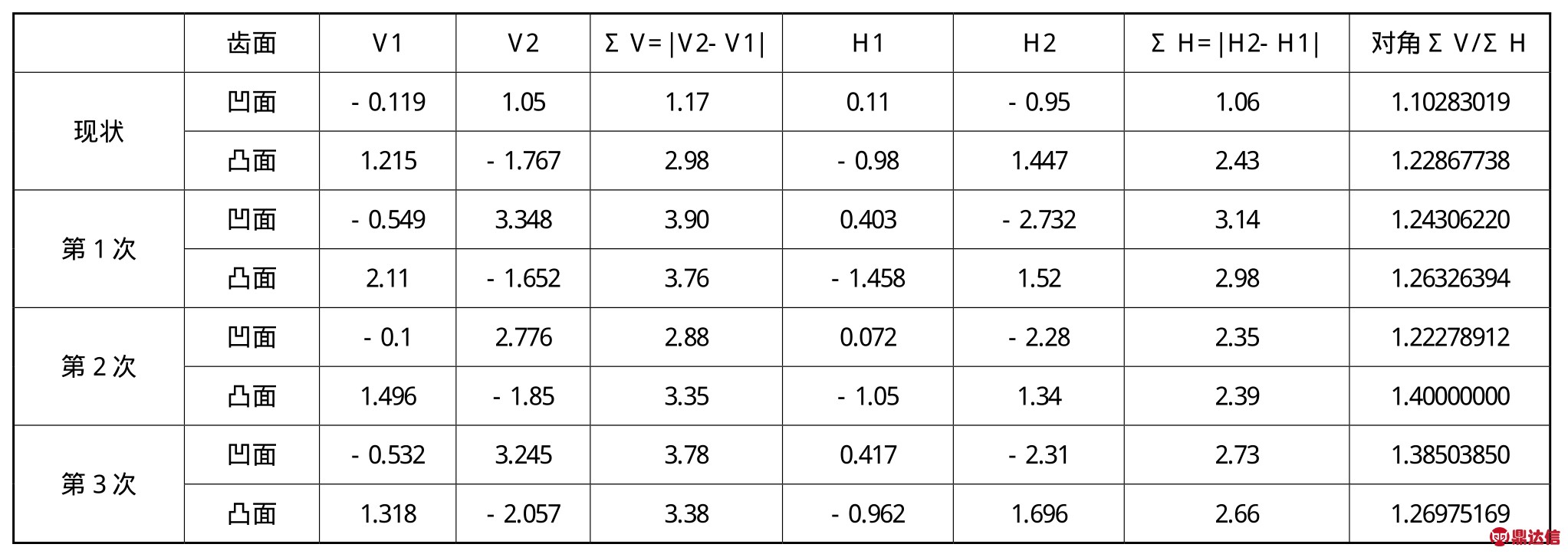
表4 凹、凸面加工参数调整
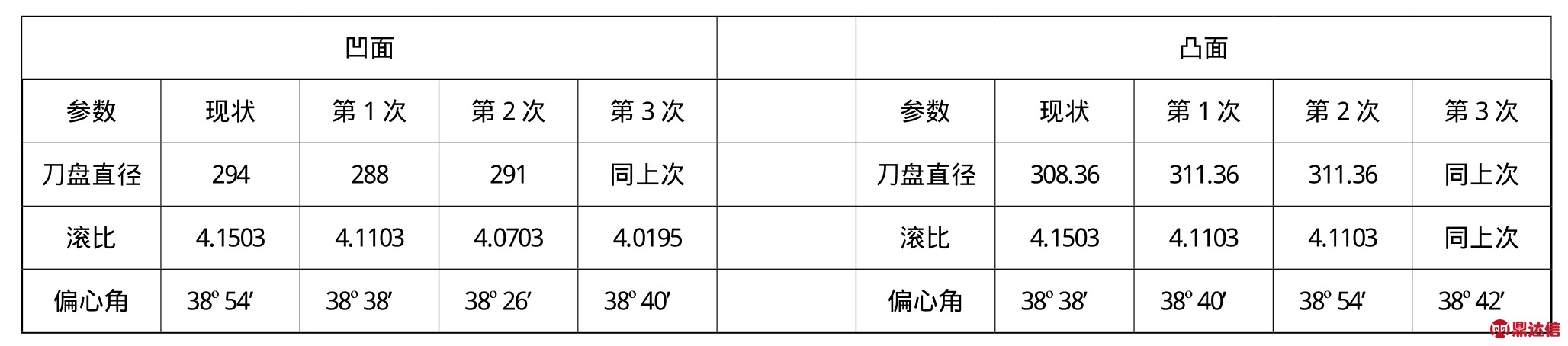