摘要:将Archard 模型与有限元仿真结合,对不同工况磨损过程进行仿真分析,得到磨损量关于磨损次数的公式并建立两种磨损预测模型;确定载荷、摆动频率、摆动角度和表面粗糙度为主要磨损影响因素,利用偏最小二乘法建立磨损量与主要影响因素关系的预测模型。将两种预测值分别与实验值比较,相对误差较小,预测效果和精准度都比较好,可以用于实际工况中垫片磨损量的预测分析。
关键词:止推垫片;磨损实验;磨损预测模型;仿真分析
止推垫片作为机械系统中常用的零部件,广泛应用于航空航天、电力、交通等领域的往复式旋转运动场合。其主要作用是定位及避免零部件间的直接接触,减少零部件窜动和磨损,提高系统稳定性。磨损是导致止推垫片失效的主要原因,不仅会造成垫片功能衰退或丧失,甚至会对机械系统造成严重影响。
针对磨损实验值预测,车建明[1]在实验基础上采取回归分析方法建立了可靠度关于压力、移动速度的三次多项式模型;钟颜得等[2]对静态实验数据采用数理统计的方法处理,有效避免随机误差对磨损机理分析的干扰;徐流杰等[3]采用多次回归方法建立高钒钢磨损量与滚动次数、碳含量的磨损模型。Blau P J[4]采取概率统计的方法研究了机械零部件在滑动磨损中的摩擦系数预测问题,获得了较好的预测精度;Clint Steele等[5]基于田口法开发了金属基复合材料耐磨性的预测模型;Sahin Y[6]借助实验数据分析,应用数值分析方法建立了铜基复合材料磨损速率与主要金属成分占比之间的回归关系;Palanisamy等[7]则使多元回归和人工神经网络两种方法对机床的刀具侧面磨损进行了研究。
大多数磨损计算模型只是针对特定的磨损工况或磨损条件,具有一定的局限性,并且摩擦副之间的应力没有被做为变量考虑进公式,只是当做普通的常量被忽视,磨损量的结果只是通过简单的加和计算得出。本文以止推垫片为研究对象,以磨损实验和有限元分析为研究手段,将Archard 模型与有限元仿真相结合,并基于偏最小二乘法建立磨损实验预测模型,同时在自制双向加载摆动磨损实验机上进行实验,最后将仿真值,实验预测值与实际值进行对比分析。
1 推垫片磨损有限元分析
1.1 垫片磨损量计算方法
在有限元分析过程中,基于Archard磨损模型,并通过仿真软件提取磨损过程中接触点指定点的不同时刻应力值,将硬度、磨损因子、运动速度均视为常数,得出该点单次滑动磨损的磨损厚度公式积分形式如下:
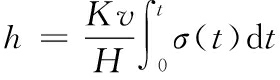
(1)
式(1)中:v为滑动速度;t为磨损过程持续的时间。
经简化分析采取对单次磨损过程拆分求解,即选择一段磨损时间Δt作为时间段,在此时间段Δt中,表面应力值σ可视为常量,对该段磨损过程造成的部分磨损量求解计算,磨损量为Δhj,n(其中j代表磨损次数,n代表节点编号),经过累加得到磨损量,一次摆动磨损时间由m个时间段构成,则磨损厚度hj,n可定义为

(2)
故k次磨损量W可表示为
(3)
垫片磨损过程中接触面的节点应力值历程曲线,如图1所示。曲线中时间段即为实际接触时节点的应力值。
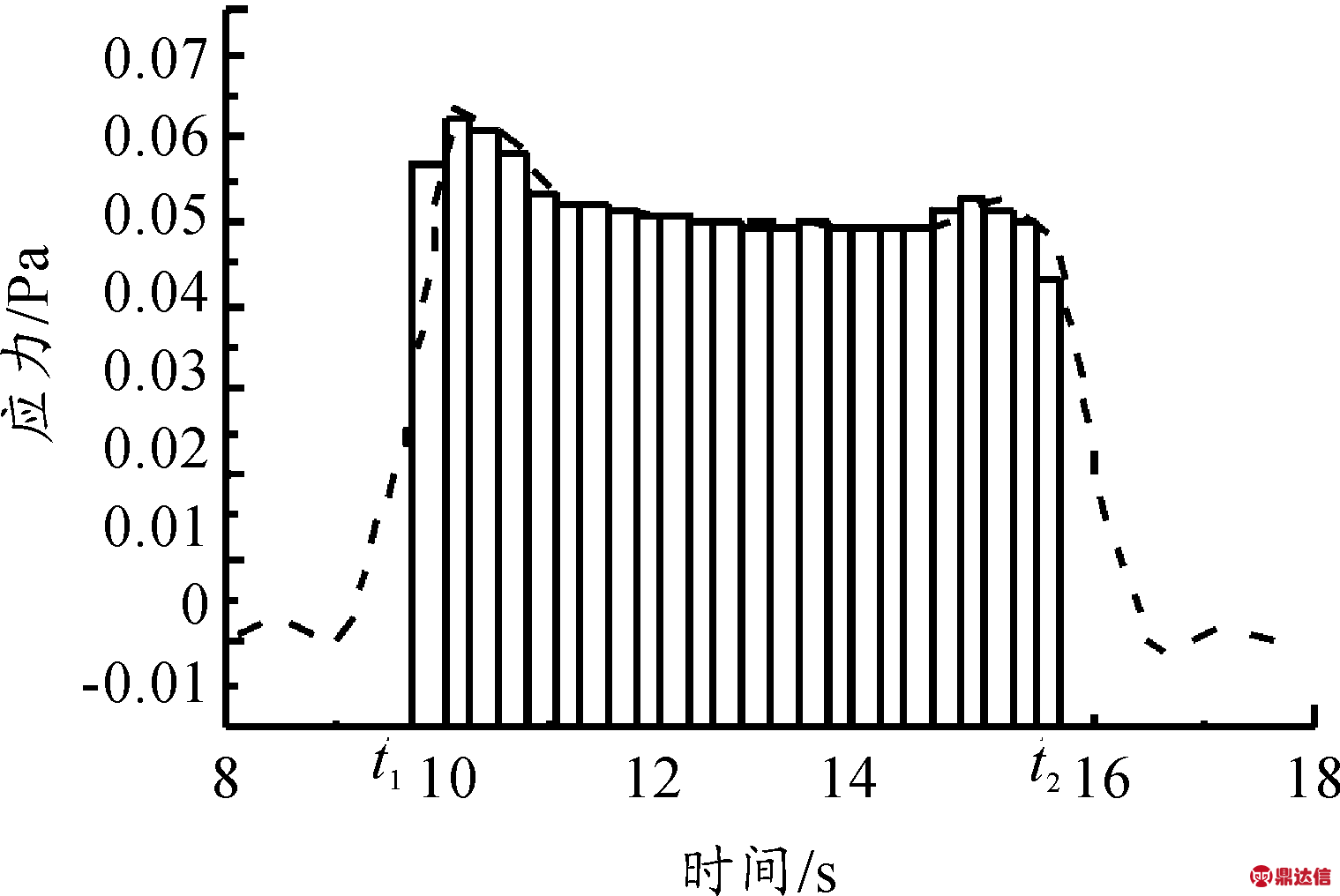
图1 节点应力的时间历程曲线
图1所示时间段t1~t2对应的应力值曲线,使用式(3)计算Δt时间段内的垫片的磨损量。
1.2 垫片磨损有限元仿真及结果分析
使用HyperWorks对垫片磨损过程进行仿真分析时,根据垫片在机械系统中的实际运行工况,在保证不影响结果精度且能降低电脑计算量的情况下,进行必要的模型简化及边界条件施加,建立垫片磨损的有限元模型(图2)。其中,上方为上衬套简化模型,中间部分为止推垫片模型,下方为静耳简化模型,起支撑作用。止推垫片、静耳保持不动,上衬套与垫片接触并作往复旋转运动。

图2 止推垫片磨损有限元模型
图3为不同工况下垫片磨损过程中相同时刻接触面的应力云图,在垫片运动过程中的某一时刻,不同位置节点的应力值是不同的。选取一种实验工况即载荷8 655 N、摆动频率1.6 Hz、角度2.5°、表面粗糙度为3.2 μm的情况下使用式(1)计算磨损厚度,要获得接触面中节点各时刻的应力值。并选取接触表面不同位置4个节点(41,51,61,71)。
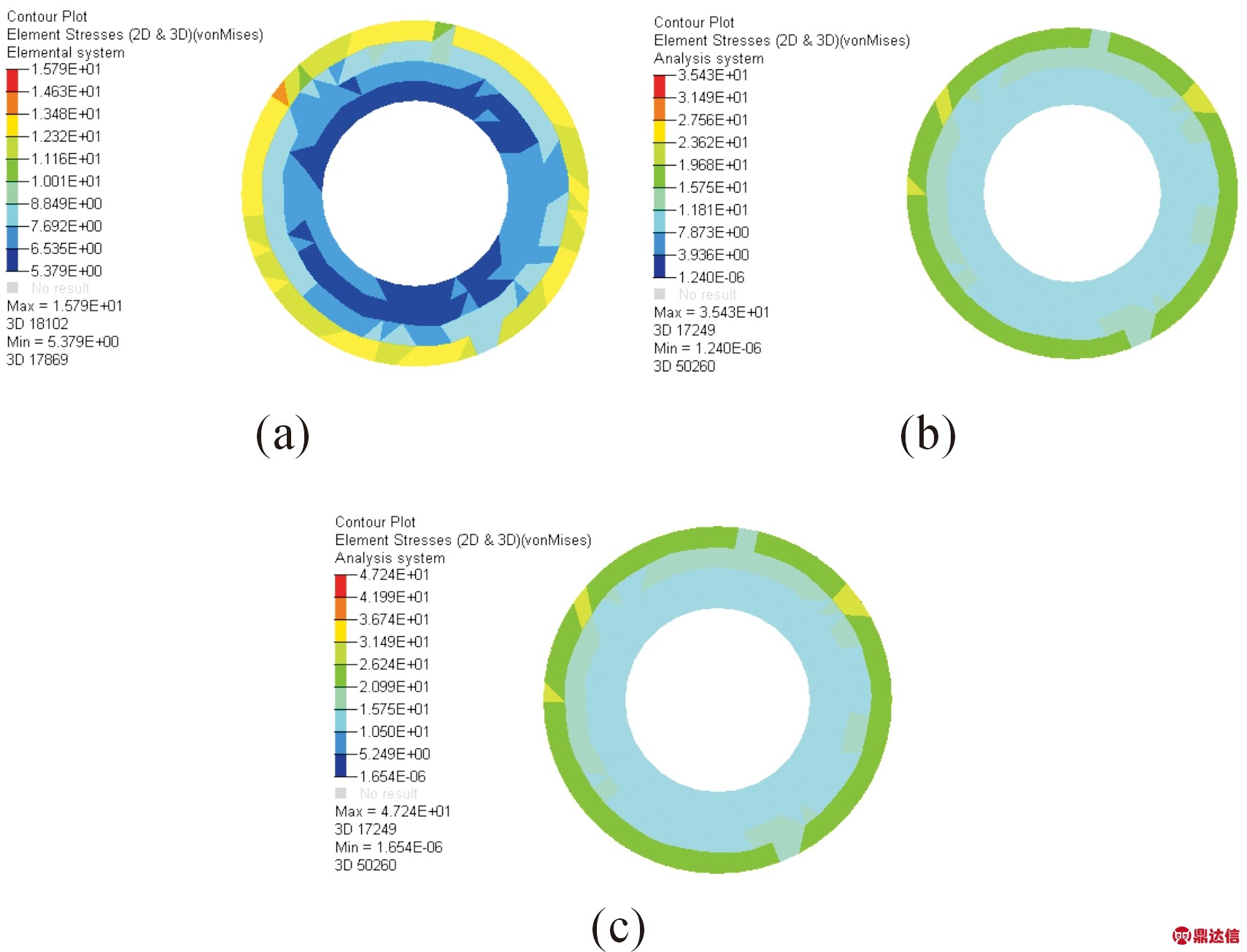
图3 不同工况下垫片表面应力云图
图4为同一接触面上的节点所对应的应力时间变化曲线,观察可知,4个节点的应力变化趋势一致且应力值差别不大。
如表1所示,为接触表面不同节点在同一时间步内磨损量变化曲线,选取41号节点为例,建立磨损量关于磨损次数的函数关系。
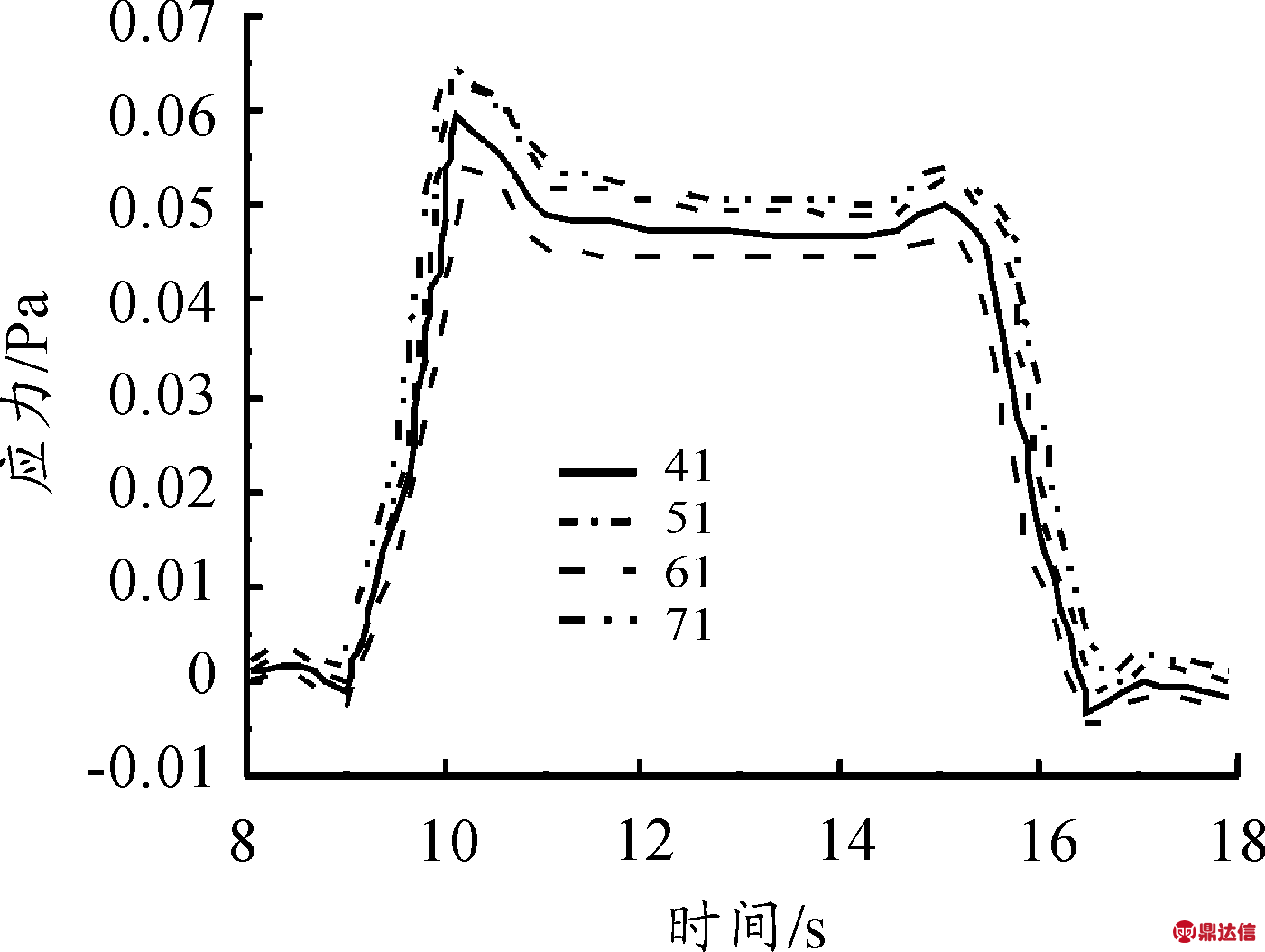
图4 不同节点应力随时间变化曲线
表1 不同节点模拟各步的磨损量变化
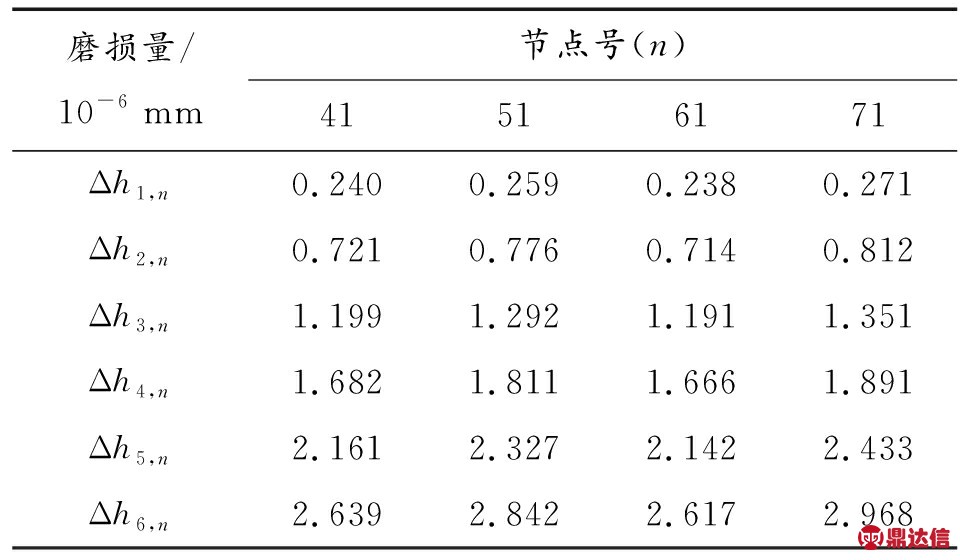
利用数值分析的方法,可得到垫片一次摆动后磨损量计算公式:

(4)
其中:h0=6.058,t1=1 449.560,A1=-21.024
则n次磨损量公式为


(5)
综上所述,式(5)为运用仿真分析及磨损模型计算结果共同拟合出的垫片总磨损量关于磨损次数的函数关系。
2 实验方案设计及结果分析
2.1 实验方案设计
本文所有垫片(如图5所示)磨损试验均在自制双向加载摆动磨损实验机上进行。图6为实验平台机构工作原理简图。图7为垫片实验装置图。
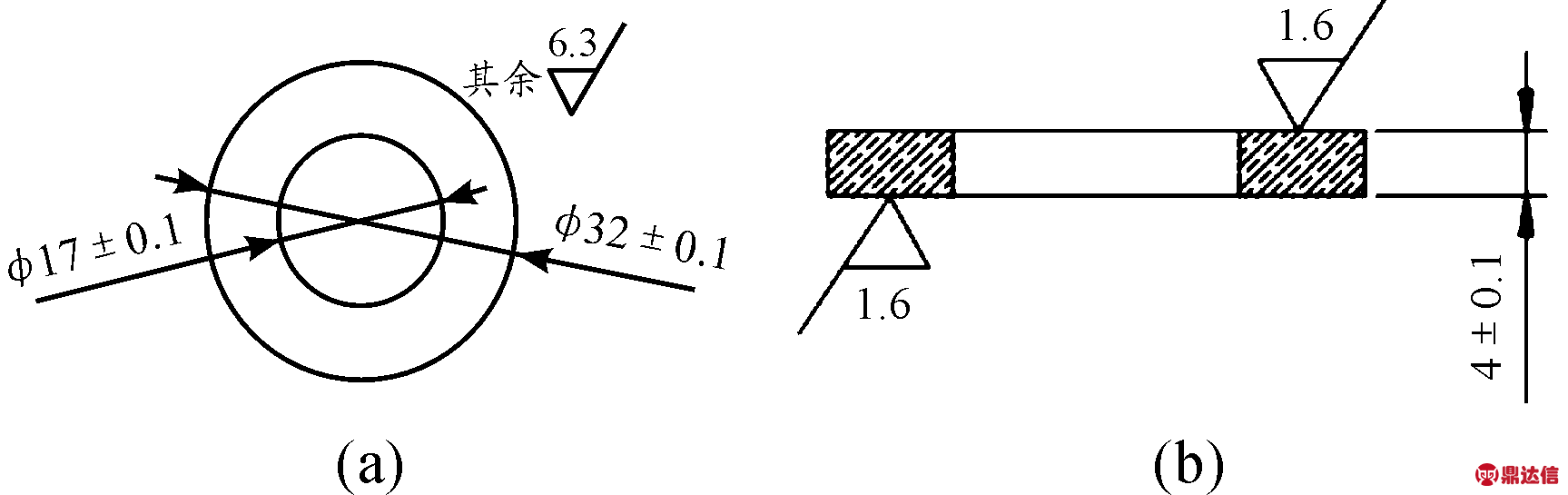
图5 止推垫片尺寸图
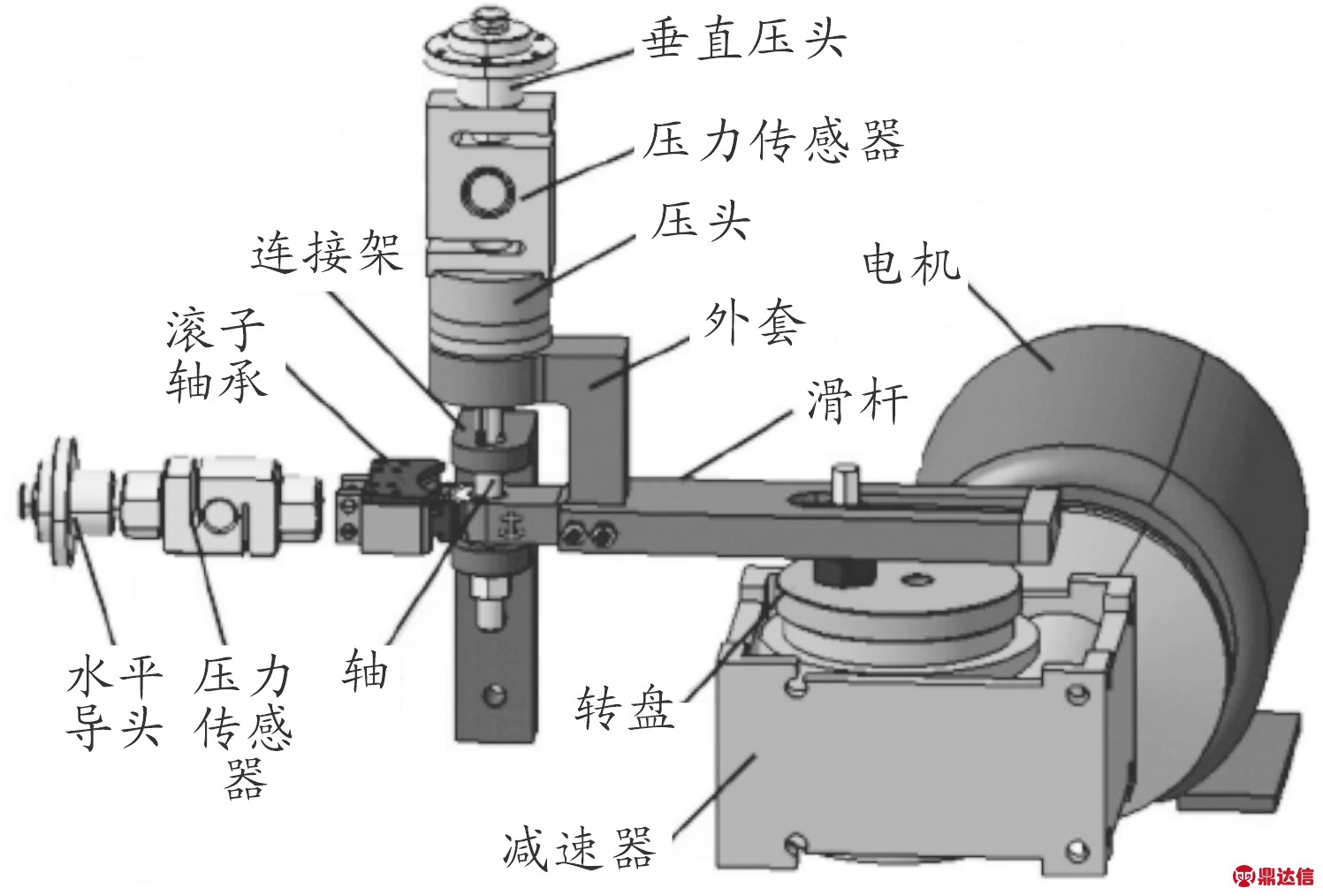
图6 机构工作原理简图
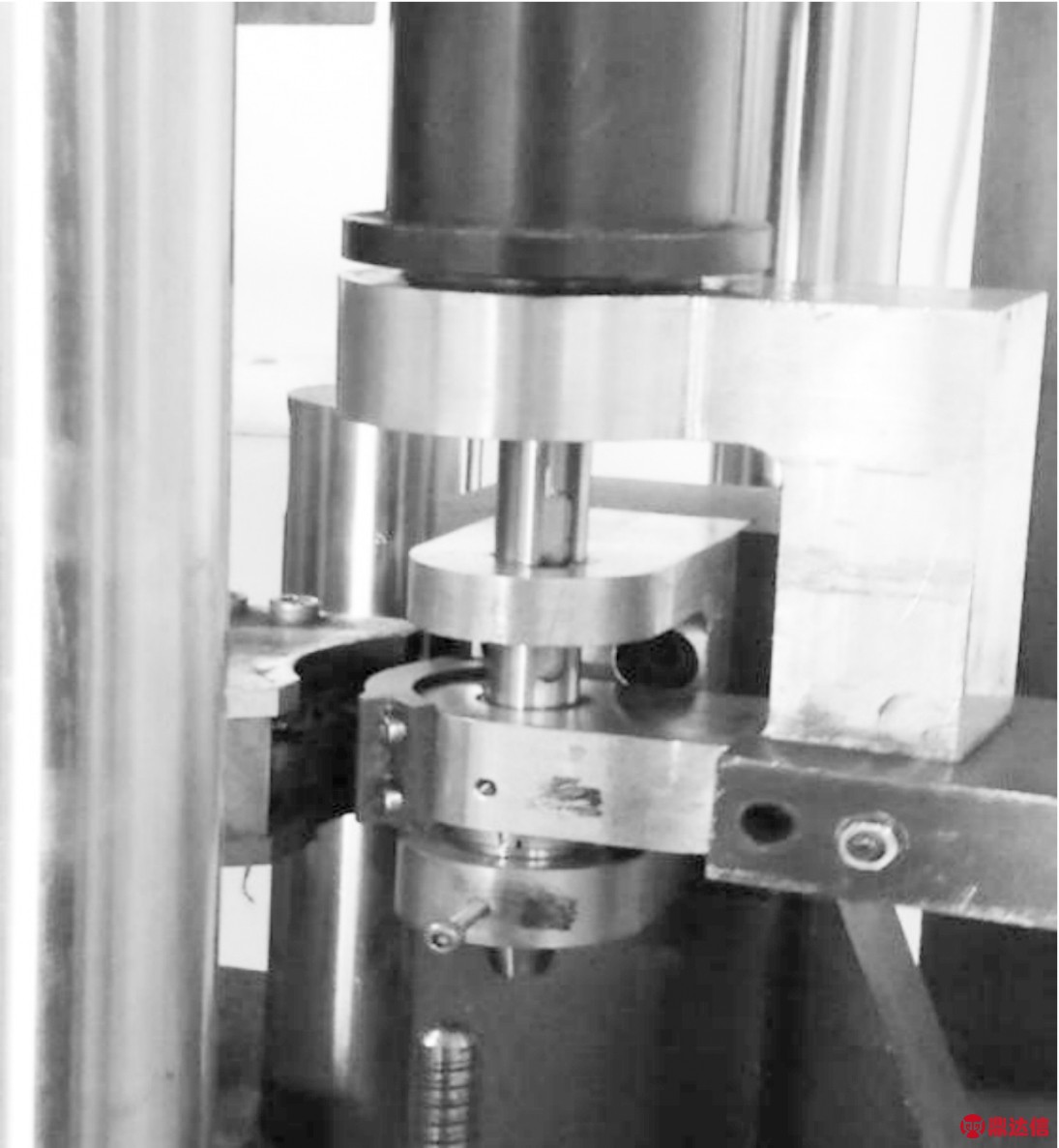
图7 垫片实验装置图
根据机械设备磨损副的材料,确定本实验所采用的磨损垫片材料为锰黄铜(HMn59-2-2),垫片材料的化学成分及尺寸如表2所示。实验的对磨环为上下衬套,所采用材料为不锈钢(1Cr18Ni9Ti),衬套的表面硬度高于磨损实验垫片。
表2 磨损试件化学成分 %

实验因素以及水平数如下:
载荷为3个水平,分别为5 770 N,8 655 N,11 540 N;
摆动频率为3个水平,分别为1.2 Hz,1.4 Hz,1.6 Hz;
表面粗糙度为3个水平,分别为1.6 μm,3.2 μm,6.3 μm;
摆动角度为2个水平,分别为±2.5°,±7.5°。
均匀磨损实验设计结果见表3。
表3 均匀磨损实验设计结果
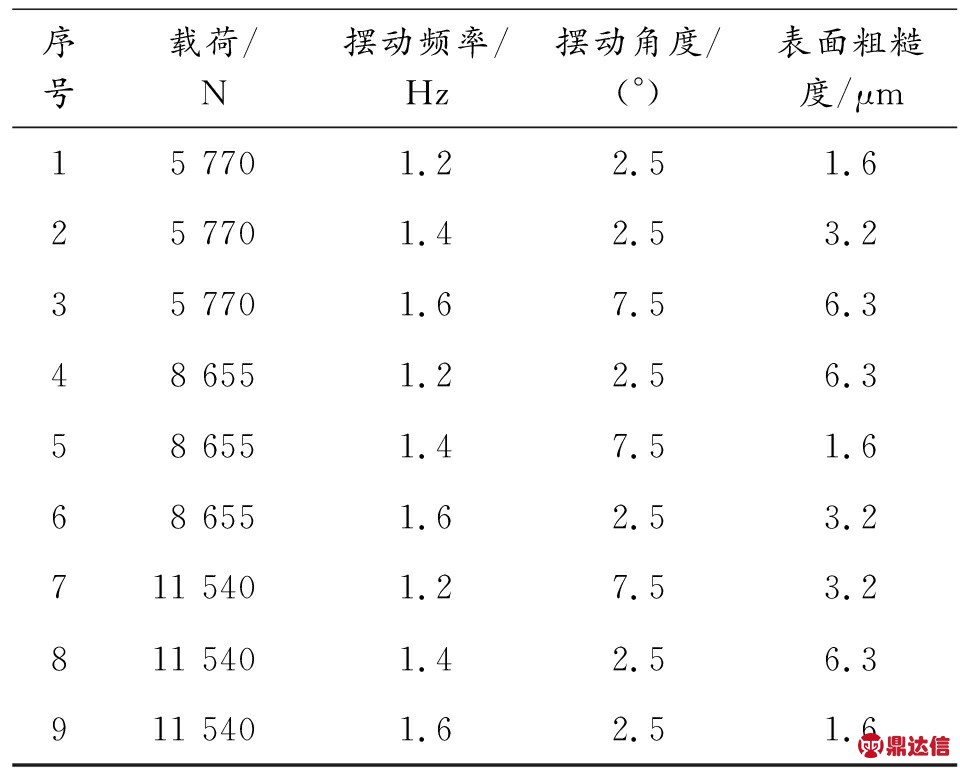
2.2 实验数据采集与分析
本实验是在干磨损条件下进行的摩擦磨损实验;每组垫片磨损总次数为10万次,每5 000次磨损后,进行磨损数据采集。测长法测量垫片磨损量。将实验垫片以90度划分为4个区域,相邻区域以“Ⅰ”、“Ⅱ”、“Ⅲ”、“Ⅳ”标记划分,获得4个测量点。并用称重法测量垫片质量磨损量。
垫片磨损过程主要存在黏着磨损和磨粒磨损两种类型并伴随转移膜的生成,会导致不同位置的磨损量存在一定的差距。经过磨损实验得到了垫片磨损量数据,并将数据分析处理,见表4。
表4 磨损实验结果
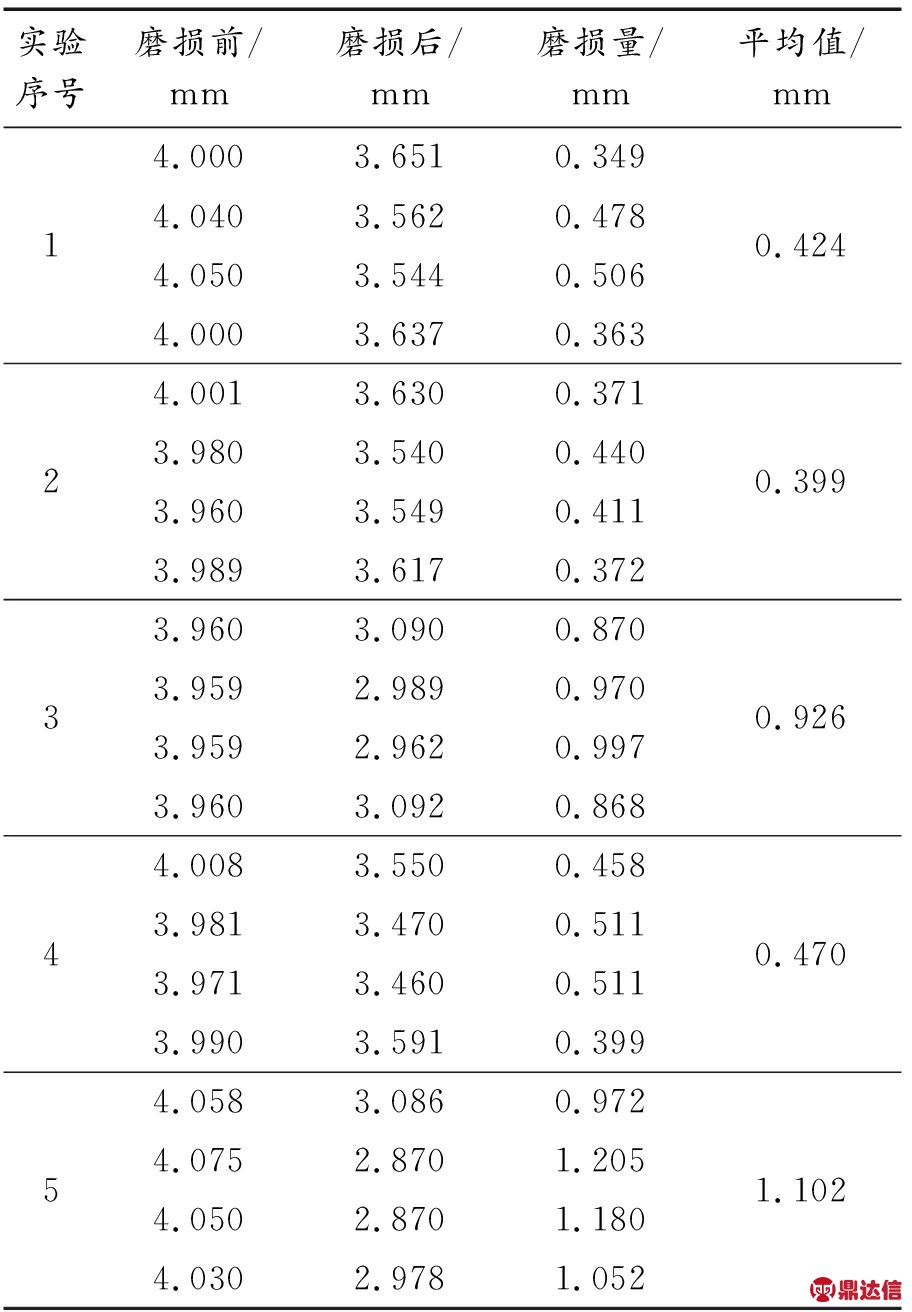
续表(表4)
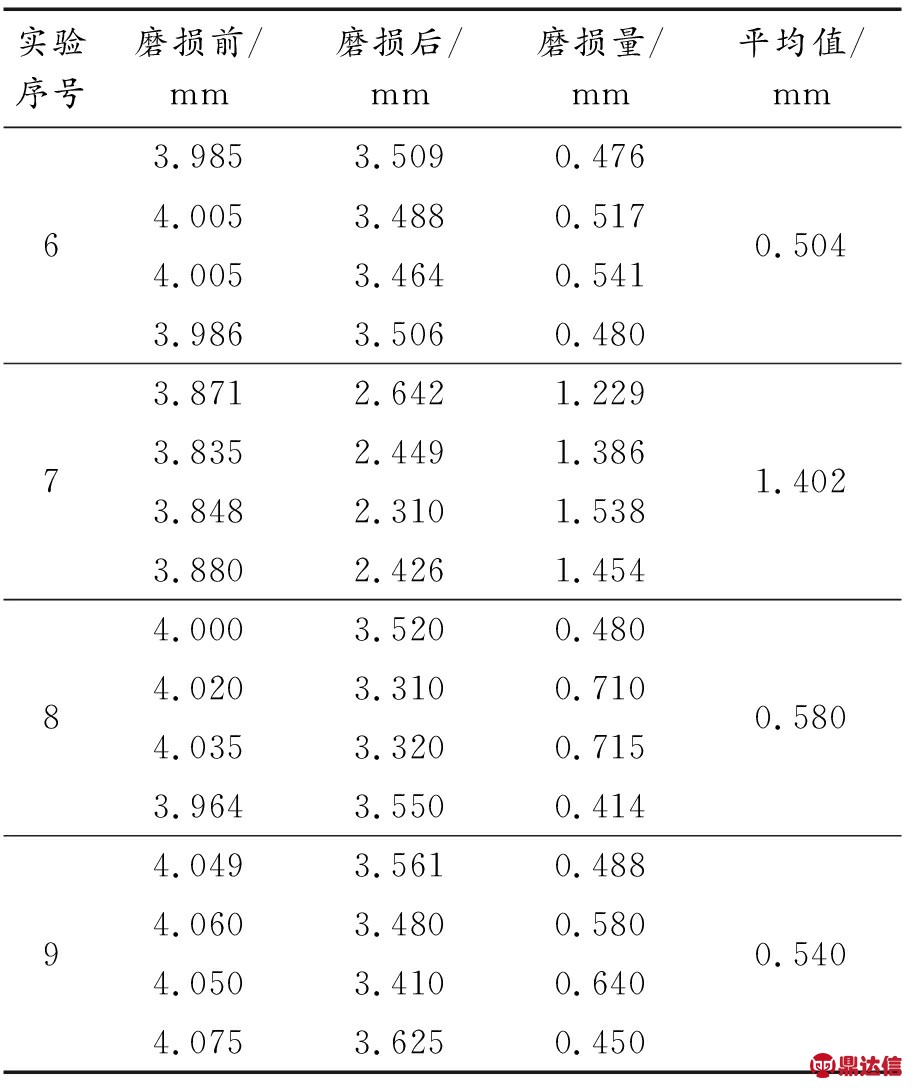
3 止推垫片磨损预测模型
3.1 偏最小二乘法磨损模型
偏最小二乘法是一种数学优化技术,是针对工程技术问题应运而生的一种数据处理方法[14]。由上文分析得到,在建立偏最小二乘法磨损模型时考虑4个因素,依次为载荷,摆动频率,摆动角度,表面粗糙度,分别用变量x1,x2,x3,x4表示,磨损量用y变量表示,多项式函数如下:
(6)
将潜在变量的数量定为3个时,将数据放入自变量矩阵:

(7)
式中
进行建立预测模型时,成分的个数即为潜在变量的数量。记因变量F0是因变量y的标准化向变量,有

(8)
式(8)中,是y的平均值,sy是y的样本标准差。
E0是集合X的标准矩阵,首先确定矩阵最大特征值的特征向量:
及成分t1=E0w1
(9)
求得回归方程向量
和系数矩阵
(10)
若得到m个成分t1,t2,…,tm,则得:
(11)
最后,可以变换成y对x1,x2,…,xp的回归方程:

(12)
接下来根据简化算法建立磨损预测模型(提取t1):
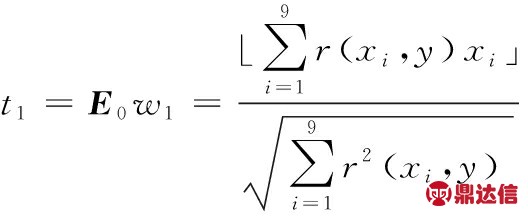
(13)
t1=0.350 1x1-0.137 0x2+0.481 12x3+


0.052 2x1x3-0.317 3x1x4-0.280 3x2x3-
0.236 4x2x4-0.297 2x3x4
(14)
做y在t1上的回归,提取成分t2:
t2=-0.007 8x1+0.518 1x2-0.151 2x3+


0.352 6x1x3-0.116 0x1x4-0.174 2x2x3-
0.208 8x2x4-0.110 1x3x4
(15)
做y在t2上的回归,提取成分t3:
t3=-0.007 8x1+0.518 1x2-0.151 2x3+


0.352 6x1x3-0.116 0x1x4-0.174 2x2x3-
0.208 8x2x4-0.110 1x3x4
(16)
自变量对因变量主效应的标准回归系数如表5所示。
表5 各自变量对因变量主效应的标准回归系数

抽取成分t3,最后得到偏最小二乘预测模型,结果如式(17):
y=0.289 6+10-5x1-0.271 8x2+0.131 5x3-


1.315×10-6x1x3-1.03×10-7x1x4-
0.035 741 7x2x3+0.002 8x2x4-0.001 355x3x4
(17)
3.2 磨损预测模型检验
根据式(17),计算了3组不同工况下的磨损量预测值,并与实验值进行比较,结果如表6所示。
结果表明:在通过实验值与磨损预测值的对比,结果显示相对误差较小,符合预期要求。
表6 实验值与磨损预测值比较
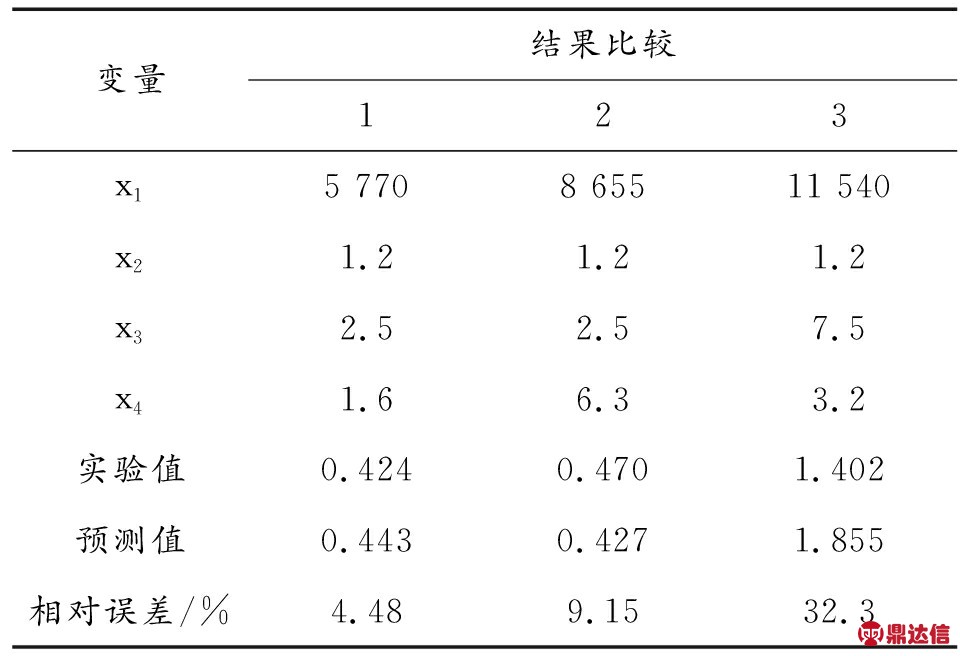
表7 实验值与仿真预测值的比较
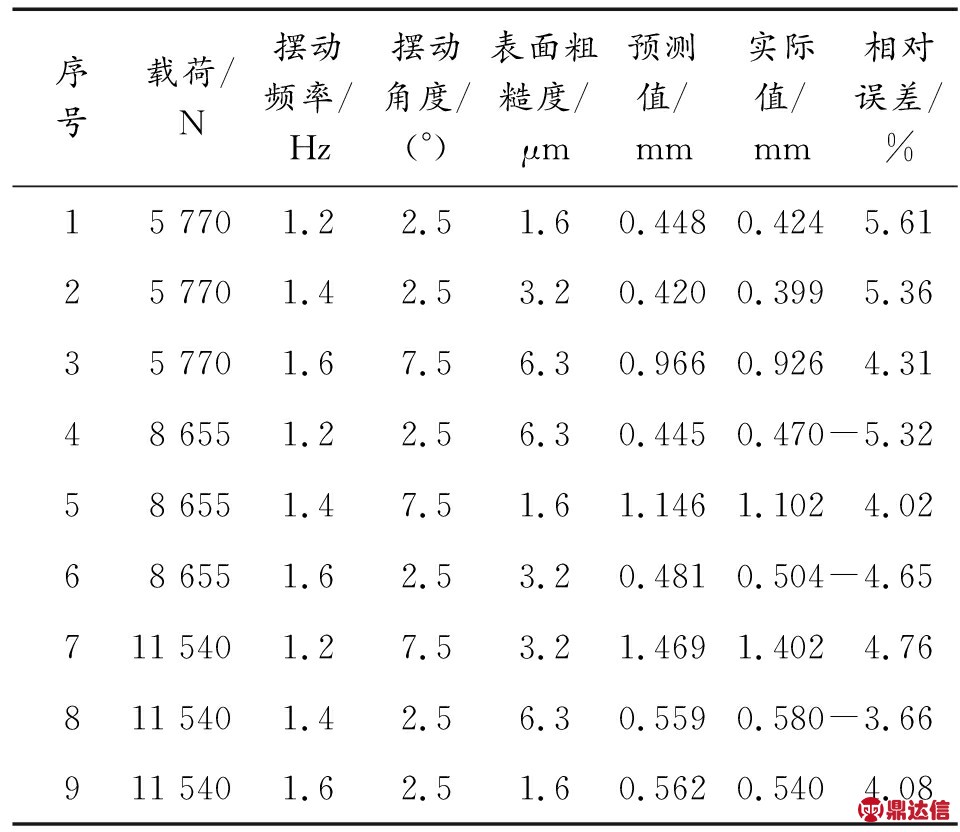
结合以上数据,将垫片磨损实验值与有限元仿真预测值进行对比,由表7可知两者相对误差稳定在±5%左右,说明仿真预测较准确,精准可以接受。
4 结论
运用Archard磨损模型与有限元分析相结合的方法,并根据仿真结果拟合出了垫片磨损量与磨损次数的函数关系。根据结果拟合出的磨损量公式对不同工况下磨损预测值进行了计算。针对止推垫片实际运行工况,实验方案按照均匀实验方法对影响因素进行科学合理的排列,获得了载荷、摆动频率、表面粗糙度、摆动角度4个影响因素下,垫片磨损量以及磨损表面形貌等实验结果,并根据实验结果建垫片磨损预测模型,并将预测值与磨损实验值进行了分析比较,结果显示预测效果和精准度都比较好,能用于实验工况水平下的垫片磨损量预测。