摘 要:针对飞机金属螺栓连接结构中螺栓孔孔边裂纹定量监测需求,提出了一种基于花萼状涡流传感器的损伤监测智能垫片,构建智能垫片监测半解析模型,分析垫片材料电磁属性对损伤监测效果的影响,并进行在线监测试验验证分析结果.半解析模型结果表明,智能垫片各个感应通道的幅值比变化量随垫片磁导率增大而增大,而随垫片电导率增大而减小.程序载荷谱作用下2A12-T4铝合金试件疲劳裂纹监测试验结果表明,铝合金和不锈钢材料的支撑垫片均能有效实现裂纹损伤的定量监测,但不锈钢材料的智能垫片其监测曲线比铝合金材料的智能垫片平滑,监测效果好.将各通道幅值比变化曲线中的拐点作为特征点,通道1能够对累积损伤进行监测,通道2,3,4能够对疲劳裂纹扩展长度进行定量监测,监测精度达到1mm.
关键词:智能垫片;损伤监测;半解析模型;涡流传感器
为了保障诸如飞机这样的大型复杂机械结构的安全性、完整性、适用性与耐久性,需要对结构性能进行安全评定,而安全评定则主要依据结构损伤监测系统所获得的数据以及数据分析结果.结构损伤监测技术将先进的传感/驱动元件集成在飞结构中,研究信息采集-信息传输-信息处理-信息物理含义-结构的健康状况之间的本质关系,获取结构运行状态参数数据,及早发现并处理结构安全隐患和耐久性缺陷,识别结构突发和累计损伤(含裂纹)发生位置与程度,并对发生后果的可能性进行判断与预测[1].
目前国外较为成熟的结构损伤监测技术有光纤传感器[2]、压电传感器[3]、相对真空度(CVM)[4]和声发射技术[5]等,在国外军用和民用航空领域都得到不同程度的应用.在国内,已开始实际工程应用,例如大型桥梁、隧道、大坝、海洋平台、高层建筑、航空航天器等[6-8].但在航空航天领域,对健康监测开展的研究较晚,结构往往工作于较恶劣的环境中,这就要求传感器必须满足耐久性、稳定性与结构相容性等要求.因此,研发损伤识别精度和准确度较高、耐久性较好、抗干扰能力强、综合效费比高的损伤监测传感器,仍是一个亟待解决的问题.
针对飞机金属螺栓连接结构中螺栓孔孔边裂纹定量监测需求,提出了一种基于花萼状涡流阵列传感器的损伤监测智能垫片,通过构建半解析正向等效模型分析了垫片材料电磁属性对智能垫片损伤监测效果的影响,并进行在线监测实验验证分析结果.
1 损伤监测智能垫片
在Goldfine等[9]研究的基础上,提出了一种花萼状涡流阵列传感器,花萼状涡流传感器的典型外形结构示意图如图1所示.
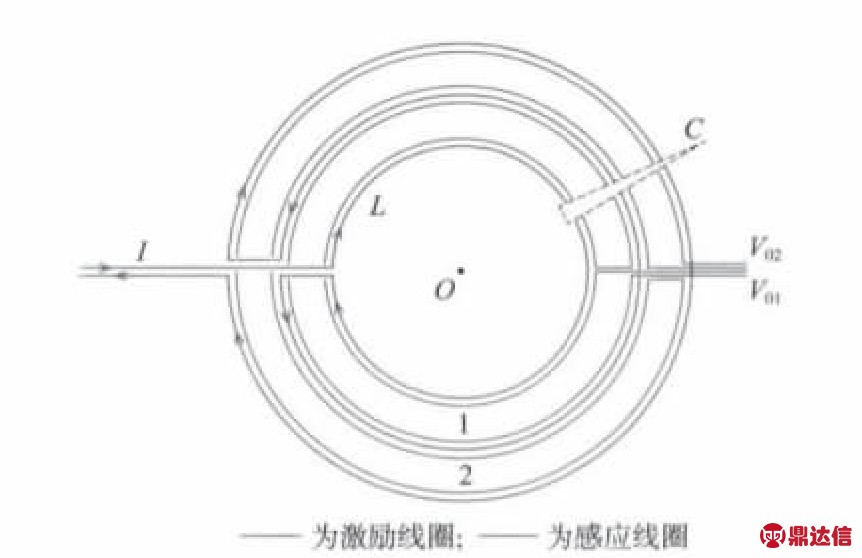
图1 花萼状涡流传感器典型外形结构示意图
Fig.1 Typical geometric schematic of rosette eddy current sensor
花萼状涡流传感器的结构损伤定量监测能力主要取决于激励线圈下间隔分布的环状感应线圈.各个环状感应线圈中的感应电流较小,其各自之间能够保持相对的独立性,环状感应线圈只接收激励场在监测空间内的发射场,而环状感应线圈只对其线圈平面下的损伤敏感.例如,当结构损伤C到达位置1时,输出V01信号,当结构损伤C到达位置2时,输出V02信号,实现了对损伤的定量监测.环状感应线圈的间隔即为花萼状涡流传感器的监测精度.
当将花萼状涡流阵列传感器应用于螺栓孔孔边裂纹的监测时,主要存在如图2所示的3种典型应用方式.
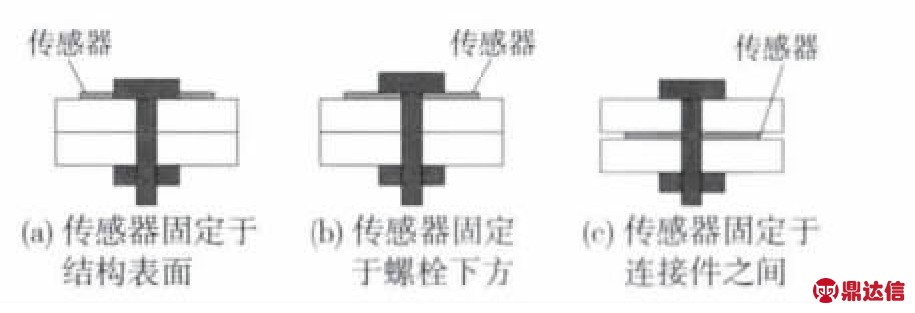
图2 传感器在螺栓连接结构处的典型应用方式
Fig.2 Typical application of sensor on bolted-joint structure
图2(a)的方式适用于裂纹容限较大的结构,如蒙皮,这种应用方式对传感器的承载和耐磨性能要求不高;而对于裂纹容限较小的结构,传感器采用如图2(b)和图2(c)所示固定方式,这2种方式下传感器与金属结构应变的不一致会导致传感器产生微动磨损,从而对涡流阵列传感器的承载能力和耐久性提出严格要求.针对花萼状涡流传感器承载能力和耐久性需求,本文提出一种损伤监测智能垫片,其示意图如图3所示.
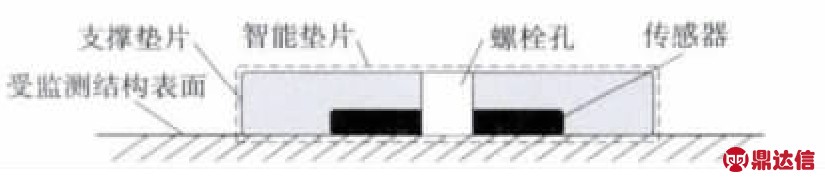
图3 损伤监测智能垫片示意图(截面图)
Fig.3 Schematic of smart washer(cross-section)
损伤监测智能垫片由花萼状涡流传感器和支撑垫片构成.花萼状涡流传感器是智能垫片的功能部件,用于实现智能垫片对螺栓孔孔边裂纹定量监测,支撑垫片是智能垫片的结构支撑部件,用于提高功能部件花萼状涡流传感器的耐久性.花萼状涡流传感器通过中心通孔固定在被监测金属结构表面.针对支撑垫片材料选择问题,大部分金属支撑垫片能够满足智能垫片的承载和耐久性需求,但考虑到金属支撑垫片作为导电材料,其必然对智能垫片中花萼状涡流传感器的损伤监测效果产生影响.
2 智能垫片半解析正向等效模型
建立智能垫片的损伤监测半解析正向等效模型.在等效模型中,将结构损伤等效为结构电磁参数的变化,例如将损伤等效为传感器与被监测试件提离距离的变化,或被监测试件电导率的变化.
2.1 智能垫片在线监测基本物理模型
将图3所示的智能垫片应用于金属螺栓连接结构中孔边裂纹的在线监测中,建立的在线监测基本物理模型(横截面)如图4所示.
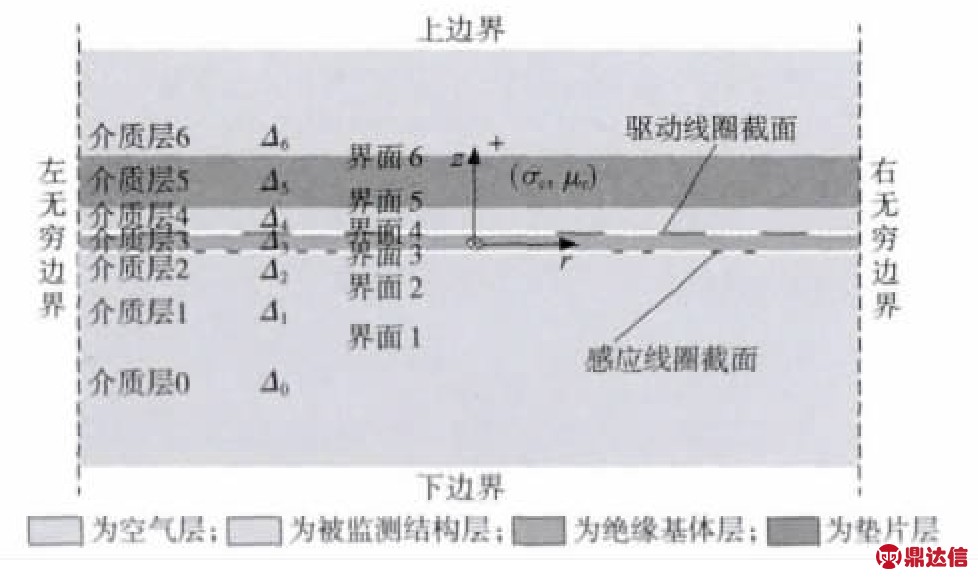
图4 智能垫片在线监测基本物理模型(横截面)
Fig.4 Physical model for damage monitoring of smart washer(cross section)
介质层3为传感器的基材,基材上下表面分别分布着激励线圈和感应线圈;介质层2为传感器与被监测结构(介质层1)之间的提离空气层;介质层4为支撑垫片与花萼状涡流传感器之间的贴附空气层;介质层6和介质层0分别是智能垫片上方和被监测结构下方的空气层;支撑垫片层5中的Gc和μc即为金属支撑垫片材料的电导率和磁导率.图中Δ表示介质层的厚度.各介质层之间的交界处定义了分界面,特殊的是,激励线圈和感应线圈的厚度相对于传感器径向尺寸而言可以忽略,故将激励线圈和感应线圈简化成面,分别位于分界面4和分界面3上.在基本物理模型中,定义了上、下、左、右4个无穷边界和模型的三维柱坐标系(在截面图中,角度φ未能标出).
2.2 建模路线
建模路线如图5所示.本节建立的半解析正向等效模型类似于传统的多层导电结构谐波涡流场的积分/级数解析模型,而后者从Cheng、Dodd和Deeds[10-11]开始,经 Theodulidis和 Kriezis[12]发展其解析理论模型已趋于成熟.但是这些传统的多层导电结构谐波涡流场积分/级数解析模型无法应用到本文所提出的花萼状涡流传感器正向模型中,原因为:① 传统的多层导电结构谐波涡流场积分/级数解析模型的应用对象是自感式涡流传感器,即传感器线圈既产生激励磁场又感应涡流磁场,而本文的花萼状涡流传感器中拥有独立的激励线圈和感应线圈;② 传统的多层导电结构谐波涡流场积分/级数解析模型在构建过程中忽略线圈中电流分布的集肤效应,而本文提出的花萼状涡流传感器其工作频率在1MHz以上,集肤效应无法忽略,这将导致在模型构建过程中无法直接从磁矢边界条件中得到Bessel级数/积分系数.

本文借鉴加权残值法在解微分方程的思路,将线圈界面处线电流密度作为待求函数,在线圈截面处配置离散点和子域,并将离散点处的线电流密度作为待定系数,通过傅里叶-Bessel级数形式得到线圈处线电流密度的试函数,构建得到模型的数值部分.根据时谐场位函数方程得到线圈界面处线电流密度和磁矢的Bessel级数系数关系式,并基于法拉第电磁感应定律,建立线圈处线电流密度所满足的微分方程,后经选取积分路径消掉微分算子,构建得到模型的解析部分.结合模型数值部分和解析部分,在线圈截面处的子域建立残值线性方程组,并根据线圈截面处配点之间线电流密度线性分布假设,构建得到导纳总体矩阵,最终求得传感器多通道跨导.
3 模型计算结果
参考二端口微波网络的概念,将跨阻定义为传感器的输出,对第n个通道的跨阻定义为

式中:VSn为第n个感应线圈的感应输出电压;IT为激励线圈总电流.式(1)定义的跨阻量为复数量,具有幅值和相位2个自由度,即感应线圈输出电压和激励线圈激励电流的幅值比和相位差(下文中简称为幅值比和相位差),本文将跨阻量ZSn简化为幅值比量ASn进行研究.
本节以花萼状涡流传感器监测2A12-T4铝合金结构疲劳裂纹损伤为研究对象,将结构疲劳损伤等效为2A12-T4铝合金电导率的变化.选取电导率从17.4MS/m减小到10.0MS/m,图6和图7分别为电导率变化引起的幅值比变化量Δ(ASn)随支撑垫片相对磁导率和电导率的变化曲线.在图6中,支撑垫片的电导率为10MS/m,激励频率为1 MHz,由图6可知幅值比变化量Δ(ASn)随支撑垫片的磁导率增大而增大.在图7中,支撑垫片的相对磁导率为1,激励频率为1MHz,由图7可知幅值比变化量Δ(ASn)随支撑垫片的电导率增大而减小.故在智能垫片中,应选取电导率小且磁导率大的支撑垫片材料.
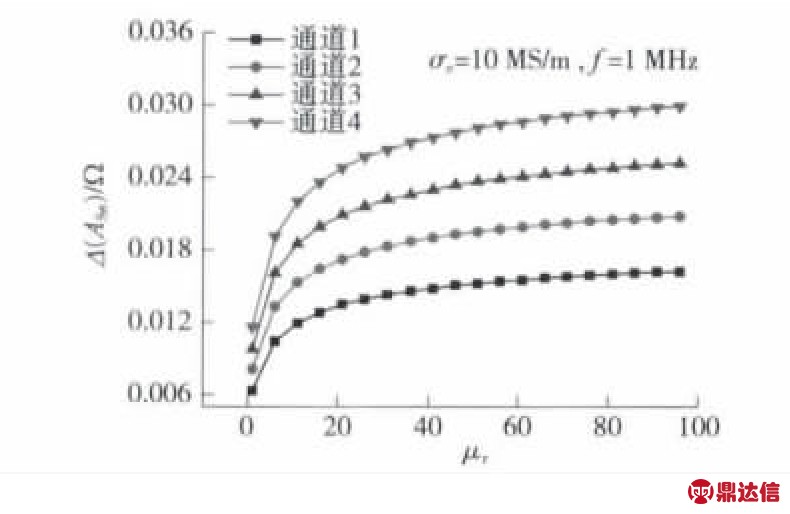
图6 Δ(ASn)随支撑垫片相对磁导率变化曲线
Fig.6 Δ(ASn)varying by relative permeability of washer
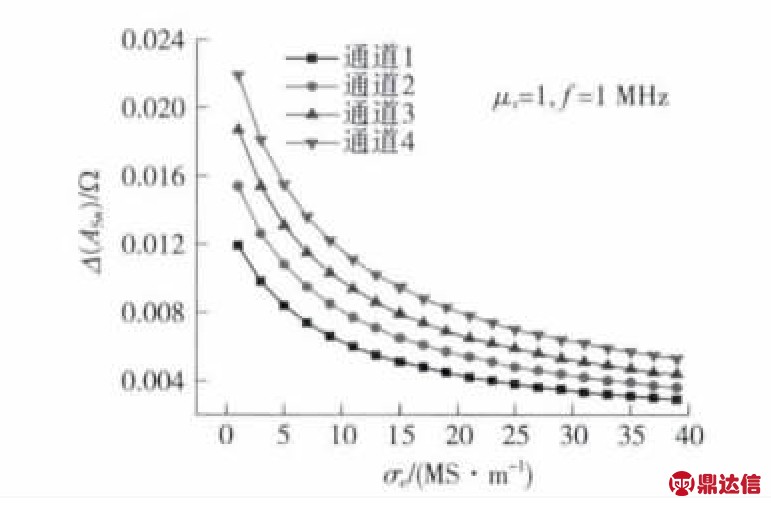
图7 Δ(ASn)随支撑垫片电导率变化曲线
Fig.7 Δ(ASn)varying by conductivity of washer
4 铝合金试件疲劳裂纹监测试验
进行2A12-T4铝合金拉伸疲劳试验以验证模型分析结果,用于比较的支撑垫片材料分别为不锈钢和铝合金.首先通过柔性电路板工艺制备花萼状涡流传感器,制备的传感器具有一个激励线圈通道和4个感应线圈通道,相邻感应线圈的间距为1mm.同时,为得到疲劳弧线,以便对断裂后试件进行断口定量分析,采用高低载交替的程序载荷幅谱,如表1所示.
表1 程序载荷谱
Tab.1 Constant loading spectrum

将试验件安装于疲劳试验机(MTS810)上,并将传感器安装于螺栓孔处,连接测量设备;启动裂纹监测系统和疲劳试验机,归一化激励信号频率为0.3,载荷施加频率为15Hz;试验过程中监测传感器各感应线圈通道的输出信号,直至试验件断裂停止.
根据采样周期与载荷施加频率关系,并使用平滑法对原始数据进行降噪处理,得到传感器输出信号随疲劳循环次数的变化曲线.图8和图9分别为铝合金和不锈钢垫片材料下的传感器4个通道幅值比信号随试件载荷次数的变化曲线.
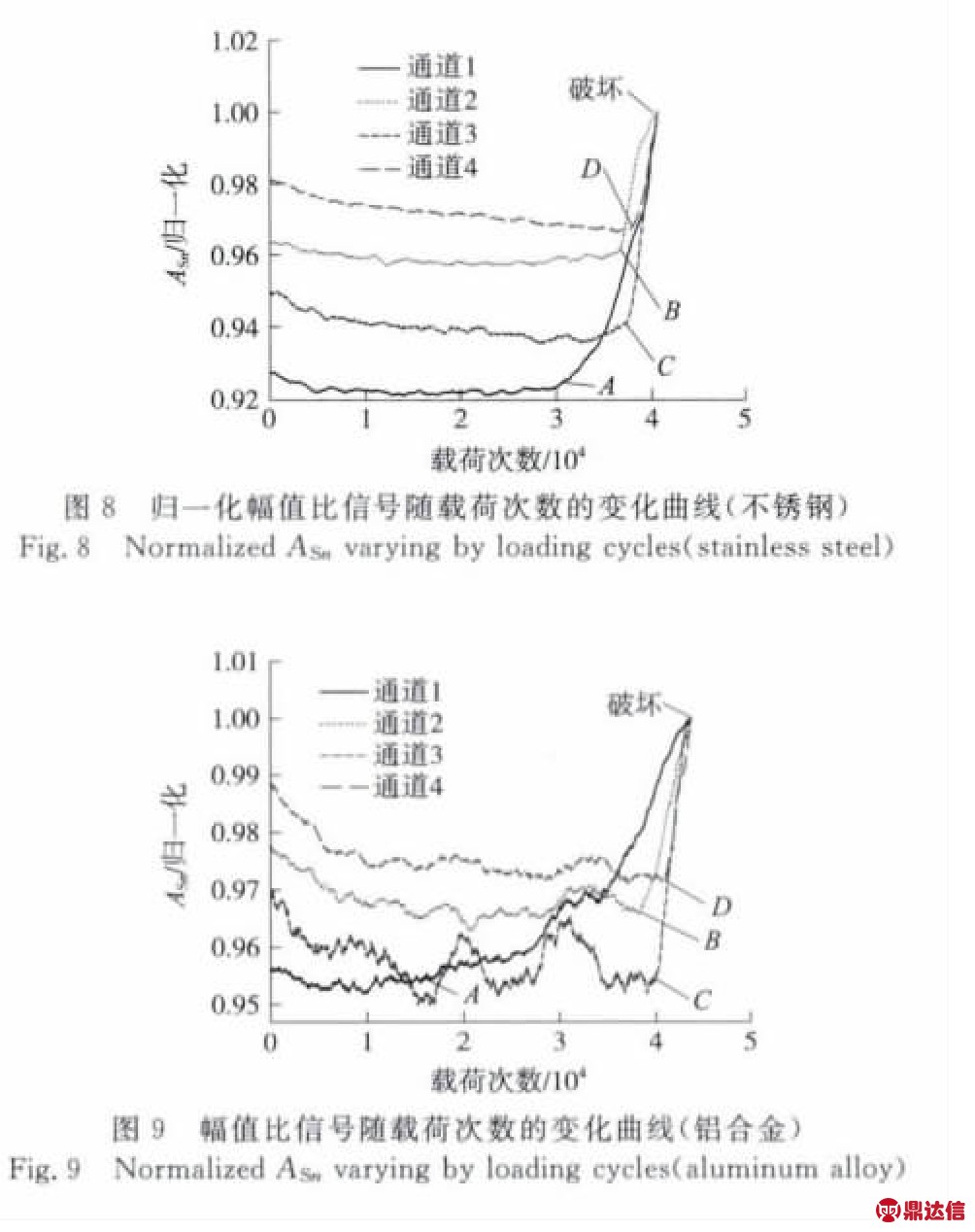
由图8和图9可知,将各感应线圈通道幅值比信号随载荷次数变化曲线中的拐点作为特征点,铝合金和不锈钢材料的智能垫片均能实现对2A12-T4铝合金拉伸疲劳试验件疲劳裂纹的定量监测.其中,第1感应通道的点A为累计损伤起始点,第2、3和4感应通道的点B,C和D分别对应为裂纹长度达到1,2,3mm时的载荷循环次数.
在上述试验方案中,采取了高低载方式的程序载荷谱,其目的为得到疲劳弧线,通过对疲劳弧线进行断口定量分析得到疲劳裂纹扩展曲线,并将疲劳裂纹监测结果与断口定量分析结果进行对比,对比结果表明,通过通道幅值比监测曲线拐点来监测裂纹扩展的方法正确.
由图8和图9中各通道曲线在载荷过程中的变化趋势可知,由于铝合金垫片材料其电导率较大,激励线圈所产生的变化磁场也会在垫片表面产生较强的涡流场,感应线圈的感应电压信号大大减小,从而引起铝合金垫片材料下的智能垫片其信号的信噪比低,导致曲线不平滑.而相对于铝合金,不锈钢的电导率较低,故不锈钢材料的智能垫片其损伤监测效果要好于铝合金材料的智能垫片,监测试验结果验证了模型分析结果.
5 结 论
① 智能垫片各个感应通道的幅值比变化量随垫片磁导率增大而增大,而随垫片电导率增大而减小.
② 将各感应线圈通道幅值比信号随载荷次数变化曲线中的拐点作为特征点,铝合金和不锈钢材料的智能垫片均能实现对2A12-T4铝合金拉伸疲劳试验件疲劳裂纹的定量监测.
③ 不锈钢材料的智能垫片其监测曲线比铝合金材料的智能垫片平滑,损伤监测效果更好.