摘 要:介绍了新型复合活塞环的静态仿真理论依据,对活塞环建立了气密分析模型,模拟计算了新型复合活塞环与传统活塞环的密封特性和相同状况下的静态试验研究。结果表明,新型复合活塞环压力维持时间是传统活塞环的1.63倍,密封性能提高了14%。同时模拟计算了装有新型复合活塞环某单缸机转速为,时活塞环所受的摩擦力,计算结果弥补了静态试验的不足。
关键词:复合式活塞环;密封;摩擦;润滑
随着内燃机不断向小型化、低排放、高速化、轻量化的方向发展,对燃烧室高温,高压的燃烧环境提出了更高的要求,燃烧内零部件也受到了越来越严峻的挑战。活塞环作为构成燃烧室的重要零件具有“密封、刮油布油、导热和支承”四大功能[1],其中密封性更是评价活塞环好坏的重要标准之一。其密封性能对发动机的性能有很大的影响。密封不良,直接影响到发动机燃烧效率,降低发动机功率,并且浪费燃料,而且排放物对环境的污染较为严重。因此提出并对新型复合活塞环的试验研究具有重要的意义。
1 复合式活塞环的结构及密封分析
1.1 复合式活塞环的结构
我们提出了一种新结构的新型复合活塞环,新型复合活塞环采用三环叠加为一环装入一个环槽的单环槽结构,并且环与环开口相互错开120°。上环和下环采用正扭曲环,中间环较上环和下环要厚一些,同时中间环开口间隙要大一些,以补偿热膨胀量,防止活塞环卡死在活塞环槽中。其结构见图1。
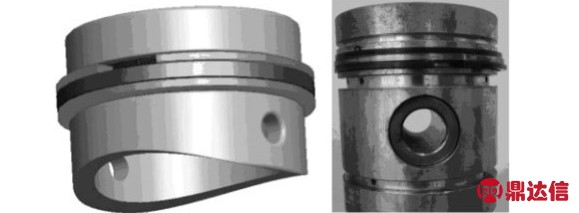
图1 新型复合活塞环三维模型和实物图
1.2 复合式活塞环密封性分析
图2 为新型复合式活塞环的结构图,其中上浮动气环,下浮动气环主要密封气缸壁和活塞之间的间隙。中间稳定气环配合上环和下环一起密封活塞环开口间隙。气体首先从燃烧室流进到气缸壁与活塞之间的间隙中,然后气体通过活塞环上端面和活塞环槽上侧面之间的间隙进人到活塞环背面中。由于此时活塞环开口间隙已经被封闭了,气体只能沿活塞环端面进入背隙空间。同时气体的曲折流动,也可以有效地增加流动阻力,减小逸放系数,从而减少气体泄漏量。
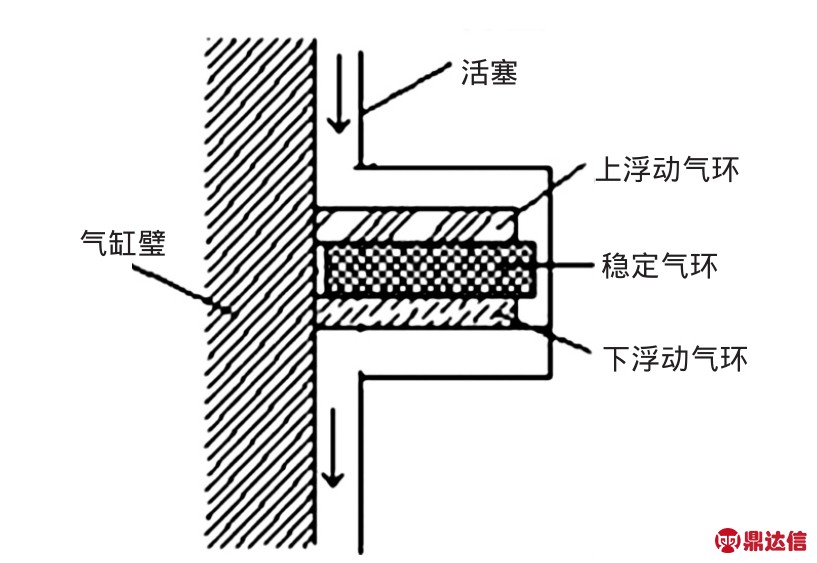
图2 新型复合式活塞环结构图
上下两环的结构可以增加活塞环自身的弹力,从而增强其自密封功能;材料的减少和制作工艺的优化降低了活塞环生产成本;中间稳定环的截面积和质量与上下浮动环不同,所以共振频率不同避免了活塞往复运动过程中所造成的活塞环悬浮和颤振;同时环与环之间相对运动可以使新型活塞环具有一定的自洁能力,避免积碳带来的影响;由于环开口间隙漏气量小,导致气体压力在活塞环所受到的力中起主要作用,这使得活塞环与环槽贴紧,有助于密封[2];因此,新型复合式活塞环使发动机的环保性、经济性和动力性将会有提高。
2 复合式活塞环密封性数值模拟
2.1 数学建模
发动机正常工作的时候,气体只能在闭口间隙处的通道发生流动。在压力差的作用下,气体从高压侧向低压侧流动,其质量流量可用一维具有常逸放系数的喷管流量公式来计算[3],具有n个活塞环的泄漏气体流动模型如图2所示,环1到环n+1是按燃烧室到曲轴箱方向顺序排列,A为漏气通道面积,T为气体温度,P为压力,V为稳压气罐和气缸总体积,Qn为n侧活塞环后的气体质量流量。
那么在压缩行程,第n侧的压力总高于第n+1侧的压力这时有
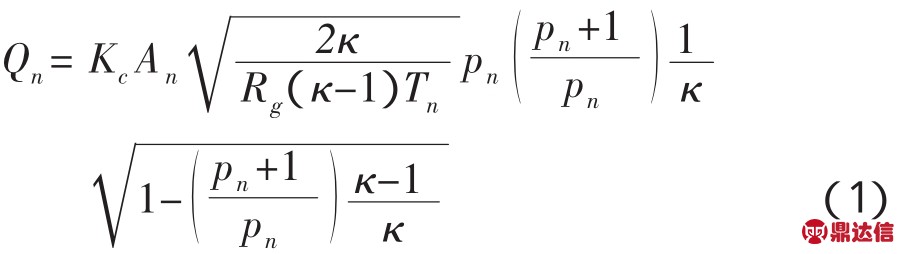
式中:
Kc为逸放系数;
An为漏气通道面积;
Rg为气体常数,取287.1J/(kg·K);
κ为气体比热,取1.4。
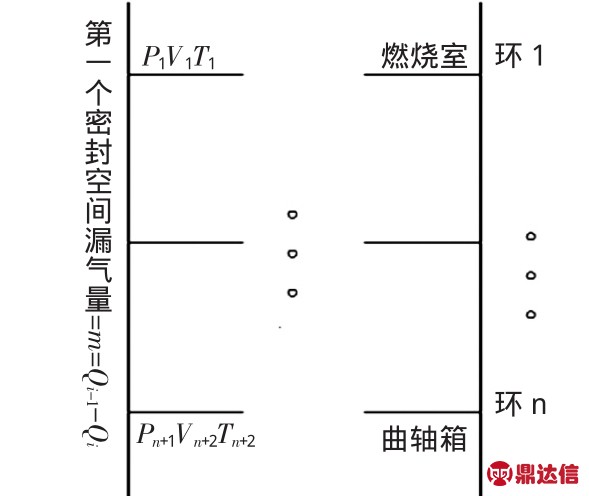
图3 气体泄漏计算模型
流动气体各参数应满足气体状态方程
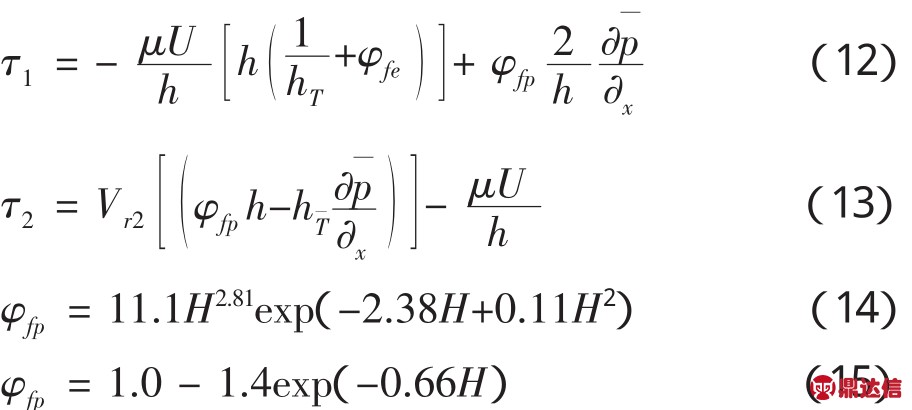
设时间t内,
有

而侧空间内气体质量的变化等于流入的质量与流出的质量差,
即

将式(2)应用于第(n-1)个活塞环,并代入式(3)得
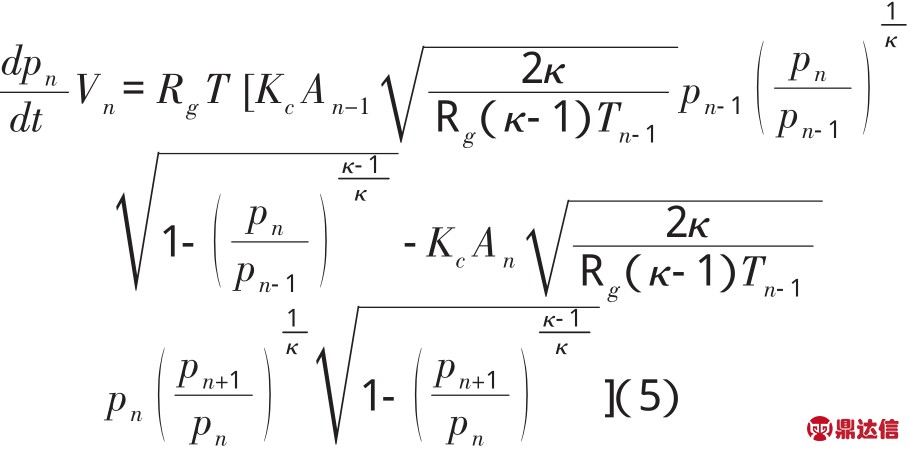
整理后得到

式子(6)就是缸内压力变化的理论计算模型,是关于环间压力Pn与Pn-1的一阶非线性微分方程可简化。具有n个活塞环的活塞环组,有(n-1)环间空间,每个空间使用式(6)得到一个微分方程,运用龙格-库塔数值解法就可以得到气体压力的分布。进行迭代计算时,为控制迭代运算时间和保证结果精度,收敛误差取10-3,即前后迭代压力值误差小于等于10-3时,迭代计算结束。
2.2 模拟结果
理论计算分析了与静态试验相同状况的密封过程,即总体积内充以某一压力值的气体,然后缸内的气体通过活塞环自然泄漏到大气中,而不是发动机整个循环时缸内气体压力的变化过程。计算模型参数:以S195发动机为模型,稳压罐体积,0.072m3,活塞环径向厚度为5.08mm,每个普通活塞环高度为2.38mm,复合式活塞环总高为2.38mm,活塞环开口间隙为16mm,闭口间隙为0.9mm,环槽高度为2.4 mm,第1环槽至活塞上端面高度为14.7mm,第1环岸高度为5mm,第2环岸高度为4mm,环岸宽度为6.3mm,充气容积为稳压罐体积,活塞环处于上止点时燃烧室体积与顶环上端面至活塞顶部缸套与活塞间隙容积和,环腔体积等可据上述参数计算,缸内初始压力为0.5MPa,曲轴箱压力为大气压力,温度取室温25℃。以MATLAB编写程序,从图4结果中可以看出,缸内气体压力不断下降直到大气压力,传统活塞环的压力维持时间1 063.31 s复合式活塞环的密封压力维持时间1 737.62 s,是传统活塞环的1.63倍。
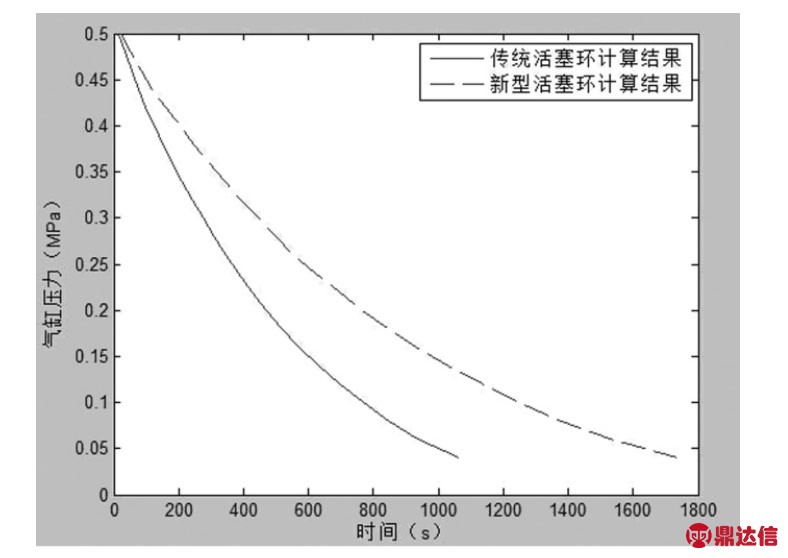
图4 两种活塞环缸内压力变化模拟图
3 复合式活塞环密封性试验研究
3.1 试验方案与方法
发动机工作受许多因素影响,即使以某一工况稳定运转时,这一循环和下一循环的燃烧过程也不断变化,并表现在压力曲线上。为方便研究,减少各不确定因素对试验的影响,设计发动机静态试验方案,并搭建了静态试验台模拟发动机的工作情况。
试验采用S195型柴油机(单缸、4冲程、缸径为95mm)及其配件,其试验系统组成如图5所示。进行发动机传统活塞环和复合式活塞环的密封性能试验,主要组成部分:
一是,试验发动机部件(发动机的机体组部件、气门组部件、活塞连杆组部件、复合式活塞环等)主要作用是通过更换活塞环,进行发动机传统活塞环和复合式活塞环的密封性能试验;
二是,气压系统(气泵,稳压气瓶、压力表、减压器、高压气管等)主要作用是给试验发动机部件的气缸中提供一定的气压;
三是,数据采集系统(压力传感器、数据采集模块等)主要作用是对试验数据进行采集和显示。
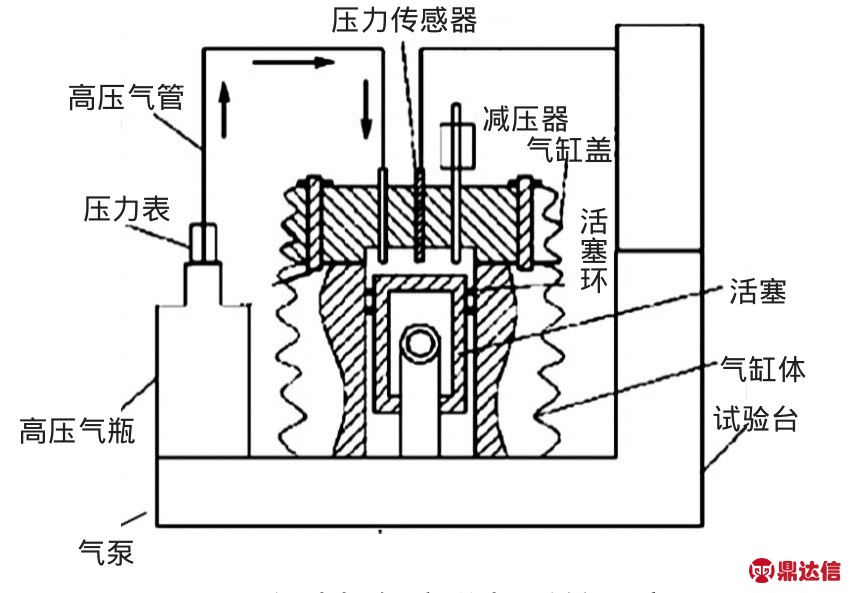
图5 发动机气密分析系统示意
试验方法为:
(1)试验发动机部件装上传统的三个活塞环,开口保持相互错开120°;
(2)打开高压气瓶,当气缸体内压力保持在一定压力时,关闭高压气瓶;
(3)通过数据采集系统,对压力变化数据进行采集和显示,直到气缸体内压力减小到初始压力时停止测量;
(4)根据测量的压力变化数据及其时间做出对应的压力-时间曲线;
(5)更换一组复合式活塞环,开口保持相互错开120°,重复 2、3、4项。
3.2 试验结果分析
在搭建的发动机气密分析系统试验台上,进行传统活塞环和复合式活塞环的密封性能试验,对缸内压力变化数据进行了采集,由图6的试验结果可以看出,传统活塞环(三气环)气缸内压力逐渐下降到967.39 s后不再发生变化,新型复合式活塞环(一组三个气环),气缸内压力逐渐下降到1641.58 s后不再发生变换,因此,发动机复合式活塞环在密封性能方面明显优于传统活塞环。为模拟发动机工作的实际工况,我们人为将活塞固定在气缸内的多个不同位置,这样可使得实验数据更真实,误差更小。图6为最终由多组试验数据拟合的曲线。
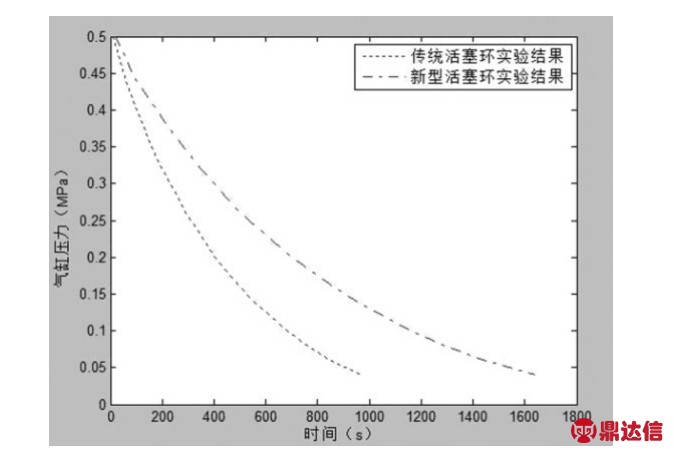
图6 两种活塞环缸内压力变化试验图
3.3 计算与试验结果对比
从对比结果可以看出,计算和试验结果存在一定误差,这主要是因为理论计算过程中只考虑闭口间隙处泄漏的气体,没有考虑侧泄与端泄,因此仿真与试验结果存在一定的误差。
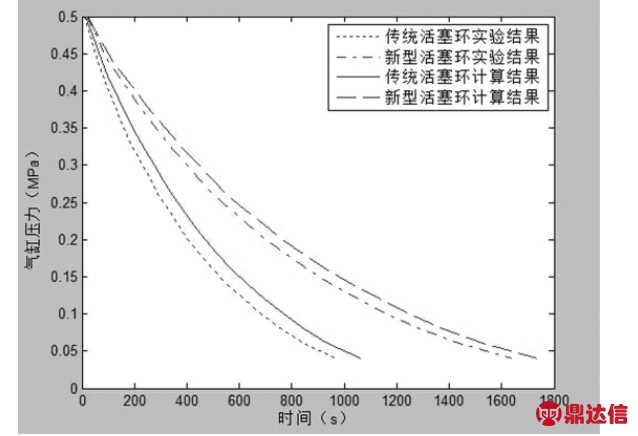
图7 试验与计算结果对比图
4 复合式活塞环所受摩擦力的分析
4.1 润滑分析
新型复合式活塞环的上浮动环,中间稳定环,下浮动环构成了一个润滑油腔见图8。这个润滑油腔可以储存少量的机油。新型活塞环组工作时,活塞环组由上止点向下止点运行时,上浮动环与气缸壁间的润滑油一部分被刮入润滑油腔内,新型活塞环组由下止点向上止点运行时,润滑油腔内的润滑油可以均匀的分布在气缸壁上,这样在气缸壁上就形成一层薄的油膜,保证了新型活塞环组的良好润滑[2]。

图8 新型活塞环储油腔示意图
对于影响新型复合式单气环与气缸套润滑状态的因素有以下几个:
(1)气缸内压力。
(2)活塞环运动的速度。
(3)新型复合式单气环和气缸套的温度。
(4)表面粗糙度。
(5)润滑油的粘度。
(6)对于润滑油的密度,考虑到受压力和温度变化不大,因此我们把润滑油密度作为一个常量来考虑。
作用于活塞环环表面的剪切力有两个部分,一个是油膜动压剪切应力,另一个是凸峰接触产生的摩擦力[4]。则作用活塞环表面的剪切力为

式中:
τ1为油膜产生的流体动压剪切应力;
τ2油膜产生的流体动压剪切应力;
τA为凸峰接触产生的摩擦力。
凸峰产生的摩擦力公式为

式中:
τ0是比例系数;
α0是剪切应力常数,它取决于材料。
凸峰接触的平均压力公式为:

式中:
WA为凸峰负荷;
Ac是单位周长上凸峰的实际接触面积。
凸峰负荷公式为:

式中:
ρ是粗糙表面的峰元密度;
β是峰元曲率半径;
L觶是复合弹性模量。
复合弹性模量计算公式为:
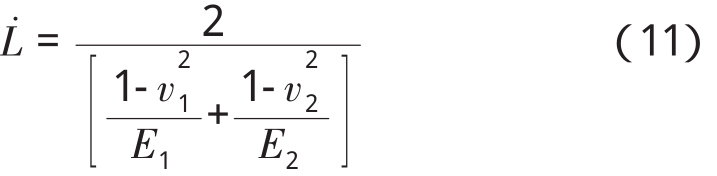
式中:
E1是气缸套的弹性模量;
E2是活塞环的弹性模量;
v1,v2是气缸套活塞环材料的泊松比。
其中油膜产生的流体动压剪切应力为:
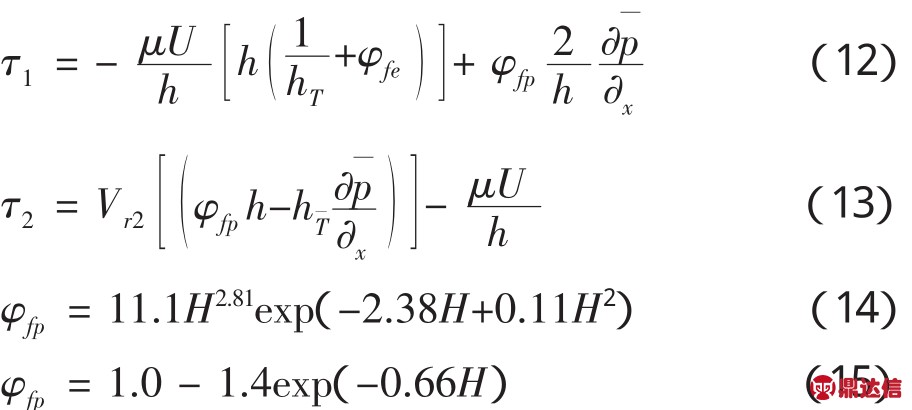
式中:
φfp是剪切力因子;
φfp是剪切力因子。

式中:
δr是联合粗糙度幅值;
f(δr)是概率密度。
f(δr)可由Christensen提出的公式计算[5]
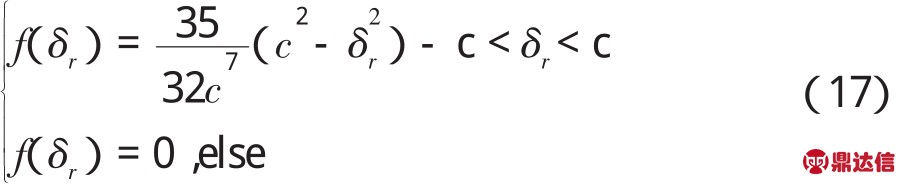
其中 c=3δ,δ是 δr的方差。
则活塞环与气缸壁的摩擦力公式为:

D是活塞环外径。
4.2 计算结果
边界摩擦系数0.1,复合式活塞环总高为2.38 mm,环表面凸起高度e=10 um,缸套表面粗糙度均方根值等于 0.6 um,其中,ηβσ =0.03-0.05,σ/β=1×10-4-1×10-2,活塞环表面粗糙度均方根值为0.1 um,活塞环缸套材料松泊比为0.4。
根据计算我们得出活塞环摩擦力曲线图,如图9、10所示。
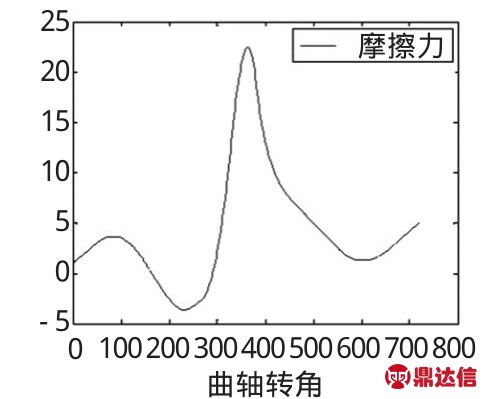
图9 新型活塞环摩擦力曲线图(1 000 r/m in)
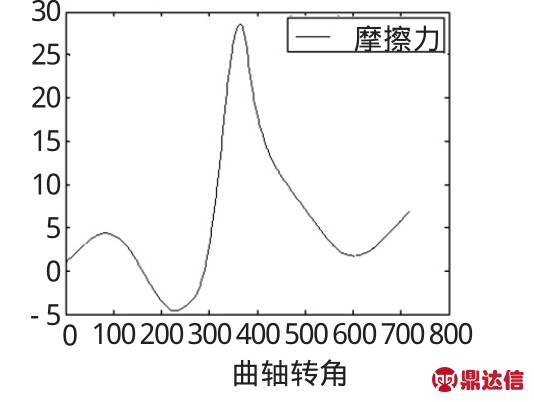
图10 新型活塞环摩擦力曲线(2 000 r/m in)
5 结束语
(1)提出了一种新型复合式活塞环,对其密封原理进行了分析。由于中间稳定气环堵住了高压气体直接从上下气环闭口间隙处的泄漏,可提高活塞环的密封性能。
(2)建立了新型复合式活塞环气密性分析的理论模型,数值模拟结果表明,在相同的工况下,新型复合式活塞环的气密性能比传统活塞环(三气环)提高约18%。同时,搭建了复合式活塞环气密性静态分析试验台架,试验结果表明,复合式活塞环的气密性能比传统活塞环提高约14%,验证了复合式活塞环的密封性能优越于传统活塞环。
(3)提出的复合式活塞环的摩擦力分析模型,研究结果表明,在转速由1 000 r/min到2 000 r/min,复合式活塞环所受摩擦力提高约23%,随着转速的提高,摩擦力越大,复合式活塞环降低摩擦功耗的潜力越大。
(4)提出的复合式活塞环可在保证气密性的前提下,其所受摩擦力再可接受范围内,为取代传统活塞环组,做出了有益尝试。