摘 要:密封性能是密封器件的一项关键指标,气密性检测是保证密封性能最为关键的手段之一。通过研究复杂腔体零件在差压式气密性检测中的特点、影响检测精度的因素等,构建检测气路的动态系统仿真模型,为优化现有差压式气密性检测系统提供理论支撑。首先依据差压气密性检测系统的工作原理,建立了相应的数学模型,然后在模型的基础上进行了Simulink仿真。通过仿真清楚地了解到检测过程中被检零件腔体内的压力和温度的变化情况以及检测参数的差异对差压大小的影响,用于指导系统的实际开发。
关键词:复杂腔体零件 气密性检测 差压法
0 引言
复杂腔体零件是指一类腔体形状复杂、结构多变、接口多而不规则的零件的总称。复杂腔体零件往往采用铸造、锻压、冲压,焊接、快速成型等制造方法成型,再经过数控加工中心,激光加工等技术进行机械加工[1],最后进行成品的质量检测,其中气密性检测通常是必检项目[2]。研究设计一套可用性强,检测精度高,效率高的气密性检测设备也是目前诸多行业发展所需的[3]。气密性检测的方法包括气泡法,涂抹法,化学气体示踪检漏法,压力变化法,流量法,超声波法等[4]。传统的气密性检测方法多采用气泡法和涂抹法,然而这两种方法均不能满足目前行业高精度、高效率的生产要求。
本文介绍的气密性检测系统中,采用先进的传感器技术和数据通讯技术,实现数据的实时采集与传输[5]。以此在较短的时间内创建标准的检测环境,采用闭环控制原理使系统检测过程自动控制和调节,再进行信号的高速实时采集、处理,按照生产节拍,实现自动化的数据统计,根据数据统计和曲线图,优化现有差压气密性检测系统,调节生产管理,实现利益最大化[6]。
1 复杂腔体零件差压式气密检测的原理
差压式气密性检测法(简称差压法)的检测原理为,首先建立一个待测工件和等容积的标准工件的比较系统,两者及其管路对称布置(图1),然后通过向两者内部同时充入相同压力的气体,待系统内气压稳定之后,利用差压传感器测量待测工件和标准工件之间是否存在压力差及压力差的大小,即可计算出待测工件的具体泄漏量[7]。其实质是通过差压传感器两端的压力差作为判定待测工件气密性的依据,而压力差是由待测工件泄漏所致。在设定的检测时间内,标准工件无泄漏,若待测工件也没有泄漏,则差压传感器处于平衡状态,如图1(a)所示;若待测工件发生泄漏,即使是很微小的泄漏,其腔内的气压就会发生变化,导致差压传感器偏离平衡状态输出差压信号,检测系统通过采集并识别该差压信号,然后依据差压计算模型换算出被测工件的实际泄漏量,如图1(b)所示。
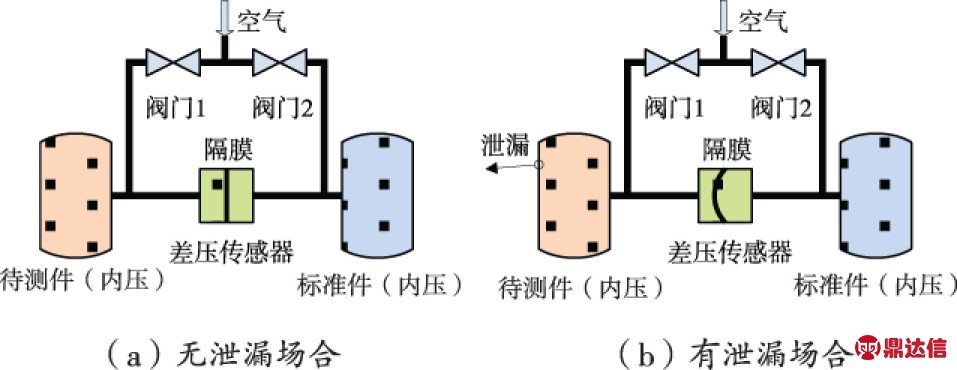
图1 差压法检测示意图
与其他检测方法相比较,差压力变化法的优点是检测灵敏度高,可以克服温度变化对测量结果的影响,使用范围广[8]。
2 差压检测过程建模
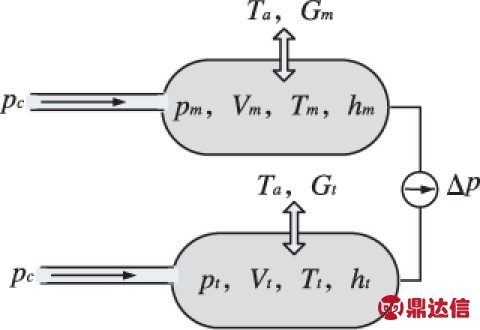
图2 差压检测模型
为了能在气密性检测实验装置开发前期对节拍和精度提供比较可靠的依据,采用建立气密性检测SIMUlink模型,然后对压差气密性检测过程进行仿真,为得出实际检测中的时间设定提供帮助。如图2所示,在气密性检测前,将压缩气体充入两腔体类零件内腔,一个为标准零件,而另一个为待检零件,经过一定时间,停止充气,保持完全密闭隔离。此时,若是待测腔体零件内腔有气体泄漏,那么必然引起待测腔体零件内腔的气压的降低,标准零件内腔与待测腔体零件内腔间形成压力差,随着时间的推移,差压会逐渐变大,由差压计算模型可算出待测腔体零件泄漏量。
采用气体状态方程,标准零件和待检零件内腔的气体状态参数(如绝对压力和温度)分别为:
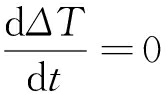
(1)
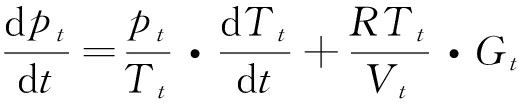
(2)

(3)

(4)
将压缩气体充入标准零件和待检零件内腔时,因为待检零件内腔泄漏气体的流量远小于充入零件内腔气体的流量,则此阶段泄漏气体的流量相对充入气体的流量可忽略不计,所以待检零件内腔与标准零件内腔气体之间的绝对压力以及温度的差值可以写为:
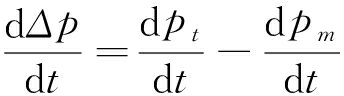
(5)
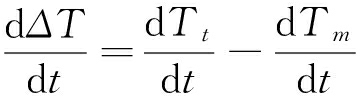
(6)
当待检零件内腔与标准零件内腔气体压力稳定并达到检测压力值,可停止充气,系统进入平衡阶段,则待检零件内腔与标准零件内腔气体各自绝对压力和温度相互作用产生变化,所以,此阶段两零件内腔间的气体绝对压力和温度的差值可以写为:
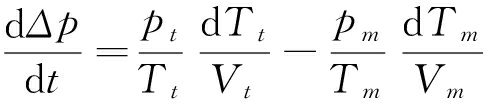
(7)
→
←[hmSh(Ta-Tm)]
(8)
从以上的方程可知,差压气密性检测法的数学模型为代数方程和常微分方程,通过求解可得待检零件内腔与标准零件内腔气体在差压检测过程的压力差和温度差的变化情况 [9]。
3 差压检测过程仿真与分析
设定仿真参数:外界温度为298.16 K(即25℃),大气压力为100 kPa,充气绝对压力为238 kPa,待检腔体零件和基准腔体零件的容积均为990 mL,热交换面积均为0.093 m2, 充、放气孔的有效截面积均为12.6 mm2,充、排气过程中的对流热传导系数均设置为30 W/(m2·K),待检腔体零件和基准腔体零件在充气过程中其腔体内的气体绝对压力和温度的计算公式:
充气过程中:
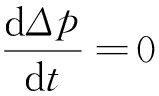
(9)
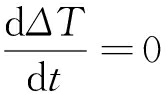
(10)
当被检腔体零件内腔的泄漏微型孔的有效截面积为0.1 mm2时,被检腔体零件和基准腔体零件内腔间的气体压力差和温度差的计算公式为:
→
←(298-Tt)
(11)
→
←+143.04-0.48Tt]
(12)
依据上述建立的数学模型,可建立如图3所示的差压气密性检测的SIMUlink仿真模型。通过设置图3的差压SIMUlink模型的不同检测基本参数进行仿真,将得到腔体零件差压气密性检测基本参数与检测气体状态变量之间的关系,通过分析检测气体状态变量仿真曲线图,为腔体零件实际差压检测过程提供指导意义。
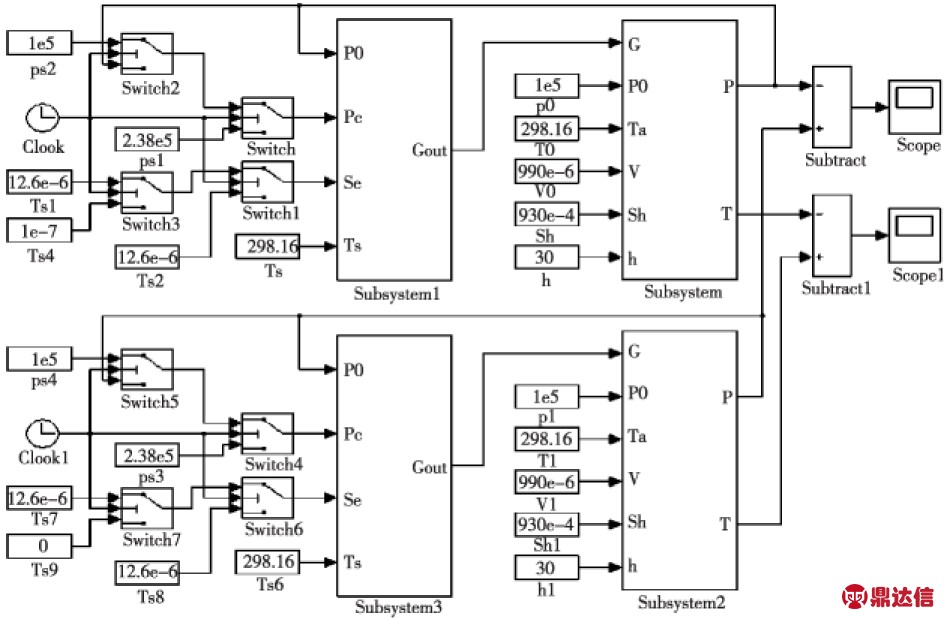
图3 差压检测仿真框图
(1)差压与有效泄漏面积之间的关系
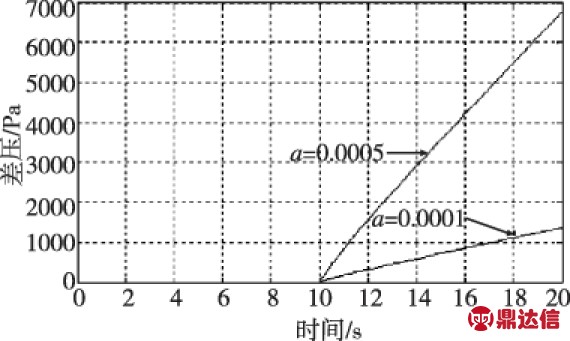
图4 不同泄漏面积的差压变化图
在差压模型设定的各参数中,改变被检腔体零件的有效泄漏面积Se,不改变其他参数,采用两次仿真将被检腔体零件的泄露微型孔的有效截面积分别设置为0.000 1 mm2和0.000 5 mm2。由图4可知:对于不同泄漏面积Se的两条曲线,有效泄漏面积Se=0.000 5 mm2的近似直线斜率大于有效泄漏面积Se=0.000 1 mm2的近似直线斜率,表明差压随有效泄漏面积Se增大而变化加快。
(2)差压与对流热传导系数之间的关系
在差压模型设定的各参数中,改变被检腔体零件的对流热传导系数h,不改变其他参数,分别将被检腔体零件和基准腔体零件的对流热传导系数h设置为30和31 W/(m2·K)进行仿真。由图5可知:在0 s~2.5 s阶段,两腔体零件内腔间的差压和温差均产生明显振荡;在2.5 s~10 s阶段,差压和温差逐渐趋于稳定;在充气结束瞬间(10 s时刻),差压和温差均迅速下降;之后,差压和温差再次趋于稳定。
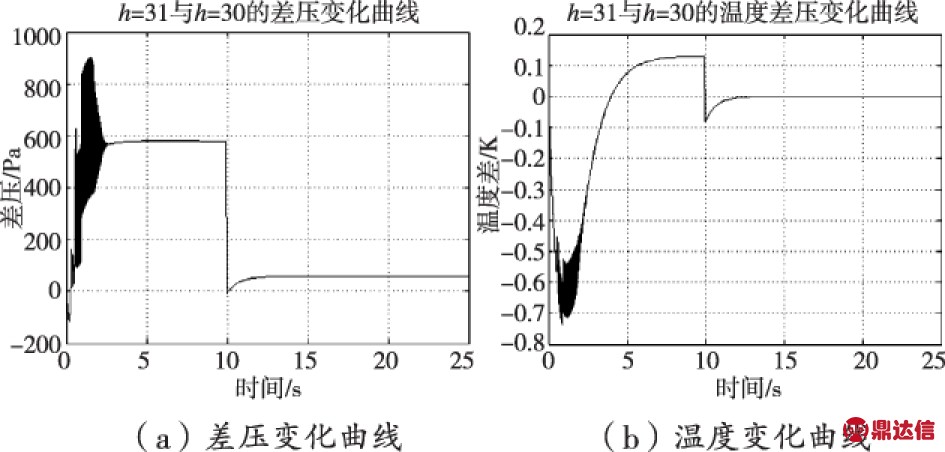
图5 不同热传导系数的差压变化和温差变化曲线
将上述差压仿真过程中两腔体零件的充气时间t改为8 s,得到图6(a)的差压变化仿真曲线,原充气时间t=10 s的差压变化仿真曲线如图6(b)所示,对比可得:当被检腔体零件和基准腔体零件的对流热传导系数h不同时,充气时间越短,两腔体零件内腔间的差压就越大。
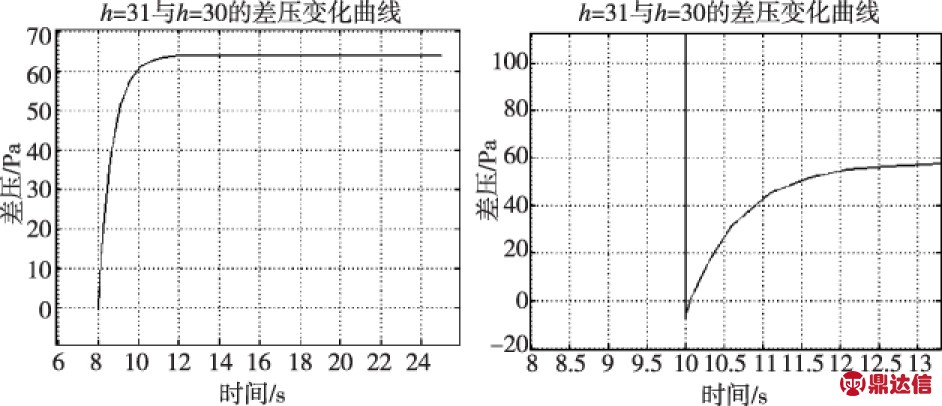
(a)t=8 s (b)t=10 s
图6 不同充气时间下的差压放大波形
(3)差压与腔体零件容积之间的关系
在差压模型设定的各参数中,改变腔体零件的容积V,不改变其他参数,分别将被检腔体零件和基准腔体零件的容积V设置为990 mL和1 000 mL进行仿真。由图7可知:在0 s~2.5 s阶段,两腔体零件内腔间的差压和温差均产生剧烈振荡;在2.5 s~10 s阶段,差压和温差逐渐趋于稳定;在充气结束瞬间(10 s时刻),差压和温差均迅速下降;之后,差压和温差再次趋于稳定,差压保持在200 Pa左右,而温差接近0。
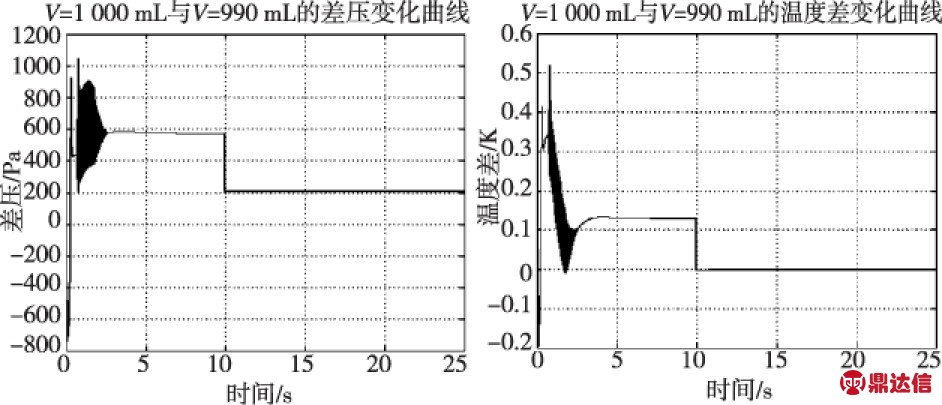
(a)差压变化曲线 (b)温度变化曲线
图7 不同容积的差压变化和温差变化曲线
对于上述差压仿真过程,当将两腔体零件的充气时间t改为8 s再次实施仿真,得到图8(a)的差压变化仿真曲线,原充气时间t=10 s的差压变化仿真曲线如图8(b)所示,对比可得:当被检腔体零件和基准腔体零件的容积V不同时,充气时间越短,两腔体零件内腔间的差压就越小。
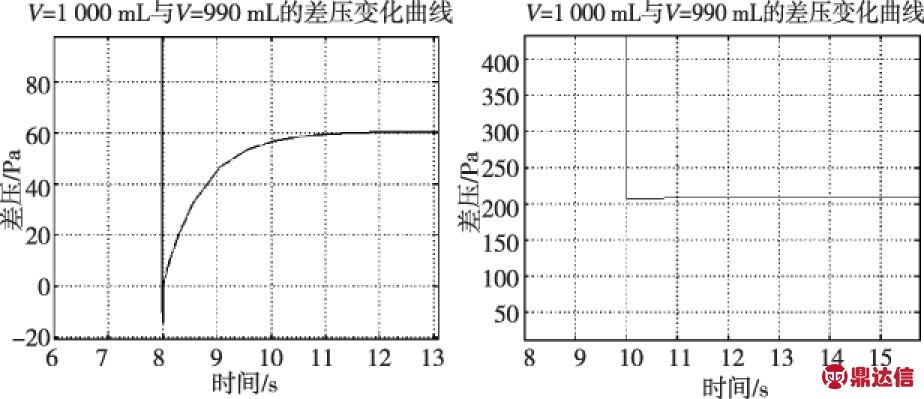
(a)t=8 s (b)t=10 s
图8 不同充气时间下的差压放大波形
(4)差压与热交换面积之间的关系
在差压模型设定的各参数中,改变腔体零件的热交换面积Sh,不改变其他参数,分别将被检腔体零件和基准腔体零件的热交换面积Sh设置为930 cm2和935 cm2进行仿真。由图9可知:在0~0.5 s阶段,两腔体零件内腔间的差压产生明显振荡,温差明显下降;在0.5 s~10 s阶段,差压和温差逐渐趋于稳定,差压迅速下降至0,而温差逐渐上升至0,最终差压和温差保持在零值附近。
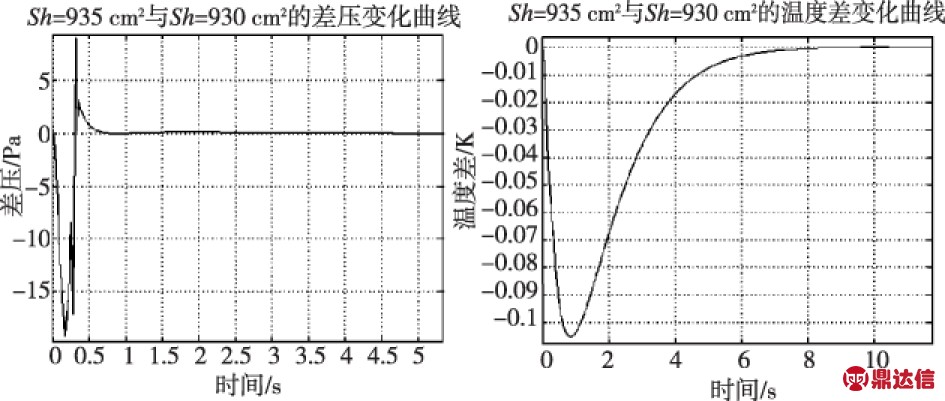
(a)差压变化曲线 (b)温度变化曲线
图9 不同热交换面积的差压变化和温差变化曲线
将上述差压仿真过程中两腔体零件的充气时间t改为8 s,再次进行仿真,得到图10(a)的差压变化仿真曲线,原充气时间t=10 s的差压变化仿真曲线如图10(b)所示,对比可得:当被检腔体零件和基准腔体零件的热交换面积Sh不同时,充气时间越短,两腔体零件内腔间的差压就越大。
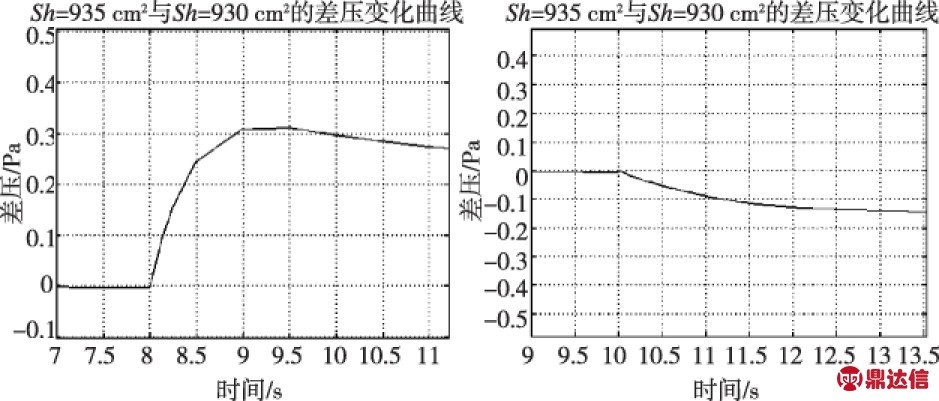
(a)t=8 s (b)t=10 s
图10 不同充气时间下的差压放大波形
4 总结
由以上仿真结果可知:差压随有效泄漏面积Se增大而变化加快;当被检腔体零件和基准腔体零件的对流热传导系数h不同时,充气时间越短,两腔体零件内腔间的差压就越大;当被检腔体零件和基准腔体零件的容积V不同时,充气时间越短,两腔体零件内腔间的差压就越小;当被检腔体零件和基准腔体零件的热交换面积Sh不同时,充气时间越短,两腔体零件内腔间的差压就越大。由此可见,在被检腔体零件与基准腔体零件内腔均没有泄漏的条件下,腔体零件的容积、外界温度、有效泄漏面积、对流热传导系数、热交换面积等参数均能使被检腔体零件与基准腔体零件内腔间的差压和温差发生变化。因此,在实际的差压气密性检测中,为了提高检测结果的准确度,就要在实际检测中采取措施使得被检回路和基准回路的测试参数尽可能的一致,并根据实际检测条件合理选取充气时间。
本文主要使用气体状态方程和热力学方程推导并建立腔体类零件差压气密性检测的数学模型,并据此创建Simulink仿真模型,然后对腔体零件充、排气过程进行仿真,并通过修改气密性检测参数的仿真结果对比分析,得出各仿真参数与腔体零件内腔的差压和温差之间的关系,为差压气密性检测系统设计的参数优化提供了指导。