摘 要: 针对快速锻造液压机组回程系统中蓄能器选用缺乏理论支持的问题,以10 MN快速锻造液压机组回程系统为例,运用AMESim软件分别对含气囊式蓄能器和含活塞式蓄能器的快速锻造液压机组回程系统进行仿真分析和试验研究。仿真结果表明:含活塞式蓄能器的快锻压机回程系统比含气囊式蓄能器的快锻压机回程系统的锻造频次高1.2倍;含气囊式蓄能器的快速锻造液压机组回程系统在回程缸回程时,其响应时间比含活塞式蓄能器回程系统的响应时间少20 ms,但在主机下压时,结束时间比含活塞式蓄能器回程系统响应时间滞后100 ms;含气囊式蓄能器的回程系统回程缸进口流量波动幅较大。在满足压机回程压力的前提下,通过不同初始充气压力、不同蓄能器容积对含活塞式蓄能器的快锻压机回程系统的试验,结果表明仿真与实测结果基本一致。
关键词: 气囊式蓄能器;活塞式蓄能器;快锻压机回程系统;动态特性;AMESim
引言
蓄能器作为快锻液压机组回程系统中的重要元件,对保证快锻液压机组回程系统正常运行、改善动态品质、保持工作稳定性、延长设备的工作寿命、辅助能源,降低噪声等起着重要的作用[1]。姚静等[2]在分析皮囊式蓄能器应力模型的基础上,提出了皮囊式蓄能器的数学模型,结合皮囊式蓄能器数学模型,对皮囊式蓄能器吸收压力冲击的功用进行理论分析,并进行了大量实验验证。王纪森等[3]对液压试验台中蓄能器的参数进行分析和仿真。从目前的研究结果可以看到,大多数学者正在研究气囊式蓄能器,但是对于具体的快速锻造液压系统回程系统而言,气囊式蓄能器和活塞式蓄能器分别对该系统的动静态响应的影响研究较少。本研究在前人研究基础上,搭建快速锻造液压机组回程系统,分别研究气囊式蓄能器和活塞式蓄能器对快速锻造液压机组回程系统的动静态响应,为工业实践中更好地选择和使用蓄能器提供理论依据。
本研究以10 MN快锻液压机组为例,采用AMESim软件对含气囊式蓄能器的快速锻造液压机组回程系统和含活塞式蓄能器回程系统进行仿真分析,进一步研究这两种蓄能器对快速锻造液压机组回程系统的影响。
1 含蓄能器的快速锻造液压机组回程系统
10 MN快锻液压机组有2个回程缸 (φ230/φ130),压机快锻时,锻造频次最大可达90 次/min,最大回程速度350 mm/s,5台排量为250 L/min的高压泵供给油液,环境温度变化范围为5~45 ℃,表1为10 MN 压机快锻时的参数。
表1 10 MN压机快锻时的参数
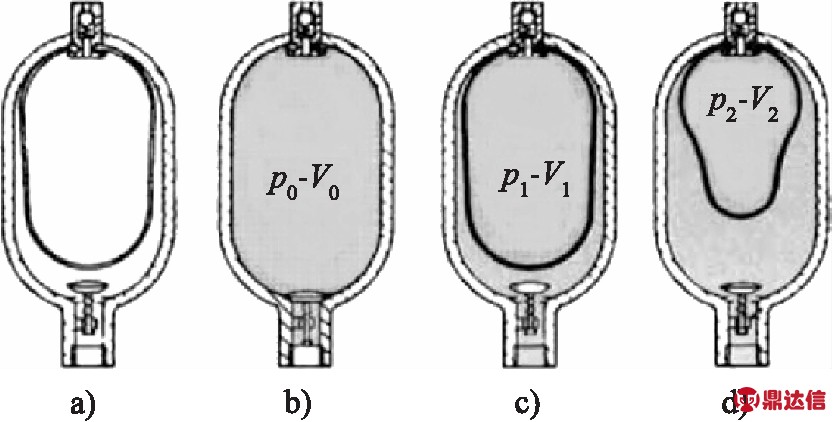
含蓄能器的快速锻造液压机组回程系统主要由回程缸、蓄能器装置和回程阀块组成。快锻时,高压油从蓄能器装置9通过二通插装阀8进入回程缸,使压机机架升起。加压时,回程缸内的油从原路返回蓄能器。在压机快锻过程中,当蓄能器内的油位(或压力)低于最小允许值时,由辅助泵装置2通过电磁阀4向蓄能器补油,当油位(或压力)超过最大允许值时,通过溢流阀3回到油箱,如图1所示。
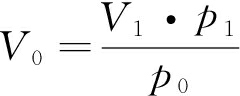
1.油箱 2.辅助泵装置 3、11.溢流阀 4.电磁阀 5.主泵装置 6.单向阀 7.电磁溢流插装阀 8.二通插装阀 9.蓄能器装置 10.压力传感器 12~14.比例流量控制阀
图1 含蓄能器的快速锻造液压机组回程系统
压机加压时,回程缸内的高压油回注到蓄能器中,这样既可以减小加压时的振动和高压溢流,降低系统发热量,又可以减少泵的供液量,节省能源,提高响应性。主要缺点是蓄能器中的压力持续存在,会部分抵消压机的锻造力。另外由于快锻压机移动工作台、横向移砧等的辅助设备在压机快锻时不会同时动作,为使压机配置更为合理,可用辅助泵为蓄能器补油。
2 蓄能器主要参数的确定
2.1 蓄能器压力确定
一般情况下,蓄能器的压力可按回程缸的回程力F回来计算。回程缸的回程力主要包括2部分:活动部分作用在回程缸上的力FG(包括机架45 t、主缸柱塞、回程缸活塞、油缸密封、机架导向处的摩擦力及回程时需要产生加速度等)和主缸泄油背压(0.9 MPa)作用到回程缸的压力Fx。
F回=FG+Fx
(1)
式中, FG —— 活动部分作用在回程缸上的压力,N
Fx —— 主缸泄油背压作用到回程缸的压力,N
根据工程实践,10 MN快锻液压机组的蓄能器的最大压力p1为17 MPa,最小压力p2为140 MPa,气体预充气压力p0为13.5 MPa。
2.2 气囊式蓄能器容积确定
蓄能器采用皮囊式,主要是惯性小,反应灵敏,避免产生振动[4],图2为气囊式蓄能器示意图。
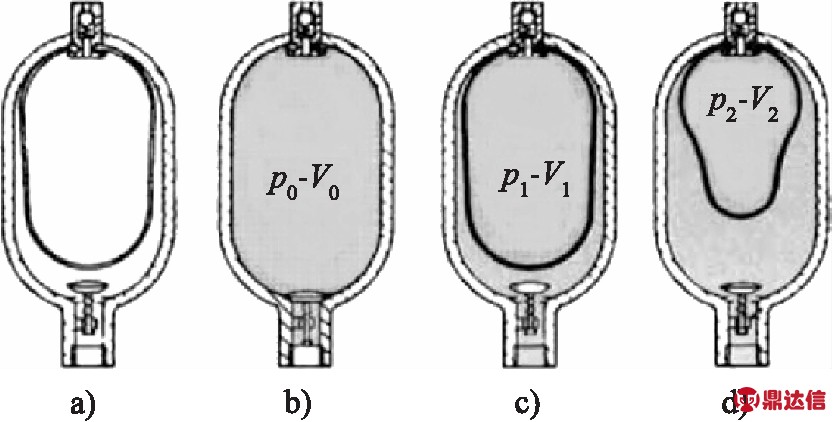
图2 气囊式蓄能器组
根据经验可知:
p0=0.9p1
(2)
式中, p1 —— 最小工作压力,MPa
p0 —— 预充压力,MPa
气囊式蓄能器内部气体的压缩与膨胀根据Boyle-Mariotte关于理想气体中状态变化的定律[6-8],即图3所示的气囊式蓄能器压力-容积关系图可知:

(3)
式中, p0 —— 预充压力,MPa
p1 —— 最小工作压力,MPa
p2 —— 最大工作压力,MPa
V0 —— 压力p0时预充氮气体积,L
V1 —— 最小工作压力下的气体体积,L
V2 —— 最大工作压力下的气体体积,L
在绝热状态下,Boyle-Mariotte定律可得如下公式:
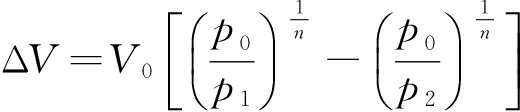
(4)
式中, ΔV —— 蓄能器储存的油液的体积,L
n —— 多变指数,n=1.4[8]
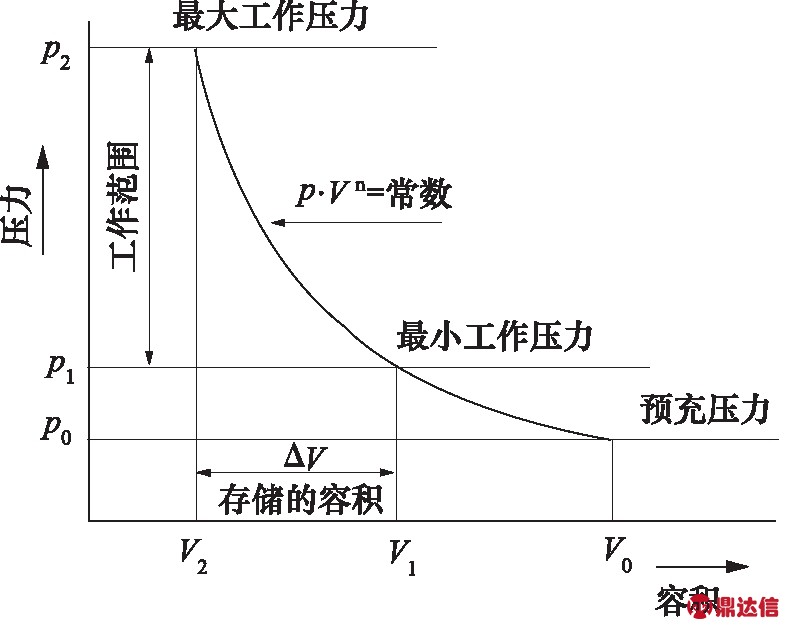
图3 气囊式蓄能器压力-容积关系图
由于实际工况下,蓄能器在运行周期中工作温度会有很大的变化,在计算容积时,温度影响应作为考虑因素,根据Iussac压力与体积之间的关系定律,温度变化则预充压力有相应变化,蓄能器体积也有相应变化。因此,为了保证正常工作,蓄能器容积应有:
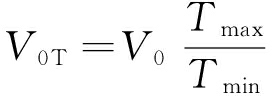
(5)
式中, V0T —— 活塞蓄能器的最小容积,L
Tmax —— 最大、最小环境温度,K
Tmin —— 最大、最小环境温度,K
根据式(5)得出:
如图12所示,当活塞式蓄能器初始压力为15 MPa,活塞式蓄能器组总容积为150 L时,回程缸进口流量实测数据与仿真曲线流量变化大致相同,但仿真曲线流量脉动较大,这主要是实际调试过程中PID控制参数较之仿真参数有所变化导致。当活塞式蓄能器组总容积为170 L时,回程缸进口流量实测数据与仿真曲线流量变化大致相同,但出现与活塞式蓄能器组总容积为150 L时相同的现象。
2.3 活塞式蓄能器容积确定
蓄能器采用活塞式,主要是为了减小蓄能器的容积,防止氮气进入管道,避免产生振动[7],图4为活塞式蓄能器组示意图。
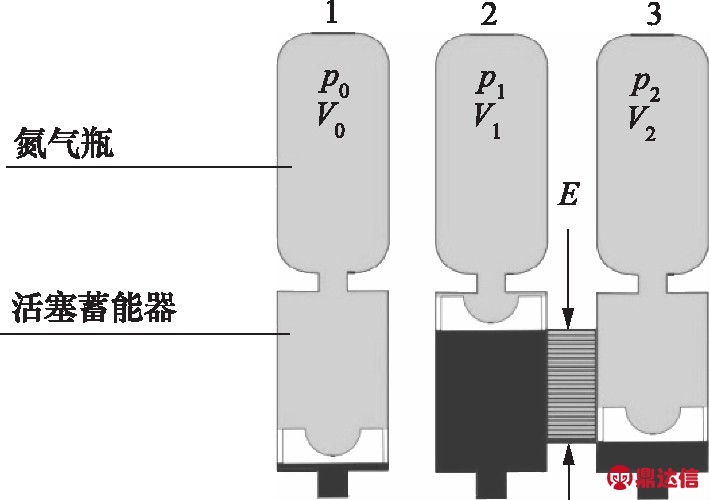
图4 活塞式蓄能器组
活塞式蓄能器需与气瓶配合使用,其中蓄能器由活塞分隔为2部分,一部分存有高压油,与液压系统直接相连,另一部分充装氮气,和气瓶连通[9]。压机在锻造过程中,蓄能器回程有耗能小、发热低、反应快[10]等优点,因此在常锻过程中,也推荐使用。虽然主要研究蓄能器回程在快锻中的应用,但因快锻回程高度较低,计算所得蓄能器容量较小,实际应用较少,为了贴合实际,便于对比,本研究按满足常锻要求进行蓄能器容量的计算。
活塞式蓄能器容积与锻造时的回程高度h1、回程速度v、回程缸数量N、回程缸(回程缸活塞直径d1、d2)有关。
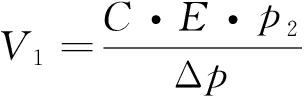
(6)
式中, V1 —— 最小工作压力下的气体体积,L
p2 —— 最大工作压力,MPa
C —— 修正因数
E —— 有效容积(V1- V2),L
Δp —— p2-p1,MPa
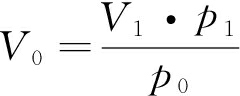
(7)
式中, V0 —— 最小工作压力下的气体体积,L
p1 —— 最大工作压力,MPa
p0 —— 预充气压力,MPa
V2=V1-E
(8)
式中, V2 —— 最大工作压力下的气体容量,L
V0T=(V0-V2)+ΔV
(9)
式中, V0T —— 活塞蓄能器的最小容积,L
ΔV —— 在考虑环境温度情况下,活塞式蓄能器容积增量,L

(10)
式中, Tmax —— 最大环境温度,K
Tmin —— 最小环境温度,K
根据式(10)得出,选取1个50 L的活塞式蓄能器和2个50 L氮气瓶组成的蓄能器组。
3 含蓄能器的回程系统仿真模型
3.1 含气囊式蓄能器的回程系统仿真模型
根据含气囊式蓄能器的快速锻造液压机组回程系统的实际原理,搭建的该系统的仿真模型,如图5所示。
3.2 含活塞式蓄能器的回程系统仿真模型
根据含活塞式蓄能器的快速锻造液压机组回程系统的实际原理,搭建的该系统的仿真模型,如图6所示。
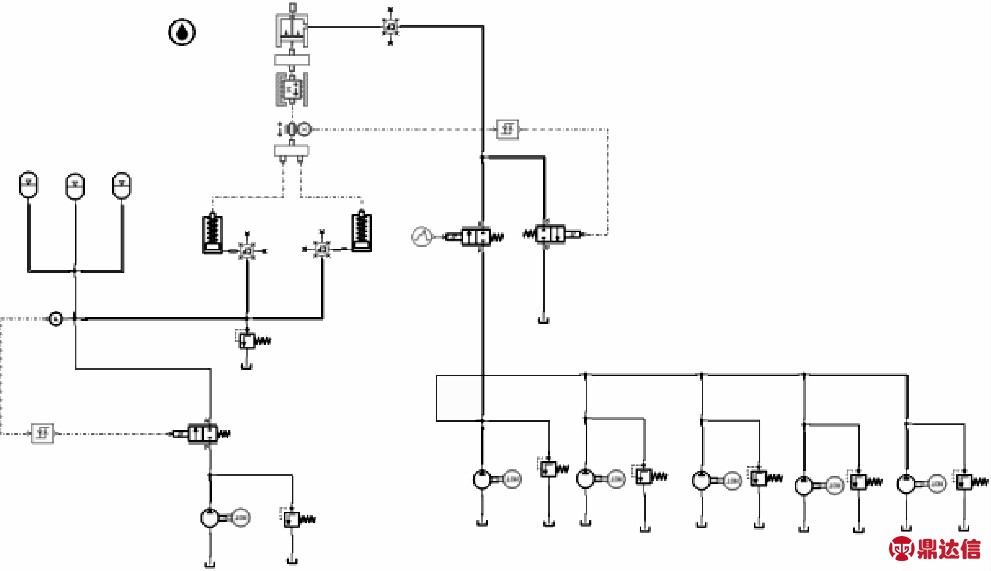
图5 含气囊式蓄能器的快速锻造液压机组回程系统的仿真模型
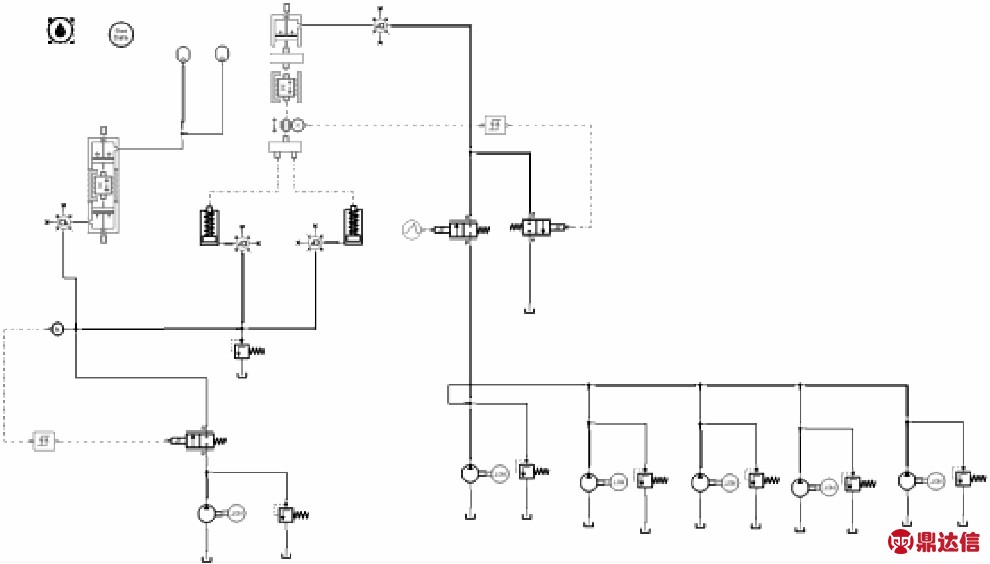
图6 含活塞式蓄能器的快速锻造液压机组回程系统的仿真模型
4 仿真与试验结果分析
4.1 锻造频次
气囊式蓄能器容积V0T为131 L,选取3个50 L的气囊式蓄能器。
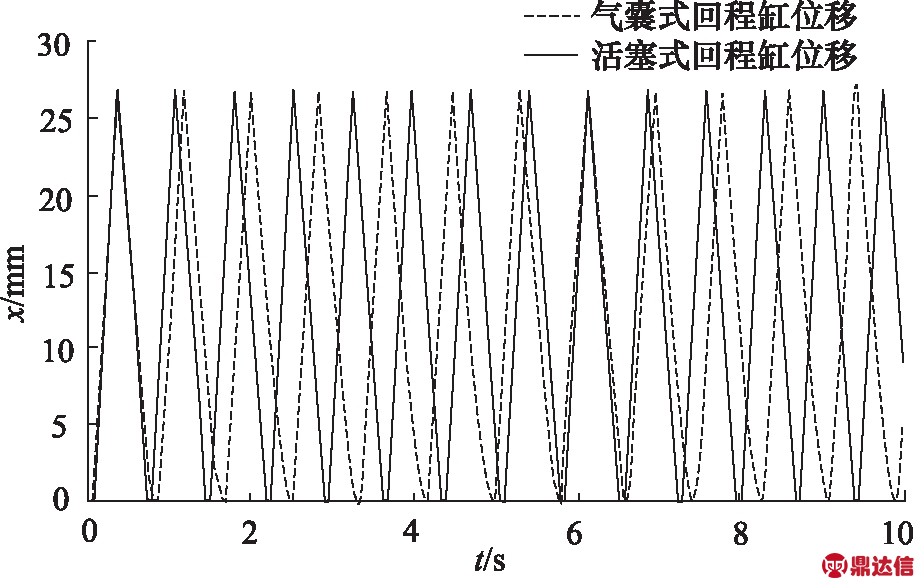
图7 两种蓄能器对锻造频次的影响
4.2 回程缸响应时间
由图8得到,在一个工作周期内,含活塞式蓄能器的快锻压机回程系统回程缸回程响应时间为0.08 s,含气囊式蓄能器的快锻压机回程系统回程缸回程响应时间为0.06 s。含气囊式蓄能器的快锻压机回程系统回程缸回程位移有一些波动,但含活塞式蓄能器的快锻压机回程系统回程缸回程位移基本没有出现这种现象。
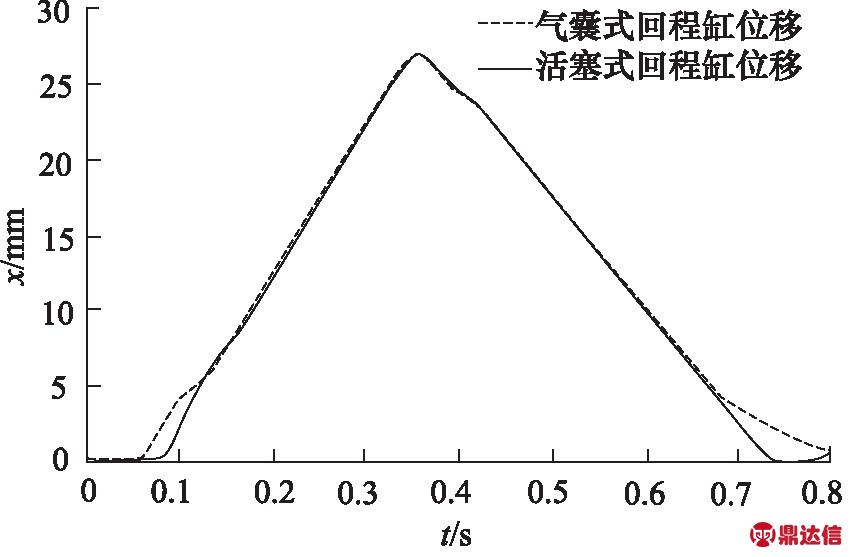
图8 两种蓄能器一个工作周期位移对比
4.3 回程缸进口流量
如图9所示,在一个工作周期内,含活塞式蓄能器的快锻压机回程系统回程缸进口流量变化范围为-301~551 L/min,含气囊式蓄能器的快锻压机回程系统回程缸进口流量变化范围为-412~623 L/min(负值表示油流的方向)。在选择相同蓄能器的容积下,含活塞式蓄能器的快锻压机回程系统回程缸流量波动大于含气囊式蓄能器的快锻压机回程系统回程缸流量波动。蓄能器中流量波动的情况,会影响蓄能器的寿命。
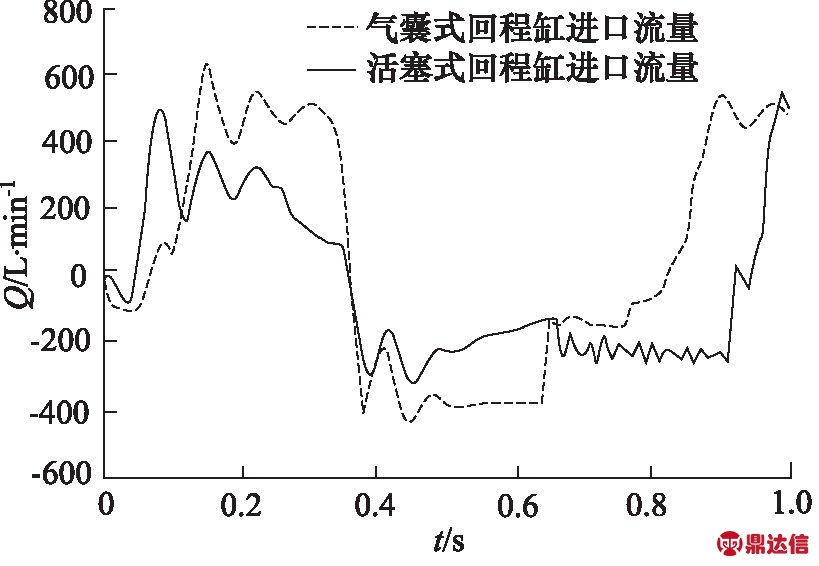
图9 回程缸进口流量对比
4.4 试验系统介绍
根据某集团的10 MN快锻液压机组。进行实验对比,如图10所示,该快锻液压机组包括机械系统、液压系统、电气控制系统。本次试验在10 MN快锻液压机组快速锻造时,在监控计算机中查看主缸的压力和回程缸的压力变化、压机位移变化量,并与相同参数下的快锻液压机组仿真系统模型的仿真数据进行比较。10 MN快锻液压机组实时控制调试采集系统的控制为德国西门子公司的S7-400系列的PLC,通过Profibus-DP即一个开放的工业现场通讯总线将各个分布式I/O 远程站进行连接。S7-400系列的PLC将10 MN快锻液压机组实时控制调试采集系统进行模块化控制。
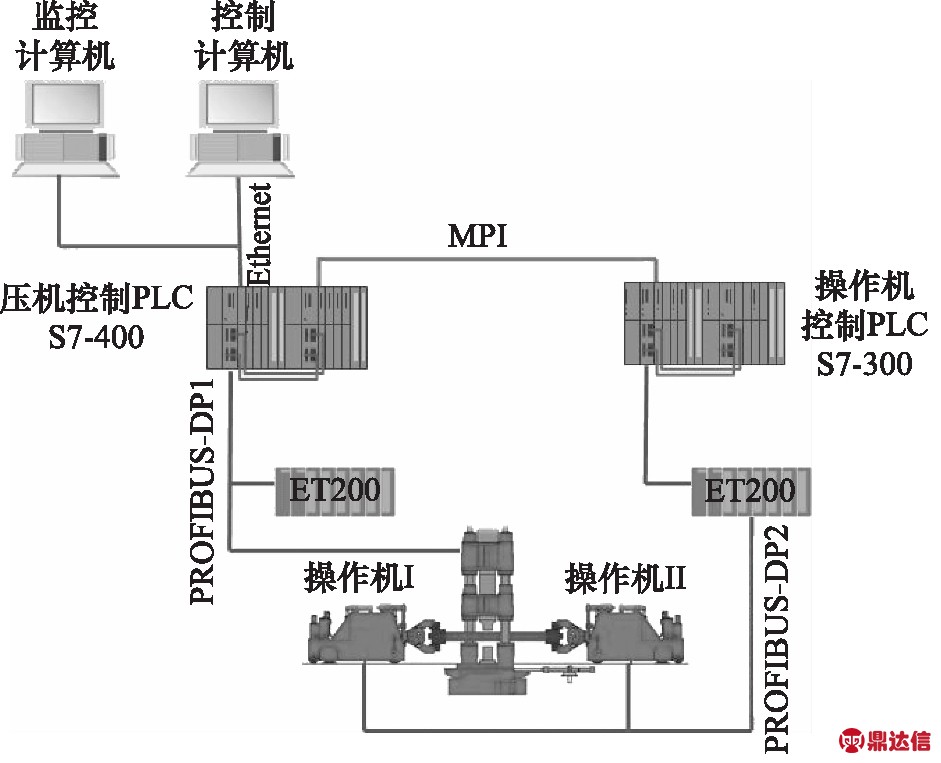
图10 10 MN快锻液压机组实时控制调试采集系统
4.5 不同初始充气压力对含活塞式蓄能器的快锻压机回程系统的影响
设置锻造回程高度为25 mm,活塞式蓄能器组总容积为150 L(蓄能器组由1个50 L的活塞式蓄能器和2个50 L氮气瓶组成),活塞式蓄能器初始充气压力分别为14 MPa,15 MPa时,仿真曲线与实验曲线如图11 所示。
从图11 可以看出,满足压机回程压力的前提下,活塞式蓄能器初始充气压力分别为14 MPa,15 MPa时,其仿真曲线与实测曲线误差精度都在2 mm范围左右,说明仿真与实测结果基本一致。
4.6 不同蓄能器容积对含活塞式蓄能器的快锻压机回程系统的影响
活塞式蓄能器初始压力为15 MPa,活塞式蓄能器组总容积分别为 150 L,170 L。
由图7得到,在仿真时间为10 s时,含活塞式蓄能器的快锻压机回程系统锻造频次为14次,含气囊式蓄能器的快锻压机回程系统锻造频次为12次,含活塞式蓄能器的快锻压机回程系统锻造频次是含气囊式蓄能器的快锻压机回程系统锻造频次的1.17倍。
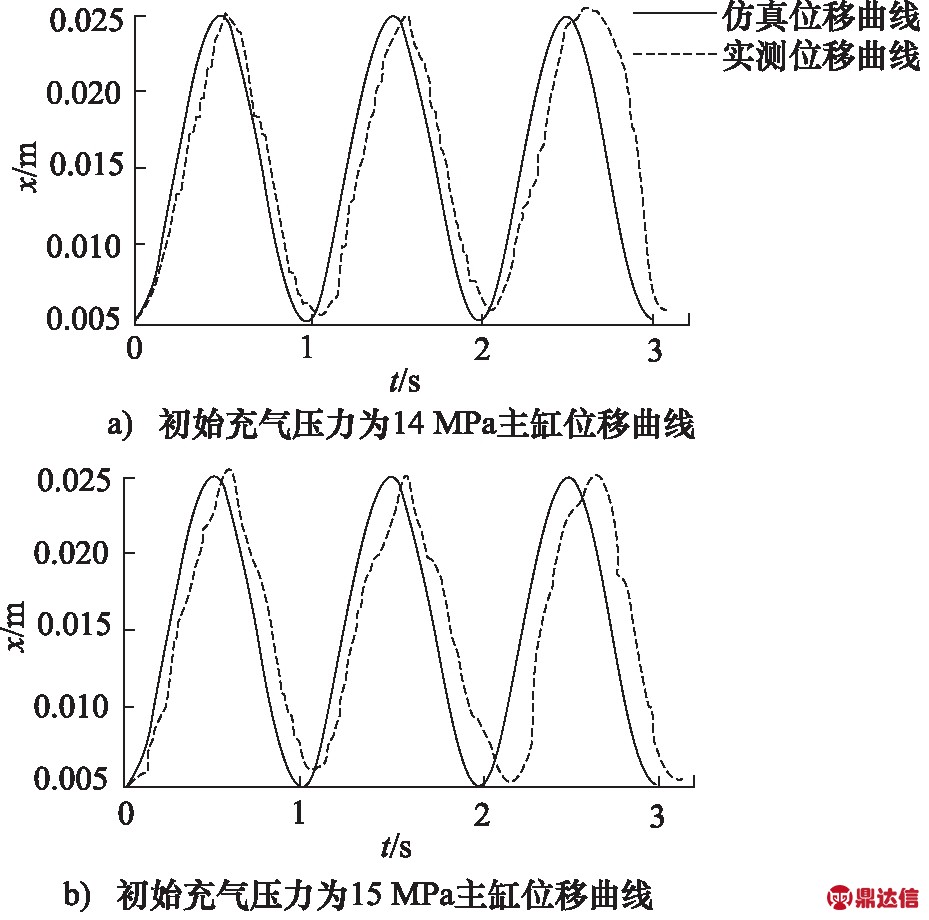
图11 不同初始充气压力对回程系统的影响

图12 不同蓄能器组总容积对回程系统的影响
因此,在不考虑实际调试过程中PID控制参数变化情况下,说明仿真与实测结果基本一致。
5 结论
(1) 在快锻压机锻造频次方面,含活塞式蓄能器的快锻压机回程系统比含气囊式蓄能器的快锻压机回程系统要高1.17倍;
(2) 回程缸响应时间方面,含气囊式蓄能器的快速锻造液压机组回程系统在回程缸回程时,其响应时间比含活塞式蓄能器回程系统的响应时间少20 ms,但其在主机下压时,结束时间比含活塞式蓄能器回程系统响应时间滞后100 ms;
(3) 回程缸进口流量来说,在一个工作周期内,含活塞式蓄能器的快锻压机回程系统回程缸进口流量变化范围为-301~551 L/min,含气囊式蓄能器的快锻压机回程系统回程缸进口流量变化范围为-412~623 L/min(负值表示油流的方向)。在选择蓄能器的相同容积下,含气囊式蓄能器的快锻压机回程系统流量波动较大,大大地降低蓄能器的寿命;
(4) 在满足压机回程压力的前提下,活塞式蓄能器初始充气压力分别为14 MPa, 15 MPa时,活塞式蓄能器组仿真曲线与实测曲线误差精度都在2 mm范围左右;当活塞式蓄能器组总容积为150 L, 170 L时,回程缸进口流量实测数据与仿真曲线流量变化大致相同,但仿真曲线流量脉动较大,这主要是实际调试过程中PID控制参数较之仿真参数有所变化导致。