摘要:针对常规旋转轴端面弹簧蓄能器密封结构的设计缺陷,如弹性补偿元件首尾对接处焊接不牢固、弹性补偿元件补偿效果差及密封使用寿命短等缺陷,通过调整密封主体及弹性补偿元件的结构,采用有限元分析方法对其结构进行优化。油封台架试验结果表明,优化后的弹簧蓄能器密封的密封性能和寿命大幅度提高。
关键词:弹簧蓄能器密封;弹性补偿元件;补偿力;接触面
弹簧蓄能器密封具有优异的密封性能,广泛应用于各种油缸密封及旋转密封中弹簧蓄能器密封可分为动密封及静密封2种类型。作为静密封时,其密封圈与配合零件之间没有相对运动,如安装在用螺栓夹紧的法兰与腔体之间的弹簧蓄能器密封。而作为动密封时,其密封圈与配合零件之间存在相对运动,包括往复移动或回转(含摆动),如液压缸中的活塞密封及活塞杆密封属于往复移动密封,而带有回转轴承的回转轴与腔体之间的密封属于旋转密封。当密封圈被径向压缩时,称之为径向密封,当压缩方向与旋转轴回转方向平行时,则为端面密封。
悬链式单点系泊装置旋转接头密封系统中,旋转接头主体结构与原油系泊装置之间为旋转的端面密封结构形式。本文作者针对常规旋转轴端面弹簧蓄能器密封结构的设计缺陷,进行结构优化,从而达到比较理想的密封效果,提高了旋转轴端面弹簧蓄能器密封的使用寿命。
1 旋转轴端面弹簧蓄能器密封结构
图1所示为常规旋转轴端面弹簧蓄能器密封的结构。目前国内外的宣传资料(样本)及实际产品也主要以这种结构形式为主。其由密封主体1及弹簧2组成,密封主体的两端面与密封沟槽的对摩面接触,磨损后由弹簧提供永久的弹性补偿力,同时弹簧还可以补偿由于制造及安装误差引起的密封件偏心[1]。
密封主体一般选择PTFE填充材料,材料选择主要根据密封介质、使用工况及寿命要求[2]。弹簧一般选择各种不锈钢(如301、302、304、316)、哈氏合金及游丝合金等材料[3-4],弹簧材料的选择主要取决于密封介质。从密封件的剖面看,弹簧形状有圆形、椭圆形、V形及U型等;从弹簧成型材料提供的形式看,分为线材(弹簧丝)及带材(弹簧片)等,其中带状弹簧又分为单排列及双排列2种。
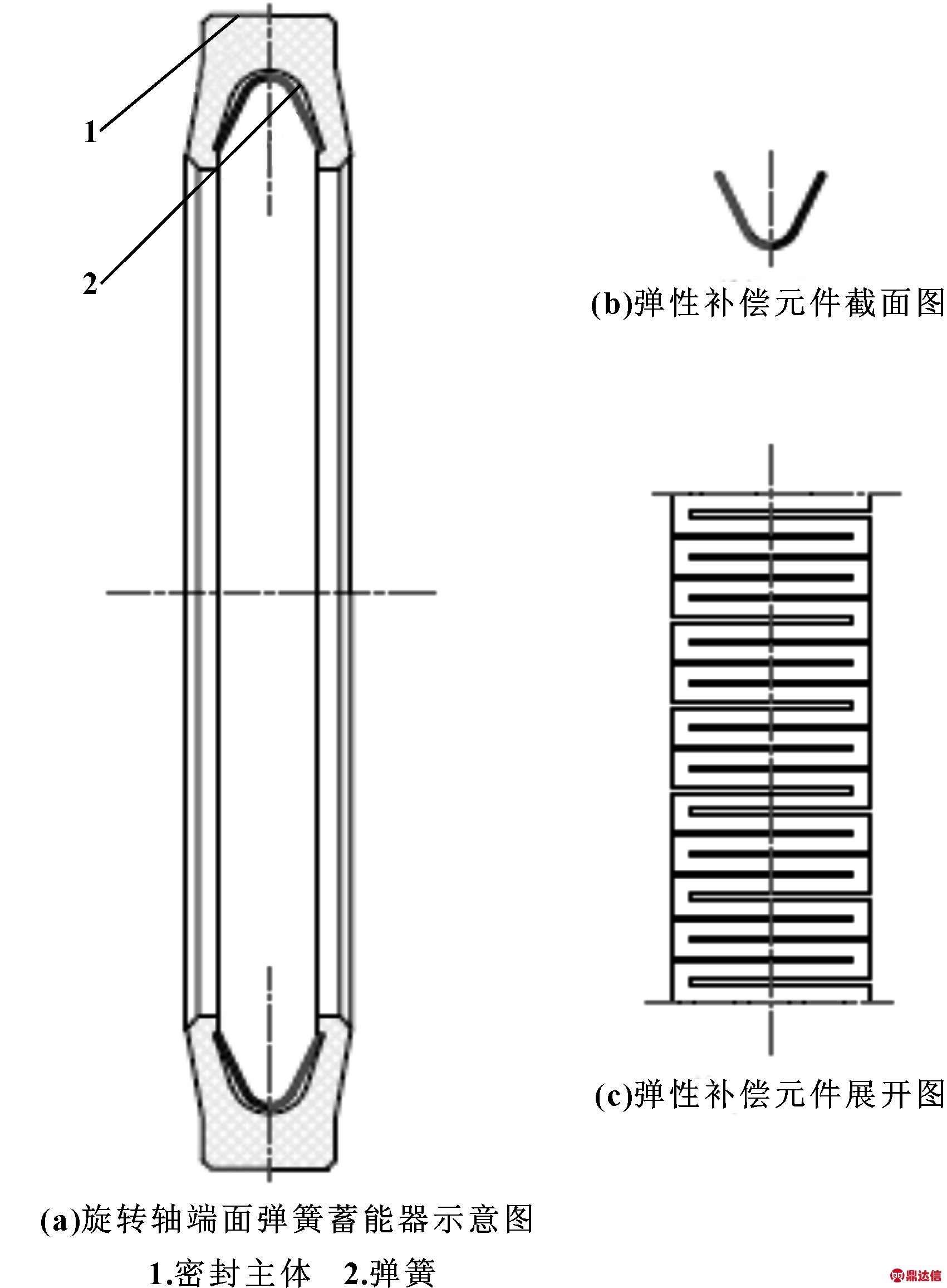
图1 常规旋转轴端面弹簧蓄能器密封结构示意图
Fig1 Structuresketchmapofconventionalspringaccumulator
sealofrotatingshaftendface
2 旋转轴端面弹簧蓄能器密封结构的设计缺陷
常规旋转轴端面弹簧蓄能器密封结构主要存在以下设计缺陷:
(1)弹性补偿元件首尾对接处焊接不牢固影响密封性能。
从图2可以看出,弹性补偿元件2为封闭的环状结构,实际制造过程中,弹性补偿元件2是由带状钢板经过落料及冲压成型,半成品为一个不封闭的V形条,一般需要经过适当的方式将V形条首尾连接在一起。常规的弹簧蓄能器密封结构对弹性补偿元件2的处理方式主要有2种:一是首尾对接处直接点焊成为连续的一整圈;二是不做任何处理,直接安装在密封主体1的沟槽中,属于一种断开的结构形式。由于弹性补偿元件2一般都比较薄,对接处直接点焊不易焊接牢固,而且容易引起焊接变形,使得圆周的补偿力不均匀,且焊接处的补偿力保持性差。如果对接处不做任何处理,缺口与其他位置的圆周补偿力不均匀,也不利于保证弹簧蓄能器产品的密封效果。
(2)弹性补偿元件冲孔形状影响补偿效果。
从图2(c)所示的弹性补偿元件展开图可以看出,弹性补偿元件2的展开形状为弯曲的蛇形,很难同时保证刚度与弹性同时达到比较理想的情况。开口宽度越大,弹性补偿元件的刚性越差,越容易变形,而且影响补偿力的均匀性;开口宽度越小,弹性补偿元件的刚性越好,但弹性变差,影响补偿效果。
(4)在密封主体两端面设置若干存储润滑脂的沟槽,以改善端面润滑效果。
常规旋转轴端面弹簧蓄能器密封置于密封的沟槽中,由于唇口倒角偏大,经过有限元模拟分析后发现,其接触长度较短,接触压力较大(见表1),对提高密封件的使用寿命不利。
表1 旋转轴端面弹簧蓄能器密封优化前后的性能参数
Table1 Performanceparametersofspringaccumulator
sealofrotatingshaftendfacebeforeand
afteroptimization
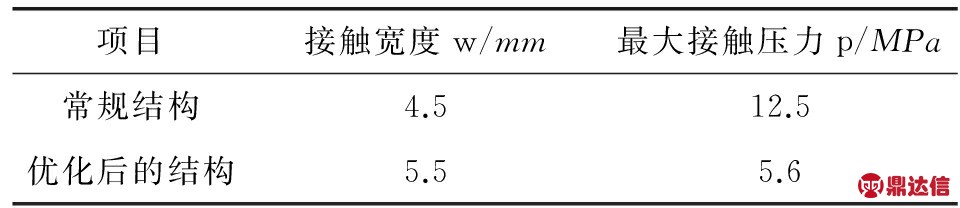
注:充分介质压力3MPa,沟槽尺寸1245mm×1203mm×15.3,产品规格:1 245mm×1 209mm×16.2。
(4)密封主体两端面结构未设置存储润滑脂的沟槽。
(3)密封主体两端孔口倒角偏大,影响密封件的使用寿命。
3 旋转轴端面弹簧蓄能器密封结构的优化
为克服常规旋转轴端面弹簧蓄能器密封结构设计存在的缺陷,对其结构进行了优化设计,优化设计后的旋转轴端面弹簧蓄能器密封结构如图2所示。
对旋转轴端面弹簧蓄能器密封主要进行了以下优化:
(1)用点焊的方式使弹性补偿元件两端连接牢固。
优化后的旋转轴端面弹簧蓄能器密封,用点焊的方式将弹性补偿元件7的首尾两端连接,且连接片8的焊接位置接近V形的两侧边缘,两侧对称布置,可以保证密封件主体1端面上的密封力均匀而且稳定。连接片8位于V形截面的内侧,便于安装,同时可避免弹性补偿元件2从密封件主体1中脱落。连接片8采用与弹性补偿元件2本体相同的材料,可以保证焊接强度,使焊接牢固。
(2)在弹性补偿元件上布置若干哑铃状的通孔,使其具有良好的刚性和弹性。
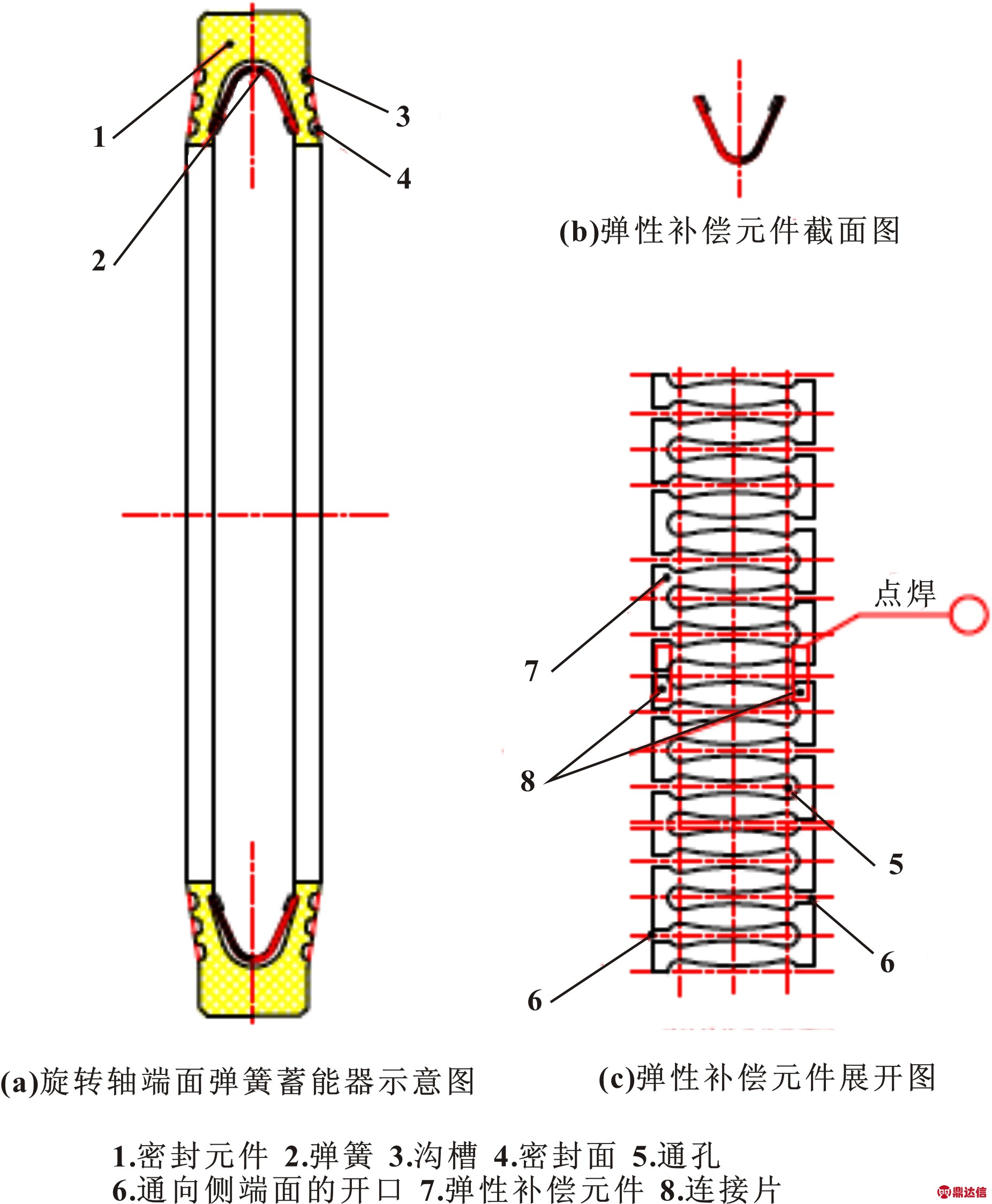
图2 优化后的旋转轴端面弹簧蓄能器密封结构示意图
Fig2 Structuresketchmapoftheoptimizedspringaccumulator
sealofrotatingshaftendface
优化后的旋转轴端面弹簧蓄能器密封,弹性补偿元件2上布置若干哑铃状的通孔5,哑铃状结构中间窄,可以保证弹性补偿元件2有好的刚性。哑铃状结构两端膨大,同时每一个通孔5有且仅有一个通向侧端面的开口6,两端交错布置,可以保证弹性补偿元件2的结构连续,而且弹性好。
(3)减少密封主体两端孔口倒角,从而减少接触力提高端面密封使用寿命。
优化后的旋转轴端面弹簧蓄能器密封,密封件主体2的两端面与内孔的交汇处不设置倒角或设置很小的倒角,通过有限元分析证明可以提高接触面的长度,在不影响密封效果的前提下减少接触力(见表1),从而减少磨损,提高旋转用端面密封的使用寿命[5]。
旋转轴端面弹簧蓄能器密封装置置于密封的沟槽中,经过一段时间的摩擦磨损,由于其结构上并未设置存储润滑脂的沟槽,随着初始安装时加入的润滑脂量逐渐减少,对摩面之间将会逐渐从原来的脂润滑变为干摩擦状态,摩擦因数的提高及摩擦热的产生将导致密封件的使用寿命缩短。
优化后的旋转轴端面弹簧蓄能器密封,其密封件主体2的两端面4设置若干个存储润滑脂的沟槽3,安装前在沟槽3内填满润滑脂,可以有效降低摩擦因数,保持密封件主体2端面(密封面)长期处于有脂润滑状态,有利于密封件使用寿命的提高。
4 结论
通过对旋转轴端面弹簧蓄能器密封的结构进行优化,从密封面的长度、密封面接触力的大小、密封面的减摩技术及持续稳定、均匀的密封补偿力提供等方面进行改进,较好地解决了目前旋转用端面密封产品密封性能较差,使用寿命短的问题。通过专用的油封台架试验验证,优化后的弹簧蓄能器密封寿命大幅度提高。