摘 要:针对压裂泵流量脉动较大带来的问题,在分析压裂泵脉动产生机理及其特点的基础上,设计可用于高压大流量场合中的气缸式蓄能器,建立气缸式蓄能器回路数学模型,得到脉动流量的幅频特性,仿真研究脉动抑制特性的影响因素,并对压裂泵安装气缸式蓄能器前后的脉动流量进行对比分析,结果表明:气缸式蓄能器可用于高压大流量场合中,其脉动抑制特性随气缸预充气压力、气缸直径、蓄能器连接管长度的增加而减弱,随气缸行程、蓄能器连接管直径的增加而增强;气缸式蓄能器能显著抑制压裂泵流量脉动,可将机械式三缸压裂泵的流量脉动由23.07%降至2.42%,将液压驱动式三缸压裂泵的流量脉动由33.33%降至3.22%;研究结果为高压蓄能器的设计和使用提供了一种新的思路和方法。
关键词:振动与波;蓄能器;气缸;压裂泵;脉动抑制
压裂泵被广泛应用于石油和天然气钻采、增产压裂作业中,但受限于自身工作原理,压裂泵不可避免地会产生流量和压力脉动,造成管线振动[1]、噪声、发热、元器件寿命缩短等不利影响。因此,需采取措施抑制压裂泵流量脉动。目前,普遍采用在管路中增加蓄能器[2-5]来抑制流量脉动。但压裂泵工作压力一般高于60 MPa,普通的蓄能器并不能适用于压裂泵高压大流量的场合中[6-8]。所以,在分析压裂泵脉动产生机理及其特点的基础上,本文提出并设计了气缸式蓄能器,对其脉动抑制动态特性进行分析,并对压裂泵安装该蓄能器前后流量脉动进行对比分析,取得了较好的抑制脉动效果。
1 压裂泵脉动产生机理及其特点
压裂泵是基于往复泵原理工作的,机械式压裂泵和液压驱动式压裂泵的液力端结构基本相同,区别仅在于动力端。
图1(a)所示为机械式单作用压裂泵工作原理。动力端通过曲柄连杆机构将旋转运动转化为直线往复运动,经十字头驱动液缸柱塞,通过柱塞腔的容积变化实现高压输出。优点是结构简单,流体脉动小;缺点是冲次高,振动大,易损件寿命低,高压下柱塞偏磨现象严重,难以实现高压输出。对曲柄连杆机构进行运动学分析可知,机械式压裂泵输出流量呈谐波变化,且奇数缸比偶数缸的流量脉动小,属于中低频脉动。理论上,一般常用的机械式三缸泵和五缸泵流量脉动分别为23.07%和7.05%[9]。
图1(b)所示为液压驱动式压裂泵工作原理。动力端由液压缸及其液压系统组成,液压缸直接驱动柱塞,通过活塞与柱塞的面积比进行增压降排,实现压裂液的高压输出。优点是冲次低、易损件寿命长,柱塞受力均匀,可实现高压输出;缺点是流体脉动大[10]。对液压缸进行运动学分析可知,液压驱动式压裂泵在液压缸匀速运动时,流量保持恒定不变,在液压缸换向时刻流量产生断流,从而造成流量脉动,其脉动大小与液压系统的设计有关,属于低频脉动。在同一时刻,一般只允许一只液压缸换向,所以,理论上,液压驱动式三缸泵、四缸泵、五缸泵的流量脉动最大分别为33.33%、25%、20%。

图1 压裂泵工作原理简图
1-排出管;2-排出阀;3-吸入阀;4-吸入管;5-压裂液腔;6-液缸柱塞(活塞);7-活塞杆;8-十字头;9-连杆;10-曲柄;11-液压缸活塞
2 气缸式蓄能器脉动抑制特性分析
2.1 结构和工作原理
根据压裂泵输出流量特点,设计气缸式蓄能器并将其接入蓄能器系统如图2所示。
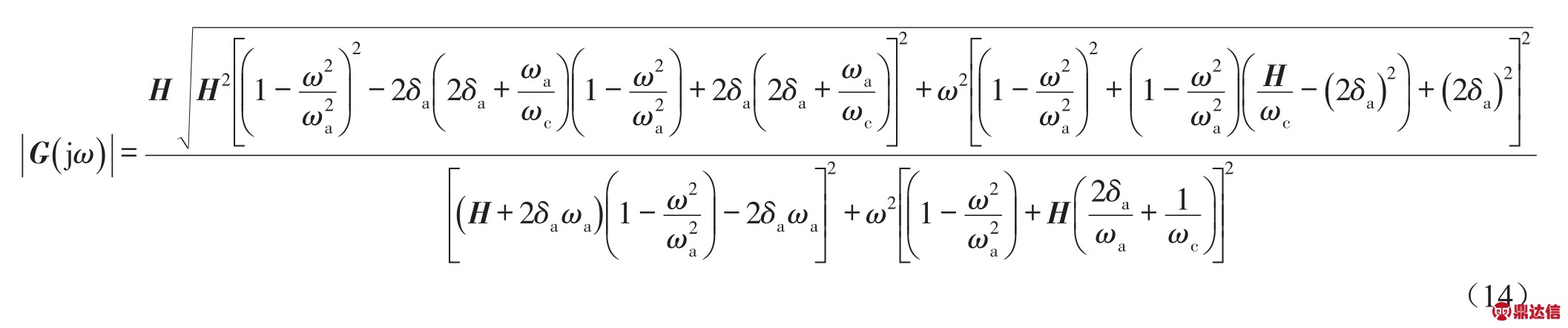
图2 气缸式蓄能器系统结构简图
1-进液口;2-压裂液腔;3-液缸柱塞(活塞);4-活塞杆;5-耐压缸体;6-气体呼吸口;7-气缸活塞;8-气腔;9-充气阀
系统采用节流阀加载。气缸有杆腔经由气体呼吸口6与大气相通。初始状态下,通过充气阀9预先对气腔8充压,气缸活塞及活塞杆全部伸出。当压裂液压力升高时,压裂泵输出的高压流体经进液口1进入压裂液腔2,通过液缸柱塞和气缸活塞面积比减压后压缩气腔8,使其体积减小压力不再升高;反之,当压裂液压力降低时,气腔8内的气体膨胀将压裂液腔2内的压裂液排出,减缓压裂液压力下降。
2.2 脉动抑制动态特性分析
2.2.1 气缸式蓄能器受力平衡方程
设液缸柱塞、气缸活塞面积分别为Ac、Ag,压力分别为pc,pg。以气缸活塞-柱塞运动体为研究对象,列出受力平衡方程,有

式中m、x、Bc、f分别为活塞、柱塞等运动体质量、位移、阻尼系数和摩擦系数,为符号函数。
2.2.2 蓄能器连接管路液柱受力平衡方程
设蓄能器连接管的长度为L1,直径为d1,横截面积为Aap,进入液缸和蓄能器连接管的流量为Q2;压裂泵输出压力为p,流量为Q1;压裂液密度为ρ,运动黏度为ν,体积弹性模量为E。以连接管内液柱为研究对象,列出受力平衡方程,有[11]

将式(2)整理可得
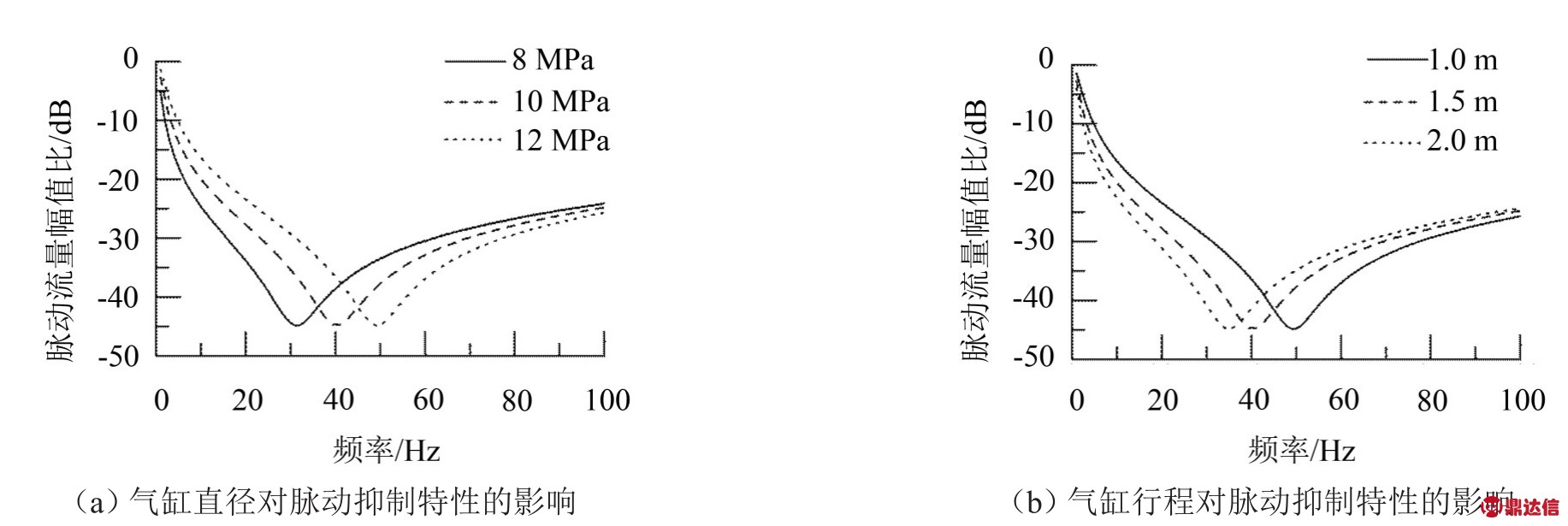
式中为蓄能器连接管路阻尼。
2.2.3 蓄能器流量平衡方程

2.2.4 系统流量平衡方程
设系统主管路长度为L2,直径为d2,横截面积为Amp;节流阀流量系数为Cd,开口面积为Ao,通过节流阀的流量为Q,有
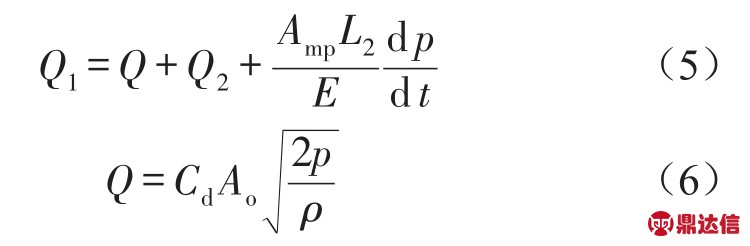
2.2.5 气腔气体状态方程
设 pg0、Vg0为气腔初始压力和体积,pg、Vg为气腔任意工作状态下的压力和体积,气缸行程为L,由气体状态方程有
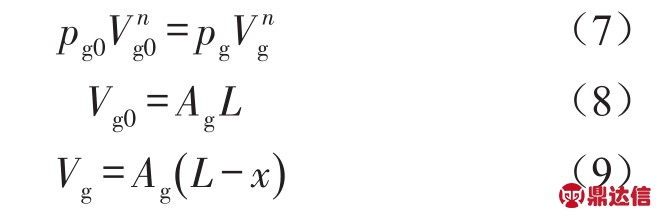
当使用气缸式蓄能器吸收流体脉动时,可看作绝热过程,则n=1.4,将式(7)在初始状态点做泰勒展开[12],略去高次项,并将式(8)、式(9)代入,有

将式(10)两边积分整理可得

式中为气缸式蓄能器压力弹簧刚度。
2.2.6 压裂泵流量脉动传递函数及幅频特性
设系统压力稳定点为p0,系统稳定后的流量为
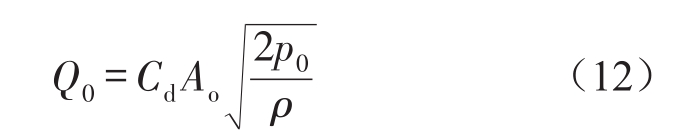
将式(1)-式(12)联立求解,经线性处理、拉氏变换后,可得系统输出流量与压裂泵输出流量的传递函数为
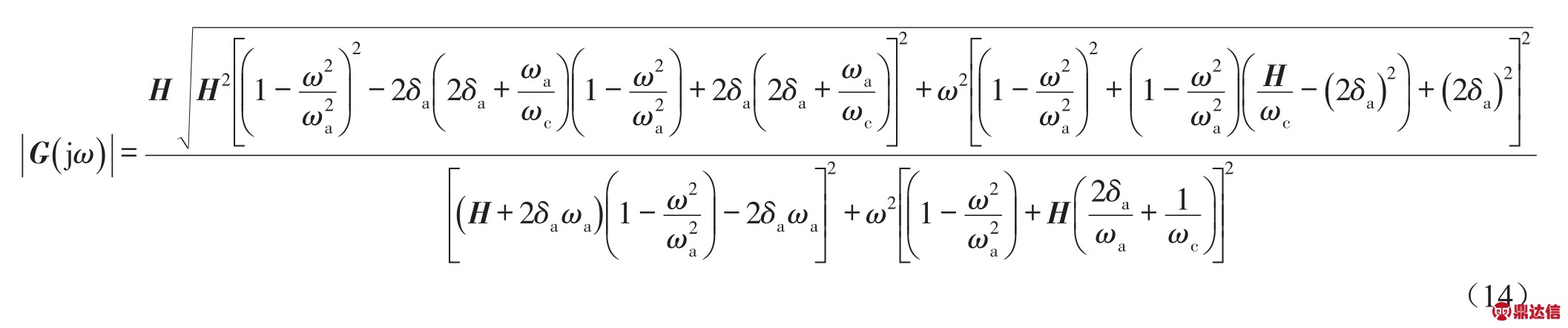
式中为增益;
ωa=为蓄能器固有频率;
δa=为蓄能器固有阻尼;
ωc=为截止频率。
式(13)就是压裂泵系统接入气缸式蓄能器后输出流量的完整数学模型。气缸式蓄能器吸收脉动的性能与气缸的缸径、行程、活塞及其运动件质量、预充压力、负载等特性有关。当管路等结构参数确定后,蓄能器固有频率ωa仅与蓄能器预充气压力 pg0有关。
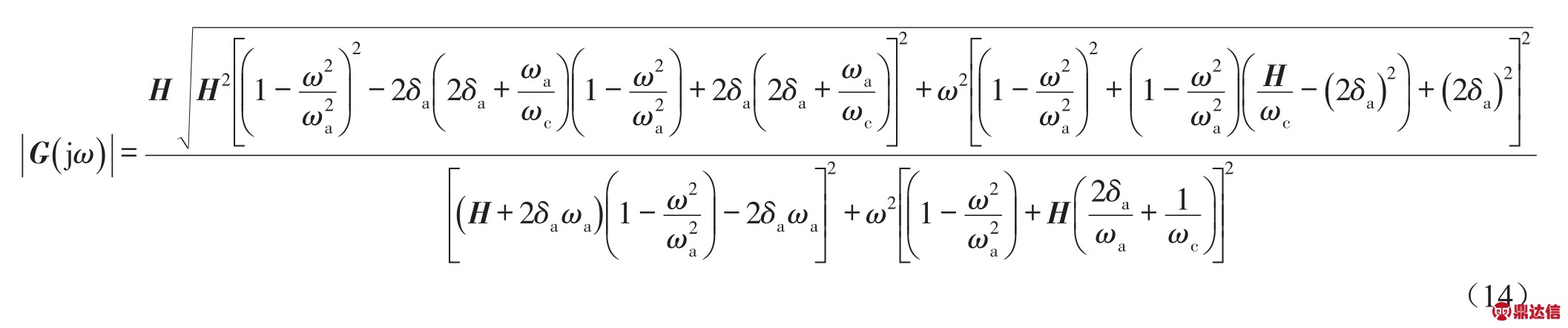
由式(13)可得系统幅频特性为
式(14)即为气缸式蓄能器安装前后系统流量脉动幅值比。由式(14)可知,当流量脉动频率ω<ωa时,气缸式蓄能器吸收脉动的效果随ω的增大而增强;当ω=ωa时,气缸式蓄能器吸收脉动效果最好,此时流量脉动幅值最小,为

当ω>ωa时,气缸式蓄能器吸收脉动的效果随ω的增大而逐渐减弱。
2.3 脉动抑制仿真研究
设置仿真参数如表1所示,根据式(13)、式(14)在Matlab中进行仿真研究得到以下结果。
(1)其他参数不变,改变气缸式蓄能器预充气
表1 仿真参数
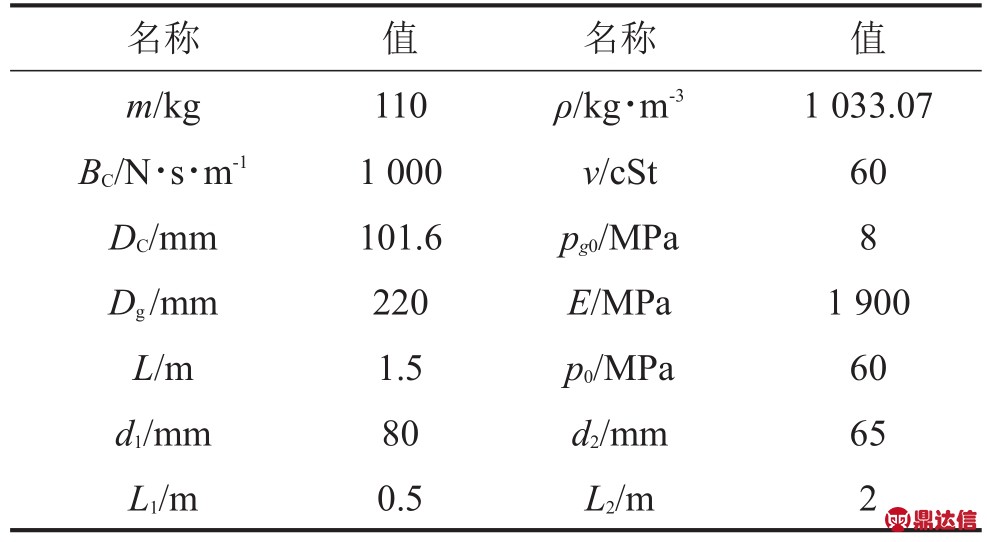
压力pg0,气缸式蓄能器脉动抑制特性如图3所示。由图3可知,对于低频脉动,当流量脉动频率一定时,气缸式蓄能器脉动抑制特性随气缸预充气压力的增大而减弱,但是预充气压力过小时,气缸压力弹簧刚度较弱。
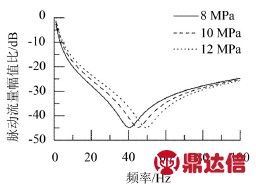
图3 预充气压力对脉动抑制特性的影响
(2)其他参数不变,分别改变气缸直径Dg、行程L,气缸式蓄能器脉动抑制特性如图4(a)、图4(b)所示。由图4可知,对于低频脉动,当流量脉动频率一定时,气缸式蓄能器脉动抑制特性随气缸直径的增大而减弱,随行程的增加而增强。但是过小的气缸直径使气体工作压力过高,过长的行程导致气缸式蓄能器体积较大。因此,需合理选择气缸直径与行程。
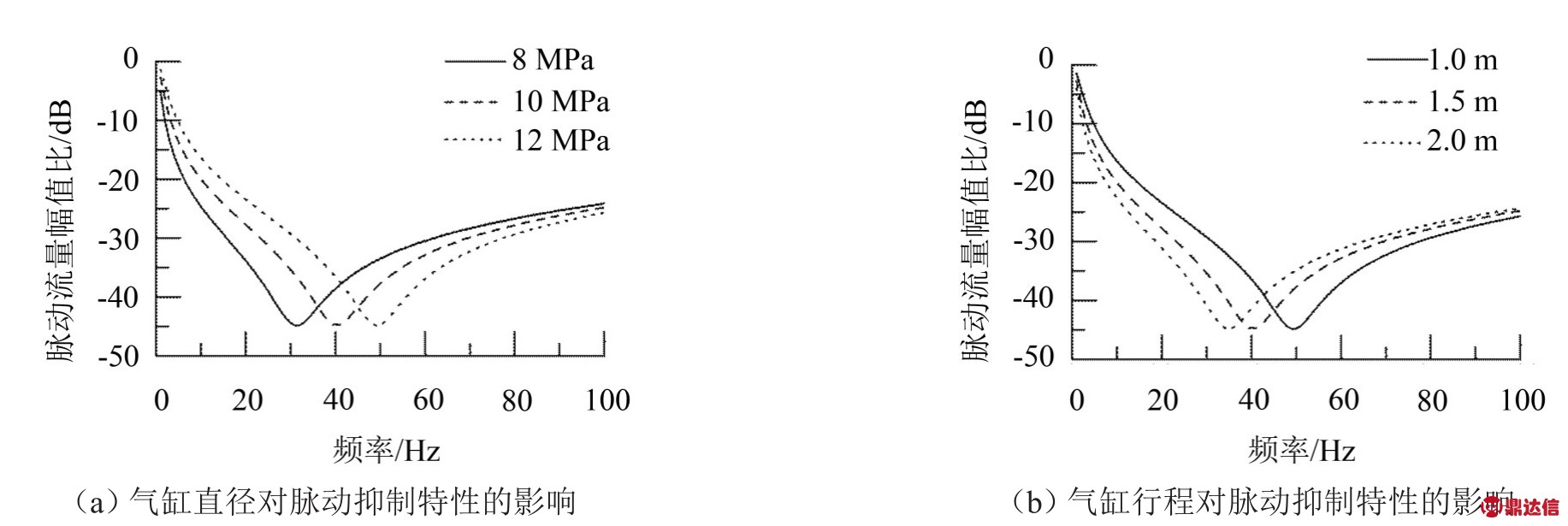
图4 气缸参数对脉动抑制特性的影响
(3)其他参数不变,分别改变气缸式蓄能器连接管直径d1、长度L1,气缸式蓄能器脉动抑制特性如图5(a)、图5(b)所示。
由图5可知,气缸式蓄能器脉动抑制特性随蓄能器连接管直径的增大而增强,随长度的增加而减弱。
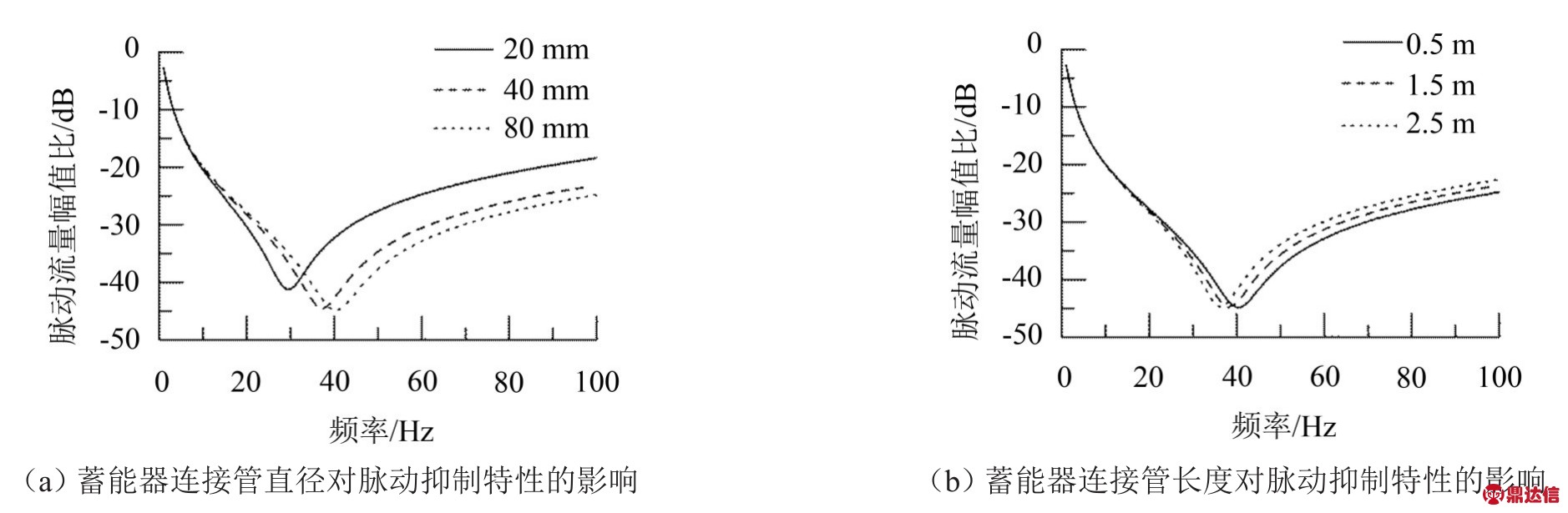
图5 蓄能器连接管参数对脉动抑制特性的影响
综上所述,气缸式蓄能器在设计时应选择合理的预充气压力,较长的气缸行程,且气缸直径不宜太大,蓄能器连接管应短而粗。
2.4 气缸式蓄能器安装前后对比分析
将气缸式蓄能器分别安装在机械式三缸压裂泵和液压驱动式三缸压裂泵上,得到流量脉动抑制结果如图6(a)、图6(b)所示。由图6可知,压裂泵流量峰值显著减小,流量脉动被显著抑制。当流量稳定后,机械式三缸压裂泵脉动流量峰-峰值由342 L/min下降至36 L/min,流量脉动由23.07%下降至2.42%;液压驱动式三缸压裂泵脉动流量峰-峰值由904 L/min下降至87 L/min,流量脉动由33.33%下降至3.22%。
3 结语
(1)气缸式蓄能器通过气缸活塞与柱塞的面积比对负载减压,可用于高压大流量场合。
(2)当流量脉动频率与气缸式蓄能器固有频率相等时,流量脉动幅值最小。而固有频率与气缸及其连接管结构参数、预充气压力有关,在设计时应选择合理的预充气压力,较长的气缸行程,且气缸直径不宜太大,使用短而粗的管道与蓄能器连接。
(3)气缸式蓄能器能显著抑制压裂泵流量脉动,可将机械式三缸压裂泵的流量脉动由23.07%降至2.42%,将液压驱动式三缸压裂泵的流量脉动由33.33%降至3.22%。
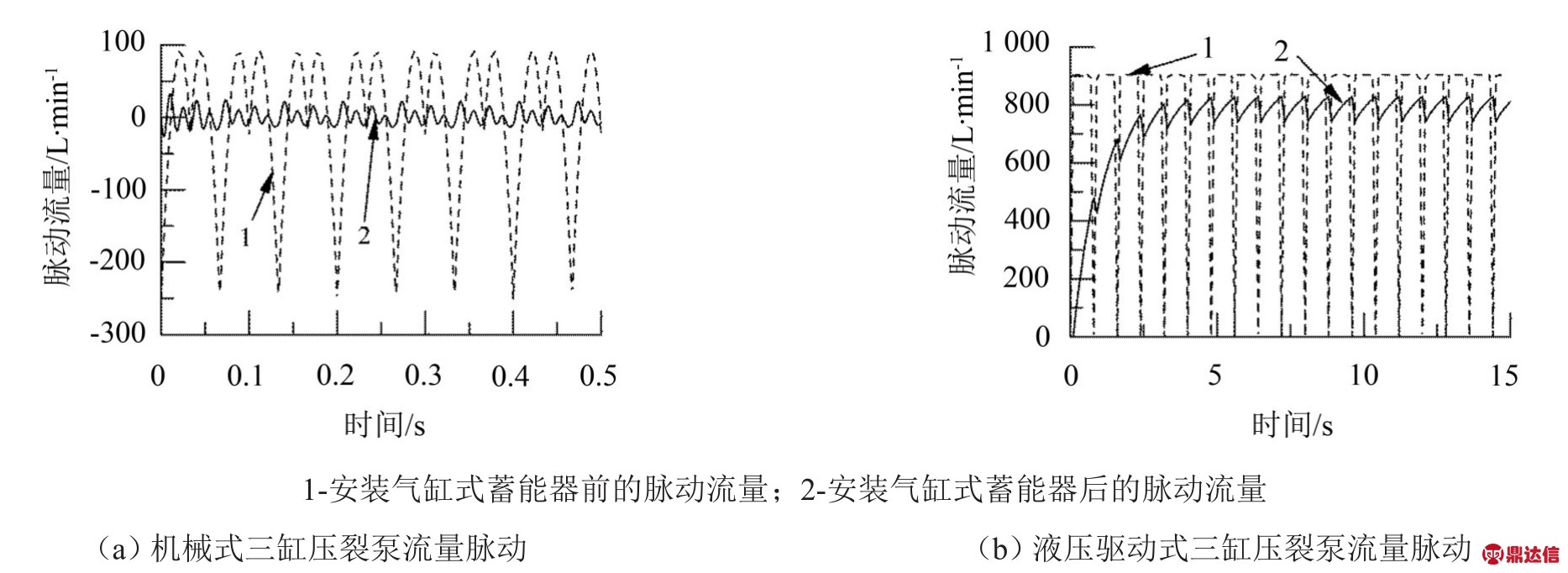
图6 压裂泵流量脉动对比曲线