摘要:蓄能器耦合特性能很好地反映液压凿岩机的非线性运动规律和流量变化情况,其系统压力响应能力直接决定了整机的工作性能。传统的耦合研究多直接以蓄能器的工作压力作为系统工作压力,这存在一个盲区,割裂了反馈控制关系。针对此不足,基于流体连续性原理,考虑泄漏与补偿等因素的影响,采用蓄能器耦合方法对液压凿岩机的工作特性和流量变化建立非线性数学模型,并推导内部各腔室的压差模型和压力计算方法。通过仿真和试验研究,分析蓄能器耦合方法和蓄能器基本参数对冲击性能的影响规律。结果表明:基于流体连续性原理的蓄能器耦合方法避免了“盲区”问题,液压凿岩机蓄能器预充压力的选择应该控制在一定的范围内,一般取冲击压力的 35% ~ 45%。
关键词:液压凿岩机;蓄能器耦合;预充压力;冲击压力
由于工况的复杂性和运动反馈的不确定性等特点,液压凿岩机压力流量变化显著,容易发生空隙现象和压力流量脉动[1-2]。作为液压凿岩机的重要组成部分,蓄能器主要是通过响应整个运动过程对流量的需求的方式来实现运动的匹配,其响应特性直接影响液压凿岩机冲击性能。因此,蓄能器动特性耦合研究能够很好地反映液压凿岩机的工作特性。目前对蓄能器的耦合研究主要集中在蓄能器耦合特性和频率等冲击参数特性的变化关系[3-5]以及蓄能器参数的影响[6-8]等方面,但上述研究主要是以蓄能器的工作压力为参考压力,割裂了配流阀、活塞和蓄能器之间的匹配控制关系,不能直接反映液压凿岩机的运动,尤其是运动中流量的变化,没有从整体上对整个系统运动进行建模和分析。笔者基于油液可压缩性,以蓄能器耦合为参考点,考虑其泄漏量与补偿量等因素,对液压凿岩机的工作特性建立了非线性数学模型,并建立内部各腔室的压差模型。通过仿真研究,分析了蓄能器耦合方法对冲击性能的影响规律。
1 蓄能器耦合特性分析
1.1 蓄能器耦合原理
作为液压凿岩机的重要组成部分之一,蓄能器主要用于吸收运动多余的流量和释放不足的流量,以满足整个运动对流量和工作压力的要求,消除空隙现象和减少压力流量脉动,其耦合响应特性直接影响液压凿岩机的冲击性能。蓄能器的耦合响应实际上是一个动态的充排油过程。为了简化分析,在此将蓄能器的耦合响应简化为一个二力平衡过程,具体的受力简化如图 1 所示。在一定的预充压力下,当系统供油能够满足运动需要时,压力油进入蓄能器充油蓄能;当系统供油不足时,蓄能器将排油。整个过程可以看作气体绝热过程,所以有

式中:ph为高压蓄能器压力;Vah为高压蓄能器的初始体积;Vh为进入蓄能器的体积 (“±”取“-”) 或排出蓄能器的体积 (“±”取“+”);k为气体绝热系数;pah为高压蓄能器的预充压力。
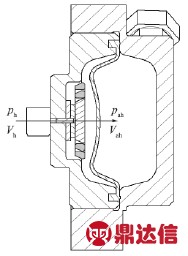
图1 液压凿岩机蓄能器耦合原理
Fig. 1 Coupling principle of accumulator of hydraulic rock drill
1.2 流量压力变化的非线性分析
液压凿岩机的运动不是一个比较确定的反馈匹配过程。液压凿岩机结构参数分布及行程反馈配流方式如图 2 所示,结合具体运动工况,以后控式液压凿岩机为例,从描述活塞和阀芯的相对运动位置变化出发,对蓄能器蓄能过程和流量压力变化展开分析。
1.2.1 阀左位静止,活塞回程加速
在此状态下,凿岩机系统供油流量为Q,除了提供活塞运动所需的流量和泄漏流量损耗外,其余的流量假定全部是蓄能器的蓄能充油,所以可得进入蓄能器的油液体积

式中:Ql为泄漏流量;Qb为补偿流量;up为活塞速度;A2为前腔的通流面积。
将式 (2) 代入式 (1),可得到此状态下蓄能器的工作压力ph。所以,结合局部损失方程,由前腔和高压蓄能器的压差计算模型可得前腔压力p2,

式中:x6为连通活塞前腔和高压蓄能器油道的阻力系数;A6为连通前腔与蓄能器之间油道的通流面积;r为液压油的密度。
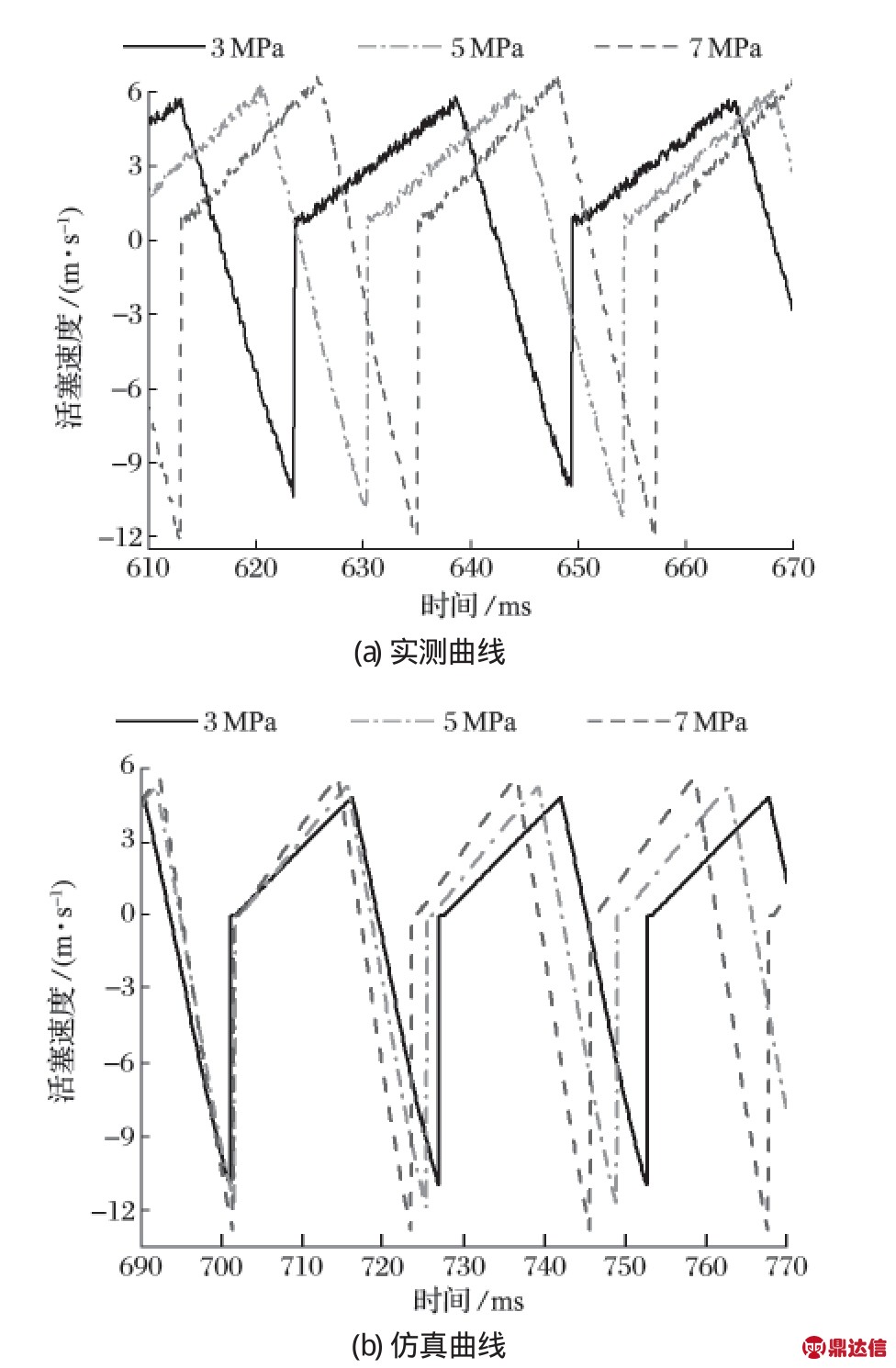
图2 液压凿岩机冲击部分的结构参数和配流方案
Fig. 2 Structural parameters and fl ow distributing scheme of impact mechanism of hydraulic rock drill
1. 钎尾 2. 活塞 3. 缸体 4. 高压蓄能器 5. 配流阀 6. 低压蓄能器
1.2.2 阀回程换向,活塞回程加速
在此状态下,与 1.2.1 状态所不同的是,输入流量Q还需提供阀芯回程换向运动所需的流量,所以这部分油液的体积

式中:uv为阀芯的速度;A3为配流阀左台阶面积。
将式 (4) 代入式 (1),可得到此状态下的蓄能器工作压力ph。同理,由前腔和高压蓄能器的压差计算模型,可得前腔压力p2,
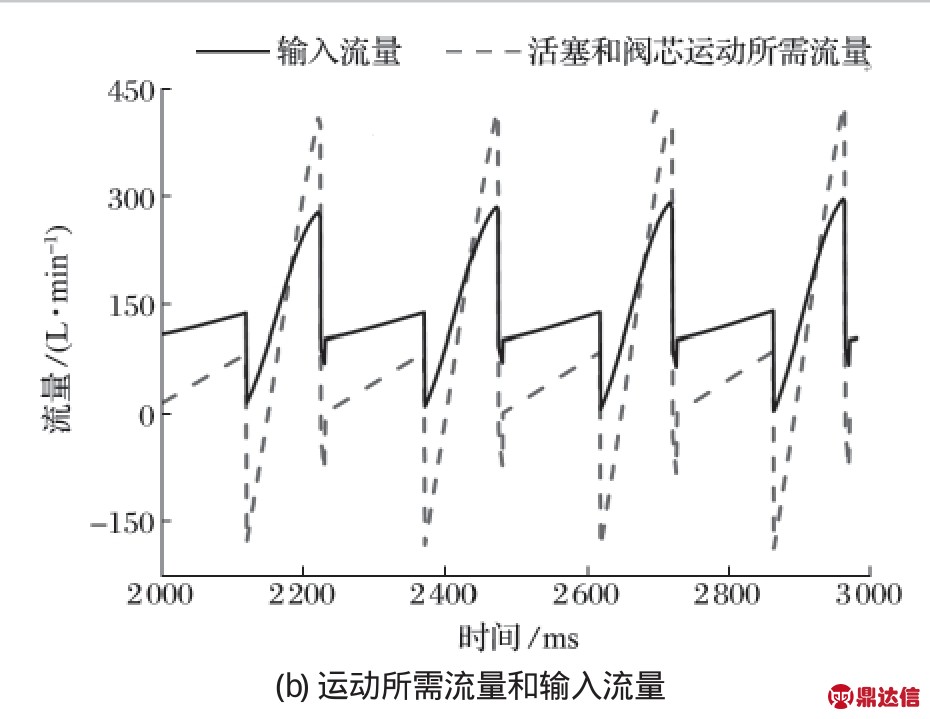
1.2.3 活塞回程制动
此时,系统供给液压凿岩机的压力油,只有一部分用于阀芯右移换向和活塞回程,其余均进入蓄能器,即高压蓄能器不仅吸收了泵输入的大部分流量,同时也吸收了活塞后腔排出的压力油,所以进入蓄能器的油液体积

此时蓄能器的工作压力ph可由式 (1) 求得,且与活塞后腔压力相同,即

由前腔和蓄能器的压力关系,可得前腔压力p2。
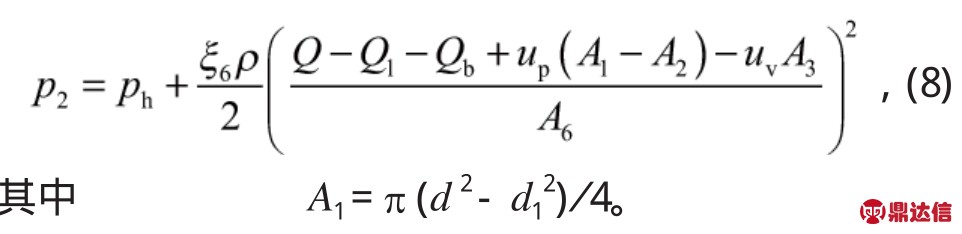
式中:A1为活塞后腔的通流面积。
1.2.4 阀换向完毕,活塞回程减速
和状态 1.2.3 不同的是,此时系统供油只有一部分作用于活塞,其余进入高压蓄能器,所以进入蓄能器的油液体积

此时系统高压油直接和蓄能器、活塞后腔连通,因此可以认为活塞后腔压力等于蓄能器的压力。将式 (9) 代入式 (1),可得到此状态下的蓄能器工作压力ph,且由式 (7) 可得p1=ph。
由状态 1.2.2 可知,前腔压力

1.2.5 阀右位静止,活塞冲程
此时活塞冲程,且随着活塞速度的增大,冲程运动所需的压力油将远多于系统供油,蓄能器将排油以释放运动所需的能量。蓄能器所排出的油液体积

此时系统高压油直接和蓄能器及活塞前、后腔连通,因此认为活塞后腔压力等于蓄能器压力。将式(16) 代入式 (1),可得到此状态下的高压蓄能器工作压力ph。
分析前腔和高压蓄能器工作压力的关系,则有

1.2.6 阀冲程换向,活塞冲程
此时阀芯和活塞运动所需的流量仍将远大于系统供油,蓄能器将排油,此外,还有小部分回油用来控制阀芯的运动。蓄能器所排出的油液体积

将式 (13) 代入式 (1),可得此状态下的高压蓄能器工作压力ph。同理,由前腔和蓄能器压差模型,可得活塞前腔压力
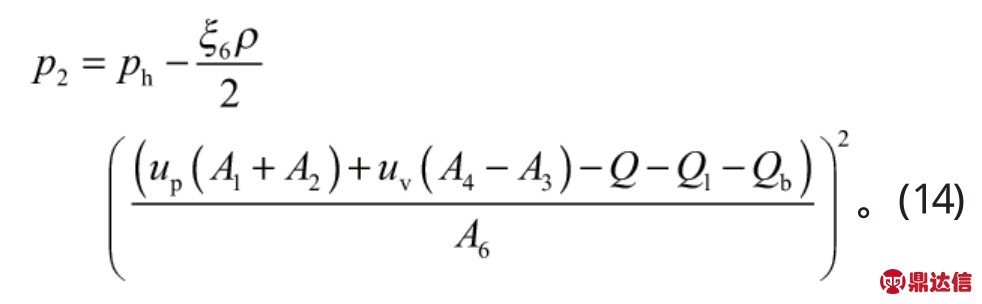
1.2.7 阀继续换向,活塞停顿
在此阶段,系统供油除了提供阀芯运动所需的流量外,全部进入蓄能器蓄能,所以进入蓄能器的油液体积

将式 (15) 代入式 (1),可得此状态下的蓄能器工作压力ph,考虑到蓄能器、阀芯右控制腔与系统输入压力油直接相通,这里认为系统压力等于蓄能器工作压力,即

式中:pq为系统供油压力。
2 仿真模型的建立
根据数学模型,对前文所述的液压凿岩机 7 个运动状态进行 MATLAB 函数编写,并基于 Simulink 仿真平台,采用函数嵌入方法进行建模。该仿真模型主要由外部参数输入、状态选择切换、数据处理、状态仿真、结果显示等 5 个模块组成,其在 Simulink 平台建立的基于 MATLAB 函数嵌入的液压凿岩机动力学仿真模型如图 3 所示。
通过该仿真模型,可以实现液压凿岩机运动规律以及各个状态下蓄能器运动特性等相关参数的仿真和数学分析,特别是冲击性能、工作压力及其对应影响因素变化规律的研究。
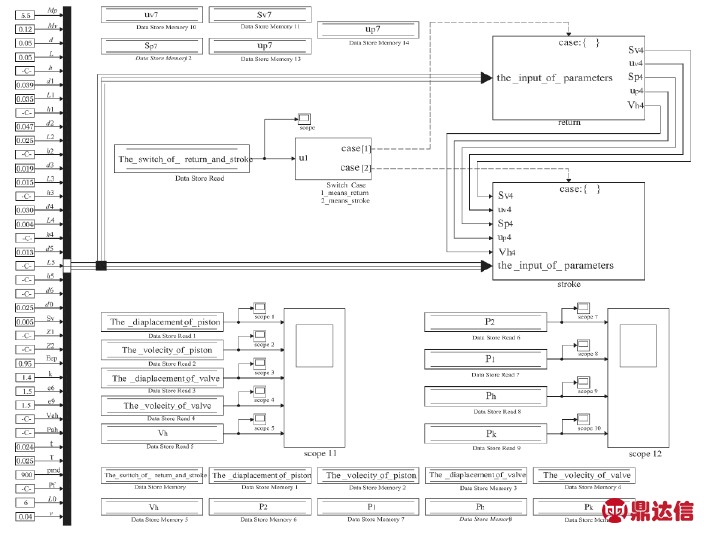
图3 基于 Simulink 的液压凿岩机仿真模型
Fig. 3 Simulation model of hydraulic rock drill based on Simulink
3 仿真与试验验证
以湖南山河智能装备股份有限公司研制的某型液压凿岩机为研究对象,其主要结构参数和工况参数设定如表 1 所列。
表1 模型的主要参数
Tab. 1 Main parameters of model
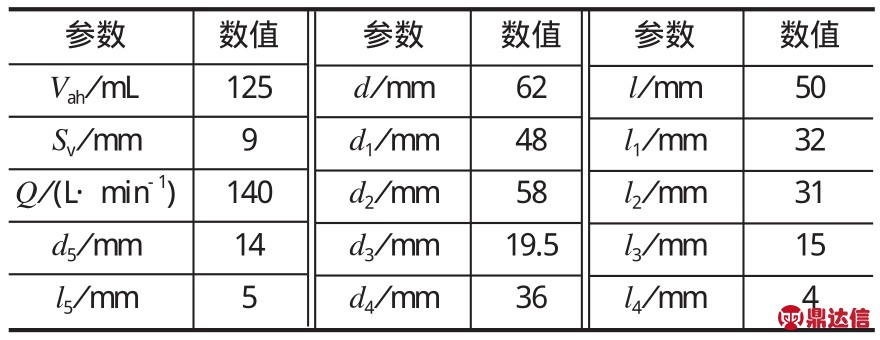
为了增强分析的可比性,保证工作与结构参数不变,对 MATLAB 函数和 Simulink 仿真模型的输入进行相应修改,即可得到预充压力分别为 3、5、7 MPa等 3 种仿真模型,并与实测进行对比验证分析。
3.1 现场试验方案
根据仿真输出,实测对象主要包括液压凿岩机缓冲腔与缓冲蓄能器的压力、流量,以及缓冲活塞速度、位移。试验测试方案如图 4 所示。该方案以钻机为平台,系统预充压力由节流阀控制,主要包括 2 个测试模块,分别是以 5060 测试仪为主的流量压力测试模块和以多普勒激光测试仪为主的速度测试模块。2 个模块共用 PC 机数据采集系统。在测试速度时,中间缸体观察孔贴有聚光防油的膜片,以保证测试的准确性。
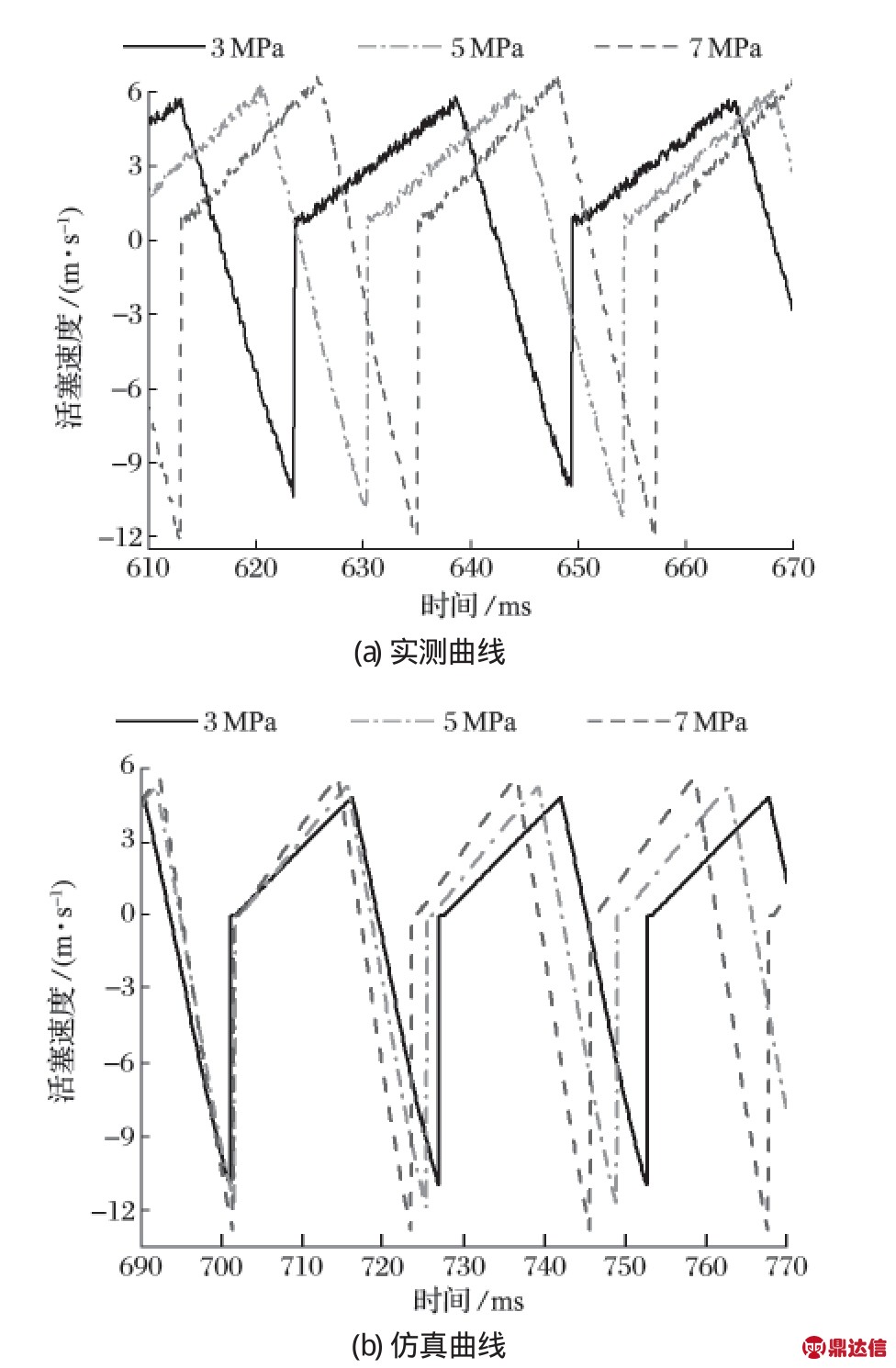
图4 测试原理
Fig. 4 Test principle
1. 电动机泵组 2. 溢流阀 3. 节流阀 4. 油冷却器 5. 供气润滑装置6. 液压凿岩机 7. 流量计 8. 压力传感器 9. 流量传感器10. 激光测速仪 11. 控制箱 12. 信号采集卡 13. 计算机 (内含数据采集处理分析程序) 14. 打印机 15. Multi-system 5060
3.2 流量压力变化关系
液压凿岩机最显著的工作特点之一是机体内压力、流量变化非常大。与一般的液压缸或马达等执行元件的压力油压力取决于外负载所不同的是,液压凿岩机的工作压力主要是由系统输入流量来决定,所以说输入流量对冲击进油压力和冲击性能有很重要的影响。
液压凿岩机输入流量和泵组供给流量的变化如图5 所示。由图 5 可知,输入流量随活塞的运动状态而呈波动变化。在回程阶段,活塞的后腔油液压缩,此时蓄能器充油,其流量变化不大;而在冲程阶段,活塞速度比较快,此时运动所需的流量比平均流量大很多。所以,此时运动所需流量主要来自于输入流量、蓄能器排油、补偿流量以及部分回油等。其中,补偿流量是因为考虑了高压进油胶管的容积膨胀效应和液压油的可压缩性等因素的影响。此时,管道流量波动比较大,且运动所需的峰值流量可达到泵组供油流量的数倍。因此,在活塞运动的一个周期内,其驱动流量会出现 2 次很大和 2 次几乎为零的变化。在传统的液压凿岩机设计与研究中,通常认为油液是不可压缩的,且工作压力是恒定的,不随运动状态的变化而变化,即冲击压力波形常作矩形波来处理。但很显然的是,相应的流量是建立对应工作压力的必要条件。
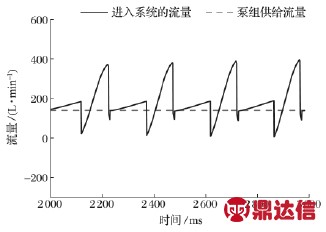
图5 输入流量和泵组供给流量的变化
Fig. 5 Variation of input fl ow and fl ow from pump
蓄能器压力、冲击压力和后腔压力的变化如图 6所示。由图 6 可知,在实际工作中,系统工作压力随局部阻力损失、配流阀油路切换以及蓄能器充排油的压力响应等因素而发生动态变化。相对矩形波来说,上述 3 种压力均会发生较大波动,其中,后腔压力波动比较明显,峰值可以达到 15 MPa,但总体波形并不是比较理想的矩形。
3.3 蓄能器耦合方法研究
以往的蓄能器耦合建模研究多直接以蓄能器工作压力作为系统工作压力。但由于蓄能器具有一定的预充压力,这在液压凿岩机工作压力小于蓄能器预充压力时会存在一个盲区,所以不能以该参考压力建立压差关系。而在前文中,主要是从运动过程中油液压缩和蓄能器体积匹配出发,结合各个运动状态,分析高压油进入或排出蓄能器的情况,以得到蓄能器工作压力,并根据相应状态下各腔室的压差模型,得到相应腔室的工作压力。这种建模方法是建立在油液压缩以及蓄能器的流量响应和匹配上。所以有必要从压力和流量的角度对蓄能器耦合方法进行仿真分析,以说明建模方法和数学模型的可靠性。蓄能器耦合方法仿真结果如图 7 所示。
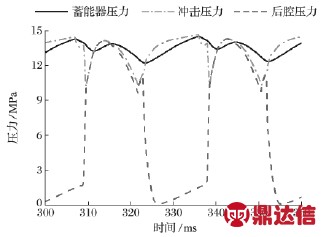
图6 蓄能器压力、冲击压力和后腔压力的变化
Fig. 6 Variation of accumulate pressure, impact pressure and back-cavity pressure
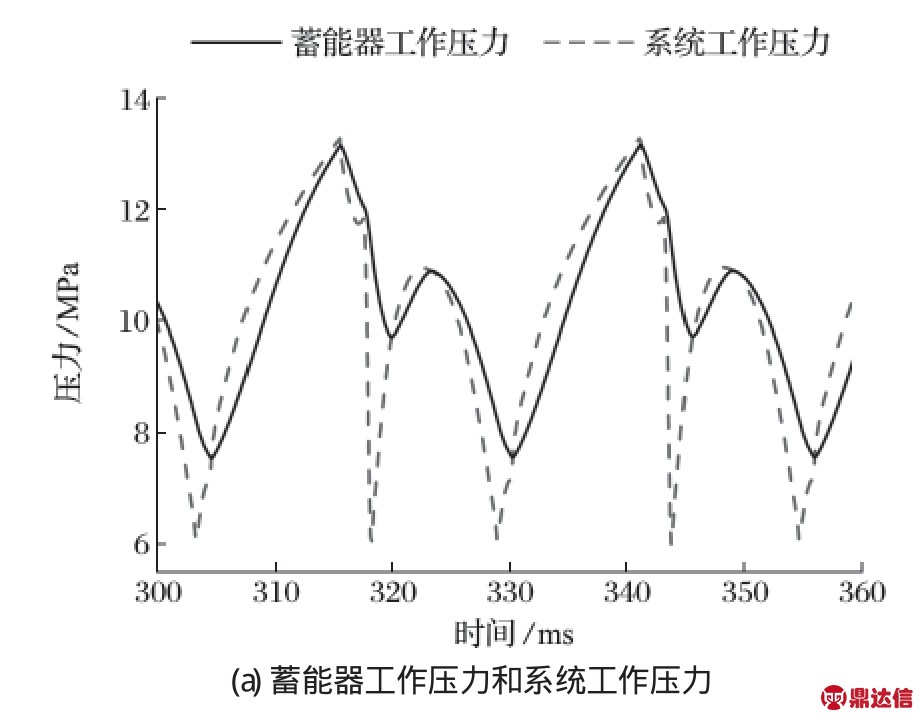
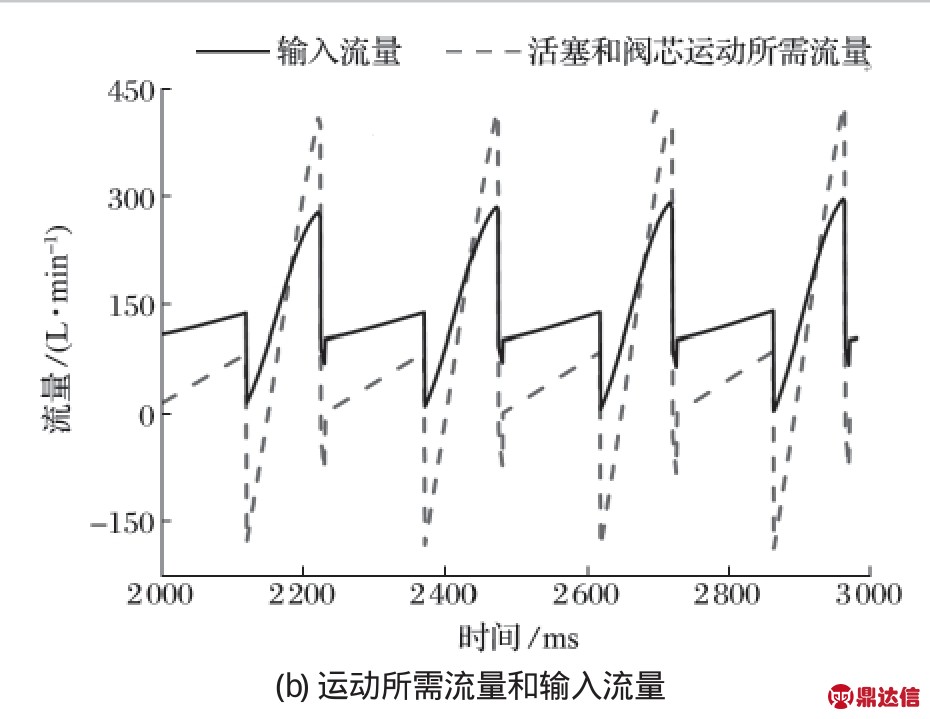
图7 蓄能器耦合方法仿真结果
Fig. 7 Simulation results by coupling method of accumulate
由图 7(a) 可知,蓄能器和系统的工作压力总体的变化趋势虽然基本一样,但很明显的是,蓄能器工作压力变化比较平稳,而系统工作压力波动相对比较剧烈。同时,考虑蓄能器预充压力的影响,在很长的工作时间内,两者间不存在一个具体且确定的关系,所以基本上很难建立一定的关系来进行求解。而对应图 7(b) 所示的系统进入液压凿岩机的流量和活塞阀芯运动所需的流量关系曲线,两者的变化基本上是同步的,且其变化和活塞的运动状态是对应同步的。而且,它们的差值可以近似为蓄能器体积的变化。所以,对蓄能器体积变化进行积分,并代入气体状态方程和相应状态的压差模型,即可得到蓄能器工作压力和各腔室压力的关系,从而建立液压凿岩机运动非线性模型。
3.4 预充压力对冲击性能的影响
压力流量关系和蓄能器耦合方法的研究表明,蓄能器的预充压力和预充体积对液压凿岩机冲击性能有重要影响。在选定液压凿岩机后,蓄能器预充体积是确定的,所以这里仅分析预充压力对系统压力和冲击性能的影响。仿真和实测结果如图 8、9 所示,对其进行数据整理和换算可得表 2。
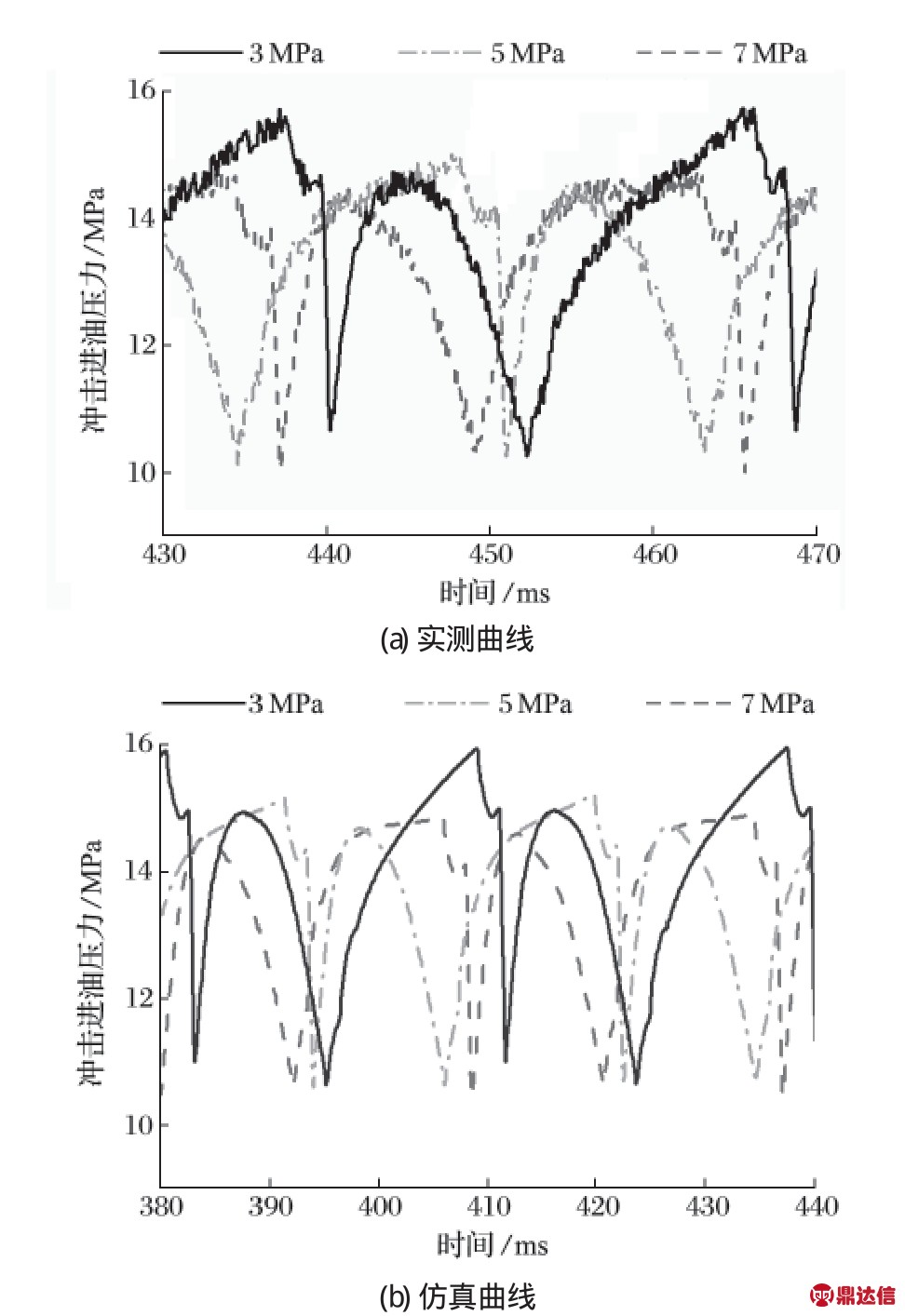
图8 不同预充压力对应的冲击进油压力实测和仿真曲线
Fig. 8 Tested curve and simulation curve of impact pressure at various pre-charge pressure
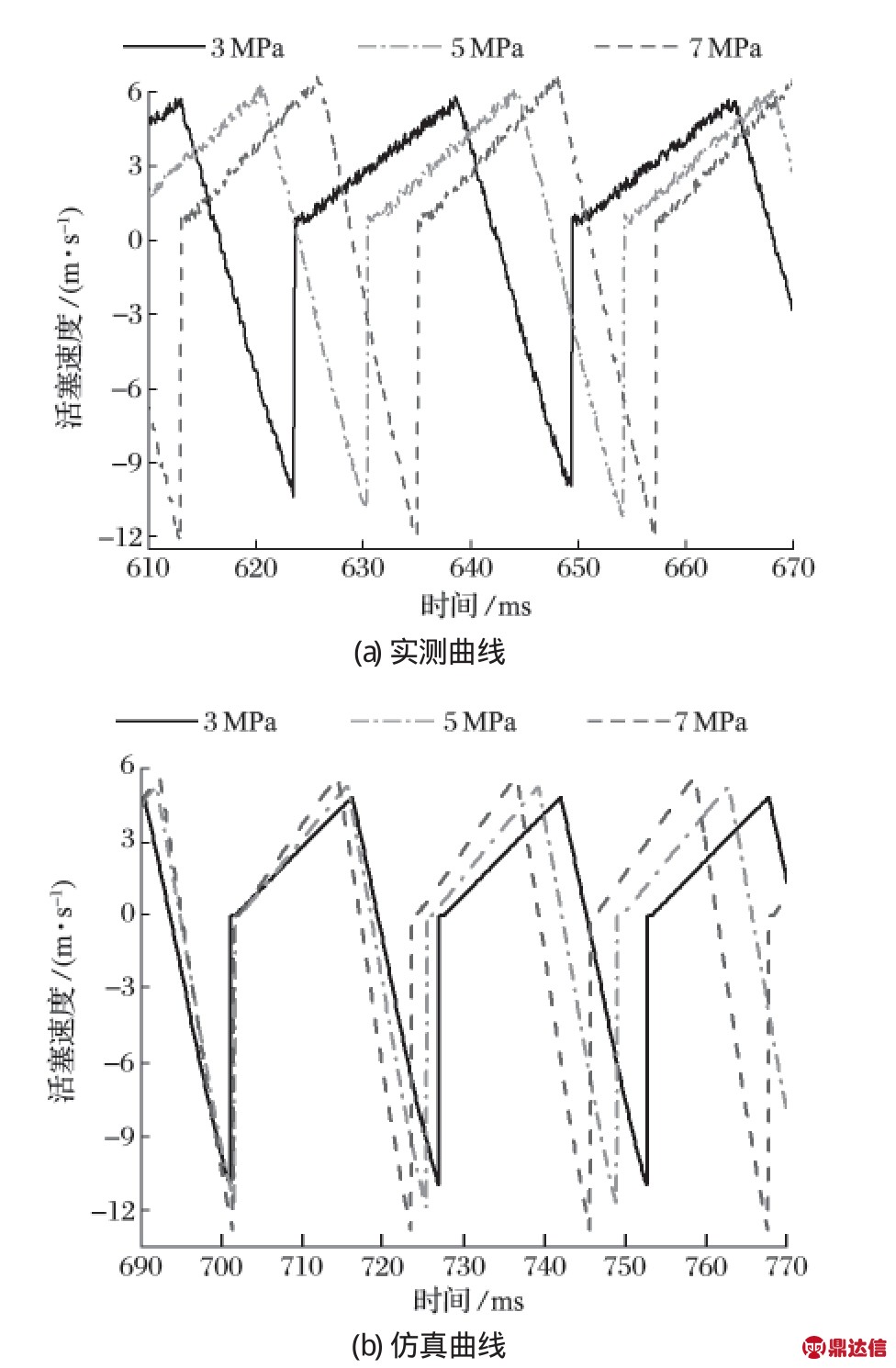
图9 不同预充压力对应的活塞速度实测和仿真曲线
Fig. 9 Tested curve and simulation curve of piston velocity at various pre-charge pressure
表2 蓄能器预充压力对液压凿岩机冲击特性影响的实测和仿真对比
Tab. 2 Comparison of test and simulation of in fl uence of accumulation pre-charge pressure on impact features of hydraulic rock drill
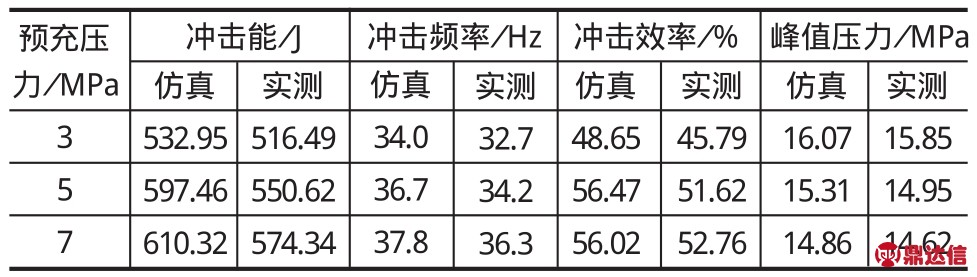
比较图 8、9,结合表 2 可知,一定的预充压力能够使系统有比较高的冲击压力以及更大的冲击能和冲击频率。实测结果偏小是因为进油胶管膨胀增大了容积,单位体积的油液压缩量减小。但当其预充压力过低或者过高时,结合图 5、6,冲击压力和流量脉动比较大,容易产生压力损失,从而影响冲击性能,产生这一现象的原因主要有 2 点:
(1) 相关研究表明,蓄能器工作的必要条件是系统冲击压力的最小值应不小于其预充压力,也就是说,如果预充压力选择过高,在冲击压力很小的时候,蓄能器不能吸收回程的能量,且在冲程时不能及时有效地释放能量,蓄能器基本不工作,从而引起系统冲击压力和进入系统的流量发生比较大的波动。此时,冲击容易造成较大的压力损失,使得冲击效率降低,影响了液压凿岩机的冲击特性。
(2) 当预充压力选择过低时,由蓄能器工作原理可知,此时蓄能器不能有效地进行补偿排油,这样也会引起一定的脉动和冲击。图 8 所示的实测和仿真曲线反映了以上两点,仿真和实测曲线走势基本相同,其误差能够控制在系统允许的最大误差范围内,所以仿真和实测分析表明,液压凿岩机蓄能器预充压力的选择应该控制在一定的范围内,对于后控式凿岩机来说,一般取冲击压力的 35%~45%。
4 结论
(1) 液压凿岩机压力流量变化是波动的,以蓄能器耦合作为建模的基础,能克服传统建模的“盲区”问题。
(2) 预充压力选择较低时,系统冲击压力波动较大,峰值相对较高,此时冲击容易造成较大的压力损失,使得其能量利用率降低,影响系统的冲击性能。
(3) 预充压力过高,会造成整个冲击压力低于或接近预充压力,而使得机体相应腔室油液压缩,压力急剧升高,同时也会因为吸收的能量不够而导致冲程时释放的能量不足以满足运动所需流量的要求,从而引起很大的流量波动和压力冲击。
(4) 液压凿岩机蓄能器预充压力的选择应该控制在一定的范围内,对于后控式凿岩机来说,一般取冲击压力的 35%~45%。