摘 要:针对目前并联式液压混合动力车存在制动特性和能量回收率不能兼顾的缺陷,通过分析蓄能器参数在液压辅助系统中的影响作用,提出了用2个小容积蓄能器代替1个大容积蓄能器,并采用蓄能器逐个充液的方案。分析了并联式液压混合动力车能量回收与辅助驱动系统的工作原理和关键元件的参数配置;建立了双蓄能器能量回收与辅助驱动AMESim仿真模型,并进行了车辆液压低速制动和高速制动的仿真分析。结果表明:采用双蓄能器逐个充液的制动方式,低速制动能够显著缩短制动时间和制动距离,高速制动能够有效提高能量回收率。
关键词:双蓄能器;液压混合动力;制动特性;能量回收;AMESim
引言
近年来,随着液压技术在汽车领域的不断创新应用,液压混合动力车正成为国内外学者的研究热点[1,2]。学者们的研究主要集中在从机理上探究二次元件、蓄能器、转矩耦合器等关键元件的选型原则, 以及应用仿真技术研究各元件参数变化对能量回收和辅助驱动的影响规律等方面[3,4]。
蓄能器作为液压混合动力车的一个关键元件,起到能量存储和释放的作用[5,6]。研究表明:蓄能器容积的确定至关重要,对于制动过程,蓄能器容积越小,越有利于改善制动特性,缩短制动时间和制动距离,但容易引起溢流损失;蓄能器容积变大,制动特性变差,但能量回收率提高。对于启动过程,蓄能器容积越大,辅助动力越持久,能量利用率越高。因此,如何优化蓄能器容积,实现优良的制动特性和较高的能量回收率对提高液压混合动力车整体性能具有重要的意义。
针对以上问题,提出了一种双蓄能器逐个充液的并联混合动力能量回收与辅助驱动方案,该方案既发挥了小容积蓄能器良好的制动特性,又发挥了大容积蓄能器较高的能量回收率,能够在一定程度上克服单蓄能器储能制动存在的缺陷,为液压混合动力车的辅助系统设计提供了思路。
1 并联式液压混合动力车原理及参数分析
1.1 并联式液压混合动力车原理
并联式液压混合动力车原理如图1所示,主要由发动机、二次元件(液压泵/马达)、蓄能器、转矩耦合器、离合器、减速器、车桥等组成。
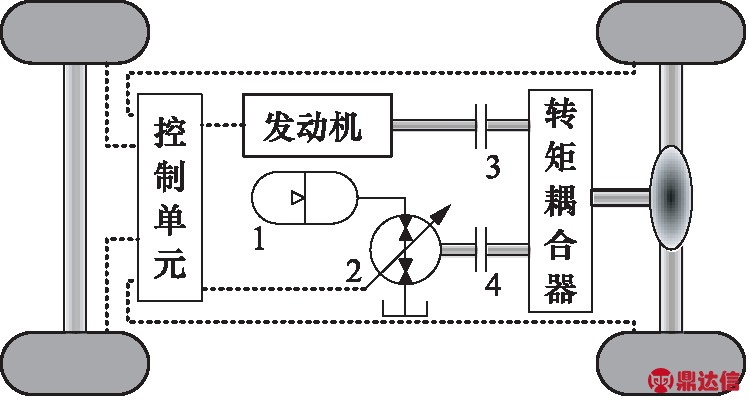
1.蓄能器 2.二次元件 3.发动机离合器 4.液压系统离合器
图1 并联式液压混合动力车原理图
其工作主要分为启动、巡航、制动三个过程。启动时首先将离合器4接通,蓄能器1中的高压油推动二次元件以马达的形式输出转矩,驱动车辆启动。当蓄能器中的压力降到最低工作压力,断开离合器4,接通离合器3,由发动机提供动力。巡航时与常规车辆相同,只接入发动机,液压系统不参与工作。制动时首先将离合器3断开,离合器4接通,车辆惯性驱动二次元件以泵的形式将油压入蓄能器,将能量以高压油的形式存储在蓄能器中。同时高压油通过作用在泵轴上的阻力矩,迫使车辆停止,这样达到既能回收能量,又能制动车辆的效果。
1.2 并联式液压混合动力车参数分析
车辆在直线行驶过程中的力平衡方程为:
F=Ff+Fw+Fi+Fj
(1)
其中,
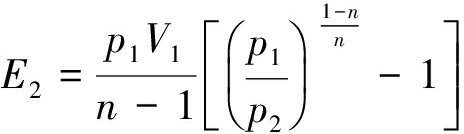
式中:F —— 驱动力,N
Ff —— 滚动阻力,N
Fw —— 空气阻力,N
Fi —— 加速阻力,N
Fj —— 坡度阻力,N
G —— 车辆总重量,N
CD —— 风阻系数
A —— 迎风面积,m2
v —— 车辆速度,km/h
y —— 车辆位移,m
δ —— 旋转质量转换系数
a —— 道路坡度角,rad
f —— 路面滚动阻力系数
若由二次元件单独驱动车辆行驶,则其输出功率为:

(2)
式中: Tp/m —— 二次元件输出转矩,N·m
ωp/m —— 二次元件的转速,rad/min
ηT —— 系统效率
ib —— 转矩耦合器速比
i0 —— 主减速器速比
r —— 车轮半径,m
当车辆在平直的路面上直线行驶时,二次元件的最小输出功率必须满足车辆以平均速度运行,即:

(3)
式中: vavg —— 平均巡航车速,km/h
二次元件的最大输出功率为车辆以最大速度vmax在平直路面上行驶时的输出功率和以速度vslop在坡度为a的斜坡上行驶的输出功率中的最大值,即:
max(Pp/m)=max[Pp/m1,Pp/m2]
(4)


气囊式液压蓄能器的主要参数有气囊的充气压力p0,气囊的充气体积V0,公称压力pr,最低工作压力p1,最高工作压力p2。蓄能器在工作过程中符合玻意耳定律,即:

(5)
式中:V1 —— p1时的气体体积
V2 —— p2时的气体体积
n —— 气体多变指数,等温过程为1,绝热过程为1.4
能量回收系统的蓄能器最低工作压力p1和最高工作压力p2由式(6)和式(7)确定。一般p1与p2满足关系式p2≤3p1,根据经验公式,推荐p1=(0.6~0.85)p2。
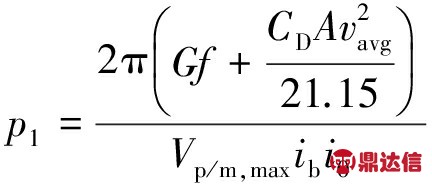
(6)
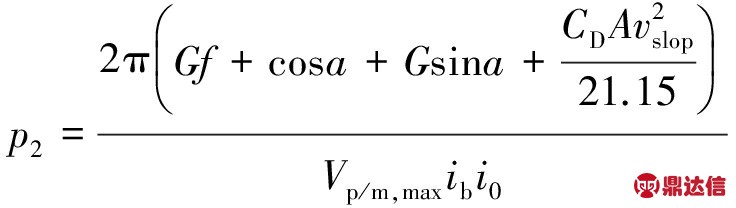
(7)
蓄能器的充气压力p0理论上应等于p1,但由于存在泄漏、温度等因素影响,p0应小于p1,一般取p0=(0.8~0.85)p1。
蓄能器容积可通过车辆在制动时的能量平衡方程(8)确定。

(8)
其中,E1=GfS=mgfS
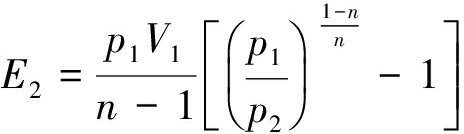
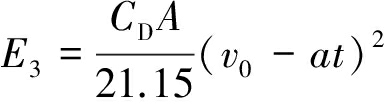
式中: v1、v2 —— 车辆在t1和t2时刻的速度,m/s
E1 —— 滚动阻力损失的能量,J
E2 —— 蓄能器回收的能量,J
E3 —— 空气阻力损失的能量,J
S —— 车辆制动位移,m
v0 —— 车辆制动初速度,m/s
a —— 车辆制动减速度,m/s2
转矩耦合器的速比选择应满足任意时刻二次元件的转数不超过其许用的最高转数如式(9)所示:
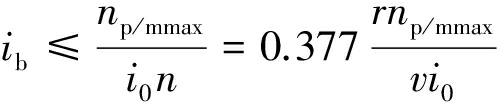
(9)
式中:ib —— 转矩耦合器速比
i0 —— 主减速器速比
r —— 车轮半径,m
v —— 车辆速度,km/h
np/m,max —— 二次元件的最高转速,r/min
2 双蓄能器液压混合动力车制动仿真分析
基于双蓄能器车辆能量回收与辅助驱动系统的工作原理,建立AMESim仿真模型,图2为双蓄能器能量回收与辅助驱动仿真模型,表1为仿真参数。该模型在保证蓄能器总容积不变的前提下,用2个30 L蓄能器代替1个60 L蓄能器。通过一个P型中位机能的三位四通电液换向阀实现2个蓄能器的充液切换。即在制动过程中,换向阀2右位首先得电,对蓄能器1充液。当其油压达到切换值30 MPa时,换向阀2左位得电,蓄能器1断开,蓄能器2接通,继续储能。当其压力达到系统极限压力31.5 MPa,停止充液,能量回收结束。在辅助驱动过程中,换向阀2工作在P型中位,两蓄能器同时释放压力,驱动二次元件工作。
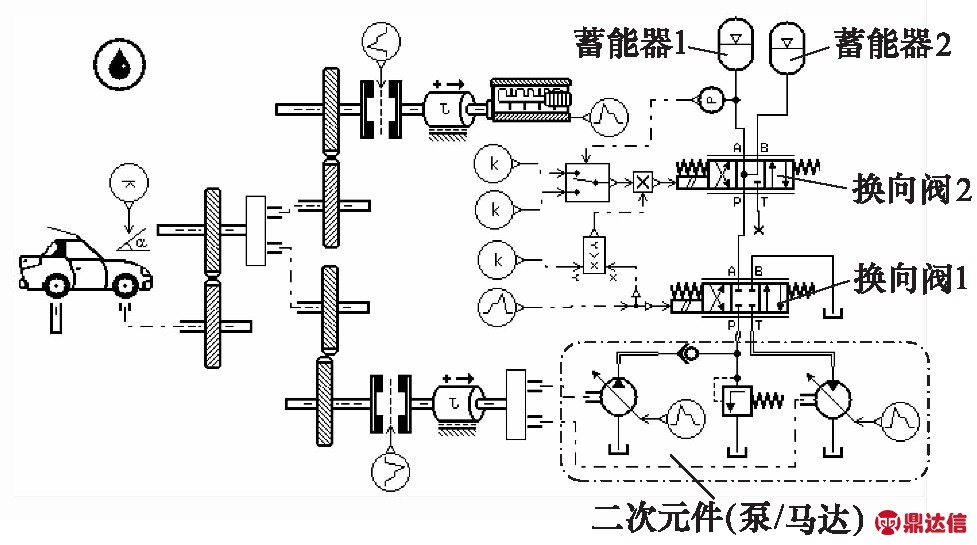
图2 双蓄能器能量回收与辅助驱动仿真模型
表1 双蓄能器能量回收与辅助驱动仿真参数表
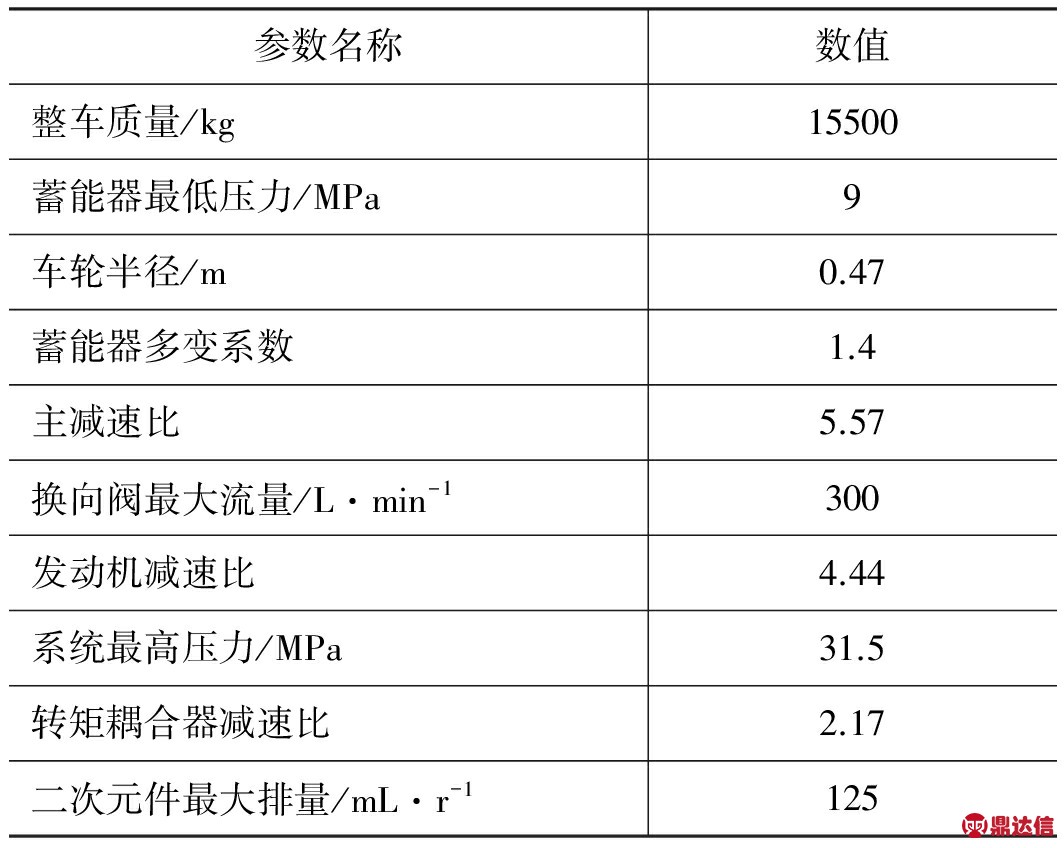
针对单蓄能器制动和双蓄能器制动两种方案,就低速制动和高速制动两种工况进行仿真分析。仿真中忽略车辆行进中的坡度、风阻、运动副间的摩擦力以及泵/马达的泄漏等因素,即是在理想条件下进行仿真。图3为低速制动时仿真特性曲线,图4为高速制动时仿真特性曲线。图中方案一为单蓄能器制动,方案二为双蓄能器制动。
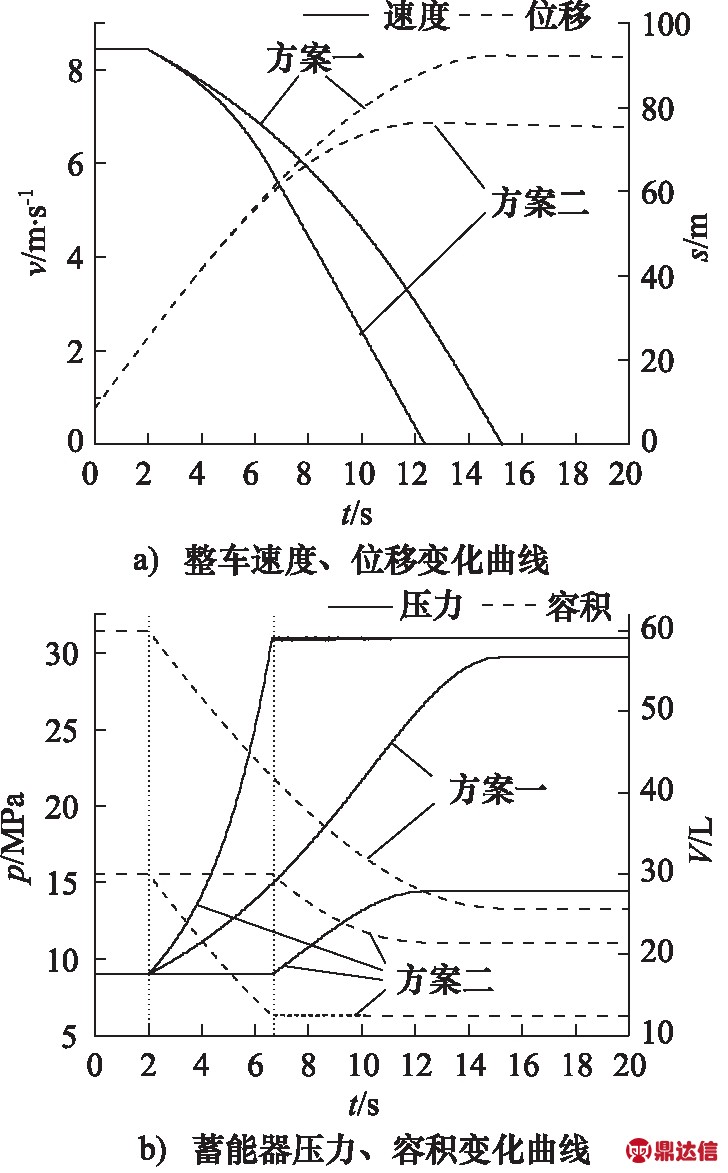
图3 低速制动时仿真特性曲线
由图3可知,当车辆以8.5 m/s的速度开始制动,采用双蓄能器方案的能量回收系统制动效果显著,车辆制动时间和制动距离分别较单蓄能器方案缩短3 s和16.5 m,说明该方案制动动态特性较好。当车辆在2 s时刻开始制动,方案一的蓄能器皮囊容积被不断压缩,蓄能器压力逐渐升高,该过程压力变化较平缓,车辆减速度较小,制动缓慢。方案二的蓄能器1首先投入使用,压力升高较快,在6.7 s时刻压力达到切换值30 MPa,蓄能器1停止充液,蓄能器2开始工作。由于整个过程压力变化较剧烈,导致车辆减速度较大,制动迅速。上述两种方案蓄能器的最终压力都没有达到系统的极限压力31.5 MPa,所以没有溢流损失,能量回收率较高。
由图4可知,当车辆以12.6 m/s的速度开始制动,双蓄能器方案的制动时间和制动距离分别较单蓄能器方案缩短1.4 s和16 m,制动效果较好。方案一在7.9 s时率先达到系统极限压力,出现溢流,溢流量达276.6 L/min。方案二在8.5 s时出现溢流,溢流量达214 L/min,说明当车辆以较高速度制动时,采用双蓄能器方案能提高能量回收率。
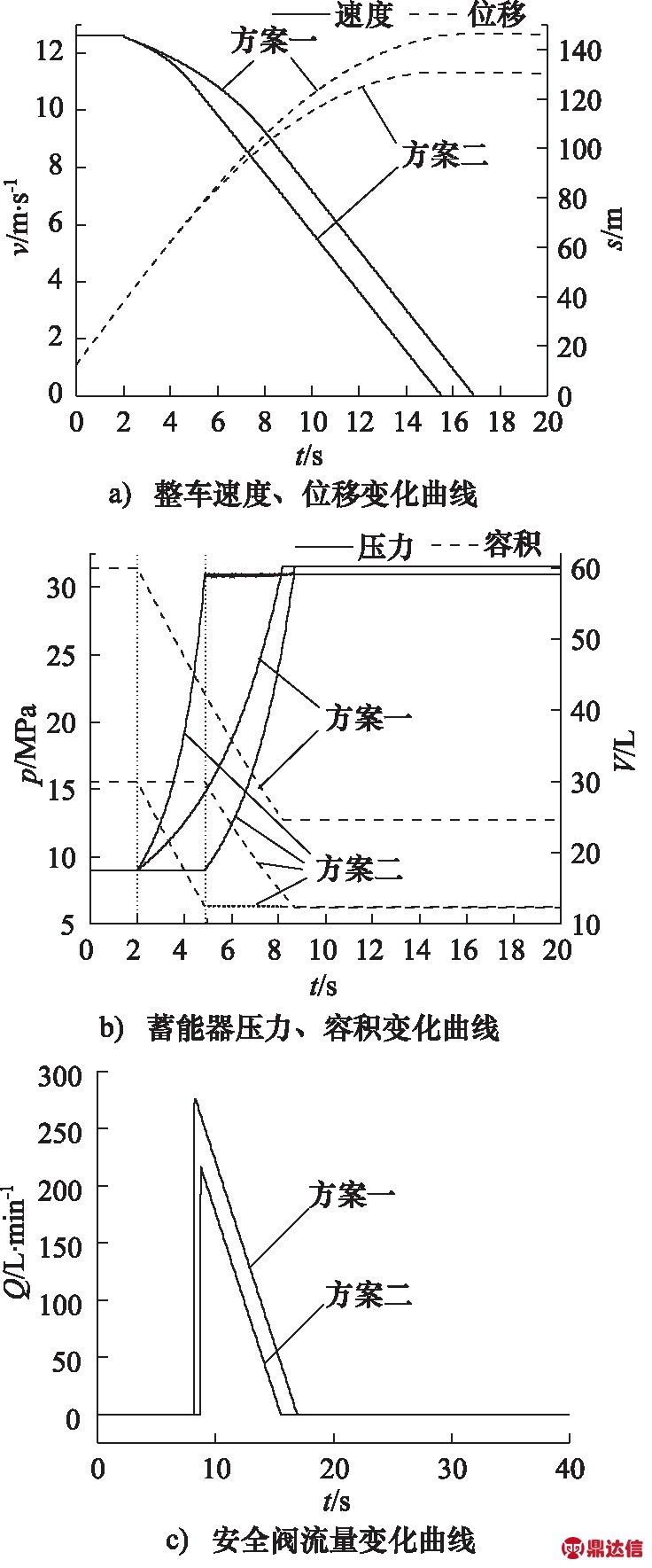
图4 高速制动时仿真特性曲线
3 结论
(1) 双蓄能器逐个充液的并联式液压混合动力车,在一定程度上克服了单蓄能器制动特性和能量回收率不可兼顾的缺陷。尤其在低速制动时,制动效果显著,制动时间和制动距离明显缩短。
(2) 高速制动时,双蓄能器液压混合动力车不仅能够缩短制动时间和制动距离,而且提高了能量回收率。