摘要:针对矿井提升机的制动过程进行了理论分析及建模,介绍了恒力矩制动液压站在使用过程中,不同的蓄能器充气压力对液压站比例阀调压性能的影响。借助 AMESim 软件对液压回路进行仿真分析,调整充气压力使液压站达到最优效果,为后期调试提供了理论依据。
关键词:提升机;制动;恒力矩;蓄能器;充气压力;调压性能
矿井提升机是煤炭、金属等矿山开采的关键设备,关系到国家基础工业和能源供应的生产,是目前大部分矿山所采用的提升装置。该提升装置主要由主轴装置、电动机、电控装置及制动系统液压站组成。制动系统液压站除了能在停车时提供定车功能外,还能够在提升装置出现紧急情况时实现安全制动,是提升装置安全运行的重要保障。目前的制动系统液压站根据其安全制动的方式不同,主要可分为恒减速制动和恒力矩制动两种。
具备恒力矩安全制动功能的液压站以中信重工机械股份有限公司 (以下简称“中信重工”) 生产的 16系列液压站为典型代表。该液压站采用恒压变量泵作为压力源,能够在系统达到最大压力时减少输出,节能、环保;采用插装阀作为主要的控制阀组,动作灵敏、可靠,抗污染性能好;油压调整采用比例溢流阀,线性度和稳定性得到很大的提高[1]。该液压站自2000 年推出后,已逐渐取代了原采用电液调压装置的13 系列产品。在提升系统发生事故时,制动系统可实现安全制动,液压站动力源油泵电动机停止运转,此时系统压力由蓄能器供油保障。因此,蓄能器的工作状况直接关系到提升系统安全制动的功能实施和性能可靠性。笔者将对恒力矩液压站的工作过程及蓄能器对制动系统性能的影响进行研究和分析。
1 制动过程分析及建模
1.1 恒力矩液压站简介
恒力矩液压站的主要作用为:在工作制动时,对盘形制动器提供制动油压,使制动器正常开闸、合闸;在提升系统发生故障时 (如全矿停电等),提升机必须实现紧急制动。在事故状态下,恒力矩二级制动系统可以使盘形制动器的油压迅速降低到预先调定的某一值,对提升机进行平稳减速制动,经延时待提升机速度降为零或接近于零时,盘形制动器的全部油压值迅速回到零,使提升系统处于全制动状态。
恒力矩液压站由蓄能器、单向节流阀及溢流阀等构成,其中安全制动部分的原理如图 1 所示。在系统发生故障时安全制动过程如下:油泵电动机、比例溢流阀线圈、电磁铁 G3 断电,电磁铁 G5 仍带电,卷筒的盘形制动器油压降为溢流阀 5 调定的压力 P1 级值,即第一级制动油压值,保压到时间继电器动作,电磁铁 G5 断电,油压降到零,实现全制动[2]。在此延时过程中,蓄能器起稳压补油作用,调节单向节流截止阀的开口度可调节其补油量,使延时过程中 P1值基本稳定在要求值[3]。系统油压变化过程如图 2 所示。
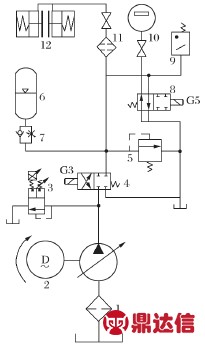
图1 液压系统原理
Fig. 1 Principle of hydraulic system
1, 11. 过滤器 2. 柱塞泵 3. 比例溢流阀 4, 8. 换向阀5. 溢流阀 6. 蓄能器 7. 单向节流阀 9. 压力继电器10. 压力传感器 12. 制动器
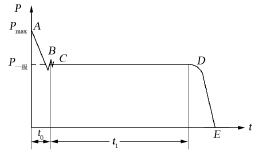
图2 恒力矩二级制动油压示意
Fig. 2 Sketch of oil pressure during constant-torque and two-stage braking
1.2 系统数学模型的建立
安全制动时,在由蓄能器、溢流阀、制动器液压缸组成的压力容积系统中,不同阶段的过程如下。
设蓄能器在预充气后,预充气体压力为 P0,气体容积为 V0,在正常开闸过程中,系统压力由油泵出口的比例溢流阀调定,对蓄能器充油并达到的最大系统压力 (即开闸油压) Pmax,此时蓄能器内气体压力为 Pmax,气体容积为 V1;此初始蓄能器充油阶段,蓄能器内气体变化为等温状态,由理想气体变化过程的Boyle-Mariotte 定律[4]得

在发生故障工况进行安全制动时,油泵电动机、比例溢流阀线圈、电磁铁 G3 断电,盘形制动器迅速贴合至闸盘,系统压力降至贴闸压力 P贴,假设此时蓄能器容积为 V2,在此波动过程中,蓄能器内气体变化近似为绝热状态,由 Boyle-Mariotte 定律得

为了研究系统在上压过程中油压的跟随性,所有电磁换向阀的带电逻辑仅按照上压过程进行仿真,仿真结果如图 4 所示。

保压过程中,由于系统中液压阀、制动器液压缸等元件存在一定的泄漏量,假定为 q,则在保压开始至结束的时间 t内,蓄能器内气体体积变为 V4,则

假设一级制动保压结束时,系统压力为 P′一级,在此保压过程中,蓄能器内气体变化近似为绝热状态,由 Boyle-Mariotte 定律得

在安全制动时,要想保持提升机由 B 到 D 的稳定减速制动,必须保证蓄能器存储足够的压力能,并有一个受控的能量释放过程,保压过程中系统制动压力波动 ΔP 尽可能地小,则

联立式 (1) ~ (6) 可得
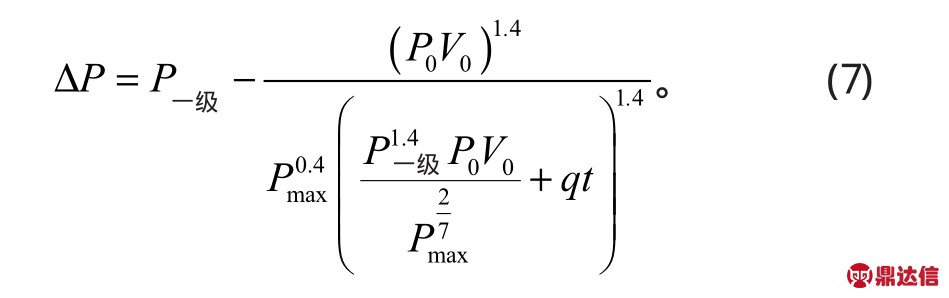
2 蓄能器对液压站的影响分析及仿真
2.1 AMESim 建模实现
以 TE161B 型号的恒力矩液压站为例,利用AMESim 软件对该系统进行建模,通过仿真分析来确定蓄能器对液压站调压性能的影响,部分简化后系统仿真模型如图 3 所示[5]。其中各元器件的参数设置如表 1 所列。
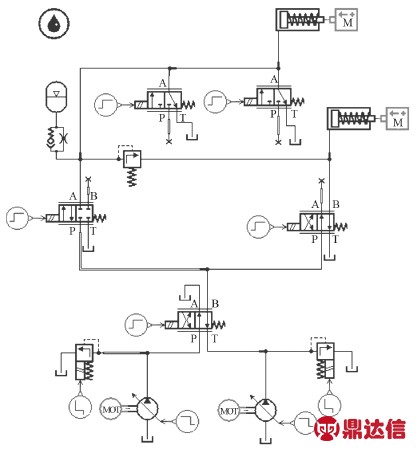
图3 液压系统仿真模型
Fig. 3 Simulation model of hydraulic system
表1 液压系统主要参数
Tab. 1 Main parameters of hydraulic system
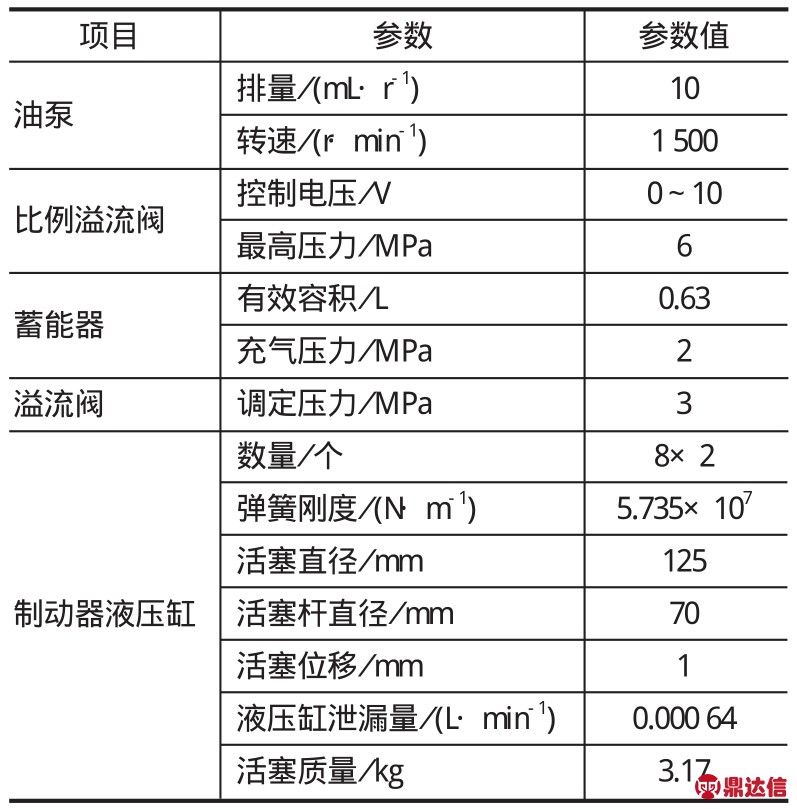
2.2 蓄能器对开闸影响分析
因液压站的开闸过程会受到蓄能器充气压力的影响,可改变充气压力,在 AMESim 软件中进行多重仿真,充气压力从 2 ~ 4 MPa 变化时仿真结果如图 5 所示。结合提升机运行的实际工况,取上压时间为 0.8 s较为合适,对应的蓄能器充气压力为 3、4 MPa。
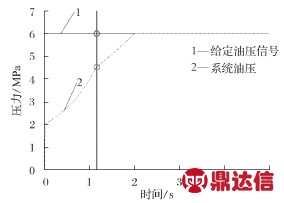
图4 开闸过程油压曲线
Fig. 4 Variation curve of oil pressure during braking start-up
在给定油压信号即比例溢流阀调定压力下,其中油泵输出的系统压力即 2 组液压缸的压力上升曲线如图 4 所示。在系统中蓄能器的充气压力为 2 MPa 情况下,其系统压力明显在2 MPa 的位置有很大的拐点,即在 2 MPa 之前有良好的跟随性,而在 2 MPa 之后压力上升明显缓慢。
同时,根据中低压制动器的性能参数,制动器的贴闸压力

式中:Pc 为制动系统综合阻力 (中低压制动器一般取 1.5 MPa)。
由式 (8) 可得,当系统压力上升到 P贴 时,对于中低压制动器来说 P贴 ≈ 4.5 MPa,此时制动器状态为贴闸,则提升系统不会出现堵转现象,不影响主电动机的正常运转。从图 4 可以看出,从系统发出信号到达到 P贴 的时间约为 1.2 s,达到 Pmax 的时间约为 2 s。根据提升机运行的状况来看,该时间稍微偏长,会影响提升控制系统的力矩建立时间,从而影响提升整体效率,需要尽量缩短该时间。
在制动器贴合至闸盘后,制动器液压缸位移基本不变,制动系统压力继续降至溢流阀 5 调定的压力P一级 值,即第一级制动油压值,并进行保压,假设此时保压开始时蓄能器容积为 V3,在此波动过程中,蓄能器内气体变化近似为绝热状态,由 Boyle-Mariotte定律得
2.3 蓄能器对恒力矩制动影响分析
由上述分析可以看出,为了避免液压站的调压特性影响到提升机的运转,建议蓄能器的充气压力为 3 MPa 左右为宜,但同时需要保证恒力矩制动的效果。假定 P一级 压力一般设定为 3 MPa,蓄能器的充气压力为 3 MPa 时,通过 AMESim 软件进行恒力矩液压站的安全制动工况仿真,结果如图 6 所示。
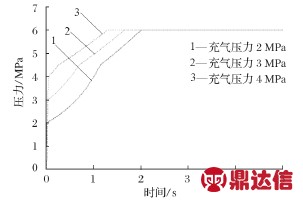
图5 蓄能器充气压力对系统油压的影响曲线
Fig. 5 Influence curve of inflation pressure of accumulator on oil pressure of system
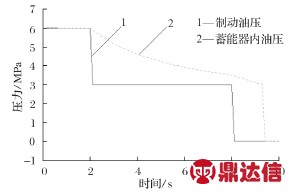
图6 恒力矩制动油压曲线
Fig. 6 Variation curve of oil pressure during constant-torque braking
从图 6 可以看出,当提升系统在 2 s 发生故障时,其中 1 组制动器的压力因电磁阀动作迅速回到0,剩余 1 组制动器通过蓄能器和溢流阀产生恒力矩制动,维持 3 MPa 的制动压力 8 s 后将为 0,达到了平稳制动的效果。
为了验证蓄能器不同充气压力对恒力矩制动保压效果的影响,可改变充气压力,在 AMESim 软件中进行多重仿真,充气压力从 2 ~ 5 MPa 变化时仿真结果如图 7 所示。
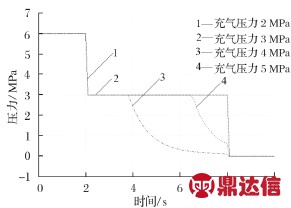
图7 蓄能器充气压力对制动过程的影响曲线
Fig. 7 Influence curve of inflation pressure of accumulator on braking process
从图 7 可以看出,恒力矩制动时保压时间随着充气压力的升高而变短,在充气压力为 5 MPa 的情况下,将无法保证制动压力稳定在 P一级 并持续 6 s 的要求。因此若充气压力过大,蓄能器将无法补偿系统的泄漏量。
从仿真效果综合来看,蓄能器充气压力过小时将延长提升机的开闸过程,充气压力太大时则无法保证恒力矩制动的保压效果,应在 2 ~ 4 MPa 区间选取。但在实际调试过程中,随着制动器数量的增加,以及制动器内部泄漏的情况不同,调定的充气压力和单向节流阀的开口度略有不同。另外,不同的电控系统、提升机的载荷不同,对压力上升的要求也不同,还需要在调试过程中进行调整。
3 结语
对于恒力矩液压站来说,蓄能器设计在主回路上影响液压站的调压性能。随着蓄能器的预充气压力不同,其曲线也有所区别,在实际调试过程中,需要根据主电动机的特性、载荷、制动器的数量及泄漏情况等进行计算和验证,在能够达到良好的提升机运行特性及保证安全制动的前提下,进行现场实际调整。