摘 要:简要介绍蓄能器在国外液压抽油机储能技术上的应用,分析蓄能器在液压抽油机上实现下行程能量回收的应用原理,以及实现蓄能器在液压抽油机储能的技术条件。
关键词:液压抽油机;蓄能器;储能
蓄能器是将压力流体的液压能转换为势能储存起来,当系统需要时再由势能转化为液压能而做功的容器。
蓄能器具有的功用:回收能量、存储能量(在实际使用中又可细分为:作辅助动力源,减小装机容量;补偿泄漏;作热膨胀补偿;作紧急动力源;构成恒压油源);缓和液压冲击压力、热胀吸收;吸收液压脉动压力、力学平衡;系统压力补偿、保压;短期容积补偿、增加流量;噪声衰减。
随着密封材料、皮囊材料等新材料不断推陈出新,特别是新型液压变压器(称New Hydraulic Transformer或称液压二次元件、泵马达)、液压传动技术、控制技术的发展,使得蓄能器储能技术的优越性得以充分展现,蓄能器储能的应用范围越来越广。利用蓄能器储存下行程重力势能在液压抽油机上的应用,正是石油矿场机械利用蓄能器提高能量利用率、节能的一个重要途径。
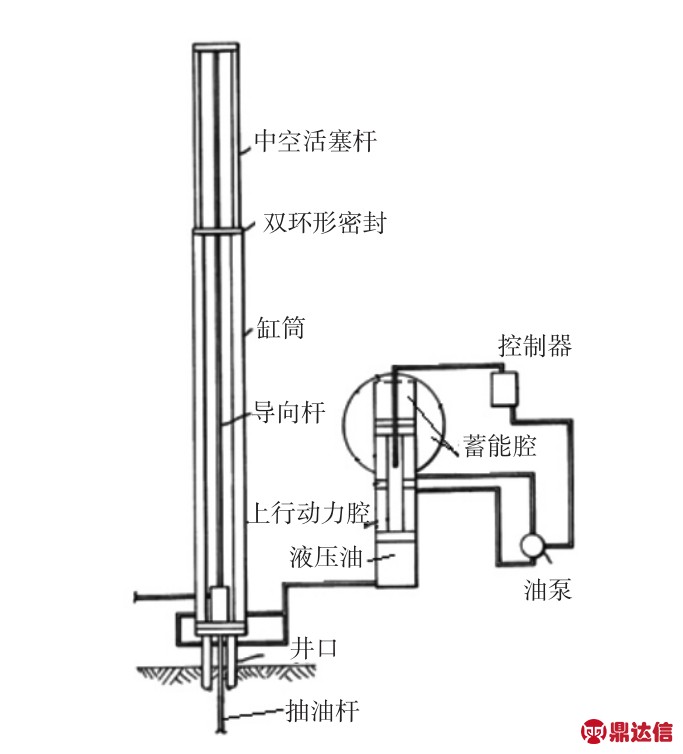
图11998 年加拿大液压抽油机专利结构简图
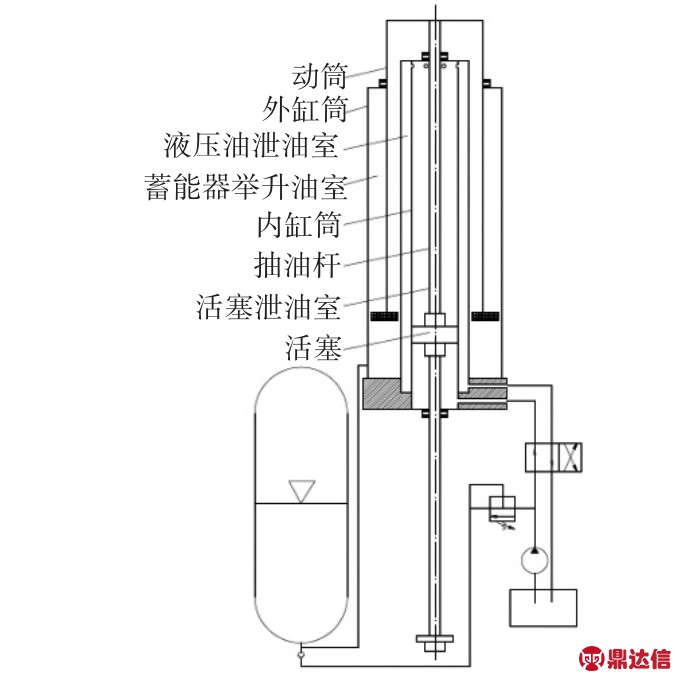
图2 2008年俄罗斯液压抽油机专利结构简图
1 蓄能器在液压抽油机的应用情况
1998年加拿大专利产品(见图1)[1],下行程靠油管自重下行,液压油驱动蓄能缸活塞上行,蓄能腔蓄积重力势能;在上行程时提供辅助动力和动力油泵共同完成油液举升。
2008年俄罗斯专利产品(见图2)[2],下行程靠油管自重下行,液压油被挤进蓄能器,蓄积重力势能;在上行程时提供辅助动力和动力油泵共同完成油液举升。
美国专利产品(见图3),电机、液马达、液压泵同轴布置,称传统型液压变压器,下行程靠油管自重下行,液压缸液压油升压,驱动泵2(马达工况)运行,带动泵1(泵工况)向蓄能器泵压,蓄积重力势能;在上行程时蓄能器高压油驱动泵1(马达工况)运行,提供辅助动力和电机一起共同驱动泵2(泵工况)向液压缸泵油,驱动活塞上行,共同完成油液举升。
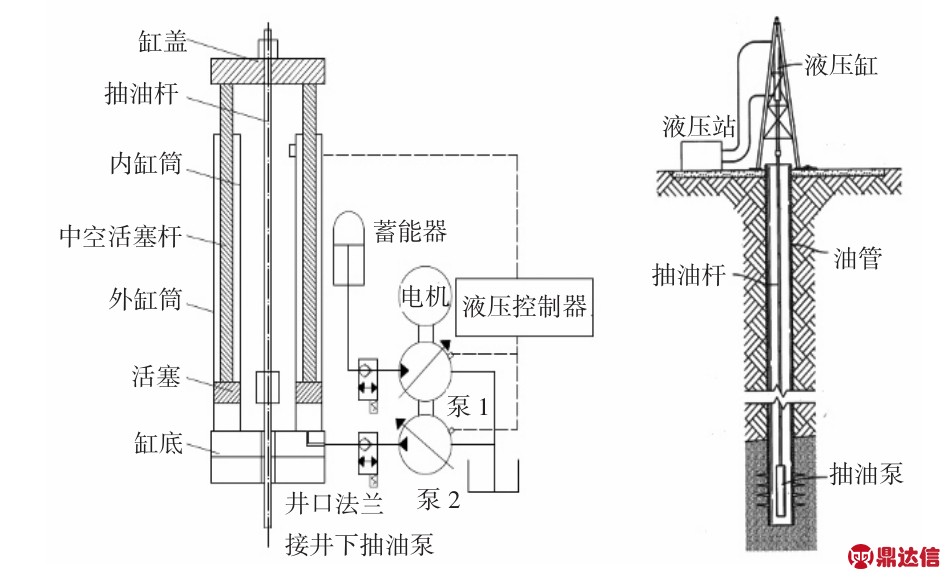
意大利SIVAM公司生产的液压抽油机(见图4),下行程,液压缸活塞在抽油杆及井液的重力势能作用下,使液压油升压,电机驱动液压泵使液压油继续升压,向蓄能缸蓄能P1+P2;上行程,蓄能缸蓄能P1+P2经电机驱动液压泵再次升压至P1+P2+P3,驱动液压缸活塞上行,实现上行程,完成油液举升。
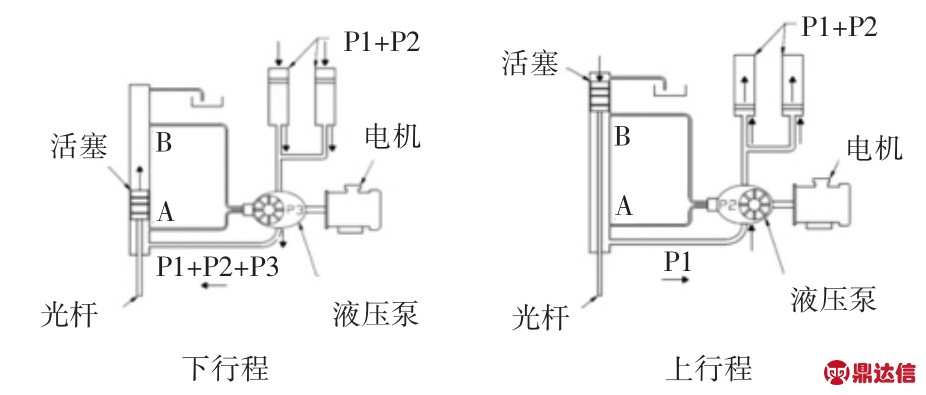
图4 意大利SIVAM公司液压抽油机原理简图
德国Bosch Rexroth持续改进型液压抽油机专利产品(见图5),电机、新型液压变压器(称New Hydraulic Transformer或称液压二次元件、泵马达)同轴布置。新型液压变压器在电气、液压控制器作用下,下行程靠油管自重下行,液压缸有杆腔液压油被加压,驱动新型液压变压器2(马达工况)带动新型液压变压器1(泵工况)泵高有杆腔液压油压,将下冲程能量回收至蓄能器;上行程,蓄能器的储存的能量驱动新型液压变压器1(马达工况)和电机一起驱动新型液压变压器2(泵工况)泵高液压缸有杆腔液压油压,带动活塞上行,完成油液提升。
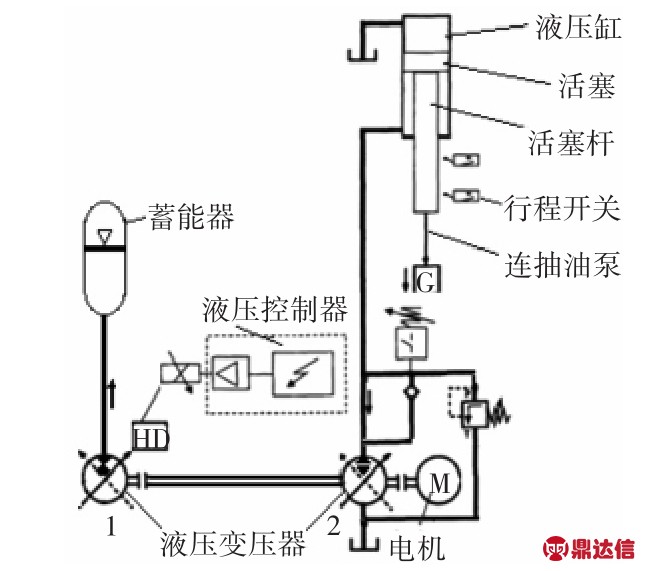
图5 德国Bosch Rexroth液压抽油机持续改进专利结构简图
2 液压抽油机的能量分配原理分析
液压抽油机运行能量分配原理是:下行程蓄积提升系统的重力势能,经过能量转换和液压动力系统共同承担抽油泵提升系统的载荷,完成上行程,如此反复,实现油井油液的提升。下面分析抽油机提升系统的动力分配:
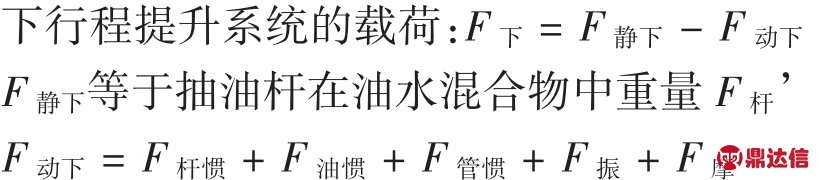
式中,F杆惯为抽油杆惯性载荷;F油惯为抽油泵柱塞上油水混合物惯性载荷(影响较小和悬点加速度有关,但方向相反);F管惯为油管伸缩引起的惯性载荷;F振为油管、油柱对柱塞振动载荷(影响较小);F摩为油管、油柱对柱塞摩擦载荷。
上行程提升系统的载荷:F上=F静上-F动上

式中,F油为抽油泵柱塞上油水混合物重;F压为油管沉没的油柱对柱塞下表面产生方向向上的压力(对于油水井,沉没压力忽略不计)。

从上述计算分析来看,代入具体数值验证,下行程提升系统载荷为上行程抽油泵提升系统载荷的2/3,如何实现下行程提升系统能量的回收与转换成为液压抽油机发展的关键因素。蓄能器储能技术、新型液压变压器、液压控制系统的日益完善,使蓄能器在液压抽油机的应用,再次成为热点。
3 液压抽油机采用蓄能器储能的技术分析
3.1 液压抽油机下行程提升系统的储能分析
由液压抽油机的结构原理分析可知,下行程提升系统的载荷F上=F静上-F动上。
式中,液压抽油机的行程为S;液压抽油机下行程提升系统的储能E=F下·S;液压抽油机正常运行前和正常运行时,蓄能器需液压抽油机下行程提升系统的储能为E.
3.2 液压抽油机下行程提升系统的储能分析
传统液压变压器到新型液压变压器的快速发展,为蓄能器在提升系统的能量回收创造了条件。
液压抽油机启动时,在电气、液压控制器指令下,电动机驱动液压变压器马达泵运行,蓄能器被加压到设定的储能压力,该设定压力为液压抽油机下行程提升系统估算的需要储能量。
液压抽油机正常运行时,在电气、液压控制器指令下,储能蓄能器以一定的储能压力驱动液压变压器泵马达运行,同时和电动机共同驱动液压变压器马达泵运行,泵高液压缸油压,带动抽油泵提升系统完成上行程。这一过程当蓄能器储能压力驱动液压变压器泵马达运行速度低于电动机驱动速度时,电动机单独驱动新型液压变压器马达泵完成上行程。
当达到上行极限位置时,在电气、液压控制器指令下,提升系统下行,液压缸液压油被加压,驱动液压变压器液压泵马达,带动液压变压器液压马达泵持续使蓄能器加压储能。
当达到下行极限位置时,在电气、液压控制器指令下,储能蓄能器以一定的储能压力驱动液压变压器泵马达运行,同时和电动机共同驱动液压变压器马达泵运行,泵高液压缸油压,带动抽油泵提升系统完成上行程。
3.3 液压抽油机提升系统载荷不确定性,蓄能器储能的适应性分析
液压抽油机的冲次取决于液压变压器的能量供应,当上、下行程提升系统的载荷发生变化时,比如油液粘度变化、抽油泵砂卡、杆管接触摩擦等影响上下行载荷,此时液压系统流量保持基本不变,液压系统压力随提升系统的载荷变化,即提升系统的载荷决定了液压系统工作压力。液压系统通过电气、液压控制器自动调节新型液压变压器的自适应节凑,使其能够实现提升系统的载荷变化引起的波动,液压系统适用于频繁往复的变工况,也就是说电气、液压控制器发出指令调节液压变压器出力,协调蓄能器储被加压的储能量化值。
4 蓄能器储能的技术条件
蓄能器储能的技术条件的原理公式:
蓄能器的选取主要由蓄能器的容积和蓄能器的许用工作压力决定。
蓄能器的正常工作压力:P3=F下/A
蓄能器容纳的液体的体积:Vx=lA
式中:A为蓄能器容纳的液体的截面积;l为蓄能器容纳的液体的高度。
设蓄能器在抽油机运行时提供的压力波动控制在10%以内,则由手册[3]可查得蓄能器工作时的压力关系,可得到:
蓄能器回路的最小工作压力:Pmin=0.9P3;蓄能器回路的最大工作压力:Pmax=1.1P3;蓄能器的充气压力:P0=0.85Pmin;
蓄能器的工作过程按等温过程计算,则所需的蓄能器的容积为:
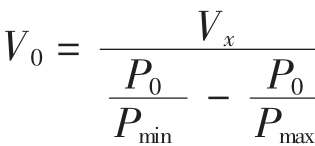
5 新型液压变压器的出现为蓄能器储能的创造了技术条件[3-4]
液压变压器是在液压系统中用来实现压力改变的液压元件,传统型液压变压器是将电机、液压泵和液马达通过联轴器机械连接组成的。
新型液压变压器是随着恒压二次调节技术从节能的角度发展而产生的,二次元件马达和泵之间所接的蓄能器消除了二者之间流量和功率的直接联系,是液压能和机械能互相转换,这使得功率储存和回收成为可能,理论上能无节流损失地传送液压能,能巧妙地将液压泵和液马达功能集成于一体,能同时控制负载压力和流量的控制元件,具有结构简单、体积小、效率高、惯性小、动态响应快等优点。
液压变压器在压力耦联的恒压网络系统中无节流损失地获取能量,而且可以接多个互不相关的负载,来控制调节液压执行元件及负载的运动,包括旋转载荷和直线载荷,动态性能好,控制性能好,能够自适应负载的变化,能对恶劣的工作条件达到快速匹配,同时实现系统制动能和重力势能、负载能量的回收与重新利用,应用前景十分广阔。
新型液压变压器的调节原理:
相对于液压阀控制的传统型液压变压器而言,新型液压变压器在液压控制器作用下,理论上没有节流损失,具有良好的节能效果,其调节原理如图6所示。
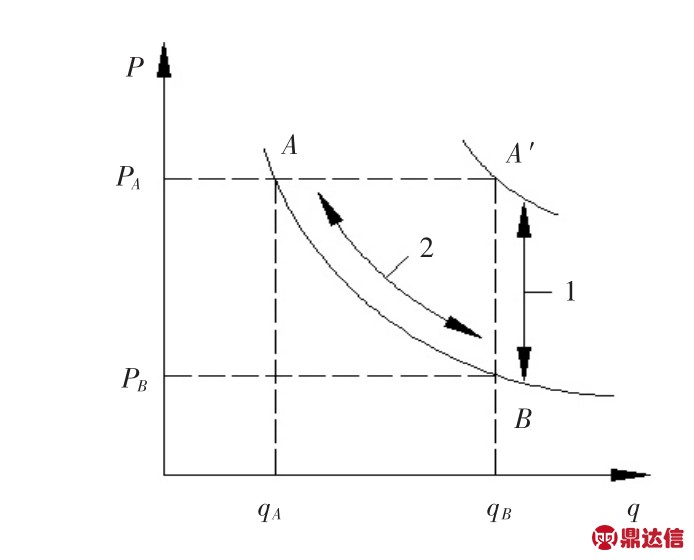
图6 液压系统的压力-流量曲线
当需要将恒压网络系统的压力PA调节到PB时,如果用液压阀控制的传统型液压变压器来调节,则按路径1进行,压力降低了,而流量没改变,能量损失为:

如果采用液压控制器控制新型液压变压器,则按路线2进行调压,即流量改变,压力也改变,忽略管路损失,符合能量守恒方程:
PAqA=PBqB
由此可见,在恒压网络中采用液压控制器控制新型液压变压器来调压,与液压阀控制的传统型液压变压器调压相比,理论上没有能量损失,尤其在大流量,大功率系统中,具有独特的优势。
其变压原理与传统变压器的变压原理一样,也是通过改变排量的比值来实现变压比的改变。
新型液压变压器的变压比λ为输出压力与输入压力的比值:
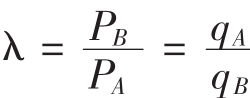
新型液压变压器流量为:
q=VA·n
式中:n为变压器转速;VA为变压器处于A位置的排量;VB为变压器处于B位置的排量,则:
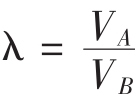
由此可知,液压控制器在电气控制系统的调控下,适当改变新型液压变压器的排量及方向就可以控制调节液压执行元件及负载的运动,回收负载的能量,同时能实现能量量化调节。
6 蓄能器储能在液压抽油机的应用前景
液压抽油机的突出特点是:(1)大幅度降低抽油机装机功率;(2)长冲程、大载荷、能耗低、自适应性好;(3)冲程冲次调节便捷,易于实现无级调,上下行程速度可分别调节,能很好地适应井况的变化;(4)启停更加平稳,启、停电流小,减少对电网冲击;(5)安全性能高;(6)可减小抽油机体积、质量和占地面积;
利用蓄能器储能的液压抽油机特点有:(1)储能响应快,蓄能器被加速时间可控;(2)释能反应快,蓄能器降速量化控制;(3)井液量不断变化的趋势有较好适应性;(4)高效节能。
随着新型液压变压器、液压系统及液压二次调节控制系统的不断升级完善,加上蓄能设施不断改进,使用寿命逐步延长,进入20世纪10年代,液压抽油机迅速进入量产的工业化时代。