摘要:针对液压再生制动系统的能量回收效率和制动安全性问题,对汽车液压再生制动系统的参数匹配进行了研究。建立了液压制动能量回收系统试验台,进行了蓄能器初始压力变化、系统最高压力变化、蓄能器总体积变化的实验研究;建立了液压再生制动系统试验台数学模型,基于Matlab/Simulink建立了液压制动能量回收系统的仿真模型,并进行了与台架相对应的仿真实验,研究了液压制动能量回收系统的能量回收效率;对液压制动能量回收系统进行了整车研究,采用ADAMS/car建立了某车型整车,并与Matlab进行了仿真研究。首先研究了液压制动能量回收系统单因素对能量回收效率和制动安全性的综合影响,其次采用正交实验法研究了多因素对能量回收和制动安全性的综合影响。研究结果表明,合理的液压制动能量回收系统参数能够显著提高能量回收效率和制动安全性。
关键词:Matlab/Simulink;ADAMS/Car;单因素;多因素;对比实验;优化设计
0 引 言
蓄电池、电机/发动机组成的再生制动系统,虽然能量密度高,但功率密度低,限制了制动能量的回收。而由蓄能器、泵/马达组成的液压再生制动系统,不仅成本较低,而且功率密度高,能量密度适中。在城市制动频繁的道路上行驶,如装备高功率密度的液压再生制动系统,则制动能量回收更有效。并联式液压制动能量回收系统是在不改变传统汽车底盘布局的前提下,通过耦合器并联一套液压系统到原传动系上。由于其节能环保、改动简单以及造价成本低的特点,它作为一种新的动力混合形式受到关注。R.P.Kepner[1]设计了液压再生制动系统,将液压系统组装到福特皮卡上,并与美国环境署合作,实验测得液压再生制动系统的汽车燃油消耗量显著减少,且尾气排放的有害气体也明显减少;Young Jae Kim and Zoran Filipi[2]以轻型卡车为对象,进行了制动能量回收的仿真研究,研究结果表明纯市区燃油消耗量节省约48%~65%,纯高速燃油消耗量节省约11%;Hiroki Shimoyama, Shigeru Ikeo and Eitaro Koyabu等人[3]对恒定压力的液压再生制动系统进行研究,并进行了相关实验,仿真和实验研究均表明能量回收效率均在73%左右;谢峰,刘昕晖[4]对液压再生制动系统的动力性匹配进行研究,并搭建相关实验台架进行实验,实验结果为整车参数匹配提供依据;刘涛,刘清河和姜继海[5]对再生制动影响因素进行研究,通过理论分析和仿真研究,表明驱动方式、耦合器耦合比和蓄能器相关参数对能量回收均有较大影响;王海飞,孔燕,徐飞宁,贾坤坤[6-7]研究了二次元件的排量对能量回收的影响,使回收的能量最大化;王国海,韩以伦[8]匹配了动力系统部件各参数,采用正交试验设计方法对这些参数进行优化,节能效率提高了21.6%;黄梦阳,吴涛[9]研究了蓄能器的储能状态对工况的影响。
本研究分析蓄能器多个参数对能量回收效率和制动安全性能的综合影响,进行仿真和台架的对比实验,并用ADAMS-car和Simulink进行整车联合仿真分析。最后,用正交优化实验法对参数进行优化,得出最优参数组合,为整车实验提供依据。
1 并联式液压制动能量回收系统的原理和数学模型
并联式液压制动能量回收系统的工作原理可以归纳为:当汽车制动时,利用汽车中的传动轴带动泵/马达旋转,此时泵/马达以液压泵的形式工作,将液压能储存在液压蓄能器中。当汽车启动、加速时,泵/马达以马达的形式工作,其将蓄能器中的液压能转化为汽车的动能,协助发动机给汽车提供能量。其原理图如图1所示。
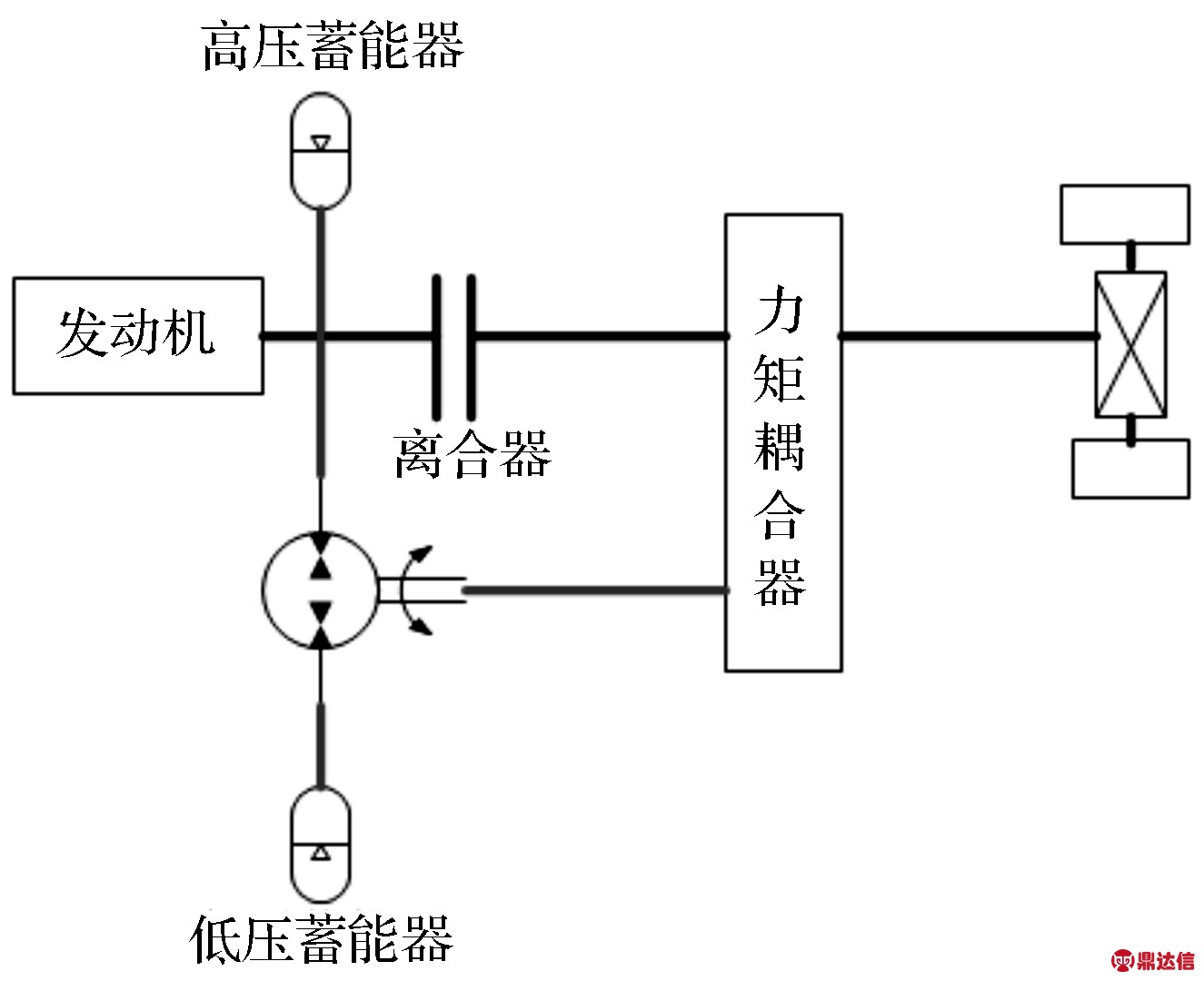
图1 并联式液压再生制动系统原理图
本研究建立了液压再生制动系统试验台架,采用飞轮模拟汽车动能,试验台原理如图2所示。
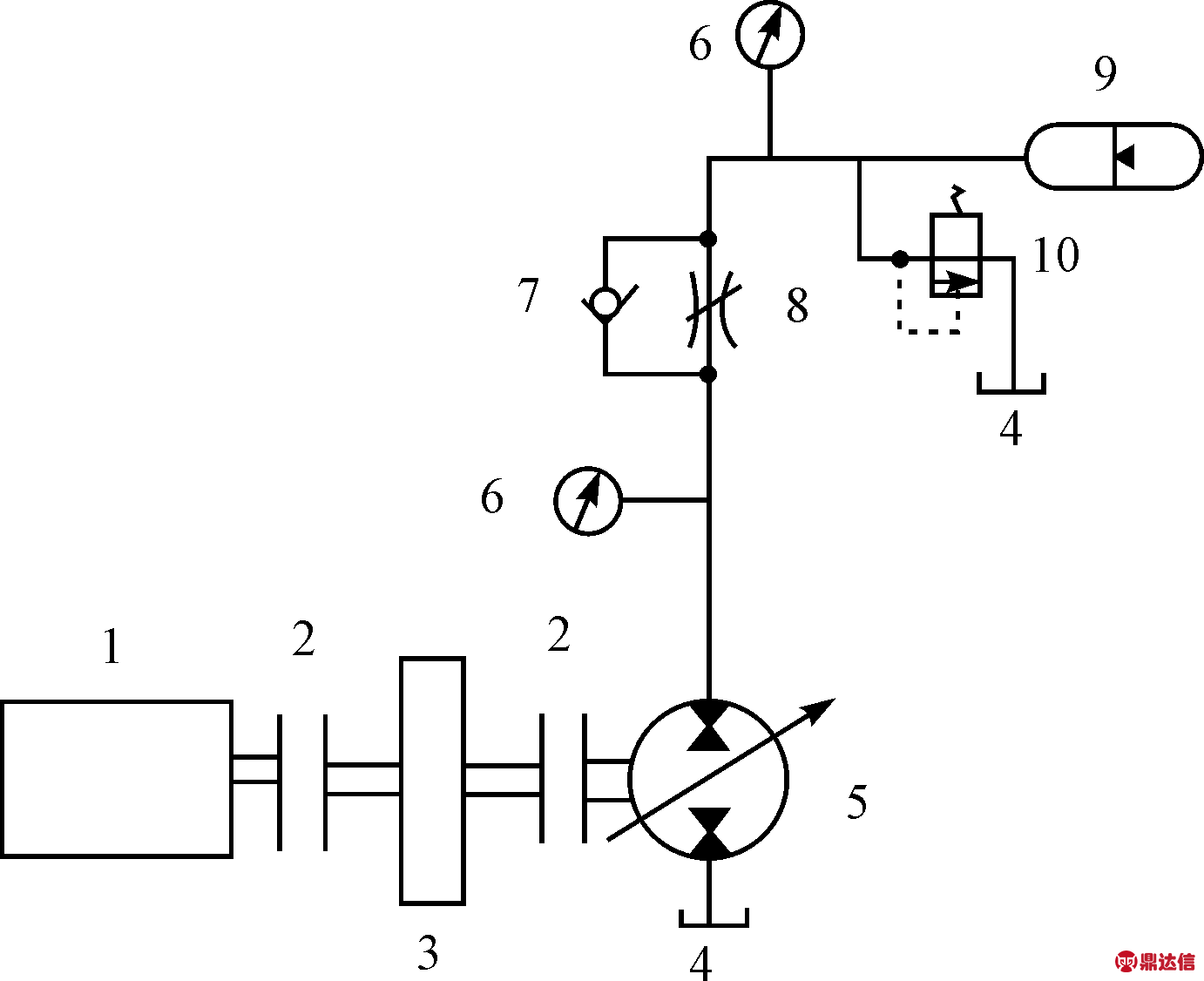
图2 液压再生制动系统实验台架原理图
1—电机;2—电磁离合器;3—飞轮;3—油箱;4—变量泵/马达;5—压力计;6—单向阀;7—节流阀;8—蓄能器;9—溢流阀
1.1 飞轮
在图2中,电机1带动飞轮3旋转,当飞轮3达到设定的稳定转速后,断开与电机连接的离合器2,结合与液压泵/马达连接的离合器2,飞轮3带着液压泵5转动。根据转矩建立飞轮模型,有:
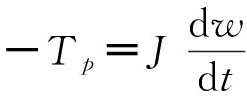
(1)
式中:Tp—泵对蓄能器的转矩,J—飞轮的转动惯量,w—飞轮的角速度。
1.2 二次元件液压泵/马达
根据功率建立二次元件数学模型[10]:
PQ=T飞轮W飞轮η
(2)
式中:P—二次元件出口油压力,Q—二次元件的流量,T飞轮—飞轮的制动力矩,W飞轮—飞轮的旋转角速度,η—传动效率。
其中:
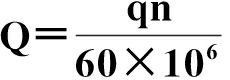
(3)
式中:q—二次元件的排量,n—二次元件的转速。
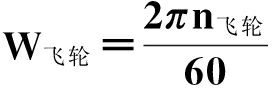
(4)
式中:n飞轮—飞轮的转速,r/min。
将式(2,3)代入式(1)中,可得:
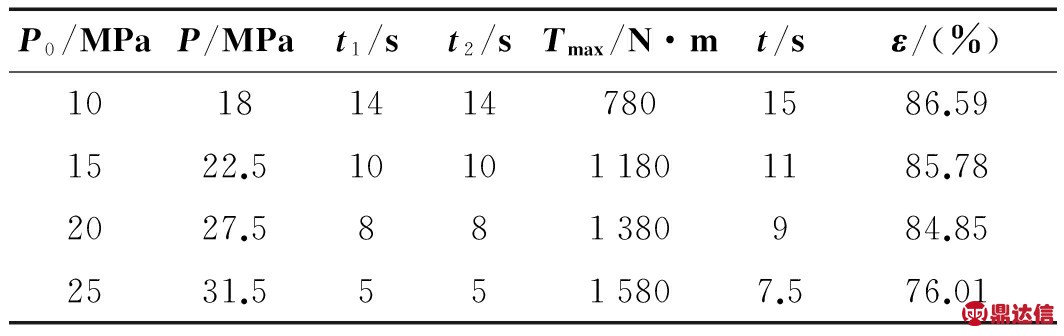
(5)
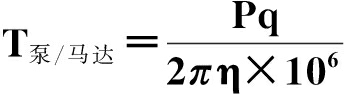
(6)
1.3 蓄能器模型
笔者选择气囊式蓄能器。由Boyle定律可知:

(7)
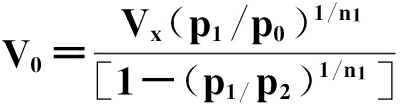
(8)
式中:P0—蓄能器初始充气压力;P1—系统最低工作压力;P2—系统最高压力;n1—多变指数;V0,V1,V2—对应压力的蓄能器气体体积;Vx—蓄能器有效容积。
为了简化实验,在此假设蓄能器在压缩和释放的过程中是绝热状态[11-15],所以n1取1.4;在实验过程中油液是不可压缩的。蓄能器在最低工作压力时,要保证足够的制动力,以确保飞轮可以在短时间内停止,因此:
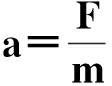
(9)
T飞轮=F×r
(10)
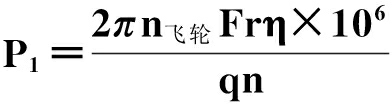
(11)
式中:F—液压泵/马达所受的制动阻力,m—飞轮质量,r—飞轮半径。
由经验得到:P1=(0.6~0.85)P2,所以蓄能器制动回收的能量为[10]:
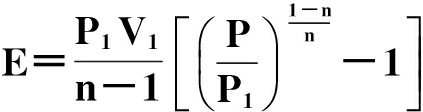
(12)
式中:P—蓄能器最终压力。
能量回收的效率:
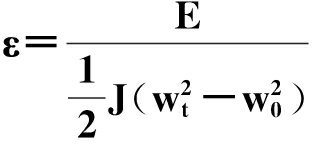
(13)
式中:w0—飞轮初始转速,wt—飞轮最终转速。
飞轮最后是停止的,取wt=0。这样能量回收的效率可简化为:
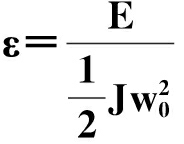
(14)
2 仿真数据和实验数据对比分析
2.1 仿真模型
在Matlab/Simulink中,本研究建立与试验台一致的模型,仿真模型由蓄能器、泵/马达、三位四通电磁阀等液压元件,传感器以及耦合器组成,一起控制飞轮的运行。液压再生制动仿真模型如图3所示。
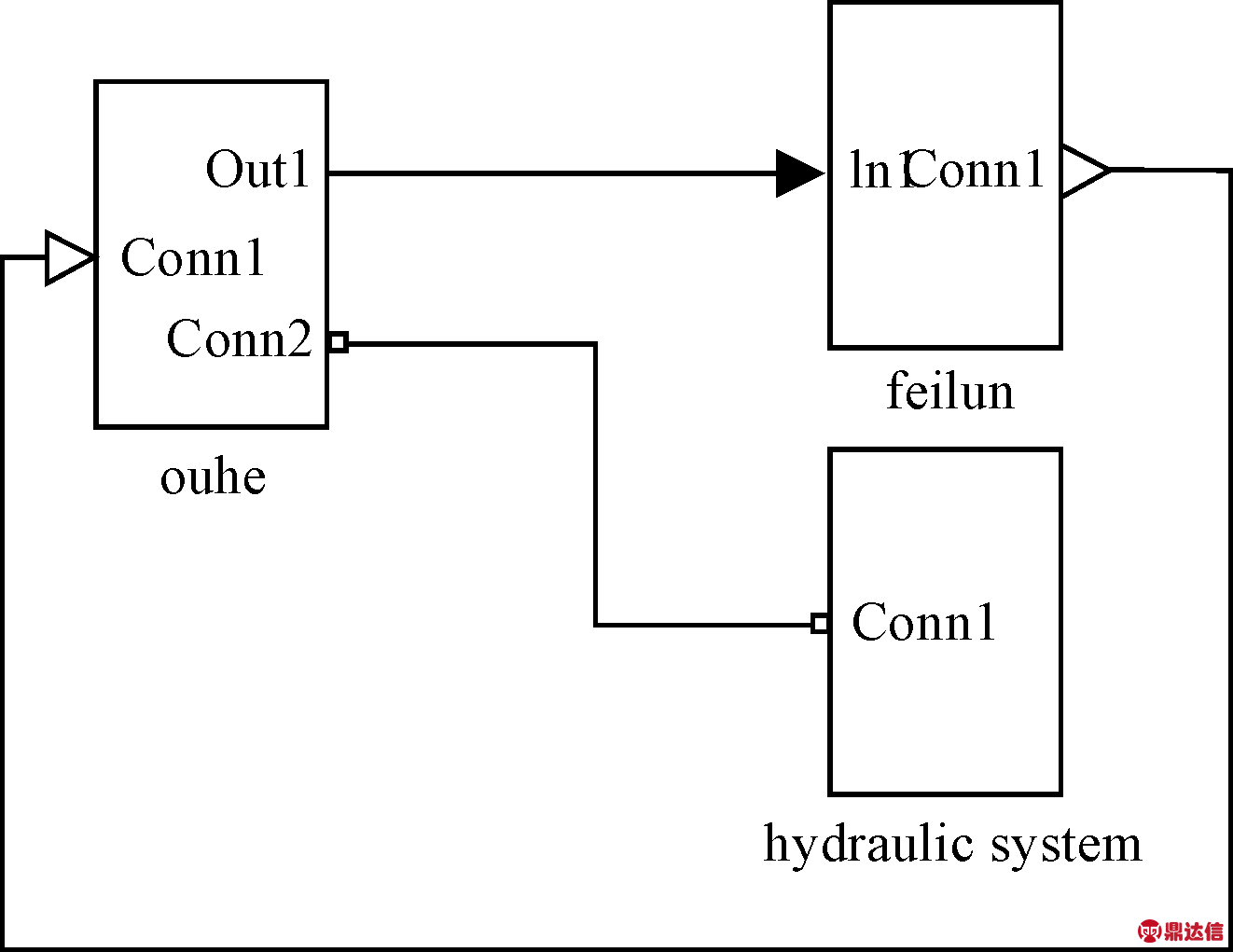
图3 台架试验原理仿真模型
feilun—飞轮仿真模型;ouhe—耦合器仿真模型;hydraulic system—液压系统仿真模型
2.2 实验台架
主要元件的参数如表1所示。
表1 台架主要硬件参数
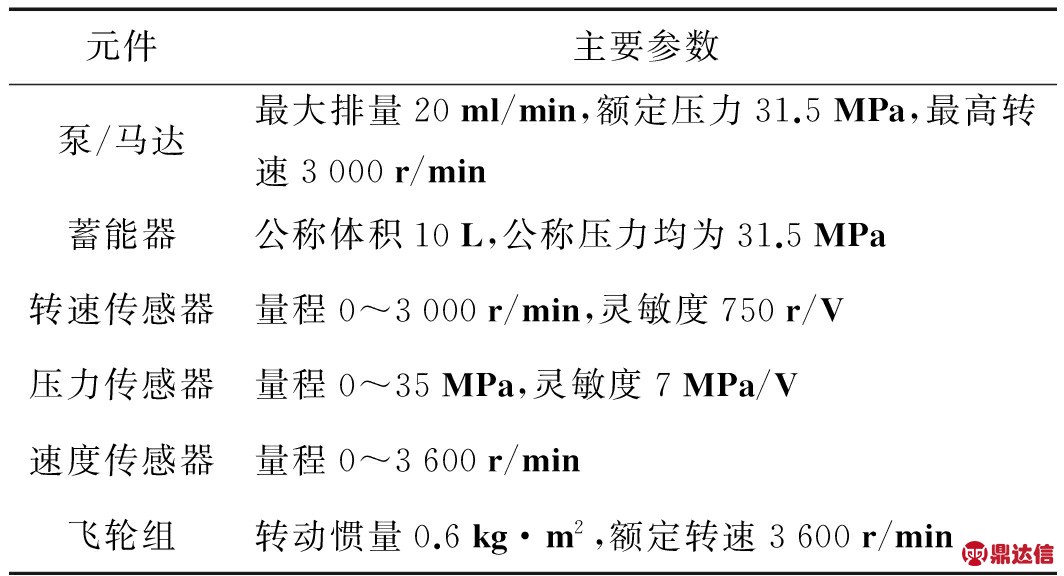
压力传感器,转速传感器,USB2812数据采集卡如图4所示。
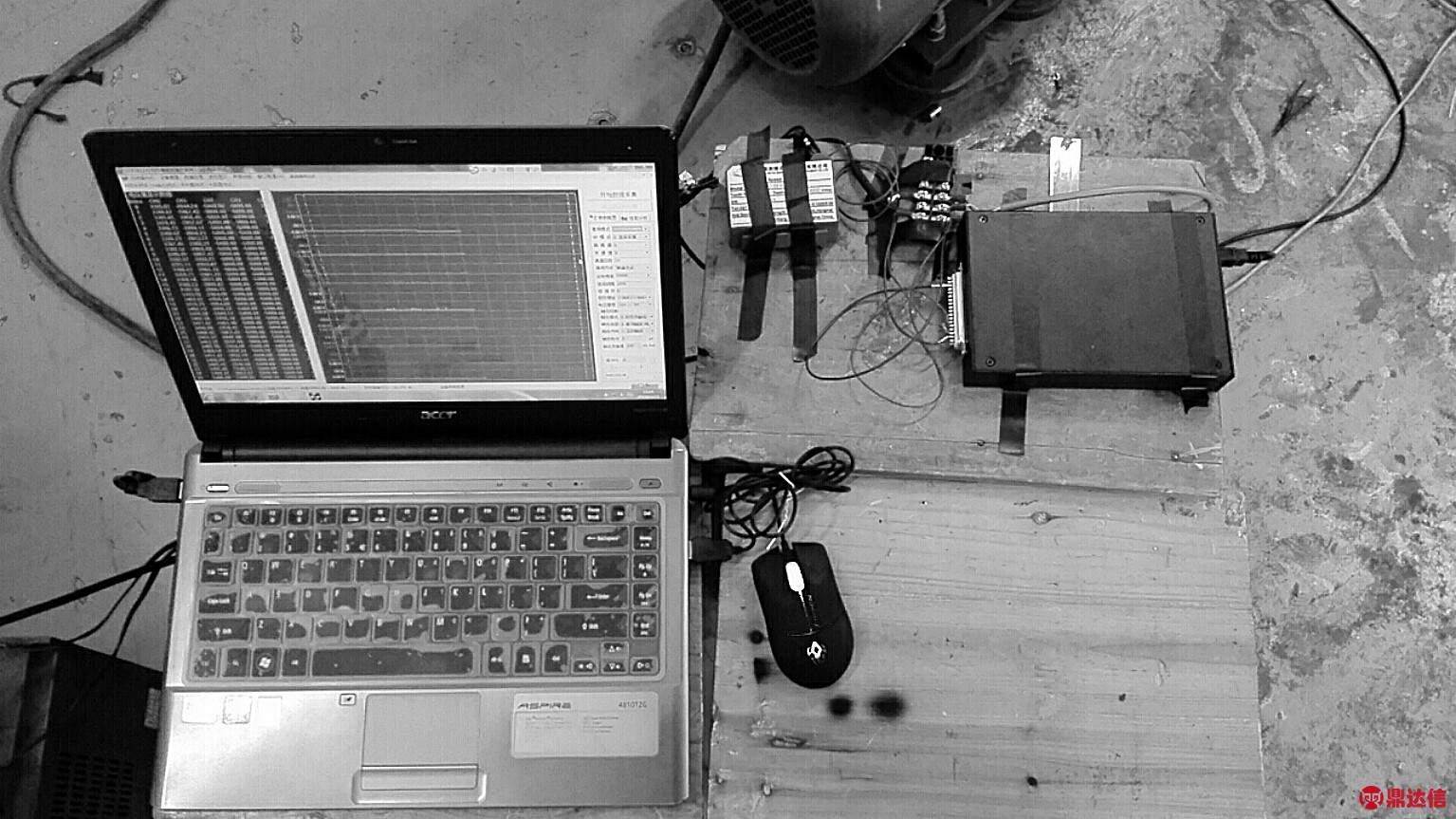
图4 动态信号采集系统
台架如图5所示。
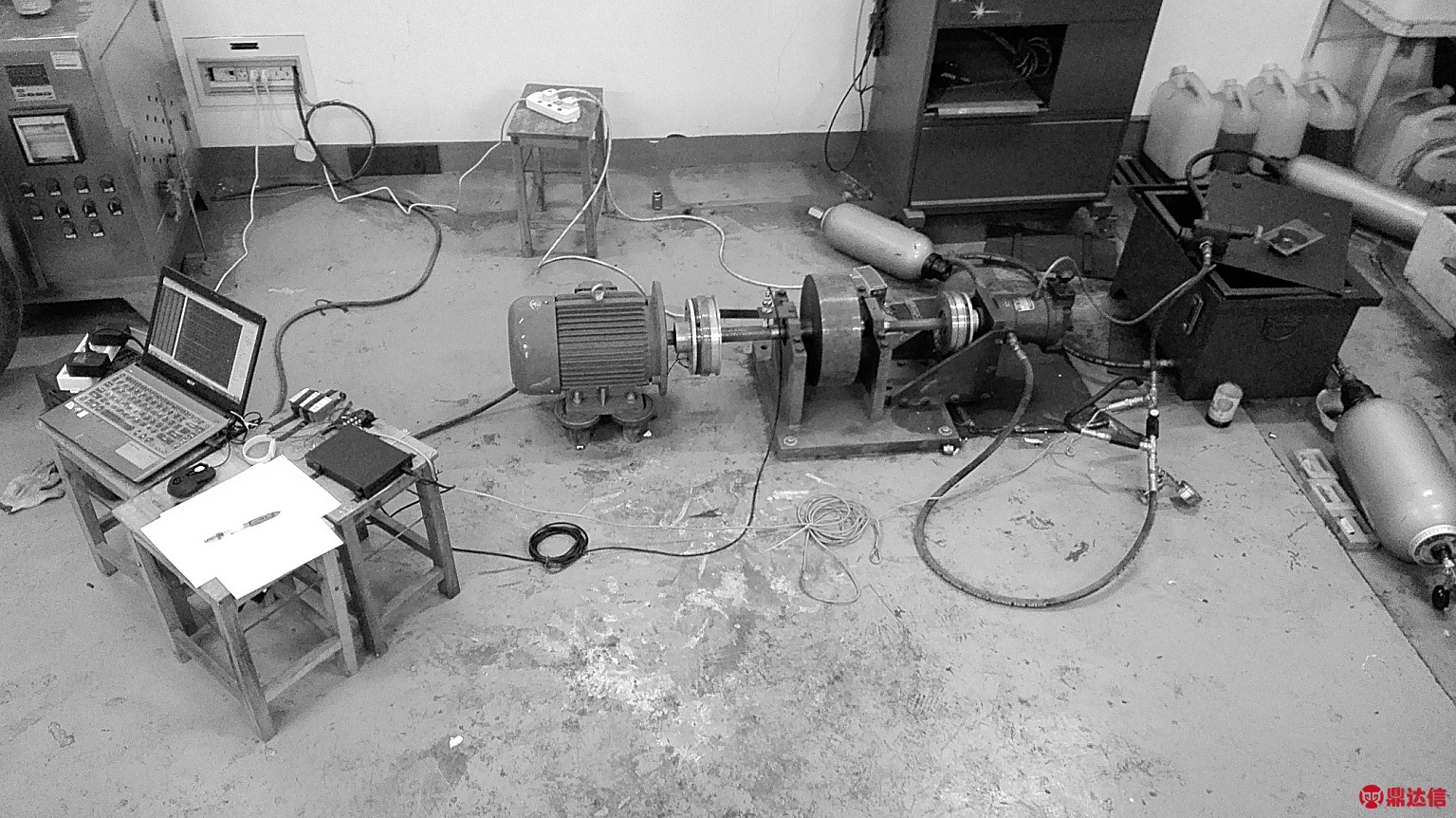
图5 液压再生制动系统实验台架图
2.3 台架与仿真对比实验
2.3.1 泵/马达排量不同的对比实验
电机带动飞轮旋转,当飞轮达到设定的实验初始值后,断开与电机连接的离合器,结合与泵/马达连接的离合器,液压泵被飞轮带着转动,同时对飞轮液压制动。
实验一:在蓄能器体积为10 L、蓄能器的初始压力为4 MPa、系统最高压力为31.5 MPa、飞轮初始转速为3 000 r/min时,进行泵/马达排量分别为6 ml/r、8 ml/r、10 ml/r共3种不同情况的仿真。蓄能器压力仿真结果如图6所示。
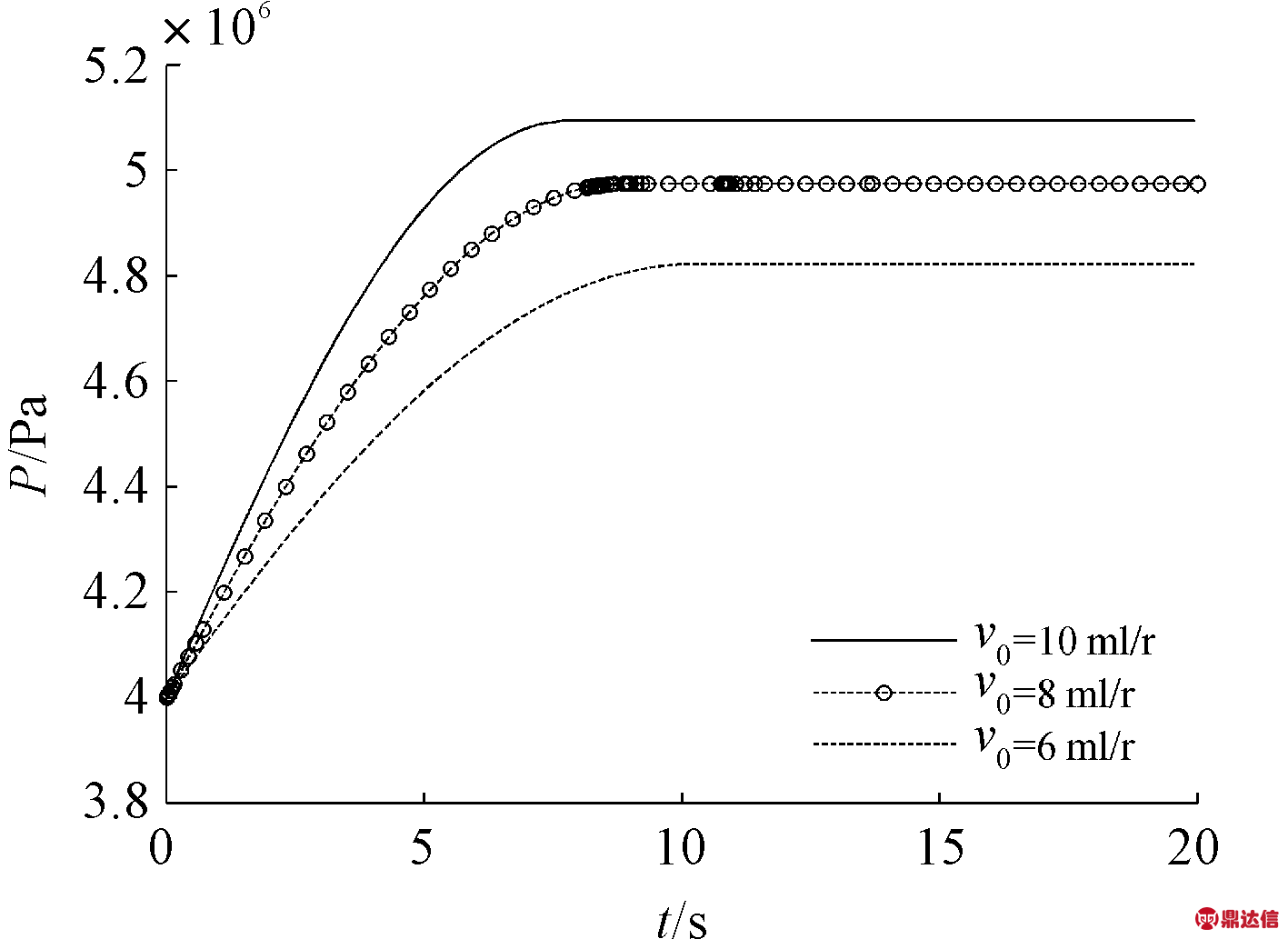
图6 蓄能器压力(仿真)
蓄能器压力实验结果如图7所示。
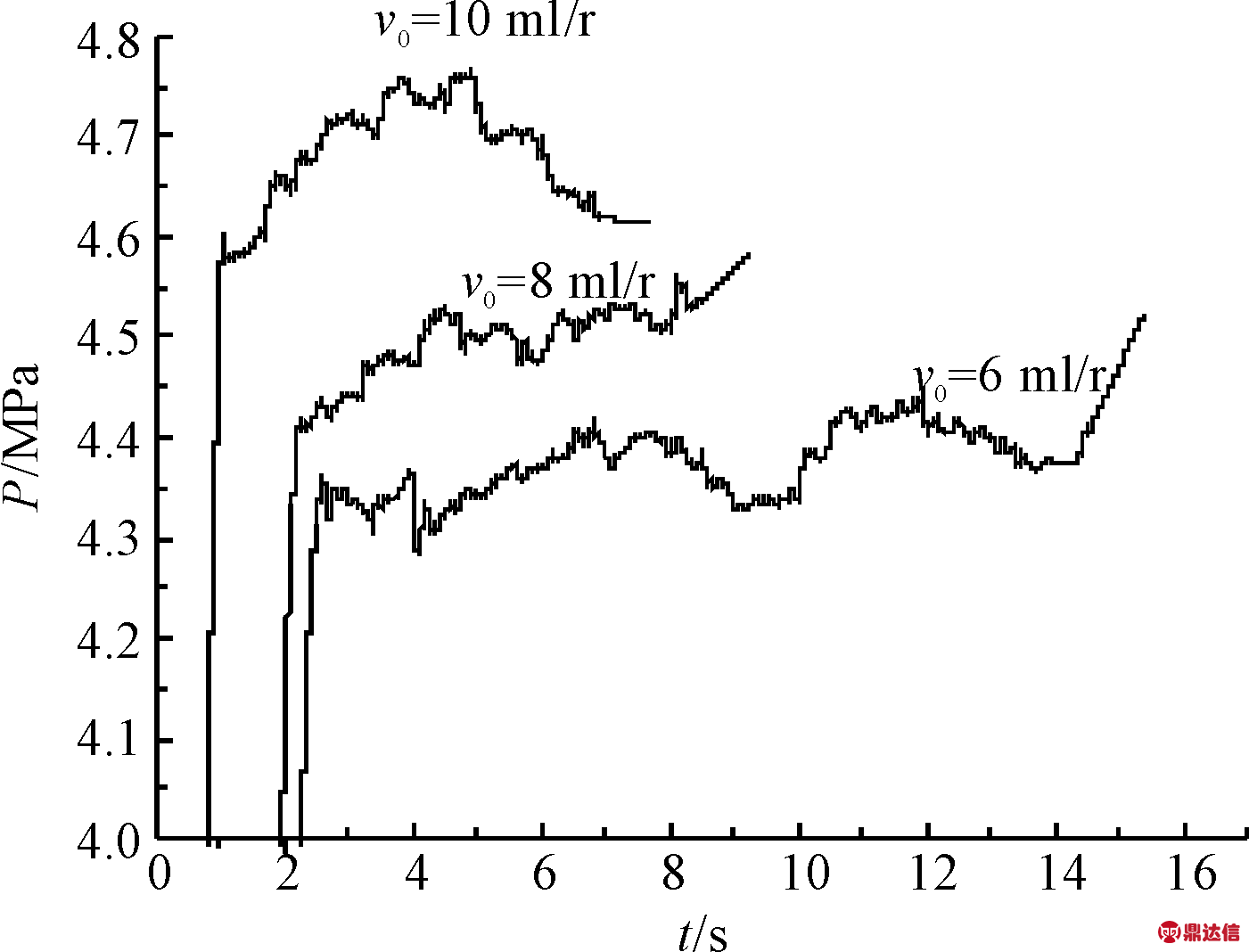
图7 蓄能器压力(实验)
从图6可以看出,蓄能器最终压力分别约为4.7 MPa、4.9 MPa、5.1 MPa。从图7可以看出,蓄能器最终压力分别约为4.35 MPa、4.5 MPa、4.7 MPa。随着泵/马达排量的增大,仿真和实验中,蓄能器最终压力都呈增大趋势。
仿真和实验压力起点差异说明:由于在台架试验中,液压管路比较长,管路的压力要过一段时间才能达到蓄能器初始压力。因为初始条件不同,这个时间又是不固定的,从而才出现图7所示的情况。
飞轮转速仿真结果如图8所示。
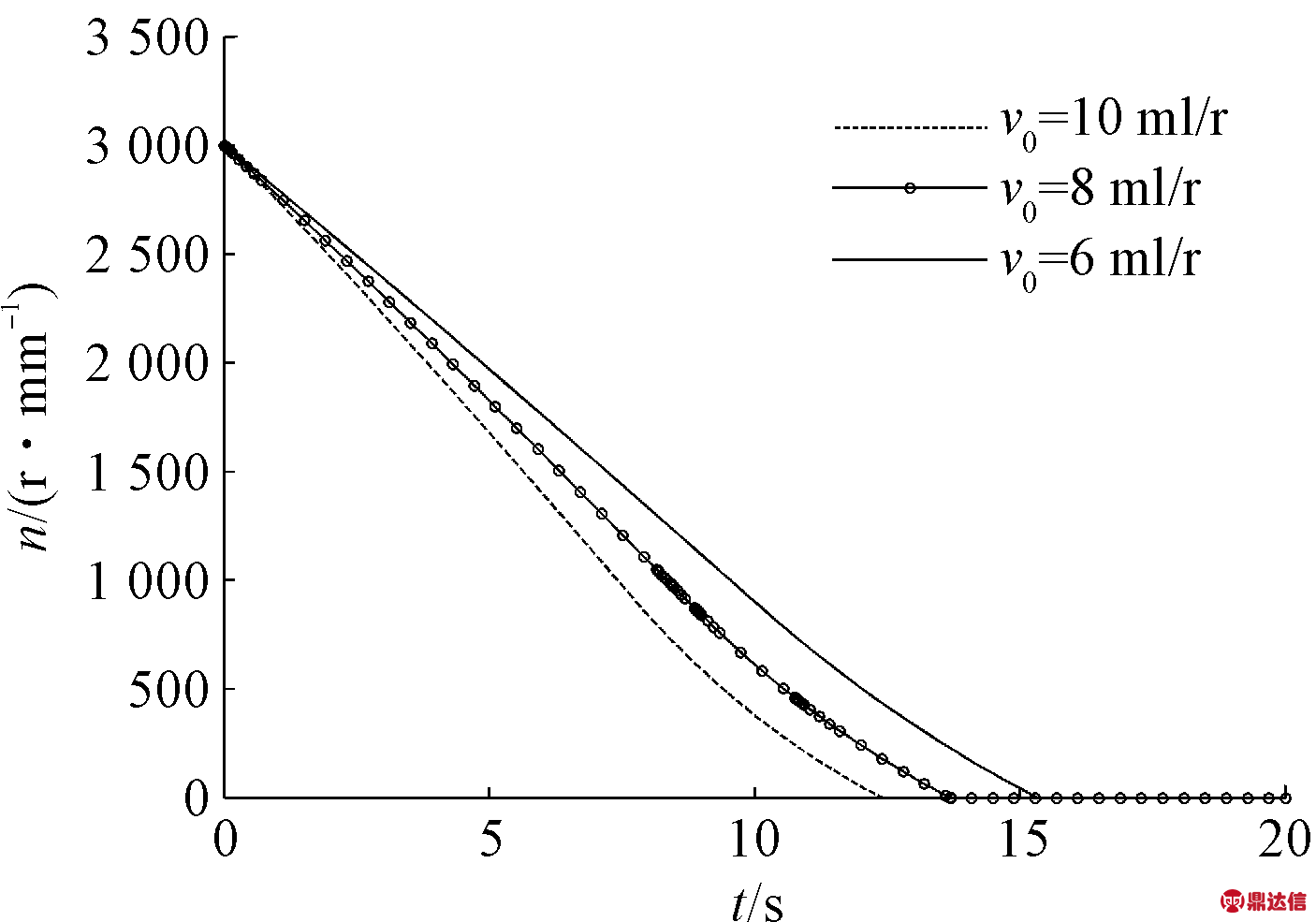
图8 飞轮转速(仿真)
飞轮转速实验结果如图9所示。
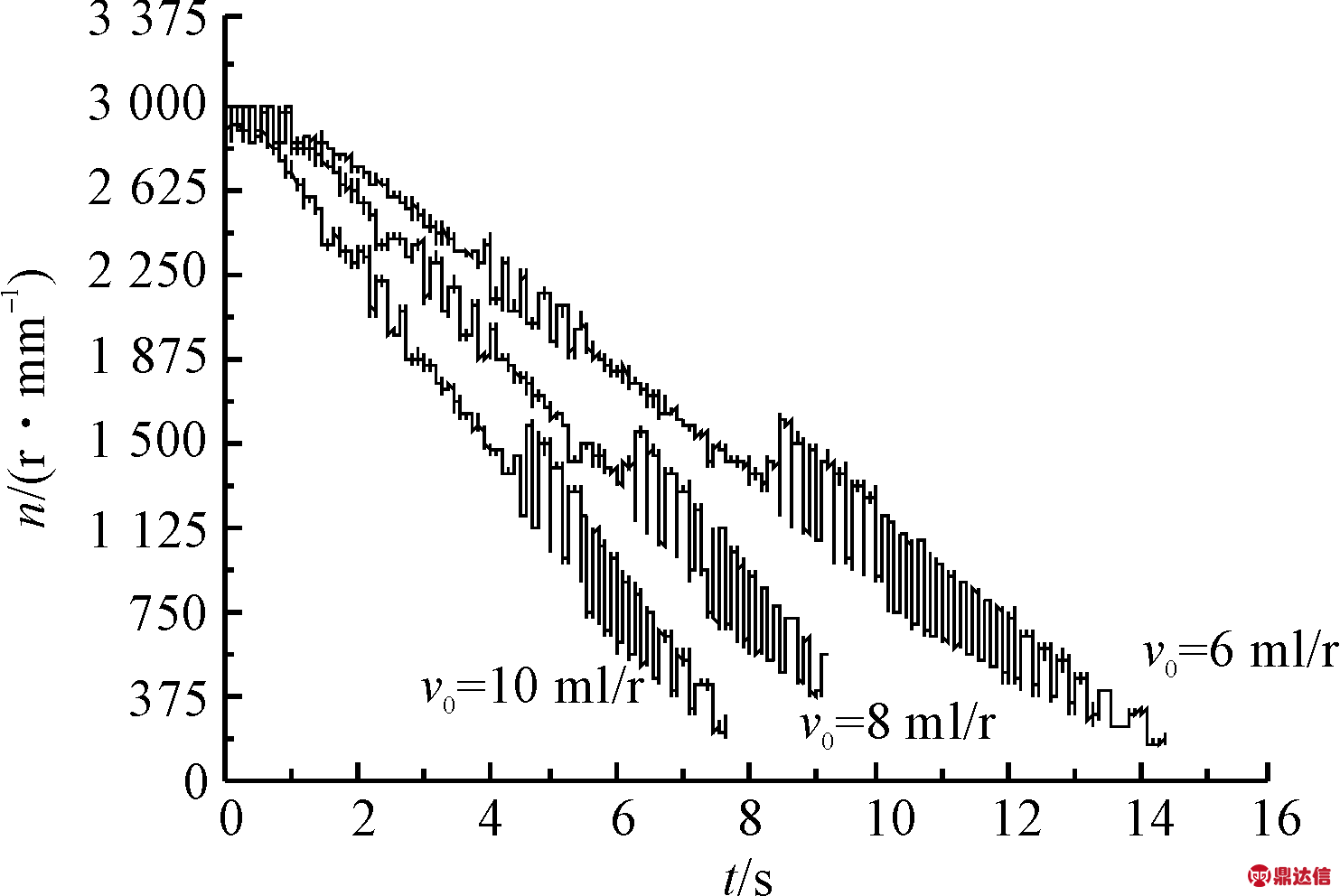
图9 飞轮转速(实验)
从图8可以看出,飞轮停止时间分别约为16 s、14 s、12 s。泵/马达排量变大,由公式(5)得液压泵阻力力矩变大,飞轮停止时间变短。由图9可以看出,飞轮制动时间分别为14 s、10 s、8 s。随着泵/马达排量的增大,仿真和实验中,飞轮的制动停止时间都呈减小趋势。
2.3.2 蓄能器初始压力不同的对比实验
实验二:在飞轮转速为3 000 r/min、蓄能器体积为10 L、系统最高压力为31.5 MPa、泵排量为10 ml/r,进行蓄能器初始压力分别为3.5 MPa、3.8 MPa、4.0 MPa共3种不同情况的仿真。结果如图10所示。
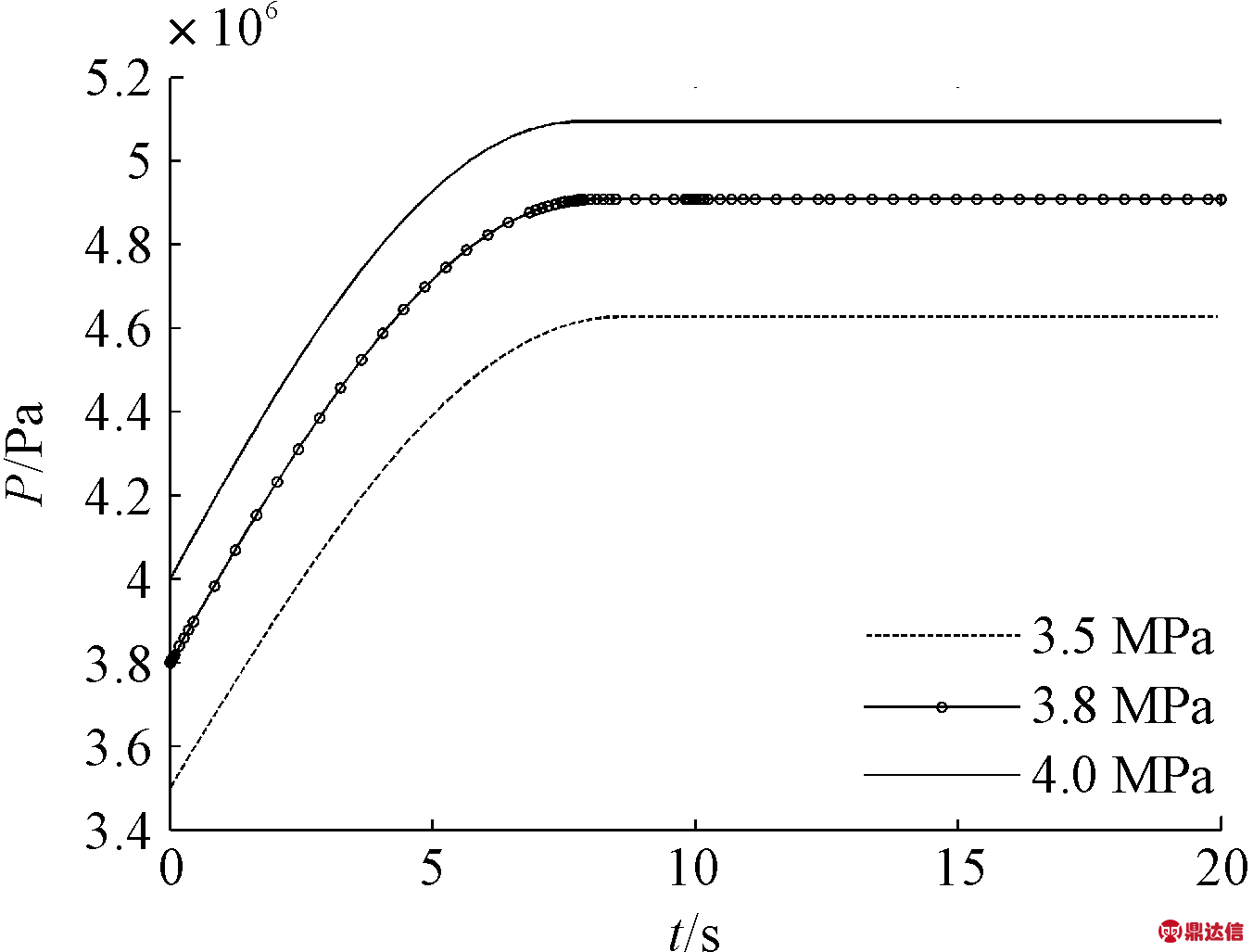
图10 蓄能器压力(仿真)
蓄能器压力实验结果如图11所示。
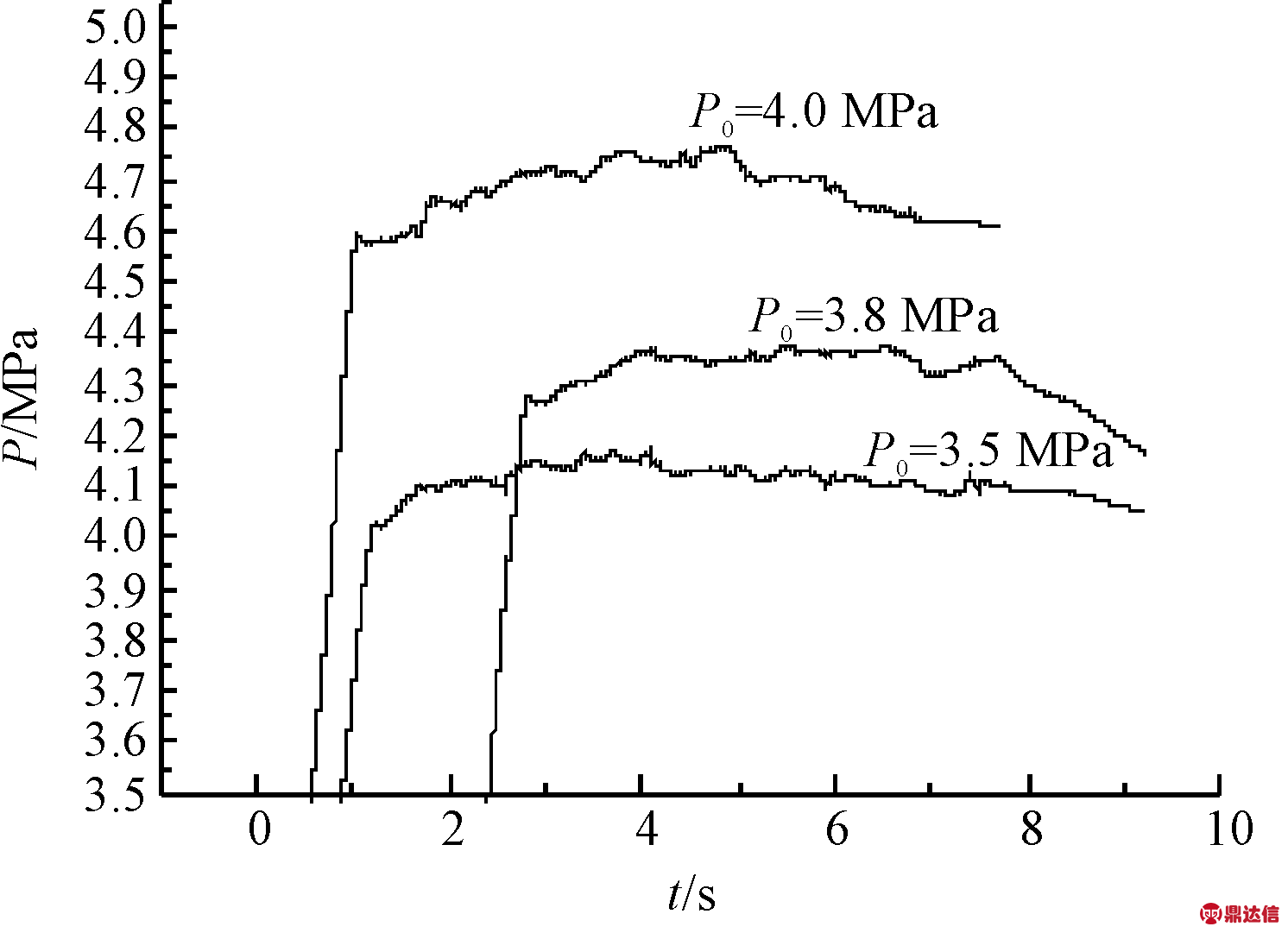
图11 蓄能器压力(实验)
从图10可以看出,蓄能器最终压力分别约为4.58 MPa、4.9 MPa、5.1 MPa。从图11可以看出,蓄能器最终压力分别约为4.1 MPa、4.35 MPa、4.75 MPa。随着蓄能器初始压力的增大,仿真和实验中,蓄能器最终压力都呈增大趋势。
飞轮转速仿真结果如图12所示。
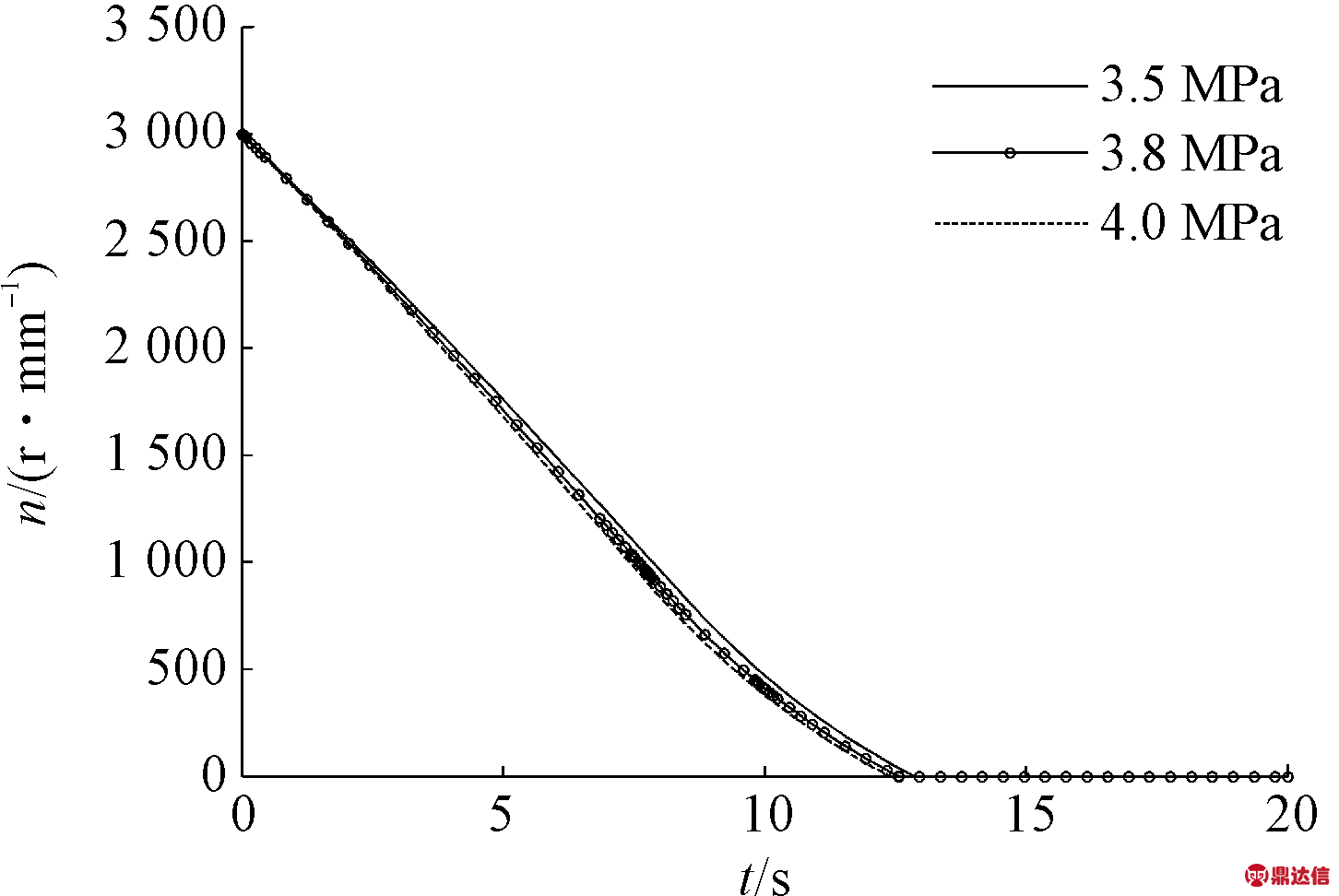
图12 飞轮转速(仿真)
飞轮转速实验结果如图13所示。
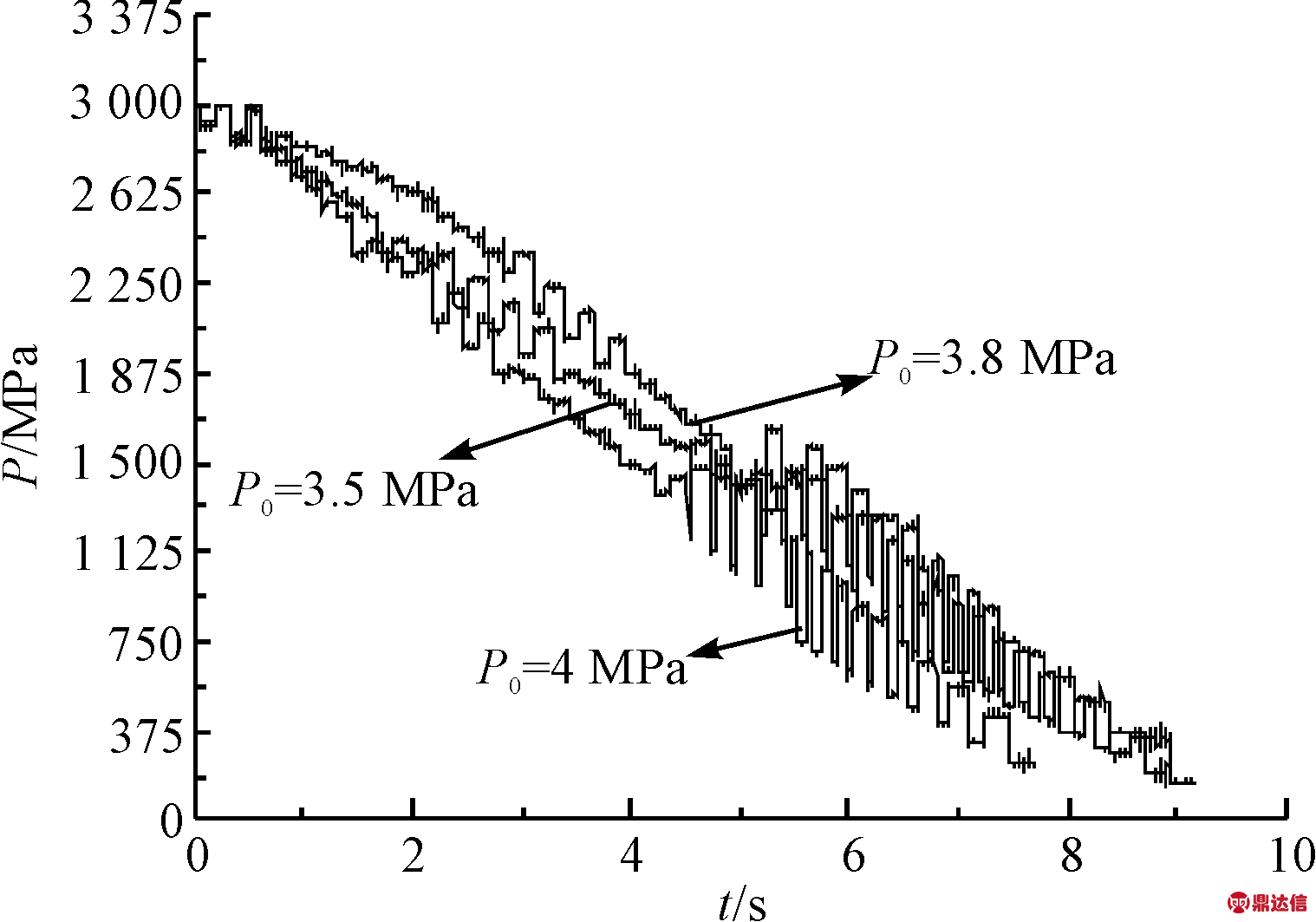
图13 飞轮转速(实验)
从图12可以看出,飞轮制动时间分别约为13 s、12.5 s、12 s。蓄能器初始压力变大,由公式(5)得液压泵阻力力矩变大,飞轮停止时间变短。从图13可以看出,飞轮制动时间分别约为9.2 s、9 s、8 s。随着蓄能器初始压力的增大,仿真和实验中,飞轮的制动停止时间逐渐减小。
综合实验一、二得,实验台架存在摩擦,所以实验数据略小于仿真数据,但仿真趋势与实验趋势一致,液压仿真模型计算结果与实验相符。
3 整车联合仿真
3.1 整联合仿真模型
本研究采用ADAMS/Car软件搭建了某车型模型。系统模型在Matlab下的SimHydraulic模块中建立,主要由蓄能器、泵/马达、三位四通电磁阀等液压元件,传感器以及耦合器组成。液压再生制动模型如图14所示。
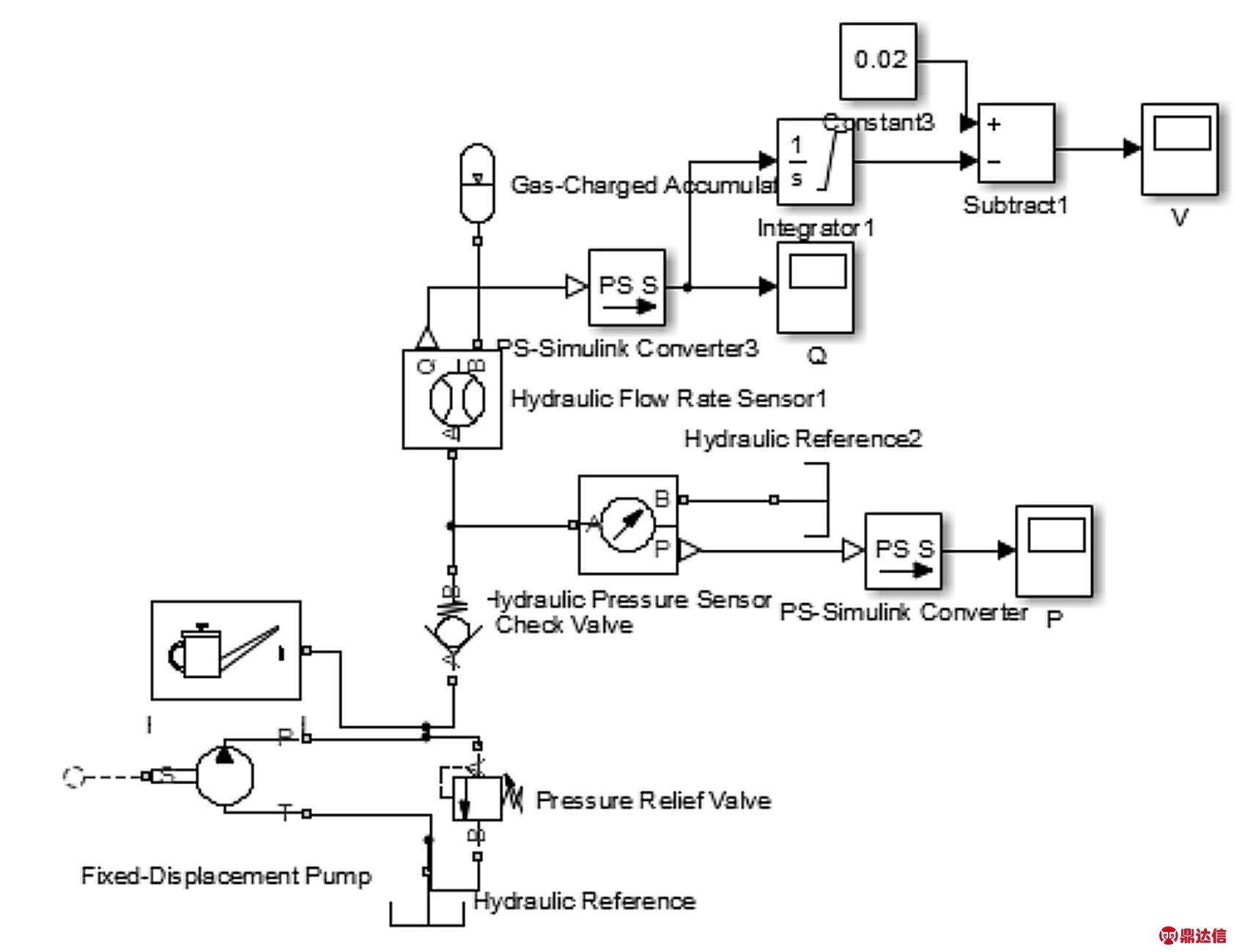
图14 液压再生制动系统
整车主要参数如表2所示。
表2 整车参数

3.2 整车仿真实验
仿真中不变因素:泵/马达排量为30 mL/r、汽车初始车速为60 km/h。
3.2.1 蓄能器初始充气压力变化
本研究在蓄能器总体积为55 L、系统最高压力P2为31.5 MPa时,分别进行蓄能器初始压力P0为10 MPa、15 MPa、20 MPa、25 MPa共4种不同情况的仿真,得到仿真结果如表3所示。
由表3可以看出,蓄能器达到最高压力的时间分别约为14 s、10 s、8 s、5 s,蓄能器体积不再变化的时间分别约为14 s、10 s、8 s、5 s。分析得,蓄能器达到最高压力后,蓄能器体积不再变化,即此后液体就通过溢流阀流回储油箱,不再向蓄能器充液。系统初始压力越低,蓄能器达到最高压力的时间越长,能回收的能量越多。
表3 P0变化的仿真结果
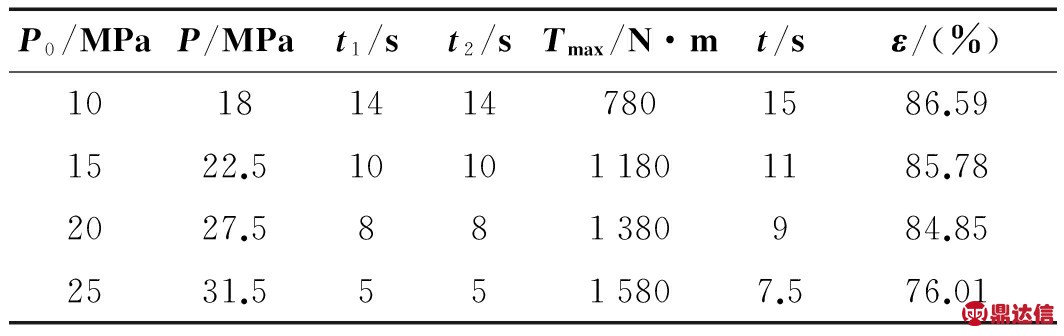
P0—蓄能器初始压力;P—蓄能器最终压力;t1—蓄能器达到最高压力的时间;t2—蓄能器体积达到最小的时间;Tmax—最大液压制动力矩;t—汽车制动停止时间;ε—制动能量回收效率
又由公式(14)计算出4种情况的回收效率分别为86.59%、85.78%、84.85%、76.01%。由此得出,当蓄能器体积、系统最高压力和车速一定时,随着蓄能器初始压力的升高,回收的制动能量在减少。
由表3可以看出,车轮制动力矩分别约为780 N·m、1 180 N·m、1 380 N·m、1 580 N·m,车速达到0 m/s的时间分别约为15 s、11 s、9 s、7.5 s。分析得,随着蓄能器初始压力的增大,车轮液压制动力矩增大,导致制动减速度增大,从而制动时间变小。由此得出,当蓄能器体积、系统最高压力和车速一定时,随着蓄能器初始压力的升高,制动时间变小。
综合分析,其他条件一定,随着P0的减小,制动能量回收效率是增大的,但是制动时间却变长了,出于对制动安全的考虑,在选择蓄能器初始压力的时候,应以GB7258—2012为依据,在满足制动安全性能的前提条件下,再尽可能地减小蓄能器初始压力,从而既兼顾了制动安全性也使能量回收效率最大化。
3.2.2 系统最高压力变化
本研究在蓄能器总体积为55 L、P0=21.52 MPa时,分别进行P2=23.5 MPa、P2=27.5 MPa、P2=31.5 MPa共3种不同情况的仿真,得到仿真结果如表4所示。
表4 P2变化的仿真结果
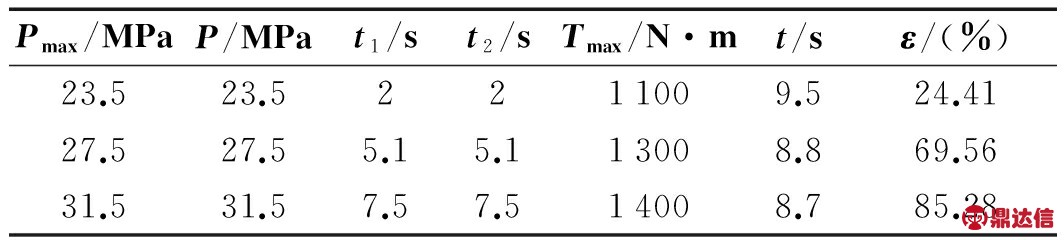
Pmax—系统最大压力;P—蓄能器最终压力;t1—蓄能器达到最高压力的时间;t2—蓄能器体积达到最小的时间;Tmax—最大液压制动力矩;t—汽车制动停止时间;ε—制动能量回收效率
从表4可以看出,蓄能器达到最高压力的时间分别约为2 s、5.1 s、7.5 s,蓄能器体积不再变化的时间分别约为2 s、5.1 s、7.5 s。分析得,蓄能器初始压力相同,当蓄能器达到最高压力时,蓄能器的体积也达到最小,就不再回收剩余的能量。系统最高压力越低,蓄能器达到最高压力的时间越短,从而导致蓄能器的回收效率降低。
又由公式(14)计算出3种情况的回收效率分别为24.41%、69.56%、85.28%,与上述分析一致。由此得出,当蓄能器体积、蓄能器初始压力和车速一定时,随着蓄能器最高压力的升高,能量回收效率增加。
由表4可以看出,随着蓄能器最高压力的增大,车轮液压制动最大力矩分别为1 100 N·m、1 300 N·m、1 400 N·m,车速达到0 m/s的时间分别约为9.5 s、8.8 s、8.7 s。分析得,随着蓄能器最高压力的增大,制动力矩增大,使制动减速度增大,从制动时间减小。
综合分析,仿真结果表明蓄能器的最高压力的增大,不但可以兼顾制动安全性,而且可以使蓄能器的有效容积变大,所以在设置蓄能器最高压力时,可以以蓄能器能够承受的最大压力为系统最高压力。
3.2.3 蓄能器总体积变化
当P0=21.5 MPa、P2=31.5 MPa时,分别进行蓄能器体积为10 L、20 L、30 L、40 L、50 L共5种不同情况的仿真,得到仿真结果如表5所示。
表5 V0变化的仿真结果
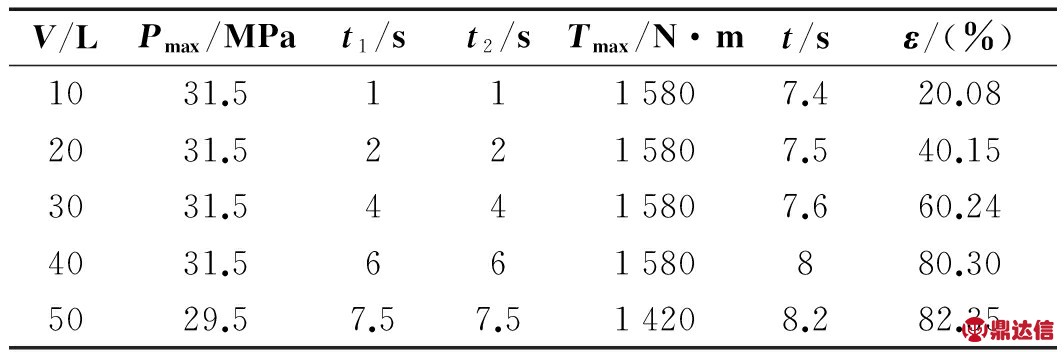
V—蓄能器总体积
由表5可以看出,蓄能器达到最高压力的时间分别约为1 s、2 s、4 s、6 s、7.5 s,蓄能器体积达到最小的时间分别约为1 s、2 s、4 s、6 s、7.5 s。分析可知,蓄能器总体积越小,蓄能器压力越先达到最高压力,此后,就不再回收剩余的能量,导致蓄能器的回收效率降低。
又由公式(14)计算出5种情况的回收效率分别为20.08%、40.15%、60.24%、80.30%、82.35%。由此得出当蓄能器初始压力,蓄能器最高压力和车速一定时,随着蓄能器总体积的升高,回收的能量增加。
由表5可以看出,汽车减速为0 m/s的时间分别约为7.4 s、7.5 s、7.6 s、8 s、8.2 s,制动力矩达到最大值的时间分别约为1 s、2 s、4 s、6 s、8.2 s,而且最高制动力均为1 580 N·m,只有V0=50 L时,最大制动力为1 420 N·m。分析得,当蓄能器的体积增大时,达到最大制动力矩的时间就越长,因此汽车制动停止的时间就越长。
综合分析,随着蓄能器体积的增大,制动能量回收的效率增大,但是制动停止的时间变长。所以在选择蓄能器时,本研究在满足制动法规GB7258—2012的前提下,选择体积稍微大点的蓄能器。
3.3 整车仿真实验总结
综合以上3个实验得出,蓄能器初始压力、蓄能器体积对回收效率影响与制动时间的影响相反;系统最高压力对二者的影响一致。
4 优化设计
笔者采用正交试验法,对液压系统各参数进行研究,选择最优参数组合。正交实验表如表6所示。
表6 试验因素、水平及计算结果
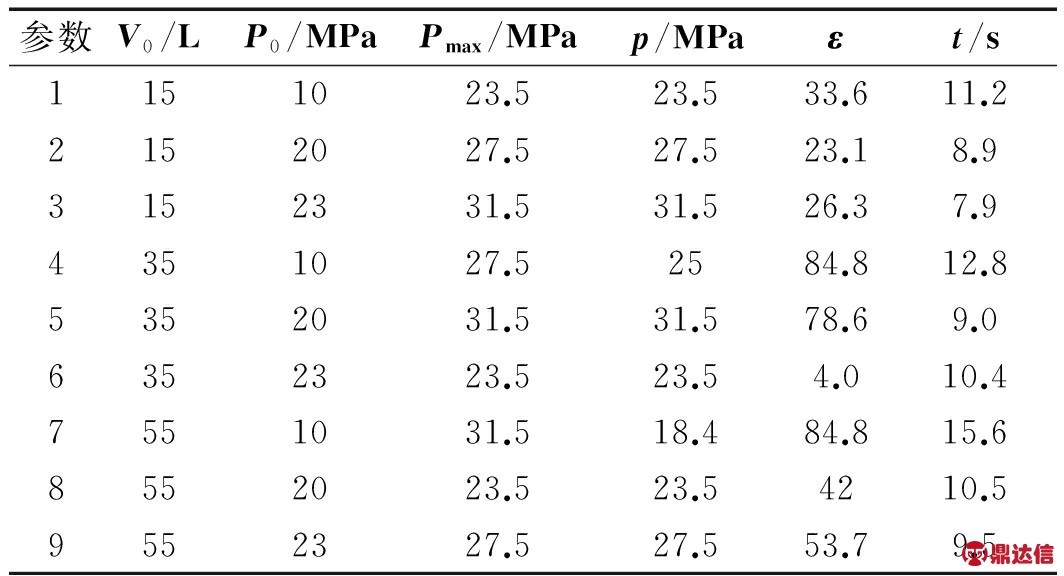
V0—蓄能器初始体积;P0—蓄能器初始压力;Pmax—系统最大压力
极差分析表如表7和表8所示。
表7 能量回收效率ε的极差分析
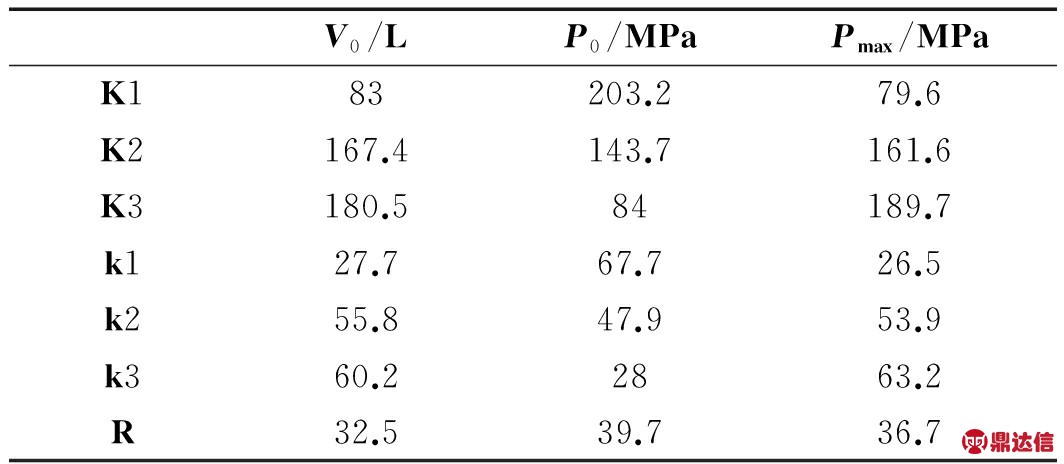
表8 制动停止时间t的极差分析
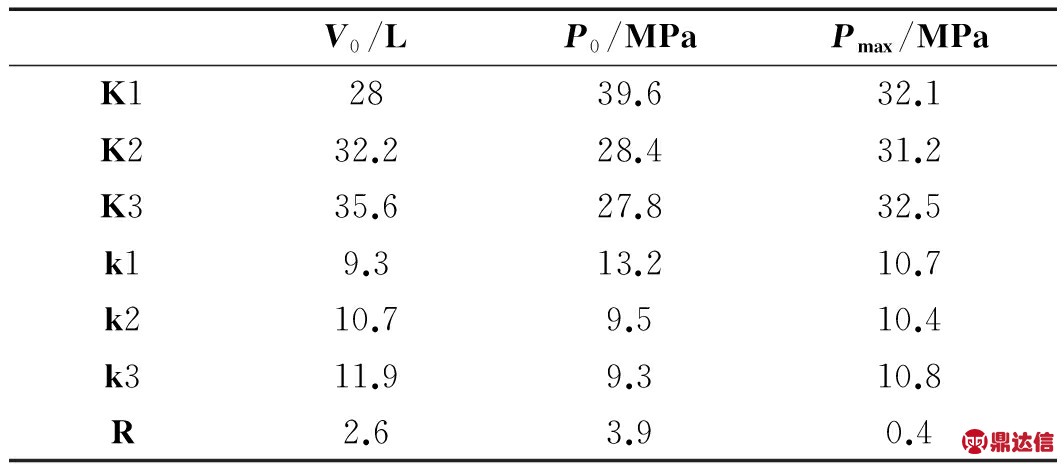
从表6所示的能量回收效率ε极差分析结果可以看出,V0、P0、Pmax的极差R分别为32.5%、39.7%、36.7%。所以蓄能器初始压力P0对回收效率影响最大,其次是系统最高压力Pmax,最后是蓄能器体积V0。最优参数组合为蓄能器体积55 L、蓄能器初始压力10 MPa、系统最高压力31.5 MPa。
从表7制动停止时间t极差分析结果可知,V0、P0、Pmax的极差R分别为2.6%、3.9%、0.4%。蓄能器初始压力P0对制动时间影响最大,其次是蓄能器体积V0,最后是系统最高压力Pmax。最优参数组合为蓄能器体积15 L、蓄能器初始压力23 MPa、系统最高压力27.5 MPa。
能量回收效率最优参数组合和制动时间最优参数组合是不一样的。下面讨论分析,选出兼顾二者的最优组合。
由表7和表8可知,P0选择10 MPa和23 MPa,对能量回收效率的影响由67.7%变化到28%,变化率约为58.6%;对t影响由13.2%变化到9.3%,变化率约为29.5%。很明显如果要想制动时间变短一点,就要损失很多能量。如果P0选择20 MPa,则对ε的影响为47.9%,对制动时间t的影响是9.5%,与P0取10 MPa相比,对ε影响变化率约为29.2%,对t影响变化率约为28.0%。所以本研究兼顾制动停止时间和能量回收效率,选择P0为20 MPa。
由表7和表8可知V0选择15 L和55 L,对ε影响由27.7%变化到60.2%,变化率约为117.3%;对t影响由9.3%变化到11.9%,变化率约为28.0%。由此可见V0对能量回收效率影响远远大于对制动时间的影响,所以本研究以最大能量回收效率为目标,选取V0为55 L。
由表7和表8可知Pmax选择27.5 MPa和31.5 MPa,对ε影响由53.9%变化到63.2%,变化率约为17.3%;对t影响由10.4%变化到10.8%,变化率约为3.8%。由此可见Pmax对能量回收效率影响远远大于对制动时间的影响,所以本研究以最大能量回收效率为目标,选Pmax为31.5 MPa。
综合制动停止时间和能量回收效率选择最优组合为蓄能器体积55 L、蓄能器初始压力20 MPa、系统最高压力31.5 MPa。
5 结束语
首先笔者通过试验与仿真研究了液压制动能量回收系统,然后通过整车仿真分析蓄能器参数对能量回收效率和制动时间的影响,最后通过正交优化设计优化蓄能器参数,结果表明:
(1)仿真与台架实验表明了液压仿真模型的正确性。
(2)蓄能器初始压力、蓄能器体积对回收效率影响与与制动时间的影响相反;系统最高压力对二者的影响一致。
(3)通过正交试验,选择蓄能器最优参数组,为整车实验提供了依据。