摘 要: 为研究环氧树脂玻璃钢-聚氨酯泡沫夹层复合材料靶的抗弹性能,利用弹道枪发射钨合金球形破片撞击不同厚度的单层板及不同组合方式的夹层靶板. 获得了不同入射速度下靶板的破坏形貌,通过高速摄影测得破片初速与余速,并利用上下调整速度法估算出靶板弹道极限速度,分析了结构特征对复合材料靶比吸收能的影响,在此基础上,对常用理论模型进行计算对比分析. 结果表明:玻璃纤维抽拔、拉伸断裂是靶板吸收能量的主要方式;聚氨酯泡沫抗弹性能较差,作为夹层材料主要作用是防护冲击波;靶板的比吸能与面密度之间呈二次函数抛物线关系,而在相同面密度下,夹层板的吸能总体上是随着玻璃钢占比的增加而增强;THOR公式更加适用于这种材料夹层板的弹道极限计算.
关键词:环氧树脂玻璃钢;夹层板;破片;弹道极限速度
环氧树脂玻璃钢的电性能十分优越,对电信号无屏蔽作用,在高频外电场的干扰作用下,微波仍然能够良好的透过,且玻璃钢仍然可以保持良好的介电性. 同时,它的比抗拉强度比较高,耐腐蚀性良好,制作工艺比较简单,被广泛用于导弹导引头、雷达天线罩等. 采用环氧树脂玻璃钢作为构件材料,一方面保证了对辐射和接收的信号尽量“透明”,另一方面保护了内部的电子设备免受外界恶劣环境的影响[1]. 而聚氨酯泡沫作为密度低的多孔介质,具有很好地吸收动能的特性. 在工程防护中被广泛用做雷达天线罩等结构件的夹芯材料. 由此组成的夹层板既克服了单一材料的缺陷,又能具备比高强度、低密度的优点.
Deng等[2]讨论了轻质夹层板与金属纤维芯的弹丸穿透过程中的能量吸收,得出夹层板在面密度相同的基础上略优于单层板;陈长海等[2-3]通过低速弹道冲击试验,研究了纤维/金属组合薄靶的破坏模式和吸能机理;随后通过高速弹道冲击试验,研究了不同钢/玻璃钢组合结构的抗弹性能,发现玻璃钢前置的组合靶抗弹性能稍强于玻璃钢后置的组合靶. 徐豫新等[4]通过破片模拟弹丸(FSP)高速撞击不同钢板-纤维增强复合材料-钢板结构的三明治板实验,得到不同三明治板的弹道极限,分析了结构特征对纤维增强复合材料三明治板比吸收能的影响. 张雁等[5]采用理论推导、数值仿真及实验验证对玻璃钢-聚氨酯泡沫夹层板的失效特性进行了研究,得到了其实际弯曲失效载荷和两种失效模式. 赵晓旭等[6]研究了钢/纤维层复合板对破片弹速侵彻防护性能的理论分析方法,分析复合板破坏模式及吸能机制,建立了复合板在破片弹速侵彻下面密度吸能的分析模型. 毛亮等[7]对钨合金破片侵彻DFRP靶板的规律进行了研究,分析了其主要破坏模式及细关吸能机制. 张鹏等[8]研究了聚脲弹性体涂覆钢板、涂覆纤维复合材料板抗破片侵彻性能以及涂层与底材层间作用机制. 现有研究多针对与钢等金属有机组合成的夹层板或者单层纤维增强复合材料的层合板,而针对玻璃钢-聚氨酯泡沫夹层板抗侵彻贯穿性能的研究相对较少.
本文设计加工了不同厚度的玻璃钢单层板、面密度相同的夹层板以及保持玻璃钢厚度相同,中间聚氨酯泡沫厚度不同的夹层板. 通过弹道枪发射钨合金球形破片,对3类靶板进行了冲击试验,获得了破片的着靶速度以及剩余速度,分析比较了玻璃钢厚度、玻璃钢在夹层板中面密度占比等对靶板破坏形态和吸能的影响规律. 进一步获得了各种靶板的极限贯穿速度,并和理论模型对比分析,探讨理论模型的适用性.
1 实验方案
1.1 弹靶材料
实验所用的破片为93钨合金球形破片,钨球直径8 mm,质量4.49 g. 钨合金材料参数如表1所示. 设计了尼龙材料的闭气弹托[9],飞行过程中弹托和破片受到空气阻力作用产生不同减加速度,弹托的减加速度大而自动脱壳,高速摄影表明弹靶作用前破片和弹托分离良好,如图1所示. 靶板材料为E玻璃纤维/环氧树脂复合材料靶板,型号为EPGC202,是由环氧树脂基体和增强材料(纤维及其织物)通过二者之间的界面复合而成的低压成型材料. 其中环氧树脂的环氧当量为170,固化剂胺值为500. 单向布织物是由高模无碱玻璃纤维编织而成,面内纤维按照相互正交的方式铺层. 材料的基本性能参数见表2. 硬质聚氨酯泡沫具有缓和冲击和吸收能量的特性,基本的性能见表3.
表1 钨合金球形破片性能参数
Tab.1 Material parameters of tungsten alloy spherical fragment

表2 环氧玻璃钢主要性能参数
Tab.2 Material parameters of epoxy resin FRP
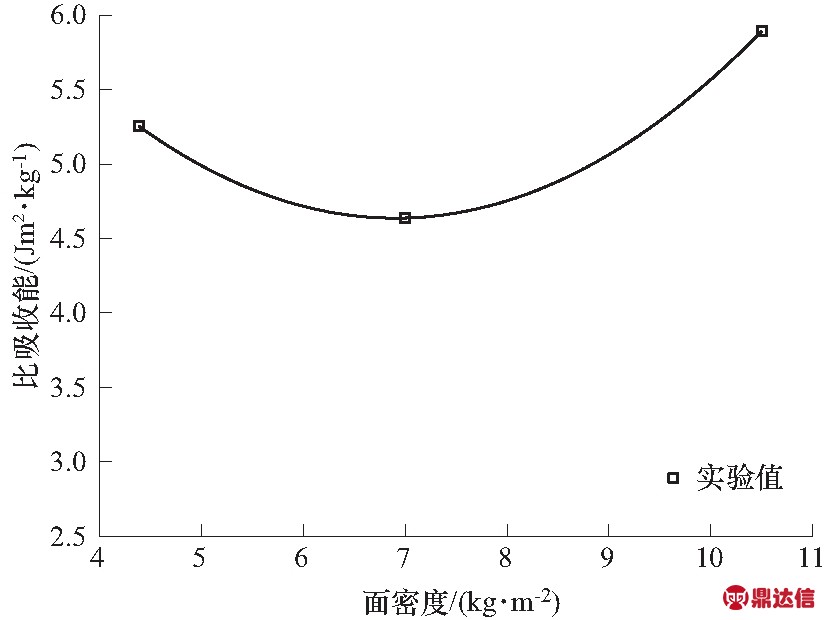
表3 硬质聚氨酯泡沫基本性能参数
Tab.3 Material parameters of poly urethane foam

1.2 实验装置与方法
破片撞击实验结构示意图如图1所示. 采用口径大小为12.7 mm的弹道枪作为发射系统来驱动钨合金球形破片,对3类靶板进行不同速度的冲击试验. 靶板用G型夹固定在45号钢支架上,弹道末端的沙箱用于回收破片,具体实验装置示意图如图2所示.
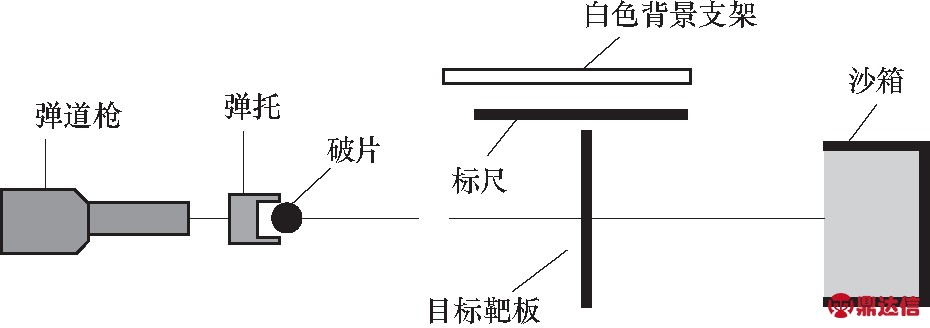
图1 破片撞击实验结构示意图
Fig.1 Sketch of fragment impact test

图2 破片飞行过程
Fig.2 Fragmentation flight process
试验中用高速摄影对破片的脱壳、飞行和作用靶板过程进行记录. 拍摄频率设置为20 000帧/s,带栅格的标尺用于标定飞行距离. 为了使拍摄更加清楚,对比度更高,靶板背后安装了白色背景的支架. 通过对高速摄影图片的处理,可以得到破片的入射速度、冲击靶板背面的位移变化以及贯穿靶板后破片的剩余速度.
1.3 实验工况设计
共设计了3组实验. 第1组为不同厚度的玻璃钢单层板,分析玻璃钢厚度对抗弹性能的影响,如图3(a)所示. 第2组为在面密度相同的5种玻璃钢-聚氨酯泡沫-玻璃钢夹层板结构,分析玻璃钢面密度占比对抗弹性能的影响. 夹层板的面板和背板材料均为玻璃钢,中间夹层为聚氨酯泡沫,用环氧树脂胶进行粘接,如图3(b)所示. 第3组为面板和背板厚度相同情况下,中间聚氨酯泡沫厚度不同的夹层板,用于分析聚氨酯泡沫的影响,其中,第3组工况包含编号1.2、2.3与3.1三种工况. 所有靶板长宽尺寸均为300 mm×300 mm. 靶板厚度方向尺寸见表4.
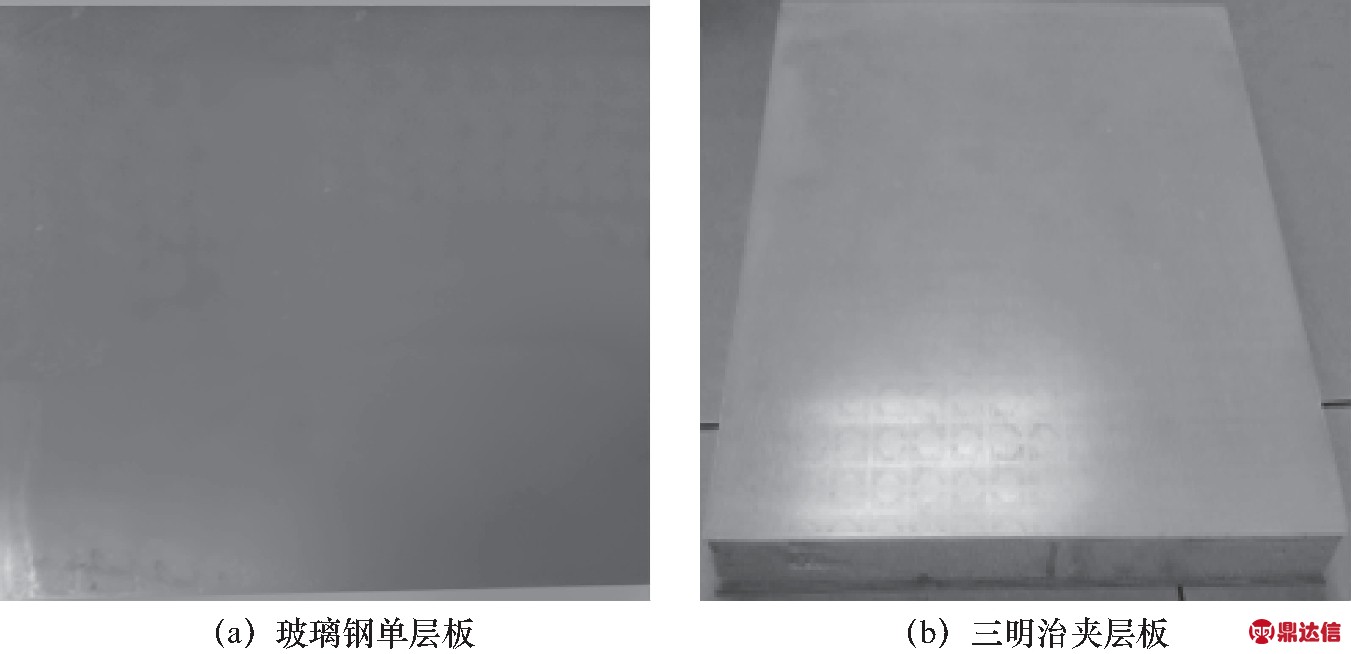
图3 靶板实物图
Fig.3 Photo of target plate
表4 靶板厚度尺寸
Tab.4 Target thicknesses
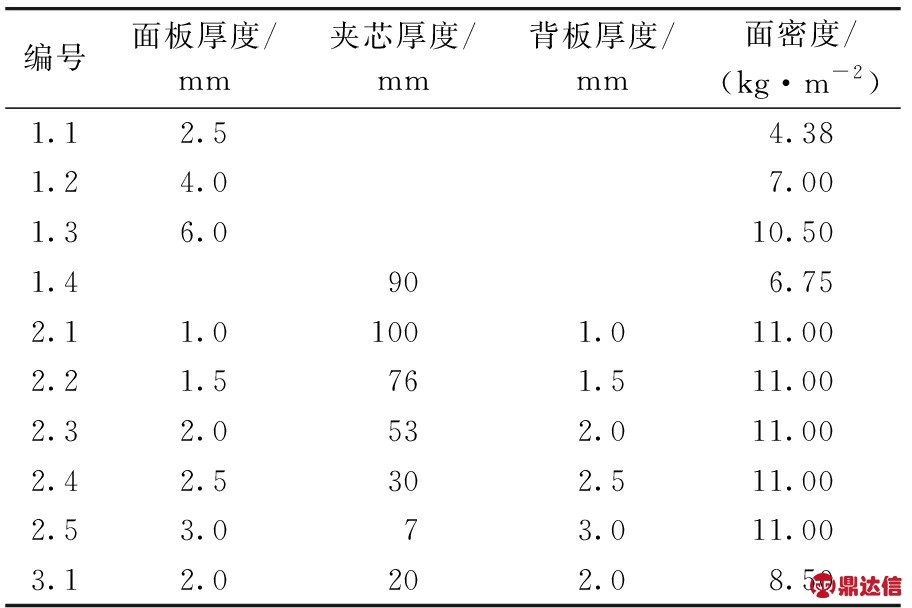
2 实验结果及现象分析
对各种不同厚度和结构的单层板和夹层板进行了弹道冲击试验,获得了破片着靶前的初始速度,回收了钨合金球形破片.
2.1 弹靶形貌分析
对回收的钨合金球形破片检测观察,发现破片除表面有明显烧蚀痕迹外,无明显塑性变形,质量基本不变,实验前后破片如图4所示.
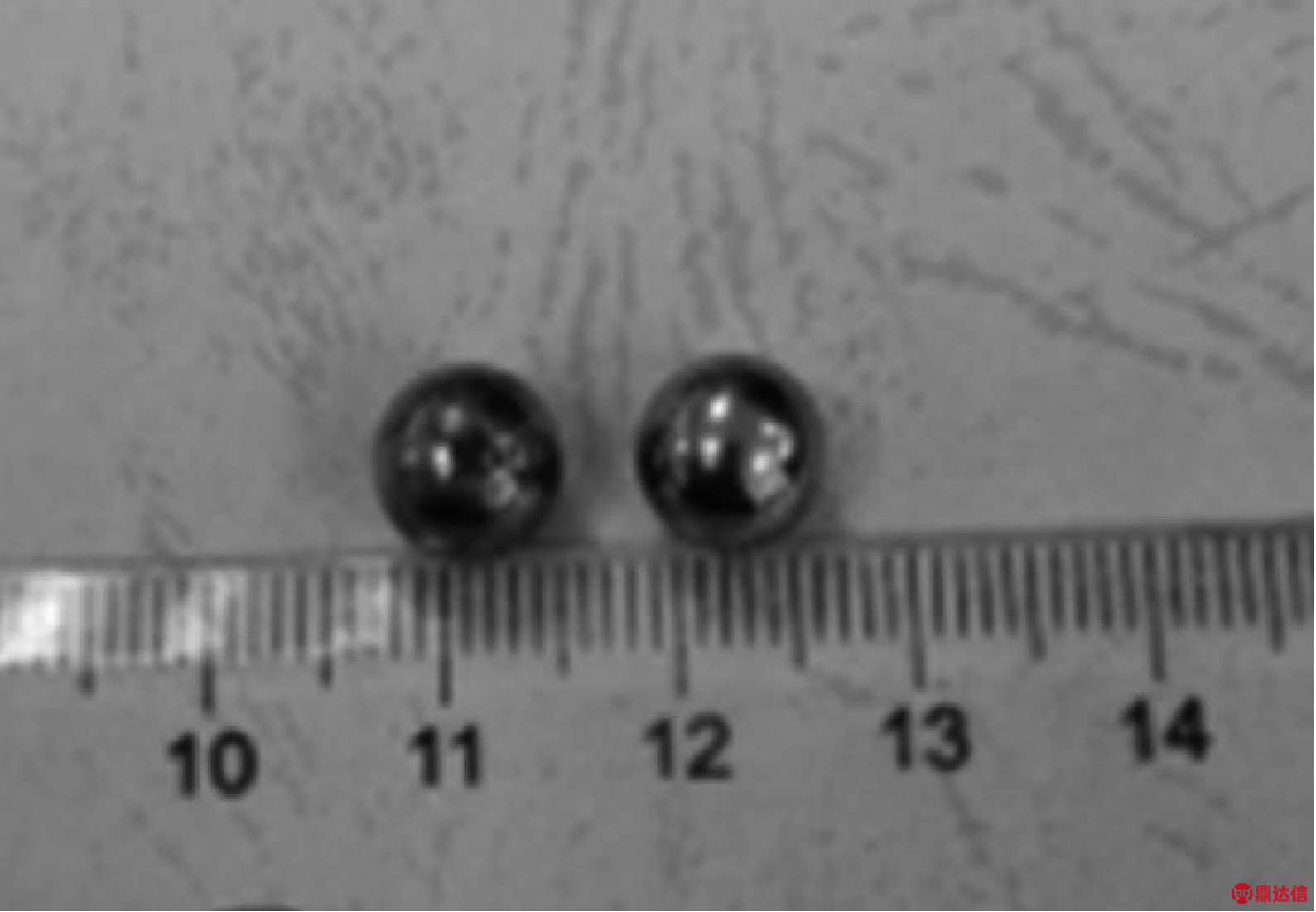
图4 实验后破片(左)与原破片(右)
Fig.4 Fragments after experiment (left) and original fragments (right)
靶板的破坏模式在不同的入射速度下破坏模式不尽相同,但均为正面的剪切破坏,背面的隆起(未贯穿)和纤维拉断(贯穿). 图5为入射速度为150,189,314 m/s时3.0 mm+7.0 mm+3.0 mm夹层板正面的破坏形貌. 150 m/s撞击速度下,破片未能穿透靶板,另外两种速度破片均穿透靶板. 可以看出:冲击速度越高,靶板正面的弹孔越接近圆形,速度越低,越不规则;弹孔尺度随着破片速度增加略有增加;破片速度越高,靶板破坏变形越容易集中在受冲击局部,纤维的断口越整齐;在弹孔周围破坏区域发现了纤维烧蚀后的黑色痕迹,这是由于破片对靶板的剪切过程中产生热量高于纤维的熔点,引起的烧蚀;靶板被撞击破坏区域近处的外围区域泛白,且沿着成对角线的经纬方向向外延伸扩张,由于这些位置发生了树脂的破裂和纤维与树脂间的脱粘.
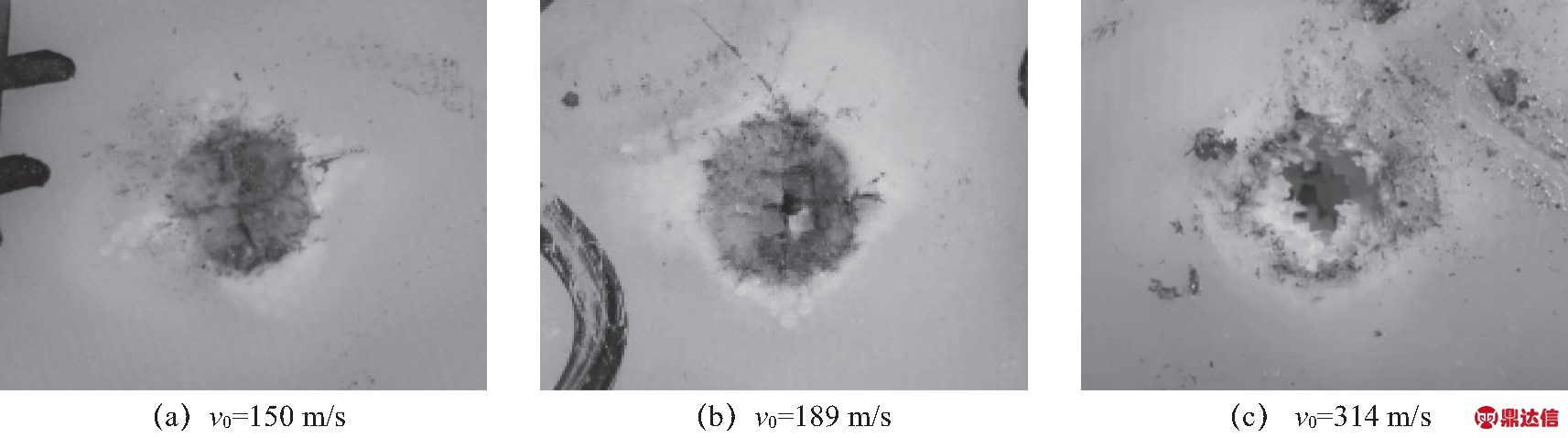
图5 夹层板(3+7+3)破坏形貌(正面)
Fig.5 Representative damage examples of sandwich plate (front)
图6为6 mm单层板在不同速度破片下背面的破坏形貌,其中速度在135 m/s和162 m/s时,未穿透靶板. 图7给出了2.5 mm+30 mm+2.5 mm夹层板在不同速度破片下背面的破坏形貌,其中速度在118 m/s和128 m/s时,未穿透靶板. 可以看出,无论是单层板还是夹层板,靶板背面都呈现出“十”字型“裂纹”或“鼓包”. 当破片速度较低,未穿透靶板时,背面的泛白区形状和裂纹接近规则圆形或椭圆. 随着破片速度的增大,撕裂尺度增大,多数靶板背面的破坏区为不规则四边形,少数靶板背面的破坏区呈现为不规则多边形. 这是由于玻璃钢内部的纤维受到垂直于纤维方向的冲击时,在剪断之前沿着纤维方向拉伸,与基体发生了脱粘. 纤维是按照相互正交的方式进行铺层的,抽拔和脱粘发生在两个正交的方向.
与正面破坏不同,背面没有烧蚀的痕迹. 破片冲击速度较低时,靶板背面只有少量纤维拉伸断裂,随着速度的增高,穿孔处大量纤维与基体间脱粘、抽拔及拉伸断裂,断裂面不整齐,非常粗糙. 这是由于破片到达靶板背面附近时,速度已大大降低,背面区域附近树脂基体对纤维的支撑作用又弱,纤维在破片作用下产生弯曲变形,再沿着纤维方向受到拉伸力作用,抽拔到一定程度再产生断裂. 破片初始速度较低时,纤维受到的拉伸力略大于纤维和基体间的脱粘力,呈现出抽拔和少量断裂. 初始速度增加到128 m/s后,抽拔和断裂的数量也随着增加,断口粗糙度增加,如图6(c)、6(d)和图7(b)、7(c)、7(d). 断口粗糙度的增加可能是应变率效应导致了纤维的抗拉强度增加,纤维更不容易拉断所致. 随着初始速度进一步增加,断口粗糙度不再增加,如图7(e)、7(f)所示.
对图6和图7中的破坏区尺度进行比对发现,在大致相同冲击速度下,夹层板背面的破坏程度远比单层板严重. 这是由于单层玻璃钢板的厚度相对于球形破片属于中厚靶范围. 尽管夹层板中玻璃钢的总厚度相对于球形破片属于中厚靶,但分成夹有聚氨酯泡沫的前后板后,球形破片对前后板的作用已经近似为对薄板作用,所以弹面的损伤区域更大.
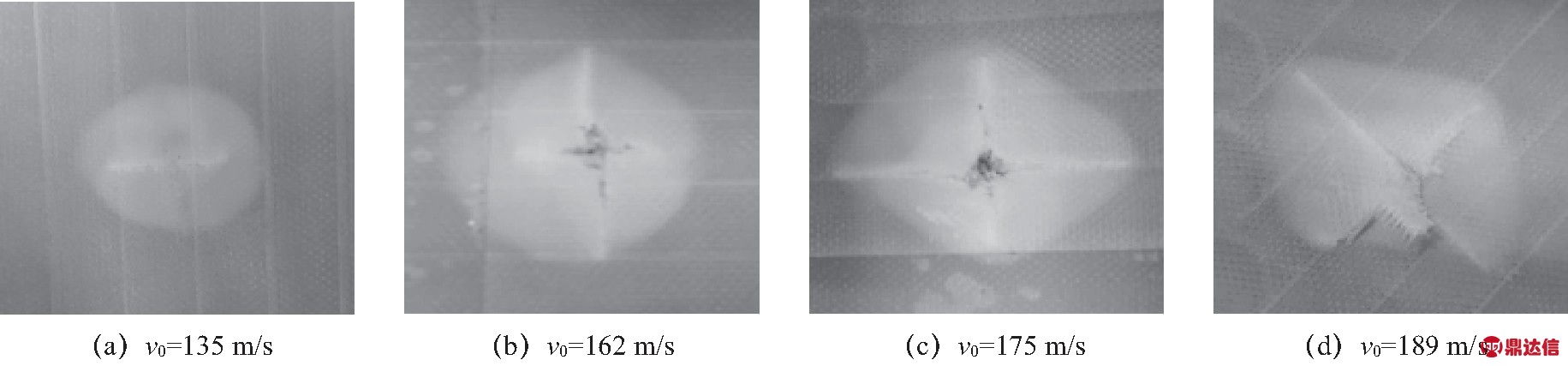
图6 6 mm单层板破坏形貌(反面)
Fig.6 Representative damage examples of 6 mm single plate (back)

图7 夹层板(2.5 mm+30 mm+2.5 mm)破坏形貌(反面)
Fig.7 Representative damage examples of sandwich plate (back)
2.2 破片侵彻贯穿靶板剩余速度分析
通过高速摄影照片,利用飞行时间和标尺,得到了各种工况下球形破片侵彻贯穿单层板和夹层板的初始入射速度和剩余速度.
对厚度为2.5,4.0,6.0 mm的3种环氧树脂玻璃钢单层板各进行了3发不同初始弹速的冲击试验,每种厚度都有两发试验的剩余速度为0,也就是球形破片未能贯穿靶板. 如图6(b)中,球形破片以162 mm初始速度侵彻6.0 mm厚单层板时,尽管背面已经开裂,但在高速摄影中的观察发现球形弹丸并未穿透靶板. 球形破片以初始速度94 m/s速度冲击2.5 mm厚单层板和以122 m/s速度冲击4.0 mm厚单层板时,板背面的破坏形态都是这种开裂未穿透形貌. 图8给出了球型破片以不同初始速度冲击不同厚度玻璃钢单层板时的剩余速度,可以看出:同一靶板厚度下,剩余速度随着初始速度增加而增加;要穿透靶板,冲击厚靶板的破片需要有更高的初始速度.
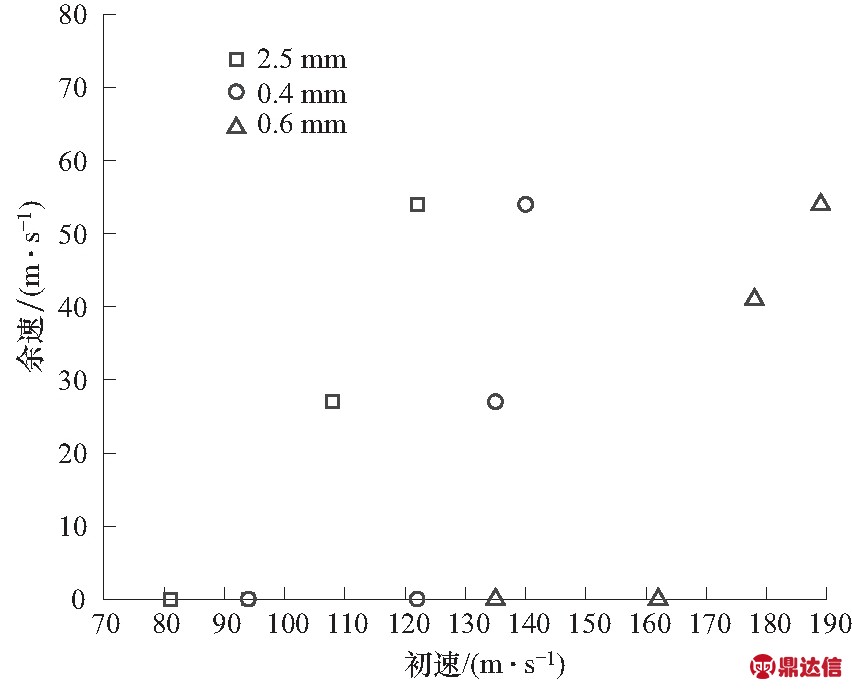
图8 不同厚度玻璃钢单层靶的初速和余速
Fig.8 Initial velocity and residual velocity of single-layer FRP target with different thickness
对6种不同结构玻璃钢-聚氨酯泡沫夹层板,其中5种夹层板的面密度相同,各进行了7~11发不同速度球形破片冲击试验. 每种夹层板结构都有1~2发的破片剩余速度为0,但1.0 mm+100.0 mm+1.0 mm厚度结构夹层板例外,因为受弹道枪发射条件限制,无法获得更低发射速度.
图9给出了5种相同面密度不同组合结构夹层板的实验初速与剩余速度关系以及非零余速试验的初速和剩余速度的二次多项式拟合. 可以看出:在极限贯穿速度附近,剩余速度随初始速度增加,呈现抛物线型缓慢上升;速度增加到一定程度后,剩余速度与初始速度近似呈线性关系. 这是因为在极限贯穿速度附近破片速度较低,靶板趋向于整体变形响应;随着初速继续增大,靶板以局部响应为主. 从图9还可以发现,在相同初速度前提下,玻璃钢占比越高,夹层板的剩余速度越低,夹层板的抗弹冲击性能越高. 因为氧树脂玻璃钢的强度远高于聚氨酯泡沫的强度. 图10给出了环氧玻璃钢前后板均为2 mm,中间聚氨酯泡沫厚度不同时聚氨酯泡沫对余速的影响. 由图可知聚氨酯泡沫对剩余速度影响较小. 结合文献[5,10]可知,由于聚氨酯泡沫夹层材料增大了结构的惯性矩,进而提高了其抗剪切能力,对爆炸载荷具有良好的吸收效果,主要用于防护冲击波. 所以,在设计雷达天线罩等实际防护结构时,在保证面密度相同的情况下,更多考虑防护风力载荷和爆炸冲击波引起的挠度变形,而不是优先考虑防护破片冲击.
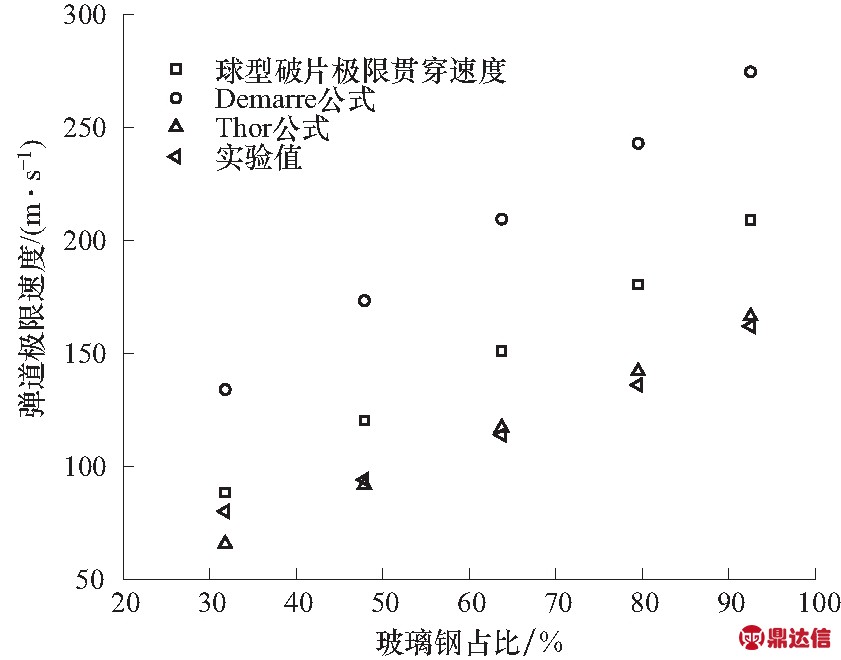
图9 面密度相同的靶板初速与余速关系
Fig.9 Relationship between initial and residual velocity of target plate with the same surface density
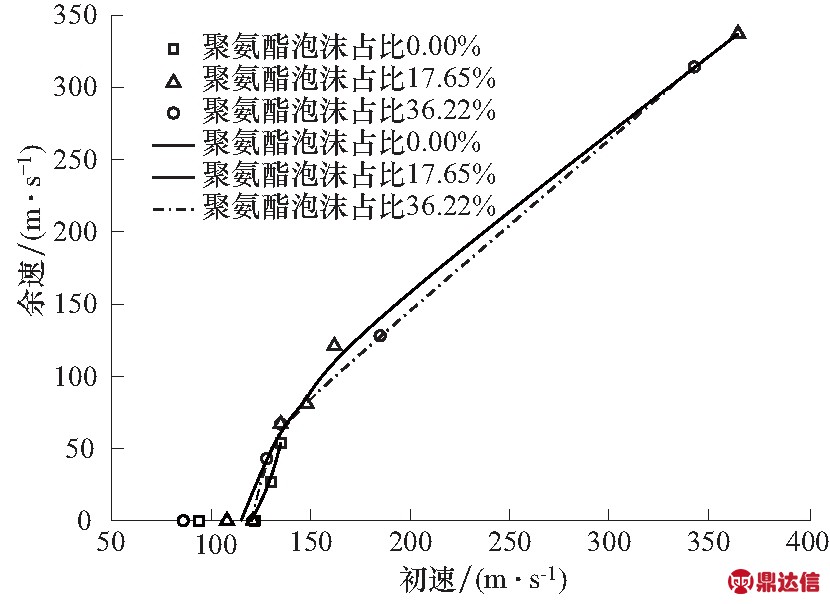
图10 不同厚度聚氨酯泡沫的初速和余速
Fig.10 Initial and residual velocities of polyurethane foams of different thicknesses
2.3 极限贯穿速度分析
靶板的极限贯穿速度指弹丸贯穿一定厚度的靶板后剩余速度刚刚为0的特殊情况,它是评估靶板抗弹性能的重要指标之一. 但在实际实验中,这种弹丸贯穿固定厚度的靶板而剩余速度恰好为0的情况一般很难发生,且往往会有“混合速度区”的出现. 在工程中,靶板的极限贯穿速度v50是取自靶板的“混合速度区”中的弹丸约50%贯穿靶板全部弹速的统计平均值.
通过上下调整法[11],采用在预计v50左右的相同发数的最高非贯穿和最低贯穿速度,对其速度平均,估算出不同组合方式夹层板弹道极限速度,如表5所示. 发现面密度相同的夹层板,其弹道极限速度随着玻璃钢占比的增大而增大. 1.4的聚氨酯泡沫靶,因为初速和余速之间的速度差太小而未能得到其弹道极限. 而对于单层靶,因为每种工况只做了4发实验,但结合图8,实验时测得的剩余速度在20 m/s左右,与入射速度相比相对较小,且图6(b)中,破片几乎恰好贯穿靶板且剩余速度为0,因此可以认为单层靶的弹道极限速度取在这个值的附近是基本合理的.
从表5中可以看出,对于单层板,弹道极限速度随着靶板后的增加而增加;对于夹层板,面密度相同时,弹道极限速度速度随着玻璃钢占比的增加而增加. 表5中,工况1.2、2.3和3.1中玻璃钢的总厚度相同,中间的聚氨酯泡沫的厚度不同,试验得到的弹道极限速度非常接近. 这是由于聚氨酯泡沫的强度远低于玻璃钢,在抗破片冲击过程中的作用有限,实验中聚氨酯泡沫对弹道极限速度的影响很小.
表5 破片贯穿每种结构靶板的弹道极限
Tab.5 Ballistic limit of fragment perforatingand specific energy absorption
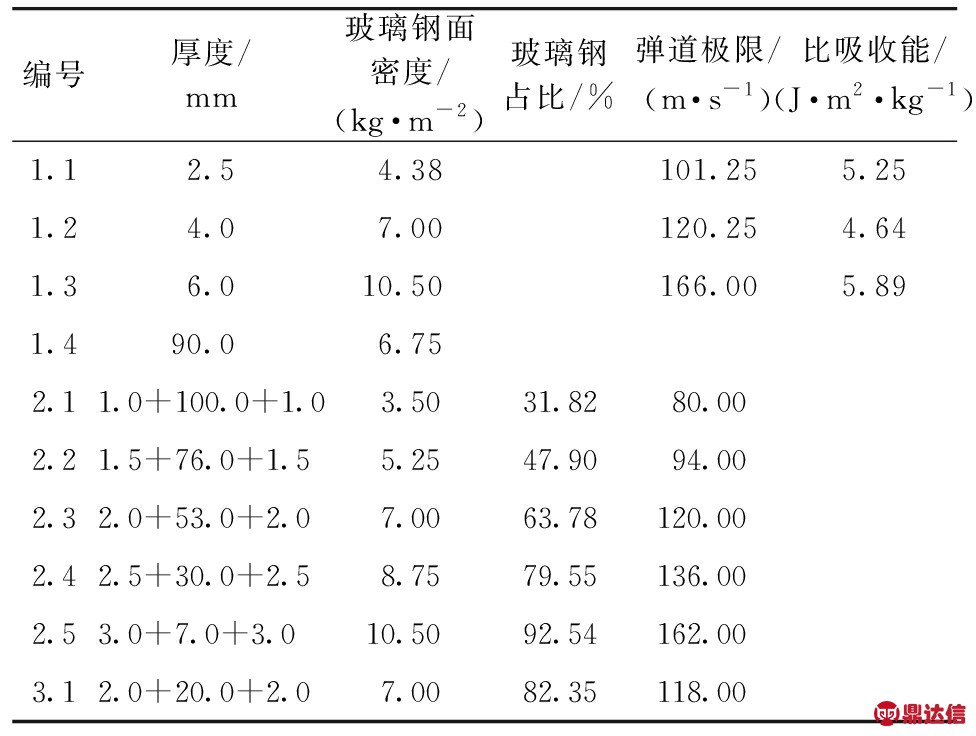
2.4 靶板抗破片冲击吸能分析
球形破片侵彻贯穿单层板或夹层板后基本没有变塑性变形,如果再忽略其弹性变形能,则可以近似认为靶板破坏和变形所吸收的能量导致了破片贯穿靶板前后速度降低,可以给出靶板的吸收能量为
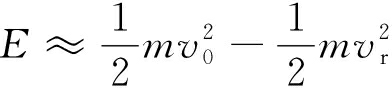
(1)
将弹道冲击试验的初始速度和剩余速度代入到式(1)中就可以计算出每发试验中靶板吸收的能量. 图11给出了5种相同面密度不同环氧树脂玻璃钢/聚氨酯泡沫组合结构夹层板的能量吸收与初始速度关系. 从图11中可以看出,在初速度基本相同时,玻璃钢在夹层板中的占比越大,夹层板抗钨球形破片冲击吸收的能量越大,玻璃钢面密度占比31.82%的夹层板吸能效果最差,玻璃钢面密度占比92.54%的夹层板的吸能效果最好. 这是由于玻璃钢的密度大约是聚氨酯泡沫的23倍多,而抗压强度却是泡沫的720倍.
从图11中还可以看出,随着钨球破片速度的增加,同一结构环氧树脂玻璃钢/聚氨酯泡沫的能量吸收都相应的增加. 在弹道极限速度附近,随着破片速度增加能量吸收几乎是快速线性增加,但当破片速度增加到一定程度后,能量吸收增加程度有限. 这种增加,是由两种材料的惯性效应和应变率共同导致的. 在初始速度较高时,试验值的离散程度较大. 这是由侵彻贯穿试验速度测量精度不足和误差计算方式造成的. 速度越高,贯穿靶板前后破片的速度降越小,高速时只有几十米每秒,此时,5%的速度测量误差就是几十米每秒. 由于正比于速度降,因此初始速度越高,测量偏差引入的能量误差就越大.
靶板受到弹丸的冲击破坏时,还经常用靶板比吸能(SEA)[12]来表征靶板的抗弹性能. 其计算公式为
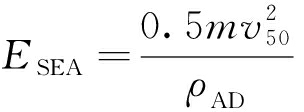
(2)
式中:ESEA为靶板比吸收能;m为弹丸质量;v50为弹道极限速度;ρAD为靶板面密度. 该方法表征的是靶板单位面密度的抗弹冲击能量吸收能力.
对于相同的破片,ρAD的增加意味着靶板相对于破片由薄靶变化为中厚靶和厚靶,吸能机理也随之变化. 2.5 cm厚单层板相对于8 mm直径球形弹丸属于薄靶范围,靶板除了局部破坏变形吸能,整体变形吸能占比较大,总的单位面密度抗弹冲击能量吸收能力较大. 随着玻璃钢厚度的增大,4.0 mm厚单层板相对于所用破片属于中厚靶范围,靶板以局部破坏和变形为主,靶板背面的稀疏波对吸能有一定影响,单位面密度抗弹冲击能量吸收能力比薄靶反而略低. 随着单层板厚度进一步增加,该球形破片所对应的极限贯穿速度增加,环氧树脂玻璃材料受冲击变形时对应的应变率增大,应变率效应导致材料的动态抗拉强度增加,破坏变形需要的能量增加,单位面密度抗弹冲击能量吸收能力比前两者都高. 还有一个因素是随着靶板厚度增加,来自靶板背面稀疏波的影响也会减小,吸能能力相应增加. 顾冰芳等[13]在高分子量聚乙烯纤维复合材料的弹道冲击试验时发现了相同的规律,并尝试将靶板的比吸能SEA拟合为了靶板面密度的二次抛物线函数. 图11给出了环氧树脂玻璃钢单层板比吸收能和面密度的二次拟合,由于试验点不足,该曲线只有定性的性质,反映基本规律.
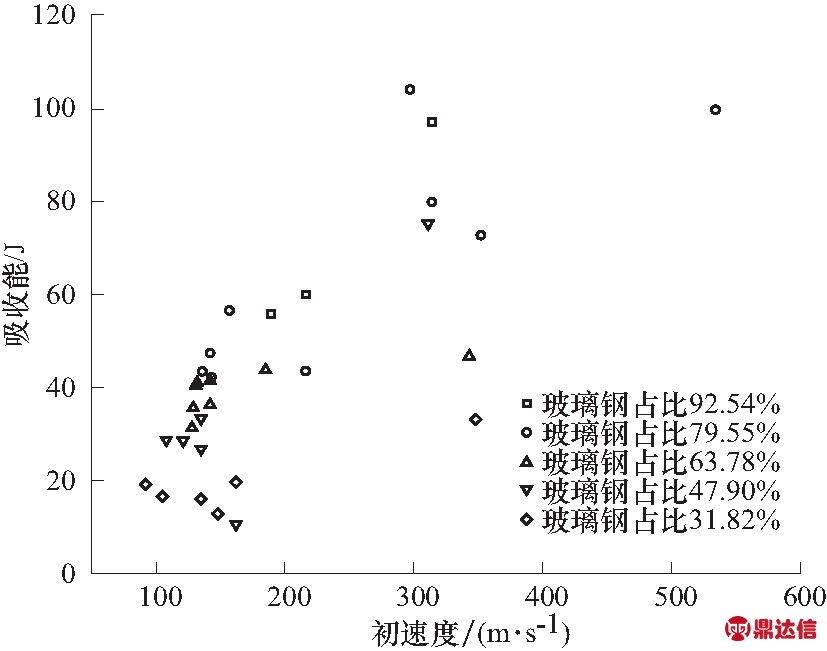
图11 面密度相同时不同夹层板能量吸收与初始速度关系
Fig.11 Relationship between initial kinetic energy and initial velocity of sandwich plates with the same surface density
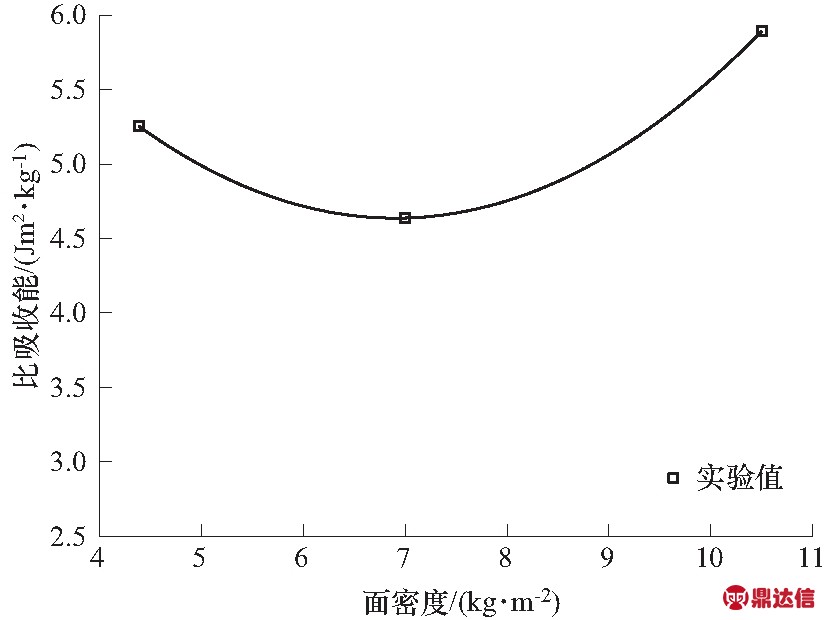
图12 单层靶ESEA与ρAD关系图
Fig.12 ESEA versus ρAD of single-layer target
3 理论模型对比分析
有很多关于破片侵彻的理论模型,这些理论模型或者说弹道极限经验公式是否适合于环氧树脂玻璃钢/聚氨酯泡沫夹层板结构的弹道速度计算还需要分析验证. 下面用一些典型的弹道极限经验公式计算出表4中5种相同面密度不同组合结构夹层板的弹道极限速度,并与实验值比较,探讨这些公式对玻璃钢-聚氨酯泡沫夹层板抗破片冲击弹道极限速度计算的适用性.
经典的球型破片极限贯穿速度公式[14]为
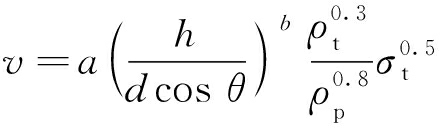
(3)
式中:h为靶厚;d为球形破片的直径;ρt为靶板的密度;ρp为破片材料的密度;σt为靶板的强度极限;a和b为靶板材料相关常数,这里a=5.47,b=0.84.
DeMarre(德·马尔)[15]在量纲分析和实验数据的基础上建立的弹丸侵彻装甲钢板的经验公式为
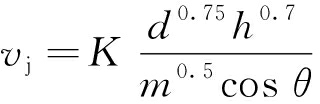
(4)
式中:vj为破片对靶板的极限贯穿速度;θ为破片飞行方向与靶板法线夹角;m为破片的质量;K为穿甲复合系数,这里K=52 935.
根据不同弹丸侵彻铝、钢、防弹玻璃等材料的实验数据拟合得到的可预测极限穿透速度估算的修正的THOR公式[16]为
vr=v0-0.3 048×10C1(61 023.75×hA)C2×
(15 432.1×m0)C3g(sec θ)C4(3.280 8×v0)C5(sec β)C6
(5)
式中:m0为破片初始质量;A为破片平均碰撞面积;β为攻角;C1~C6是与靶板材料相关系数,其中,C1=6.399,C2=0.889,C3=-0.945,C4=1.262,C5=0.019,C6=-0.813 2.
计算过程为:先通过密度强度等效原则将玻璃钢-聚氨酯泡沫夹层板等效为一定厚度的Q235钢靶,然后代入这些公式得到图13. 从图13可以看出Demarre公式与实验值相差较大,并不适用于复合材料夹层板极限贯穿速度的预估;球形破片极限贯穿速度仅在低速范围内,实验值与理论值接近;THOR公式在各个工况的计算结果与实验值均比较接近,可用于球形破片侵彻靶板的极限贯穿速度的计算,对比以上的结果THOR公式更适用于这种复合材夹层板弹道极限速度的预估.
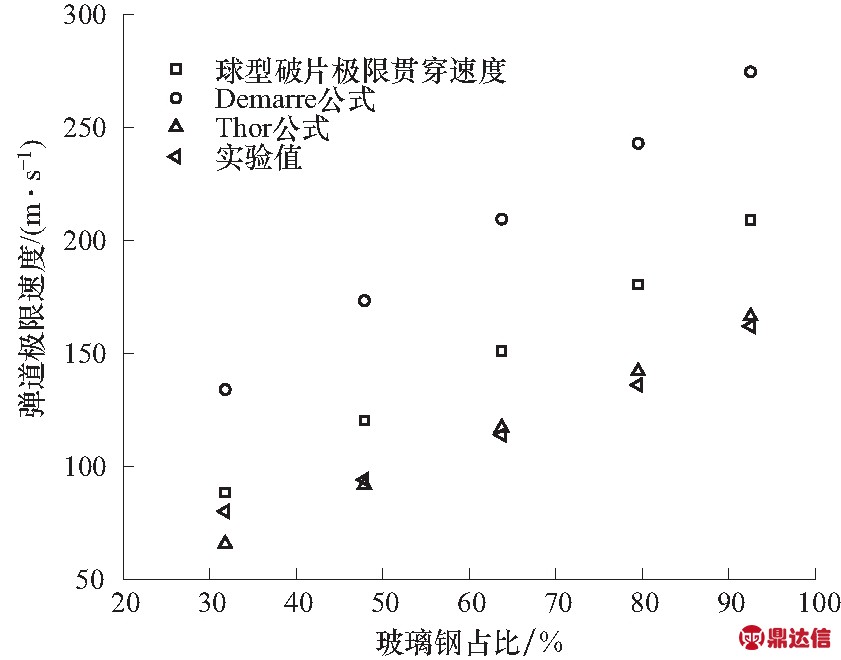
图13 贯穿速度理论公式值与实验值的比对
Fig.13 Comparisons of limited velocity formulas
4 结 论
① 通过靶板的破坏形貌观察可以看出:玻璃钢的破坏模式主要为玻璃纤维剪切破坏和拉伸断裂;其主要吸收能量方式为纤维与基体脱粘,抽拔、拉伸断裂.
② 聚氨酯泡沫抗弹性冲击吸能较差,作为夹芯材料主要用于吸收爆炸冲击波能量.
③ 由于环氧树脂玻璃钢的抗压和抗拉强度远大于聚氨酯泡沫,在相同面密度下,夹层板的吸能随着玻璃钢占比的增加而增强,弹性性能随着玻璃钢占比的增大而提高.
④ 环氧树脂玻璃钢单层板的抗弹冲击能力随着厚度的增加而增加,比吸收能和面密度之间呈二次函数抛物线关系.
⑤ 对于不同结构的夹层板,用3种理论公式计算得到的弹道极限速度与实验估算出的弹道极限速度比对发现,THOR公式更加适用于这种复合材料夹层板的弹道极限速度计算.
摘 要: 为研究环氧树脂玻璃钢-聚氨酯泡沫夹层复合材料靶的抗弹性能,利用弹道枪发射钨合金球形破片撞击不同厚度的单层板及不同组合方式的夹层靶板. 获得了不同入射速度下靶板的破坏形貌,通过高速摄影测得破片初速与余速,并利用上下调整速度法估算出靶板弹道极限速度,分析了结构特征对复合材料靶比吸收能的影响,在此基础上,对常用理论模型进行计算对比分析. 结果表明:玻璃纤维抽拔、拉伸断裂是靶板吸收能量的主要方式;聚氨酯泡沫抗弹性能较差,作为夹层材料主要作用是防护冲击波;靶板的比吸能与面密度之间呈二次函数抛物线关系,而在相同面密度下,夹层板的吸能总体上是随着玻璃钢占比的增加而增强;THOR公式更加适用于这种材料夹层板的弹道极限计算.
关键词:环氧树脂玻璃钢;夹层板;破片;弹道极限速度
环氧树脂玻璃钢的电性能十分优越,对电信号无屏蔽作用,在高频外电场的干扰作用下,微波仍然能够良好的透过,且玻璃钢仍然可以保持良好的介电性. 同时,它的比抗拉强度比较高,耐腐蚀性良好,制作工艺比较简单,被广泛用于导弹导引头、雷达天线罩等. 采用环氧树脂玻璃钢作为构件材料,一方面保证了对辐射和接收的信号尽量“透明”,另一方面保护了内部的电子设备免受外界恶劣环境的影响[1]. 而聚氨酯泡沫作为密度低的多孔介质,具有很好地吸收动能的特性. 在工程防护中被广泛用做雷达天线罩等结构件的夹芯材料. 由此组成的夹层板既克服了单一材料的缺陷,又能具备比高强度、低密度的优点.
Deng等[2]讨论了轻质夹层板与金属纤维芯的弹丸穿透过程中的能量吸收,得出夹层板在面密度相同的基础上略优于单层板;陈长海等[2-3]通过低速弹道冲击试验,研究了纤维/金属组合薄靶的破坏模式和吸能机理;随后通过高速弹道冲击试验,研究了不同钢/玻璃钢组合结构的抗弹性能,发现玻璃钢前置的组合靶抗弹性能稍强于玻璃钢后置的组合靶. 徐豫新等[4]通过破片模拟弹丸(FSP)高速撞击不同钢板-纤维增强复合材料-钢板结构的三明治板实验,得到不同三明治板的弹道极限,分析了结构特征对纤维增强复合材料三明治板比吸收能的影响. 张雁等[5]采用理论推导、数值仿真及实验验证对玻璃钢-聚氨酯泡沫夹层板的失效特性进行了研究,得到了其实际弯曲失效载荷和两种失效模式. 赵晓旭等[6]研究了钢/纤维层复合板对破片弹速侵彻防护性能的理论分析方法,分析复合板破坏模式及吸能机制,建立了复合板在破片弹速侵彻下面密度吸能的分析模型. 毛亮等[7]对钨合金破片侵彻DFRP靶板的规律进行了研究,分析了其主要破坏模式及细关吸能机制. 张鹏等[8]研究了聚脲弹性体涂覆钢板、涂覆纤维复合材料板抗破片侵彻性能以及涂层与底材层间作用机制. 现有研究多针对与钢等金属有机组合成的夹层板或者单层纤维增强复合材料的层合板,而针对玻璃钢-聚氨酯泡沫夹层板抗侵彻贯穿性能的研究相对较少.
本文设计加工了不同厚度的玻璃钢单层板、面密度相同的夹层板以及保持玻璃钢厚度相同,中间聚氨酯泡沫厚度不同的夹层板. 通过弹道枪发射钨合金球形破片,对3类靶板进行了冲击试验,获得了破片的着靶速度以及剩余速度,分析比较了玻璃钢厚度、玻璃钢在夹层板中面密度占比等对靶板破坏形态和吸能的影响规律. 进一步获得了各种靶板的极限贯穿速度,并和理论模型对比分析,探讨理论模型的适用性.
1 实验方案
1.1 弹靶材料
实验所用的破片为93钨合金球形破片,钨球直径8 mm,质量4.49 g. 钨合金材料参数如表1所示. 设计了尼龙材料的闭气弹托[9],飞行过程中弹托和破片受到空气阻力作用产生不同减加速度,弹托的减加速度大而自动脱壳,高速摄影表明弹靶作用前破片和弹托分离良好,如图1所示. 靶板材料为E玻璃纤维/环氧树脂复合材料靶板,型号为EPGC202,是由环氧树脂基体和增强材料(纤维及其织物)通过二者之间的界面复合而成的低压成型材料. 其中环氧树脂的环氧当量为170,固化剂胺值为500. 单向布织物是由高模无碱玻璃纤维编织而成,面内纤维按照相互正交的方式铺层. 材料的基本性能参数见表2. 硬质聚氨酯泡沫具有缓和冲击和吸收能量的特性,基本的性能见表3.
表1 钨合金球形破片性能参数
Tab.1 Material parameters of tungsten alloy spherical fragment

表2 环氧玻璃钢主要性能参数
Tab.2 Material parameters of epoxy resin FRP
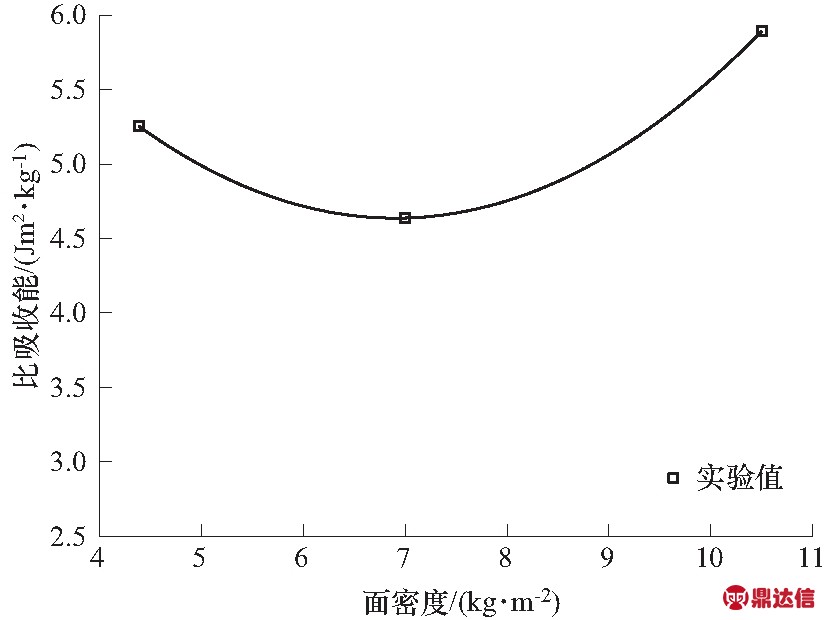
表3 硬质聚氨酯泡沫基本性能参数
Tab.3 Material parameters of poly urethane foam

1.2 实验装置与方法
破片撞击实验结构示意图如图1所示. 采用口径大小为12.7 mm的弹道枪作为发射系统来驱动钨合金球形破片,对3类靶板进行不同速度的冲击试验. 靶板用G型夹固定在45号钢支架上,弹道末端的沙箱用于回收破片,具体实验装置示意图如图2所示.
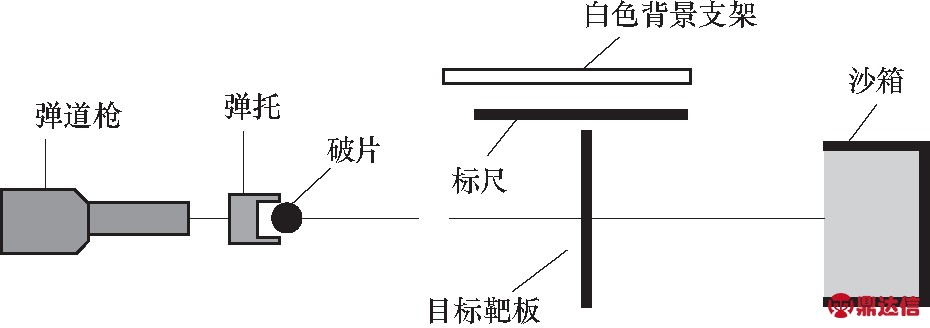
图1 破片撞击实验结构示意图
Fig.1 Sketch of fragment impact test

图2 破片飞行过程
Fig.2 Fragmentation flight process
试验中用高速摄影对破片的脱壳、飞行和作用靶板过程进行记录. 拍摄频率设置为20 000帧/s,带栅格的标尺用于标定飞行距离. 为了使拍摄更加清楚,对比度更高,靶板背后安装了白色背景的支架. 通过对高速摄影图片的处理,可以得到破片的入射速度、冲击靶板背面的位移变化以及贯穿靶板后破片的剩余速度.
1.3 实验工况设计
共设计了3组实验. 第1组为不同厚度的玻璃钢单层板,分析玻璃钢厚度对抗弹性能的影响,如图3(a)所示. 第2组为在面密度相同的5种玻璃钢-聚氨酯泡沫-玻璃钢夹层板结构,分析玻璃钢面密度占比对抗弹性能的影响. 夹层板的面板和背板材料均为玻璃钢,中间夹层为聚氨酯泡沫,用环氧树脂胶进行粘接,如图3(b)所示. 第3组为面板和背板厚度相同情况下,中间聚氨酯泡沫厚度不同的夹层板,用于分析聚氨酯泡沫的影响,其中,第3组工况包含编号1.2、2.3与3.1三种工况. 所有靶板长宽尺寸均为300 mm×300 mm. 靶板厚度方向尺寸见表4.
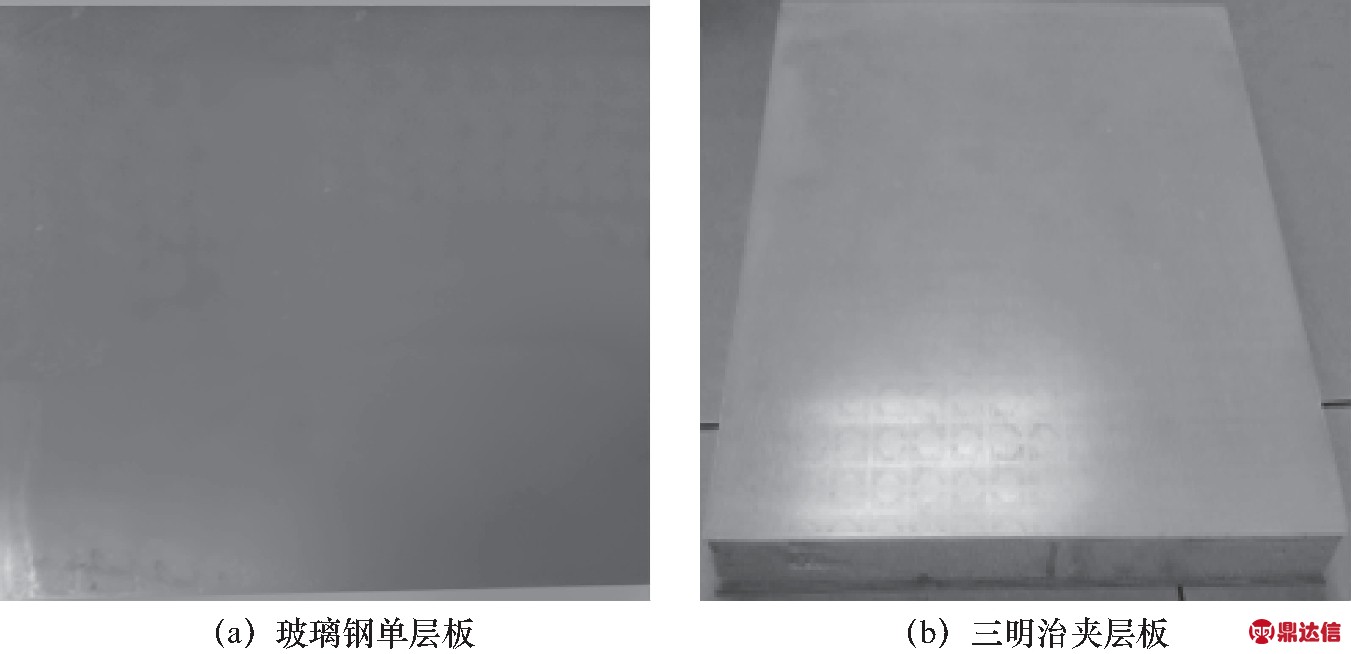
图3 靶板实物图
Fig.3 Photo of target plate
表4 靶板厚度尺寸
Tab.4 Target thicknesses
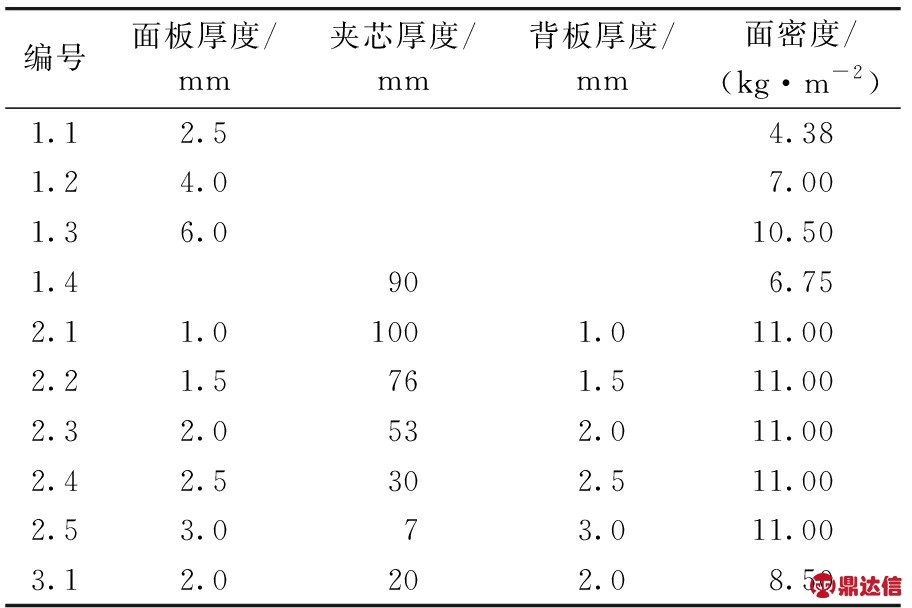
2 实验结果及现象分析
对各种不同厚度和结构的单层板和夹层板进行了弹道冲击试验,获得了破片着靶前的初始速度,回收了钨合金球形破片.
2.1 弹靶形貌分析
对回收的钨合金球形破片检测观察,发现破片除表面有明显烧蚀痕迹外,无明显塑性变形,质量基本不变,实验前后破片如图4所示.
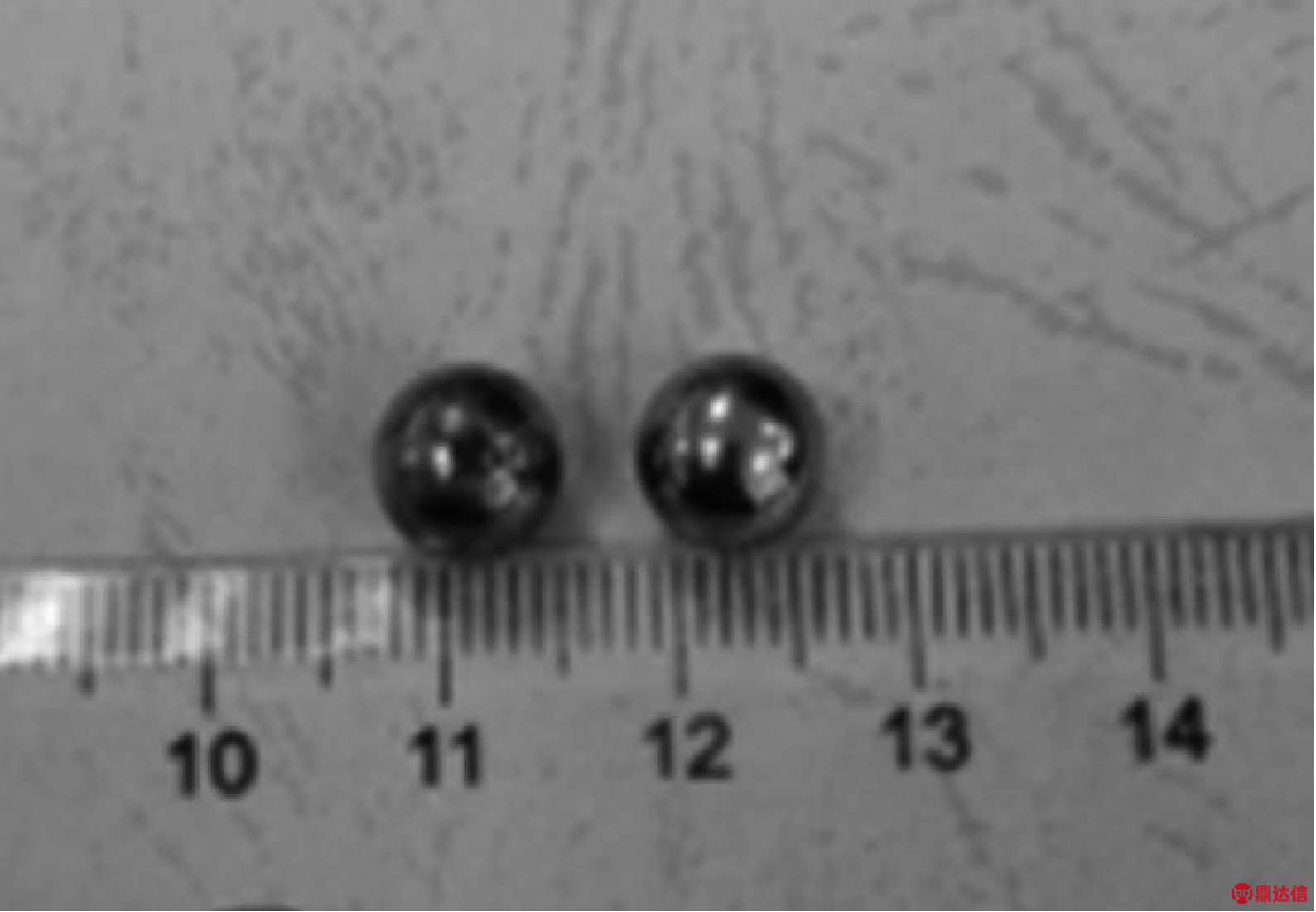
图4 实验后破片(左)与原破片(右)
Fig.4 Fragments after experiment (left) and original fragments (right)
靶板的破坏模式在不同的入射速度下破坏模式不尽相同,但均为正面的剪切破坏,背面的隆起(未贯穿)和纤维拉断(贯穿). 图5为入射速度为150,189,314 m/s时3.0 mm+7.0 mm+3.0 mm夹层板正面的破坏形貌. 150 m/s撞击速度下,破片未能穿透靶板,另外两种速度破片均穿透靶板. 可以看出:冲击速度越高,靶板正面的弹孔越接近圆形,速度越低,越不规则;弹孔尺度随着破片速度增加略有增加;破片速度越高,靶板破坏变形越容易集中在受冲击局部,纤维的断口越整齐;在弹孔周围破坏区域发现了纤维烧蚀后的黑色痕迹,这是由于破片对靶板的剪切过程中产生热量高于纤维的熔点,引起的烧蚀;靶板被撞击破坏区域近处的外围区域泛白,且沿着成对角线的经纬方向向外延伸扩张,由于这些位置发生了树脂的破裂和纤维与树脂间的脱粘.
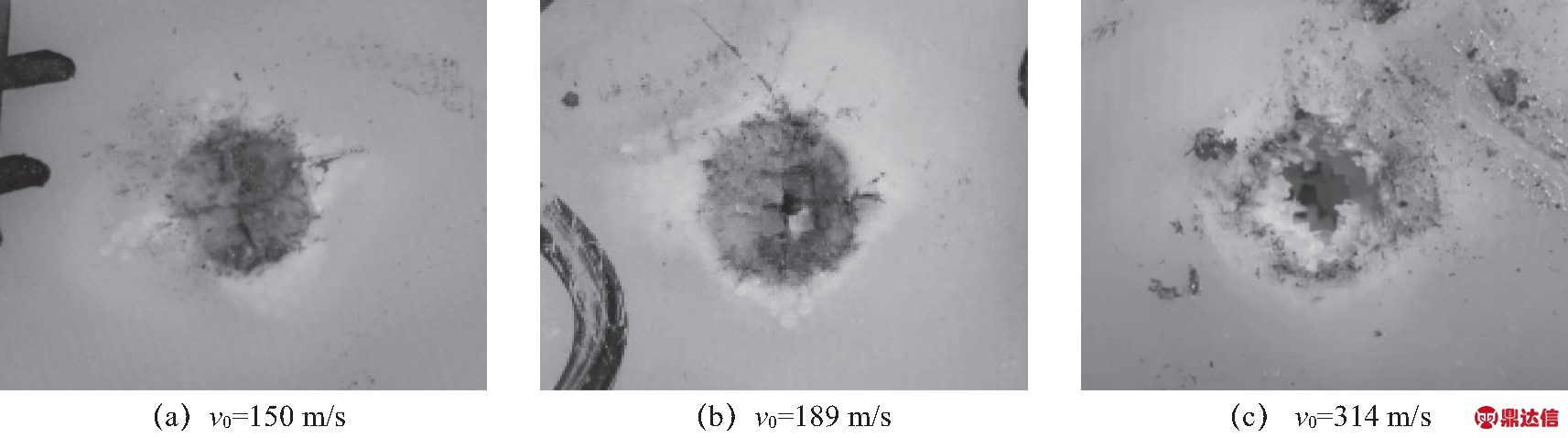
图5 夹层板(3+7+3)破坏形貌(正面)
Fig.5 Representative damage examples of sandwich plate (front)
图6为6 mm单层板在不同速度破片下背面的破坏形貌,其中速度在135 m/s和162 m/s时,未穿透靶板. 图7给出了2.5 mm+30 mm+2.5 mm夹层板在不同速度破片下背面的破坏形貌,其中速度在118 m/s和128 m/s时,未穿透靶板. 可以看出,无论是单层板还是夹层板,靶板背面都呈现出“十”字型“裂纹”或“鼓包”. 当破片速度较低,未穿透靶板时,背面的泛白区形状和裂纹接近规则圆形或椭圆. 随着破片速度的增大,撕裂尺度增大,多数靶板背面的破坏区为不规则四边形,少数靶板背面的破坏区呈现为不规则多边形. 这是由于玻璃钢内部的纤维受到垂直于纤维方向的冲击时,在剪断之前沿着纤维方向拉伸,与基体发生了脱粘. 纤维是按照相互正交的方式进行铺层的,抽拔和脱粘发生在两个正交的方向.
与正面破坏不同,背面没有烧蚀的痕迹. 破片冲击速度较低时,靶板背面只有少量纤维拉伸断裂,随着速度的增高,穿孔处大量纤维与基体间脱粘、抽拔及拉伸断裂,断裂面不整齐,非常粗糙. 这是由于破片到达靶板背面附近时,速度已大大降低,背面区域附近树脂基体对纤维的支撑作用又弱,纤维在破片作用下产生弯曲变形,再沿着纤维方向受到拉伸力作用,抽拔到一定程度再产生断裂. 破片初始速度较低时,纤维受到的拉伸力略大于纤维和基体间的脱粘力,呈现出抽拔和少量断裂. 初始速度增加到128 m/s后,抽拔和断裂的数量也随着增加,断口粗糙度增加,如图6(c)、6(d)和图7(b)、7(c)、7(d). 断口粗糙度的增加可能是应变率效应导致了纤维的抗拉强度增加,纤维更不容易拉断所致. 随着初始速度进一步增加,断口粗糙度不再增加,如图7(e)、7(f)所示.
对图6和图7中的破坏区尺度进行比对发现,在大致相同冲击速度下,夹层板背面的破坏程度远比单层板严重. 这是由于单层玻璃钢板的厚度相对于球形破片属于中厚靶范围. 尽管夹层板中玻璃钢的总厚度相对于球形破片属于中厚靶,但分成夹有聚氨酯泡沫的前后板后,球形破片对前后板的作用已经近似为对薄板作用,所以弹面的损伤区域更大.
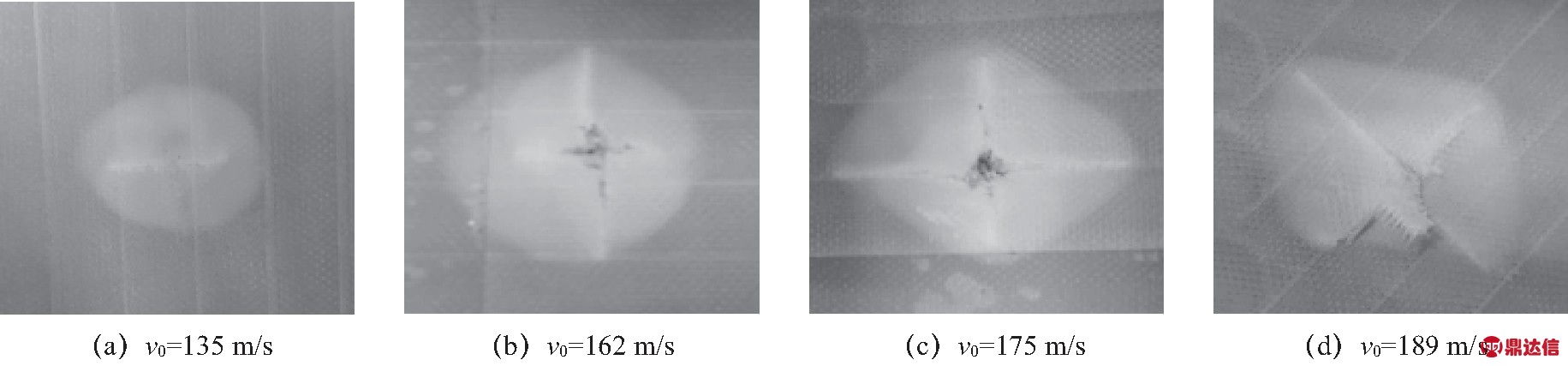
图6 6 mm单层板破坏形貌(反面)
Fig.6 Representative damage examples of 6 mm single plate (back)

图7 夹层板(2.5 mm+30 mm+2.5 mm)破坏形貌(反面)
Fig.7 Representative damage examples of sandwich plate (back)
2.2 破片侵彻贯穿靶板剩余速度分析
通过高速摄影照片,利用飞行时间和标尺,得到了各种工况下球形破片侵彻贯穿单层板和夹层板的初始入射速度和剩余速度.
对厚度为2.5,4.0,6.0 mm的3种环氧树脂玻璃钢单层板各进行了3发不同初始弹速的冲击试验,每种厚度都有两发试验的剩余速度为0,也就是球形破片未能贯穿靶板. 如图6(b)中,球形破片以162 mm初始速度侵彻6.0 mm厚单层板时,尽管背面已经开裂,但在高速摄影中的观察发现球形弹丸并未穿透靶板. 球形破片以初始速度94 m/s速度冲击2.5 mm厚单层板和以122 m/s速度冲击4.0 mm厚单层板时,板背面的破坏形态都是这种开裂未穿透形貌. 图8给出了球型破片以不同初始速度冲击不同厚度玻璃钢单层板时的剩余速度,可以看出:同一靶板厚度下,剩余速度随着初始速度增加而增加;要穿透靶板,冲击厚靶板的破片需要有更高的初始速度.
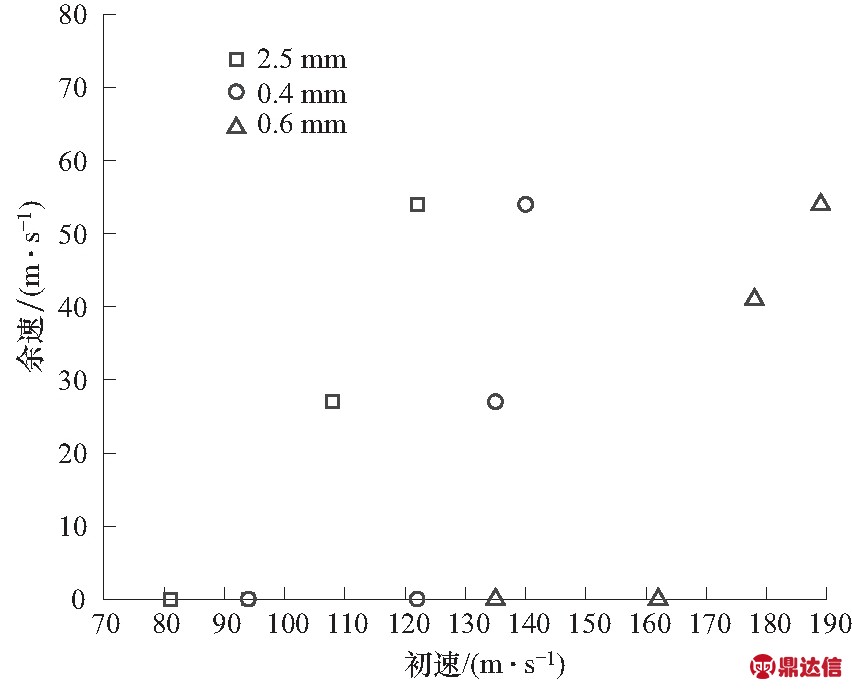
图8 不同厚度玻璃钢单层靶的初速和余速
Fig.8 Initial velocity and residual velocity of single-layer FRP target with different thickness
对6种不同结构玻璃钢-聚氨酯泡沫夹层板,其中5种夹层板的面密度相同,各进行了7~11发不同速度球形破片冲击试验. 每种夹层板结构都有1~2发的破片剩余速度为0,但1.0 mm+100.0 mm+1.0 mm厚度结构夹层板例外,因为受弹道枪发射条件限制,无法获得更低发射速度.
图9给出了5种相同面密度不同组合结构夹层板的实验初速与剩余速度关系以及非零余速试验的初速和剩余速度的二次多项式拟合. 可以看出:在极限贯穿速度附近,剩余速度随初始速度增加,呈现抛物线型缓慢上升;速度增加到一定程度后,剩余速度与初始速度近似呈线性关系. 这是因为在极限贯穿速度附近破片速度较低,靶板趋向于整体变形响应;随着初速继续增大,靶板以局部响应为主. 从图9还可以发现,在相同初速度前提下,玻璃钢占比越高,夹层板的剩余速度越低,夹层板的抗弹冲击性能越高. 因为氧树脂玻璃钢的强度远高于聚氨酯泡沫的强度. 图10给出了环氧玻璃钢前后板均为2 mm,中间聚氨酯泡沫厚度不同时聚氨酯泡沫对余速的影响. 由图可知聚氨酯泡沫对剩余速度影响较小. 结合文献[5,10]可知,由于聚氨酯泡沫夹层材料增大了结构的惯性矩,进而提高了其抗剪切能力,对爆炸载荷具有良好的吸收效果,主要用于防护冲击波. 所以,在设计雷达天线罩等实际防护结构时,在保证面密度相同的情况下,更多考虑防护风力载荷和爆炸冲击波引起的挠度变形,而不是优先考虑防护破片冲击.
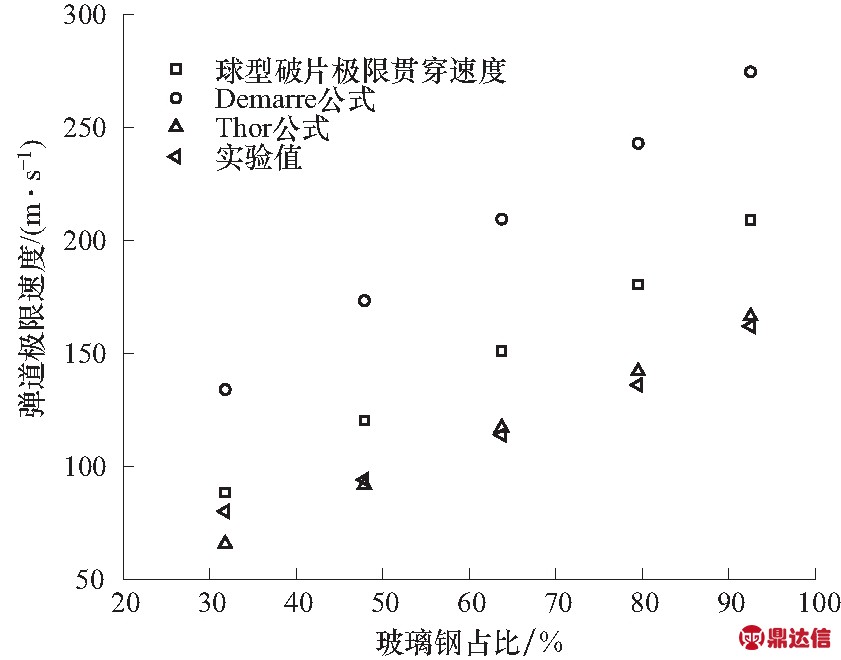
图9 面密度相同的靶板初速与余速关系
Fig.9 Relationship between initial and residual velocity of target plate with the same surface density
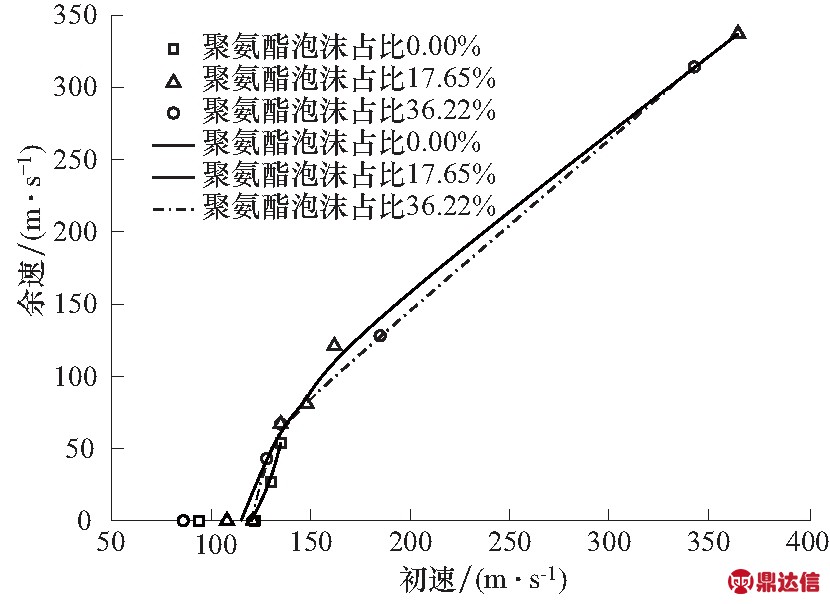
图10 不同厚度聚氨酯泡沫的初速和余速
Fig.10 Initial and residual velocities of polyurethane foams of different thicknesses
2.3 极限贯穿速度分析
靶板的极限贯穿速度指弹丸贯穿一定厚度的靶板后剩余速度刚刚为0的特殊情况,它是评估靶板抗弹性能的重要指标之一. 但在实际实验中,这种弹丸贯穿固定厚度的靶板而剩余速度恰好为0的情况一般很难发生,且往往会有“混合速度区”的出现. 在工程中,靶板的极限贯穿速度v50是取自靶板的“混合速度区”中的弹丸约50%贯穿靶板全部弹速的统计平均值.
通过上下调整法[11],采用在预计v50左右的相同发数的最高非贯穿和最低贯穿速度,对其速度平均,估算出不同组合方式夹层板弹道极限速度,如表5所示. 发现面密度相同的夹层板,其弹道极限速度随着玻璃钢占比的增大而增大. 1.4的聚氨酯泡沫靶,因为初速和余速之间的速度差太小而未能得到其弹道极限. 而对于单层靶,因为每种工况只做了4发实验,但结合图8,实验时测得的剩余速度在20 m/s左右,与入射速度相比相对较小,且图6(b)中,破片几乎恰好贯穿靶板且剩余速度为0,因此可以认为单层靶的弹道极限速度取在这个值的附近是基本合理的.
从表5中可以看出,对于单层板,弹道极限速度随着靶板后的增加而增加;对于夹层板,面密度相同时,弹道极限速度速度随着玻璃钢占比的增加而增加. 表5中,工况1.2、2.3和3.1中玻璃钢的总厚度相同,中间的聚氨酯泡沫的厚度不同,试验得到的弹道极限速度非常接近. 这是由于聚氨酯泡沫的强度远低于玻璃钢,在抗破片冲击过程中的作用有限,实验中聚氨酯泡沫对弹道极限速度的影响很小.
表5 破片贯穿每种结构靶板的弹道极限
Tab.5 Ballistic limit of fragment perforatingand specific energy absorption
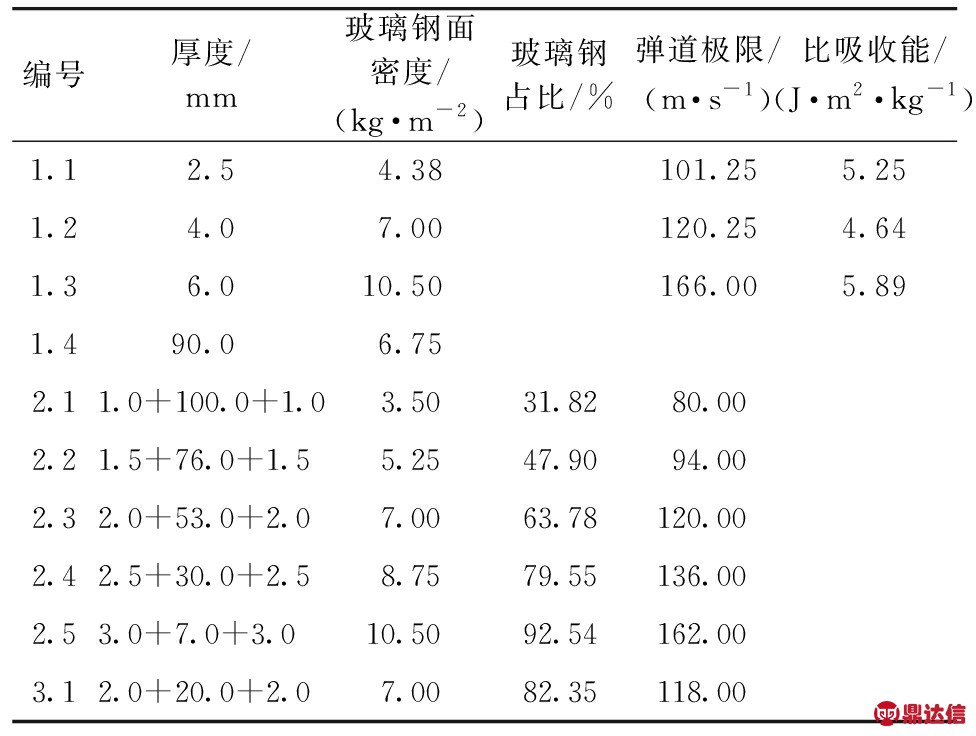
2.4 靶板抗破片冲击吸能分析
球形破片侵彻贯穿单层板或夹层板后基本没有变塑性变形,如果再忽略其弹性变形能,则可以近似认为靶板破坏和变形所吸收的能量导致了破片贯穿靶板前后速度降低,可以给出靶板的吸收能量为
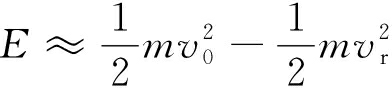
(1)
将弹道冲击试验的初始速度和剩余速度代入到式(1)中就可以计算出每发试验中靶板吸收的能量. 图11给出了5种相同面密度不同环氧树脂玻璃钢/聚氨酯泡沫组合结构夹层板的能量吸收与初始速度关系. 从图11中可以看出,在初速度基本相同时,玻璃钢在夹层板中的占比越大,夹层板抗钨球形破片冲击吸收的能量越大,玻璃钢面密度占比31.82%的夹层板吸能效果最差,玻璃钢面密度占比92.54%的夹层板的吸能效果最好. 这是由于玻璃钢的密度大约是聚氨酯泡沫的23倍多,而抗压强度却是泡沫的720倍.
从图11中还可以看出,随着钨球破片速度的增加,同一结构环氧树脂玻璃钢/聚氨酯泡沫的能量吸收都相应的增加. 在弹道极限速度附近,随着破片速度增加能量吸收几乎是快速线性增加,但当破片速度增加到一定程度后,能量吸收增加程度有限. 这种增加,是由两种材料的惯性效应和应变率共同导致的. 在初始速度较高时,试验值的离散程度较大. 这是由侵彻贯穿试验速度测量精度不足和误差计算方式造成的. 速度越高,贯穿靶板前后破片的速度降越小,高速时只有几十米每秒,此时,5%的速度测量误差就是几十米每秒. 由于正比于速度降,因此初始速度越高,测量偏差引入的能量误差就越大.
靶板受到弹丸的冲击破坏时,还经常用靶板比吸能(SEA)[12]来表征靶板的抗弹性能. 其计算公式为
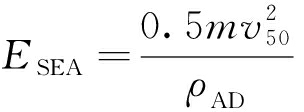
(2)
式中:ESEA为靶板比吸收能;m为弹丸质量;v50为弹道极限速度;ρAD为靶板面密度. 该方法表征的是靶板单位面密度的抗弹冲击能量吸收能力.
对于相同的破片,ρAD的增加意味着靶板相对于破片由薄靶变化为中厚靶和厚靶,吸能机理也随之变化. 2.5 cm厚单层板相对于8 mm直径球形弹丸属于薄靶范围,靶板除了局部破坏变形吸能,整体变形吸能占比较大,总的单位面密度抗弹冲击能量吸收能力较大. 随着玻璃钢厚度的增大,4.0 mm厚单层板相对于所用破片属于中厚靶范围,靶板以局部破坏和变形为主,靶板背面的稀疏波对吸能有一定影响,单位面密度抗弹冲击能量吸收能力比薄靶反而略低. 随着单层板厚度进一步增加,该球形破片所对应的极限贯穿速度增加,环氧树脂玻璃材料受冲击变形时对应的应变率增大,应变率效应导致材料的动态抗拉强度增加,破坏变形需要的能量增加,单位面密度抗弹冲击能量吸收能力比前两者都高. 还有一个因素是随着靶板厚度增加,来自靶板背面稀疏波的影响也会减小,吸能能力相应增加. 顾冰芳等[13]在高分子量聚乙烯纤维复合材料的弹道冲击试验时发现了相同的规律,并尝试将靶板的比吸能SEA拟合为了靶板面密度的二次抛物线函数. 图11给出了环氧树脂玻璃钢单层板比吸收能和面密度的二次拟合,由于试验点不足,该曲线只有定性的性质,反映基本规律.
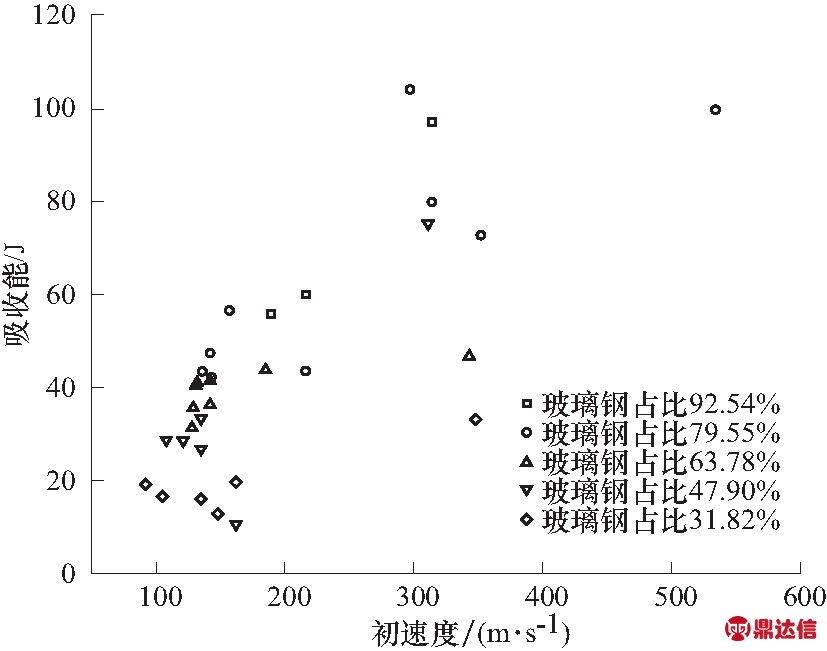
图11 面密度相同时不同夹层板能量吸收与初始速度关系
Fig.11 Relationship between initial kinetic energy and initial velocity of sandwich plates with the same surface density
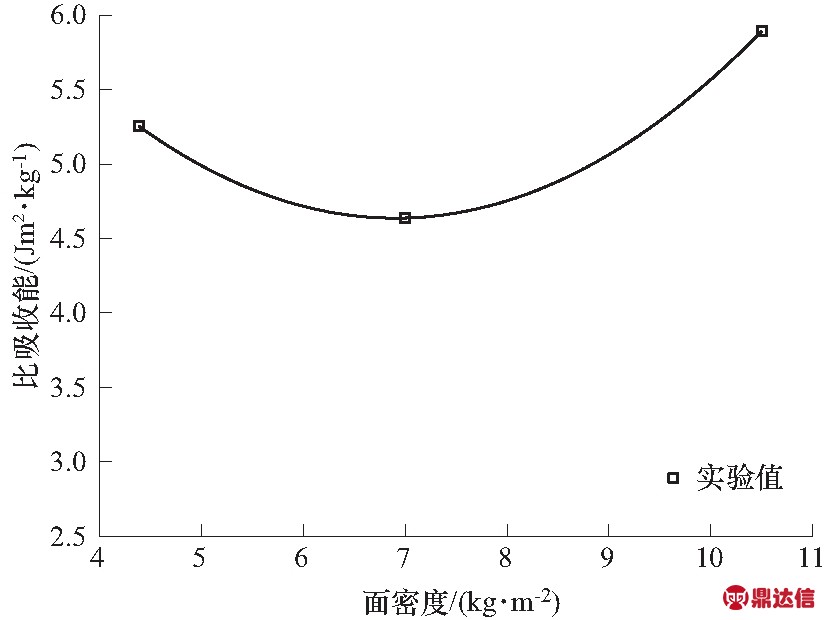
图12 单层靶ESEA与ρAD关系图
Fig.12 ESEA versus ρAD of single-layer target
3 理论模型对比分析
有很多关于破片侵彻的理论模型,这些理论模型或者说弹道极限经验公式是否适合于环氧树脂玻璃钢/聚氨酯泡沫夹层板结构的弹道速度计算还需要分析验证. 下面用一些典型的弹道极限经验公式计算出表4中5种相同面密度不同组合结构夹层板的弹道极限速度,并与实验值比较,探讨这些公式对玻璃钢-聚氨酯泡沫夹层板抗破片冲击弹道极限速度计算的适用性.
经典的球型破片极限贯穿速度公式[14]为
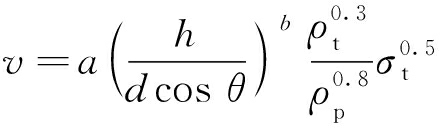
(3)
式中:h为靶厚;d为球形破片的直径;ρt为靶板的密度;ρp为破片材料的密度;σt为靶板的强度极限;a和b为靶板材料相关常数,这里a=5.47,b=0.84.
DeMarre(德·马尔)[15]在量纲分析和实验数据的基础上建立的弹丸侵彻装甲钢板的经验公式为
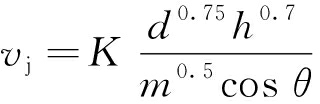
(4)
式中:vj为破片对靶板的极限贯穿速度;θ为破片飞行方向与靶板法线夹角;m为破片的质量;K为穿甲复合系数,这里K=52 935.
根据不同弹丸侵彻铝、钢、防弹玻璃等材料的实验数据拟合得到的可预测极限穿透速度估算的修正的THOR公式[16]为
vr=v0-0.3 048×10C1(61 023.75×hA)C2×
(15 432.1×m0)C3g(sec θ)C4(3.280 8×v0)C5(sec β)C6
(5)
式中:m0为破片初始质量;A为破片平均碰撞面积;β为攻角;C1~C6是与靶板材料相关系数,其中,C1=6.399,C2=0.889,C3=-0.945,C4=1.262,C5=0.019,C6=-0.813 2.
计算过程为:先通过密度强度等效原则将玻璃钢-聚氨酯泡沫夹层板等效为一定厚度的Q235钢靶,然后代入这些公式得到图13. 从图13可以看出Demarre公式与实验值相差较大,并不适用于复合材料夹层板极限贯穿速度的预估;球形破片极限贯穿速度仅在低速范围内,实验值与理论值接近;THOR公式在各个工况的计算结果与实验值均比较接近,可用于球形破片侵彻靶板的极限贯穿速度的计算,对比以上的结果THOR公式更适用于这种复合材夹层板弹道极限速度的预估.
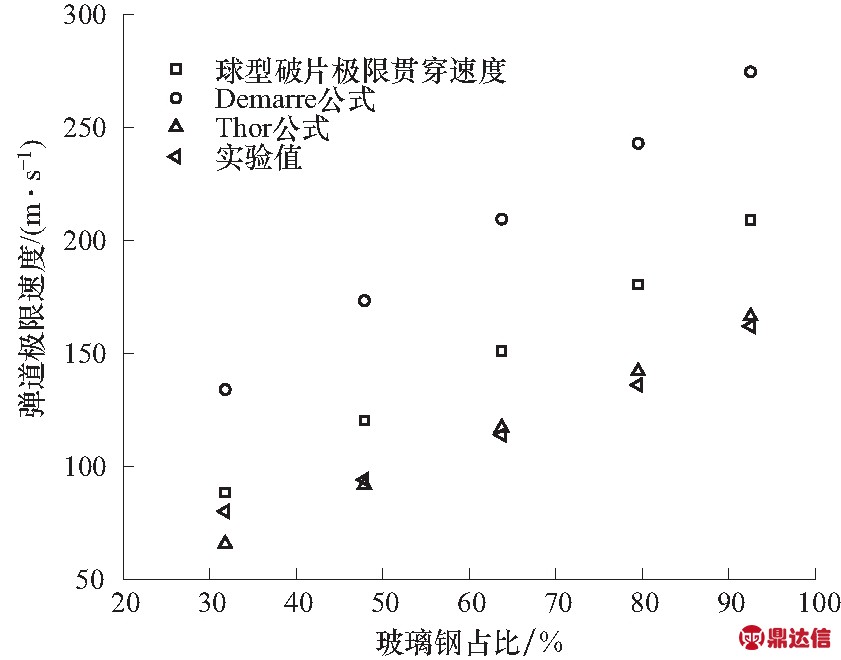
图13 贯穿速度理论公式值与实验值的比对
Fig.13 Comparisons of limited velocity formulas
4 结 论
① 通过靶板的破坏形貌观察可以看出:玻璃钢的破坏模式主要为玻璃纤维剪切破坏和拉伸断裂;其主要吸收能量方式为纤维与基体脱粘,抽拔、拉伸断裂.
② 聚氨酯泡沫抗弹性冲击吸能较差,作为夹芯材料主要用于吸收爆炸冲击波能量.
③ 由于环氧树脂玻璃钢的抗压和抗拉强度远大于聚氨酯泡沫,在相同面密度下,夹层板的吸能随着玻璃钢占比的增加而增强,弹性性能随着玻璃钢占比的增大而提高.
④ 环氧树脂玻璃钢单层板的抗弹冲击能力随着厚度的增加而增加,比吸收能和面密度之间呈二次函数抛物线关系.
⑤ 对于不同结构的夹层板,用3种理论公式计算得到的弹道极限速度与实验估算出的弹道极限速度比对发现,THOR公式更加适用于这种复合材料夹层板的弹道极限速度计算.