摘 要:电源汇流板是雷达产品供电系统的重要组件,需要较高的可靠性,其中焊接质量的保障尤为关键。某雷达产品中应用的电源汇流板采用内部加厚的覆铜板设计,同时又采用铝板作为安装底板,大电流、高热容量的设计给电源汇流板的焊接带来了很大的困难。文中主要针对大电流、高热容量的电源汇流板,分析焊孔透锡率的影响要素并提出工艺解决方案,经过工艺试验验证,将电连接器引脚的透锡率从20%逐渐提高到85%,解决了焊接难题,对软钎焊焊接工艺具有一定的参考价值。
关键词:电源汇流板;高可靠性;透锡率
引 言
随着电子产品向小型化、便携化和高性能方向发展,印制电路板制造也向多层化、功能化和集成化方向飞速发展。印制电路板的层数越来越高,依据印制板设计规范,其中存在多层大面积覆铜层。将通孔元器件的引脚焊接至连接大面积覆铜层的通孔焊盘时,焊点的形态、外观很难满足要求,主要是焊点渗锡不良现象。美国标准IPC-A-610D 中将少于75%焊料填充的通孔焊点视为不合格焊点。此类不合格焊点的机械强度不足,还会造成助焊剂残留、孔内焊料体与镀铜层交界面应力集中等缺陷,在后续力学环境、热环境等试验条件下可能导致焊点失效[1]。
电源汇流板作为雷达供电链路的重要组件,通常采用多层的大面积、厚铜箔覆铜板,给制造工艺带来了新的挑战,主要是焊接过程中焊料不易达到熔点温度,流动性不足,会导致通孔元器件的透锡率难以达到75%以上。
本文主要针对某电源汇流板焊接透锡率低的问题进行原因分析并开展试验研究,通过采取不同的工艺措施,将通孔元器件的焊点透锡率从20%逐渐提高到85%,解决了大电流汇流板的焊接难题。
1 汇流板结构及特点
图1 为电源汇流板典型结构图。电源汇流板主要由多层印制板、电连接器、安装底板等组成,结构轻量小巧。电连接器从安装底板的正面安装后,引脚与多层印制板需要采用熔点为183 ◦C 的锡铅焊料进行软钎焊连接。
电源汇流板的多层印制板采用10 层叠层结构设计,见图2。其中第3,4,6 和7 层为大面积电源层,需要经过大电流,设计上采用厚度不小于0.21 mm的覆铜层,其他层采用35 µm 的覆铜层。整体板厚3.4 mm,其中铜层厚度累计为1.26 mm。
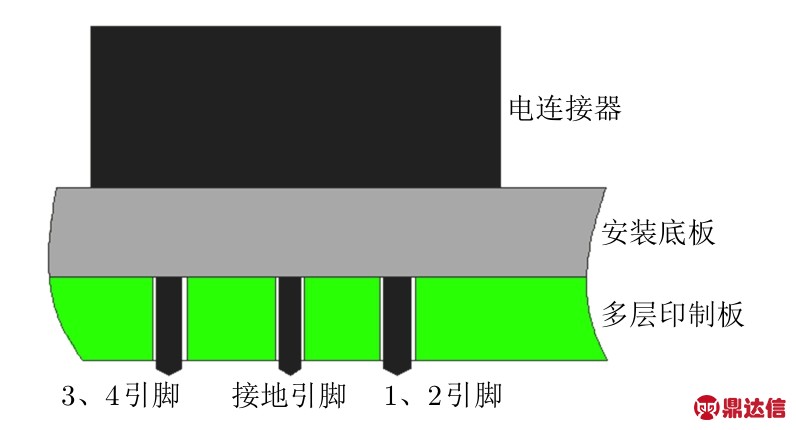
图1 电源汇流板结构
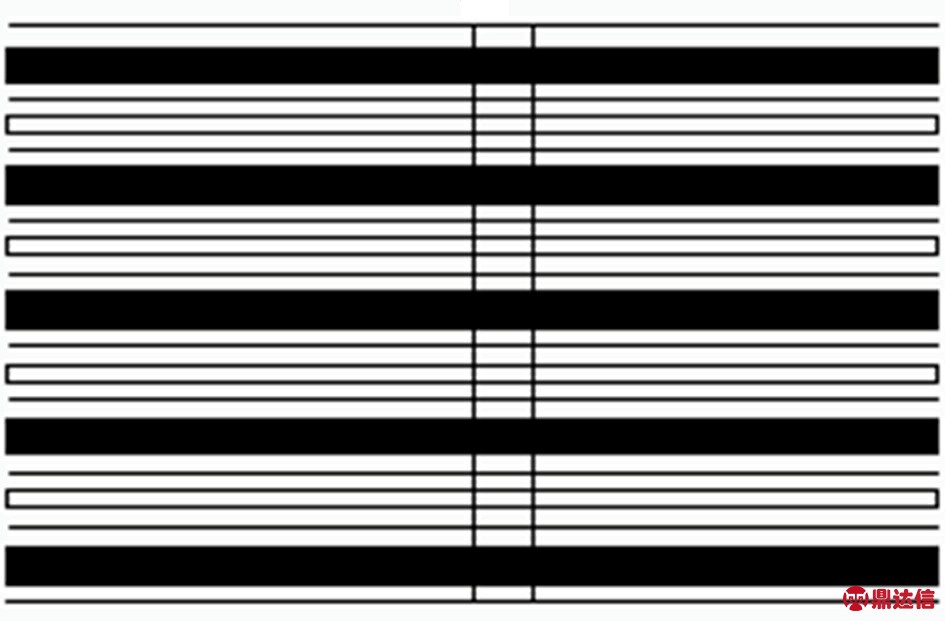
图2 多层印制板结构
电源汇流板的安装底板采用厚度为4.5 mm 的5A05(H112)铝板加工而成。电连接器的引脚采用镀金涂覆。
将电源汇流板预烘至85 ◦C 并保温1 h,采取400 ◦C 控温烙铁手工焊接的工艺方法焊接后,通过X光扫描检测发现电连接器的引脚透锡率平均只有20%(图3),远低于美国标准IPC-A-610D 和SJ 20632《印制板组装件总规范》规定的金属化通孔75%的透锡率,满足不了产品使用要求。
由于电源汇流板采用了内部铜箔加厚的覆铜板设计,形成了高热容量的特点,同时薄层安装底板直接与多层印制板接触,因此焊接时焊点散热快,加剧了焊接难题。
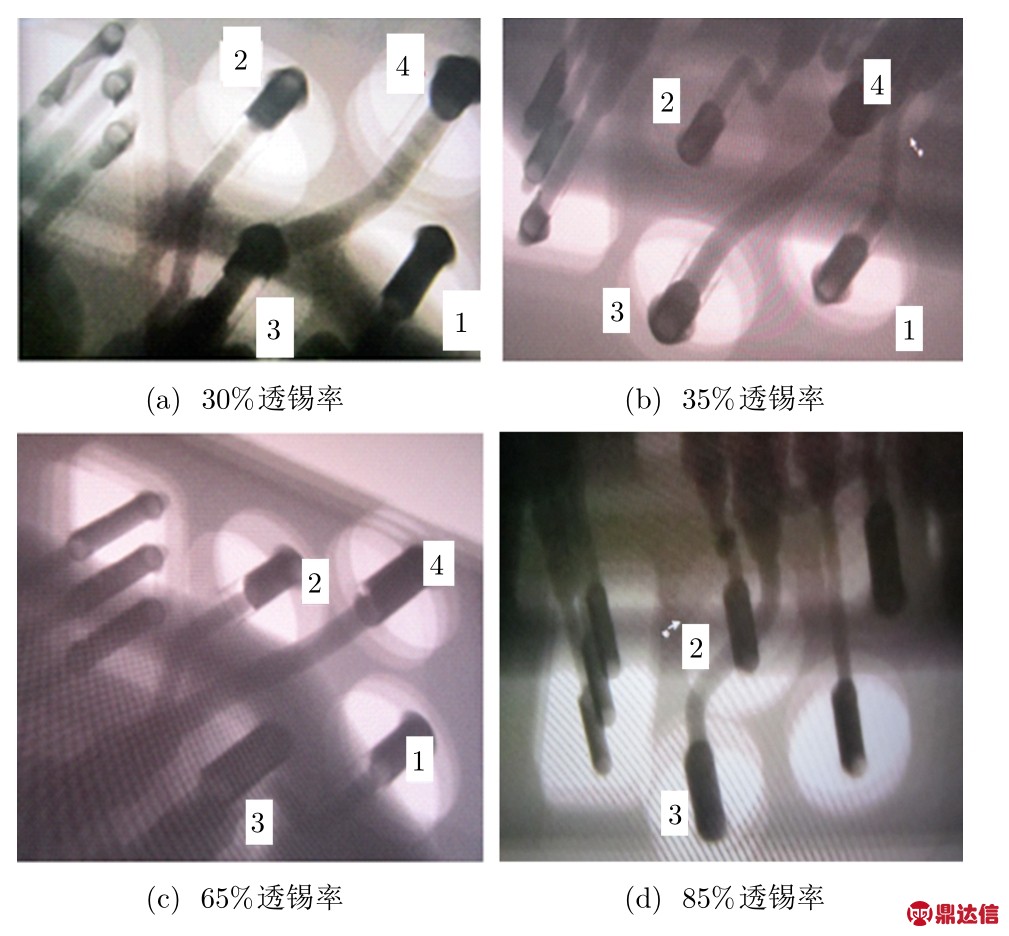
图3 电连接器引脚超低的透锡率
2 透锡率影响因素分析及解决方案
2.1 透锡率的影响因素分析
对电源汇流板结构进行分析后可知,影响电连接器引脚透锡率的因素有:
1)印制板金属化孔与电连接器引脚的可焊性。经分析,该汇流板金属化孔和电连接器的引脚都为镀金层,经过可焊性试验,可焊性良好,满足焊接要求。
2)印制板金属化孔与电连接器引脚之间的透锡间隙。经过分析,1—4 引脚的透锡间隙为0.4 mm,另外3 个接地引脚的透锡间隙为0.2 mm。一般情况下采用手工焊接工艺时,金属化孔孔径比元器件引线直径大0.2 ~0.4 mm;采用波峰焊焊接工艺时,金属化孔孔径比元器件引线直径大0.2 ~0.3 mm,该汇流板透锡间隙在合理范围内,满足焊接要求。
3)焊接温度和时间。一般印制板元器件的锡铅焊接温度为320 ◦C 左右,焊接时间为3 ~5 s,安装底板与电连接器、多层印制板大面积直接接触,在一定程度上起到了散热器的作用,手工焊接过程中电连接器引脚的温度很难均衡保持,焊接过程中焊料无法到达焊孔的深处。图3 中采用手工焊接工艺方法,引脚平均只有20%的透锡率也就不足为奇了。
4)焊料流动顺畅性。焊接过程中,焊料的流动性要好,没有“憋气”结构。根据SJ 20632《印制板组装件总规范》中要求,元器件与印制板表面之间至少保留0.25 mm 的透气间隙,便于焊接、清洗和涂覆操作。然而,分析电源汇流板的结构发现,电源汇流板由于整机安装空间受限,在高度设计上尽量压缩,印制板与安装板之间采用零间隙设计,直接导致焊料的流动性很差,造成电连接器引脚的透锡率很低。
经过分析,电源汇流板电连接器引脚透锡率低的主要因素为焊接过程中焊接温度达不到焊接材料的熔点温度,焊料的流动性不足。
2.2 工艺解决方案
经过焊接透锡率的影响因素分析,决定采取以下几种工艺方案提高引脚的透锡率:
1)在印制板与安装底板之间增加0.5 mm 厚的垫片,增加透气间隙提高焊料的流动性。电源汇流板结构改善图如图4 所示。
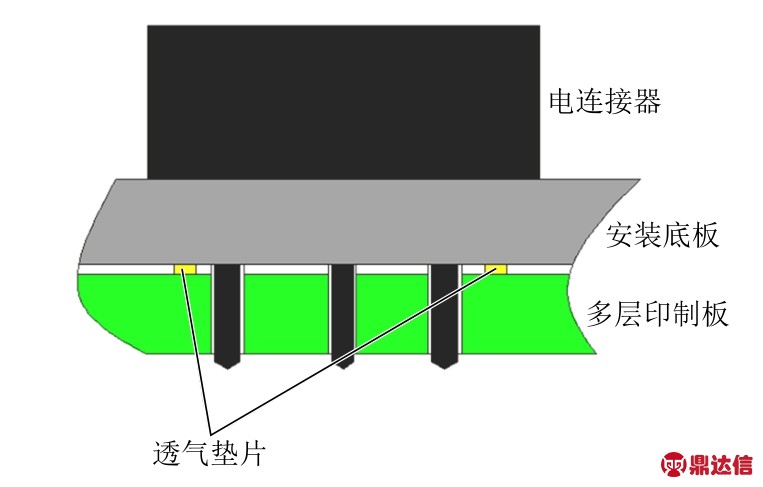
图4 电源汇流板结构改善图
2)提高电源汇流板的预烘温度,将预烘温度从85 ◦C 提高到120 ◦C。
3)在增加透气垫片的基础上,采用波峰焊设备焊接代替控温烙铁手工焊接。波峰焊就是借助泵的作用将熔融的液态焊料在焊料槽液面形成特定形状的焊料波,插装了元器件的印制板置于传动链上,以某一特定角度和一定的浸入深度穿过焊料波峰,从而实现焊接过程。通过波峰焊设备焊接能够获得更好的焊点。
4)在增加透气间隙的基础上,焊接前对金属化孔和电连接器引脚增涂助焊剂再进行波峰焊。
3 工艺措施试验验证
3.1 试验验证1
在多层印制板与安装底板之间增加0.5 mm 透气间隙,预烘至85 ◦C 再保温1 h,采用控温烙铁进行400 ◦C 手工焊接。焊接后进行X 光扫描检测发现,1—4 引脚的透锡率平均约为30%,说明通过增加透气间隙减少“憋气”影响能够在一定程度上改善透锡率,但仍不满足要求。
3.2 试验验证2
在多层印制板与安装底板之间增加0.5 mm 透气间隙,提高预烘温度至120 ◦C 并保温1 h,采用控温烙铁进行400 ◦C 手工焊接。焊接完成后对电连接器的焊点进行X 光检测,发现1—4 引脚的透锡率平均只能达到35%左右,说明单纯提高汇流板的预烘温度不能持续保证焊点处的基础温度,焊锡熔融和流淌不足,仍无法实现透锡率75%的目标。
3.3 试验验证3
在多层印制板与安装底板之间增加0.5 mm 透气间隙,预烘至70 ◦C,采用波峰焊设备焊接,波峰焊参数设置为:480 ◦C,520 ◦C 和150 ◦C 3 温区预热;链速0.4 m/min;锡锅温度260 ◦C。焊接后进行X 光扫描检测发现,1 和2 引脚平均透锡率为50%,3 和4 引脚平均透锡率达80%以上,焊点透锡率有了很大的提升。试验表明,通过改变焊接方式,采用波峰焊设备焊接代替手工焊接,焊点处的基础温度得到有效保证,大大提高了焊点的透锡率。
3.4 试验验证4
在多层印制板与安装底板之间增加0.5 mm 透气间隙,预烘至70 ◦C,焊接前对金属化孔和引脚增涂助焊剂,波峰焊参数设置同试验3。焊接后进行X 光扫描检测发现,1—4 引脚的透锡率均达到了85%以上。试验结果表明,在试验3 的基础上对金属化孔和引脚增涂助焊剂,进一步提高焊锡浸润性,效果明显,达到了焊接质量要求。
3.5 试验结果
通过4 种不同工艺措施进行试验验证,将电连接器1—4 引脚的平均透锡率从30%逐渐提高到85%。图5 是电连接器1—4 引脚平均透锡率的提升图,表明提出的工艺解决方案有效可行。
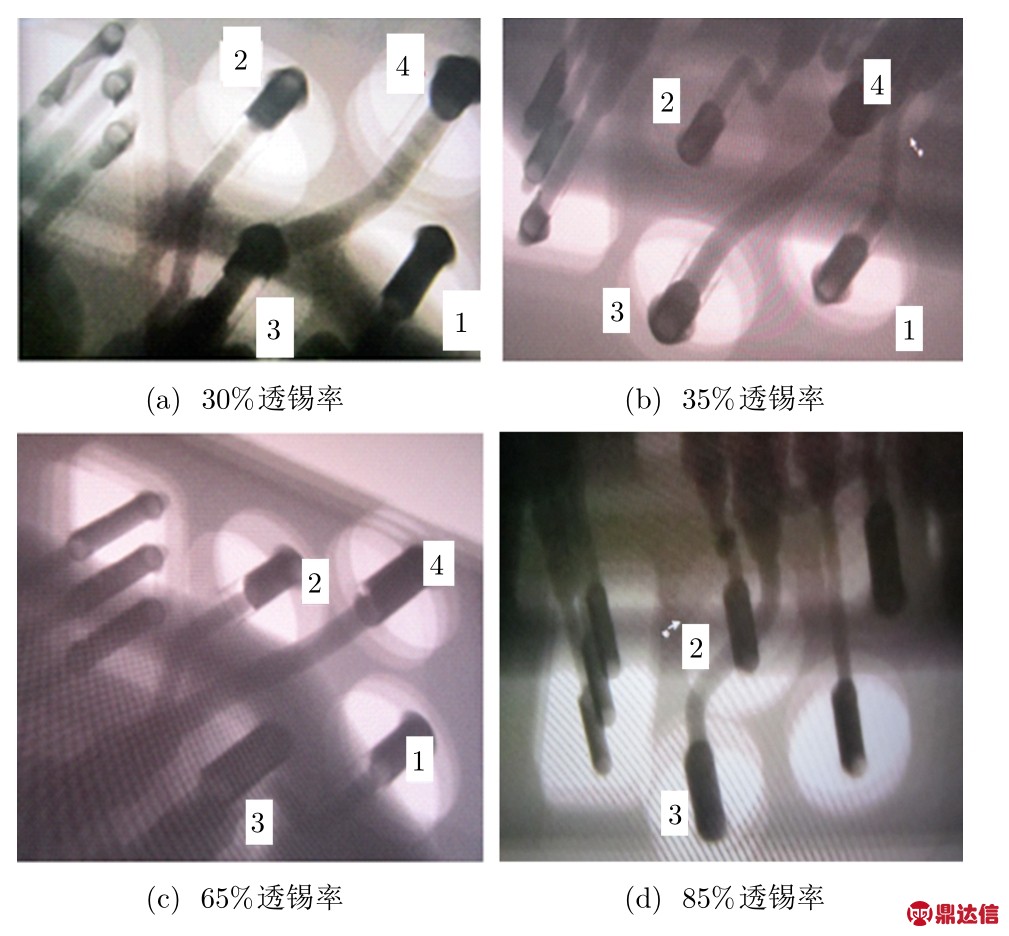
图5 电连接器引脚透锡率
4 结束语
综上所述,通孔元器件与大面积覆铜层的多层印制板焊接时,需要考虑的设计和工艺因素有:
1)印制板设计时,连接的大面积覆铜层要尽量小,覆铜层不得高于0.21 mm。若覆铜层高于0.21 mm,可改变印制板的金属化孔形状,可将通用的圆柱型设计成“米”字分叉型。
2)通孔元器件与多层印制板之间最好有0.5 mm以上的透气间隙,避免焊接过程中的“憋气”现象。
3)设计选型通孔元器件时,既要考虑引脚的可焊性,还需考虑与印制板金属化孔之间的透锡间隙。一般情况下,采用手工焊接工艺时,透锡间隙为0.2 ~0.4 mm;采用波峰焊焊接工艺时,透锡间隙为0.2 ~0.3 mm。最好选择较大的透锡间隙以利于焊料的流动性。
4)最好采用波峰焊设备代替传统的手工焊接,可以获得更可靠的焊点。焊接参数要通过试验获得。
5)焊接时对元器件引脚及印制板的金属化孔增涂适量的助焊剂能获得更好的焊点。
6)焊接前,要设置合理的预热温度,要综合考虑零件材料和镀层的耐温性。
本文针对某大电流高热容量汇流板的通孔透锡率进行了比较全面的工艺研究,解决了产品实际需求,对电子设备软钎焊接工艺具有一定的普适性指导意义。但本研究所针对的对象和焊接方法还有必要进一步深入,在焊接手段的实现上,除了采用波峰焊接设备之外,还需探索别的实现手段,多层叠加印制板焊接厚度的极限等问题还需要进一步的研究。