摘要:本文围绕电动自行车用长寿命铅酸蓄电池的研发,从电池内部结构设计、板栅合金、固化及充电化成工艺四个方面进行了研究。实验结果表明:采用整体铸焊、汇流排直连胶封的结构,能够延长大电流用户电池的使用寿命;板栅合金中添加稀土和银,能够提高板栅的耐腐蚀性和蠕变强度;合理的固化工艺及充电量可使板栅和活性物质的结合强度提高,大大延长电池的使用寿命。
关键词:长寿命电池;电动自行车;板栅;固化;内化成
0 引言
随着电动自行车性能的改进,要求电池使用寿命越来越长。所以,近两年一些电动自行车生产厂家要求将电池的三包期提高到两年以上,同时对电池高倍率放电性能提出了更高的要求。为了适应整车厂的要求,研究超长寿命的蓄电池显得越来越紧迫和重要。但由于环保的进一步趋紧,寿命性能相对较好的铅锑镉合金已处于禁用状态,铅钙合金成为了自行车电池的首选合金,而铅钙合金电池寿命的影响因素众多,寿命相对较短。本文对电池的结构设计、板栅合金、极板固化和化成充电工艺进行了研究,探讨如何延长铅钙合金电池的寿命。
1 长寿命电池结构设计
在常规电池外观尺寸不变的前提下,对电池内部结构进行了一种新的设计,主要目的是提高电池在高倍率放电条件下的使用寿命,以满足目前市场上大电流骑行条件。
1.1 结构设计
首先汇流排采用整体铸焊、直连的结构,电池内部结构如图 1 所示。在该设计结构下,导电路径得到缩短,因而减少了放电过程中的电阻[1],提高了放电过程中的电压平台;其次采用汇流排整体胶封,结构如图 2 所示,汇流排胶封后能够减少电解液对连接处的腐蚀,因而避免了汇流排在使用过程中因腐蚀而导致内阻增大和寿命缩短。
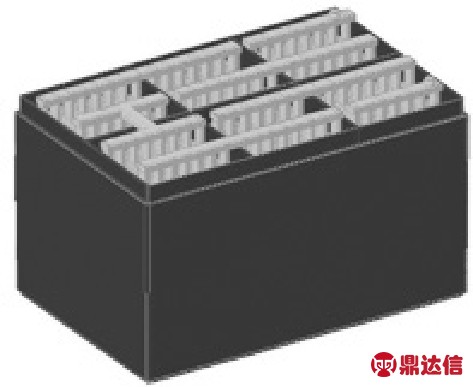
图 1 汇流排直连示意图
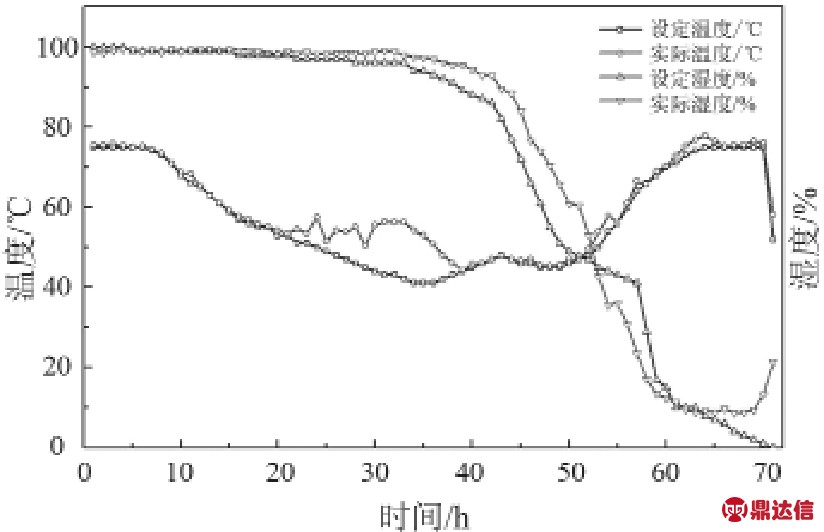
图 2 汇流排胶封示意图
再次对负极汇流排长度进行了加长设计,让汇流排直接架在电池槽的槽沿上,结构如图 3 所示,在铸焊前不进行捏两边负板极耳的操作,避免了两边负板极耳内弯给极群带来的损伤;最后该结构设计将端极柱与汇流排都连为一体,在汇流排进行胶封时对极柱底部处也进行了密封,结构如图 4 所示,减少了端子处爬酸的可能。
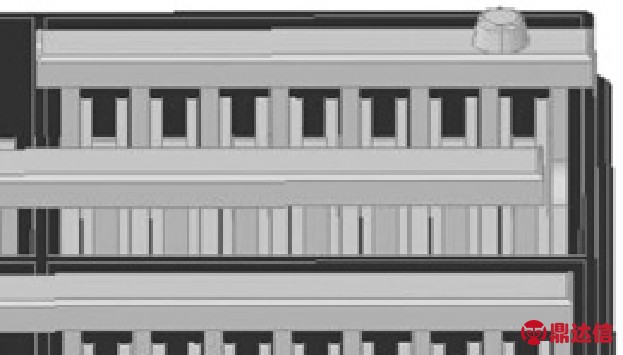
图 3 负极汇流排加长示意图
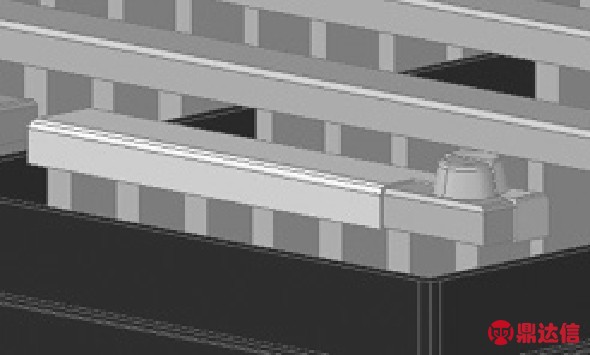
图 4 汇流排极柱一体胶封示意图
表 1 新结构与常规结构 6-DZM-12 性能测试
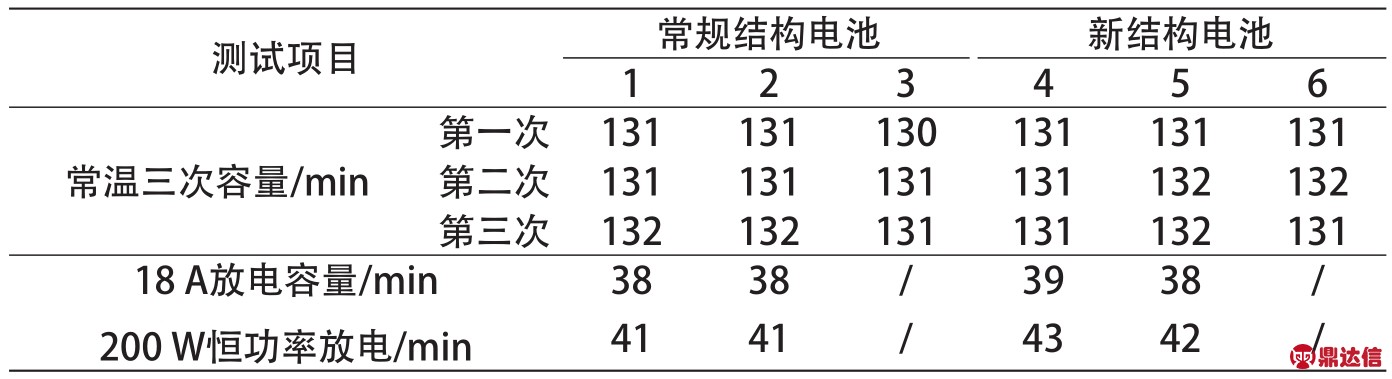
1.2 样品初期性能测试
根据改进结构的设计,开制了塑壳及铸焊模具,试制样品电池,进行常温容量测试,除此之外,因为目前市场上电动自行车起动及行驶最大电流有的达到了 1.5C,所以对 6-DZM-12 型号电池进行了 18 A 大电流放电性能及 200 W 恒功率放电测试,数据如表 1 所示。
从常温容量及 18 A 放电容量来看,新结构和常规结构电池性能几乎无差异,我们对 18 A 大电流放电过程和 200 W 恒功率放电过程的电压变化进行了分析,放电曲线如图 5 和图 6 所示。从放电曲线图上可以看到新结构电池的电压平台明显要高于常规结构电池的,具体在用户使用过程中,会明显感觉在骑行的过程中,新结构的电池要比常规结构的电池动力更强劲。
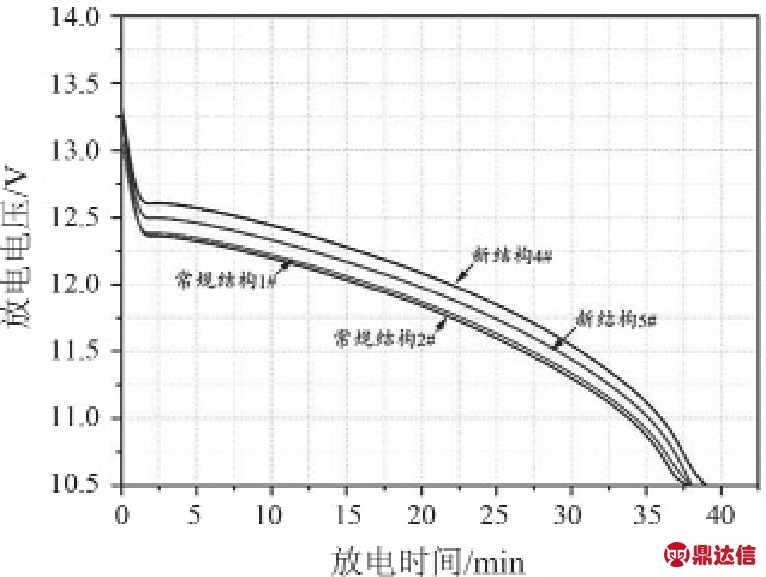
图 5 18 A 大电流放电电压变化曲线图
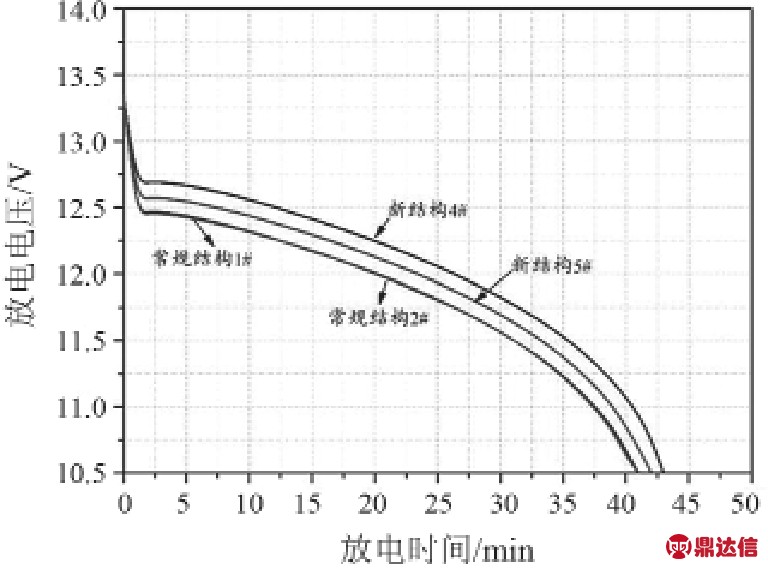
图 6 恒 200 W 功率放电电压变化曲线图
2 长寿命电池板栅
板栅是电池长寿命的基础,如何提高板栅的耐腐蚀性显得尤为重要,这与板栅用合金配方、铸造工艺、极板固化及电池化成均有关系[2]。对于深循环用途的动力电池而言,铅钙锡铝四元合金在耐腐蚀方面同国家明令禁止的铅锑镉合金存在一定的差距,使用过程中发现晶间腐蚀严重,制约了电池寿命的提高[3],因此,必须寻找更耐腐蚀的板栅合金来提高板栅的耐腐蚀性能。
2.1 合金配方
为了研究合金的耐腐蚀性能,选择了三种合金配方,见表 2 。对三种合金,分别铸造了恒流腐蚀样:20 mm×20 mm×2 mm 的方形合金样品,负板为电解铅合金铸造,尺寸同正板相同。按照一正两负进行装配,在恒温 25 ℃ 环境中,电流密度在10 mA/cm2,电解液为 1.28 g/cm3H2SO4,恒流腐蚀 15 d,腐蚀结束后采用糖碱溶液剥离腐蚀产物,真空干燥后进行称重,计算腐蚀失重,结果如图 7所示。
从图 7 可以看到,1# 铅钙锡铝四元合金腐蚀速率在 5.22 mg/(cm2・d),加入稀土元素以后,2# 合金的耐腐蚀性能得到显著提高,腐蚀速率下降到4.37 mg/(cm2・d),3# 合金样品在稀土元素的基础上,通过添加质量分数占 0.022 % 的 Ag,耐腐性能进一步提高,腐蚀速率最低,为 4.02 mg/(cm2・d),因此通过在铅钙锡铝四元合金中添加稀土和银,能够显著降低合金的腐蚀速率,提高板栅的耐腐蚀性能。此外 Ag 的加入在提高耐腐蚀性能的同时,加快了合金的时效硬化速度,便于铸板过程中的脱模和定位操作,还可提高合金材料的抗蠕变强度,减少充放电过程中应力下的腐蚀,抑制寿命过程中正极板栅的生长,因此 3# 合金成为长寿命电池板栅材料的首选。
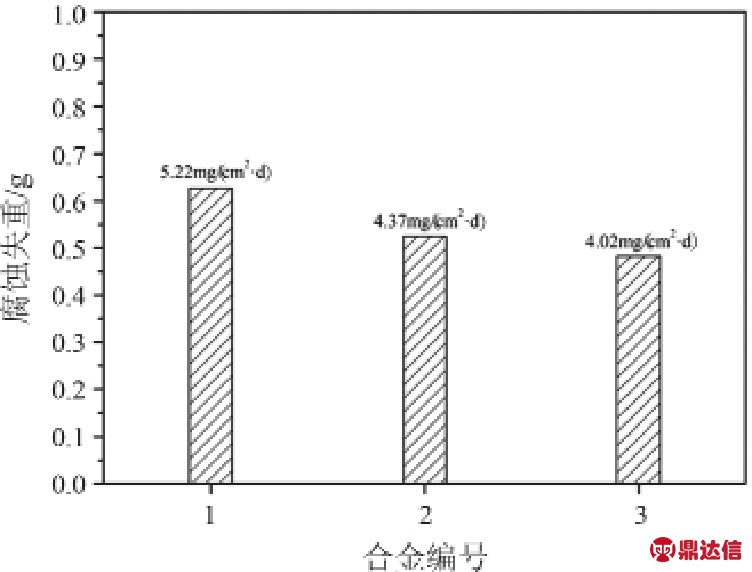
图 7 不同配方合金恒流腐蚀失重
表 2 不同配方合金元素含量

3 长寿命电池正极板固化
固化是铅酸蓄电池生产中一道关键工序,良好的固化不仅要使活性物质中游离铅的质量分数降低到 3 % 以下,板栅形成良好的腐蚀层,还要使活性物质彼此之间有良好的结合强度,固化的好坏严重影响电池的寿命[4]。
针对长寿命电池正极板的特点,对目前常规的固化工艺进行了改进,图 8 和 9 分别为固化工艺改进前后极板游离铅和水分的变化曲线。从图 8 可知,固化前游离铅的质量分数都为 12 % 左右,干燥结束后都在 2.5 %~3.0 % 之间;不同的是在固化结束后,改进前游离铅的质量分数为 6.0 % 以上,改进后降低到 3.0 % 左右。从图 9 可知,固化前极板中水的质量分数都为 8.5 % 左右,干燥结束后都约为 0.15 %;不同的是在固化结束后,改进前水的质量分数为 8.0 % 左右,改进后降低到 4.5 % 以下,改进前水分在固化阶段下降缓慢,改进后水分在固化和干燥阶段呈直线趋势下降。
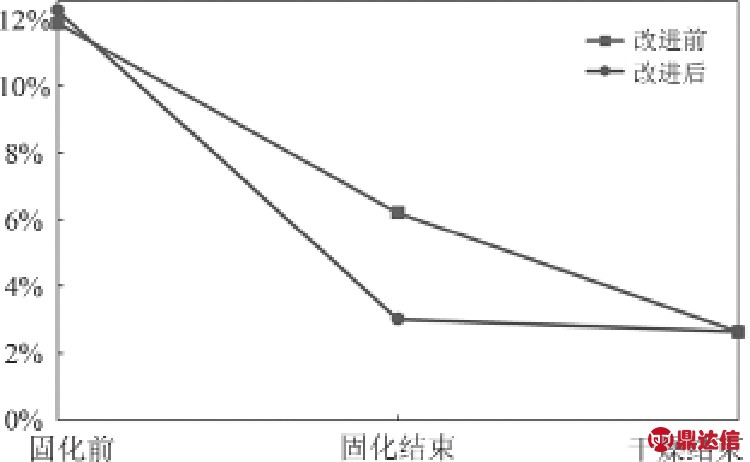
图 8 固化工艺改进前后游离铅的变化曲线
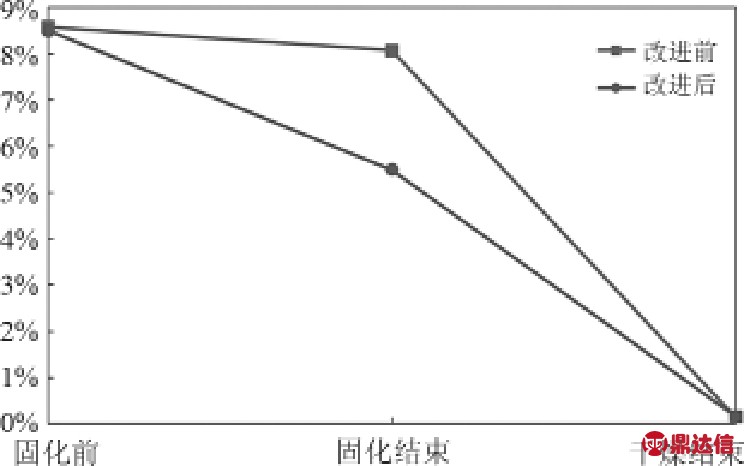
图 9 固化工艺改进前后水分的变化曲线
图 10 为本次改进后长寿命电池正极板的固化工艺,固化过程中温度由 75 ℃ 降至 57 ℃ 时,极板表面无凝露现象,温度由 57 ℃ 降到 40 ℃ 及湿度下降阶段,从曲线上可以看到实际温度下降至50 ℃ 左右时便很难再下降,推测此时为游离铅快速反应阶段,放出大量的热[5],从图 8 游离铅的变化也可以印证,本次实验的固化工艺,游离铅氧化主要发生在固化阶段。这里要说明的是湿度与设定值前期吻合较好,后期湿度下降阶段滞后于工艺设计,这主要是受限于固化室条件。固化结束后取样敲掉铅膏后,生极板铅膏和板栅表面颜色呈现均匀的桔黄色,表明板栅均匀腐蚀,与铅膏之间形成了良好的结合层,对电池寿命的提高奠定了基础。
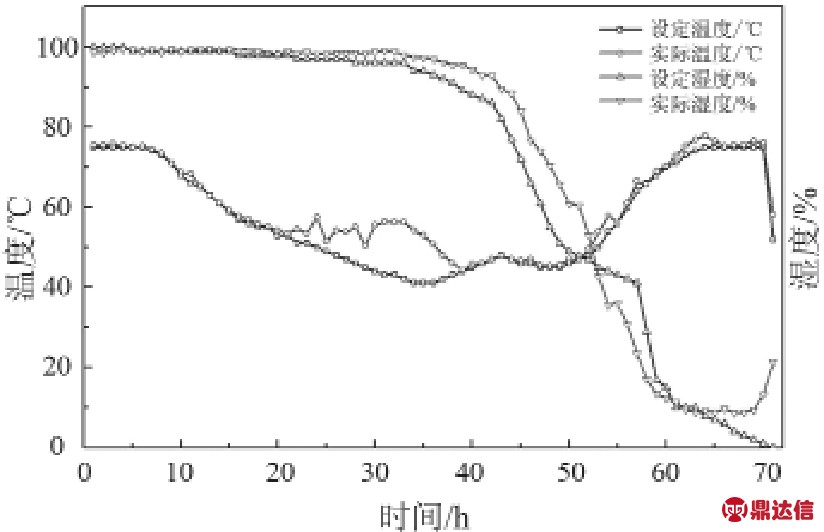
图 10 固化过程记录曲线图
4 长寿命电池充电化成
电池化成工艺主要控制电解液密度、加酸量、加酸后电池静置时间、化成过程温度和充电量等因素[6]。笔者对电池化成工艺进行了大批量实验,在长寿命电池充电化成工艺中,减少了化成净充电量,表 3 所示是对同一批 6-DZM-12 型号电池,采用两种工艺进行化成后极板的理化指标和电池的常规性能,该批实验电池采用整体铸焊、汇流排直连的结构,板栅为 3# 合金成分。
从表 3 数据可以看出,两种化成工艺下正板中二氧化铅以及负板海绵状铅的含量基本接近,说明工艺 2 在减少充电量的情况下,极板活性物质已经完成转化。工艺 1 中过多的充电量对活性物质已无明显作用,主要起到分解水的作用,这样也加速了正板栅的腐蚀。虽然对于两小时率容量来说,采用工艺 2 只能达到 126 min,比采用工艺 1 时放电容量小了些,但仍在标准要求以上,这主要是由于电解液密度对放电容量产生了的影响,电解液的密度越低,电池的放电容量越少,这从电池化成结束后静置 24 h 开路电压也可看出。对同一批电池进行配组,图 11 为采用工艺 1 和工艺 2 的实验电池整组(4只)全充全放循环寿命测试。
表 3 不同化成工艺的极板理化指标和电池常规性能
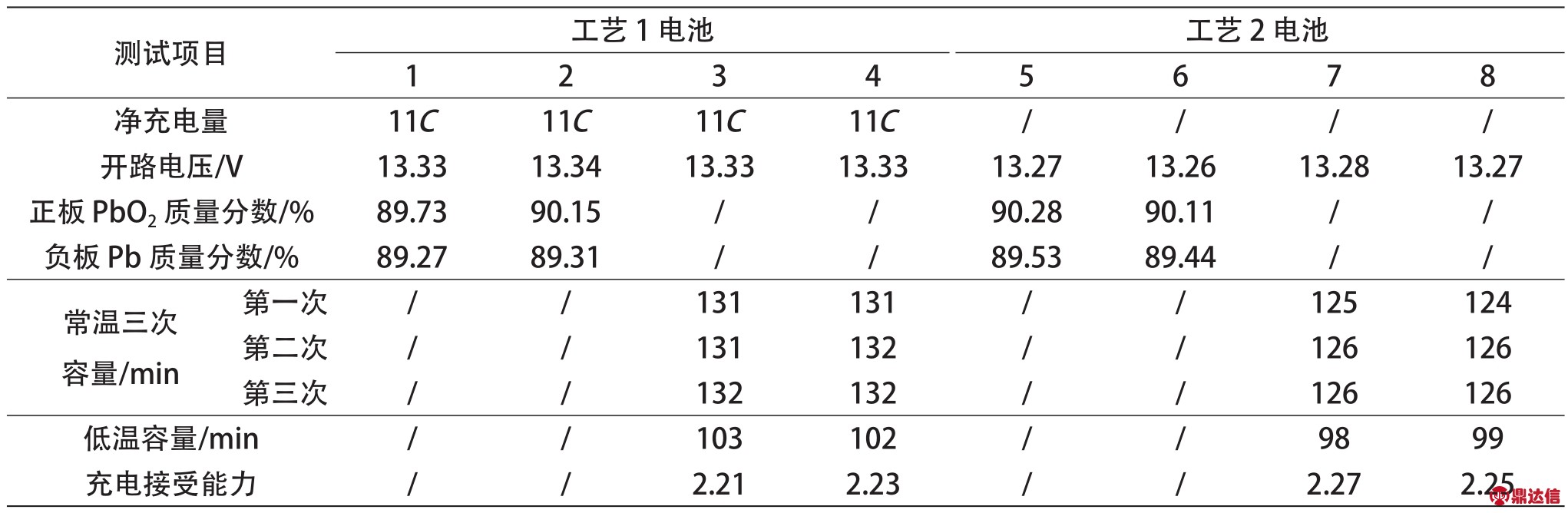
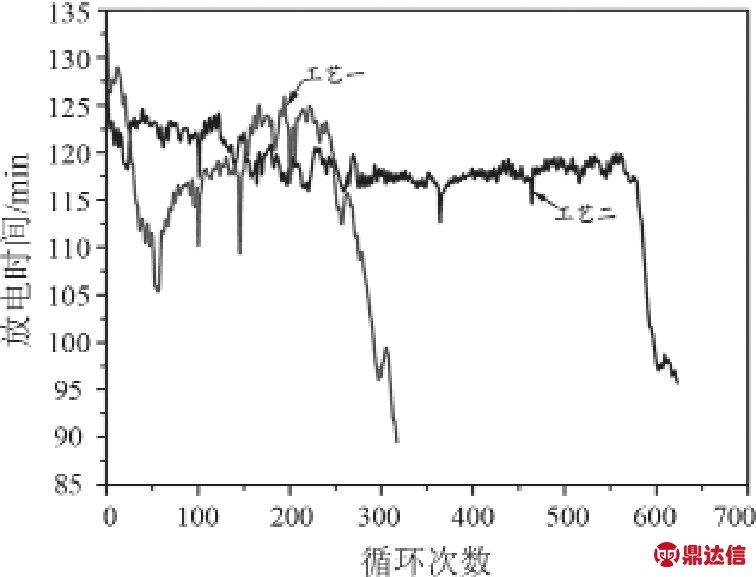
图 11 不同化成工艺的实验电池循环寿命
从图 11 中电池的寿命曲线可以看出,采用工艺 1 的实验电池的寿命在循环 250 次后开始出现明显衰减,寿命终止后对其进行了解剖分析,解剖照片如图 12(a) 所示,正极活性物质整层脱落,而采用工艺 2 的实验电池寿命明显延长,达到了 623次,解剖照片如图 12(b) 所示,未发现活性物质脱落,这显然与充电工艺有关。充电过程中如果充电量过多,在活性物质完成转换后多余的电量会做无用功,也就是腐蚀板栅和析气,同时带来温升。过度的板栅腐蚀以及化成后期大量的析气是板栅与活性物质结合强度变差的原因。
工艺 2 实验电池后续出现寿命急速衰减主要是由于整组的一致性问题,对落后电池进行了解剖失效分析,正极汇流排如图 13(a) 所示,可以看到汇流排还具有金属光泽,显然这是胶封起了作用,正极板活性物质出现了软化,图 13(b) 为解剖后的正极板栅,可以看到板栅虽然出现腐蚀,但是还比较完整,另外从整个板栅外观来看,板栅并没有发生蠕变长大,进一步验证了 3# 合金配方的耐腐蚀性能和抗蠕变性能。
该组实验电池对外放电总容量是 7333.06 Ah,平均每次放电容量为 11.7 Ah,按照电动自行车时速 20 km/h 计算,累积行驶里程达 2.4×104km,这样的电池应该能满足用户两年的使用要求。
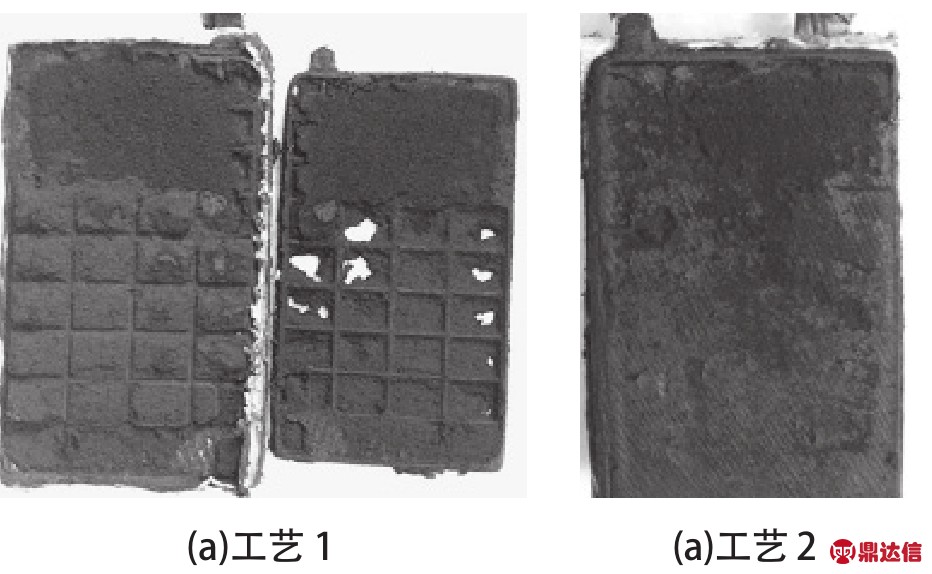
图 12 电池寿命终止后解剖正极板
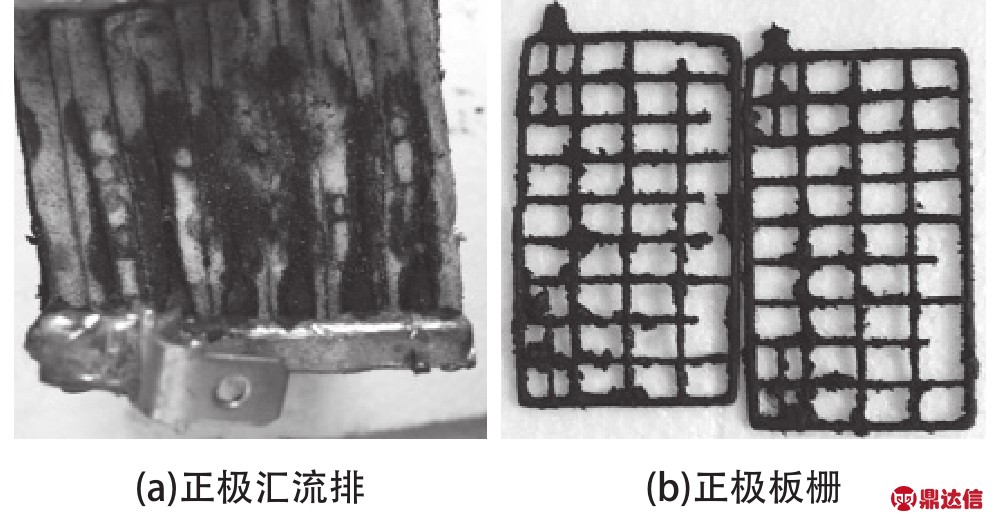
图 13 工艺 2 电池寿命终止后正极汇流排和板栅
5 结论
本文通过上述研究得出:
(1)采用整体铸焊、汇流排直连胶封的结构,能够满足大电流用户的使用要求,延长大电流用户的使用寿命;
(2)通过在板栅合金中添加稀土和银,能够显著提高板栅的耐腐蚀性能和抗蠕变性能;
(3)合理的固化工艺可提高板栅和活性物质的结合强度,进而延长电池的使用寿命;
(4)控制化成过程中充电量,使电解液密度达到了最适值,同时减少化成过程中板栅的腐蚀,提高活性物质的结合强度,从而使铅钙合金电池深循环寿命明显提高。