摘要:利用CPFD(computational particle fluid dynamics)模拟方法对三维、全尺寸的气流床气化炉进行了模拟计算,建立起了适用于CPFD 模拟方法的气化模拟模型。模拟结果与实验数据相一致,说明模型基本准确且CPFD模拟方法适用于气流床气化过程的模拟。借由CPFD 模拟方法给出了颗粒相在气化炉中的具体反应历程及颗粒停留时间的概率分布;结果表明,在单喷嘴顶喷的气化炉中,同时存在颗粒相的轴向流动短路及返混,短路主要发生在炉中心区域;颗粒在炉中心区域反应剧烈而边壁区域反应则很缓慢,而且从气化炉流出的第一股短路颗粒主要由充分反应了的粉煤颗粒构成。
关键词:气流床;气化炉;CPFD模拟;气化反应;颗粒停留时间
引 言
气流床煤气化技术是目前主流的气化技术。它具有碳转化率高、气体产品清洁等优点。气流床气化炉内的流动与反应非常复杂,深入研究其规律对于实现碳的高效转化及超净排放有重要意义。目前对于气流床气化炉的研究主要采用实验和数值模拟两种方法,通过实验方法能获得比较可靠的实验数据,但受限于测量手段和气化炉内的高温环境,很多影响炉内气化反应的重要参数及其分布(如流场和温度场分布、反应速率等)却很难通过实验获得。随着计算流体力学(CFD)的发展,通过先进的数值模拟方法来对气化炉内流动与反应特性进行模拟和预测已成为非常重要的研究手段。
文献中对气流床气化炉的模拟研究已有不少报道。吴玉新等[1-2]采用简化PDF 模型对Texaco 气化炉建立起了热态模拟模型,其模拟结果与工业数据基本一致。毕大鹏等[3]基于相同模型对GSP 气化炉进行了模拟,并得到了炉内流场和组分分布。Sun 等[4]采用EF 模拟方法得到了多喷嘴对置型气化炉中的温度场和流场。Abani 等[5]利用大涡模型对一个小型气流床气化炉进行了模拟,并捕捉到了气化炉内的湍流流动特性。
以往的这些报道中,大多使用商用软件Fluent对气流床气化炉进行模拟。由于煤气化反应的复杂性,在有限的计算资源条件下,这些模拟研究往往采用二维或“拟三维”气化炉模型。在“拟三维”模型中,其数值计算区域为炉体的四分之一[1,3],并设定了圆周向周期边界。由于气化炉的非稳态数值计算非常复杂,文献中报道的模拟研究大都选择了稳态数值模拟的方法。这些模拟研究[4-5]均采用基于拉格朗日模型的DPM(discrete particle method)方法来追踪计算颗粒相,但为了简化计算往往忽略颗粒间的相互作用。还有一些研究认为气化炉中的均相反应是处于平衡状态的而不必进行详细计算,例如吴玉新等[1-2]采用PDF 模型来简化气化炉中的均相反应。因此目前通过模拟研究对于气化炉内流动与反应的了解还很不全面和深入,尤其缺少颗粒相在全尺寸气化炉中具体反应过程的研究。
近年来,由Snider[6]开发的CPFD(computational particle fluid dynamics)模拟方法开始被应用于气固多相流的模拟研究中。CPFD 方法基于欧拉-拉格朗日模型,属于DEM(discrete element method)[7]模拟方法。不同于一般的DEM 方法,CPFD 模拟方法将颗粒进行打包[6]并采用MP-PIC 方法[6,8-9]来简化计算颗粒间的相互作用,这使得它可以在可接受的时间范围内完成全尺寸、非稳态的气流床气化炉模拟,为进一步了解气化炉内的流动与反应特性提供了新途径。目前国内外采用CPFD 方法研究流化床气化炉的报道[8,10]较少,尚无用此方法研究气流床气化炉的报道。本文将尝试采用CPFD 方法对全尺度气流床气化炉模型进行模拟研究,探讨气化反应动力学模型和适合的反应参数,给出颗粒相在气化炉中的具体反应过程,与已有的实验结果进行比较、分析和研究。
1 模拟对象及基本设置
1.1 模拟对象
模拟对象为Brown 等[11]建立的一个直径为200 mm、长为2 m的粉煤气流床气化炉,其结构如图1所示,图中的x 轴和z 轴分别表示气化炉的径向和轴向。实验中使用的是Utah Bituminous 煤,其工业分析及元素分析见表1。实验装置采用单喷嘴进料,喷嘴设有中心(primary)和环隙(secondary)两个通道,粉煤和氧气均由中心通道通入,环隙通道只通入水蒸气,具体的实验操作条件和物料组成见表2,粉煤的粒径分布见表3。
1.2 几何模型和边界条件的建立
为便于模拟计算,本研究先在Solidworks 中建立了三维全尺度的简化模型,并利用商用软件Barracuda 中的网格生成器(mesh generator)将其进行网格划分。考虑到喷嘴所在中心区域的流动与反应最为复杂,所以该区域的网格划分较为密集。Liang 等[12]的研究表明,过度增加网格数对CPFD 模拟结果的影响很有限,本文采用的网格数为15372个。在CPFD 方法中,计算颗粒数由颗粒数密度(number density)来控制,在CPFD 公司给出的示例中,这一参数一般为200 ~2000。本文的颗粒数密度设置值为10000,采用了较多的计算颗粒数来提高模拟精度,其在本模拟中等同于每秒注入5966个计算颗粒。
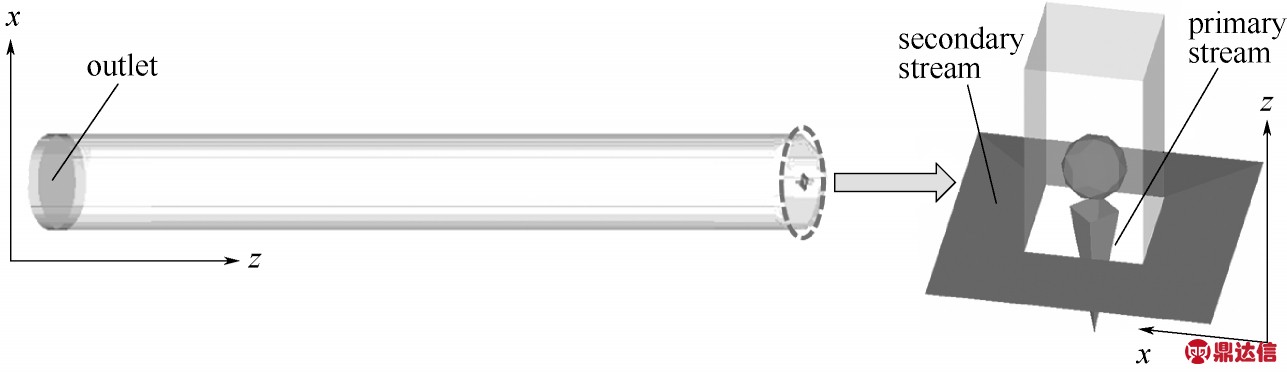
图1 气化炉模型与CPFD模拟边界条件
Fig.1 Schematic diagram of gasifier model and CPFD boundary conditions
表1 Utah Bituminous煤的性质[11]
Table 1 Properties of Utah Bituminous coal[11]

注:均为质量分数。
表2 Brown等[11]所采用的实验操作条件
Table 2 Experimental test conditions operated by Brown et al[11]
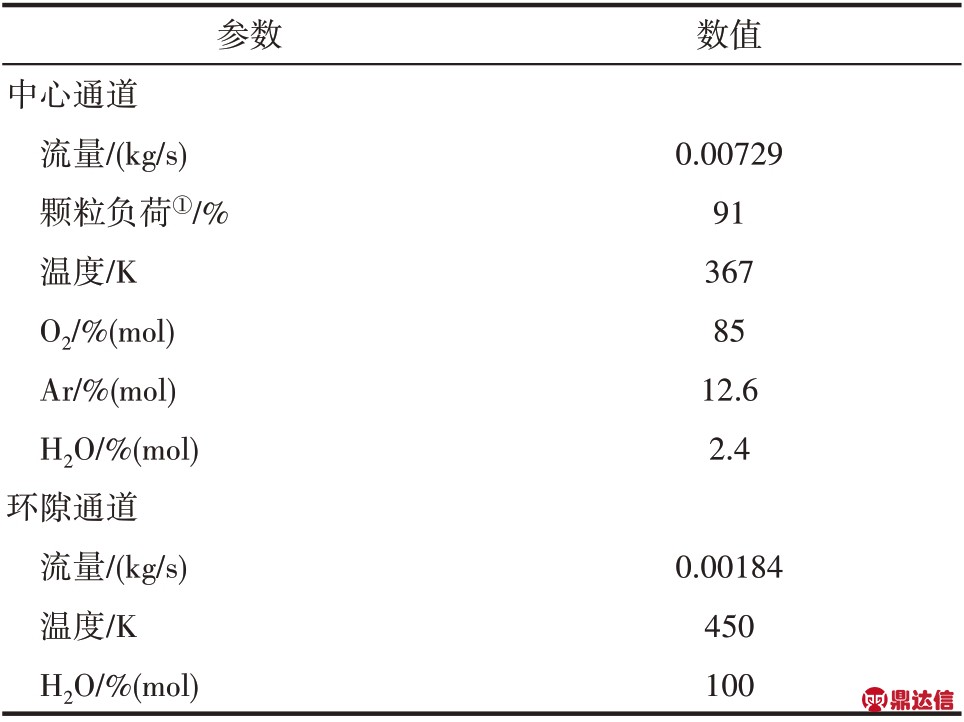
注:①煤粉质量与气相质量的比值。
表3 Brown等[11]和本模拟中所采用的颗粒粒径分布
Table 3 Particle size distribution used in this study and experiment by Brown et al[11]
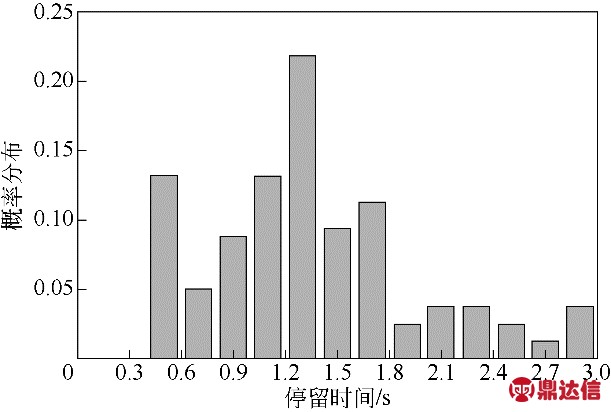
在CPFD 方法中,入口边界的设置方法主要有流动边界(flow BCs)和注射点边界(injection BCs)两种。喷嘴中心通道的结构尺寸相对于气化炉而言是微小的,如果采用Barracuda 中的流动边界来设置这一入口,则需要细密网格来捕捉喷嘴中心通道的几何形体,这将会极大地降低模拟计算的效率。如图1所示,本文采用CPFD的注射点边界来模拟喷嘴中心通道并作为入口边界,这一边界的特点是可以不依赖于细密的网格来模拟煤粉颗粒被喷入到气化炉中的效果。本文的注射点边界气相喷射速度为20 m/s,并假定颗粒相与气相在注射点边界处速度相同。在使用注射点边界时,需要指定颗粒相的喷射张角(angle expansion),本文将颗粒相的喷射张角设置为40°,然而颗粒相在被喷出时,其张角度会受到气相流动的极大影响,使得颗粒相最终呈现的张角如图4(a)中t=1.018 s 时颗粒的锥形分布所示(约为20°),这一角度与吴玉新等[1]所模拟的顶喷气化炉的估计相符。同时,对于流动面积相对较大的喷嘴环隙通道则采用流动边界(flow BCs)来模拟,由于环隙通道的几何形体在Barracuda 中也需要采用大量网格来捕捉[13],为了控制网格数量进而保证计算效率,本文采用了相同流通面积的正方形通道来代替喷嘴环隙通道(图1)。最后,在气化炉底部设置了一个常压出口边界,该边界同时允许颗粒相和气相流出计算区域。
在CPFD 方法中,颗粒与壁面的相互作用分别由法向动量保留(normal-to-wall momentum retention)、切 向 动 量 保 留(tangent-to-wall momentum retention)和漫反弹(diffuse bounce)来描述。由于缺少文献报道,本文将这三个参数设置为默认值,分别为0.3、0.99 和0。类似地,本文同样采用CPFD 默认参数来设置颗粒与颗粒之间的相互作用。模拟中各边界的其他设置参数与Brown 等[11]在实验中所采用的参数相同(表2)。
2 数值模型
2.1 控制方程
本文所采用的控制方程为CPFD 方法的通用方程,具体表达式见Snider等[6,8]的描述。
2.2 化学反应模型
(1) 脱挥发分模型由于气化炉的操作温度较高,挥发分脱去的速率非常快[3,5]。一般认为颗粒脱挥发分的表达式[14]为

其中,a1 + a2 + a3 + a4 + a5 + a6 + a7 = 1。
按照Abani 等[5]所建立的脱挥发分模拟方法,本文同样忽略颗粒脱挥发分过程中的惰性气体,并假设该过程中主要析出的气体产物为CH2、CO、CO2、H2和H2O。
本文采用单步模型[15]来描述脱挥发分的速率

式中,mv为颗粒中剩余的挥发分质量;T 为颗粒相与气相的加权混合温度(颗粒占0.8,气相占0.2);活化能Ev的取值[2]为2.1×105 s-1;指前因子Av的取值[2]为3.28×107 J·kmol-1。
(2) 非均相反应模型挥发分脱除后,颗粒主要由焦炭和灰分组成。这时应主要考虑焦炭与O2、H2O和CO2之间发生的非均相反应[4-5]
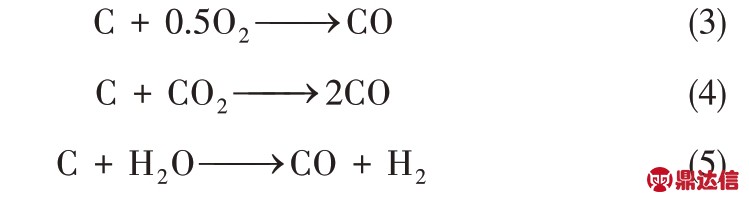
吴玉新等[1]和毕大鹏等[3]的研究均认为,非均相反应的速率主要受本征动力学和外扩散协同控制,本文采用了同样的非均相速率表达式,其反应速率式可统一表达为

式中,Ri 为第i 种气体与焦炭的非均相反应速率,kg·m-2·s-1;Ri,d 为外扩散速率,kg·m-2·s-1,其表达式为

式中,Ci 是扩散速率控制常数,其取值[3]为5×1012 s·K-0.75;Tp为颗粒相温度,K;Tf为气相温度,K;dp为颗粒直径,m;Ri,k 为本征反应速率,kg·m-2·s-1,其表达式为

式中,n 为反应级数;Ai为指前因子;Ei为活化能。其各自的取值[1,3]见表4。
表4 非均相反应速率各个参数的取值
Table 4 Value used for parameters of heterogeneous reaction rates
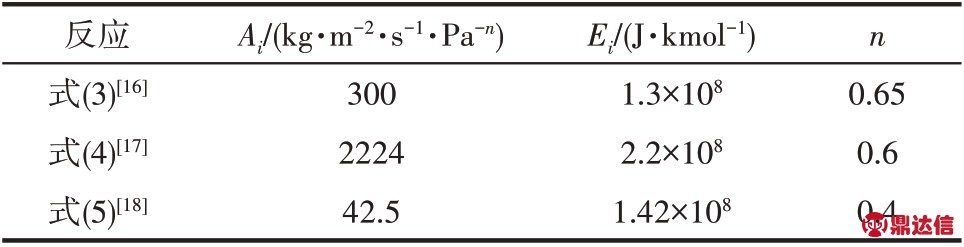
(3)均相反应 按照Abani等[5]以及Anderson 等[19]对均相反应的模拟方式,本文同样将反应过程中的烃类统一按CH2来表达,并采用适用于CH4的反应速率式来表达CH2的反应速率。本文在气化反应过程中主要考虑以下几个主要的均相反应[4]
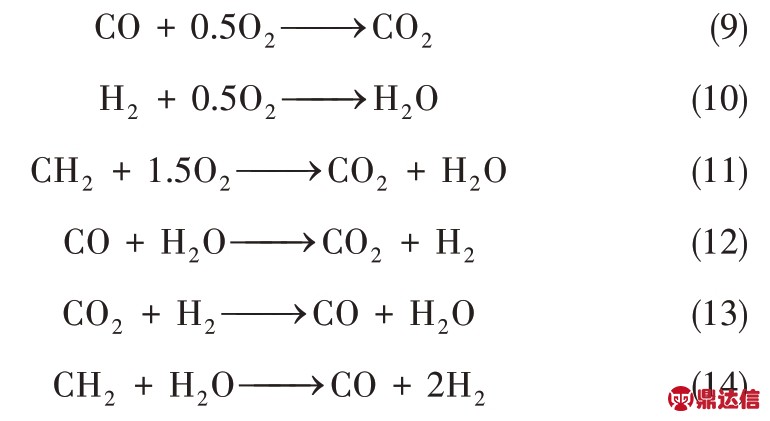
Yan 等[20]建立了一组简洁的均相反应速率表达式来模拟一个流化床气化炉,并取得了与实验相一致的模拟结果。考虑到CPFD 模拟计算的效率和稳定性,本文也采用了Yan 等[20]所建立起的均相反应速率表达式(表5)。
表5 均相反应速率表达式
Table 5 expressions for homogeneous reaction rates
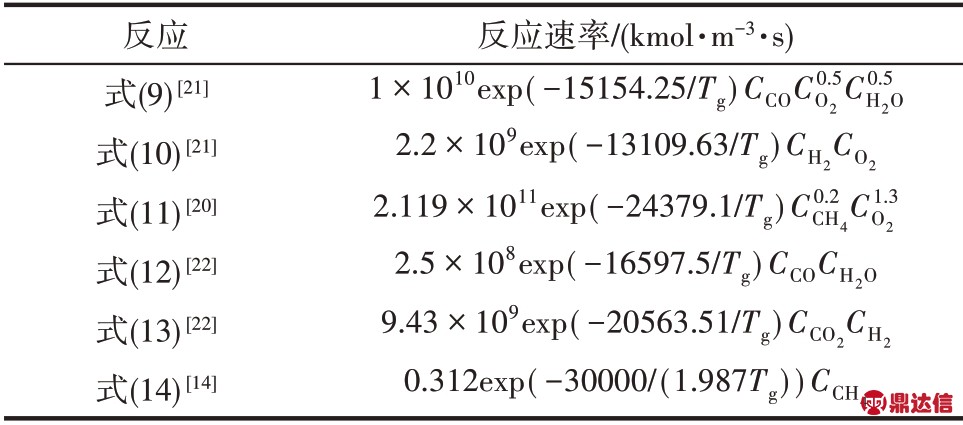
2.3 传热模型
本文所采用的流体与颗粒、流体与壁面间的传热模型为CPFD 的通用传热模型,其数学表达式见文献[6]中的描述。此外,实验中气化炉的热损失量较大而不能被忽略[11],所以模拟中通过设置固定的气化炉壁面温度来考虑这些热损失,这一方法也与Sun 等[4]在模拟气化炉热损失时的做法一致。本文所采用的气化炉壁面温度为1100 K,其值与Brown等[11]在实验中热电偶测得的气化炉壁面温度相同。另外,在模拟中采用了CPFD 方法内置的颗粒与壁面间的辐射传热模型来计算辐射传热,以更为准确地模拟气化炉中的温度场。
2.4 其他
本文所采用的湍流模型为大涡模拟(LES)模型,CPFD 模拟方法在该湍流模型中引入了Subgrid scale(SGS)模型[23]来计算涡流黏度,其具体的表达式见文献[6]。本文所采用的曳力模型为Wenyu-Ergun关联模型,其表达式见文献[12]。
3 模拟结果
3.1 模拟结果验证
表6为CPFD模拟结果与Brown等[11]的实验数据对比。其中模拟和实验的气相组成数据均为距离气化炉底部出口0.23 m 高度处炉中心位置的数据,结果为从模拟开始到4 s 时段的均值。从表中可以看出,模拟结果与实验测量值基本一致,说明本文所建立的CPFD 气化模拟模型基本准确,并且CPFD方法对于气流床气化过程的模拟有良好的适用性。
3.2 气化炉内气相温度、速度场及组成
图2 和图3 为模拟结果,均为气化炉的中间剖面图。图2(a)为气化炉内的时均温度分布,如图所示,气化炉喷嘴下方首先存在一小段接近于进料温度(400 K 左右)的低温区,直到粉煤颗粒因升温而开始迅速脱除挥发分并燃烧,同时引发焦炭的氧化反应,在喷嘴正下方形成一个温度分明的下行高温区,其温度随下行高度的增加而从3200 K 逐渐降低至1450 K 左右。图2(b)所示的气相时均速度分布和图2(c)所示的颗粒瞬时速度表明,进料颗粒在从喷嘴喷出并经过一小段下行后,速度开始急剧增加,尤其是轴心位置处的气相和颗粒速度,增加了约30%,这主要是由焦炭和挥发分燃烧所致的气相膨胀所致。另外,CPFD 模拟结果同样预测了喷嘴周围存在的气相回流区和气相在下行时逐步向平推流流型的转变,这与文献[3]中的报道是一致的。
表6 CPFD模拟与实验数据的对比
Table 6 Data comparison between simulation and experiment
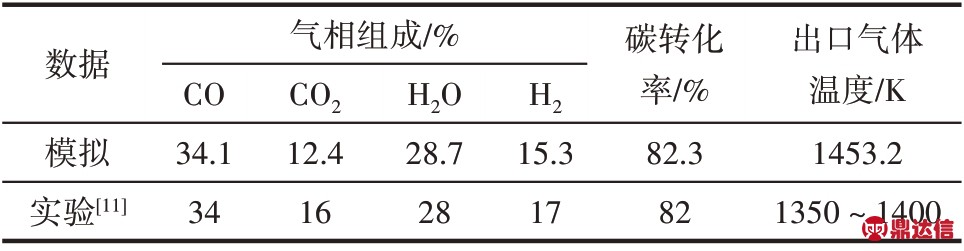
图3为气化炉内各气相组分的时均摩尔分数分布。如图3(a)、(b)所示,H2和CO 均随着气化炉高度的降低而增加,并且在气化炉中心位置处的增加尤为明显。图3(c)所示的CO2浓度在气化炉顶部高温区处最高,这表明此处是焦炭完全燃烧和CH2发生燃烧反应最为剧烈之处。图3(d)所示的H2O 浓度分布也同样表明,H2和CH2在气化炉顶部高温区发生了较为剧烈的燃烧反应。
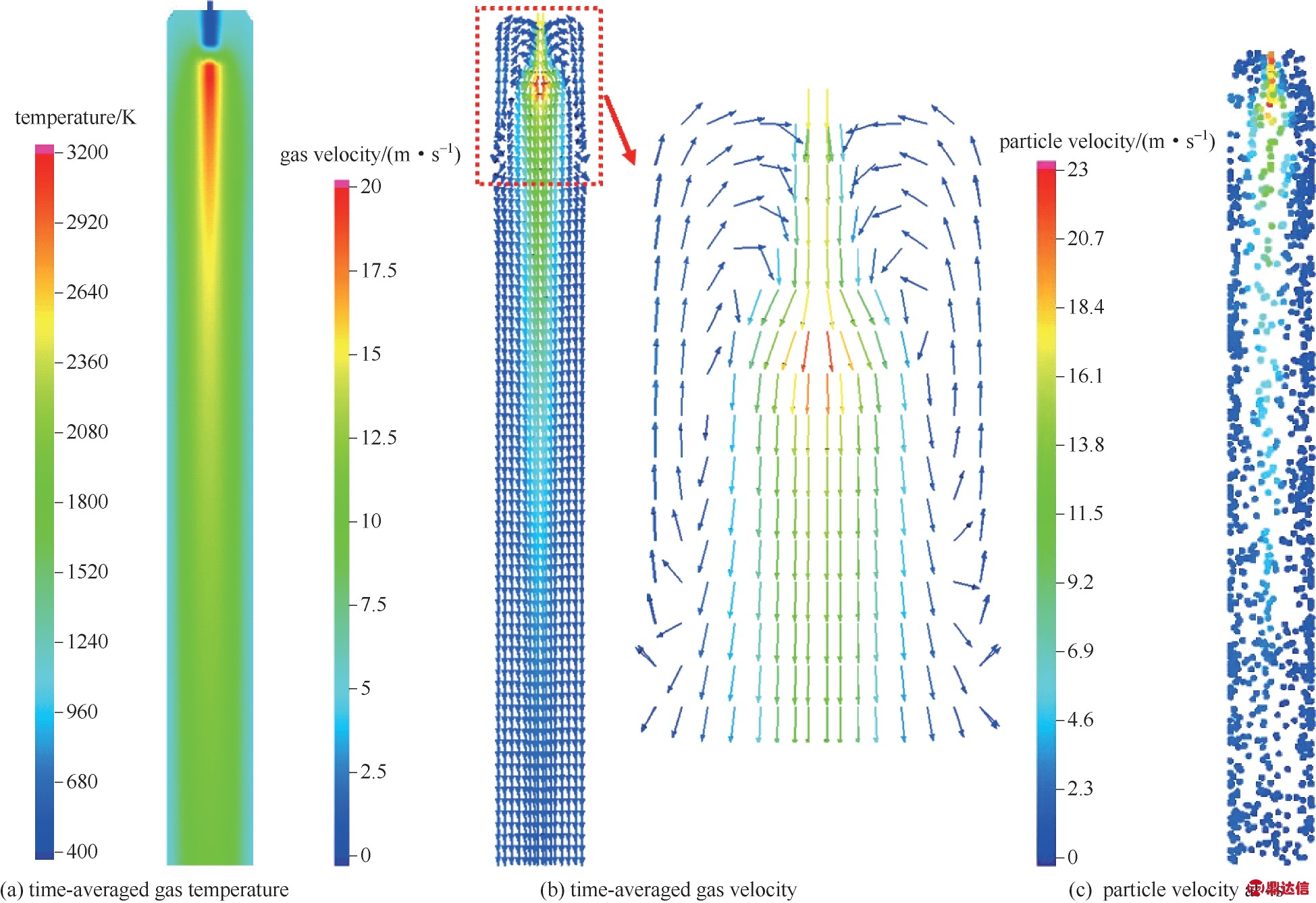
图2 t=0~4 s气化炉内的温度场与速度场
Fig.2 Distributions of gas temperature and gas/solid velocity in gasifier(t=0—4 s)
3.3 气化炉内颗粒相的反应历程
本文在模拟中采用了注入示踪颗粒的方法来具体观察颗粒相在气化炉中的具体反应历程。示踪颗粒与进料粉煤颗粒完全相同,并在气化炉模拟进行至1 s时开始注入,此时气化炉内的流动已较为平稳,适于注入示踪颗粒。示踪颗粒持续注入的时间为0.03 s,并在注入示踪颗粒时关闭粉煤颗粒的进料,以达到将进料粉煤颗粒完全切换成示踪颗粒的目的。示踪颗粒的注入流率也与粉煤颗粒在进料时的流率完全相同。示踪颗粒注入结束后,立刻重新开启粉煤颗粒进料,以达到颗粒进料流率在整个模拟过程中保持不变的目的。
图4 为示踪颗粒在不同时刻的位置与碳含量(质量分数)分布。需要说明的是,为了更好地展现示踪颗粒在气化炉内的反应历程,本文所示的示踪颗粒模拟结果均只显示示踪颗粒,隐藏了气化炉中同时存在的粉煤进料颗粒。如图4(a)所示,颗粒首先从气化炉顶部被集中喷入到炉内,但不久(1.044 s左右)就开始分散并呈倒锥形分布,这一分布与图2(b)所示的炉内气相速度分布相一致。这表明颗粒相在脱挥发分和燃烧时,气体产品急剧增加,颗粒相随气相的迅速膨胀而在轴、径向上加速扩散。从1.080 s 时颗粒的位置分布可观察出,颗粒的轴向下行速度存在较大差别,结合图2(c)可知炉中心处的颗粒下行最快,而靠近边壁处的颗粒下行缓慢,而且从图4(a)中1.044~1.518 s 时颗粒相的位置可以观察到中心和边壁区域颗粒的轴向间距越拉越大,同时部分靠近边壁区的颗粒受图2(b)所示的气化炉顶部回流区的影响会转而上行造成颗粒相的轴向返混。
图4(b)为图4(a)的水平视图。如图4(b)所示,颗粒随时间逐渐向边壁处扩散,在这一过程中,位于气化炉中心(高温区)的颗粒进行了较为充分的反应,碳含量已接近于0,然而靠近边壁的颗粒并没有进行充分的反应,相当一部分颗粒的碳含量仍接近80%。结合图4(a)中1.132~1.518 s 时颗粒位置和碳含量分布可知,被气相回流携带的颗粒主要分布在边壁附近,虽然它们在气化炉中停留了更长的时间,但反应进程缓慢,对气化炉的碳转化率贡献很有限,这主要是由于边壁区温度低且反应物浓度也相对较低造成的。
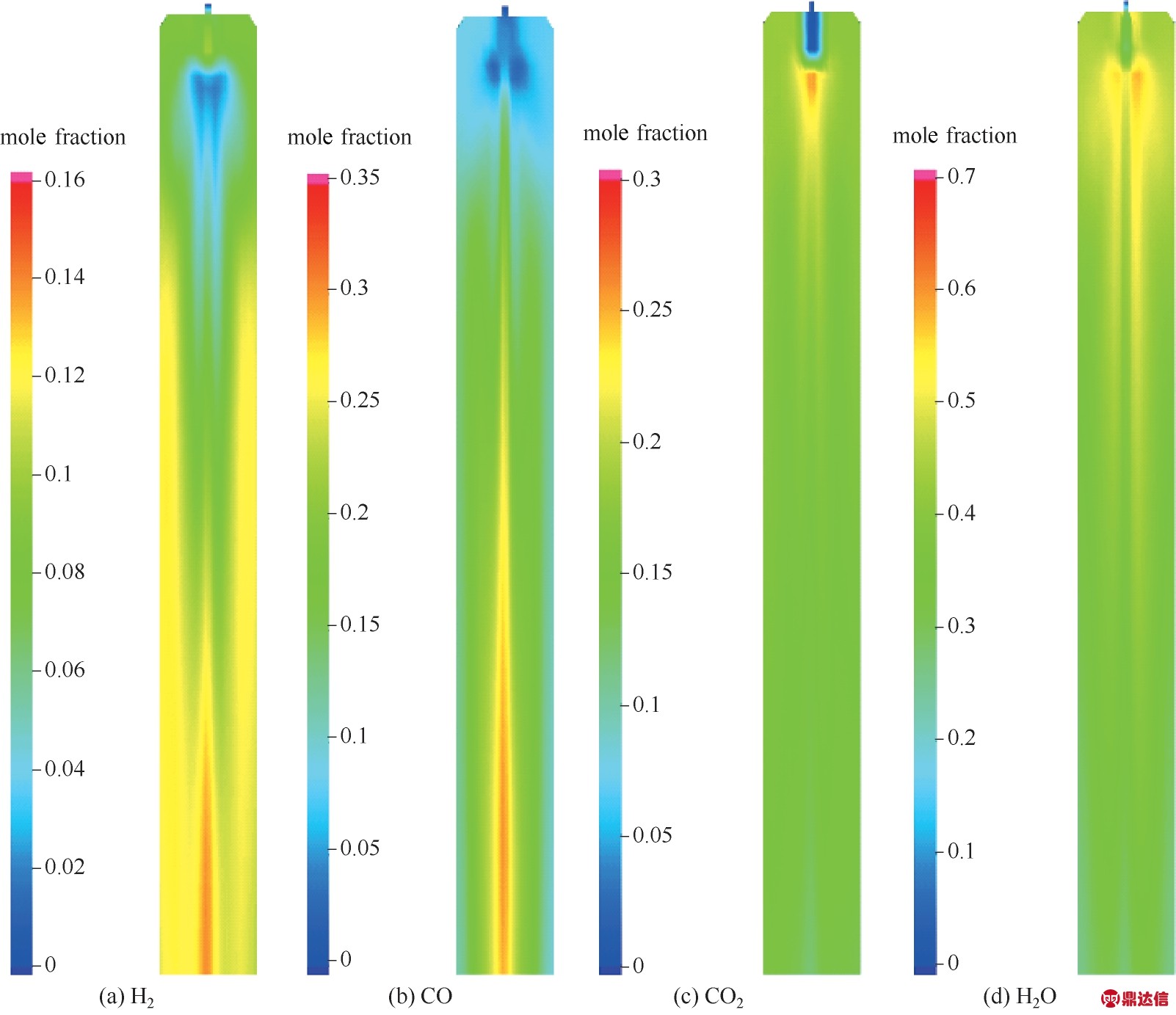
图3 t=0~4 s气化炉内的气相时均摩尔组成分布
Fig.3 Distribution of time-averaged(t=0—4 s)gas composition in gasifier
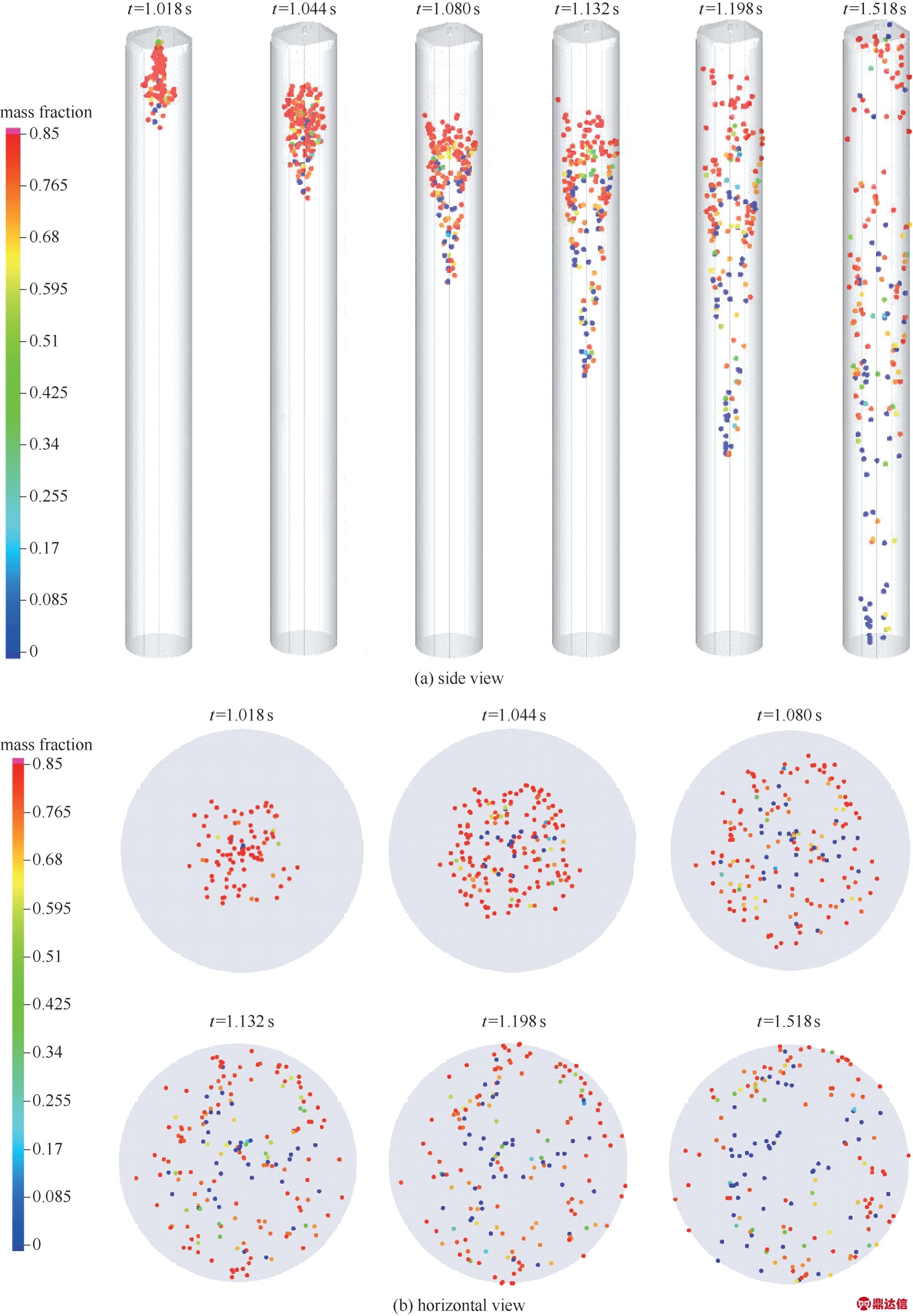
图4 示踪颗粒在不同时刻位置与碳含量(质量分数)的分布
Fig.4 Distribution of locations and carbon contents for particle tracers at different times
图5为在气化炉出口按0.2 s的时间间隔统计得到的示踪颗粒停留时间概率分布。如图所示,一部分颗粒(约13%的示踪颗粒)在0.4~0.6 s 内最先流出了气化炉,形成了流动短路。结合图4(a)可知,这部分颗粒是位于气化炉中心的颗粒,它们不仅受气化炉中心高速气流的加速,并且由于中心处颗粒反应更快,颗粒质量迅速变小,从而加剧了这部分颗粒的下行速度,正如图2(c)所展示的,气化炉中心颗粒的速度(尤其是在气化炉上半部分)较之边壁区域的快得多。通常会认为,在设计气化炉时应尽量减少其中的短路流动颗粒,因为延长颗粒的停留时间往往会使颗粒的碳转化率进一步提高。然而上述结果表明:气化炉中的第一股短路流动颗粒主要由充分反应了的颗粒构成,这部分颗粒的短路流动不仅不会降低气化炉中颗粒的碳转化率,其较高占比反而是该气化炉中颗粒反应更充分的一个表现。图5 中1.2~1.4 s 处的概率峰值,主要是由不在中心区域的下行速度相对缓慢的颗粒所贡献的,而且这部分颗粒占了示踪颗粒数量的大多数。另外,图5 中1.5 s 以后概率分布的“长拖尾”主要是由回流区的返混颗粒和紧贴边壁下行速度极慢的颗粒共同构成的。这部分颗粒的停留时间虽然长,但结合图4(a)的结果可知,其反应进程则要缓慢得多,也就是说颗粒停留时间长并不意味着其碳转化率就一定会高。
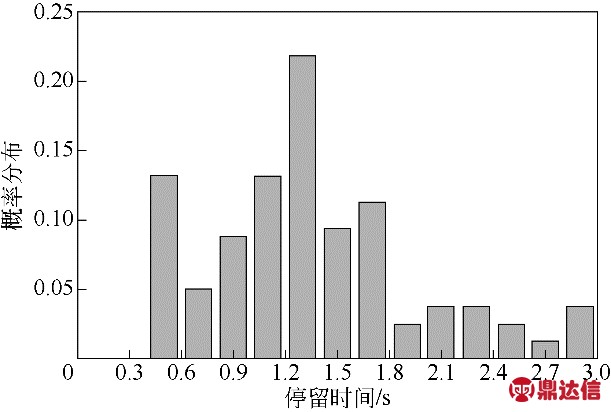
图5 示踪颗粒停留时间的概率分布
Fig.5 Probability distribution of particle residence time for particle tracers
总之,在本气化炉中,被气相回流所夹带的颗粒虽然停留时间更长,但回流区处于低温区,即便在该区域停留的很久但颗粒的碳转化率也并不高,只有经由回流区再重新回到气化炉中心高温区的颗粒,其碳转化率才明显提高。同时,紧贴壁面缓慢下行的颗粒,停留时间也很长,但由于这些颗粒同样处于低温区其碳转化率依然不高。最后,位于气化炉中心的颗粒,虽然停留时间短,但由于这些颗粒经过了高温区,其碳转化率反而很高。
4 结 论
本文针对气流床煤气化过程建立起了适用于CPFD 模拟方法的模型,并得到了与实验相一致的结果,从而验证了CPFD 模拟方法对于气流床气化过程模拟的适用性。同时,本文通过CPFD 模拟方法给出了颗粒相在气化炉中的具体反应历程。结果表明,粉煤颗粒在单喷嘴顶喷的气化炉中同时存在轴向流动短路与返混,短路主要发生在喷嘴正下方的中心区而返混主要由喷嘴附近的回流区所引起。另外,粉煤颗粒在气化炉中心与边壁处的反应进程相差很大,在中心高温区反应极其剧烈,颗粒碳含量接近于0,但在边壁区反应却很缓慢,颗粒碳含量接近80%。本文还通过在模拟中注入示踪颗粒的方法得到了气化炉中颗粒停留时间的概率分布,结果表明气化炉中颗粒的碳转化率与颗粒所经历的温度区间密切相关,从气化炉流出的第一股短路颗粒主要由充分反应了的粉煤颗粒构成。这些结果有利于进一步了解气化炉内的复杂化学反应,同时对气化炉的优化设计提供了可借鉴的依据。
符 号 说 明
Ai——指前因子,kg·m-2·s-1·Pa-n
Av——脱挥发分速率指前因子,J·kmol-1
a——脱挥发分速率指前因子,J·kmol-1
Ci——扩散速率控制常数,s·K-0.75
dp——颗粒直径,m
Ei——活化能,J·kmol-1
Ev——脱挥发分速率活化能,s-1
mv——颗粒中剩余的挥发分质量,kg
n——反应级数
Pi——第i种气体的分压,Pa
Ri——第i种气体与焦炭的反应速率,kg·m-2·s-1
T——混合温度,K
Tf——气相温度,K
Tp——颗粒温度,K
t——时间,s