摘要:固态渣层能够保护气流床气化炉的水冷壁,防止其受到高温合成气直接辐射以及液态熔渣的侵蚀。本文提出一种数值模拟渣层热应力的改进方法,并应用该改进方法对降温阶段渣层热应力的变化进行模拟研究。在渣层热应力的数值模拟研究中,经常假定水冷壁渣层的热应力变化基于一个固定的参考温度(比如环境温度25℃)。然而对于降温阶段的水冷壁气流床气化炉,一个固定的参考温度值并不能表征渣层“无应力”的初始状态,在此基础上计算将会得到一个不合理的渣层应力分布结果。针对该问题,提出了一种改进方法:将水冷壁渣层分割为多个子计算域,每个子计算域内单独设置参考温度,以此实现在整个水冷壁渣层上施加一个近似为降温初始时刻的参考温度分布,从而使渣层在降温初始时刻处于“无应力”状态。同时,对前人文献中的三维水冷壁渣层结构在降温过程中的热应力变化情况进行计算,以此测试改进方法的准确性,改进方法得到的模拟结果与其他参考文献得到的渣层热应力变化趋势一致。
关键词:气化;气流床气化炉;渣层;热应力;参考温度
气流床气化炉在工业生产中已经得到了广泛应用[1-4]。气流床气化炉高温运行(约1500℃),煤中的灰分会熔化为液态熔渣,液态熔渣沉积在水冷壁上形成渣层。渣层可以分为接触水冷壁的固态渣层以及接触高温合成气的液态渣层。固态渣层对于气流床气化炉非常重要,能够保护水冷壁,防止其被炉内高温火焰直接辐射以及液态渣层侵蚀。然而当气化炉降温时,渣层经常会由于温度变化产生的热应力超过其结构强度,最终产生裂纹甚至脱落[5-6]。渣层受损后裸露出的水冷壁由于缺少保护将迅速被烧损。
目前关于气化炉渣层的热力学性能和力学性能的研究已经有相关报告[7-8]。由于气流床气化炉炉内高温高压环境以及相关测量设备的限制,数值模拟已经成为研究渣层热应力变化的常用手段。作为材料进行热应力分析时的温度基准,参考温度是数值模拟渣层热应力时最重要的参数之一。当渣层的实时温度值与参考温度不一致时,渣层会发生体积膨胀或收缩,由此则形成热应力。已有文献中对于降温阶段渣层热应力数值模拟研究时,水冷壁和初始固态渣层的参考温度一般设为固定值,比如环境温度 25℃[9]。然而气流床气化炉一个运行周期约为6~18个月[10],并维持炉内高温(约 1500℃),这意味着高温蠕变松弛已经成为一个决定材料应力状态的重要因素。高温蠕变松弛能够释放材料内部的应力,最终使其达到“无应力”的状态。因此在气化炉运行稳定且渣层平衡时,渣层热应力处于稳定状态[5-6]。这种现象在与渣层类似的多层结构——热障涂层中经常出现[11-13]。因此对于经历过长时间高温稳定运行的气流床气化炉的渣层在降温过程中进行热应力数值模拟时,设置一个固定的参考温度(比如环境温度25℃)将导致在降温初始时刻参考温度和真实温度分布之间存在差异,渣层材料则在该温度差值的作用下发生热变形,由此将得到一个不合理的初始热应力分布计算结果。
为解决以上提出的问题,本文提出了一种渣层热应力模拟的改进方法:将降温过程中的初始温度分布作为参考温度施加给整个水冷壁渣层结构。利用该改进方法,本文使用ANSYS软件对LIN等[9]的3D水冷壁渣层结构重新计算,并对渣层表面点和内部点在降温过程中的温度及热应力变化规律进行了研究。
1 渣层热应力数值模拟改进方法的原理及数值模拟步骤
渣层热应力数值模拟改进方法的核心思想是:通过预设参考温度分布与降温初始时刻的温度分布一致,使降温初始时刻的渣层及水冷壁处于“无应力”状态,从而使其与经过高温蠕变松弛所形成的实际渣层与水冷壁的“无应力”状态相吻合,并以此为基础,计算渣层热应力在降温过程中的变化。为了使参考温度分布与降温初始时刻的温度分布一致,本文将计算水冷壁渣层切割为若干子计算域,每个子计算域被赋予的参考温度数值为该子计算域的平均初始温度,以此使参考温度分布与降温初始时刻的温度分布近似一致。
渣层热应力的计算步骤如下:
①计算降温初始时刻渣层内的温度分布;
②将计算水冷壁渣层结构切割为若干子计算域,并为每个子计算域赋予单独的材料属性,每个子计算域被赋予的材料属性中的参考温度值设为该子计算域的平均初始温度;
③使用ANSYS软件的单元生死功能模拟渣层的相变;
④施加边界约束,计算渣层的热应力。
2 水冷壁渣层热应力的有限元计算方法
本文应用ANSYS 10.0有限元分析软件,选择LIN等[9]进行计算的 3D水冷壁渣层结构进行模拟研究。所研究的水冷壁渣层结构包括水冷壁管、鳍片、氧化铝层、碳化硅层和渣层。提出的改进模拟方法与LIN等[9]采用的模拟方法仅在渣层的“参考温度”设置方式及数值上存在不同,相应的计算软件、控制方程和定解条件均一致,详细计算方法可见文献[9],相关材料属性见文献[14-18]。图1所示水冷壁渣层结构被分割为16个子计算域。为获得较为准确的渣层热应力分布,在渣层区域分割较密。图中所标示的两条直线(AB,CD)在下文的分析中用来表征沿着渣层厚度方向的变化。
经过渣层热应力计算步骤①和②后,沿直线AB和 CD,降温初始时刻的温度以及设置的参考温度分布如图2所示。可见改进方法所提出的连续参考温度分布更加接近降温初始时刻的真实温度分布,而文献[9]所设定的固定参考温度25℃,则与初始温度分布相差较大。
3 数值模拟方法验证
根据温度分布,选取温度大于灰分转变温度(1130℃[9])的体积,可以计算出液态渣层的体积分数,计算结果如图 3(a)所示。可以看出,尽管在降温初始阶段改进方法计算的液态渣层体积分数略大于LIN等[9]的计算结果,但是其最大差异小于6%。因此本文的计算方法与文献[9]的计算方法相比,具有类似的精度。由于本文提出的热应力模拟改进方法与文献[9]采用的模拟方法在计算水冷壁温度分布时完全一致,相近的计算结果表明本文所采用的网格精度满足计算需要。
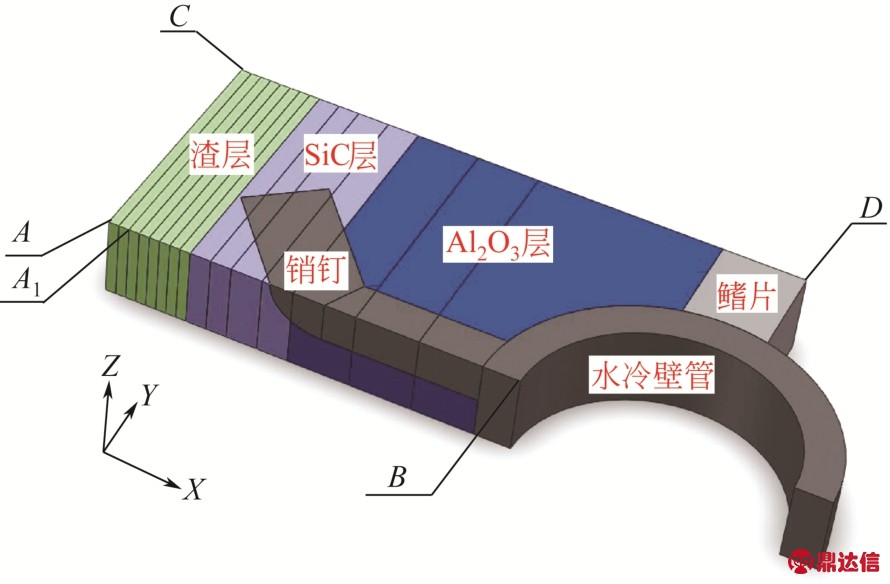
图1 切割后的计算水冷壁渣层结构图
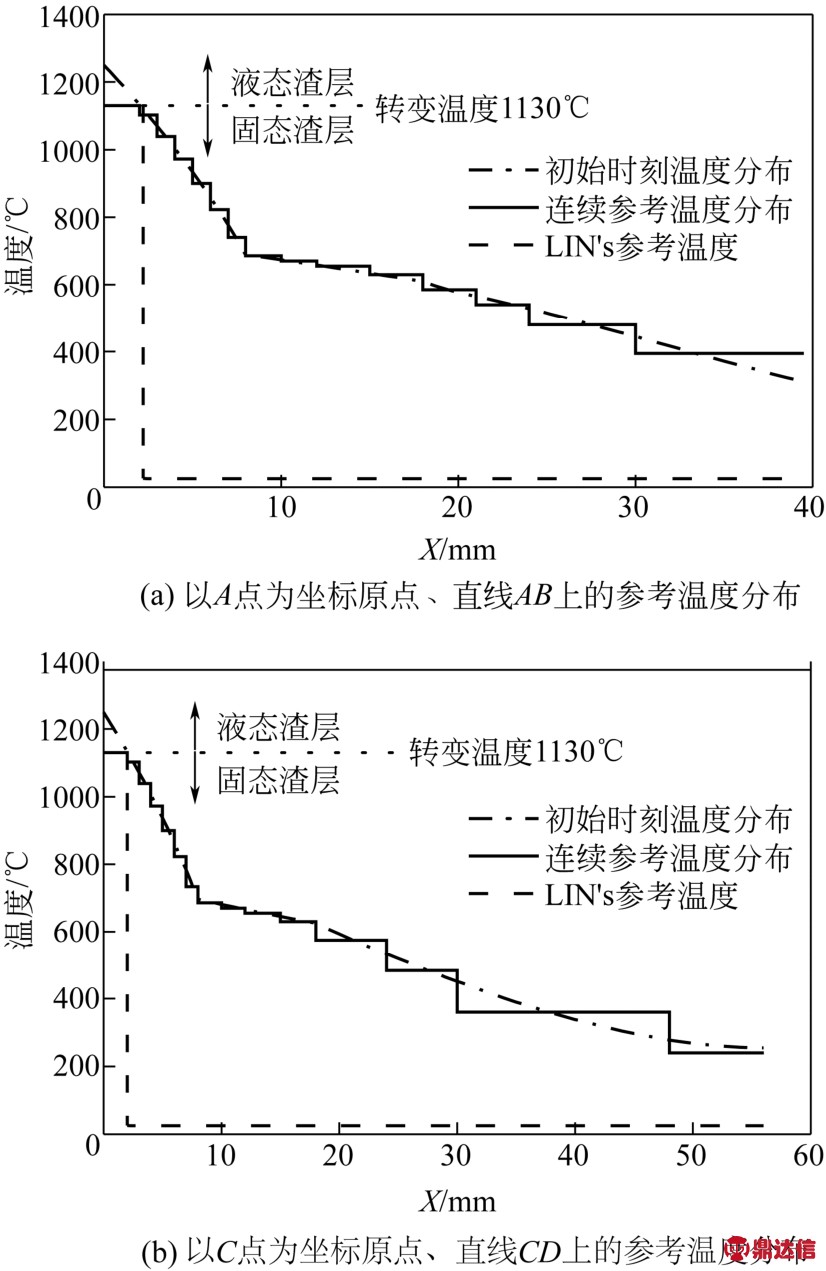
图2 AB和CD直线上的参考温度分布
由图 3(a)也可以发现,液态熔渣在完全凝固为固态渣层之前,其消失速率近似为常数,即液态渣层随时间变化,以近似等速率凝固为固态渣层。经过拟合,可得液态渣层体积分数随时间的变化关系,如式(1)。

式中,y为液态渣层的体积分数;t为时间,s;拟合的相关系数R2大于0.99。
为了验证热应力模拟方法的准确性,本文对文献[10]中所记载的渣层结构进行了热应力计算。如图3(b)所示,二者结果之间显示出良好的吻合关系,由此可以证明所采用的模拟方法能够准确进行渣层热应力的计算。
综合图3(a)和图 3(b)两个部分的验证,则可以证明本文所采用的模拟方法对于温度场及应力场的计算结果的准确性。
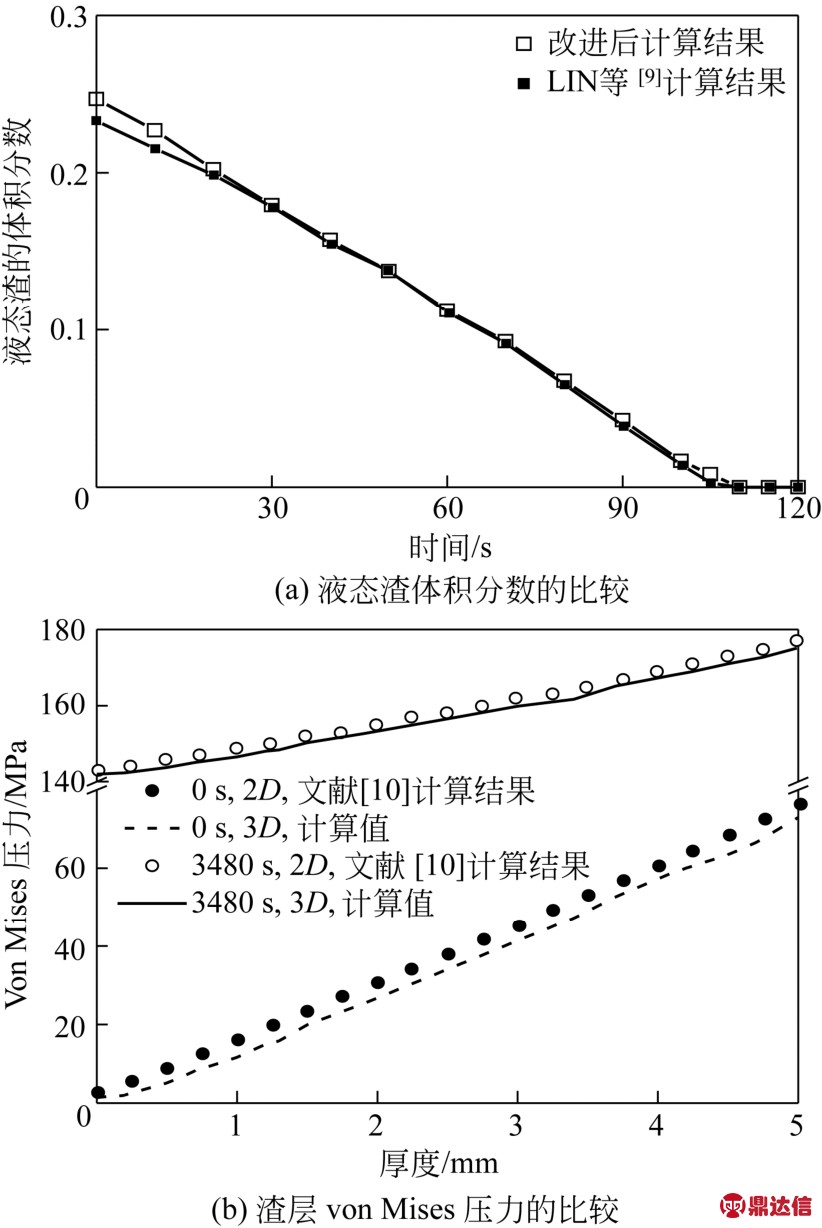
图3 液态渣体积分数和 von Mises压力的结果比较
4 计算结果及分析
4.1 降温过程中渣层表面点以及内部点的等效热应力的变化
图4所示为渣层表面点A以及内部点A1的温度及等效热应力随时间的变化关系。在降温 108s之前,A点的温度高于转变温度,所以其仍为液态渣,处于“无应力”状态,内部的等效热应力为 0。降温108s以后,A点的温度低于流动温度,液态渣层凝固,其等效热应力从0开始逐渐升高。降温过程进行到1800s时,A点温度降低到522℃,而等效热应力则从0升高到53MPa。A点的温度变化曲线和等效热应力变化曲线均为非等速率变化:在降温前期,温度急剧下降,而等效热应力则快速上升;在降温后期,温度缓慢下降,等效热应力表现出缓慢上升趋势。利用二阶函数对其降温曲线和热应力变化曲线进行拟合,可得式(2)、式(3)。

式中,σ为等效热应力,Pa;T为温度,℃;两条曲线拟合的相关系数R2均大于0.99。
A1点位于渣层内部,由于其降温初始时刻温度低,为固态渣层,因此其没有经历“无应力”状态的液态渣层阶段。随着温度逐渐降低,等效热应力逐渐升高。此外由于A1点相比A点更为靠近水冷壁,其温度要低于A点。在降温1800s时,其温度为468℃,低于 A点;而其等效热应力则为 55.4MPa,高于 A点,该趋势与周俊虎等[5]计算得到的规律一致。
综上可见,A点以及A1点在降温主体阶段,其等效热应力均随着降温而逐渐升高,该变化趋势与文献[10]一致。
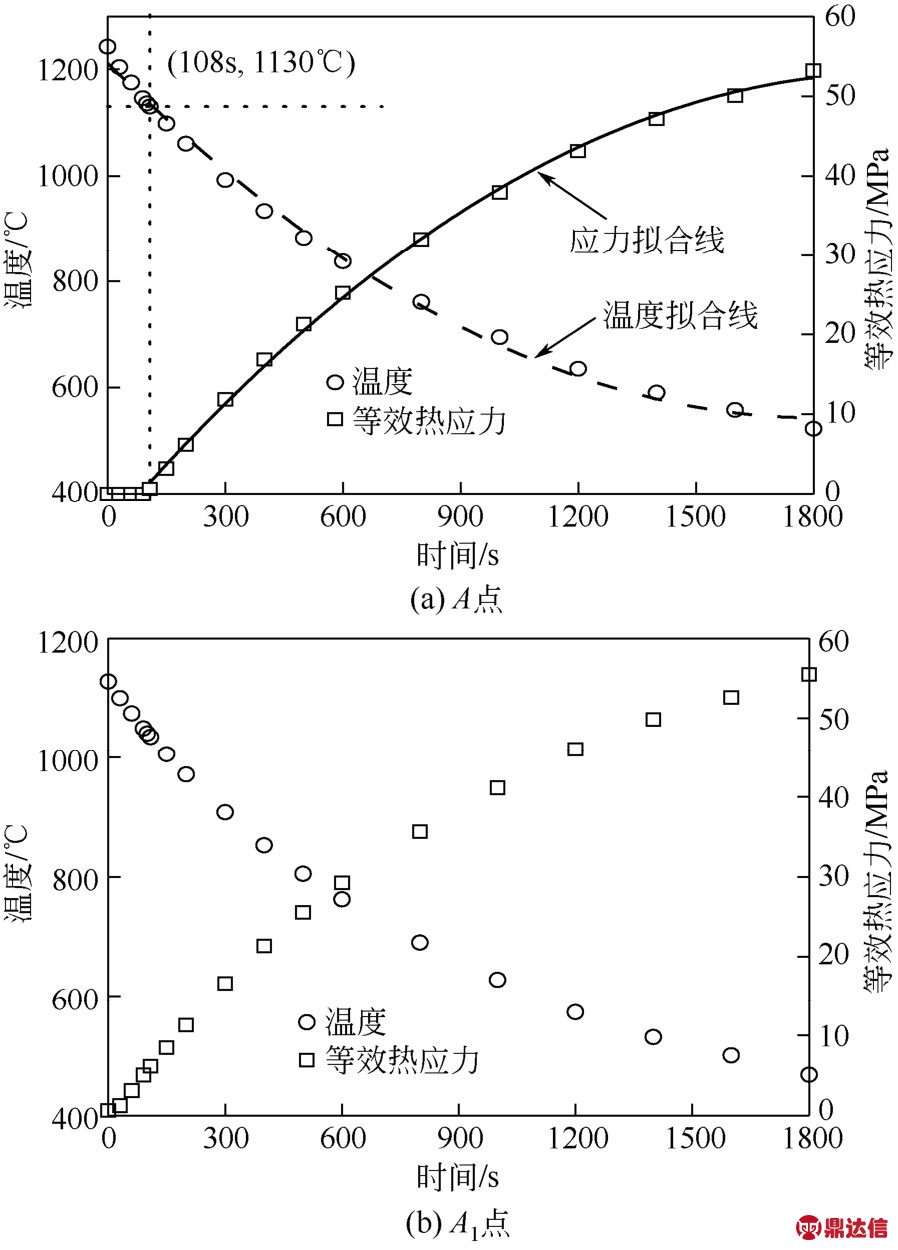
图4 A点和A1点温度及等效热应力随温度的变化关系
4.2 渣层的等效热应力分布
渣层在面ABCD上的等效热应力在不同时刻的分布结果如图5所示。在降温初始时刻(t=0),渣层近似处于无应力状态,这与上文讨论一致。这是因为预设参考温度分布与降温初始时刻的实际温度分布近似一致,由于实际温度与参考温度之间没有形成温度差,因此渣层内部不存在热应力。
随着气化炉逐渐降温(t>0),见图5,其渣层整体的等效热应力数值均逐渐升高,并且热应力在整个渣层上连续分布。这是由于随着温度逐渐降低,渣层实际的温度分布与设定的参考温度之间的差异逐渐增大,渣层的热应力逐渐升高,该趋势与参考文献[10]一致。
4.3 渣层的等效热应力分布
由于等效应力计算无法区分压应力与张应力,因此参照文献[9],本文应用第一主应力(σ1)和第三主应力(σ3)进行判断渣层内部的应力状态,σ1值表示为最大拉应力,σ3值表示为最大压应力。在 t=600s和t=1800s时刻,面ABCD上渣层的σ1和σ3值如图6所示。在t=600s时刻,见图6(a),在面ABCD上其σ1值已升高至约30MPa,而σ3约为0MPa。这表明在面ABCD上,渣层内部几乎没有压应力,拉应力占有主导地位。这可能是由于SiC和渣层膨胀系数之间较大的差异导致的[10]。此外渣层中存在着较为剧烈的温降,这导致渣层在降温过程中会出现较大的收缩,使得热应力以拉应力的形式存在。在t=1800s时刻,见图6(b),可以发现其σ1最大值已升高到约58MPa,而σ3仍保持约为0。这表明随着气化炉降温,渣层内部的热应力主要以拉应力为主,并且其随着降温进行逐渐增大。而在真实气化炉降温过程中,逐渐增大的拉应力有可能会超过渣层的抗拉强度,而这会导致渣层表面裂纹的形成[5-6,9-10]。
5 结论
本文提出一种水冷壁气化炉渣层热应力数值模拟的改进方法,并且将其应用于降温过程中渣层热应力数值模拟的计算中。得到如下具体结论。
(1)连续参考温度分布的设置能够更加接近降温初始时刻渣层内部的真实温度分布。在设置连续性参考温度的模拟结果中,渣层在降温初始时刻处于无应力状态,其等效热应力随着温度降低逐渐升高,热应力在整个渣层内部连续性分布。
(2)降温过程中,初始液态熔渣以等速率凝固为固态渣层。初始液态渣层凝固后,渣层表面点A的温度和等效热应力随时间变化曲线遵循二阶函数变化规律。在降温前期,温度急剧下降,等效热应力则急速上升;而在降温后期,温度缓慢下降,等效热应力则缓慢上升。
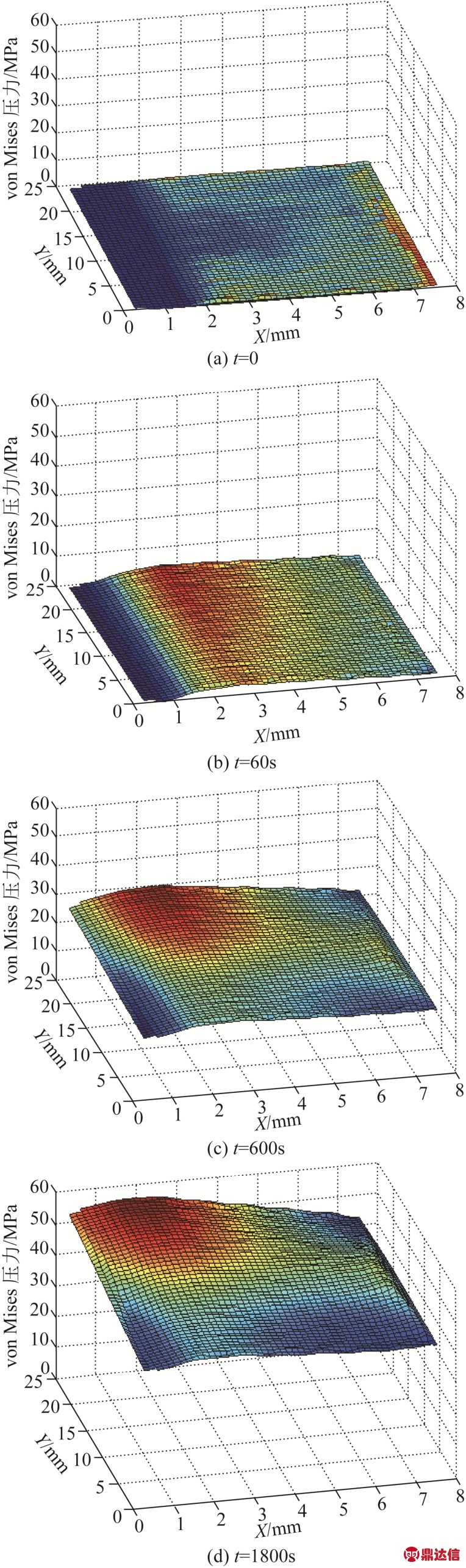
图5 面ABCD上的渣层的等效热应力在不同时刻的分布结果
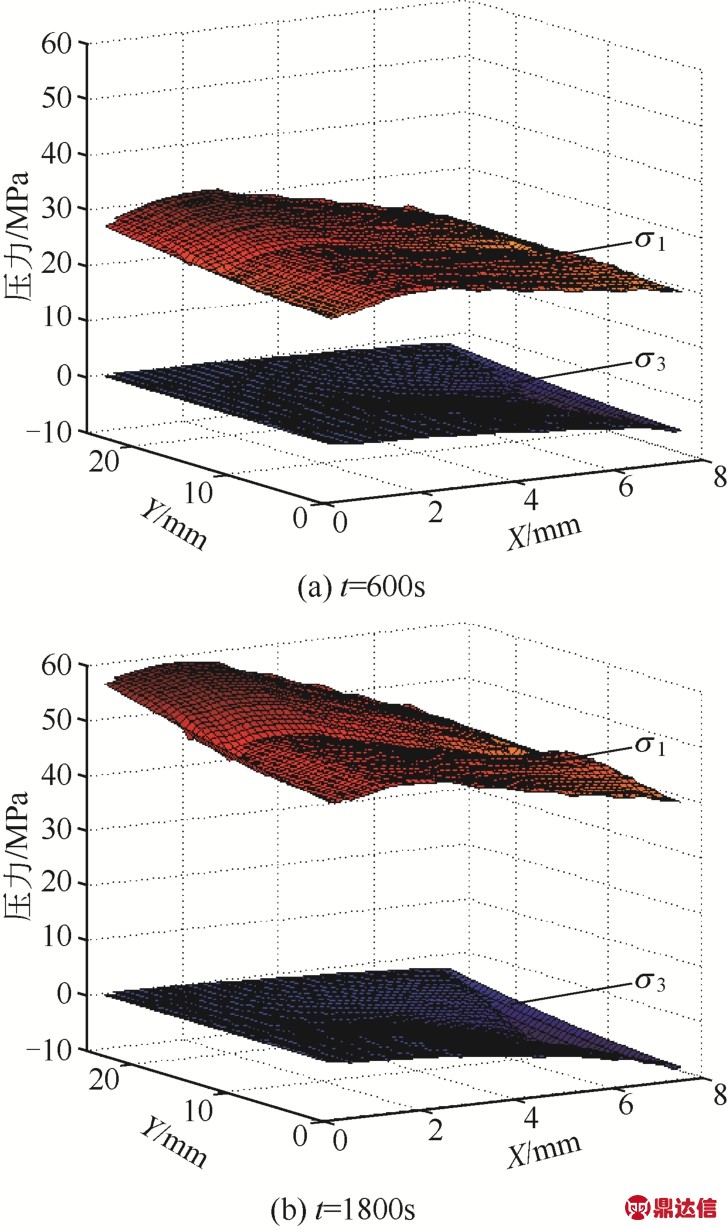
图6 面ABCD上的渣层在不同时刻的应力分布