摘要:提出一种基于逆向工程和阻抗力控制的打磨方法来实现形位、刚度不确定回转腔体内壁表面的精确打磨操作。采用准在线激光测量方法对形位不确定回转腔体内壁表面进行粗、精测量,提取纵截线簇数据,处理后重构内壁曲面。联合阻抗力控制和智能控制方法,提出参考轨迹的模糊调节算法;采用激光探测内壁曲面信息计算参考轨迹,根据接触环境刚度变化,建立模糊调节规则;通过调节因子对当前控制周期的参考轨迹变化量进行调整,使机械手打磨头在回转腔体内具有柔顺控制能力,实现对形位、刚度不确定回转腔体内壁表面的精确打磨。搭建了机器人激光测量与打磨开放式试验平台,进行了力控制打磨试验研究。试验结果表明:采用准在线纵截线激光预测与测量,重构曲面模型的相对平均误差小于0.024%;采用模糊调节力控制算法对固体火箭发动机壳体绝热层内表面进行打磨,目标打磨深度为0.200 mm时,打磨正压力相对误差小于±5%,回转腔体内表面打磨深度的相对平均误差为6.5%。结果显示所提方法可实现对具有复杂回转腔体内壁表面的精确打磨。
关 键 词:逆向工程;阻抗力控制;打磨;模糊控制;机器人;回转腔体
1 引 言
机器人在从事精密装配、工件表面打磨、抛光、擦洗及轮廓跟踪等作业时,要求其终端执行装置和环境之间保持接触,同时控制其终端位置和接触力,使机器人具有柔顺控制能力,即机器人力控制的能力[1]。针对受限环境的接触任务所提出的传统力控制方法可分为力/位混合控制和阻抗控制两大类[1]。传统方法需要受限环境形位信息已知,实际工作中会遇到接触表面环境刚度、几何形状和工作位置不确定或未知的情况。例如,由于加工工艺等原因,通过模具形成的回转腔体,其内壁表面通常存在较大的起伏,如圆柱表面实际为圆锥表面等,在这类回转腔体内执行打磨任务具有较大的难度。
目前,国内外学者对机器人打磨问题进行了相关研究。A.Robertsson及其团队建立的一体化机器人试验系统,通过基于CAD模型的防碰撞、路径生成、规划、调整等一体化仿真的方法实现高效力/位控切削、打磨等操作[2]。日本的Mamoru Minami教授带领其团队对不使用力反馈信息下的力控制方法进行了一系列的研究[3],通过机械手状态及输入转矩的计算得到机械手与受限环境之间作用力,实现未知受限环境的预测,提高力控制精度。Philippe Hamelin等学者对水下打磨机器人在打磨过程中遇到的固有刚度缺失问题,提出了“状态观测器+扰动观测器”的双观测器方法来无延迟地预测机器人的速度,实现对水下打磨机器人力与位置的精确控制[4]。国内部分学者还对自由曲面、回转曲面的磨削问题进行了深入的研究,如上海交通大学李建勋等人对欠驱动机器人的力/位置控制方法研究[5],清华大学宋亦旭等人对机器人砂带打磨的自适应模型控制方法研究[6]。Kline、Doulgeri、Vandertorght等学者对机器人的柔顺性进行了研究,对切削力的预测、受限曲面斜率自适应、刚度自适应等问题进行了探讨[7-9];言兰等人深入地研究了磨削机理及打磨工序对曲面粗糙度的作用[10-11]。此外,国内外学者对复杂曲面的激光测量与重构问题也进行了研究。Molleda介绍了一种基于三维模型重建的带钢成型技术[12];王欣、张玉香、冯肖维等学者研究了激光扫描数据的处理方法,对数据抽取、迭代方法等曲面重构问题进行了讨论[13-15]。综上所述,国内外学者的研究工作包括自由曲面、回转曲面的磨削问题等,提出了复杂曲面激光测量、建模,提高磨削质量及效率的各种方法。目前,大部分打磨方法研究均针对外表面进行抛光、打磨,而对小口径、狭长的回转腔体内壁表面的机器人打磨方法研究较少。
针对回转腔体中形位、刚度不确定内壁表面的打磨任务,提出了一种基于逆向工程的精确打磨控制方法。采用准在线纵截线智能激光测量方法,对不确定回转腔体内表面的形位进行测量与预测;将得到的数据进行拟合、处理后重构接触曲面信息。联合阻抗力控制和智能控制方法,提出参考轨迹的模糊调节算法。将激光探测的内壁曲面信息用于参考轨迹的计算,根据内壁表面刚度变化,建立了相应模糊调节规则,调整当前控制周期的参考轨迹变化量,实现了对内壁表面的精确打磨。搭建了机器人激光测量与打磨开放式试验平台,采用所提出的方法进行了打磨试验研究、分析和验证。
2 3-DOF机器人运动学与动力学分析
2.1 运动学模型
对于小口径、狭长的腔体的内壁表面,为实现较好的打磨效果,3-DOF机械手需要伸入到小口径、狭长的腔体内完成一系列操作,适应腔体内壁表面存在环境刚度、几何形状和工作位置不确定或未知的情况。3-DOF打磨机械手结构如图1所示,实现在回转腔体内打磨头的姿态调整,部件1、2、3分别为机械手的大臂、小臂和腕部关节,部件4为机械手的执行器(打磨头),部件5为待打磨形位和刚度不确定的回转腔体,在打磨过程中由外部托滚驱动壳体外壁以一定速度旋转,辅助机械手完成打磨。
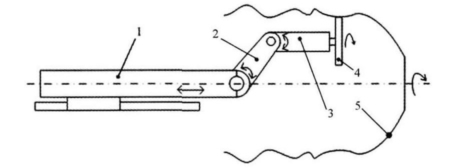
图1 3-DOF打磨机械手结构示意
Fig.1 Sketch map of 3-DOF manipulator
以机械手的基座为基坐标系O0x0y0z0,建立各关节坐标系模型如图2所示。关节1为移动关节,对应的关节变量为xL,长度为l1;关节2、3为转动关节,对应的变量分别为θ2、θ3,长度为l2、l3。建立受限环境坐标系Ocxcyczc。
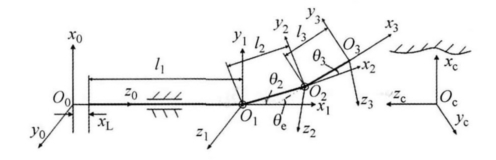
图2 机械手与环境坐标系
Fig.2 Coordinate systems of manipulator and constrained environment
为保证回转腔体内壁表面的有效打磨,打磨过程中需要打磨头与待打磨表面(接触表面)间保持一定的角度,这里定义机械手末端坐标系x3轴与z0轴间的夹角为打磨角θe。机械手的末端位置为[px 0 pz]T,在某一确定打磨角形成的位姿条件下,各关节变量存在唯一解。机械手末端位姿与各关节变量的关系为:

式(1)求取了机器人运动学逆问题,实现了由末端位置求取各关节变量;由各关节变量求取末端位置可通过机器人运动学正问题实现。
2.2 动力学模型
机械手在关节空间的动力学模型为:

其中 分别是关节的加速度、速度和位置向量。M(q)是机械手的惯性矩阵,C(q,˙q)是哥氏矩阵,G(q)是重力项,τ是关节驱动力矩,J是雅可比矩阵。式(2)经过变换得到了笛卡儿坐标系中的动力学模型:

其中,Mx(x)=J-T MJ-1,Gx(x)=J-T G,Gx(x,˙x)=J-T(C-MJ-1˙J)J-1。
3 基于阻抗模型的模糊力控制方法
打磨过程中要对被打磨表面的切削深度与平均磨削力进行精确控制,切削深度与平均磨削力、进给速度、切削硬度成正比[10]。当机械手末端以一定的速度沿回转腔体内表面的切线方向磨削时,机械手末端与被打磨表面保持恒定的正压力,使磨削接触面和磨削力保持稳定,进而控制被打磨面恒定的磨削深度。基于以上原因,在打磨过程中建立阻抗力控制模型,通过模糊规则调节模型中相关参数,实现对回转腔体内表面的打磨操作。
3.1 阻抗控制模型
机器人阻抗控制通过将机械手末端力和位置的关系等效为弹簧-质量-阻尼模型,建立机器人末端位移与接触力的关系[16],其模型为:

式中:矩阵Md,Dd,Kd分别是机械手期望的惯性,粘性阻尼和刚度矩阵;Fd是机械手末端的期望接触力,Fe 为实际接触力,Fe=[fn ft]T;fn 为法向力,ft为切向摩擦力。
¨x,˙x,x 分别是机械手末端实际的加速度、速度和位置,根据机械手关节安装的光电码盘反馈信号,得到各关节变量,可由式(1)反向求解,即运动学正问题求得机械手末端位置x;xd为机械手的期望轨迹,这里指机械手在受限表面上的接触力 为期望 值 时 应 达 到 的 理 想 位 置 ;˙xd,¨xd 是 相 应的速度和加速度。式(4)还可以表示为:

式中=xd-x 分 别 为 机械手末端位置、速度及加速度误差。
3.2 参考轨迹的模糊调节算法
当环境的动态特性未知时,为了使受限表面接触力Fe能够达到期望的接触力Fd,将参考轨迹算法引入阻抗控制模型[16]。定义xr为用于实际控制的目标轨迹,称为“控制目标参考轨迹”,简称“参考轨迹”:
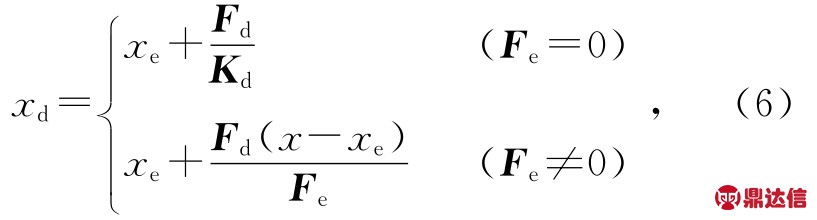
式(6)为对环境刚度进行补偿的参考轨迹算法,xe为未发生变形时的环境位置。实时检测的接触力Fe和位置信息x直接参与运算,实现在环境刚度未知时对受限表面力的跟踪,但需已知未发生变形时的环境位置xe,同时力控制精度受到力和位置反馈信号精度的影响。当检测信号偏差过大时,这种偏差可能引起参考轨迹的较大变化,导致较大的力跟踪误差,严重时甚至损坏机械手及受限表面。
为克服以上的不足,同时补偿环境刚度的不确定性,使机械手更好地与受限表面接触并保持恒定的接触力,采用力和位置检测信号作为模糊控制器的输入,建立模糊规则,推导出一种简单有效、可行的参考轨迹模糊调节算法,应用于阻抗控制模型中。
定义n为接触表面的单位法线向量,接触表面法线方向上的位置误差ep为:

模糊调节的参考轨迹为:

式中:Δxr为参考轨迹的调整量,参考轨迹的离散形式为:
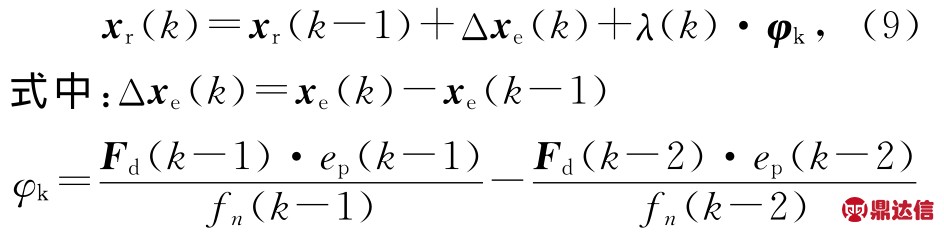
其中:φk为参考轨迹增量的变化范围,它的大小决定了受限运动中接触环境受到期望接触力后位置变化的范围。这里引入调节因子λ(k),λ(k)∈[0,1],每个控制周期内的取值由模糊控制器确定。二维模糊控制器的输入为法向力误差ef(k-1)=nT[Fe(k-1)-Fd(k-1)],及表征环境刚度变化率的出为调节因子λ(k);对应的模糊语言变量分别为EF、KC、LD,模糊子集为 T、R、L,表示为 T={PB1,PS1,Z1,NS1,NB1},R={PB2,PS2,Z2,NS2,NB2},L={VB,MB,B,M,S,MS,VS}。T中PB1、PS1、Z1、NS1、NB1表示力误差正大、正小、零、负小、负大,R中PB2、PS2、Z2、NS2、NB2表示刚度变化正大、正小、零、负小、负大,L中 VB、MB、B、M、S、MS、VS表示调节因子非常大、中大、大、中、中小、小、非常小,分别对应输入与输出的各个等级。模糊子集T、R、L中隶属度函数均选择高斯型函数。调节原理为:(1)当环境刚度由软变硬时,在法线方向上期望力引起的环境变形量由大变小,如图3(a)所示,若此时实际接触力超过期望值,为使实际接触力达到期望力,参考轨迹需要向未变形环境表面的外侧方向移动且需要较大调整量,这时调节因子趋于1;若实际接触力小于期望值,参考轨迹较小的调整量即可适应环境刚度由软变硬的变化,此时调节因子趋于0。(2)当环境刚度由硬变软时,在法线方向上期望力引起的环境变形量由小变大,如图3(b)所示,可对比条件(1)建立相似的推理过程。(3)当环境刚度变化不大时,引起的力误差较小,当前时刻对参考轨迹调节较小,λ(k)保持适中或偏小。
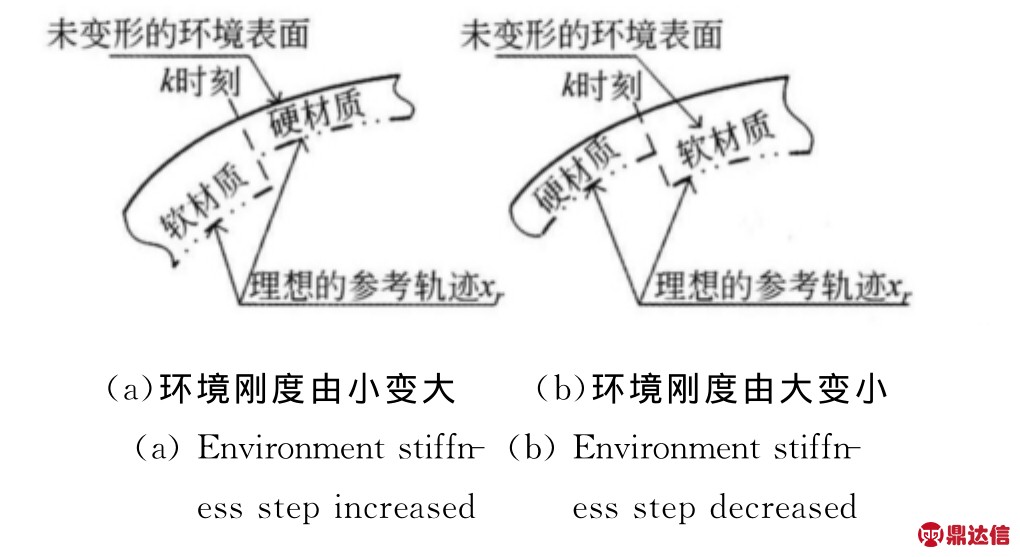
图3 环境刚度变化下的理想参考轨迹
Fig.3 Desired reference trajectories of stiffness changing environment
表1 调节因子模糊控制规则表
Tab.1 Fuzzy logic rules list of regulatory factor
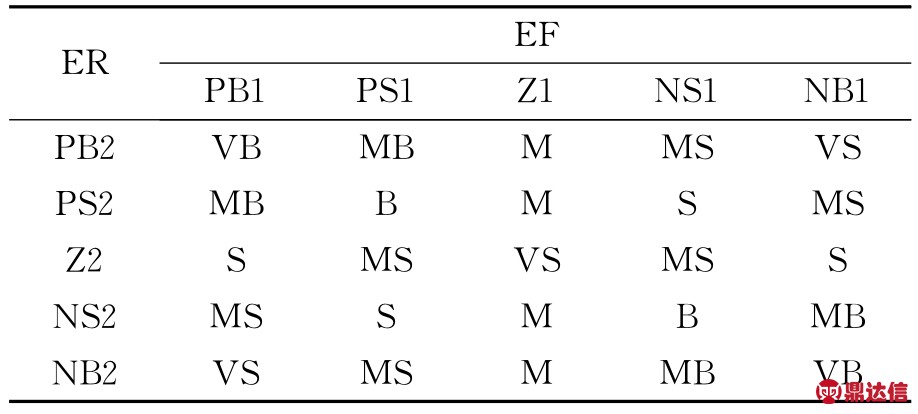
3.3 阻抗模型参数的在线调整
阻抗模 型 中 的 Md,Dd,Kd 为,er 的 权重,如果在受限运动中调节阻抗控制参数,可以减少由非接触到接触时的力冲击和力干扰,以便适应环境的变化。由于实际工作过程中准确的加速度反馈信号很难获得,设定控制律为u≡¨x,由式(5)得:

式中:c=kd/dd 为常量,kd 和kd/dd 分别是式(5)中Kd和Dd矩阵中的初始系数。将式(10)带入式(3)中,得到关节的驱动力矩:

同时,在线调整阻抗模型中的粘性阻尼矩阵,改善整个系统的力跟踪性能[16]。参考轨迹模糊调节的力控制系统如图4所示。
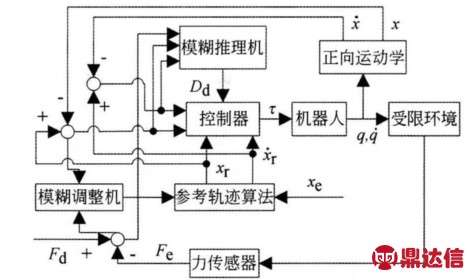
图4 参考轨迹模糊调节力控制框图
Fig.4 Block diagram of force control strategy with on line adjusting of reference trajectory by fuzzy logic
4 约束曲面测量与重构
为了在几何形状、环境刚度均具有不确定性的回转腔体内壁表面完成打磨任务,需对内壁表面进行测量,得到近似准确的环境信息,应用于阻抗模型参考轨迹的计算。为便于对回转腔体内表面后续打磨加工的路径规划,简化数据处理过程,对形位不确定回转腔体内表面的测量原理与测量方法进行研究,提出了准在线纵截面线测量方法。
采用3-DOF装有激光测距仪的机械手伸入到旋转的回转腔体内进行测量,通过回转腔体不同方位纵截线信息的提取,由纵截线簇构成曲面的三维实体模型。
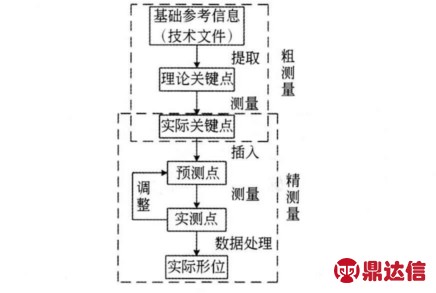
图5 纵截线测量方案
Fig.5 Scheme of shape measuring
为得到回转腔体工件内表面纵截线的精确信息,分粗测量和精测量两个过程对回转腔体内表面的实际形状进行测量,测量过程如图5所示。在粗测量中,利用待测回转腔体技术文件中的信息,识别出回转腔体内表面中构成曲面类型及其特征量,如样条曲面、柱面、球面等曲面的起始点、半径、结构点数量等,作为准在线纵截线测量方法的基础参考信息。根据这些基础信息,找出部分理论关键点进行测量,得到实测关键点。由于曲面位形的不确定性,实测关键点间可能有不确定的凸、凹等形状变化,致使激光测距仪的测量无效。为避免出现测量盲区,提高测量的准确度,在实测关键点之间插值,根据插入值与实测值之间的误差调节相邻插入点间的斜率,对下一时刻的插入点位置进行预测、调整,完成对回转腔体不确定位形的测量。
在精确测量中,需根据粗测的关键点和实测数据对插入点进行在线调整,实时预测回转体内表面的形位变化,如图6所示。图中虚线为待测曲面技术文件中所得到的理论曲线,实线为实际回转腔体的内表面截线,pr为粗测时得到的实测关键点,作为参考点;pa为预测点;p为实测得到的曲面位置。预测点表达式为:
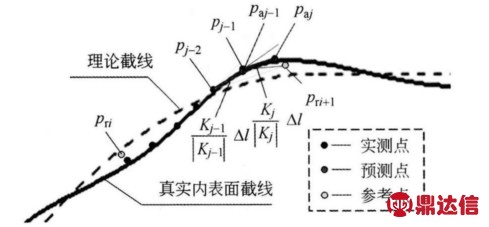
图6 激光测量实时调整方法
Fig.6 On-line adjusting algorithm in laser measuring process
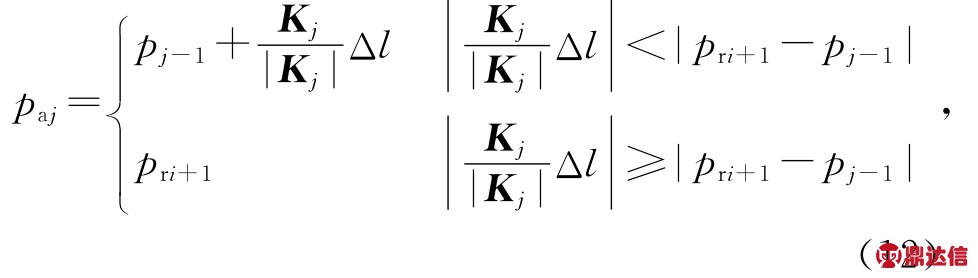
其中:i(i=0,…m)为粗测参考点的数量,j(j=0,…n)为实时测量点的数量,Δl为测量步长,Kj为方向参考向量[17]。
精测量以粗测量数据为基础,通过重复预测、逆运算、运动/测量、正运算的过程,完成对形位不确定腔体内壁表面纵截线的测量。在实际粗、精测量中,获取截线数据后,通过曲线拟合方法对完整内壁表面进行数学描述,得到一系列纵截线构成的回转曲面,为阻抗力控制模型提供了参考轨迹的腔体内壁表面环境信息。配置了双端口RAM,从硬件上保证了数据的实时通讯。另外,采用模糊规则进行了Matlab仿真,生成了模糊规则表,实际打磨过程中可通过在线查询离线生成的模糊规则表来保证系统的实时性。系统最高采集频率为1.22MHz,在1ms完成程序解算。
采用的激光测距传感器分辨率为40μm,三维力传感器安装在腕关节上,精度为1%FS,待测腔体圆柱段内径约为(490±10)mm,长度约为500mm。
研制了不确定曲面探测与打磨软件系统,主要功能包括硬件通信、关节及力信息实时显示、数据处理等,试验过程的控制与监测。
采用提出的纵截线测量方法对待打磨的内壁表面进行了探测,测量系统如图7所示。由试验分析得:测量数据过多时不仅增加了曲面测量过程的时间,且所占用的资源过多、数据处理所需的时间变长而拟合误差并无明显减小。选择步长为20mm的实测数据为曲面重构依据,重建了待测回转腔体的内表面,被测位形不确定回转腔体的三维实体模型如图8所示。重建后的回转腔体内表面相对误差绝对值平均值小于0.024%。纵截线激光探测方法获取了形位不确定内壁表面的形状及位置信息,为阻抗模型中参考轨迹的计算提供了表面形位信息。
5 不确定腔体测量及打磨试验研究
5.1 打磨试验研究
为了对所提出的不确定复杂曲面探测与打磨方法进行验证,在3-DOF平面机械手试验平台上进行了试验研究。
试验平台采用工控机(IPC)+DSP多轴运动控制卡的模式驱动各关节伺服电机,构建了一个开放式的机器人打磨力控制平台。
基于“IPC+DSP”所构成的开放式力控制实验系统中,可施加参考轨迹模糊调节力控制算法,采用模块化技术的硬件和软件来实现。为保证力控制的实时性:在控制系统中IPC与PMAC之间
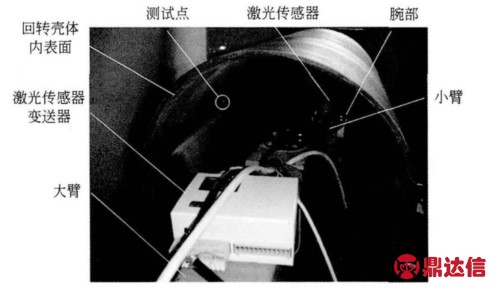
图7 回转腔体内表面测量试验
Fig.7 Laser measurement experiment of a rotary shell′s inner-surface
为适应表面刚度的不确定性,采用所提方法对打磨过程中正压力进行控制,机器人打磨试验如图9所示。
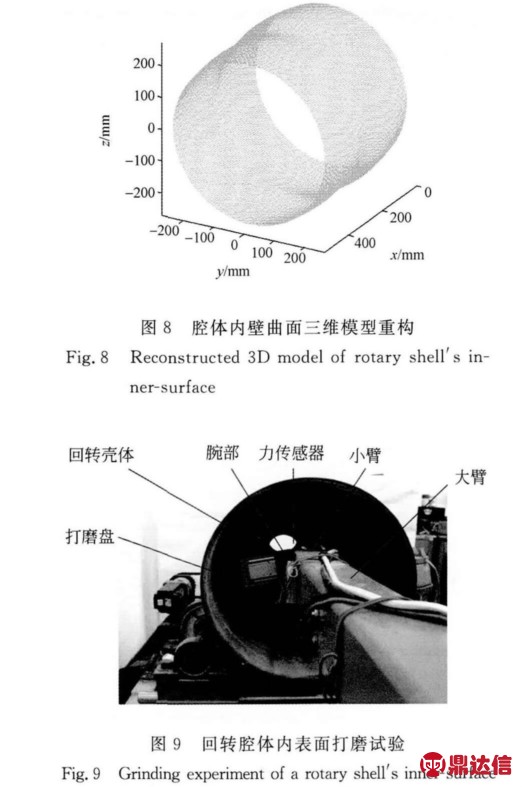
5.2 打磨结果分析
本试验系统打磨对象为固体火箭发动机壳体绝热层内表面,材料为浸胶石棉布,目标打磨深度为0.200mm,经多次试验确定,打磨正压力为5 N时可满足绝热层打磨目标深度的要求。打磨正压力的响应曲线如图10所示。
由于打磨盘高速旋转及噪声的影响,反馈的力信号受到了影响;在打磨的初始阶段(自由运动和受限运动转换过程中),有一定的力冲击。在50~70s左右,由于曲面的曲率较小且变化较大,打磨盘与被打磨表面的接触面积变化较大,打磨正压力受到内壁表面曲率不确定性变化的影响,通过调节因子调整,接触力在微小振荡后趋于稳定,力误差控制在[-0.3,0.2]N。整个力跟踪过程,接触力相对误差小于±5%,打磨后的内壁表面如图11所示。
经激光传感器对打磨后的内壁表面进行精确测量,回转腔体内表面的平均打磨深度为0.213 mm,相对平均误差为6.5%。
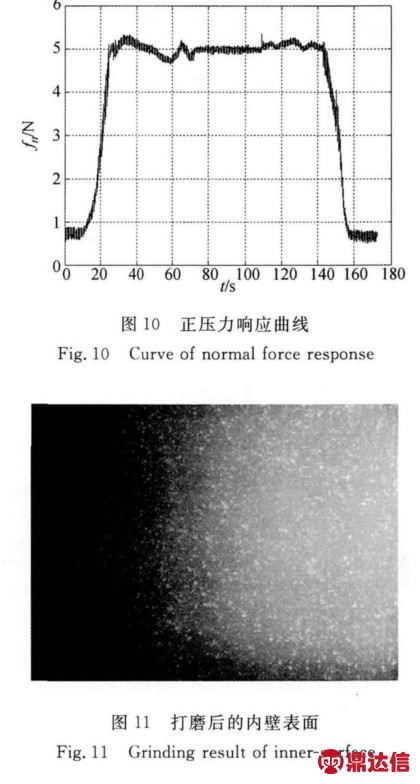
6 结 论
针对形位具有不确定性回转腔体内表面的打磨任务,提出了一种联合逆向工程和智能力控制的精确打磨控制方法。理论分析和试验研究表明:采用不确定回转腔体内表面的准在线纵截线智能激光测量方法,对不确定回转腔体内表面的形位进行预测及测量,重构曲面模型的相对平均误差小于0.024%,为参考轨迹计算提供了环境形位信息;联合阻抗控制力控制模型和模糊控制方法,提出了参考轨迹的模糊调节方法,可以适应形位、刚度不确定受限表面的动态特性变化;搭建了机器人打磨开放式试验平台,系统可在1ms完成程序解算;对固体火箭发动机壳体绝热层内表面进行了打磨试验,实际打磨深度为0.213 mm,打磨正压力相对误差小于±5%,回转腔体内表面打磨深度的相对平均误差为6.5%。