摘 要:从压力容器的设计角度出发,通过构建双腔体等压压力容器力学模型,对容器进行应力计算及容器理论壁厚校核,总结出双腔体等压压力容器在结构上和性能上的优点。设计出的该类压力容器有一定的市场竞争力和经济性,实现小体积小壁厚的安装、生产需要。
关键词:非圆形截面; 双腔体; 隔板
0 引 言
长圆形截面压力容器是为了满足工艺要求设计的一种设备。与圆形截面压力容器相比,非圆形截面压力容器具有结构简单紧凑、平稳性好、有较大的表面积及较高的传热效率。因此,在石化、冶金、炼油等行业应用广泛,如各种洗槽、锅炉联箱、储油罐、反应罐等。在特定的工艺要求下为了实现双流道,必须在腔体内设置一个隔板,将腔体分为双腔体。隔板在设计中可认为具有足够的刚度,可忽略其伸长,只考虑隔板的变形,对隔板两侧等压长圆形截面压力容器进行应力分析(见图1)。笔者针对现场实际工况,提出以双腔体压力容器的结构设计,通过建立力学模型与强度计算,达到结构上和性能上的需要。

图1 长圆形截面双腔体压力容器简图及长圆形截面图
1 力学模型
对图1所示B处截面1/2(轴向为一个单位长度)进行讨论。可认为隔板只可被拉伸或压缩,用截面法将隔板与筒体分离,并代之以相互作用力2F及F内力N=PCr,弯矩M及可通过截面切割处的变形协调方程及筒体与隔板在B点处的变形协调关系求得,因容器对称,B处截面总转角为0。建立力学模型如图2所示。
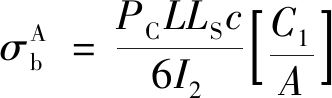
图2 力学模型
2 应力计算
2.1 C点处的应力计算(1)
2.1.1 C点处的薄膜应力计算
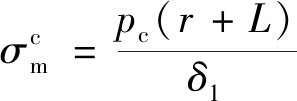
(1)
式中:为C点薄膜应力,MPa;Pc为计算压力,MPa;r为内半径,mm;L为长边侧板长度,mm;δ1为侧板短边有效厚度,mm。
2.1.2 C点处的弯曲应力计算

(2)
式中:为C点弯曲应力,MPa;Ls为非加强件宽度,取1 mm;C为截面至计算截面外表面距离,mm;I1为短边侧板的惯性距,mm4;C1为设计参数,mm2。
C1=r2(2r2+3πγα2+12α2)
(3)
式中:γ为设计参数。
γ=L/r
(4)
式中:α2为设计参数。
α2=I2/I1
(5)
式中:I2为长边侧板的惯性距,mm4。
A为设计参数:A=r(2γ+πα2)
2.1.3 C点处的总应力计算(2)
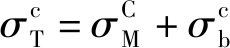
(6)
式中:为C点总应力,MPa。
2.2 B点处的应力计算(2)
2.2.1 B点处的薄膜应力计算

(7)
式中:为B点的薄膜应力,MPa;F为轴向力,MPa。

(8)
式中:α为设计参数:
α=E1A1/E2A2
(9)
β为设计参数:
β=r/δ1
(10)
2.2.2 B点处的弯曲应力计算
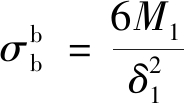
(11)
式中:为B点的弯曲应力,MPa;M1为弯矩,MPa。
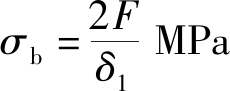
(12)
2.2.3 B点处的总应力计算
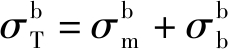
(13)
式中:为B点的总应力,MPa。
2.3 A点处的应力计算
2.3.1 A点处的薄膜应力计算
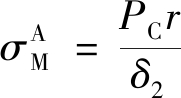
(14)
式中:为A点薄膜应力,MPa;δ2为侧板长边有效厚度,mm。
2.3.2 A点弯曲应力计算
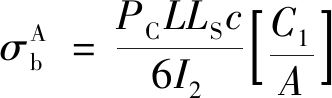
(15)
式中:为A点弯曲应力,MPa。
2.3.3 A点处的总应力计算
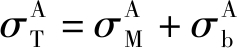
(16)
式中:为A点总应力,MPa。
通过以上的应力计算,可初步确定长圆形截面压力容器及隔板的厚度。
3 理论壁厚的校核
依据以下公式对截面压力容器及隔板的厚度进行校核:
A点壁厚校核(3):

式中:a为长轴半径,mm;C为腐蚀余量,mm;K为壳体对其轴线极回转半径,mm;
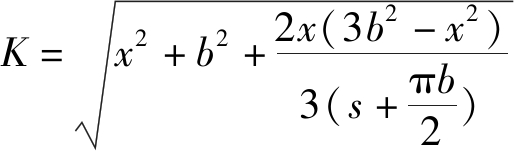
结论:当σA≤[σL]、σA≤[σY]为合格([σL]、[σY]为材料许用应力)
C点壁厚校核:

式中:b为短轴半径,mm。
结论:当σA≤[σL]、σA≤[σY]为合格。([σL]、[σY]为材料许用应力)
B点隔板的厚度校核:
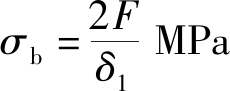
结论:当σb≤[σL]为合格。([σL]为材料许用应力)
4 结 语
在设计长圆形截面双腔体等压压力容器,采用试算算法,根据设计条件,假定容器计算壁厚,然后计算应力并校核,直到满足强度要求。一般需要多次参数修改试算,才能得到合理的结构参数。通过以上的计算可得出以下结论:长圆形截面双腔体等压压力容器的弯曲应力大于薄膜应力,其容器长短轴比越大,弯曲应力越大,因而在设计长圆形截面双腔体等压压力容器时,(在工艺参数允许的条件下)尽量减小长短轴之比,以减小弯曲应力,从而减小容器壁厚,使容器设计更合理、更经济。设计出的该类压力容器实现小体积小壁厚的安装、生产需要。