摘 要:本文主要介绍组件封装腔体内水汽含量的来源及失效种类,并针对各种水汽含量来源提出了对应的可能解决方案。
关键词:多芯片模块;腐蚀;水汽
0 引言
在军用设备方面,大量使用了各种微电路、混合电路,多芯片模块等,随着武器装备的发展以及使用环境的严苛要求,水汽含量对组件造成的失效凸显为重要的因数。从封装腔体内部来看,单单水汽一个因数是不会造成器件失效的,也不会造成腐蚀,更多的是因为水汽作为载体引起的腐蚀作用,导致电路失效。
1 水汽的来源
封装腔体内的水汽主要有三个来源:A腔体密封效果不理想导致的外部水汽漏入腔体内部;B腔体内壁,内部材料以及内部使用的元器件释放的水汽;C腔体内部氢气和氧气发生化学反应生成的水。
按照“GJB548B-2005方法1018内部水汽含量”的要求,密封腔体内部的水汽应低于5 000 ppm,这是因为5 000 ppm水汽对应的露点(空气中水蒸气变为露珠时候的温度)-2 ℃(水汽含量越小,露点越低),而水的凝固点为0 ℃,故当在封装内部水汽含量低于5 000 ppm时,水或者以气态或者固态冰的方式存在,就不会引起液态水造成的损伤。
此外业界目前存在一个共识:能够促进腐蚀所必须的液态水量是三个单分子层厚的水,在不同尺寸的封装内,将三个单分子层的液态水转换成水汽会产生不同的含量,在大封装内水的体积要比小封装内的水的体积大得多。所以如果这些封装的漏率相同,大封装漏入等效于三个单分子层的液态水比小封装需要更长的时间。
1.1 腔体密封效果不理想导致外部水汽漏入腔体内部
对于采用金属、陶瓷,玻璃等材料进行封装的腔体,可以近似的认为这部分封装材料是气密的,我们可以这么认为:经过加压粗、细检并被判定合格的上述材料封装可以忽略外面水汽的漏入。
计算金属到封装内部的水汽的方法请见以下公式:
Lh20=-V/t[in(1-qh2o/Δph2o)].
式中:Qh2o为漏入到封装内的水;V为封装内空余的体积,cc;t为时间,s;Lh2o为真实水汽漏率,atm.cc/s;ΔPh2o为封装内网初始水汽分压的差值。
1.2 腔体内壁、内部材料及内部使用的元器件释放的水汽
目前,常规的军表产品均在充满氮气的手套箱内进行封装,但即使手套箱完全密封也会含有一定的水汽,通常为20 ppm~100 ppm。同时封装内部的材料会释放大量水汽,释放水汽的量主要决定于材料的种类,制备工艺和密封前的预处理情况。释放出的水汽主要有两种来源:吸附在材料表面的水汽和分布在材料内部的水汽,前者在很短的时间内就能去除,而材料内部的水汽则需要很长时间才能去除。一般只采用金锡、金硅、金锗等不需要采用助焊剂的合金焊料进行贴片的封装内部的水汽,通过120 ℃~130 ℃,16 h~20 h真空烘烤即可去除,从而很容易满足封装内水汽小于5 000 ppm。
而采用导电胶进行贴片的封装内,由于存在易吸水的环氧材料,一般需要更高的温度或更长的时间才能将水汽去除,经正常固化后的封装经过120 ℃~130 ℃,16 h~20 h真空烘烤,封帽后直接RGA测水汽,一般都能满足小于5 000 ppm。如果环氧固化不充分,则需要更长的时间或更高的温度进行烘烤。
如果采用助焊剂或其他的有机材料等,即使通过120 ℃~130 ℃,48 h真空烘烤也很难满足水汽含量小于5 000 ppm。
另外对于封装来说,封装内镀层水汽会是一个非常严重的问题,在电镀过程中,水汽被封闭在镀层内,释放出的水汽的量与镀层的表面积成正比。小体积的封装表面积对体积的比率比大体积的封装大得多,被封装在镀金层的水汽量因电镀工艺不同也存在着很大的差异。封装内部出现的水汽很少,约等于密封箱内的水汽含量,通常在20 ppm~100 ppm,大部分的水汽释放过程发生在老化和高温工作过程,在给定的温度下,释放出的水汽量与时间成对数关系,主要有两个原因:可释放的水汽量在逐渐减少;随着水汽的释放,封装内的水汽压力在逐渐增加,从而降低了水汽释放的速度。
1.3 腔体内部氢气和氧气发生化学反应产生水
虽然理论上存在氢气和氧气发生反应的可能性,但是这个反应的速率在常温和常压下非常慢,以至于多年也不能形成可以检测到的水汽量。然而,合适的催化剂将导致这个化学反应发生,在封装内氢气和氧气是否发生化学反应的问题上,目前业界仍然存在争议。
2 产品故障分析
在实际装配检测过程中,存在组件水汽含量超标,针对其失效现象进行分析,查找失效定位。对于封帽工艺而言,在缝焊前采用适当的条件进行烘烤,立即进行RGA试验,确保水汽含量满足国军标要求是非常容易实现的,但如果不对封装材料进行预处理直接封帽,经过长时间的老炼或高温烘烤后再进行RGA试验,封装内的水汽是很难满足国军标要求的。
2.1 高温烘烤试验
采用镀金合金材料制作密封样品,样品内部填充高纯氮气。样品分四组,分别在125 ℃进行48 h,168 h,500 h,1 000 h的烘烤,测试结果如表1。测试数据显示,随着时间的延长,材料排放出的气氛大部分是氢气和少量的水汽。
表1 内部气氛分析结果1
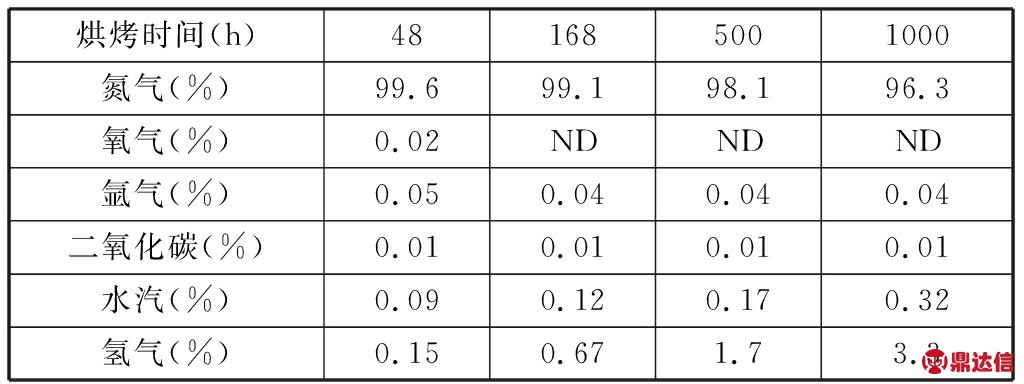
另外,取未经过电镀处理的可伐材料再密封、高纯氮气环境中,密封在合适的玻璃容器中。样品分三组,第一组是空封,进行320 ℃,150 h烘烤,第二组有可伐材料,进行320 ℃,100 h烘烤,第三组有可伐材料,进行320 ℃、150 h烘烤,三组样品分别进行内部气氛含量的测量,结果如表2。
表2 内部气氛分析结果2
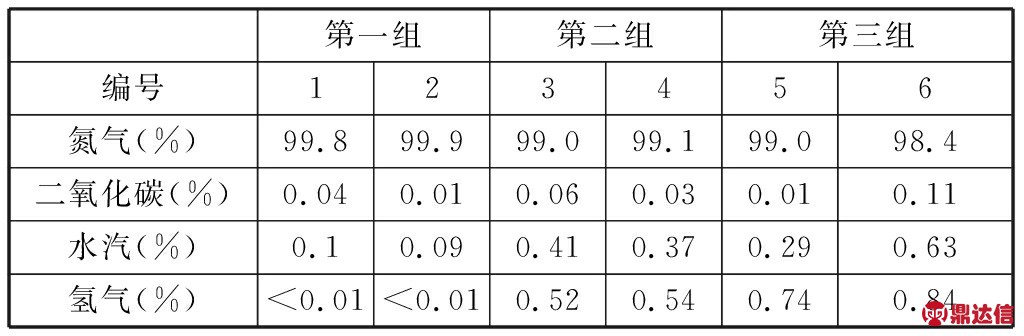
测试结果表明:金属材料内部吸附了大量的氢气和水汽,在密封环境中,慢慢释放在腔体内,造成氢气中毒。
2.2 故障数分析
根据高温烘烤试验结果,在分析封装内部水汽含量超标问题时候要搞清楚测试前是否经过长时间的高温烘烤,因为经历不同时间高温烘烤的封装内部水汽含量不具备可比性,例如封帽后封装内部水汽正常,不代表经过长时间高温烘烤也正常,这不能作为评判前面工艺或操作是否正常的根据。
因此在不考虑RGA试验本身异常的前提下,针对生产过程中某产品水汽含量超标的问题可以建立如下故障树。
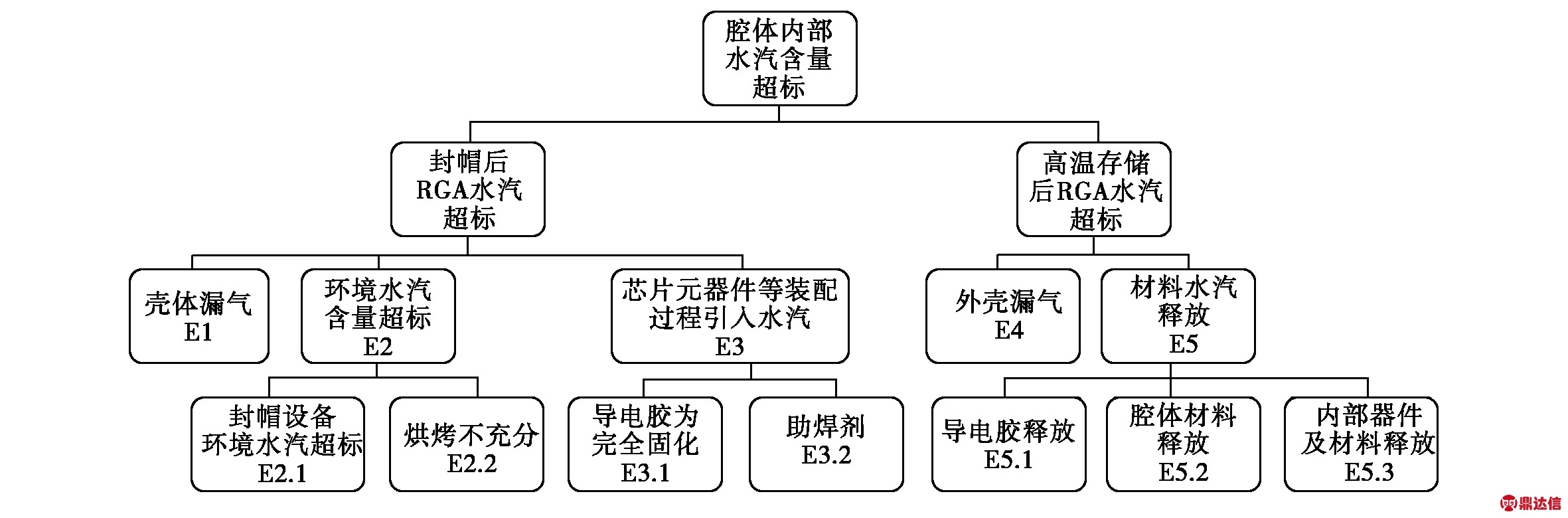
图1 水汽含量超标故障树图
2.3 分析验证图
2.3.1 E1壳体漏气
外壳漏气会导致封装内部在封帽RGA时水汽含量超标。一般情况下,空气中的水汽含量约为20 000 ppm,如果封装很少泄露,封帽后立即进行RGA试验时可以检测出一定量的He。如果腔体本身大漏,空气会通过封装的漏孔和内部的气体交换,甚至达到平衡。可通过监测腔体中出现的气体比例,如果纯氮转化为空气气氛比例的趋势,则腔体大漏。总之通过He捡漏及气体成分分析,可以判断腔体漏气的情况。
2.3.2 E2封帽环境水汽含量超标
封帽环境对于最终产品的腔体水汽含量具有直接的影响,从工艺角度来分析主要存在两种可能。E2.1封帽设备环境水汽超标和E2.2烘烤不充分。封帽一般按照露点仪上的露点进行控制,常规的工艺要求相对湿度小于1%RH时才可以将烘烤完毕的产品转移到手套箱进行封帽。如果E2.1封帽设备环境水汽超标,首先建立在露点仪故障的前提下,如果露点仪正常,排除人为不按要求操作,则封帽设备环境受控。
2.3.2.1 E2.2封帽设备环境水汽超标
封帽设备环境为氮气环境,水汽超标的原因是输入的氮气水汽超标引起的,氮气水汽超标的情况建立在露点仪故障的前提下,如果氮气本身水汽超标,则会导致产品内部水汽含量封帽后超标。可通过针对同管道输入的其他设备的产品进行判断,如果多台套设备均出现水汽指标异常则存在氮气水汽含量超标的可能性。
2.3.2.2 E2.2烘烤不充分
烘烤记录需完整详实,追溯产品的烘烤条件以及烘烤设备的运行情况,针对同台设备封帽的产品进行水汽分析,判断烘烤设备是否异常,排除设备故障后,在正常操作记录的前提下可排除烘烤不充分导致失效的可能。
2.3.3 E3芯片元器件装配过程引入水汽
目前组件、模块用的装配方式主要有两种:导电胶粘接和共晶焊料焊接。在这两种工艺中分别存在E3.1导电胶未完全固化和E3.2助焊剂两种引入水汽的可能。导电胶未完全固化分析过程类似E2.2烘烤不充分,如能排除烘烤条件和烘烤时间异常,则E3.1现象可排除。而E3.2助焊剂引入的水汽难以通过常规烘烤进行水汽清除,建议使用金锡、金硅、金锗等不需要采用助焊剂的合金焊料进行焊接,确保腔体内部水汽含量满足国军标要求。
2.3.4 E4外壳漏气
此处的外壳漏气是在高温储存后RGA试验水汽超标的外壳漏气现象。E4外壳漏气应为非常细微漏气以至于封装后水汽含量未发现异常,但针对高温储存后的外壳细漏现象,检测的首选方法还是通过He检漏进行确认。
2.3.5 E5材料水汽释放
如封装后RGA检测,水汽含量满足国军标要求,经过高温储存后水汽含量明显增加,主要有两种来源,吸附在材料表面的水汽和分布在材料内部的水汽。前者通过正常烘烤在很短时间内就可去除;而材料内部的水汽则需要很长时间才能去除,材料本身、镀层、导电胶、芯片及金丝表面及内部都有可能释放水汽导致封装内水汽含量的超标。
2.3.5.1 E5.1导电胶释放
导电胶主要由树脂基体、导电粒子和分散剂等组成。环氧树脂本身易吸水,同时导电胶内各有机材料,如果固化不完全甚至固化完全的条件下,经过长期高温存储,也有可能释放出CO2,H2O、H2等,造成水汽或氢含量超标。此外管芯和衬底的有机粘接材料在固化后存在许多空洞和气泡,空洞和气泡中含有水汽不易去除,密封后也会随热应力的激发慢慢的释放出水汽。因此对于导电胶的使用,可以依据使用经验,选用经多个型号产品使用无异常的胶类型号且对粘接后采用X光检测其空洞情况,按照国军标要求进行空洞率控制筛选。
2.3.5.2 E5.2腔体内材料释放
镀金金属材料内部吸附大量的氢气和水汽,在密封环境中,通过长时间高温烘烤,必然会造成封装内部水汽和氢含量增加。管壳壁的微小划伤等也可产生毛细管凝聚作用,在密封时或密封后的热应力作用下,凝聚的水汽也会释放出来。目前对于腔体材料释放水汽的情况,各单位的工艺水平和使用经验均存在差异,需进一步分析研究。建议对腔体内部镜检,镀金后加热预处理,观察是否存在鼓泡(可利用鼓泡的产生定性表征含水汽的程度)等方法,排除潜在水汽超标因素,提升产品成品率。
2.3.5.3 E5.3内部器件及材料释放
组件内部装配的主要是芯片,信号连接电路,以及起电气互联的金丝金带或者铝丝铝带等,随着组件设计的发展,其中芯片及连接电路均可采用半导体材料及工艺实现,选用LTCC或者HTCC,DBC等材料替换原有的PCB板,可有效降低该失效现象。
3 结束语
本文对各种微电路、混合电路,多芯片模块等组装器件内部水汽含量超标的原因进行分类分析,并就各种原因进行验证。随着武器装备的发展以及各种组件器件对使用环境的严苛要求提高,水汽含量超标还需要进一步解决。