摘 要: 在芯片级铷原子钟中,需要微腔体来承载Rb—87滤光泡,为此,提出了一种用于制作高品质微腔体的新技术。为了获得光滑的腔体侧面和避免腐蚀过程中凸角处产生削角现象,研究中采用了超声腐蚀技术和凸角补偿技术。首先,分别在纯KOH溶液,并结合搅拌和超声等方法,对(100)硅片进行湿法腐蚀,并运用激光共聚焦扫描显微镜对腐蚀后的{111}表面进行粗糙度测量,表明运用超声腐蚀技术可以获得光滑的{111}腔体侧面。在此基础上,引入条形掩模凸角补偿方法进行微腔体腐蚀。实验结果表明:在80 ℃、质量分数为30 %KOH、超声频率和功率分别为59 kHz和160 W的溶液中腐蚀,其{111}腐蚀表面粗糙度为0.117 μm,同时条形的长度取1200 μm时,可以获得平滑规整的微腔体。
关键词: 微腔体; 铷原子钟; 各项异性湿法腐蚀; 超声腐蚀; 激光共聚焦扫描显微镜; 凸角补偿
0 引 言
硅各向异性腐蚀工艺是MEMS 加工技术的重要组成部分。(100)硅片各向异性腐蚀后,{111}斜面与{100}底面成54.74°。通过提高KOH腐蚀溶液的溶度、在腐蚀溶液添加异丙醇、腐蚀过程中采用磁力搅拌等技术,而后进行表征,发现上述腐蚀技术能够明显改善{100}晶面的腐蚀质量,能够有效降低腐蚀表面的粗糙度[1~3]。相比较而言,对于{111}腐蚀表面形貌状态的研究比较少,这与AFM,SEM等形貌设备在斜面表征功能上存在着局限性有关。激光共聚焦扫描显微镜(laser scanning confocal microscope,LSCM)弥补了这一缺陷,它可以对{111}腐蚀表面进行定性和定量分析。LSCM 所具有的共聚焦成像,光学层析和扫描过程中光强调节等特点[4],使得LSCM具备大角度斜面粗糙度的测量功能。
微小型铷原子钟或称芯片级原子钟不仅可以提供精确的时间标准,而且体积小,功耗低,在国防和民用的众多领域有广泛的应用前景,可以为卫星通信技术、全球定位系统(GPS)、雷达系统、交通控制系统以及电力调度等提供精确时间标准[5]。微空腔是微小型铷原子钟用于放置滤光泡的载体[6],要求空腔体形制规则,空腔体四周侧壁平滑。采用各项异性腐蚀的技术制作微空腔,依据其原理,空腔体四周侧面是{111}面。鉴于{111}面腐蚀研究相对缺乏的状况,本文将探讨腐蚀改进的工艺并结合LSCM 的表征手段,以获得侧壁光滑的微空腔体,同时针对硅进行各向异性腐蚀会产生削角现象,在微空腔体凸角处将采用条形补偿的方法,保证微空腔的形状规则, 用于芯片级原子钟。
1 制造工艺过程
选用采用4 in(l in=2.54 mm),n型、厚度为900 μm的双面抛光硅片作为实验片,具体工艺步骤如表1所示。所设计的的微空腔体如图1所示,单个腔体的单边尺寸从2 000~4 000 μm不等,腔体的凸角处在各向异性腐蚀时要采用凸角补偿,避免产生削角现象。
表1 微空腔的制作工艺步骤
Tab 1 Fabrication process of micro-cavity
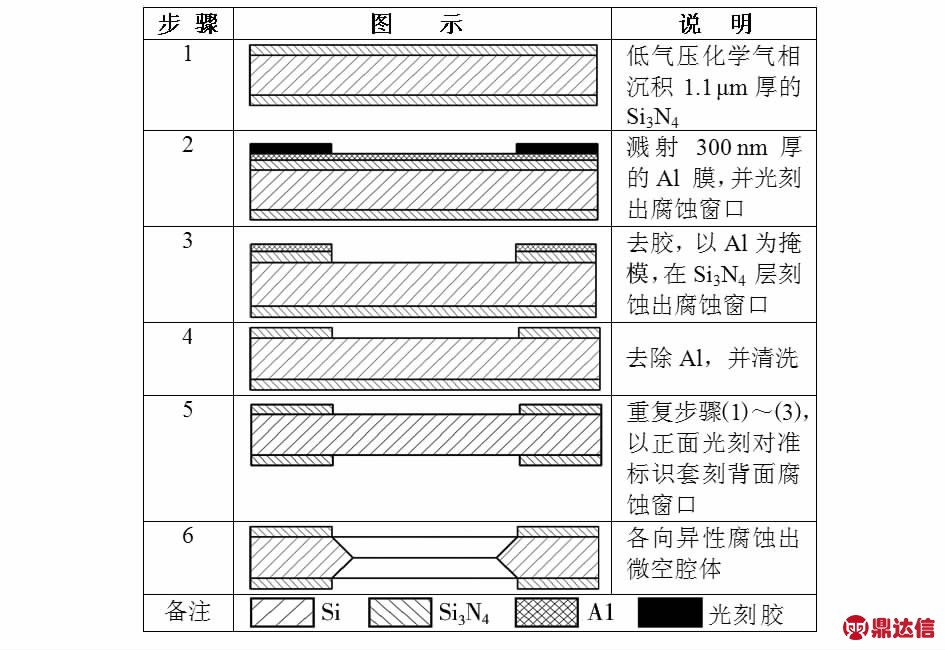
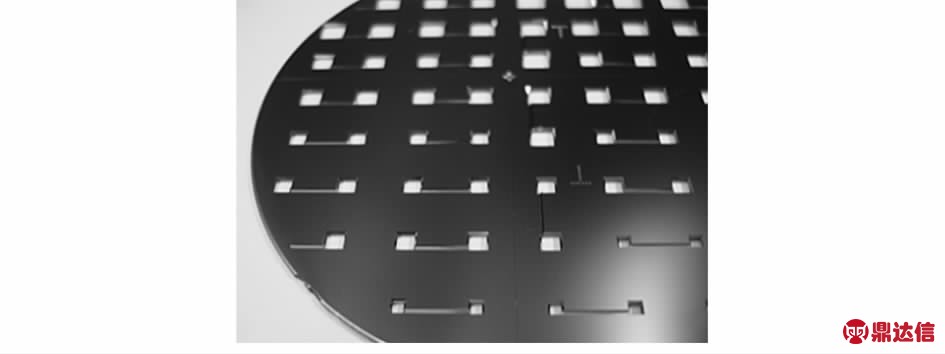
图1 硅的各向异性湿法腐蚀
Fig 1 Anisotropic wet etching of silicon
2 LSCM的表征技术
2.1 LSCM成像原理
图2为共聚焦成像原理。LSCM采用点照明方式,入射光线和发射光线对于物镜焦平面是共轭的,这样来自焦平面上下的光线均被针孔阻挡,当针孔大小合适时,便可获得高清晰的图像。LSCM采用短波长激光作为点光源,不仅可以提高水平分辨率,而且具有高亮度、高纯度等特点。在点照明状态下,为了获得完整的样品表面信息即多点的信息,则必须使入射光线在焦平面(XY) 上逐点逐行扫描,将每点扫描的图像信息经过PC采集、存储、处理,转换后合成二维图像。三维图像是Z方向以一定间距扫描,得出Z方向位置的多幅X—Y图像,并经过PC堆积合成,获得三维带有高度信息的重建图像。研究中采用Olympus公司生产的OLS1200—FAR2型LSCM。该设备采用He—Ne激光束作为光源,其横向分辨率为0.15 μm,纵向分辨率为0.01 μm。
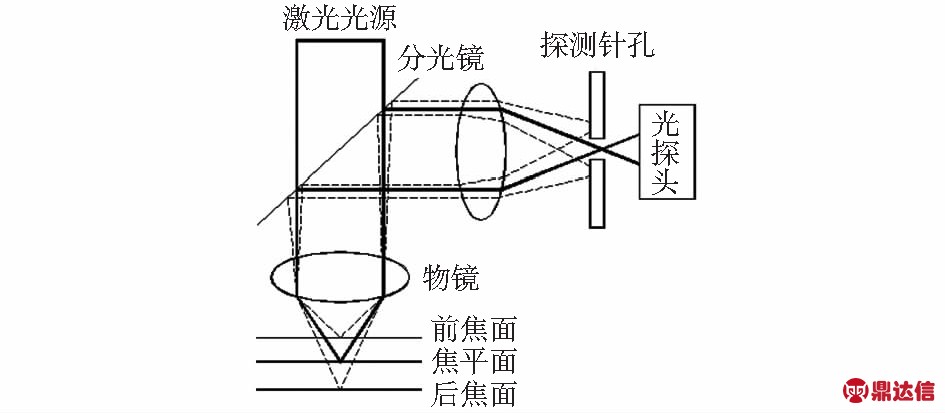
图2 LSCM的成像原理
Fig 2 Imaging principle of LSCM
2.2 斜面表征
根据LSCM成像原理可知,LSCM的分辨率除了与光源波长有关外,还取决于针孔直径与物镜的数值孔径。由于有针孔的存在,所用光源和光探头都是点状的,只有来自焦平面的光可以参与成像,而其它来自焦平面上、下的光由于不能进入针孔而不能参与成像,使分辨率较普通光学显微镜大为提高,显著改善了视野的广度和深度。此外,由于纵向扫描装置的存在,使得LSCM不但具有横向分辨率,还具有纵向分辨率,不但增加了同一平面两点间的分辨率,也使得各横断面的图像能够清晰地显示。在整个扫描过程中,上下2个表面设置的光强强度较低,而斜面设置的光强强度较高。光学系统在向被测表面逼近的过程中,光探头接收到的光强经历了一个从无到有、从弱到强、再变弱直到无的过程。这样,可根据判断光强的最大值来确定光探头在被测表面准确位置,从而准确描绘出整个斜面的形貌[7]。
图3所示为硅片在80 ℃下,质量分数为30 %的KOH 溶液后应用LSCM进行表征。图4表示应用LSCM所具备的“Curve-Fitting”功能对整个3D图进行旋转,使{111}斜面旋转为平面,以利进行表面粗糙度的测量。图5是对旋转后的{111}面进行粗糙度测量,其Rq值为0.169 μm。
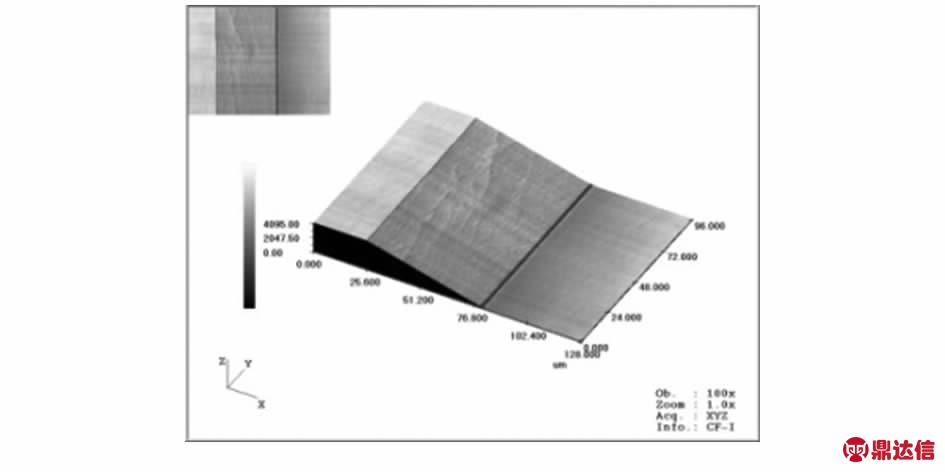
图3 LSCM 表征{111}腐蚀面
Fig 3 The etched surface Si{111}surface characterized by LSCM
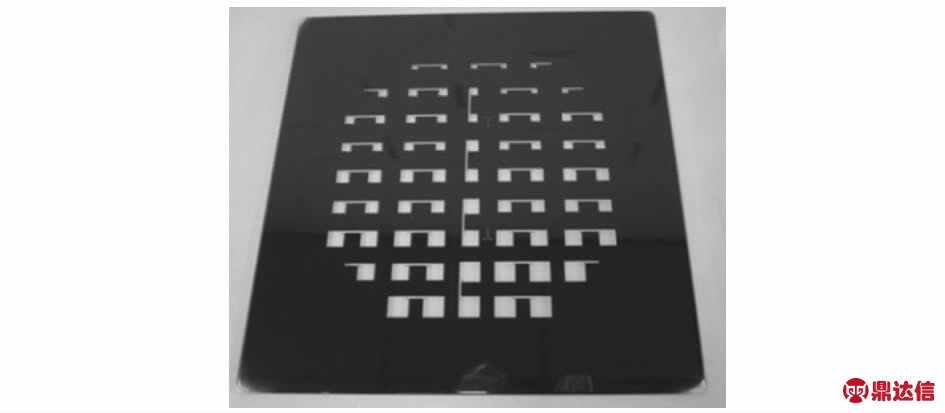
图4 斜面旋转为平面
Fig 4 Inclined Si{111}plane rotates to flatplane in LSCM

图5 {111}腐蚀面粗糙度测量
Fig 5 Roughness measurement of the etched surface of Si{111}
3 基于各向异性腐蚀之{111}斜面粗糙度的改善
3.1 超声腐蚀系统的改进
(100) 硅片分别在纯KOH 溶液,带有磁力搅拌的KOH 溶液和带有超声的KOH溶液中腐蚀,并用LSCM表征{111} 面的腐蚀结果。图6为改进前的超声腐蚀系统,瓶盖通入冷却水,可有效防止腐蚀溶液受热挥发。此系统的不足在于超声炉加热器置于底部,另外,长时间腐蚀后底部的超声换能器会发热,导致腐蚀瓶底部溶液的温度高于腐蚀瓶顶部溶液的温度,其温差可达2°~3°,从而造成腐蚀速率的不均匀。
图7为改进后的超声腐蚀系统,该系统不采用超声机自带的加热装置对溶液进行加热,而是引入环形加热圈,经过恒温水浴锅加热后的去离子水在环形加热圈内进行回流,从环形加热圈顶部流入,再从环形加热圈底部流出,最后回流至恒温水浴锅。同时超声能增加搅拌作用,有助于改善腐蚀溶液各个层面的温度的均匀性。采用该系统,其溶液温差可控制在0.5°之内。
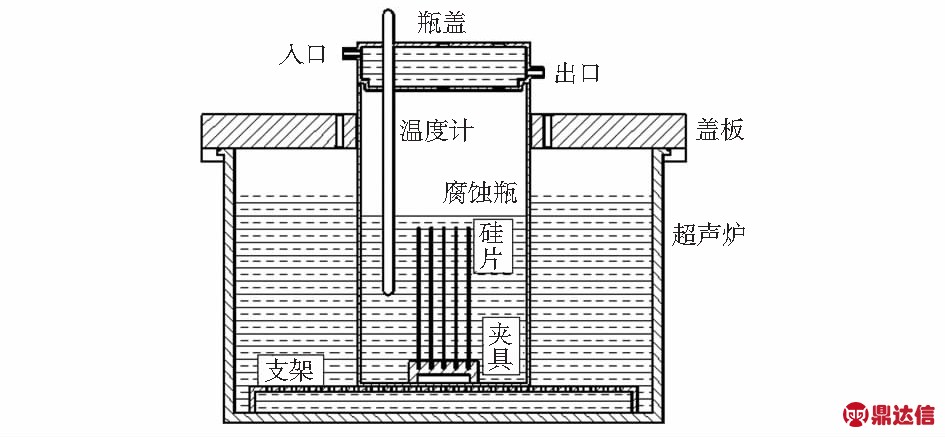
图6 改进前的超声腐蚀系统
Fig 6 Pre-improved system of etching under ultrasonic stirring

图7 改进后的超声腐蚀系统
Fig 7 Post-improved system of etching under ultrasonic stirring
3.2 实验结果
实验选用质量分数为30 %KOH的腐蚀溶液,腐蚀溶液质量分数大于30 %,可以获得比较平滑的腐蚀表面[3,7]。图8~图10分别是(100) 硅片在80 ℃,30 %的KOH溶液;80 ℃,30 %KOH,磁力搅拌功率为400 W的溶液;80 ℃,30 %KOH,超声频率与功率分别为为59 kHz和60 W的溶液中进行各向湿法腐蚀后,运用LSCM对{111} 腐蚀斜面进行表征的结果。
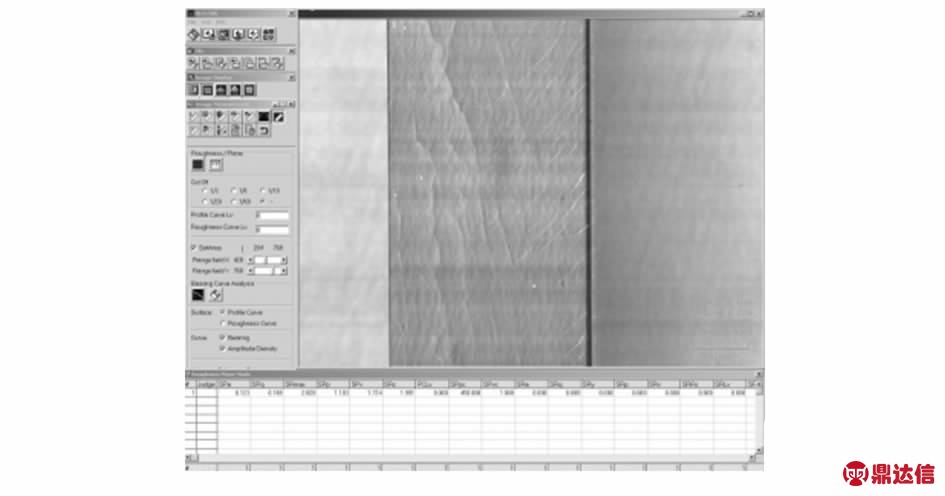
图8 纯KOH溶液腐蚀后表面形态
Fig 8 Surface morphology of Si{111}plane etched by pure KOH solution
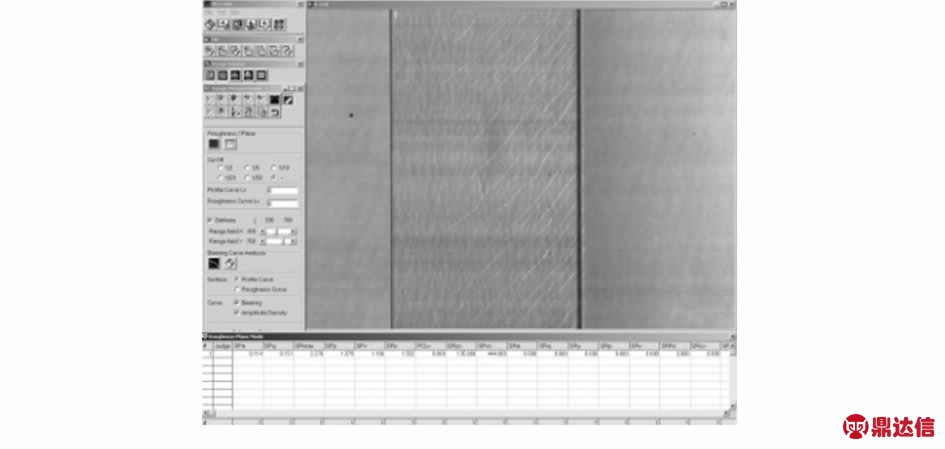
图9 磁力搅拌腐蚀后表面形态
Fig 9 Surface morphology of Si{111}plane after etching under magnetic stirring
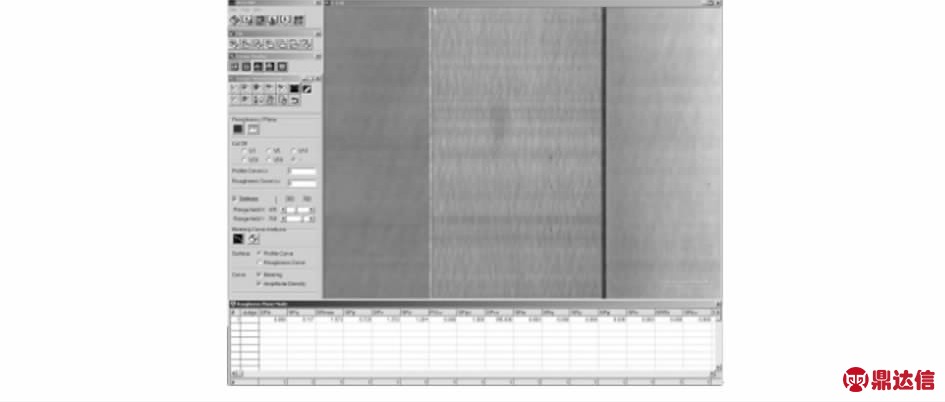
图10 超声腐蚀后表面形态
Fig 10 Surface morphology of Si{111}plane after etching under ultrasonic stirring
表2为在3种不同工艺下腐蚀,{111}腐蚀表面的粗糙度Rq值。实验结果说明:采用超声腐蚀的方法,能够显著改善腐蚀的表面质量。上述3种不同实验的腐蚀速度大致相等,约为75.5~76 μm/h。
表2 腐蚀表面粗糙度
Tab 2 Surface roughness of the etched Si{111}plane
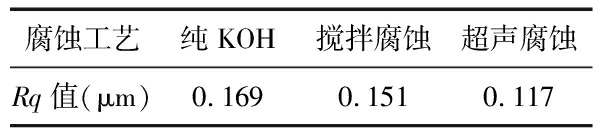
3.3 磁力搅拌和超声对{111}腐蚀表面粗糙度的改善
应用KOH腐蚀硅的化学反应机理如式(1)所示。各向异性腐蚀过程中产生的氢气是造成腐蚀表面粗糙的主要原因。如图11所示,氢气气泡附着在硅表面,形成了“假的”掩模层,阻碍了腐蚀溶剂和硅原子的反应,不仅会使腐蚀速率明显降低,同时会使腐蚀表面形成橘皮状,造成腐蚀表面粗糙度的增加。
Si+2KOH+H2O→K2SiO3+2H2↑.
(1)
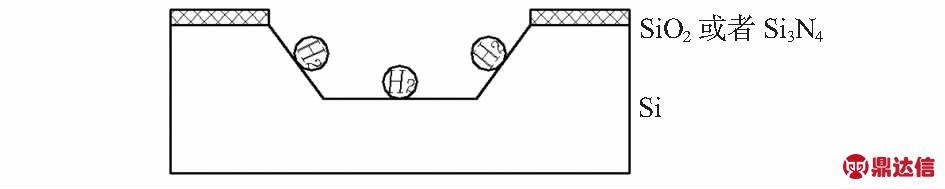
图11 氢气形成“假的”掩膜层
Fig 11 Pseudo-mask layer on the etched surface caused by H2
如图8所示,(100)硅片经纯KOH溶液腐蚀后,{111}斜面有明显的橘皮现象。如图9所示,与纯粹的KOH溶液腐蚀相比,搅拌腐蚀可以改善腐蚀表面质量,这主要是基于磁粒搅拌带动腐蚀液流动,以达到对流的作用,促使氢气气泡脱离腐蚀表面,但此方法无法达到均匀流动和快速扩散的现象,因此,改善腐蚀表面质量的作用有限。
如图10所示,超声能够显著提升{111}腐蚀表面质量,这主要是基于超声空化的作用。空化是指在液体中由于超声波的物理作用,某些地方形成局部的暂时的负压区,从而引起液体或液固界面的断裂,形成微小的空泡或气泡。当声压达到一定时,气泡迅速增长,然后突然闭合,在气泡闭合时产生冲击波,在其周围产生上千个大气压力,破坏氢气气泡黏附在硅片表面上而使它们分散于腐蚀溶液中[8]。超声空化在固体和液体表面上所产生的高速微射流能够快速去除氢气气泡,对氢气气泡起到机械剥离作用,同时超声空化还能增加腐蚀溶液机械搅拌的效能,强化腐蚀溶液的腐蚀功能,提升促使腐蚀溶液与硅原子的化学反应效率。所以,采用超声腐蚀能够明显改善{111}斜面的表面腐蚀质量。超声腐蚀的工艺参数为:腐蚀温度80 ℃,KOH腐蚀溶液质量分数为30 %,超声频率为59 kHz ,腐蚀功率为160 W。
4 基于超声各向异性腐蚀的凸角补偿
4.1 凸角掩模补偿图案的选择
以正方形或长方形方块设计的掩模板图形来制作微空腔,如图1所示都存在着凸角,在各向异性腐蚀过程中不可避免会存在凸角因为腐蚀而导致削角现象,如图12所示。通过LSCM表征,其主要的削角斜面与底面{100}的夹角为46.3°,即为{311} 面,其与{100} 面交线方向为〈310〉方向,如图13所示。
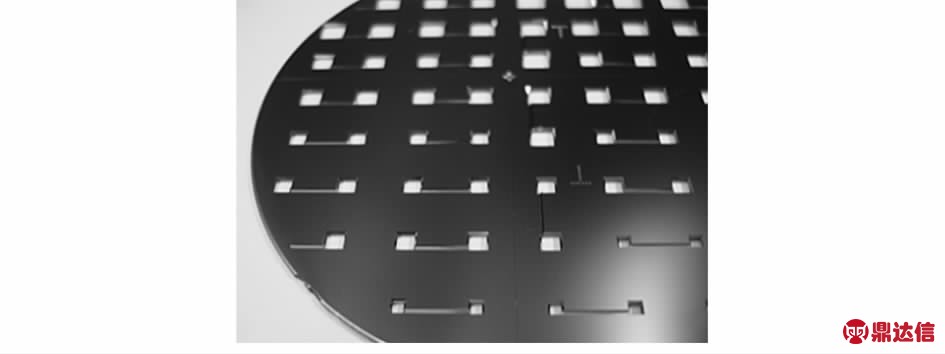
图12 腐蚀过程中的凸角削角
Fig 12 Convex corner undercutting in the process of etching

图13 削角斜面的表面形态
Fig 13 Surface morphology of undercutting inclined plane
为了获得规整的微空腔体,必须进行凸角补偿,主要是依据削角斜面的晶面方向制定掩膜补偿图案。研究中采用的补偿图案是条形掩模补偿,如图14所示。
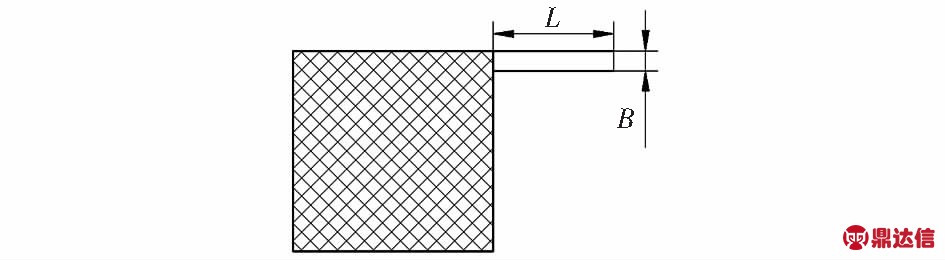
图14 条形掩模补偿
Fig 14 Strip mask compensation
根据经验公式[9~11],条形的长度L取决于腐蚀深度H,即为
L≈2.7H.
(2)
条形的宽度为
B=0.2L.
(3)
制作微空腔所需的硅片厚度为900 μm,由于是采用双面腐蚀,故腐蚀深度H为450 μm,根据式(2)和式(3),条形的长度L和宽度B分别为1 215,243 μm。
4.2 微空腔的制备
采用超声湿法腐蚀制备微空腔,其工艺参数为:腐蚀温度80 ℃,KOH腐蚀溶液质量分数为30 %,超声频率为59 kHz,腐蚀功率为160 W。针对凸角,采用条形掩模补偿法,条形的长度分别为1 150,1 200,1 250 μm,对应宽度为230,240,250 μm。图15所示为用于制作微空腔所需的掩模版。
图16显示微空腔的腐蚀过程,采用条形长度为1 200 μm的补偿图案最佳。验证了经验式(2)和式(3)所计算的条形尺寸。经过6 h腐蚀后,形成微空腔。图17是采用上述工艺,所获得的侧壁光滑、形制规整的微空腔。
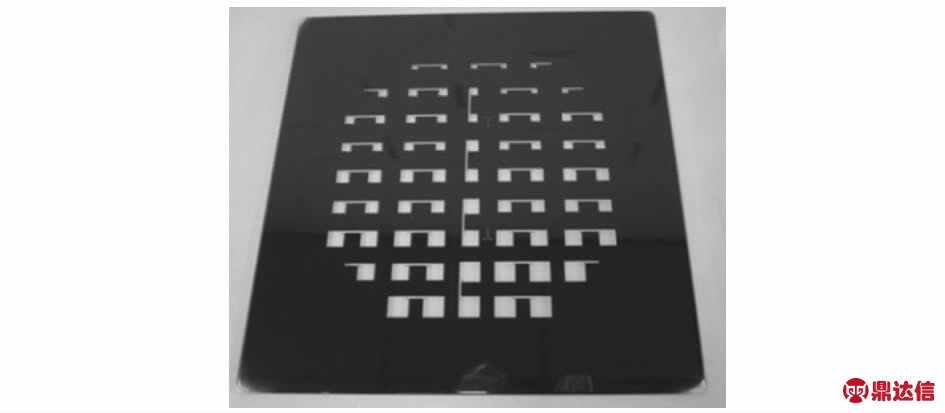
图15 用于制作微空腔所需的掩模版
Fig 15 Mask for fabrication of micro-cavity
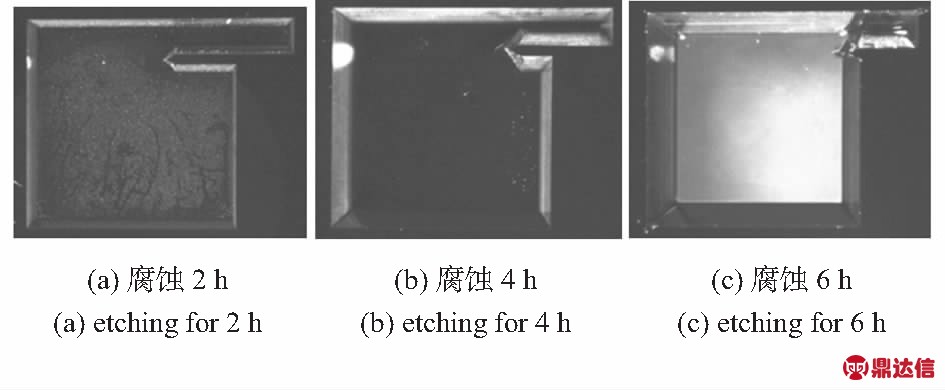
图16 湿法腐蚀制备微空腔
Fig 16 Micro-cavity fabricated by wet-etching
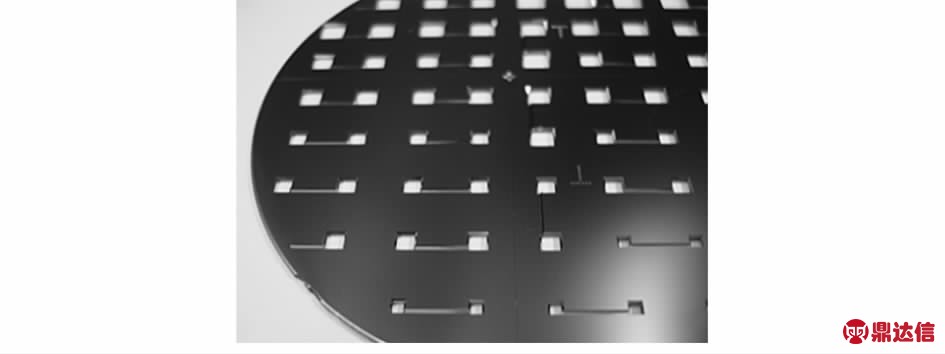
图17 微空腔
Fig 17 Micro-cavity
5 结 论
1)在硅各向异性腐蚀中引入超声技术,基于超声空化原理,对黏附在硅片腐蚀表面上氢气气泡起到有效的机械剥离作用,从而明显改善{111} 斜面的腐蚀质量;
2)利用LSCM对所腐蚀的{111} 斜面进行表征,实现了对腐蚀斜面的定性和定量分析,弥补了AFM,SEM等形貌设备在斜面表征功能上所存在着的局限性;
3)采用条形掩模补偿法有效避免了凸角腐蚀过程中所产生的削角现象,经过实验认证,选用条形长度为1 200 μm,宽度为240 μm 的补偿图案最佳;
4)实验结果表明:采用上述工艺和表征手段,能够获得侧壁光滑、形制规整的微空腔,用于芯片级铷原子钟的滤光泡与吸收泡。