摘要:本文针对产业园激光封焊类腔体盖板出现不合格品的情况,分析不合格品产生的原因,提出解决方法及改变加工腔体直角R的方案,提高封焊腔体和盖板的适配性的合格率。
关键词:激光焊接;激光封焊类腔体与盖板;圆角配合
随着科学技术的发展,激光焊接技术广泛用于各行各业,特别是微电子工业中得到了广泛的应用。由于激光焊接热影响区小、加热集中迅速、热应力低,因而在集成电路和半导体器件壳体的封装中,显示出独特的优越性,得到了广泛的应用。激光焊接机是采用激光器产生的波长为1064nm的脉冲激光束经过扩束、反射、聚集后辐射被加工件表面,表面热量通过热传导向内部扩散,使工件融化,形成特定的熔池,当熔池冷却后将熔池两侧的金属熔接在一起,从而实现对被加工件的激光焊接,因此要求激光焊接位置需非常精确,务必在激光束的聚焦范围内。激光焊接是一种特殊的熔焊过程。在激光密封焊接中,容易产生两种典型的缺陷:裂纹和气孔,其中裂纹的产生因素和机加工的精度有关。
目前,在微波产品对几何尺寸的技术要求是在加工尺寸需要满足封焊要求,对需激光封焊的腔体和盖板的尺寸,其配合尺寸应设计为:腔体尺寸公差0~+0.03mm,盖板尺寸公差-0.04~-0.07mm。在加工配合中,单边配合间隙≤0.05mm,转角R允许为0.07mm。
一、激光封焊腔体与盖板的生产情况
在生产中,腔体的内腔由数铣加工,盖板外形由线切割加工。加工后经测量腔体和盖板的长度尺寸和圆角尺寸都能满足公差要求。
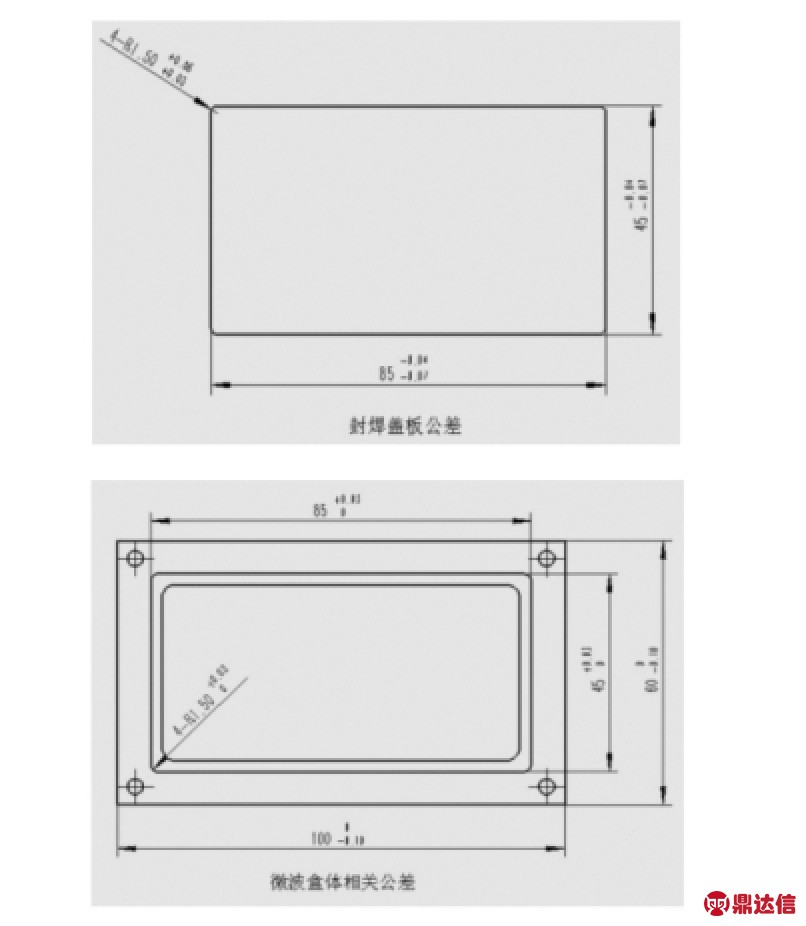
通常在加工腔体凹R时,实际的加工轨迹与数控程序的预定轨迹并不吻合,这种差异是由机床和刀具的特性造成的。首先机床与刀具的刚度有限,在加工圆角时,刀具会有一定程度的倾斜,造成轨迹偏差;另外,在加工圆角时对于机床是X轴运动转向Y轴运动的过程,实现运动的滚珠丝杠机构存在一定的空程差,导致刀具运动与电机转动的不同步,也造成了轨迹偏差,这两方面因素导致了腔体凹R的超差,同时因机床和刀具不同,超差的情况也有所不同。在加工盖板凸R时,起始切割点的确定是非常重要的。盖板的切割路线是封闭图形,所以起始切割点也是切割的终点。由于加工过程中存在各种工艺因素的影响,电极丝返回到起点时必然存在重复位置误差,造成加工痕迹,导致加工精度和外观都受到影响。当各相交角相同时,起切点的优先顺序是:直线与直线的交点、直线与圆弧的交点、圆弧与圆弧的交点。对于工件各切割面无技术要求的交点的工件,起切点尽量选择在便于钳工修复的位置上。在电火花线切割加工的轨迹控制采用数控法及自动编程,在对盖板的切割过程中电极丝的蚀除量、切割的脉冲电流以及电极丝的振动都对盖板的精度存在一定的影响。
二、提高产品合格的改进方案
改变加工参数。腔体凹R超差是由机床与刀具的刚度和滚珠丝杠的空程差造成的,当走刀速度越高时,刀具轨迹与理论轨迹偏差越大,所以可以通过在加工圆角时降低走刀速度来减少刀具轨迹的偏差。
腔体圆角凹R超差均为偏大,可以通过数控程序把理论轨迹设置为负差,与实际加工中出现的向上公差的偏差相叠加,使最终的公差控制在设计范围内,该方法需要使刀具的半径小于圆角的半径,因为当刀具半径等于圆角半径时,无法实现负差,即当圆角为R1.5mm时,使用d2的刀具和数控程序共同进行控制。同时,把加工圆角的走刀速度由330mm/min降为80mm/min,实际操作结果表明,出现不合格品的情况有所下降,但仍会出现不合格品。经分析,此类方法只能减小刀具轨迹和理论轨迹的偏差,不能消除两者之间的偏差;并且不同的机床、刀具的特性不同,偏差也不同,因此不能完全保证腔体凹R不超差,所以该方法可以降低产品的返修率。
在按照上述的加工要求加工后,在配合时盖板和腔体的间隙不是十分均匀,有的时候还有卡滞现象发生,尤其是在腔体电镀后。通过放大可以发现在微观情况下,在与之相对应的盖板的同一位置在理论上也应该是一处直角,但实际上是一处内圆角。这是由于盖板是线切割加工的,线切割是通过电火花放电产生的热量来熔解去除金属的。在加工过程中,线切割的最小角部半径是有限制的,是电极丝的半径加上加工间隙,在该处走丝过程中必然留下电极丝直径的四分之一圆弧,即R0.10mm,这是个刚性误差——不能避免的!对于上述腔体和盖板形状复杂的配合,盖板在腔体的直角处相抵,这个误差会导致配合间隙的重新分配,会直接影响腔体和盖板的焊接质量。
针对这个问题,提出的改进方法是在加工腔体的直角时,把腔体的直角加工成R0.09—0.13mm,这样就可以有效的解决配合的问题。