摘要:针对金属熔融涂覆成形过程中铝合金铺展不充分的难点以及铝合金对激光吸收率低的问题,设计了惰性气体钨极保护焊电弧辅助预热的成形装置。基于有限差分法,采用Fortran语言自编程与Flow3D软件相结合的方式,分别建立了电弧热源对熔池产生的驱动力的单独作用模型以及耦合分析模型,并阐述了熔池内温度场和流场的演化过程。研究发现,当电流为200 A时,熔池内驱动力影响由大到小的排序为表面张力、电弧压力、洛伦兹力、拖曳力、浮力,该结果可为驱动力耦合作用时熔池内部流场方向的演化提供分析基础。对焊接熔池与喷头流出的高温液体之间的传热传质过程进行了计算,发现高温液体在表面张力与分子亲和力的作用下,接触熔池的瞬间快速流进熔池。将数值计算结果与实验结果进行对比得到,熔池的最大宽度及高度误差分别为1.1%、0.6%,热影响区的最大宽度及高度误差分别为9.3%和5.4%,单层单道件的最大宽度和高度误差分别为3.5%及2.1%,表明数值计算模型对成形过程的分析有较高的可信度。
关键词:熔融涂覆;电弧预热;熔池驱动力;流场
增材制造技术将复杂的三维零件分层成形,实现了零件的降维制造,极大缩短了研发周期。传统的金属增材制造设备主要采用激光、电子束、电弧及等离子作为热源[1]。应用较为广泛的选区激光烧结技术(SLS)[2]、激光选区熔化技术(SLM)[3]、激光熔覆沉积技术(LCD)[4]以及电子束近净成形(EBM)技术[5]等均采用粉材作为成形材料。电弧填丝增材制造技术[6-8]、激光熔丝技术(LBW)以及等离子焊接熔丝技术(PAW)[9]等则采用丝材作为成形材料。以激光和电子束为热源的金属增材制造技术通常设备昂贵,采用粉材作为成形材料的增材制造技术成形效率普遍偏低,极大地限制了其应用和推广。与以激光和电子束等为热源的增材制造技术相比,电弧填丝增材制造技术在能量利用率上优势显著[10],但成形原材料局限为丝材。
金属熔融涂覆工艺是一种新兴的增材制造技术,可以快速地实现零件的近净成形。电弧预热熔融涂覆系统示意图如图1所示,成形系统采用坩埚和喷头进行供料,原材料的形式不再局限于粉材和丝材。以电磁感应加热的方式代替了昂贵的大功率激光器等热源,极大地降低了设备成本。
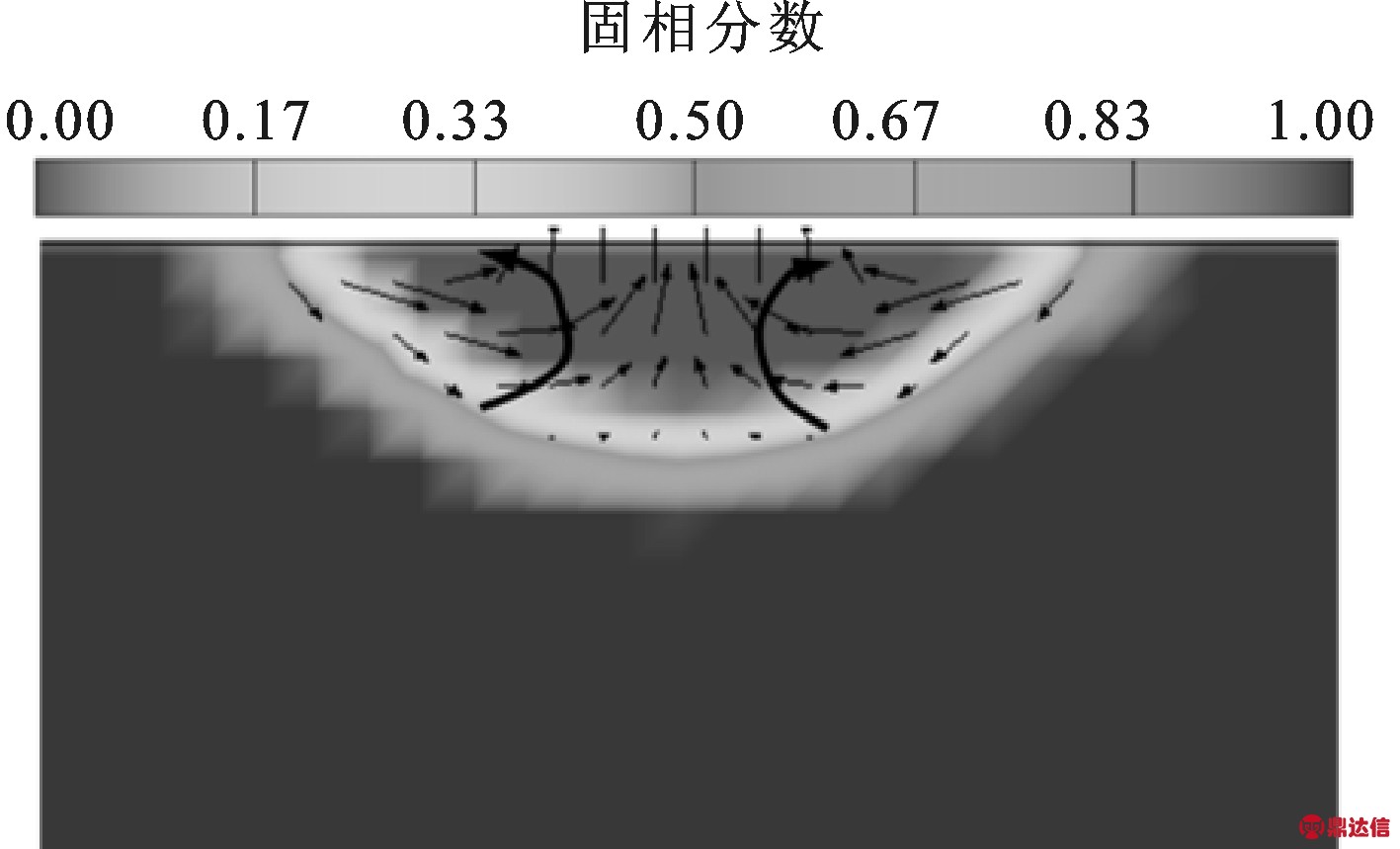
图1 电弧预热熔融涂覆系统示意图
本课题组前期对锡铅合金材料的涂覆成形做了部分研究[11]。与锡铅合金相比,铝合金的熔点及表面张力系数较大而密度较小,当基板温度低于铝合金熔点时,喷头内流出的液态铝合金在铺展、凝固过程中易团聚成球状,无法与基板达到充分的冶金结合,且无法形成均匀稳定的涂覆层。整体提高基板的温度至熔点之上会造成基板的熔化流淌,采用辅助热源在基板表面形成局部浅层熔池是实现液态铝合金充分铺展的最佳途径之一。很多学者在研究焊接熔池时没有考虑电弧带来的驱动力以及熔池表面的自由变形[12],本文基于有限差分法分别建立了电弧热源对熔池产生的驱动力的单独作用模型以及耦合分析模型,并建立了电弧辅助铝合金熔融涂覆的数值计算模型。
1 数学模型
1.1 电弧热源与驱动力
电弧辅助熔融涂覆成形工艺主要分为电弧预热及喷头涂覆两个物理过程。电弧驱动力对熔池内部流场分布的影响较大,是决定熔池形貌的主要因素之一[13]。如图2所示,熔池内的驱动力主要包括表面张力、电弧压力、洛伦兹力、浮力以及拖曳力[14-16]。
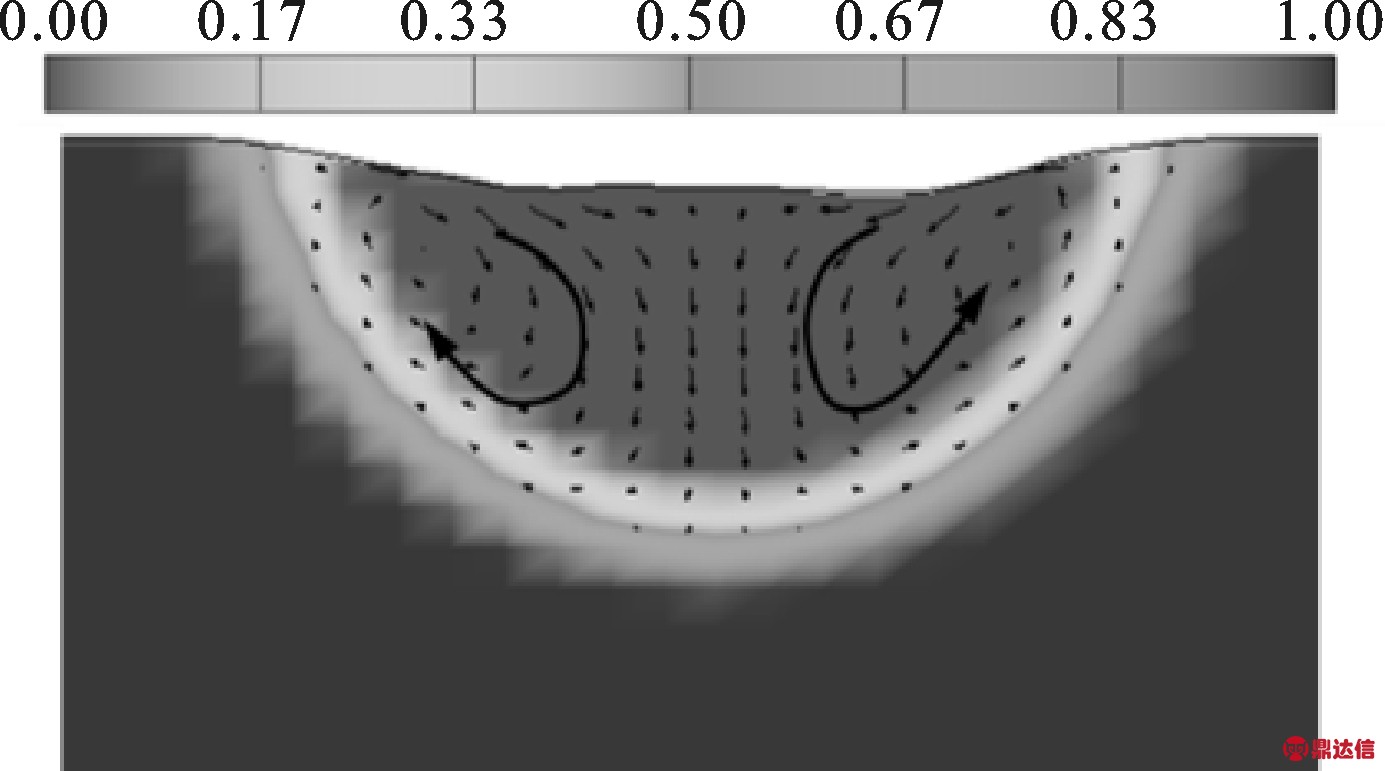
图2 熔池内部驱动力示意图
为了提高计算精度,采用与焊接热源更相匹配的双椭球热源模型[17-18]。热流密度沿热源移动方向分成前后两个椭球,数学模型如下
qf(x,y,z,t)=

(1)
qr(x,y,z,t)=

(2)
式中:qf(x,y,z,t)与qr(x,y,z,t)分别为双椭球热源前、后两部分的热流密度;ff、fr为分配系数且ff+fr=2;af和ar分别为椭圆的前后半轴长度;b、c分别为熔池的半宽和深度。
表面张力跟材料的组分以及温度有关,可采用下式进行计算[19]

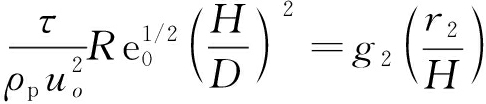
(3)
w1=w(S)10(-94.2/T+0.0396)w(Cr)
(4)
式中:为金属在熔点时的表面张力;A为表面张力随温度变化的系数;Tm为材料熔点温度;Γs为表面过饱和度;k1为分离熵;w1为活性元素的质量分数;ΔH0为热焓;w(S)、w(Cr)分别是硫和铬的质量分数。
由于铝合金在相变过程中密度随温度变化而改变,因此铝合金熔化过程中在熔池内部产生浮力,数学表达式为
Fb=-ρ0α(T-T0)g
(5)
式中:α为材料的线膨胀系数;ρ0为在参考温度T0时材料的密度,通常取室温作为参考温度。
根据文献可知,电弧压力的表达式为
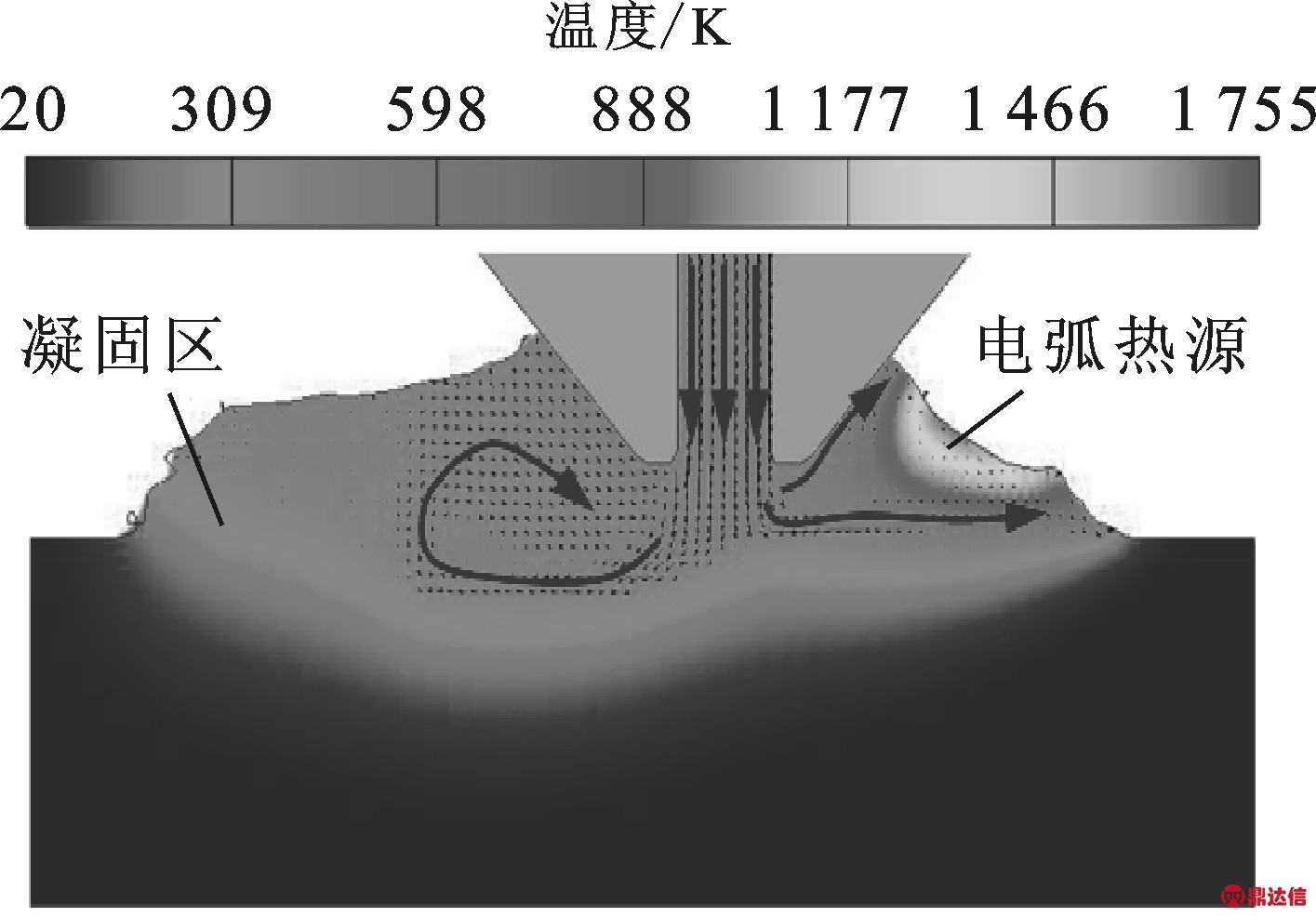
(6)
式中:μ0为空间的磁导率;rA为电弧作用的有效半径;I为电流密度。洛伦兹力是由电流与自诱导产生的磁场相互作用的结果,表达式为
F=J×B
(7)
在x、y、z方向的分力表达式分别为
Fx=
(8)
Fy=
(9)

(10)
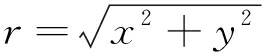
(11)
式中:σj为电流分布参数;zL为基板的厚度。
拖曳力[20]是由电弧等离子的碰撞引起的,方向从电弧中心吹向两侧,表达式为
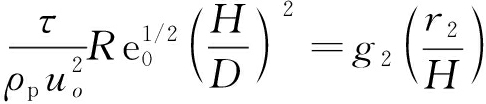
(12)
式中:τ为剪切力;ρp和u0分别为等离子的密度和初始速度;r2为受力点与电弧中心的距离;g2为通用函数;H是钨针与基板表面的高度;D为钨针的直径。
1.2 熔融涂覆过程中的控制方程
流体体积法(VOF)是建立在欧拉网格下的表面追踪方法,本文采用VOF方法[21-22]追踪流体的自由界面,不可压缩牛顿流体的控制方程为
·V=0
(13)
基于网格内液相分数的守恒方程为
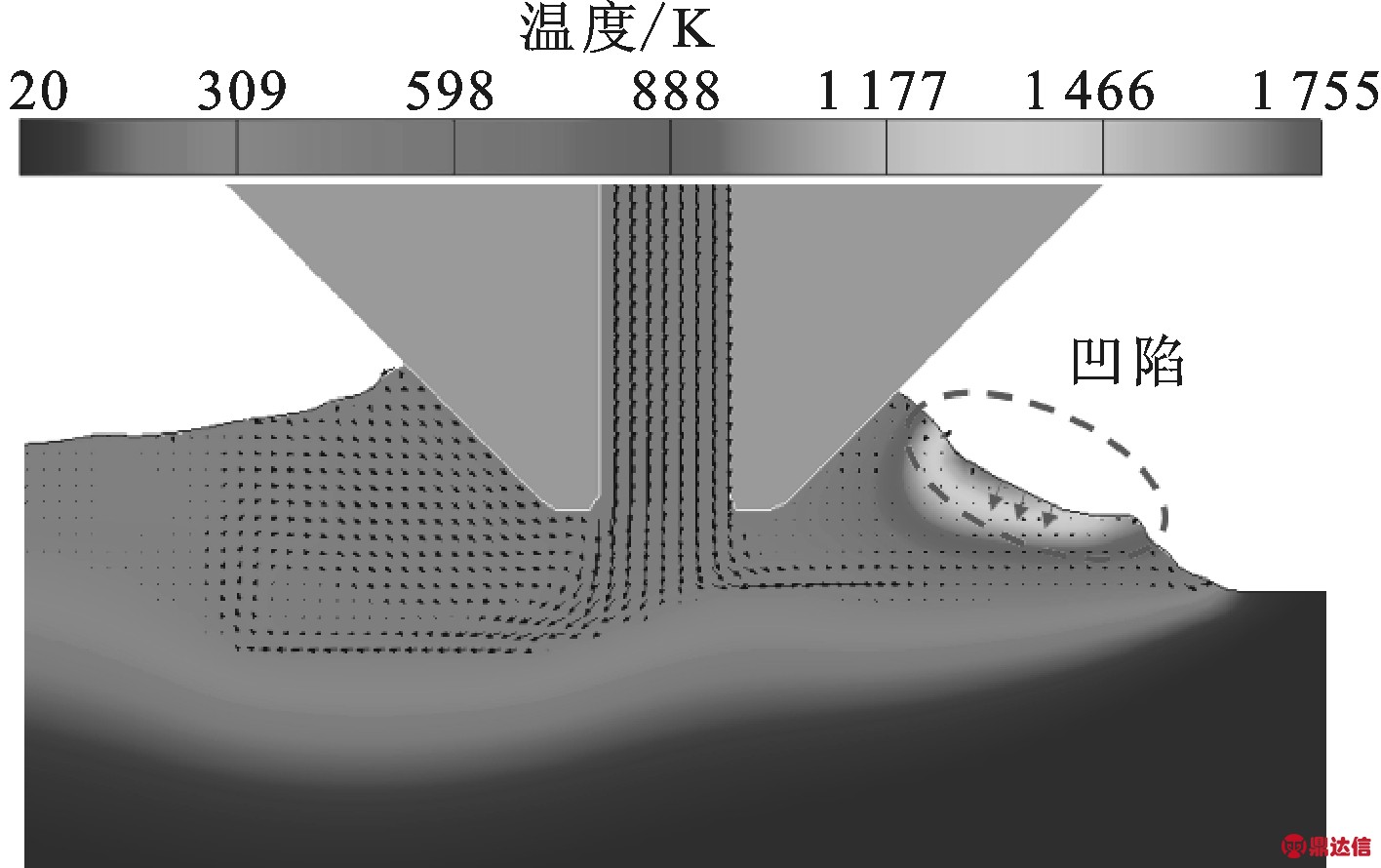
·(VF)=0
(14)
式中:F=1表示网格单元内充满流体,F=0表示网格内充满固体,0<F<1表示网格内固液共存。
采用等效热焓法来计算相变时的熔化潜热,公式为
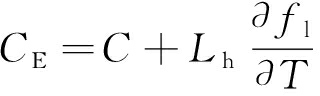
(15)
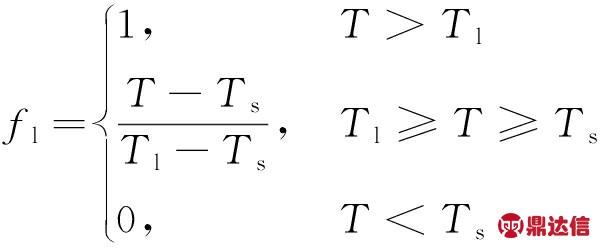
(16)
式中:CE为等效热焓;C为真实比热容;Lh是熔化潜热;Tl和Ts分别为材料液相线和固相线温度;fl为液相分数。
1.3 数值分析模型初始条件与边界条件
本文采用Flow-3D软件对电弧驱动力及涂覆过程进行建模,计算的初始条件如表1所示,2024铝合金的物性参数如表2所示。
表1 涂覆过程初始条件
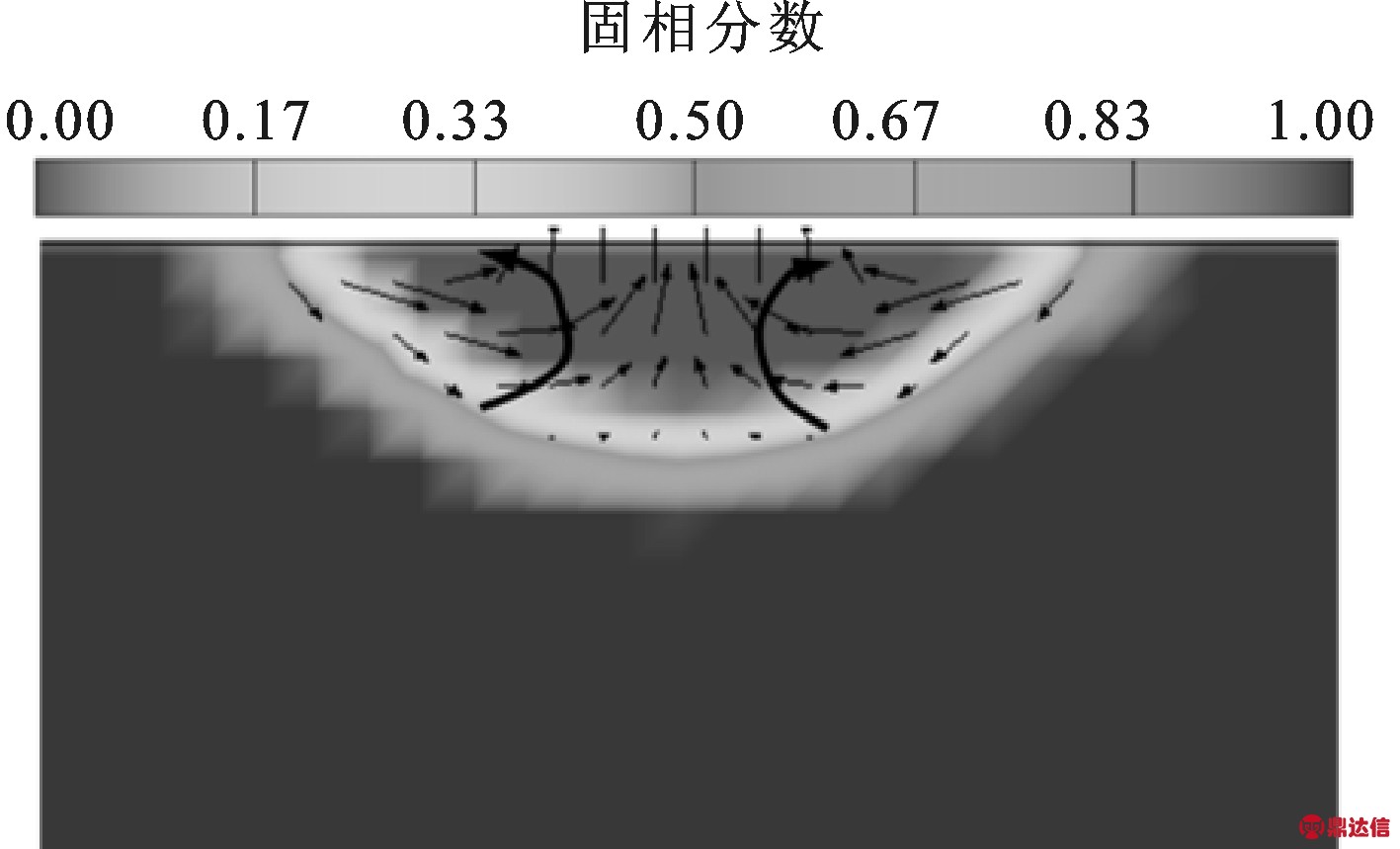
表2 2024铝合金的物性参数
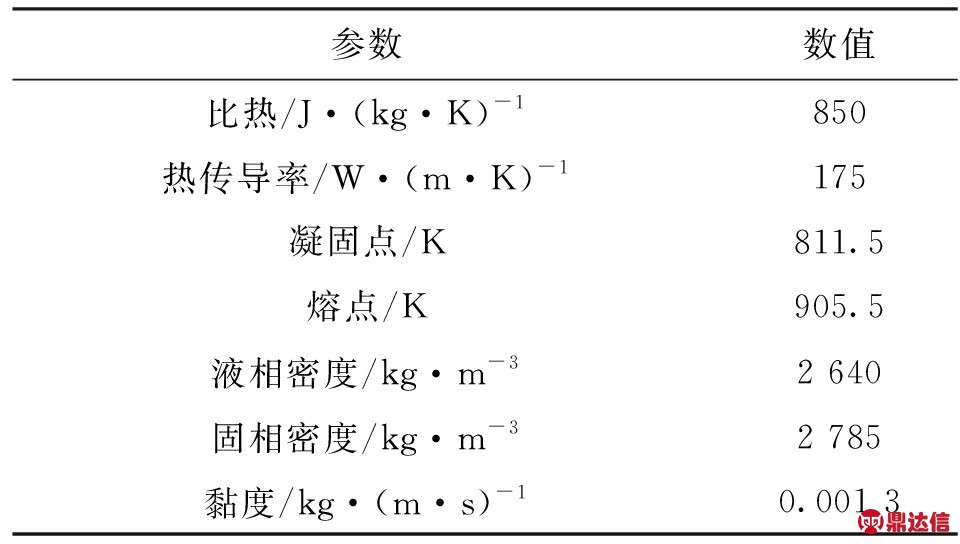
图3为数值分析模型的边界条件,与其他数值分析软件不同,Flow-3D软件对整个计算区域而非单独对计算部件进行网格划分。工艺实验过程中基板放置在隔热绝缘的云母板(型号为hp-5hp-8)上,壁面边界的导热系数设置为4.5 W/(m·K),由于计算区域与实际基板尺寸相比足够小,其余网格平面采用连续性边界条件。初始环境温度为室温(298 K)。
电弧热源及驱动力无法直接施加在模型中,控制方程分别通过Fortran语言自编程的形式与Flow3D预留接口编译到一起,程序编写的基本思路为:①追踪熔池自由表面,基于VOF思想,编写程序实时追踪熔池自由表面,确定熔池表面各网格单元的坐标;②确定热源与驱动力作用中心位置处的坐标,热源与驱动力中心位置的xc、yc坐标为焊枪钨针中心位置,是恒定的,可直接写入程序,z轴坐标zc可由xc、yc与步骤①确定;③计算各网格单元的热量与驱动力,双椭球热源与各驱动力的计算公式均为网格单元坐标(x,y,z)的显式方程,已知作用中心点坐标,可直接利用Fortran语言将公式写为代数形式,各网格单元的热量与驱动力由程序自动计算出来。
对于双椭球热源方程,网格单元x坐标大于xc与小于xc时分别施加式(1)与式(2)的热流密度。热源中心在基板上表面与y=0平面的相交线上,基板以v=5 mm/s沿x轴负方向移动。图3b为电弧与涂覆过程的耦合计算模型,为使模型表达更清楚,已将网格隐去。z方向上网格面同样采用压力边界条件,其压力设置为坩埚内气压与喷头上方金属液静压力之和,并且网格面上设置有温度为973 K的流体源项,以保证在涂覆过程中喷头内始终充满流体。其他边界条件与图3a一致。
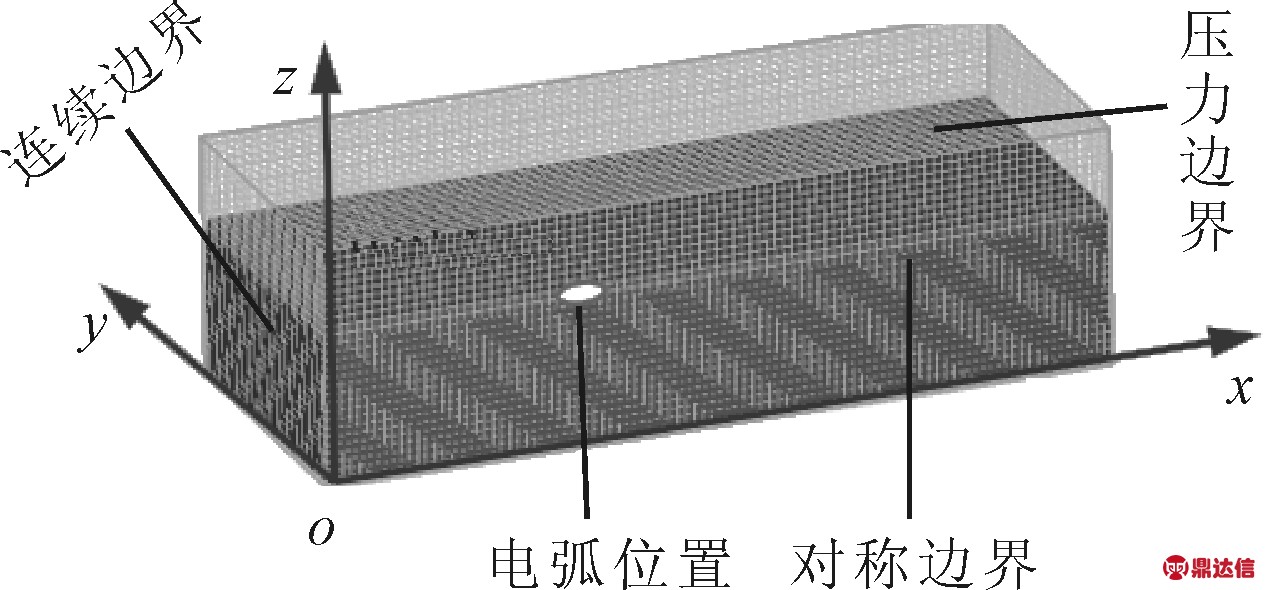
(a)电弧驱动力模型边界条件
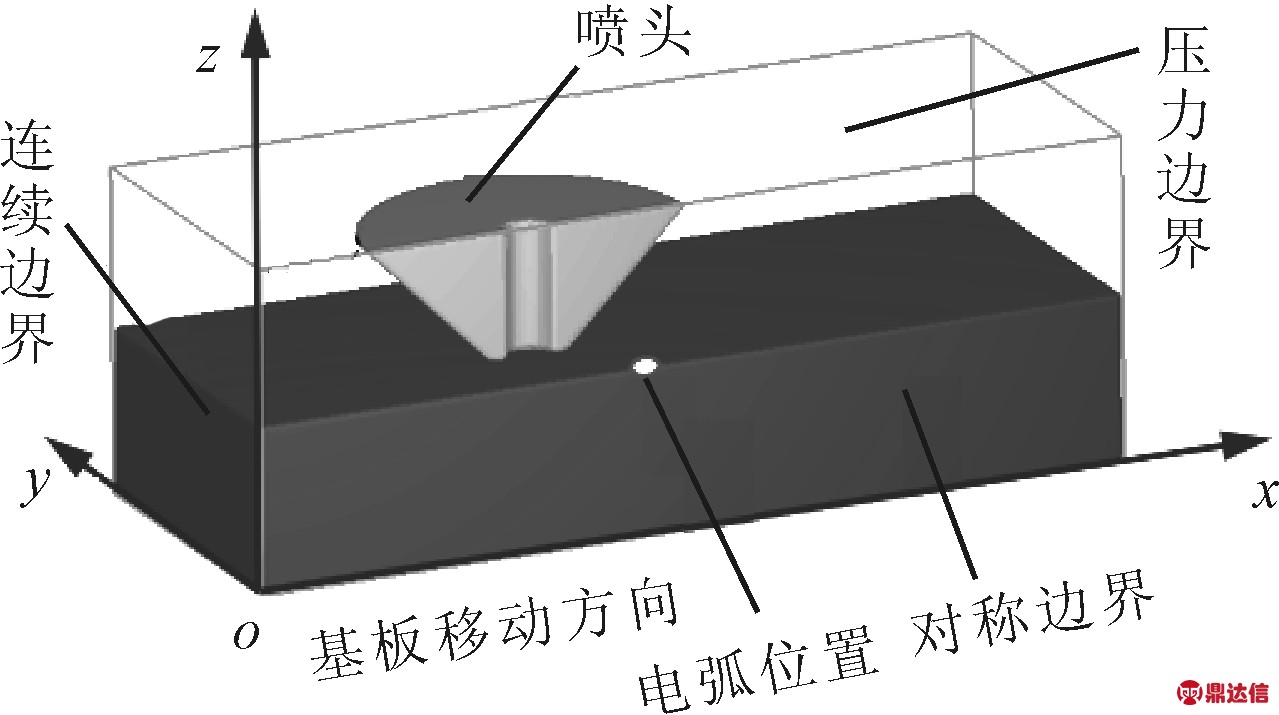
(b)电弧辅助熔融涂覆模型边界条件
图3 数值分析模型的边界条件
2 结果与讨论
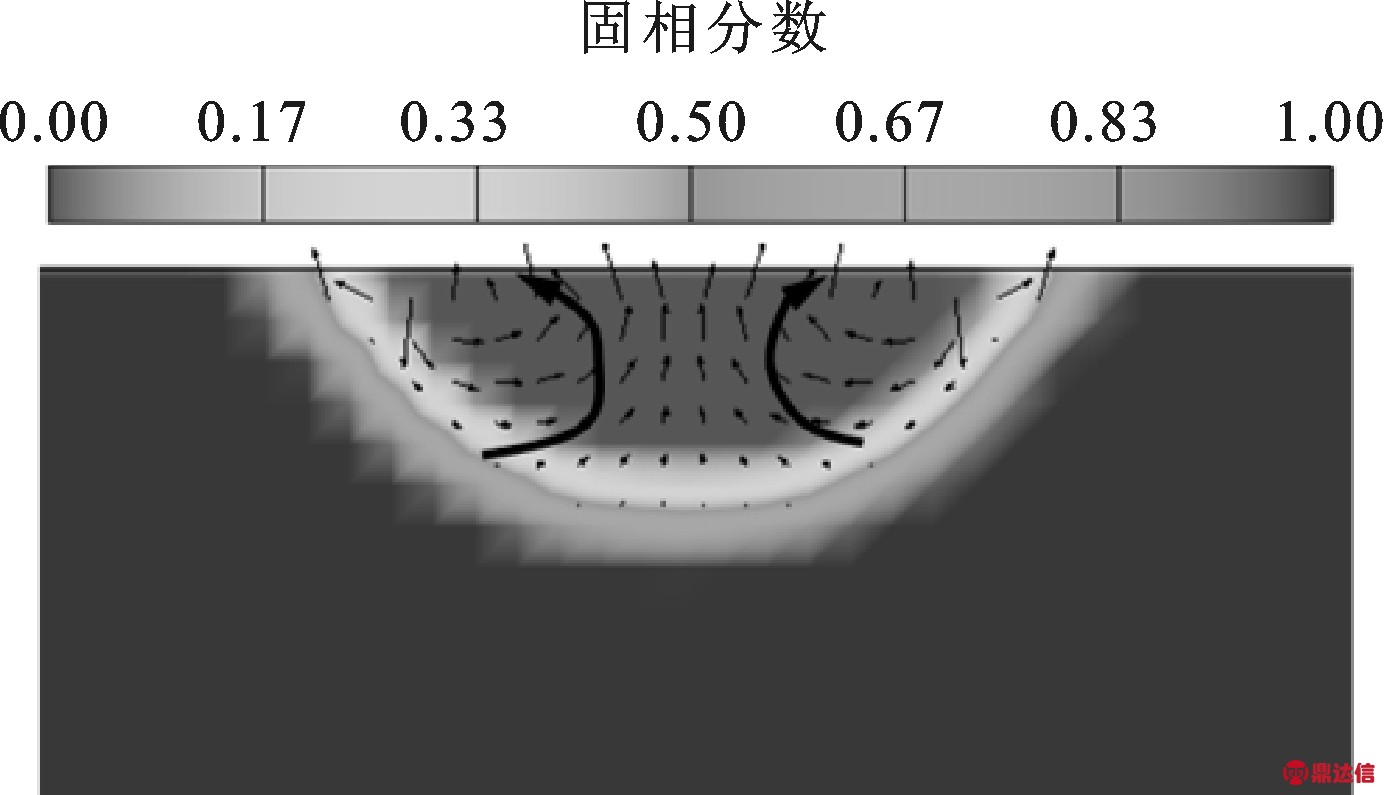
(a)表面张力
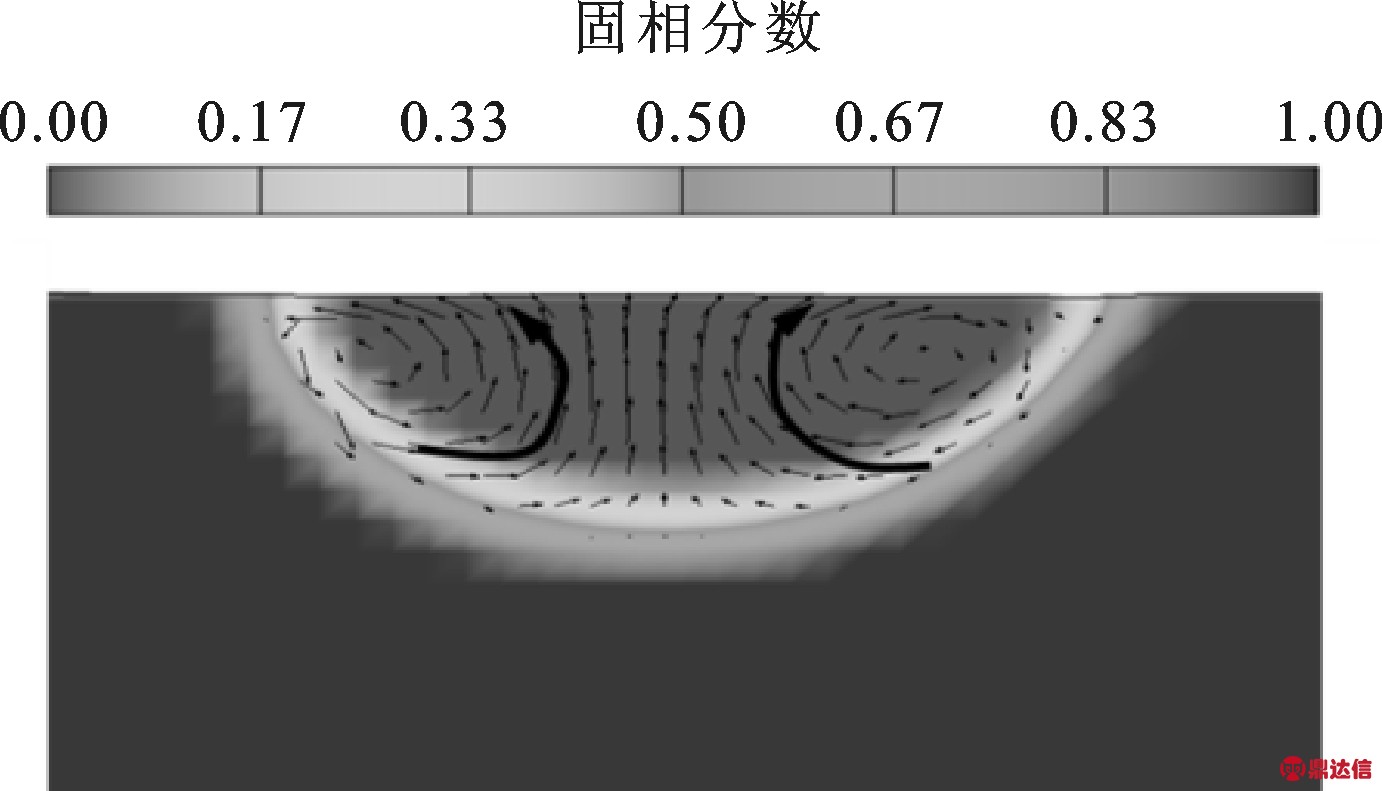
(b)浮力
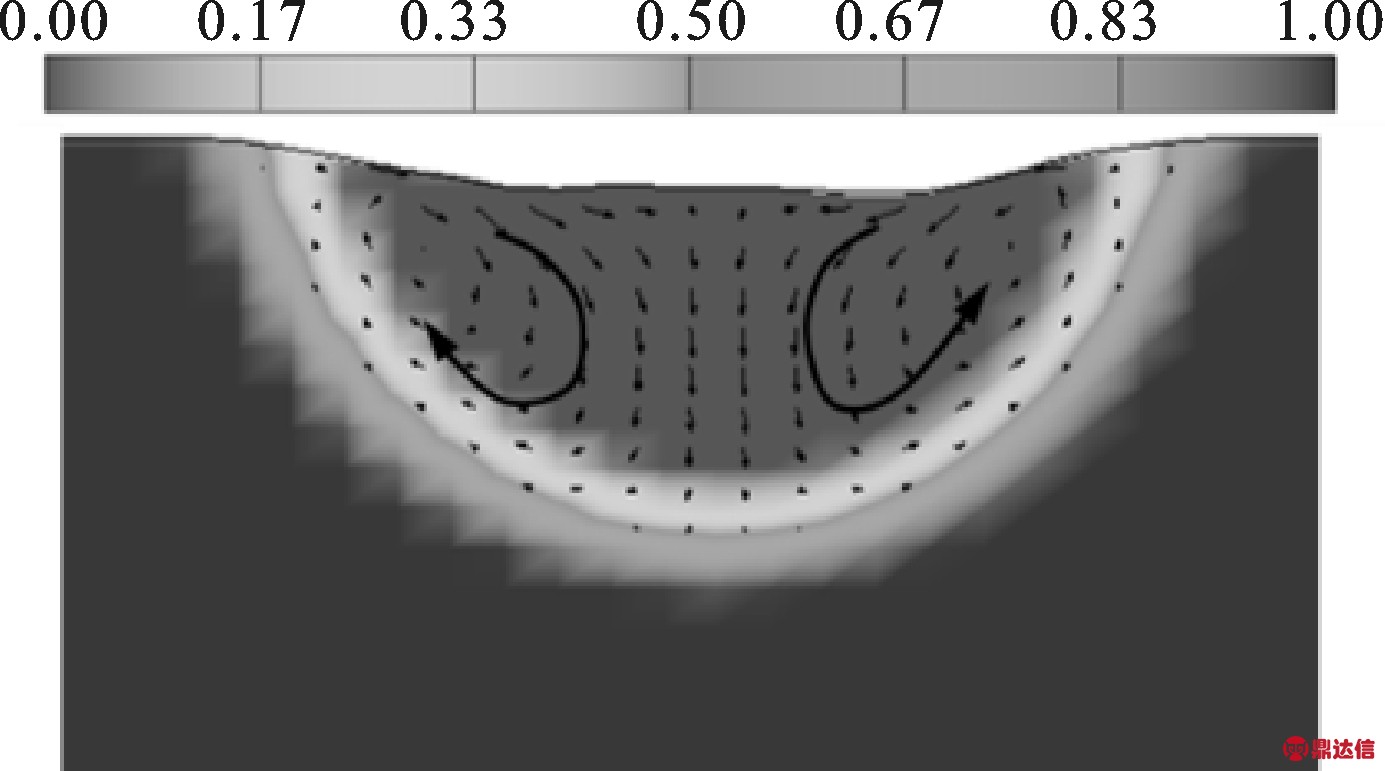
(c)电弧压力
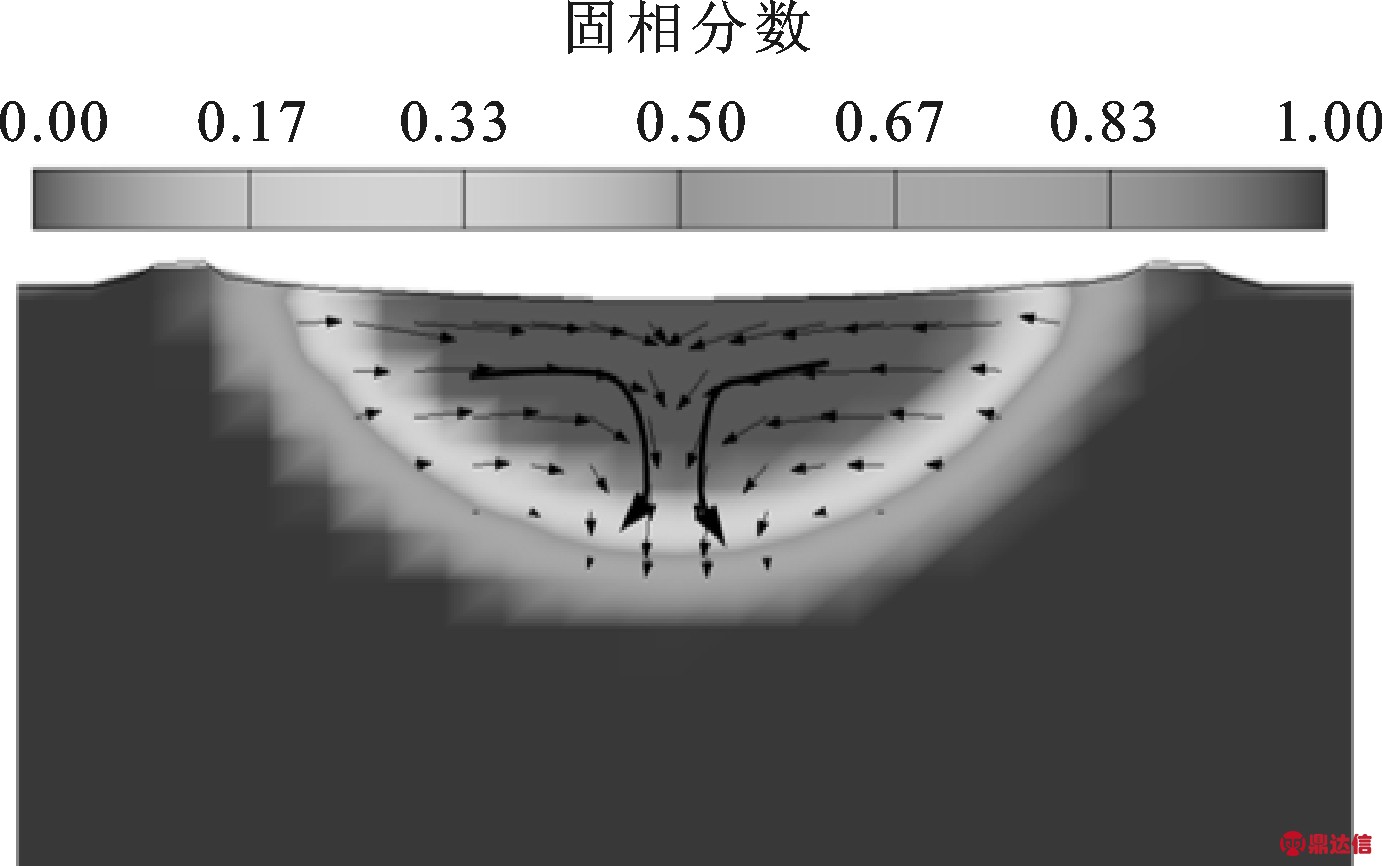
(d)洛伦兹力
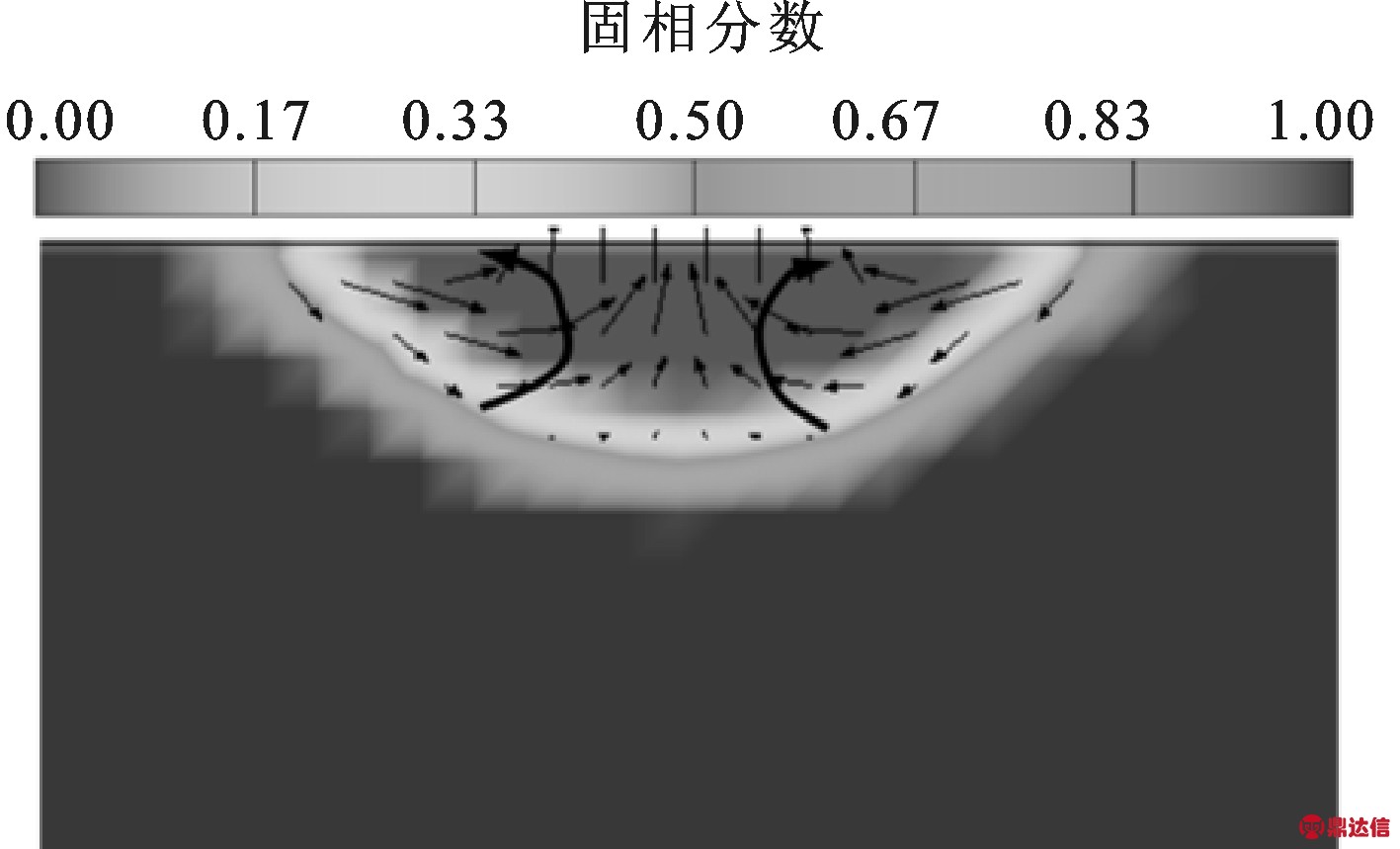
(e)拖曳力
图4 驱动力单独作用时横截面的固相分数与流场分布情况
熔池内驱动力单独作用时横截面的固相分数与流场分布如图4所示。从图4可以看出,熔池各驱动力单独作用时,熔池横截面内均形成两个对称环流。图4a的环流(即马兰格尼对流)方向是从熔池表面中心指向四周。这是由于表面张力随温度的升高而降低,流体从表面张力低的位置流向表面张力高的位置。如图4b所示,浮力环流的方向与表面张力引起环流的方向相同,且液面比固体基板表面微微升高,这是由于铝合金熔化后密度减小导致体积增加。如图4c所示,在电弧压力的作用下,熔池表面下陷,形成的环流方向与马兰格尼对流方向相反。洛伦兹力产生的流场方向与电弧压力产生的流场方向一致,且洛伦兹力是体积力,可作用在熔池底部,使熔池加深。由拖曳力产生的原因可知,其在熔池表面的流场方向为从电弧中心指向四周。
由计算得出图4a~图4e熔池内流体的最大速度分别为4.04×10-2、4.72×10-4、2.14×10-2、1.95×10-3、9.98×10-4 m/s,因此驱动力的影响程度由大到小顺序为表面张力、电弧压力、洛伦兹力、拖曳力、浮力。将所有驱动力进行耦合计算,流场与温度场的沿扫描方向的计算结果如图5所示。
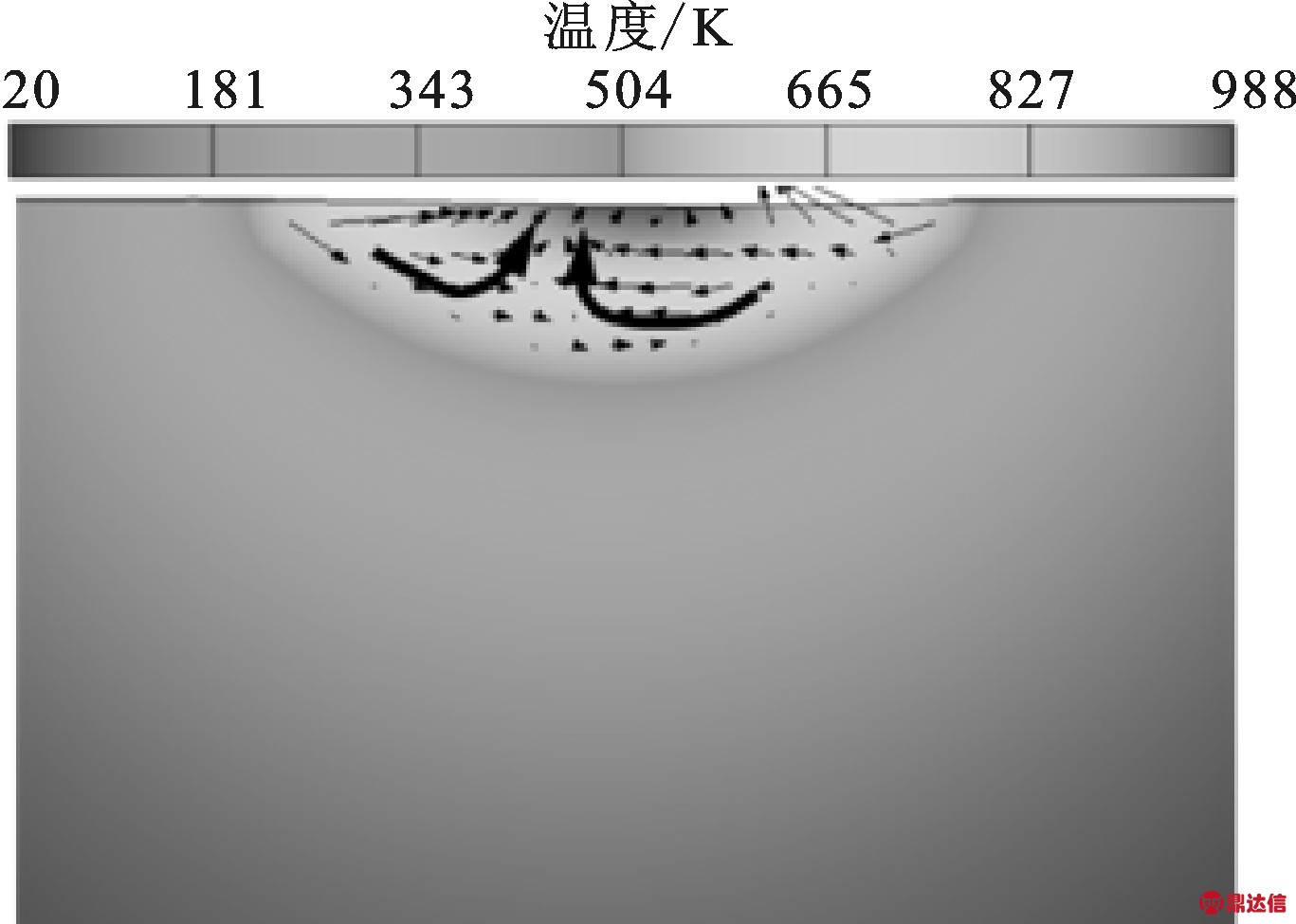
(a)0.2 s
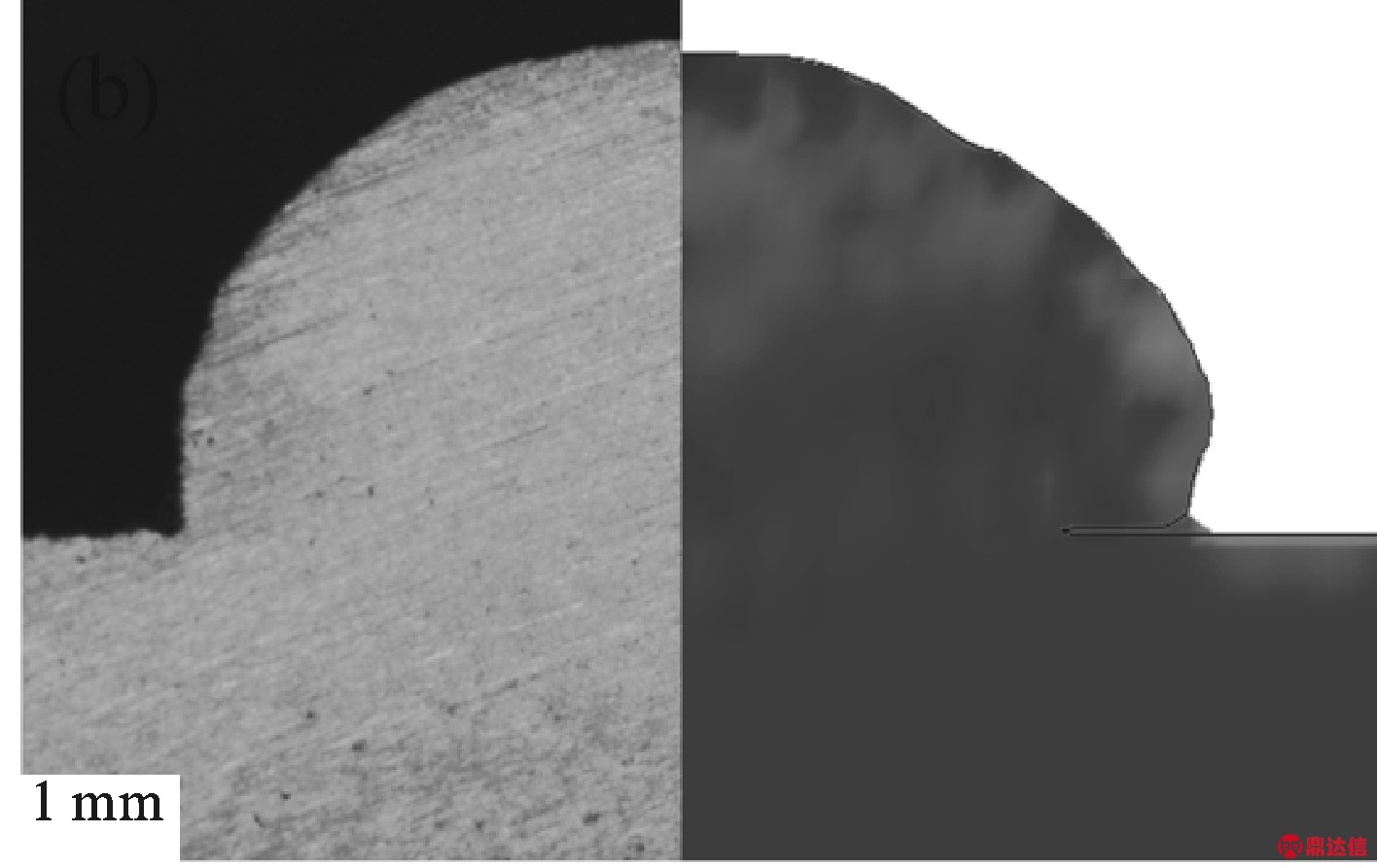
(b)1.8 s
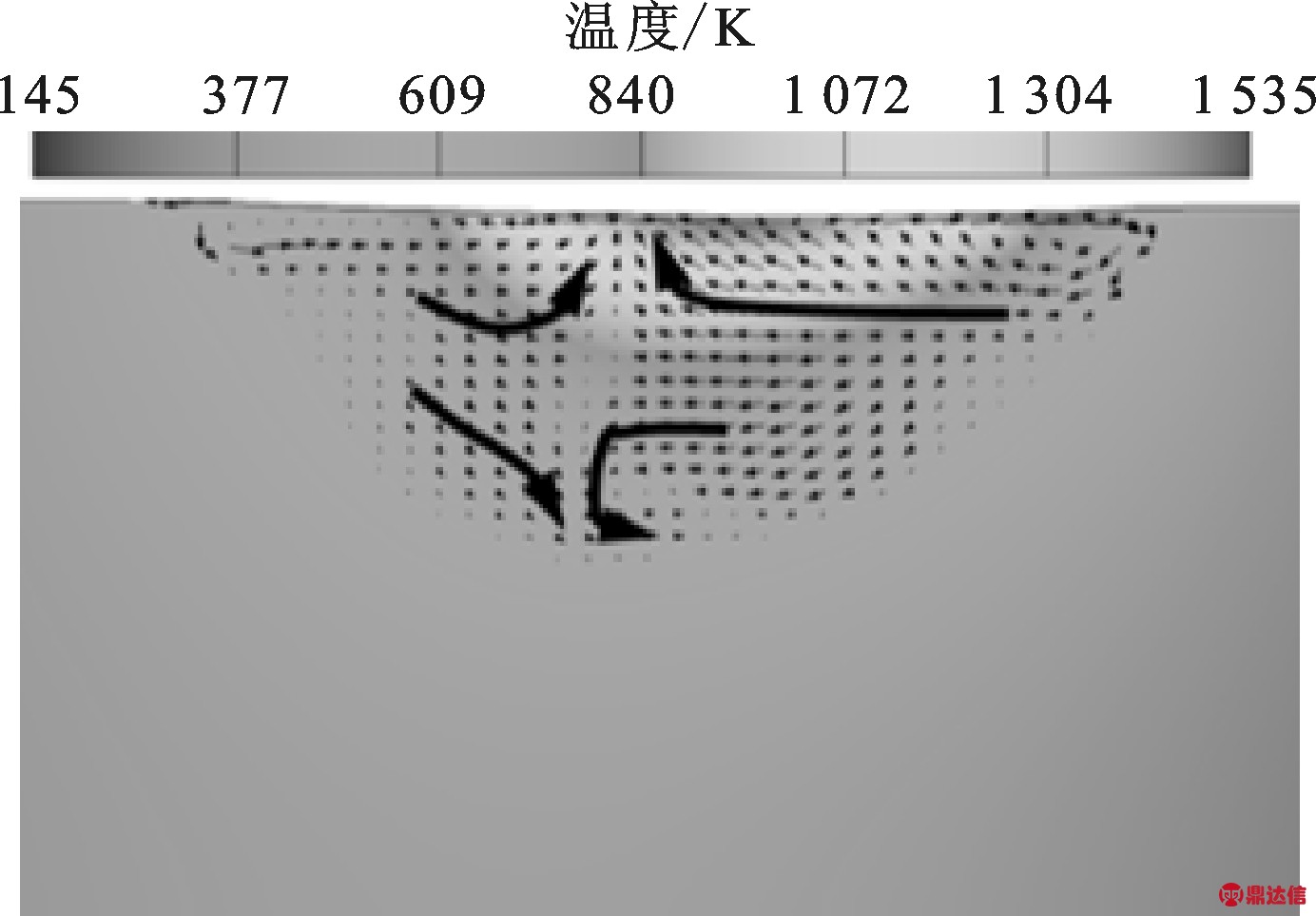
(c)5.6 s
图5 沿扫描方向流场与温度场随时间的演化
由计算得到的驱动力影响程度可知,在初始阶段,表面张力起主导作用,流场方向与马兰格尼对流方向一致,如图5a所示。随着熔池深度的增加,在熔池底部,表面张力的影响逐渐降低,洛伦兹力作为体积力,作用逐渐超过表面张力。从1.8 s开始,熔池内部开始形成4个环流,见图5b。图6为熔池横截面流场与固相分数计算结果,从图中可以看出,充分发展后熔池内形成4个环流,且在横截面方向上是对称的。
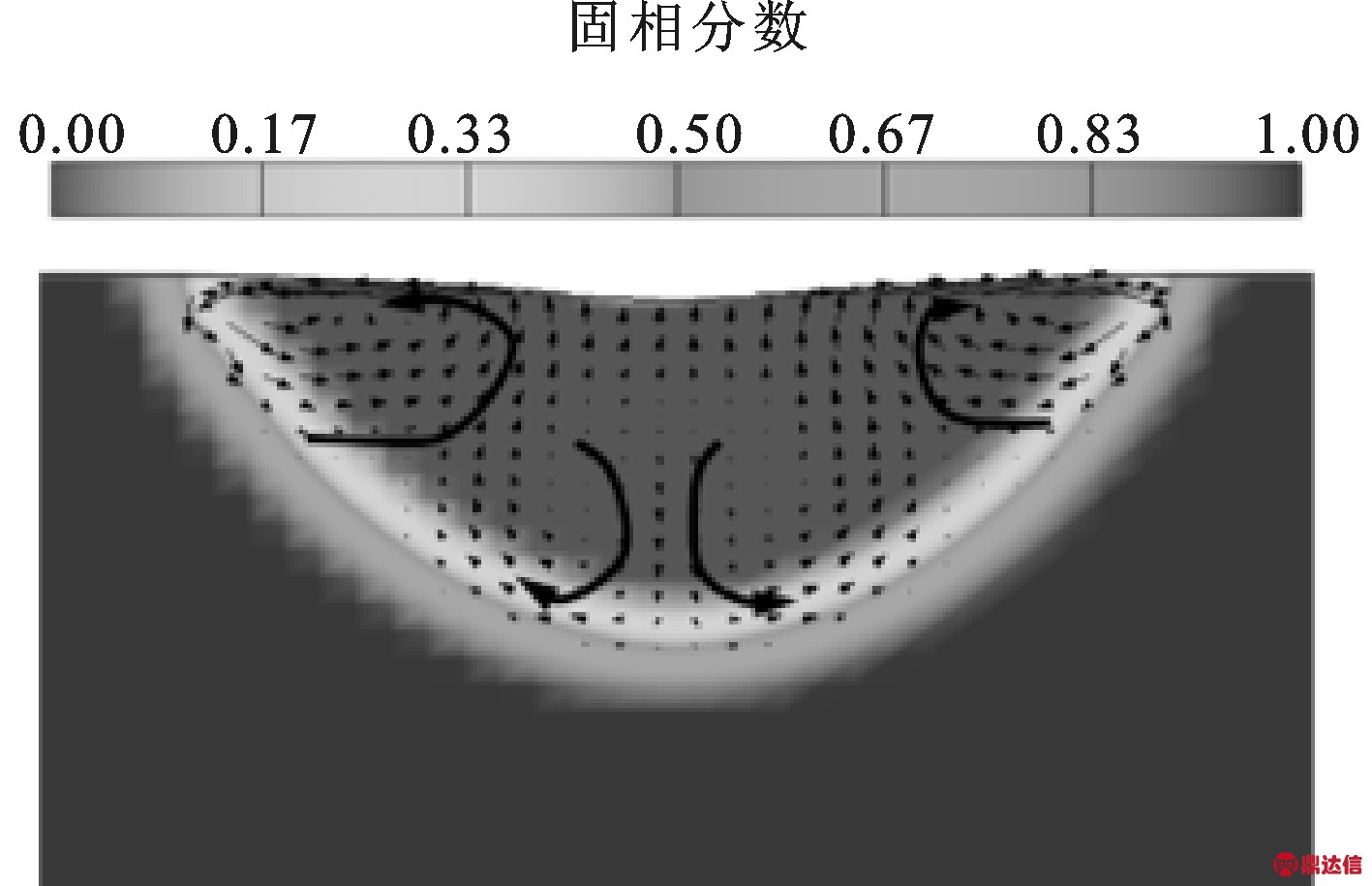
图6 熔池横截面流场与固相分数计算结果
本文在对电弧热源及熔池驱动力进行计算的基础上,将电弧预热与涂覆过程进行耦合计算,涂覆过程中温度场与流场的演化如图7所示。
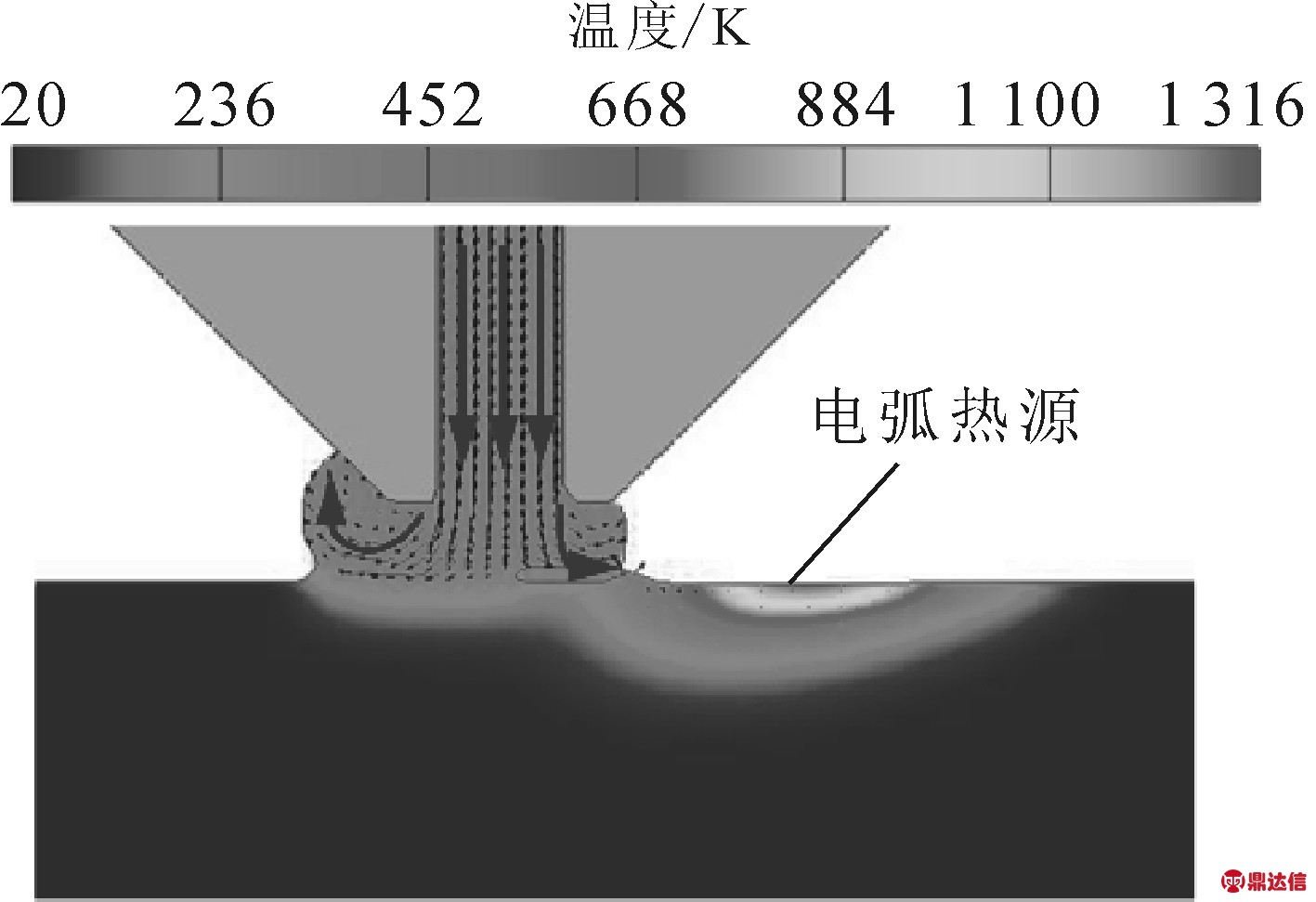
(a)0.14 s
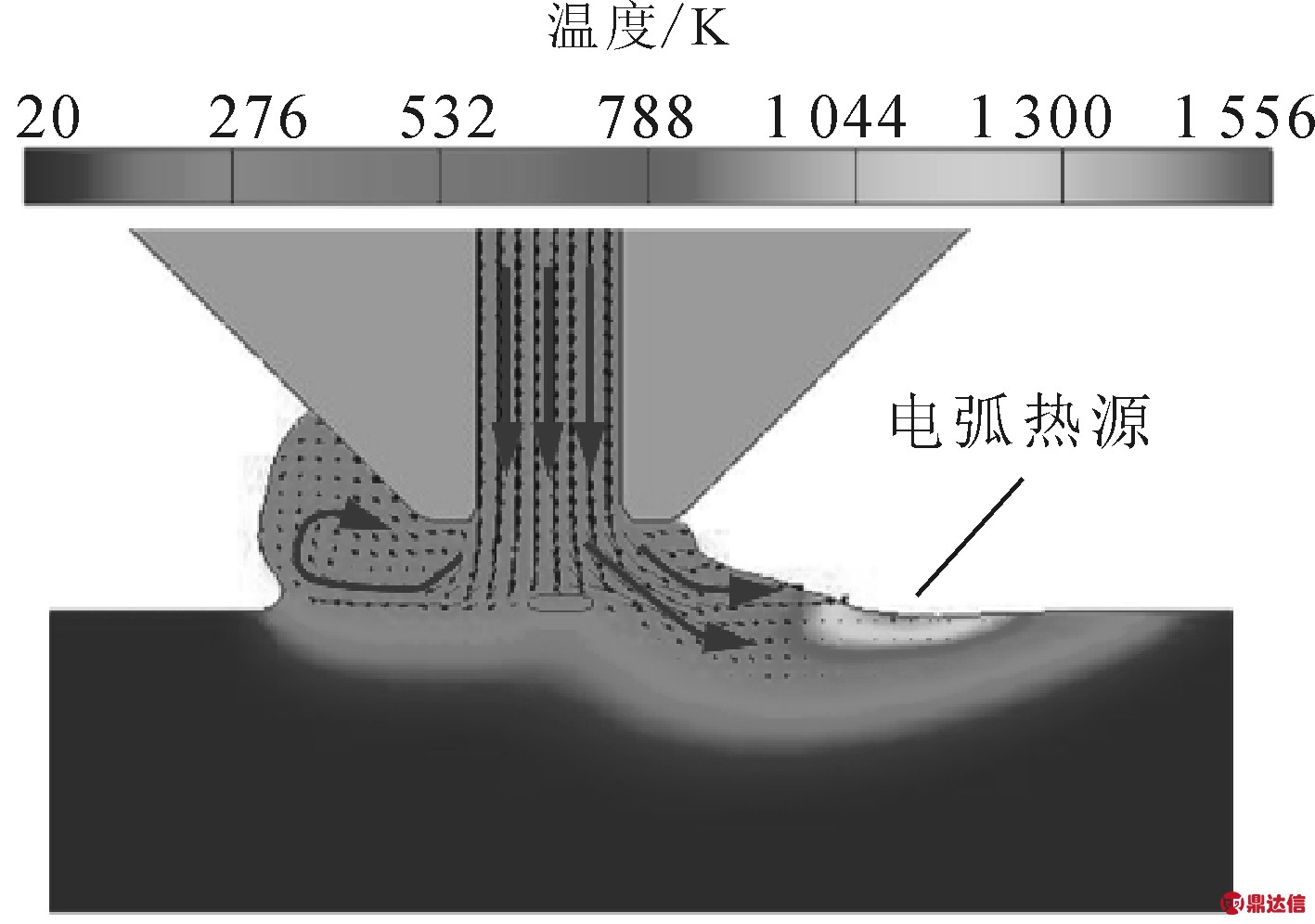
(b)0.20 s
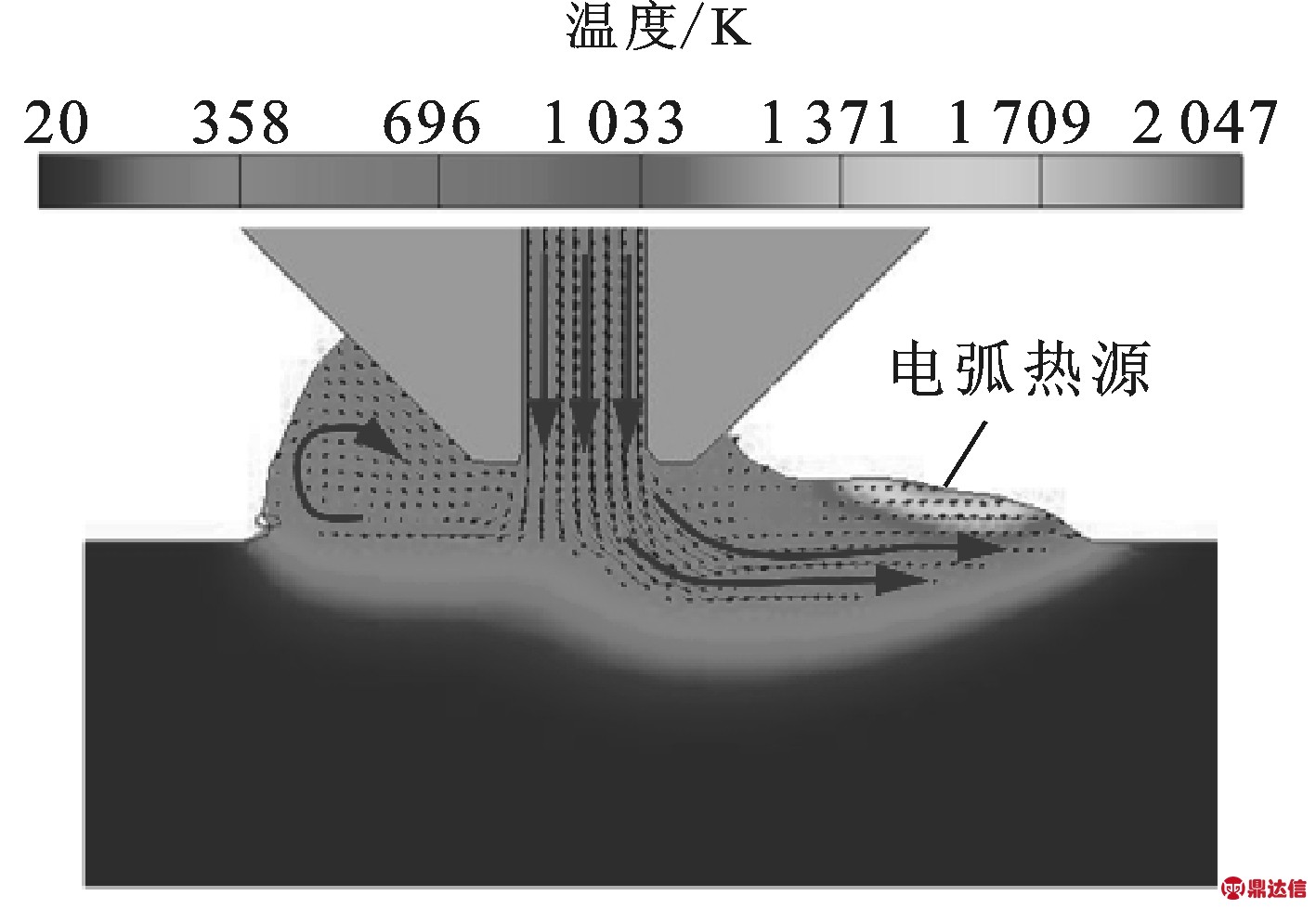
(c)0.26 s
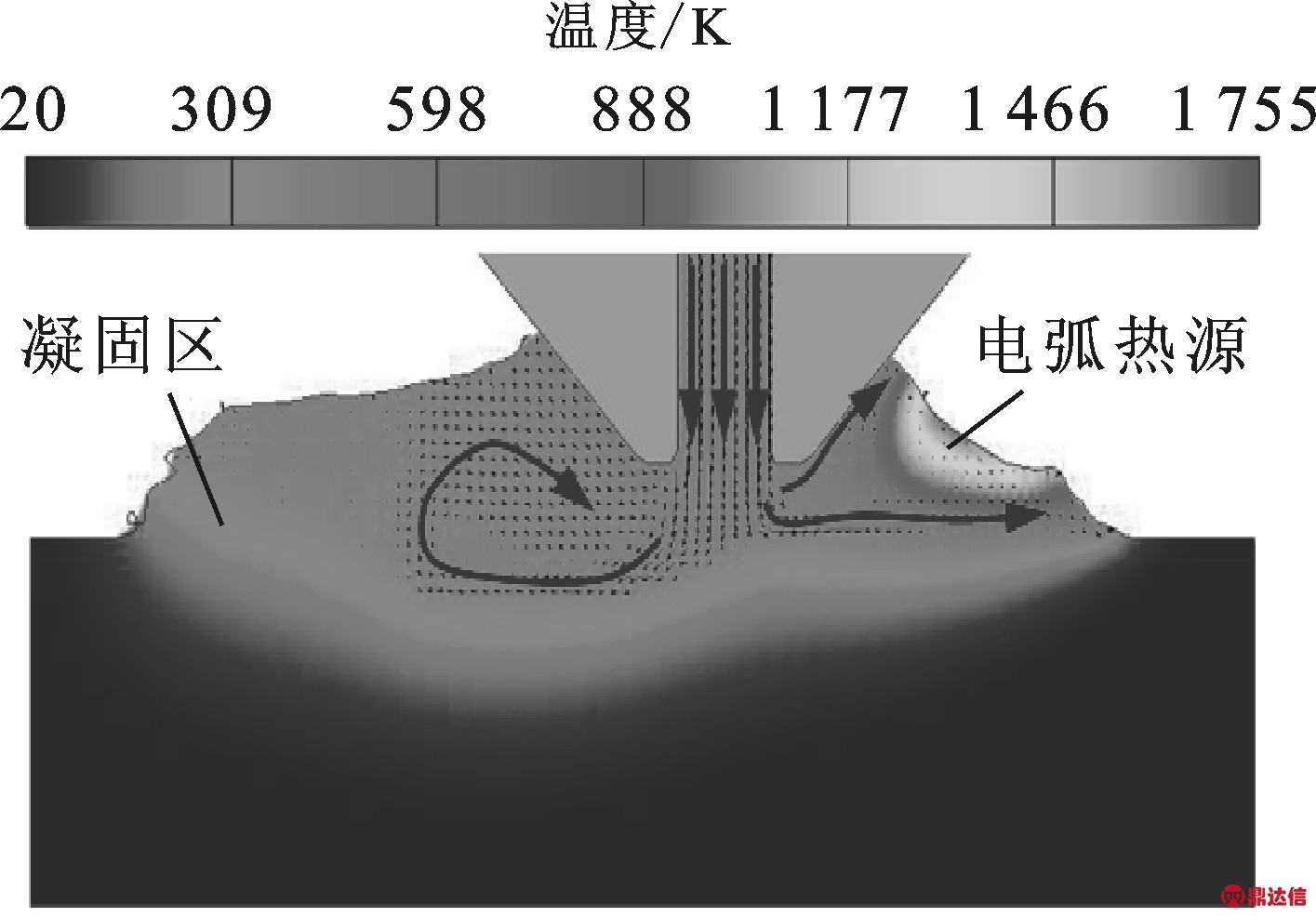
(d)0.60 s
图7 涂覆过程温度场与流场的演化
如图7a所示,在0.14 s之前,熔池与喷头内流体之间没有相互作用,流体向四周铺展且沿喷头爬升。随着基板的移动,流体与熔池开始接触并且快速流向熔池,见图7b。这是由于流体之间的亲和力远大于流体与基板以及流体与喷头之间的亲和力。随着基板的继续移动,电弧热源开始作用在熔池薄层上,涂覆层远离热源端开始凝固,温度最高的区域始终为电弧作用区域。
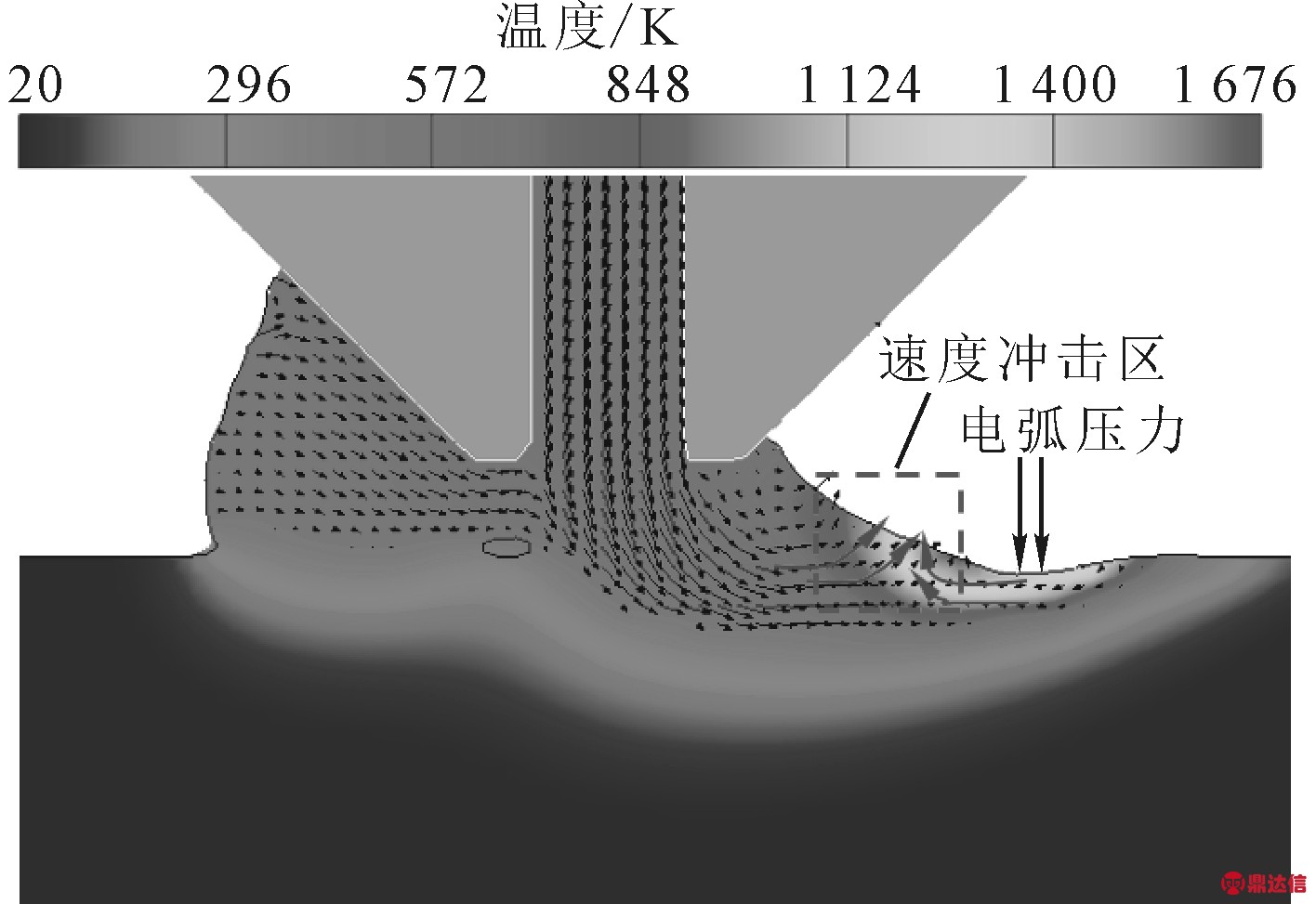
(a)涂覆层与熔池接触时的流场分布
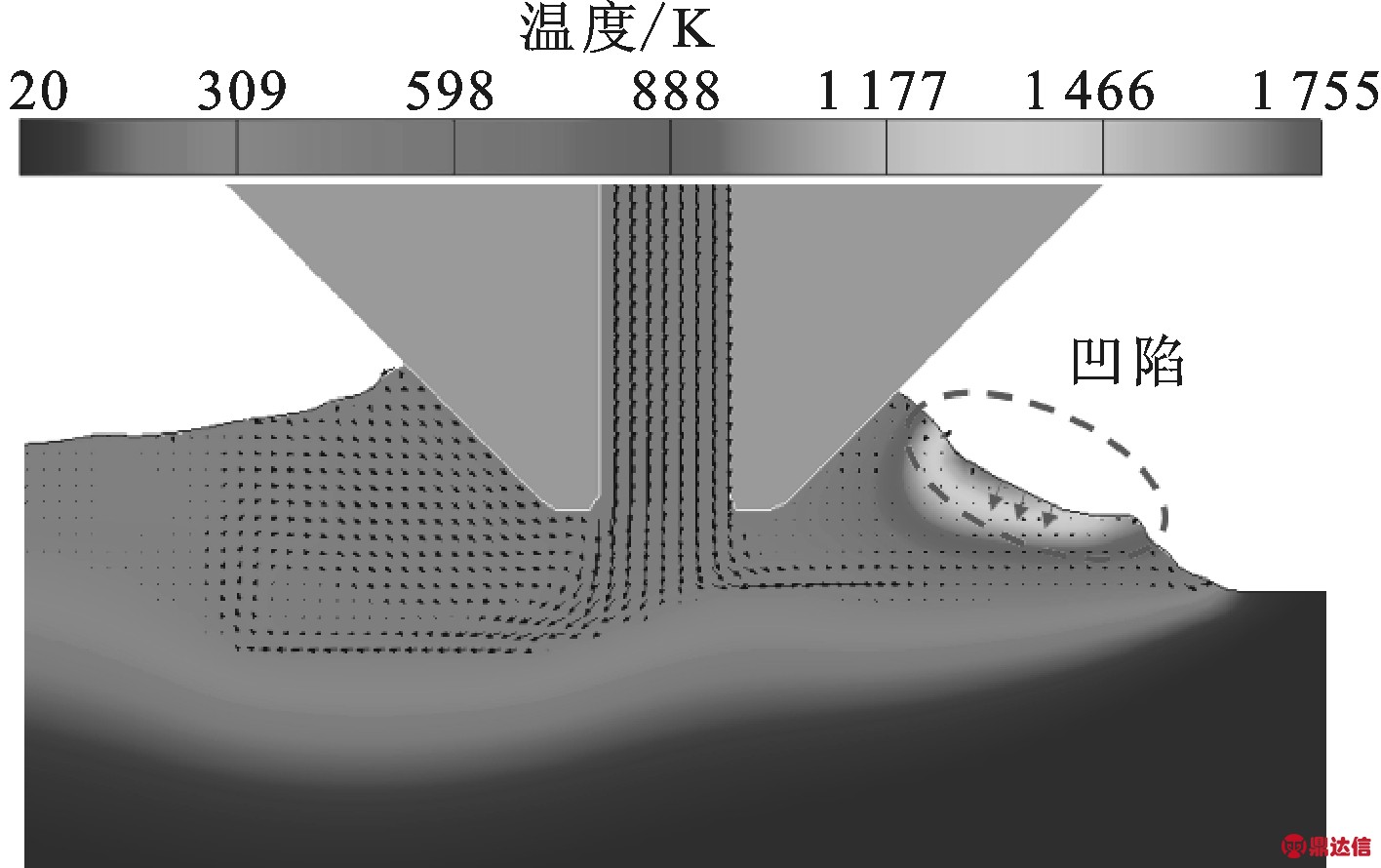
(b)电弧驱动力对流体攀升的阻碍作用
图8 电弧驱动力对涂覆过程的影响
对涂覆层与熔池接触时的流场分布进行分析,如图8a所示,由于熔池内速度矢量与涂覆层流体速度矢量方向不同,流体接触部位存在速度冲击区,熔池表面在电弧压力的作用下发生凹陷,电弧驱动力对涂覆层流体的流动起阻碍作用。图8b中,涂覆头右侧流体在电弧驱动力的作用下发生凹陷,电弧驱动力阻止流体沿喷头进一步攀升,有利于提高涂覆过程的稳定性以及涂覆层形貌的均匀性。
本文对电弧驱动力计算结果及涂覆计算结果分别进行了实验验证。将焊枪垂直安装于2024铝合金基板上方,使钨极距基板的高度为3 mm,三维运动平移平台以5 mm/s的速度直线运动,焊接电流为200 A。在实验过程中,控制坩埚内金属液不流出,取焊道稳定段并垂直于焊接方向将熔池剖开,观察空焊时熔池与热影响区的形貌和尺寸。图9a为凝固后熔池形貌的实验结果与仿真结果的对比。采用表1所示参数将电弧预热与熔融涂覆工艺结合进行单层单道件成形实验,将单层单道实验件沿横截面剖开,利用倒置金相显微镜对形貌进行观察测量,并与计算结果进行对比。单层单道件形貌的实验结果与仿真结果对比如图9b所示。
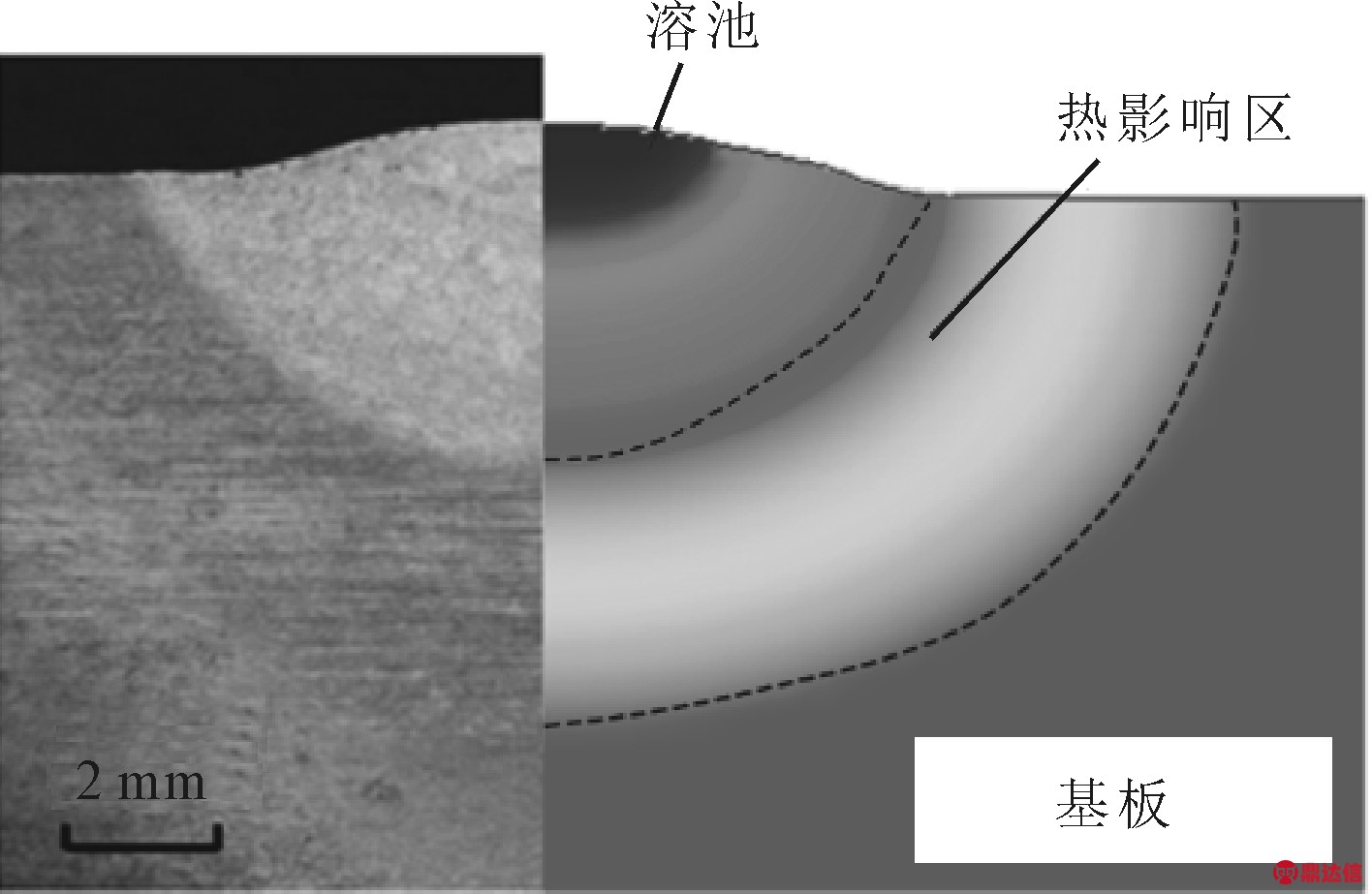
(a)熔池形貌
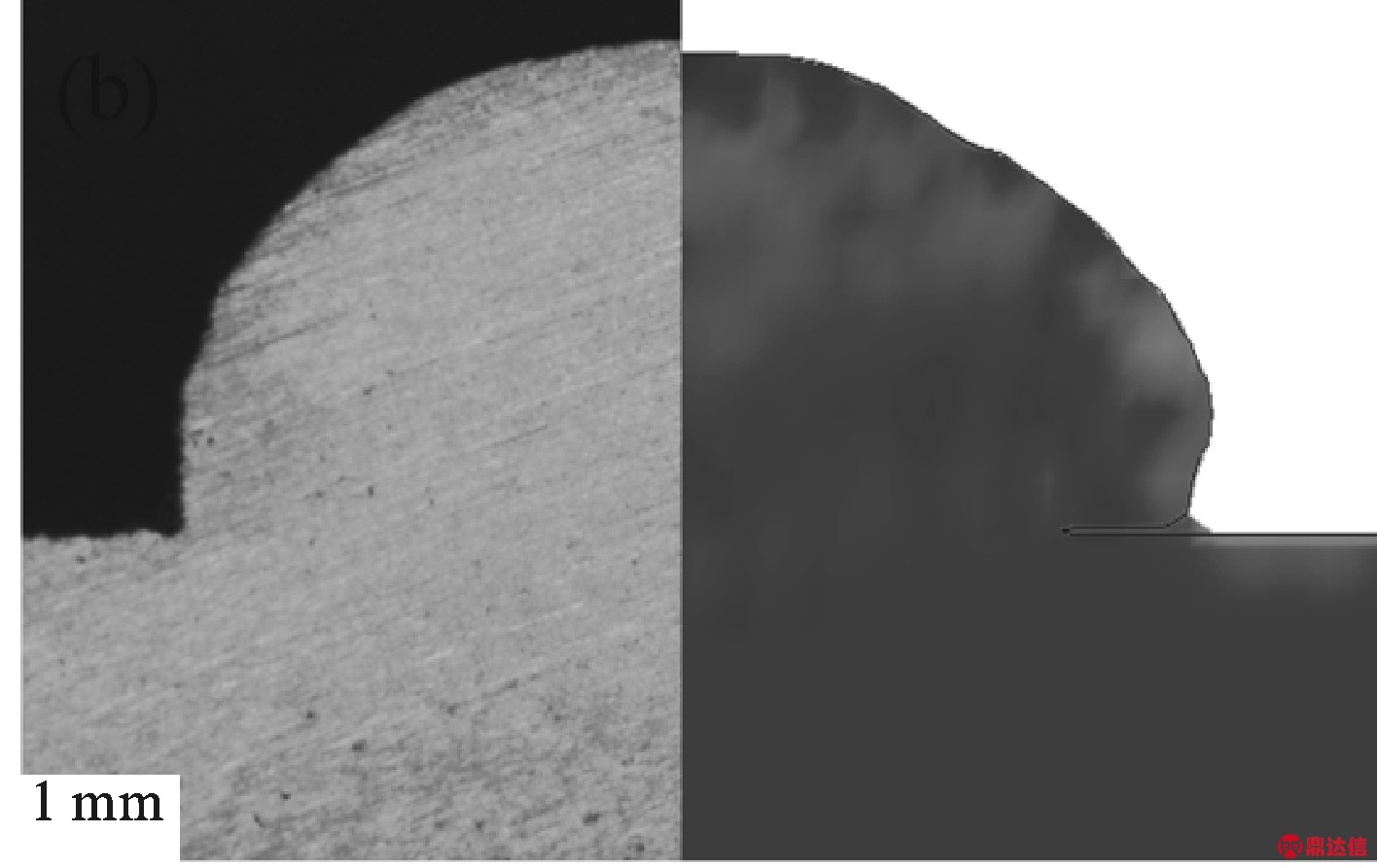
(b)单层单道件形貌
图9 熔池形貌和单层单道件形貌的实验与仿真结果对比
沿电弧扫描方向,在电弧压力的作用下熔池前端会发生凹陷,由于体积守恒,熔池凝固后横截面中心部位微凸,如图9a所示。计算所得熔池的最大宽度、深度分别为9.28 mm、3.25 mm,热影响区的最大宽度、深度分别为3.97 mm、3.51 mm,实验所得熔池的最大宽度、深度分别为9.38 mm、3.27 mm,热影响区的最大宽度、深度分别为3.63 mm、3.33 mm。熔池的最大宽度与高度的误差分别为1.1%、0.6%,热影响区最大宽度与高度的误差分别为9.3%和5.4%。
对图9b所示的单层单道件的最大宽度和高度进行了统计,数值计算结果分别为8.02 mm和3.66 mm,实验最大宽度和高度分别为7.75 mm和3.74 mm,误差分别为3.5%和2.1%。
在图9a所示的熔池横截面图中,取基板水平线为x轴,熔池对称轴为y轴建立直角坐标系,分别提取实验与计算结果的熔池凸起轮廓线形貌。当x轴坐标相同时,实验与计算轮廓线高度的差异如图10a所示。
以图9b基板水平线为x轴,单道件对称轴为y轴建立直角坐标系,分别提取实验与计算结果的单层单道横截面轮廓线形貌。当x轴坐标相同时,实验与计算轮廓线高度值的差异如图10b所示。
如图10a所示,相同x轴坐标实验值与计算值的连线长度即相同位置处轮廓线高度差值,从图10a可以得出,高度最大误差为0.09 mm。
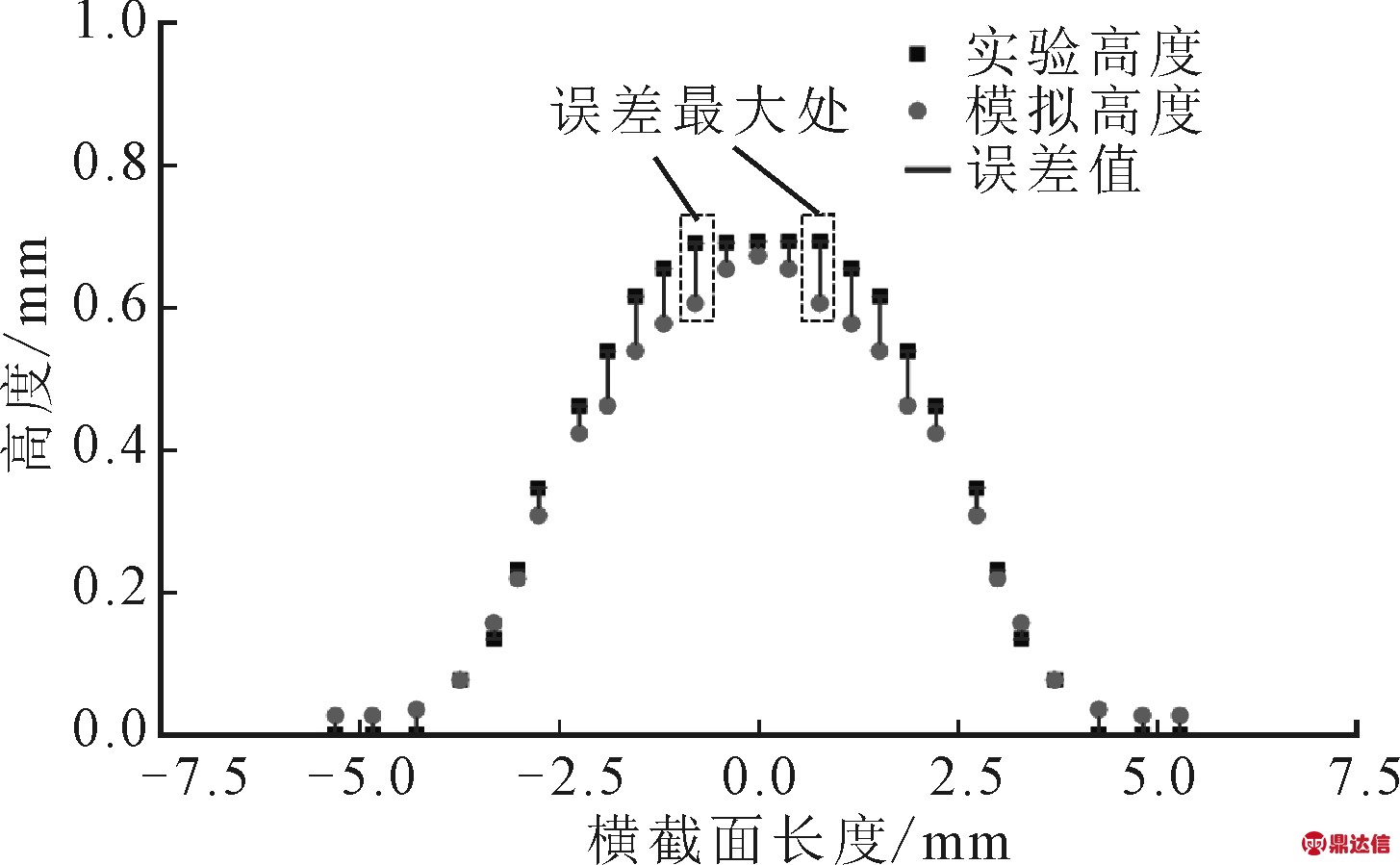
(a)熔池凸起轮廓线
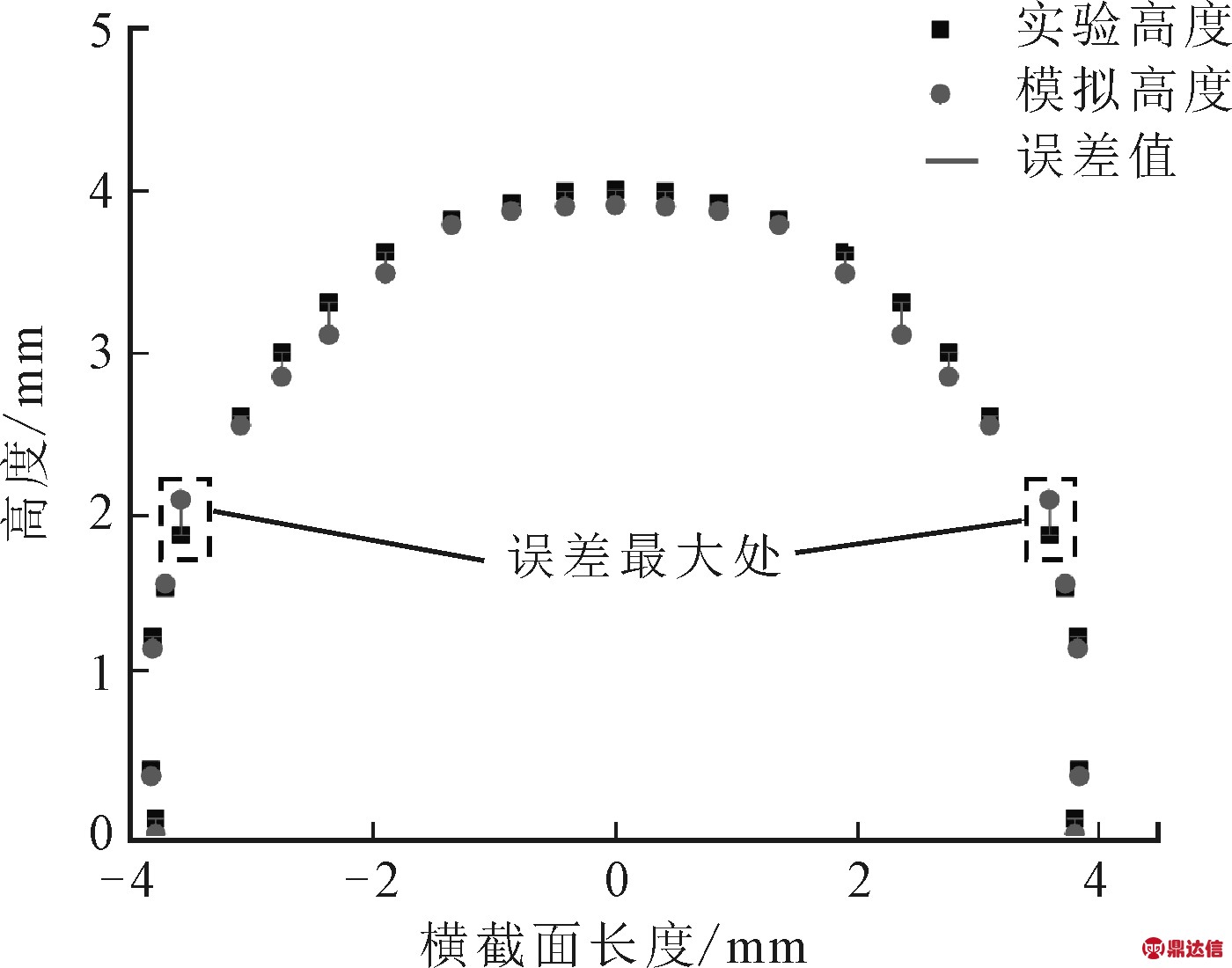
(b)单层单道横截面轮廓线
图10 熔池与单层单道横截面轮廓的数值计算与实验结果对比
如图10b所示,相同x轴坐标实验值与计算值的连线长度即相同位置处轮廓线高度差值,从图10b可以得出,高度最大误差为0.21 mm。
3 结 论
电弧预热铝合金熔融涂覆工艺的研究主要分为电弧预热过程与涂覆过程两个部分,本文对这两部分分别进行了研究。
(1)对熔池驱动力单独作用及耦合作用时熔池内的流场进行了分析发现,在本文所述初始条件下驱动力的影响程度的由大到小顺序为表面张力、电弧压力、洛伦兹力、拖曳力、浮力。研究为电弧熔池流场的分析提供基础。
(2)随着熔池深度的增加,在深度方向洛伦兹力的影响逐渐超过表面张力,并且在熔池底部开始逐渐形成4个环流。
(3)由于流体之间的亲和力远大于流体与基板以及流体与喷头之间的亲和力,随着基板的移动,喷头内流体开始与电弧熔池接触并迅速流入熔池。
(4)对熔池尺寸和单层单道的形貌进行实验测量,并与数值计算结果进行比较,结果表明误差均小于10%。