摘 要:建立液压机械无级变速器换挡非线性动力学模型,根据连续换挡过程仿真曲线,对决定变速器换挡品质的一类工况进行基于物理参数和换挡时序的换挡控制策略研究。研究表明通过优化变速器物理参数和换挡时序可大大提高换挡品质。基于物理参数的换挡控制策略为在发动机小转速,外负载小转矩,较小的主油压以及较大的调速阀流量时,可获得较好的换挡品质。基于换挡时序的换挡控制策略为首先切换换挡机构离合器,再切换行星齿轮机构待分离离合器,最后切换行星齿轮机构待接合离合器。
关键词:液压机械无级变速器;非线性动力学;换挡过程;换挡控制策略
1 引言
变速器是连接发动机和行走装置的传动机构,其性能直接影响车辆的动力性、经济性和平顺性。液压机械无级变速器是一种复合双流无级变速装置,能够发挥单流传动装置的优点,摈弃其缺点,具有良好的发展前景[1-2]。它通过机械变速机构实现高效传动,由液压调速机构实现无级变速,混合动力经行星齿轮汇流至换挡机构,实现高、低档位的切换。目前,液压机械无级变速器的研究主要集中在结构设计和性能特性上[3],对以换挡为代表的过渡工况和以人-机-环境一体化为代表的稳定工况的动态特性研究甚少,为此,以自主设计的一款液压机械无级变速器为研究对象,对其换挡动态特性进行分析,并进一步优化换挡策略,为液压机械无级变速器的动态性能分析提供了理论依据。
2 液压机械无级变速器设计
2.1 结构设计方案
为实现高效无级变速,设计了一款多离合器参与换挡的分段式单行星齿轮汇流液压机械无级变速器[4],如图1所示。该变速器通过离合器的切换实现传动轴的不同组合,使用行星机构离合器实现混合动力的汇流,通过换挡机构离合器与行星机构离合器的配合实现液压机械低档位向高档位的无级调速,液压机械从静止到传动的过渡由液压档换挡机构离合器完成。
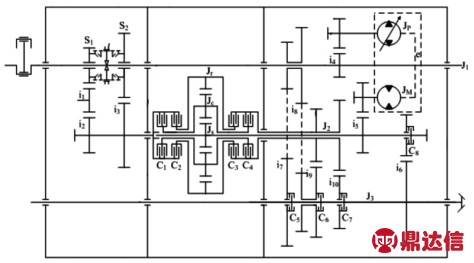
图1 液压机械无级变速器结构图
Fig.1 Transmission Schematic Diagram of HMCVT
图中:ii—齿轮 i传动比;Ci—离合器 i;J1/J2/J3—输入轴/中间轴/输出轴转动惯量;JP/JM—变量泵/定量马达转动惯量;Js/Jr/Jc—太阳轮轴/齿圈/行星架转动惯量;e—液压系统排量比。
离合器液压系统通过液压油油压实现湿式离合器内、外毂的接合与分离,如图2所示。内毂与传动轴的双平键连接,外毂与齿轮由螺栓连接。
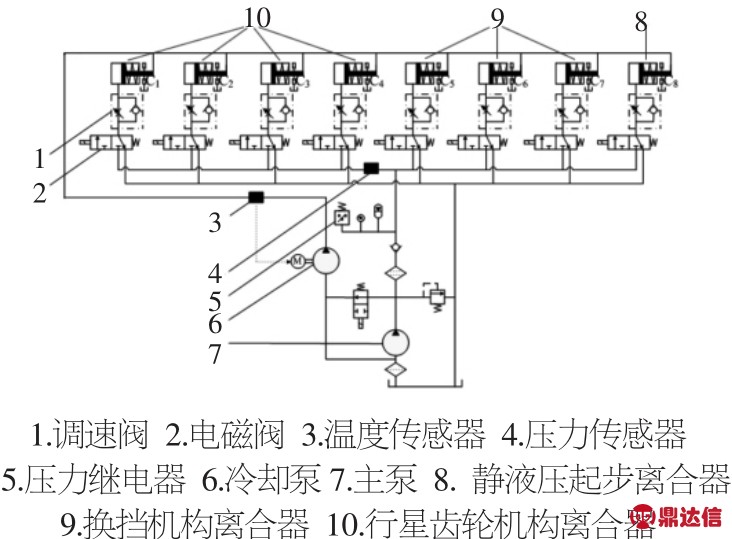
图2 离合器液压系统
Fig.2 Hydraulic Circuit Diagram of Clutch Control
2.2 换挡评价指标
选用输出轴速度降幅度、输出轴动载荷系数、输出轴最大冲击度和换挡时间作为换挡评价指标。湿式离合器工作油路兼做冷却油路,故不将滑磨功作为评价指标[5]。输出轴速度降幅度体现转速的波动程度,定义为:

式中:no—输出轴稳态输出转速;nomin—输出轴最低输出转速。
输出轴动载荷系数体现转矩的波动程度,定义为:
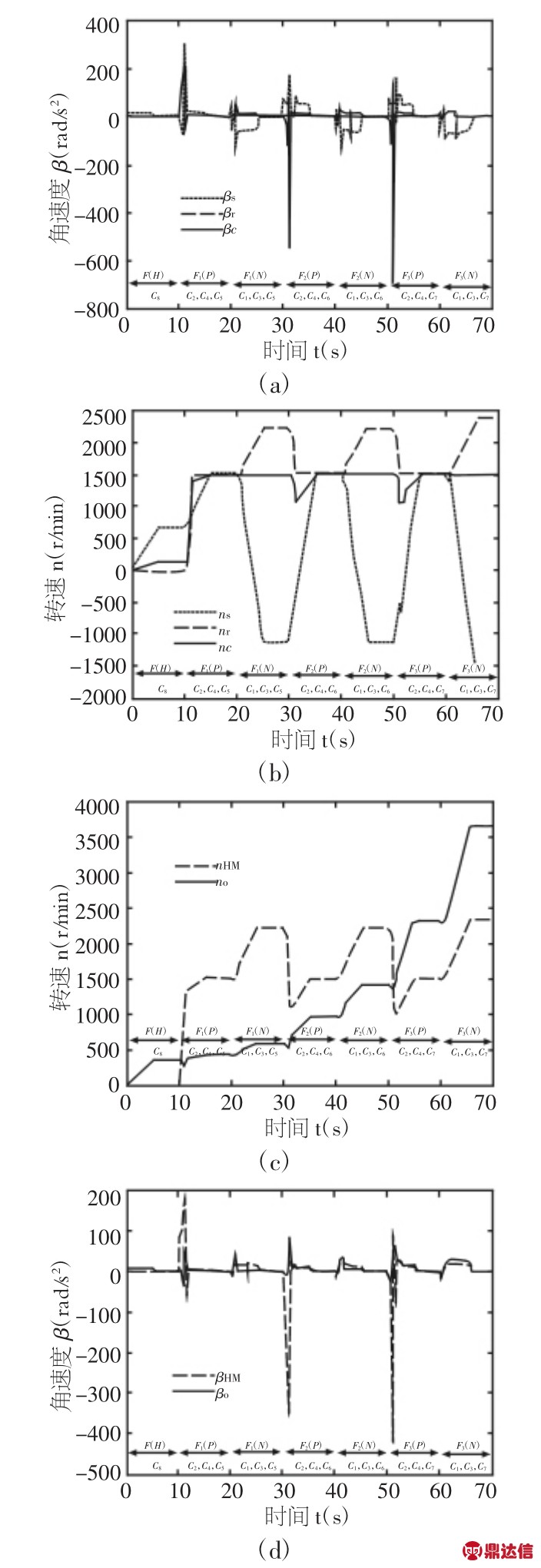
式中:To—输出轴稳态输出转矩;Tomin—输出轴最大输出转矩。
冲击度为车辆行驶过程中纵向速度的二阶微分。最大冲击
式中:v—车辆行驶速度。
在基于换挡时序的换挡评价指标中,由于离合器切换时序的变化对中间轴的冲击影响很大,也将中间轴最大冲击度也作为评价指标。换挡时间取输出轴转速达到稳速99%的时刻作为换挡结束时刻。
3 换挡非线性动力学模型
3.1 非线性动力学模型
为便于研究系统规律,将液压机械无级变速器模型简化为轴系、行星齿轮机构、泵控马达系统以及离合器系统[6]。根据不同离合器的接合状态,变速器运行方式可分为静液压驱动和液压机械传动两种。静液压驱动系统等效动力学模型,如图3所示。

图3 静液压驱动系统等效动力学模型
Fig.3 Equivalent Dynamic Model of Hydrostatic Transmission
图中:JCi/TCi/ωCi—离合器转动惯量/转矩/转速;T1/T3—输入轴/输出轴转矩;ω1/ω3—输入轴/输出轴转速;TP/TM—变量泵/定量马达转矩;ωP/ωM—变量泵/定量马达转速;Ts/ωs—太阳轮轴转矩/转速。
轴的传动方式分为各轴独立转动和多轴联体转动两种。液压档各轴独立转动动力学方程为:
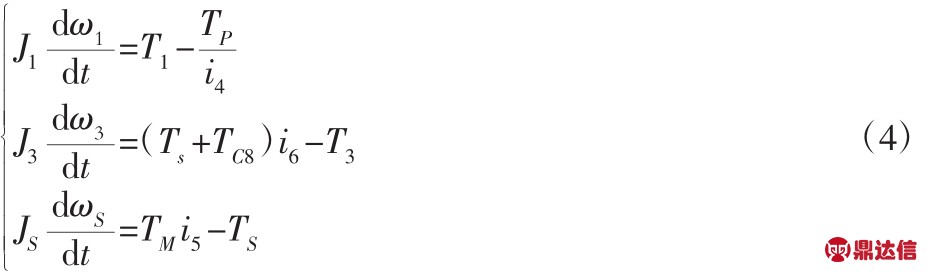
液压档多轴联体转动动力学方程为:
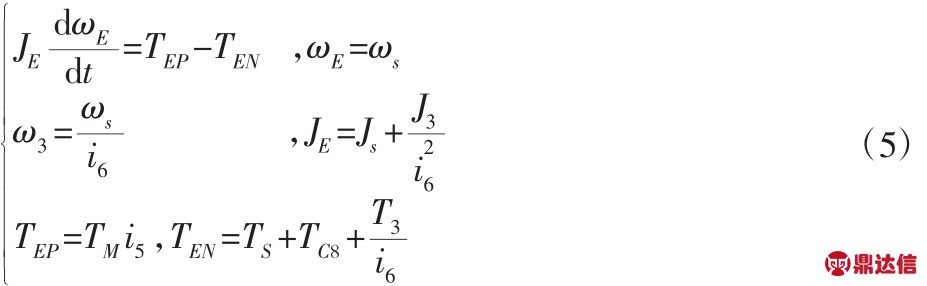
式中:JE—等效转动惯量;TEP—等效正向;TEN—负向转矩;ωE—等效转速。
液压机械传动系统等效动力学模型,如图4所示。

图4 液压机械传动系统等效动力学模型
Fig.4 Equivalent Dynamic Model of HMT
图中:T2/ω2—中间轴转矩/角速度;Tr/Tc—齿圈/行星架转矩;ωr/ωc—齿圈/行星架转速。
液压机械各轴独立转动动力学方程为:
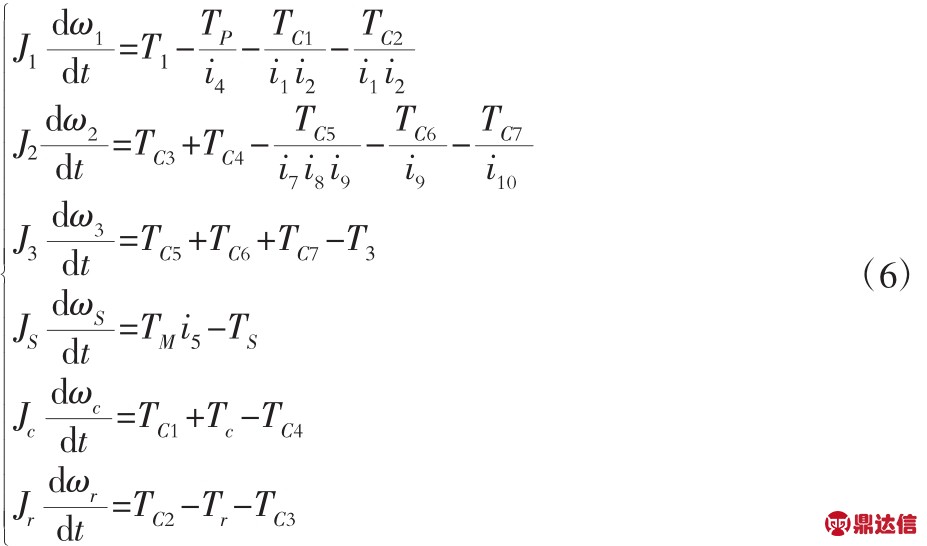
针对研究的液压机械无级变速器,将离合器分为四组:第1组离合器为C1和C3;第2组离合器为C2和C4;第3组离合器为C5、C6和C7;第4组离合器为C8。每组离合器状态分为分离、切换和接合,液压机械传动离合器接合状态为3×3×4=36种,静液压驱动离合器接合状态为1种,故多轴联体转动状态共有37种。
行星齿轮机构运动学方程和动力学方程为:

式中:k—行星齿轮特性参数。
泵控马达系统包括变量泵-定量马达系统、变量泵控制系统、阀集成以及补油和冲洗系统等。泵控马达系统简化动力学模型,如图5所示。
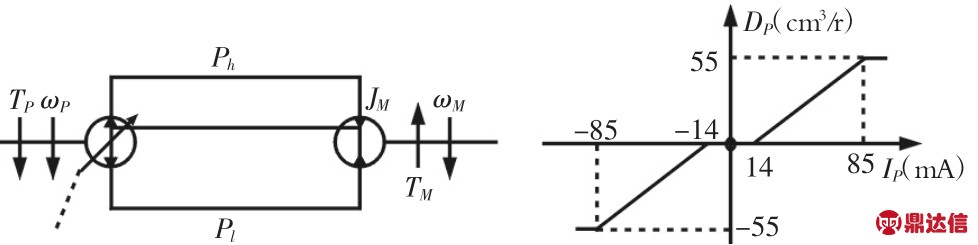
图5 泵控马达系统简化动力学模型
Fig.5 Equivalent Dynamic Model of Pump-Control Motor System
图中:ph/Pl—液压系统高/低端压力;TP/TM—变量泵/定量马达转矩;ωP/ωM—泵/马达转速;IP—泵的控制电流;DP/DMmax—泵转速/马达最大转速。
泵控马达系统动力学方程为:
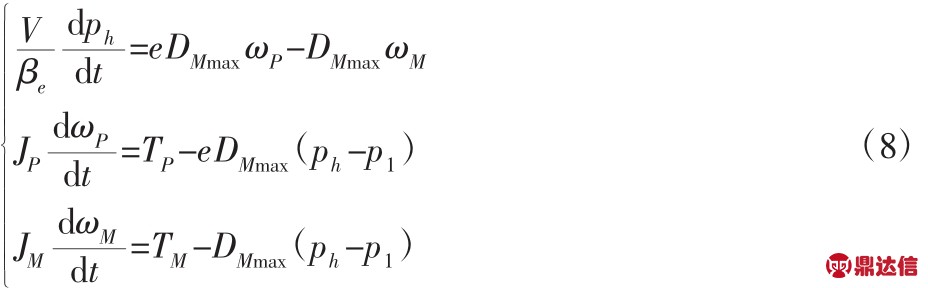
式中:V—液压系统容积;βe—油液体积弹性模量。
两个离合器参与换挡的切换过程涉及4个阶段分别为切换前、转矩相、惯性相和切换后。切换过程等效动力学模型,如图6所示。
图中:ωz/ωc—主/从动盘转速,其它符号同上述。该模型用′区别液压机械无级变速器离合器的实际模型。
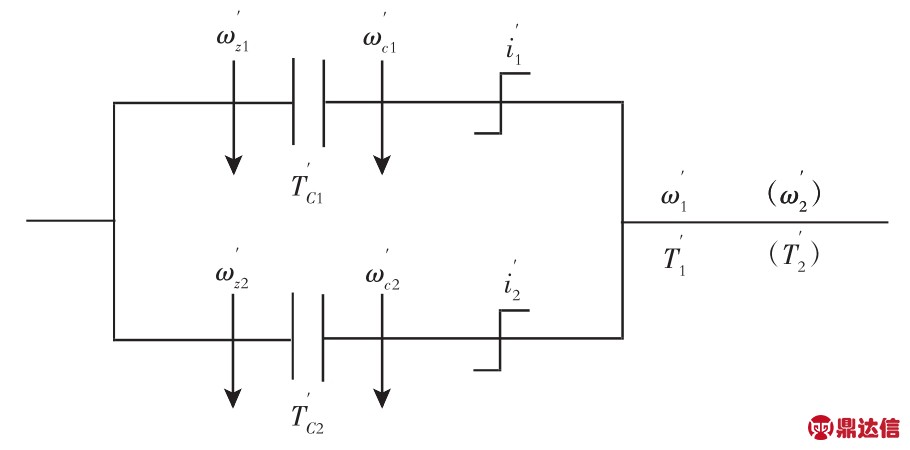
图6 两个离合器参与切换的等效动力学模型
Fig.6 Equivalent Dynamic Model of Two Clutch to Engage Gears
在切换前阶段接合
分离,各传动部件的转速和转矩保持不变,离合器
传递的转矩为静摩擦转矩。该阶段传递规律为:
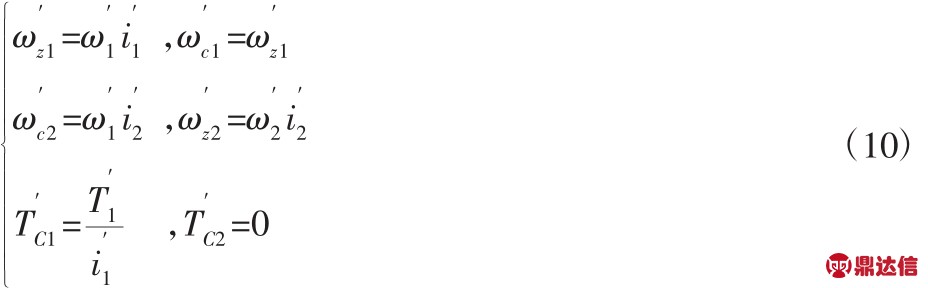
在转矩相阶段接合,开始泄油,
打滑,开始充油,传递动摩擦转矩,各传动部件只有转矩的变动,无急剧的转速变化。该阶段传递规律为:
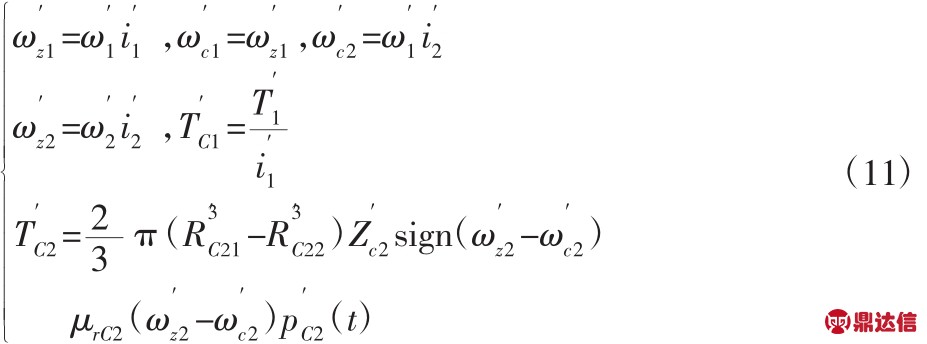
式中:RCi1/RCi2—离合器Ci摩擦片的内径/外径;ωCi1/ωCi2—离合器 Ci主动盘/从动盘角速度;ZCi—离合器Ci摩擦片数;μrCi—离合器Ci动摩擦系数;pCi—作用在离合器Ci上的充油压力。
在惯性相阶段,开始打滑
未完全接合,仍处于打滑状态,传递的动摩擦转矩随油压及摩擦系数的改变而不断变化,造成输出轴转矩和转速的剧变,是产生换挡冲击的最大阶段。该阶段传递规律为:
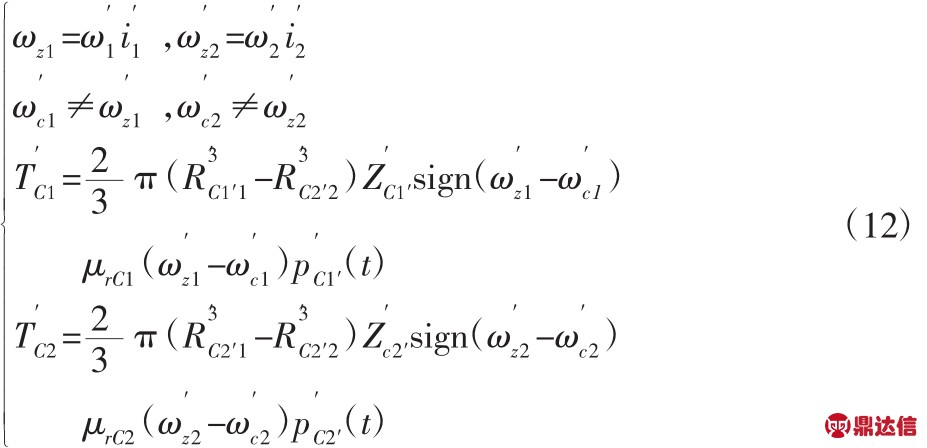
在切换后阶段,分离,不再传递转矩
接合,开始传递静摩擦转矩。该阶段传递规律为:
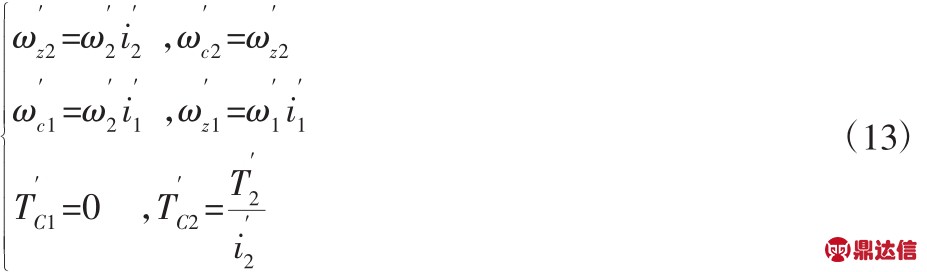
离合器压力控制的数学模型为:

式中:τ′—延迟时间—离合器
接合/分离压力变化率;CCi′—TCU 控制指令;CCi′=0—第 i个离合器泄压分离;CCi′=1—第i个离合器加压接合;
—作用在离合器
上的充油压力。
3.2 换挡过程特性分析
根据非线性动力学模型,应用Simulation X建立变速器仿真模型。仿真通过控制液压系统排量比,每隔10s换挡一次,且各离合器无切换时间差。行星齿轮(太阳轮、齿圈和行星架)和轴系(中间轴和输出轴)转速及角加速度的仿真曲线,如图7所示。由图7知,对换挡品质影响较大的区域在F(H)→F1(P)、F1(N)→F2(P)、F2(P)→F3(P)三个阶段。F(H)→F1(P)阶段为静液压驱动向液压机械传动的过渡阶段,一方面换挡冲击可被马达以牺牲转速的代价“吸收”,另一方面静液压驱动可保持变速器稳步启动。换挡策略研究集中在后两个阶段,而这两个阶段类型相同,即液压机械负向传动向液压机械正向传动过渡,故仅以F2(N)→F3(P)阶段进行研究。
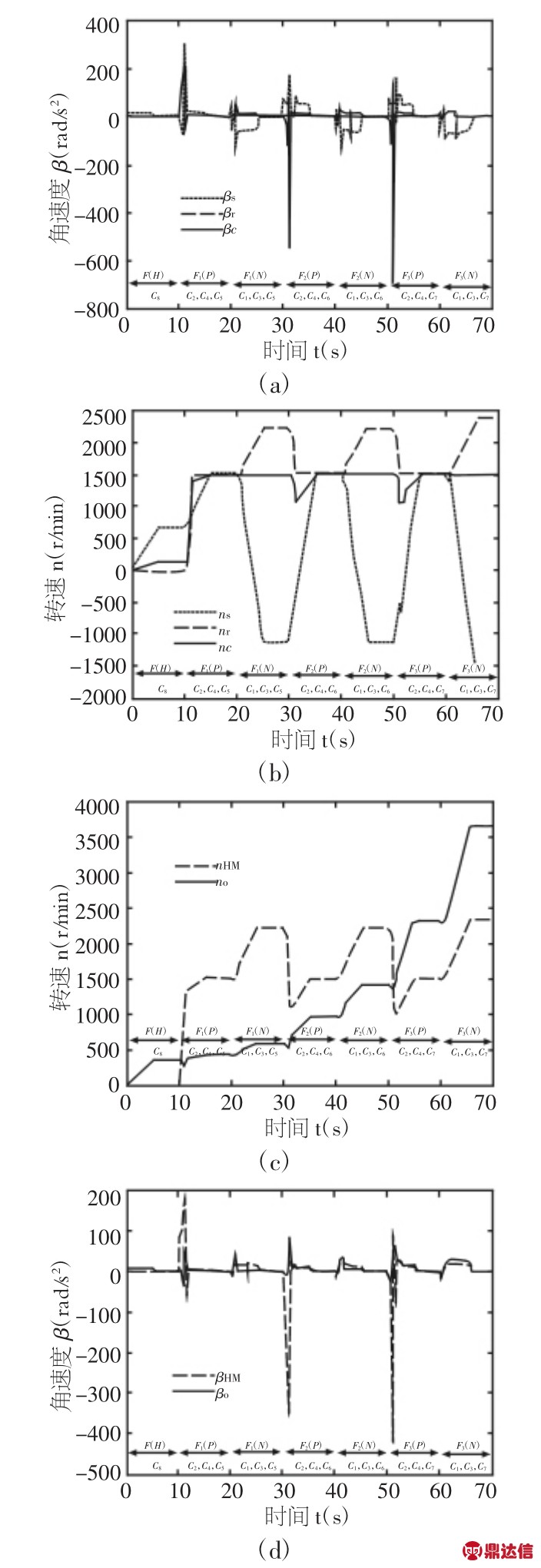
图7 连续换挡过程仿真曲线
Fig.7 Simulation Curve of Shifting Process
4 换挡策略研究
4.1 基于物理参数换挡策略研究
基于物理参数的换挡策略研究是多指标多因素的优化问题,故选用L9(34)正交表进行分析。由于仿真结果具有唯一性,使用极差法进行研究。鉴于多次试验导致试验数据的误差,通过比较各因素的离差平方和和误差平方和,使用F检验法得出方差分析结论[7-8]。评价指标Ⅰ、Ⅱ、Ⅲ和Ⅳ分别为输出轴速度降幅度、输出轴动载荷系数、输出轴最大冲击度和换挡时间。因素A为发动机转速,取900r/min、1200r/min和1500r/min;因素B为负载转矩,取75Nm、100Nm和125Nm;因素C为主油路油压,取3MPa、4MPa和5MPa;因素D为调速阀流量,取3L/min、4L/min和5L/min。每个评价指标试验9次,根据极差分析法,各评价指标的优化方案,如表1所示。
表1 基于物理参数的换挡品质优化方案
Tab.1 Optimization Scheme of Shifting Quality based on Physical Parameters
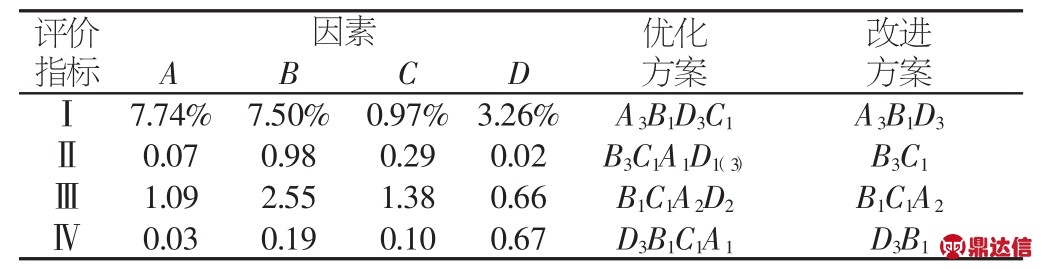
为体现综合性能,不考虑占比较少的因素,得到改进方案:方案A3B1D3的指标Ⅰ的范围为[9.91%,10.88%],方案B3C1的指标Ⅱ的范围为[1.88,1.97],方案 B1C1A2的指标Ⅲ的范围为[7.95,8.64],方案D3B1的指标Ⅳ的范围为[1.24,1.37]。
综上,基于物理参数的换挡策略为采取较小的发动机转速、负载转矩及主油路油压,以及较大的调速阀流量。
4.2 基于换挡时序换挡策略研究
变速器从液压机械中档位向高档位切换时涉及三组离合器,其中第1组离合器为C1和C3,第2组离合器为C2和C4,第3组离合器为C6和C7。离合器分离会造成动力中断,接合会影响其寿命,同时离合器切换时间过短会造成冲击过大,而过长会造成速度降幅加大。为符合实际情况,先对变速器进行组间分析,然后分析组内切换。评价指标Ⅰ、Ⅱ、Ⅲ和Ⅳ分别为输出轴速度降幅度、输出轴动载荷系数、中间轴最大冲击度和输出轴最大冲击度。因素A、B、C分别为第1、2、3组离合器,分别取离合器提前0.5s,按时和推后0.5s切换;因素D为空白列。每个评价指标试验9次,根据极差分析法,各评价指标的优化方案,如表2所示。
表2 基于换挡时序的组间换挡品质优化方案
Tab.2 Optimization Scheme of Shifting Quality based on Shifting Time Sequence
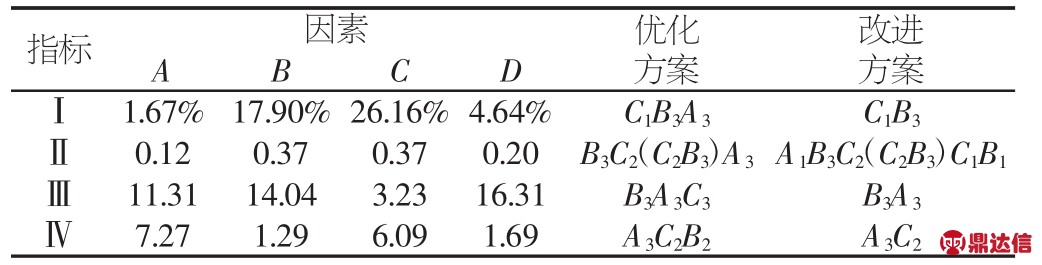
同理,不考虑占比较少的因素,从而得到改进方案:方案C1B3的指标Ⅰ的范围为[-1.03%,5.01%],方案B3C2(C2B3)的指标Ⅱ的范围为[2.02,2.34],方案 B3A3的指标Ⅲ的范围为[9.19,25.50],方案A3C2的指标Ⅳ范围为[4.56,6.25]。
根据上述分析,第3组离合器换挡应早于第1、2组离合器,因此将第3组离合器与前两组离合器分开讨论。由于第3组离合器仅涉及一组2个离合器的切换,采用单因素加载试验进行仿真分析。第1、2组离合器在10s时同时切换,而第3组离合器分三种情况:C6在 9s时分离,C7在 9.5s时接合;C6、C7同时在 9.5s时切换;C6在9.5s时分离,C7在9s时接合,仿真结果,如图8所示。由图8可知,输出轴速度在10.94s、11.05s和10.85s达到最低转速1066r/min、1021r/min 和 1059r/min,降幅度分别为 7.15%、6.39%和7.74%,这表明第3组离合器切换时序对速度降幅影响不大,在同时切换时,速度降幅度略低,稳定性略好。输出轴转矩在11.21s、11.35s和11.07s达到最大转矩187Nm、189Nm和203Nm,动载荷系数分别为1.88、1.89和2.03,这表明C6分离时间不晚于C7接合时间,动载荷差异不大。中间轴冲击度在11.13s、11.13s和10.99s达到峰值27.40、19.76和20.32,这表明C6分离时间不早于C7接合时间时,中间轴最大冲击度较为理想。输出轴冲击度在11.23s、11.36s和11.09s达到峰值8.24、8.48和13.03,这表明C6分离时间不晚于C7接合时间时,输出轴最大冲击度较为理想。由上述可知,C6、C7同时切换时有较好换挡品质。
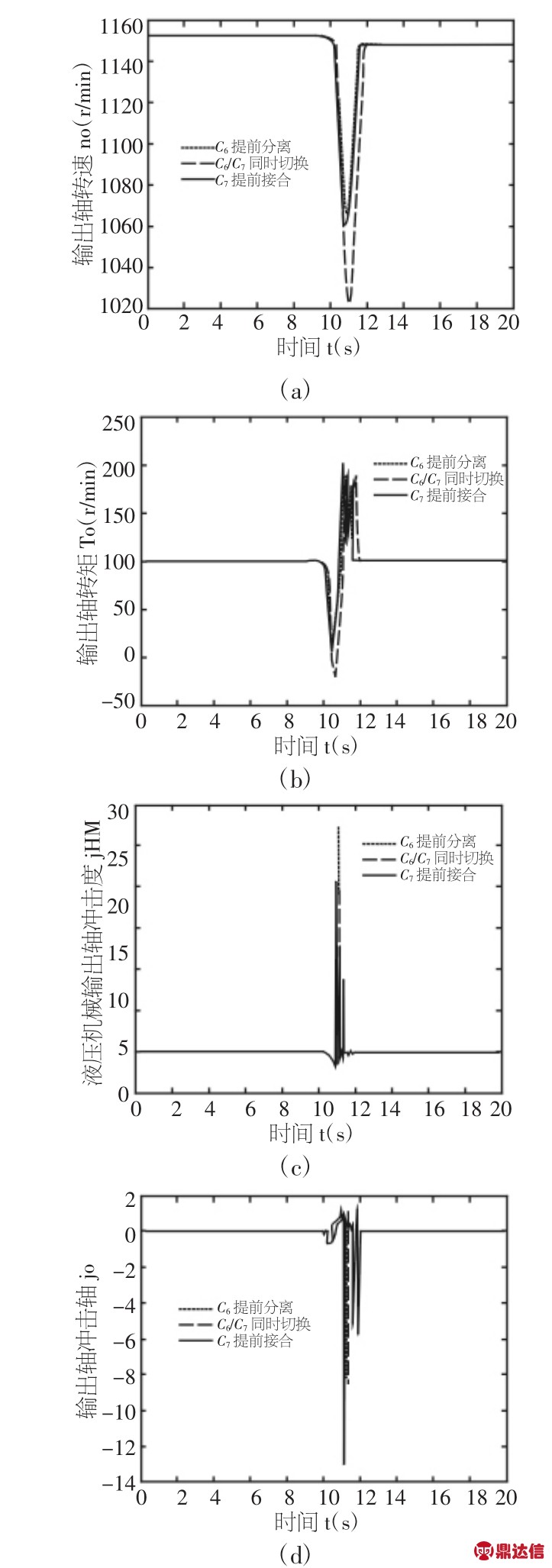
图8 第3组离合器切换时间对换挡品质的影响
Fig.8 Influence on Shifting Quality of Switching Time in 3rd Clutchs
第1、2组离合器的切换涉及到两组4个离合器的接合与分离,采用正交试验极差法进行分析。第3组离合器在10s时同时切换,而第1、2组离合器选取11s为标准切换点,设定10.5s和11.5s为提前和推后切换点作为正交设计三水平,离合器C1~C4为四因素,建立L9(34)正交表,优化方案,如表3所示。由表3可知,各评价指标的优化方案为:方案A3B3C3的指标Ⅰ的范围为[3.58%,4.14%],方案A1C1B1的指标Ⅱ的范围为[1.91,2.17],方案D3C1B1的指标Ⅲ范围为[11.70,13.64],方案A1C1B2的指标Ⅳ范围为[-3.99,2.56]。
表3 基于换挡时序的组内换挡品质优化方案
Tab.3 Optimization Scheme of Shifting Quality in the Cluster based on Shifting Time Sequence
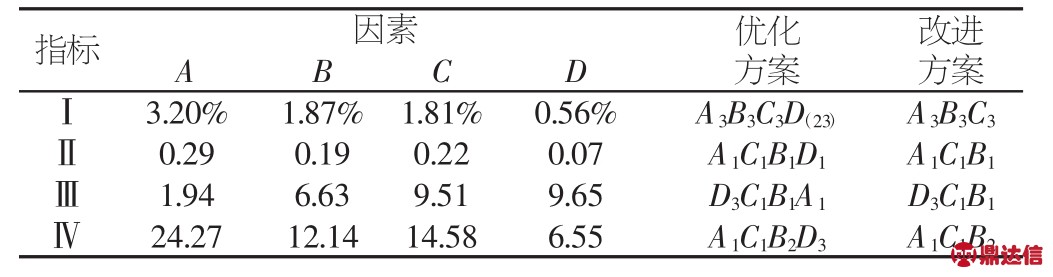
综上,基于换挡时序的换挡策略为先切换第3组离合器,再切换第1组离合器,最后切换第2组离合器。
5 结论
以自主设计的一款液压机械无级变速器为研究对象,建立其换挡非线性动力学模型,并应用Simulation X构建变速器仿真模型进行仿真分析,分析表明:(1)液压机械负向传动向液压机械正向传动过渡时,物理参数和换挡时序对分段式液压机械无级变速器换挡品质因素都具有较大的影响;(2)基于物理参数的换挡策略为采取较小的发动机转速、负载转矩及主油路油压,以及较大的调速阀流量;(3)基于换挡时序的换挡策略为先切换换挡机构离合器,再切换行星排待分离离合器,最后切换行星排待接合离合器。