摘 要:为适应碳钢车体生产制造的发展趋势,提出了横梁吊钩模块工艺方案。介绍底架横梁吊钩模块化工艺方案的特点及流程,通过横梁吊钩模块现场试验件尺寸测量与数据分析优化工艺方案,应用优化后的工艺方案再次进行试验。试验证明,该方案效果良好,已投入应用。
关键词:160客车底架模块化;横梁吊钩模块;横梁组成;底架翻转
中国轨道客车近10年来取得了飞跃式发展。铁路客车不断更新换代,2018年底复兴号动车组成员扩容,时速160 km CR200J型复兴号动车组(以下简称160客车)研制成功,取得国家铁路局颁发的型号许可证与制造许可证,160客车正式成国内新一代主力普速列车。160客车车体制造精度、车体质量相比上一代25型客车均有明显提升。为保证160客车车体制造精度的提升,底架横梁、底架吊钩以及整体底架尺寸精度均需要相应提升[1]。
1 底架横梁吊钩模块化工艺方案特点分析
底架是整个车体结构的重要组成部分。中车唐山机车车辆有限公司(以下简称中车唐山公司)车体生产现阶段采用的底架工艺方案如下:底架横梁采用底架骨架胎位横梁散装工艺,横梁下面连接各式吊钩,在底架翻转胎位采取吊钩散装工艺。在160客车的试制过程中,对底架制造精度提出更高的要求,此种工艺方案难以满足160客车底架尤其是底架吊钩的精度需求。为此急需一种新工艺方案解决以上问题。
依据目前底架设计结构,底架横梁与吊钩可以作为单独的横梁吊钩模块,通过横梁、吊钩的模块化工艺方案去解决生产效率瓶颈及制造精度不足等问题。
底架横梁吊钩模块化工艺方案,主体思路是将底架横梁与吊钩优先组装焊接形成横梁吊钩模块,在底架骨架组装过程中,用横梁吊钩模块取代原单根横梁。横梁吊钩模块整体组装后,吊钩不需要在底架翻转胎位进行组装,底架翻转胎位吊座组焊的各种不足就不存在了。通过此方案,底架横梁吊钩模块化工艺方案的关键转换成了如何获取合格的横梁吊钩模块。
横梁吊钩模块工艺方案主体思路为:首先横梁与吊钩在前期备料过程进行组装焊接,组装焊接完成后对横梁吊钩进行调修、检测、焊缝探伤,将原有在底架翻转胎位的工作,前移到横梁备料工序。通过以上工序的前移,获得合格的横梁吊钩模块就有效解决了吊钩散装的不足点[2]。
2 横梁吊钩模块制造工艺方案
横梁吊钩模块制造工艺方案的主要目标是获得高质量标准的横梁吊钩模块,通过横梁吊钩模块的精度提升,有效提升整个底架组装后的制造精度,并且提升整个底架产线的模块化、节拍化水平。
横梁吊钩模块制造工艺方案主体工艺流程如图1所示,其详细工艺流程如下:
(1)横梁压紧,以横梁中心为定位基准,组装横梁内侧筋板,之后横梁与筋板进行焊接,形成横梁组成;
(2)横梁组成入横梁吊钩组焊工装,横梁组成以横梁中心为定位基准,每次同时入胎2根横梁,并将横梁对称布置入横梁吊钩组焊胎并定位压紧;
(3)吊钩入胎并定位、压紧、点固,其中吊钩定位以横梁中心为基准,要求横梁上所有4个吊钩全部完成入胎定位、压紧、点固;
(4)横梁与吊钩之间焊缝焊接,焊接过程通过变位机转动,确保不同位置的焊缝均处于较好的焊接方位。横梁与吊钩采用对称焊接顺序执行,确保横梁与吊钩之间的焊接变形相互消减;
(5)焊接完成后冷却约20 min,横梁与吊钩之间焊缝冷却,拆下横梁吊钩模块压紧装置并移出横梁吊钩组焊工装。横梁吊钩模块在调修平台进行调修。调修过程重点在于吊钩与横梁连接位置,重点调修横梁直线度、吊钩安装平面的平面度,确保调修后达到模块精度要求;
(6)横梁吊钩模块调修后,在交验平台对横梁吊钩模块进行焊缝磁粉探伤;
(7)横梁吊钩模块进行尺寸检测并填写相应检查卡片,横梁吊钩模块交付下道底架骨架组装工序。
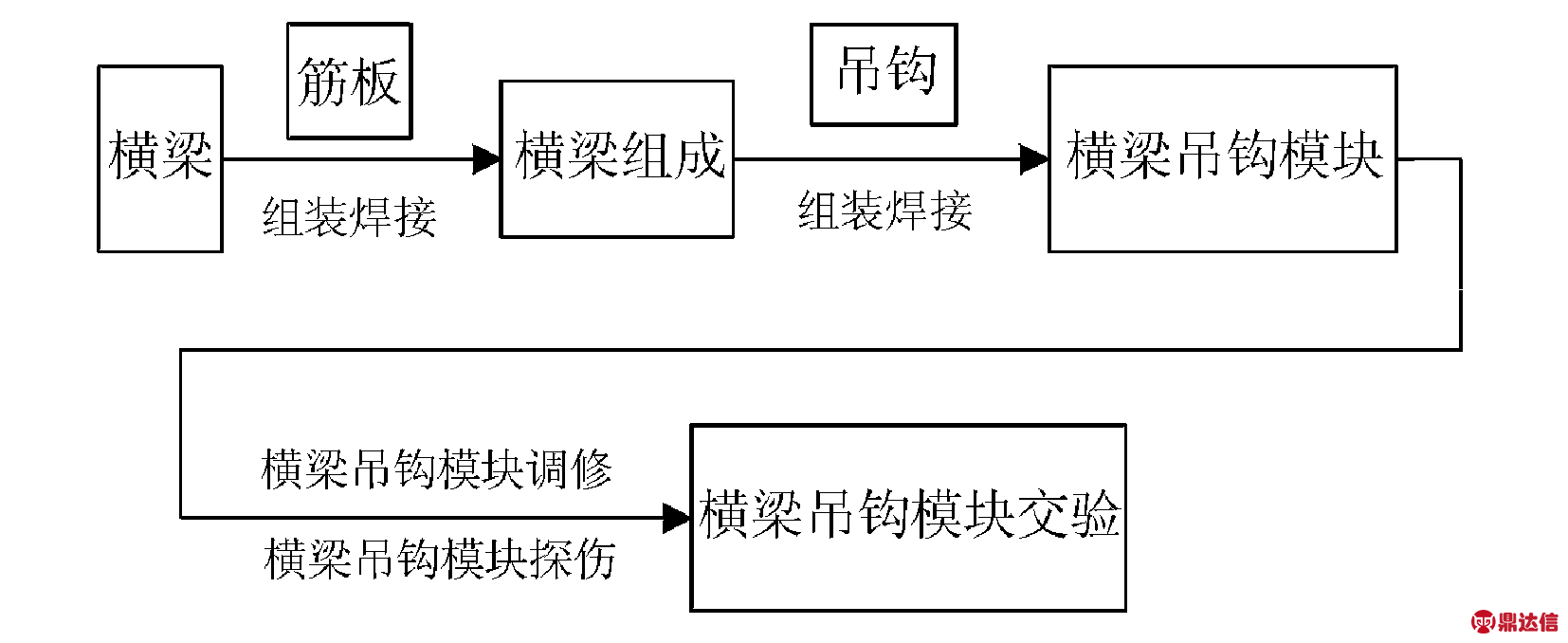
图1 横梁吊钩模块制造过程工艺流程图
3 横梁吊钩制造方案试验与优化
3.1 横梁吊钩模块制造工艺方案试验
为验证横梁吊钩制造工艺方案的可靠性与可实施性,现通过试验进行可行性研究,同时通过试验过程出现的问题进行工艺方案再优化。

图2 双横梁对称压紧图
按照横梁吊钩模块制造工艺方案,2个横梁对称入胎并压紧(见图2)。横梁定位压紧后,吊钩通过中心定位入胎并压紧,压紧形式如图3所示。横梁、吊钩完成压紧后进行横梁与吊钩翻转焊接(见图4)。

图3 吊钩对称压紧图
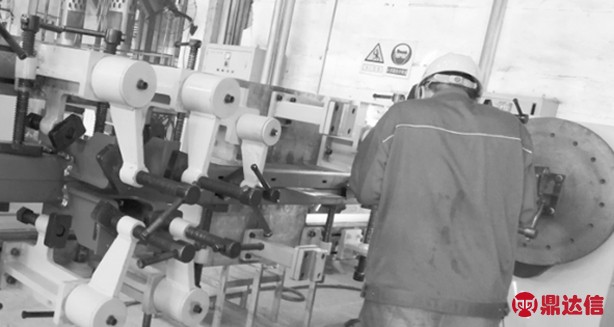
图4 横梁与吊钩翻转焊接图
焊接完成后,在横梁吊钩焊接工装冷却15 min,待焊缝冷却后,横梁吊钩模块去除压紧并下胎。下胎后在测量平台对横梁吊钩进行现场尺寸检测,横梁吊钩模块现场数据检测过程如图5所示。
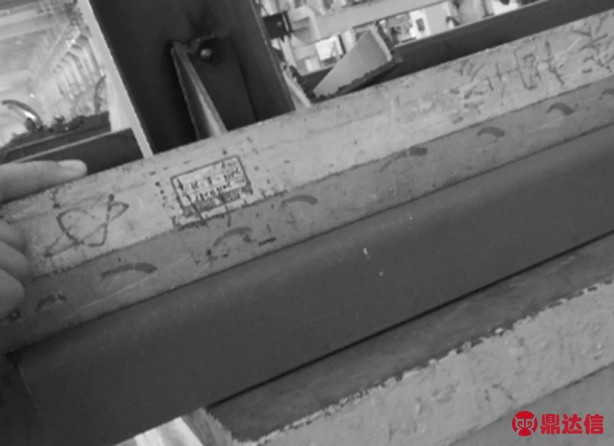
图5 横梁吊钩模块尺寸检测图
通过以上流程制造完成第一批横梁吊钩模块并选取其中10组进行横梁吊钩模块尺寸检测,现场获得横梁吊钩模块尺寸数据,如表1所示。
表1 横梁吊钩模块第一批尺寸数据 /mm

经过现场尺寸测量数据统计分析发现,第一批横梁吊钩模块焊接后变形较大,尤其在焊接后横梁直线度方面普遍达到5 mm左右。针对横梁直线度变化较大问题,经过数据变化趋势分析,发现横梁的弯曲方向、弯曲位置比较有规律,变形大部分发生在横梁与吊钩焊接位置,并且横梁两端有明显的向外弯曲,同时向上弯曲的趋势。横梁向外弯曲、向上弯曲导致吊钩出现高度差、吊钩平面度超差等问题。
由于横梁吊钩模块并没有与底架相连接,可调修性较好,经过现场不断调修,获得了7组合格的横梁吊钩模块,另外3组最终在横梁直线度、吊钩平面度等测量项点中超出标准0.5 mm。
3.2 横梁吊钩模块制造工艺方案优化
依据第一批横梁吊钩试验数据分析、工艺方案分析,在第二批横梁吊钩模块试验前,对原制造工艺方案做了如下修改优化:
(1)为解决横梁两端向上弯曲现象,在横梁吊钩胎中心位置增加反变形,将横梁吊钩胎中心垫高6 mm,在两横梁中心位置产生高出横梁两端6 mm的反变形;
(2)为解决横梁两端向外弯曲现象,在两横梁组成入胎后增加插入4 mm板材,在横梁中心产生4mm向外偏转反变形,两横梁中间增加4 mm反变形(见图6);

图6 两横梁中心增加4 mm反变形图
(3)在变形比较大的横梁两端增加压紧装置,确保焊接过程中横梁两端紧固稳定,横梁两端增加压紧装置,如图7所示。应用优化后的横梁吊钩模块制造工艺方案,再次进行横梁吊钩模块制造试验。

图7 横梁两端增加压紧装置图
优化方案后制造完成第二批10组横梁吊钩进行横梁吊钩模块尺寸测量,现场获得横梁吊钩模块尺寸数据(见表2)。
通过第二批横梁吊钩数据分析,焊接前横梁预制反变形量与焊接过程变形部分相互抵消,在焊接后横梁直线度有了较大改善,由原变形量5~6 mm偏差提升到2.5~3 mm。横梁吊钩模块其他尺寸如吊钩高度差、吊钩平面度等也有所提升。工艺方案优化后横梁吊钩模块第二次制造精度提升明显,横梁吊钩模块制造工艺方案优化效果较理想。
表2 横梁吊钩模块第二批尺寸数据 /mm
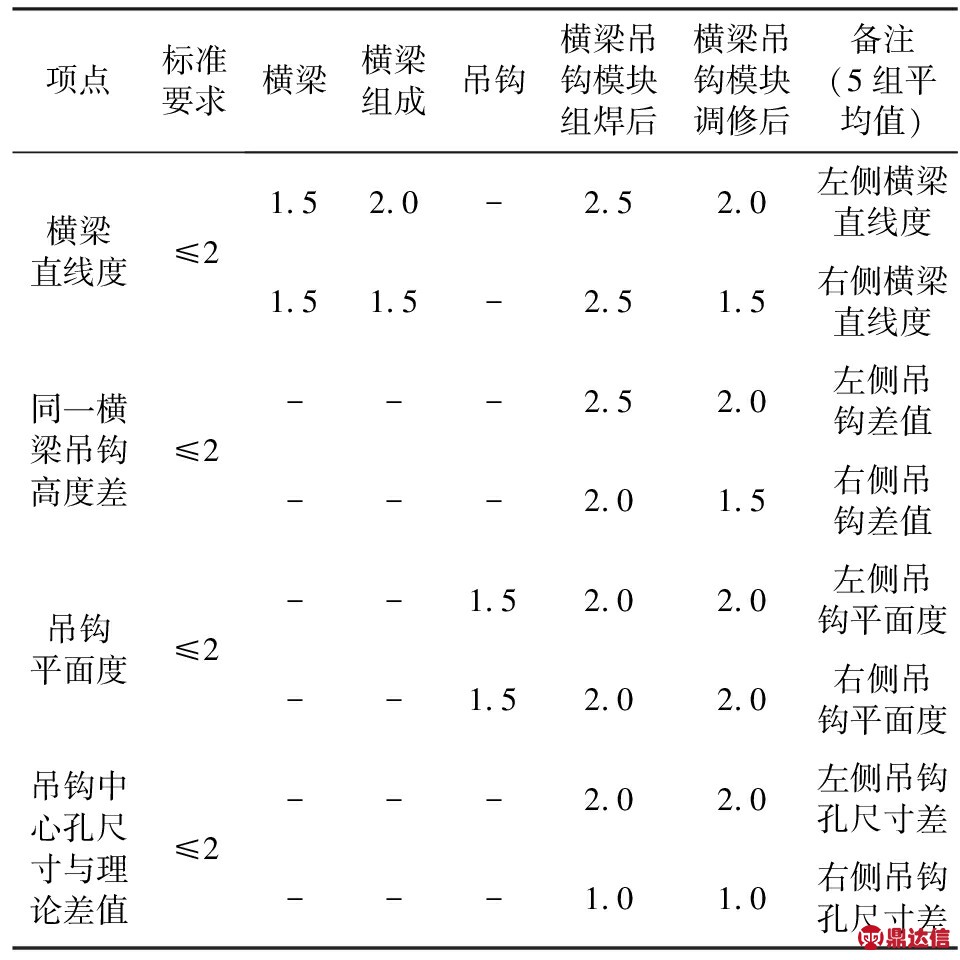
对第二批试验10组横梁吊钩模块进行调修,调修后的10组横梁吊钩模块全部合格,且本次横梁吊钩的调修工作量较第一批明显降低。通过第二批横梁吊钩模块试验证明在横梁两个方向分别增加4 mm、6 mm反变形量,横梁两端增加压紧装置等工艺方案的优化,成功抵消了部分焊接变形,有效提升了横梁吊钩模块的制造质量。
调修后的横梁吊钩模块经过焊缝表面磁粉探伤,焊缝情况良好,磁粉探伤一次全部通过,满足横梁吊钩模块的焊缝要求。焊缝磁粉探伤合格的横梁吊钩模块如图8所示。

图8 焊缝磁粉探伤合格的横梁吊钩模块图
工艺方案优化后横梁吊钩模块制造精度高,获得了合格的横梁吊钩模块。
通过以上试验证明横梁吊钩模块制造工艺方案具有较强可实施性,可为底架制造产线大批量供应合格的横梁吊钩模块,实现底架制造的初步模块化。
4 横梁吊钩模块工艺方案总结
通过横梁吊钩模块制造试验,应用优化后横梁吊钩工艺方案制造出了合格的横梁吊钩模块。现阶段横梁吊钩模块工艺方案已经开始应用在中车唐山公司车间批量化底架生产中,横梁吊钩模块底架生产应用效果如图9所示。
应用横梁吊钩模块制造工艺后,底架吊钩精度提升明显,底架翻转工位工作量降低,生产线效率提升。

图9 横梁吊钩模块底架制造过程应用效果图
伴随着节拍化生产进一步推行,在本批客车生产对横梁吊钩模块工艺方案充分实施验证后, 将继续优化底架横梁吊钩模块化工艺方案,继续提升横梁吊钩模块制造精度,进而提升底架吊钩制造精度。