摘 要:应用拼焊板技术对保险杠横梁的厚度及材料进行多目标优化,控制横梁质量变化,提高保险杠吸能,以提高保险杠横梁的耐撞性。根据实验要求建立原保险杠横梁与拼焊板横梁摆锤冲击有限元模型,并对其求解。进行三点静压试验,试验与仿真载荷曲线高度吻合,验证了仿真分析的有效性。通过正交试验来确定拼焊板材料,用拉丁超立方采样方法对各材料的厚度进行试验设计,得到不同厚度组合的结果;利用响应面法构造近似目标函数,用ASA自适应模拟退火算法在各自响应面上寻找各板厚最优值。结果表明:优化后的拼焊板横梁比吸能提高了15.16%,具有更好的变形模式,提高了保险杠横梁的耐撞性。
关键词:保险杠横梁;拼焊板;摆锤冲击试验;响应面法;多目标优化
在汽车碰撞事故中,发生概率最大的是前部碰撞,提高保险杠系统的耐撞性能够减少正面碰撞中的驾乘人员伤亡和车辆损坏[1]。保险杠横梁是汽车发生正面碰撞时起初发挥作用的部件,其性能的优劣对车身前端碰撞安全性有重要影响[2]。
汽车技术发展的两个长久主题是安全和节能,轻量化是实现汽车节能的重要方法,但是简单的结构轻量化可能影响汽车的安全性,特别是汽车的碰撞安全性[3]。研究者在进行保险杠设计时,应将轻量化与安全性结合在一起考虑。
现有的研究中已经出现很多的保险杠种类,如铝合金保险杠[4]、双帽型保险杠[5]、液压成型保险杠[6]以及碳纤维复合结构[7]等,然而这些保险杠大多材料昂贵、加工较为复杂。汽车上常用的钢材具有相对便宜的价格和更加成熟的加工技术。如今,多种高强度钢的研究日益成熟[8-9],研究成果已经广泛应用于汽车轻量化之中。拼焊板技术的出现可以更好地应用高强度钢,通过将厚度、材料不同的金属薄板焊接,然后再冲压成所需的零部件[10]。拼焊板的优点是材料和厚度的不同组合,可以使部件安全性能提高,而且控制了其质量增加[11]。
为提高保险杠安全性并控制其质量增加,本文将拼焊板技术应用到保险杠横梁上,通过正交试验来确定拼焊板材料,以拉丁超立方采样方法对各材料的厚度进行试验方案设计,得到不同厚度组合的碰撞信息,通过响应面法构造近似目标函数。对拼焊板横梁的厚度及材料进行多目标优化设计,控制横梁质量变化,提高保险杠吸能,以提高横梁的耐撞性。
1 保险杠横梁模型
1.1 原保险杠模型
本文所用的某保险杠模型如图1所示。保险杠横梁板材厚1.2 mm,吸能盒板厚2.0 mm。横梁的长度为1330 mm,高度为130 mm,宽度为50 mm,截面形状为B型。横梁采用B410LA钢板。
根据《GB17354—1998汽车前、后端保护装置》规定的低速碰撞实验标准,在CATIA中建立摆锤的模型,在此基础上建立汽车保险杠横梁和吸能盒模型。将模型导入Hypermesh中进行有限元网格划分,保险杠横梁选用Belytschko-Tsay壳单元,沿厚度方向积分点个数设置为3,网格尺寸为5 mm,共包含30 003个壳单元,三角形单元有112个,只占0.37%,网格质量良好。
摆锤与保险杠之间的接触算法设置为自动面面接触,保险杠自身为自动单面接触,动摩擦与静摩擦因数分别为0.2、0.3。对各部件赋予材料与属性,得到碰撞系统有限元模型,如图2所示。约束摆锤Y、Z方向的自由度,给X方向施加4 km/h的初速度,导入LS-DYNA求解器中计算。
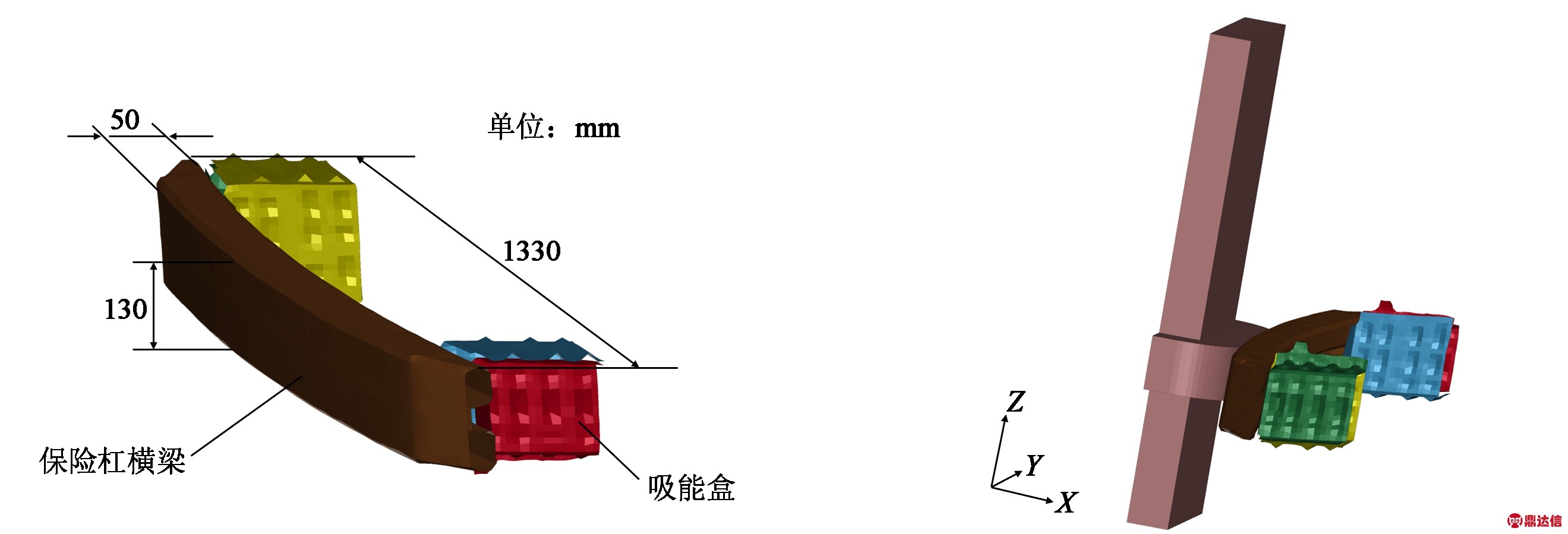
图1 保险杠模型 图2 保险杠摆锤冲击仿真实验
系统能量计算结果如图3所示,得出沙漏能为内能的0.002 1%,仿真要求沙漏能低于内能的5%。总能量守恒,动能逐渐转化为内能,动能逐渐减小,碰撞仿真结果可靠。
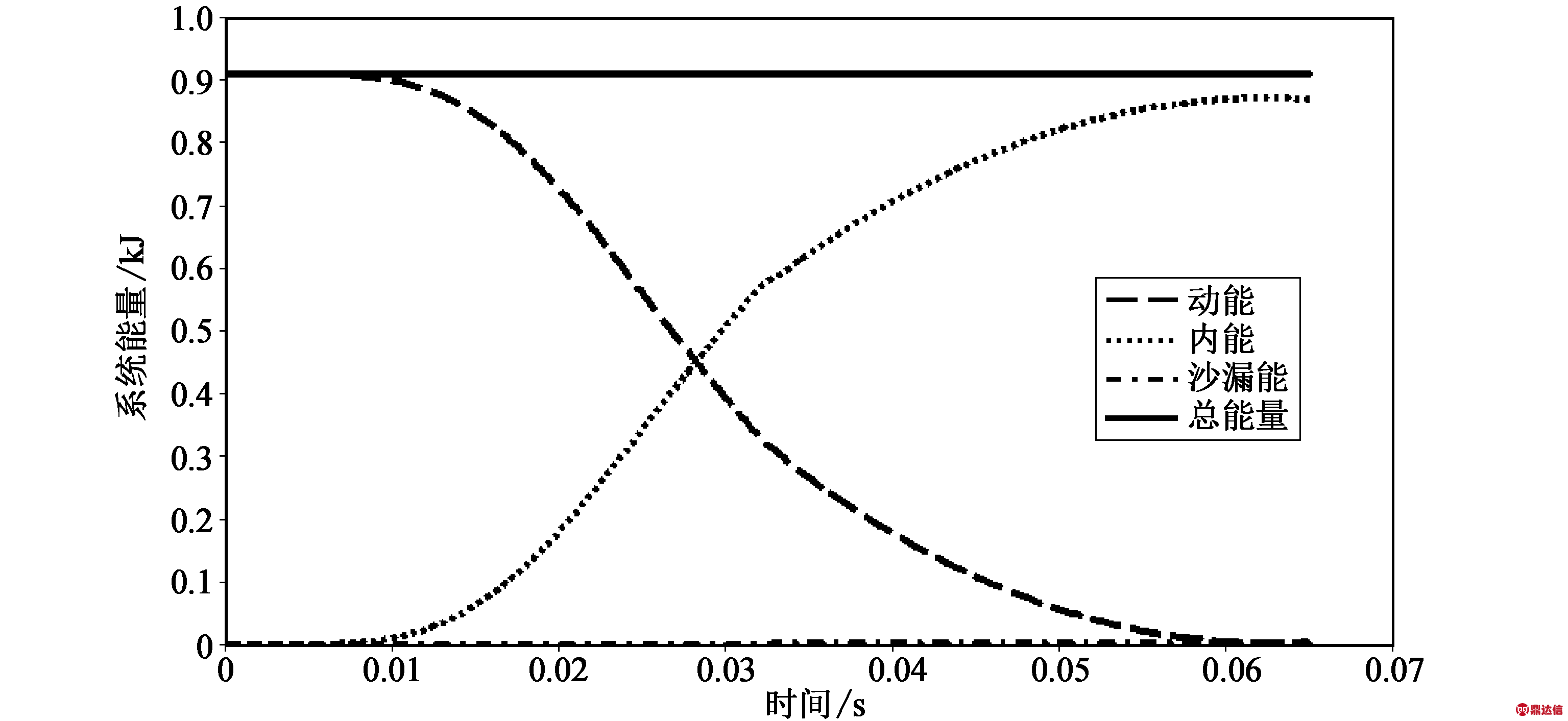
图3 系统能量变化图
1.2 仿真分析验证
用一个长度为200 mm,外径为30 mm,板材厚度为1.4 mm的圆形截面梁,在承载能力100 kN的INSTRON 4482试验机上作径向10 mm/min的准静态压缩实验,验证仿真分析的有效性。由图4变形图可知,试验与仿真中的压头加载点处的变形相同。由图5中的载荷曲线可知,试验与仿真中的载荷曲线基本吻合,试验峰值6.18 kN,仿真载荷峰值为6.03 kN,误差约为2.43%,与试验结果相比,试样的变形方式和载荷特性的数值结果明显吻合,验证了仿真分析的有效性[12]。
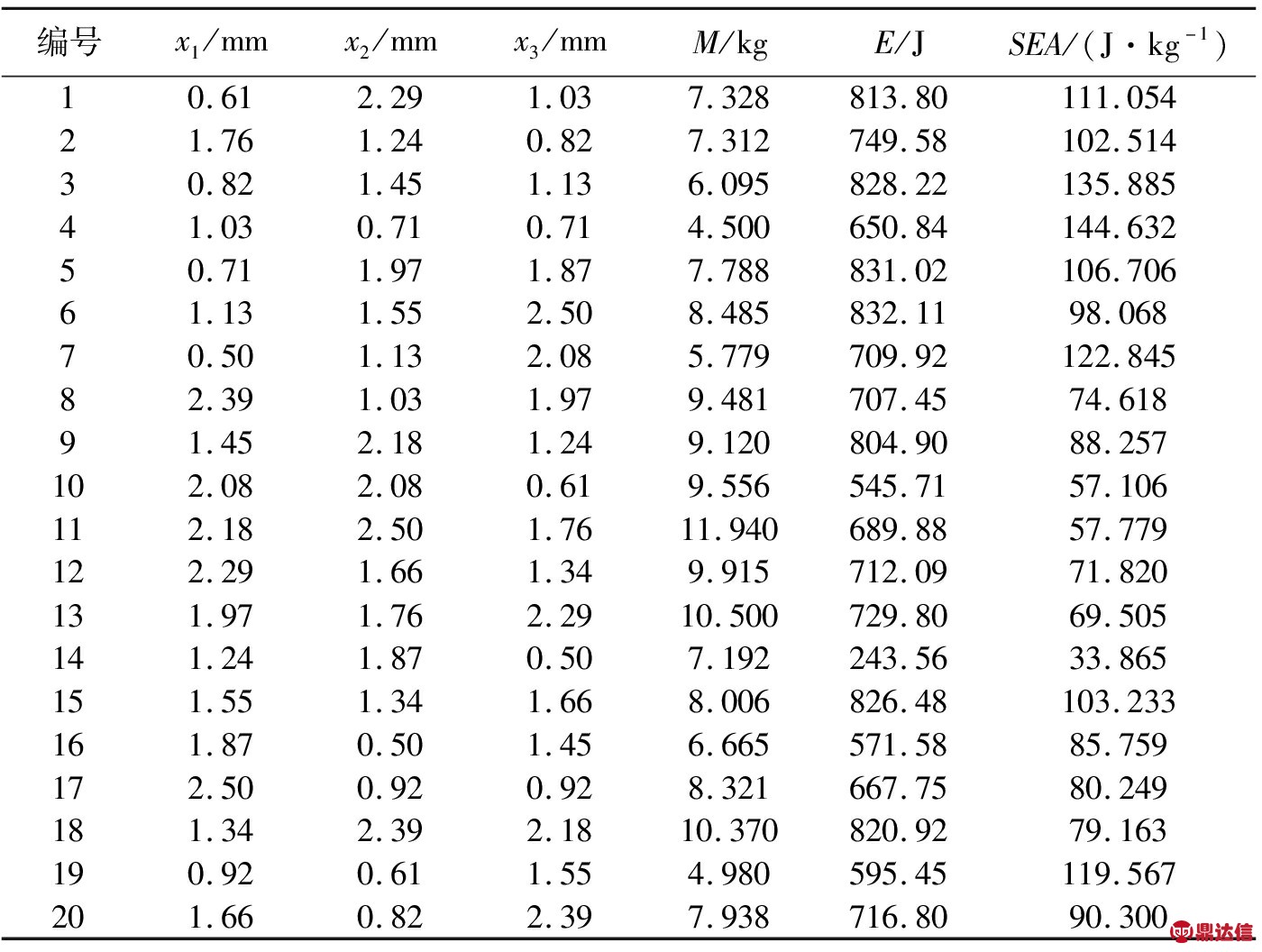
(a)试验变形 (b)仿真变形图
图4 试验与仿真变形图
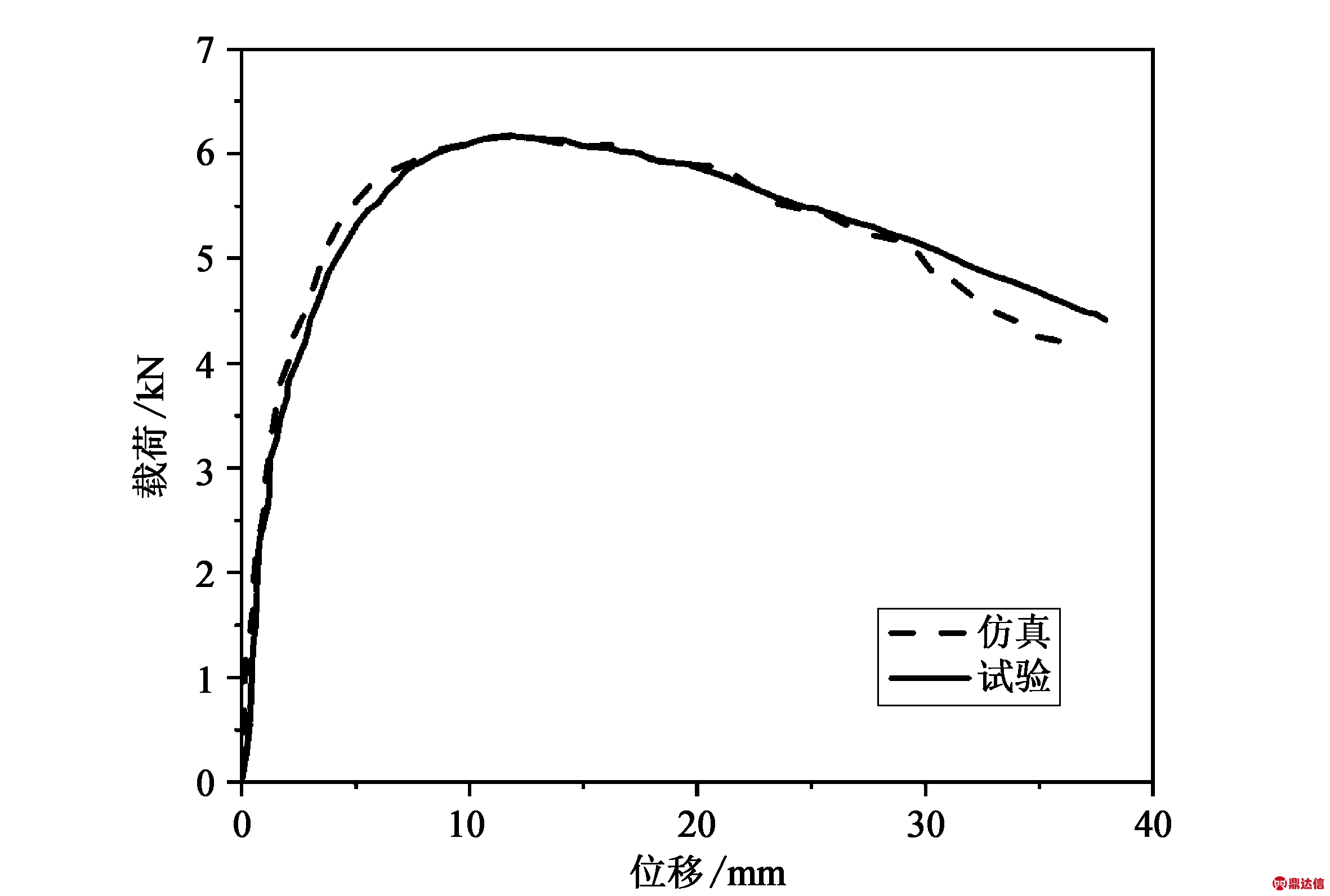
图5 试验与仿真位移载荷曲线
1.3 拼焊保险杠横梁模型
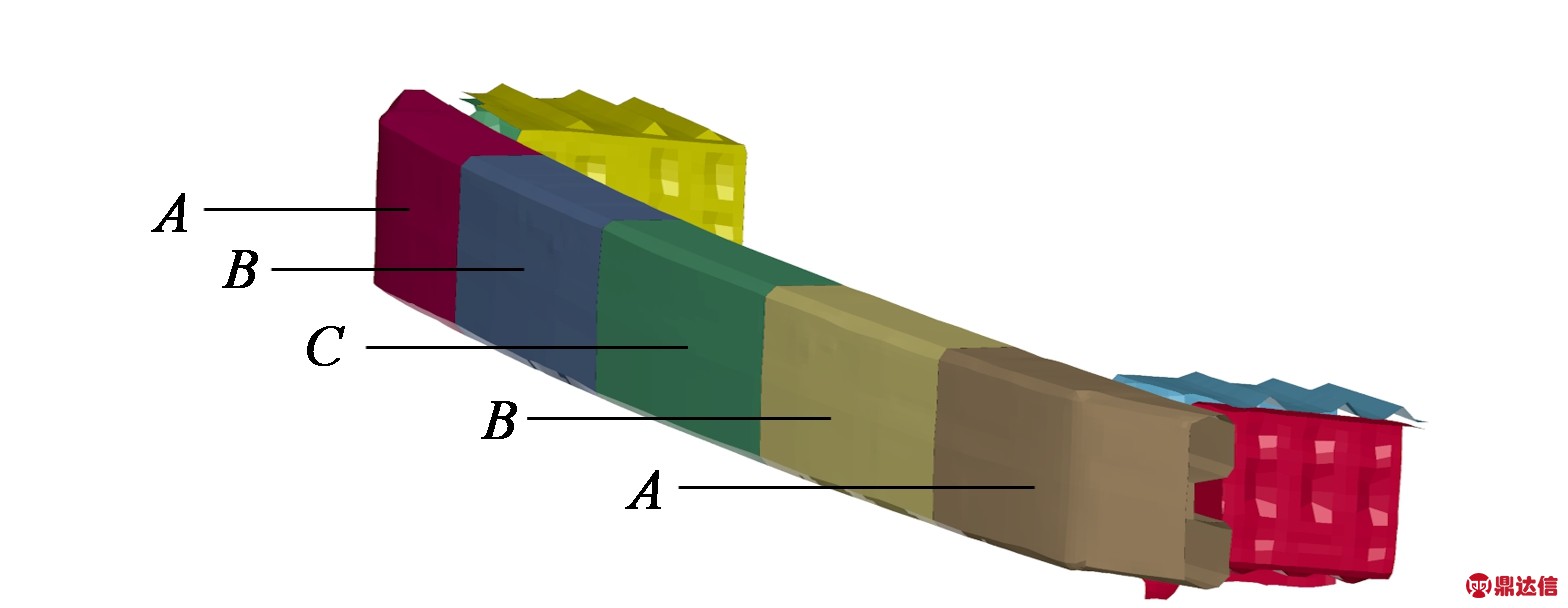
图6 拼焊板保险杠横梁
由于拼焊板和单一钢板的抗拉强度非常接近[13],因此,拼焊板保险杠模型不考虑焊缝对耐撞性的影响,不同板材之间以共节点的方式连接[11]。摆锤正面冲击保险杠横梁,其结构和受力状况具有对称性,本文将横梁分为左右对称且长度相等的5段,对称位置的材料和厚度都相同。如图6所示,根据不同的位置分别用A、B、C编号。
2 保险杠横梁的优化设计
通过正交试验来确定拼焊板材料,用拉丁超立方采样方法对各材料的厚度进行试验设计,得到不同厚度组合的碰撞信息,通过响应面法构造近似目标函数。将轻量化与安全性结合在一起考虑,对拼焊板横梁进行多目标优化设计,控制质量变化,提高保险杠吸能。
2.1 拼焊板横梁材料的确定
对保险杠横梁A、B、C处分别以不同的5种材料作为设计变量,按编号1到5分别对应的材料为DP300、B410LA、DP600、DP780、DP800,以保险杠横梁的总吸能作为响应,进行试验分析设计。对于上述3因素5水平试验,以不考虑交互作用的L25(56)进行正交分析,进行25次试验,选取理想的材料组合。
按表1的试验方案进行数值模拟,将保险杠横梁的总吸能作为评价指标,对试验结果进行极差分析,结果如表2所示。从表中可以得出,对保险杠横梁吸能量影响的主次顺序为A>C>B,最优组合为A2C3B4,即在A位置选择B410LA,B位置选择DP600,C位置选择DP780。
表1 正交试验方案及结果
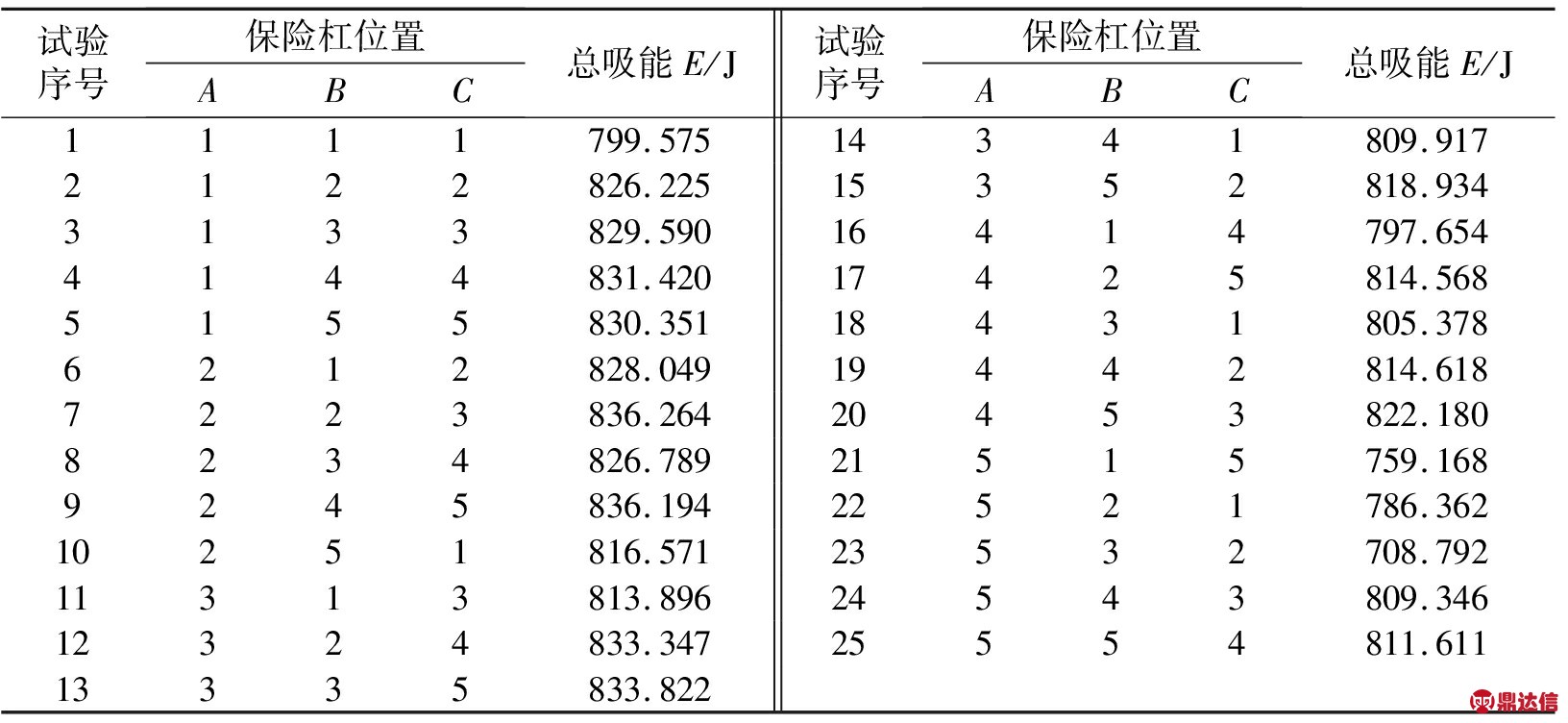
表2 正交试验数据分析表
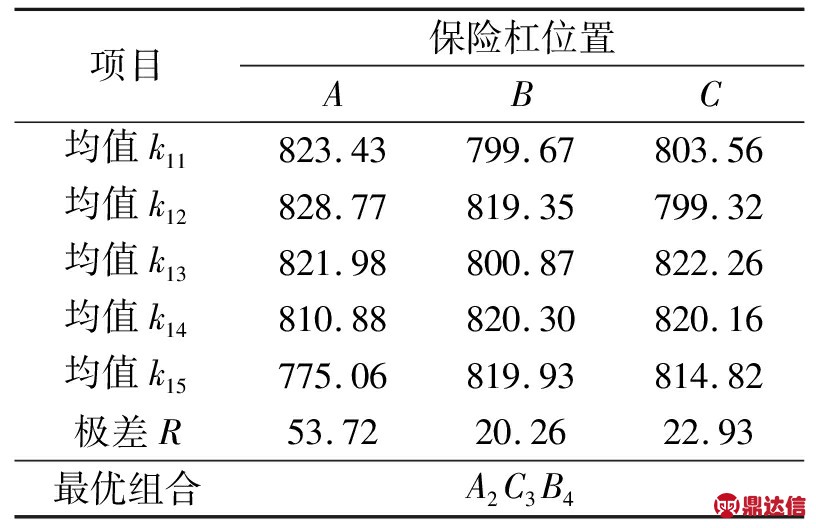
2.2 拼焊板厚度确定
为了更好地确定拼焊板的厚度,提高保险杠的耐撞性与轻量化,需要大量的碰撞模拟试验,在对接触-碰撞这样高度非线性的优化问题需要花费大量的时间,因此本文选择建立近似模型的方法。近似模型可以减少仿真计算时间,提高优化效率,而且建立了经验公式,能获得输入、输出变量之间的量化关系,更好地将优化算法应用到工程领域[14]。
为了建立响应面近似模型,需要一定数量的试验设计数据,所采用的数据必须能够代表整个空间样本。拉丁超立方采样方法能够有效地填充样本空间和拟合非线性响应[15]。利用拉丁超立方采样取得A、B、C处的厚度,分别记作x1、x2、x3,从而计算出保险杠横梁质量M、吸能量E以及比吸能SEA的目标试验值。表3所示为20组仿真设计采样及目标试验值。
表3 拉丁超立方采样及其目标试验值
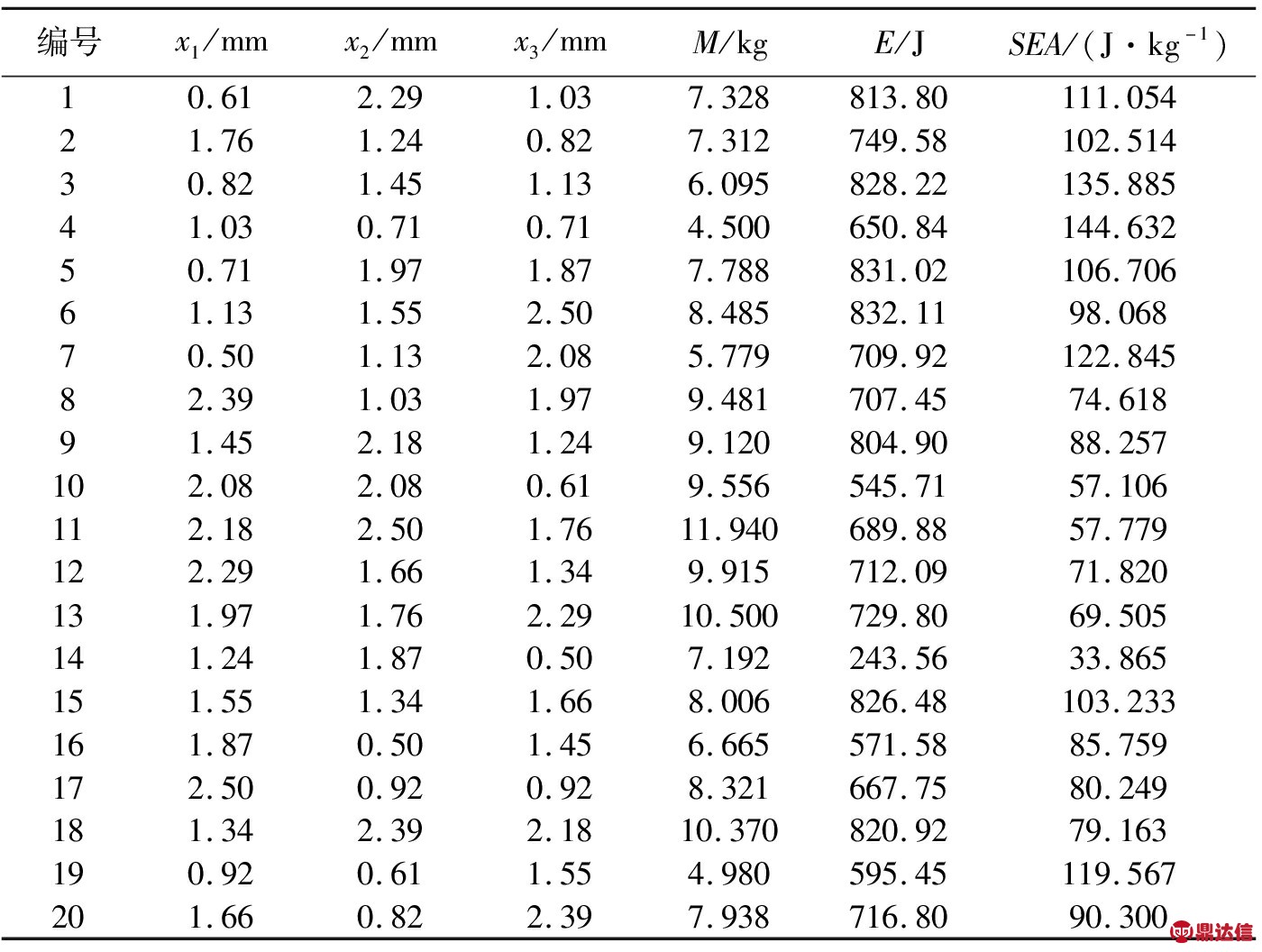
建立材料厚度与质量、吸能量、比吸能之间的响应面关系,各响应的决定系数R2分别为1.000、0.994、0.972,具有较高的近似精度,以x1、x2、x3分别代表A、B、C处材料的厚度,以yM、yE、ySEA分别代表质量、吸能量、比吸能响应面函数,拟合出的二次多项式为
yM=-1.455×10-6+0.002 136x1+0.002 134x2+0.011 07x3-4.020
(1)
yE=485 115.117 5-158 534.708 5x1+577 716.910 298x2-123 690.783 2x3+

112 501.389 0x1x3+38 696.648 89x2x3,
(2)
ySEA=279 321 399.859 0-125 218 409.230 5x1+5 150 411.019 55x2-
75 436 900.096 9x3+13 183 138.959
1 352 472.469 252 305.727 5x1x2+29 132 415.123 7x1x3+
14 691 002.221 2x2x3。
(3)
根据上述分析,采用以下数学模型来描述保险杠横梁的多目标优化问题。横梁优化数学模型就简化为如下形式。
变量:材料厚度x1、x2、x3;
约束条件:x1、x2、x3=0.8~2.5 mm;
优化目标:min(yM)、max(yE)、max(ySEA)。
利用ASA自适应模拟退火算法,用构造出的响应面模型,根据优化目标和约束条件进行迭代求解,迭代到4570次时得到了最优解,共迭代10 103次,得到满足性能要求的最优的拼焊板厚度组合,经圆整后的结果为x1=0.8 mm,x2=1.6 mm,x3=1.2 mm。
2.3 优化结果分析
表4为初始设计与优化设计的保险杠横梁对比情况。可以看出,优化模型与原保险杠横梁相比,吸能量增加13.71%,质量下降1.27%,比吸能提高15.16%。
表4 优化设计与初始设计的计算结果对比
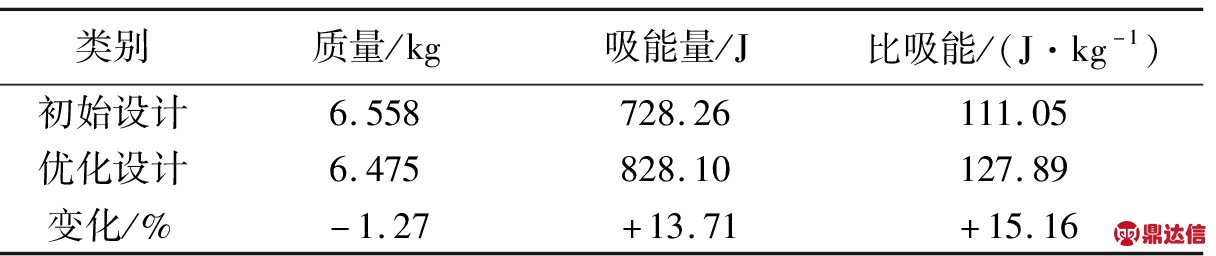
由图7保险杠的变形情况可以看出,原横梁的中心为主要的变形区,出现了局部塌陷弯曲变形,参与变形的材料少。优化的拼焊板横梁形变得到控制,变形模式实现了改善,变形较小,参与变形吸能的材料增加,这样就吸收了更多的能量。
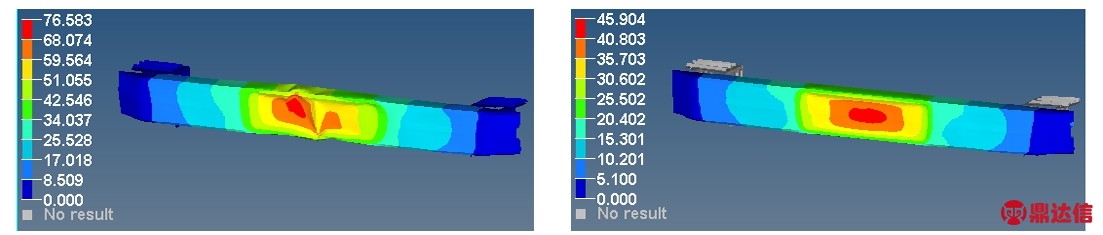
(a)原保险杠横梁形变图 (b)优化后保险杠横梁形变图
图7 优化前后形变对比图
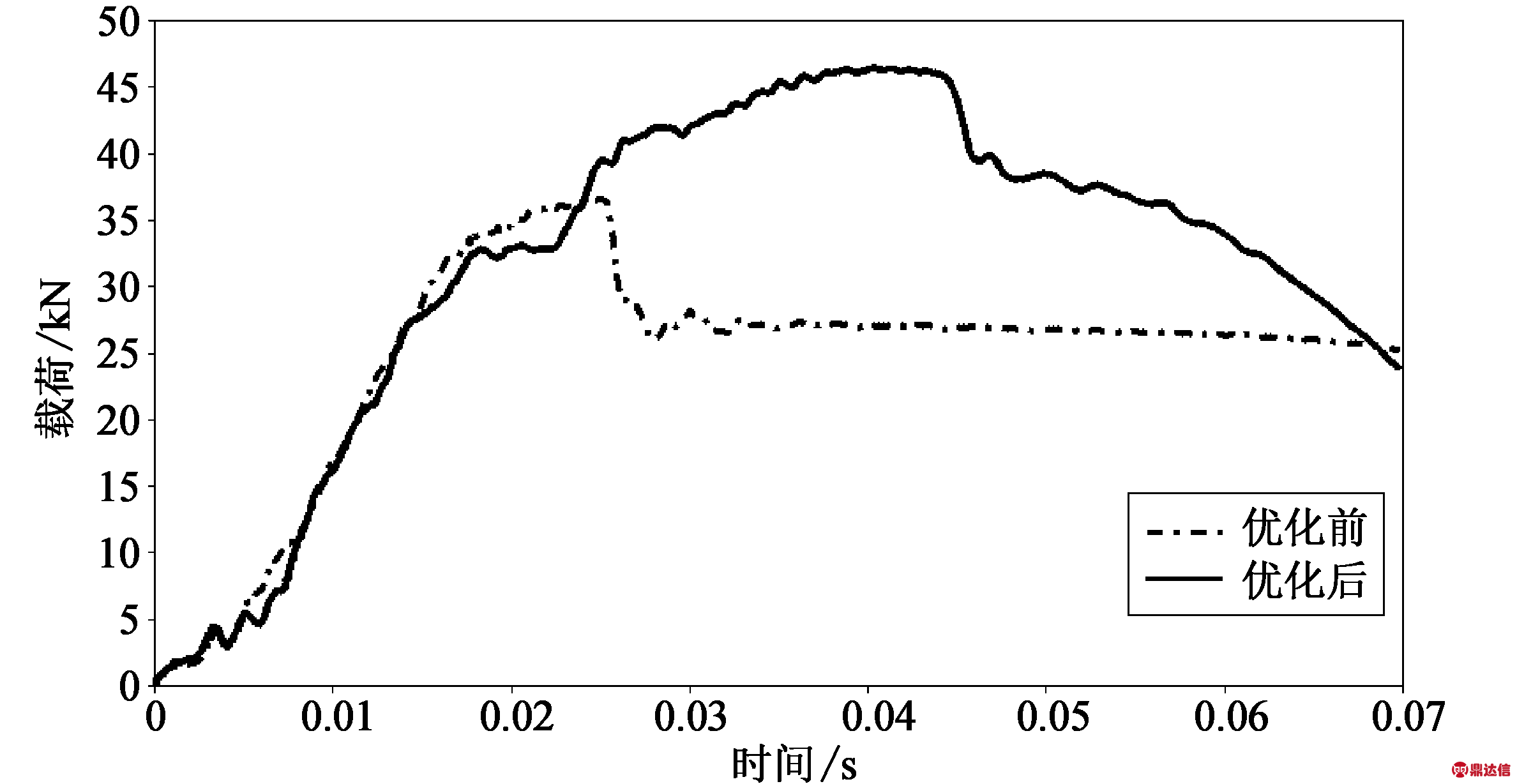
图8 优化前后载荷-时间曲线
由图8优化前后载荷-时间曲线可知,优化后保险杠横梁的接触力峰值明显增加,一定程度上增加了横梁承受载荷的能力。拼焊板横梁的压力达到了峰值的时间推迟,能够较长时间承受碰撞载荷,承载冲击的能力增强,就能较好地保护驾乘人员的安全。原横梁的接触力载荷峰值要小于优化后的峰值,且达到峰值的时间短,承载能力较弱。优化后,保险杠横梁的吸能量提高,承载能力增加,减小了保险杠横梁的质量,提高了保险杠横梁的耐撞性。
3 结论
对保险杠横梁进行摆锤冲击仿真试验,对拼焊板保险杠横梁进行了多目标优化。经过ASA自适应模拟退火算法计算,得到了优化结果。横梁的比吸能提高了15.16%,质量减少了1.27%,提高了保险杠耐撞性。
本文只考虑了中间位置的摆锤冲击,没有模拟汽车碰撞事故中可能发生的偏置碰撞,为了得到更加全面的优化设计结果,在后续研究中可以结合偏置碰撞,以完善优化结果。