摘要:介绍了一起因橡胶垫安装方向错误引发的避雷器故障,并针对该类型故障,对相关制造厂和设备运维单位分别提出了加强工艺流程控制水平、及时对密封孔进行排查工作等建议。
关键词:橡胶垫;安装方向;密封孔;避雷器;运维单位
在电力系统中,避雷器用于保护发输变电设备的绝缘,使其免受雷电过电压和操作过电压的损害。实际运行中发现,避雷器经常因为密封不良、水分潮气进入其内部而发生故障。本文介绍一起因橡胶垫安装方向错误致使避雷器内部受潮、继而引发的故障。并针对该类型故障,对相关设备制造厂和设备运维单位分别提出建议。
1 故障简介
2014年3月9日,220 kV某变电站1号主变A套差动保护动作,跳开主变三侧开关,故障电流3696 A。现场检查发现,1号主变110 kV侧A相避雷器泄漏电流表烧毁(该避雷器3月7日投运),避雷器上下压力释放装置均冲开,压力释放口侧瓷套上烧蚀痕迹明显,顶部伞裙瓷釉脱落,避雷器情况如图1所示。
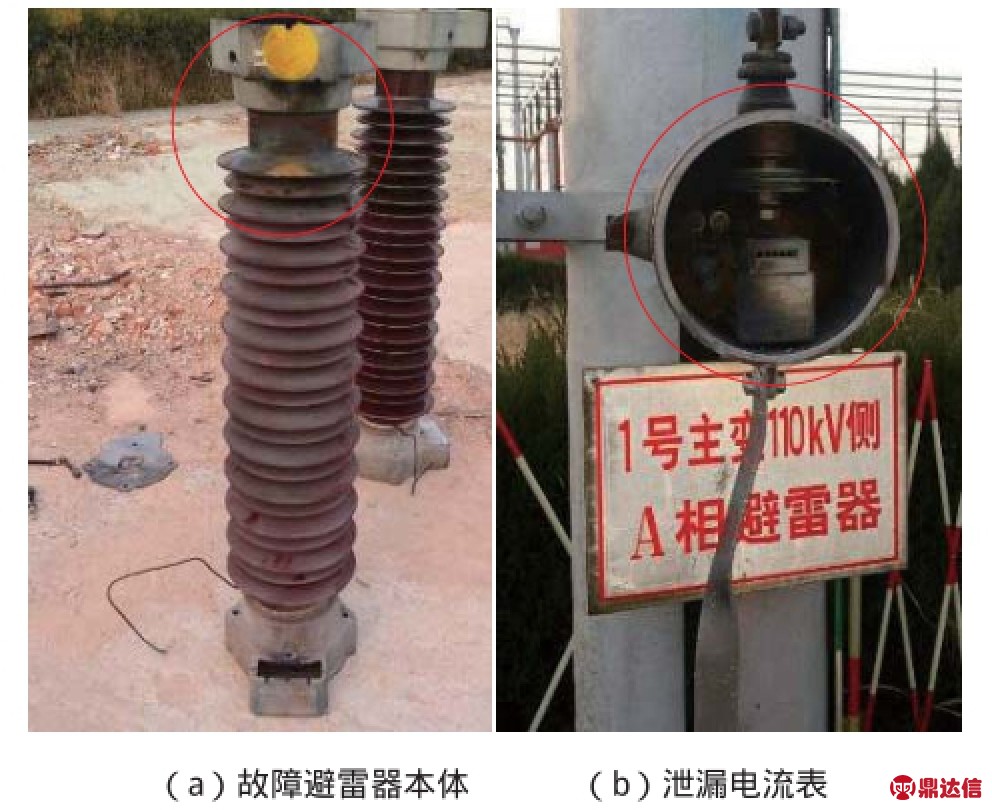
图1 避雷器故障情况
2 故障避雷器介绍
2.1 设备参数
设备参数如表1所示。
表1 设备参数
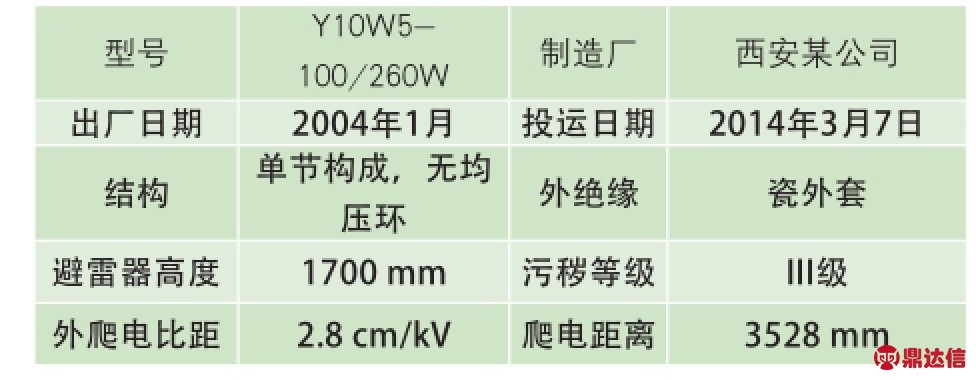
2.2 设备结构
Y10W5-100/260W型避雷器结构示意图如图2所示。避雷器包括上下法兰和瓷套;瓷套内部为避雷器阀柱,由氧化锌电阻片、垫片、绝缘支撑杆等组成;瓷套和法兰之间为密封结构、防爆膜和压力释放装置。
电阻片为空心圆柱,其四周圆柱面涂有绝缘釉,上下表面为铝。电阻片每2片一组,每组下方有垫片(铝片),绝缘支撑杆从电阻片及铝片中心穿过,阀柱下端通过金属部件与下端法兰密封板结构相连。
防爆膜两侧分别为盖板和密封板,其中法兰侧为盖板(圆环形状),瓷套侧为密封板,防爆膜与密封板、密封板与瓷套之间有密封圈,密封板与法兰之间有防水圈。
3 避雷器检测与解体分析
3.1 外观检查
对3支避雷器进行外观检查及比较分析,其中1支为1号主变110 kV侧A相(故障相),另外2支为B、C相(正常相),检查结果如表2所示。
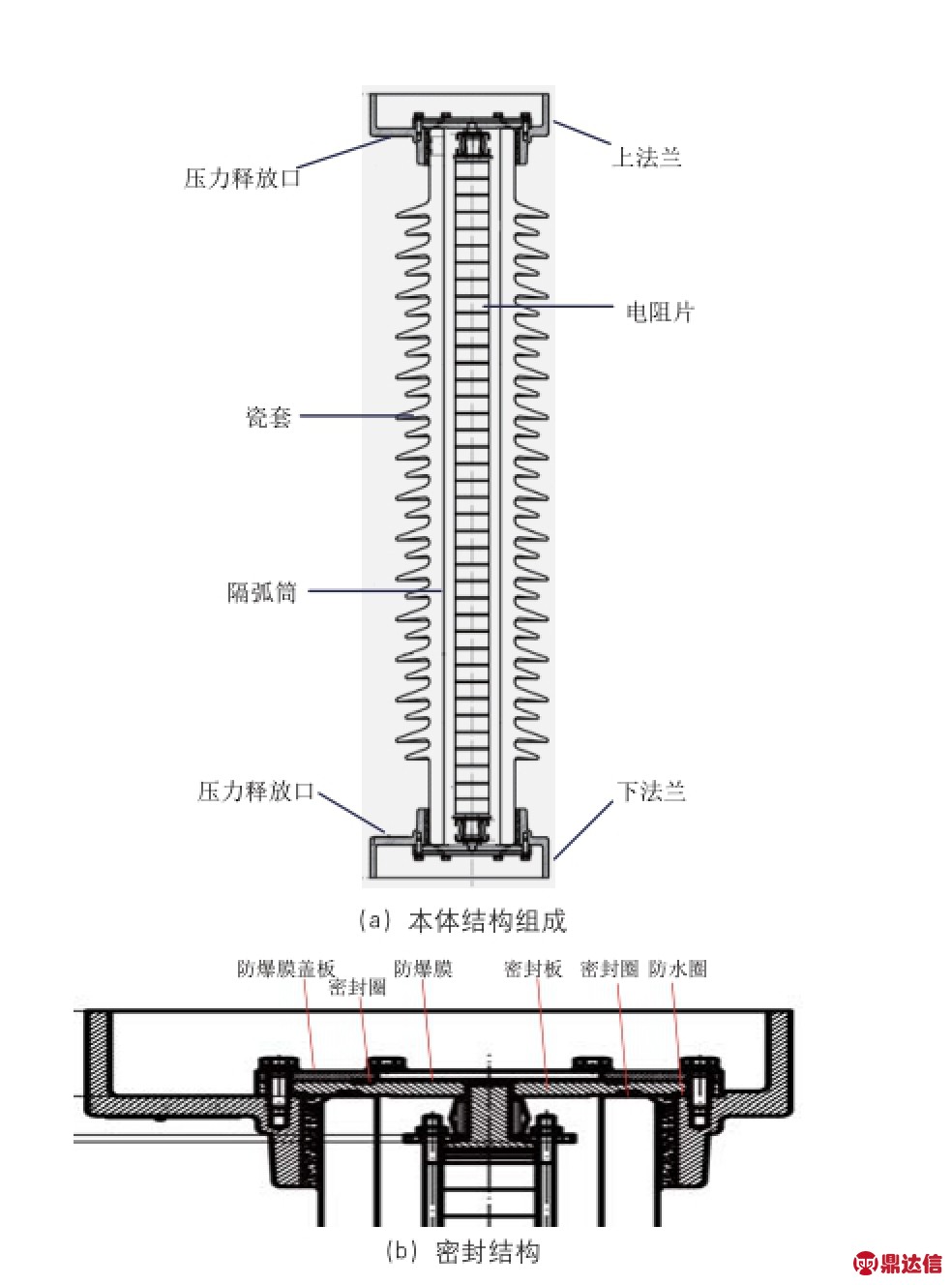
图2 避雷器结构示意图
表2 避雷器外观检查项目及检查结果
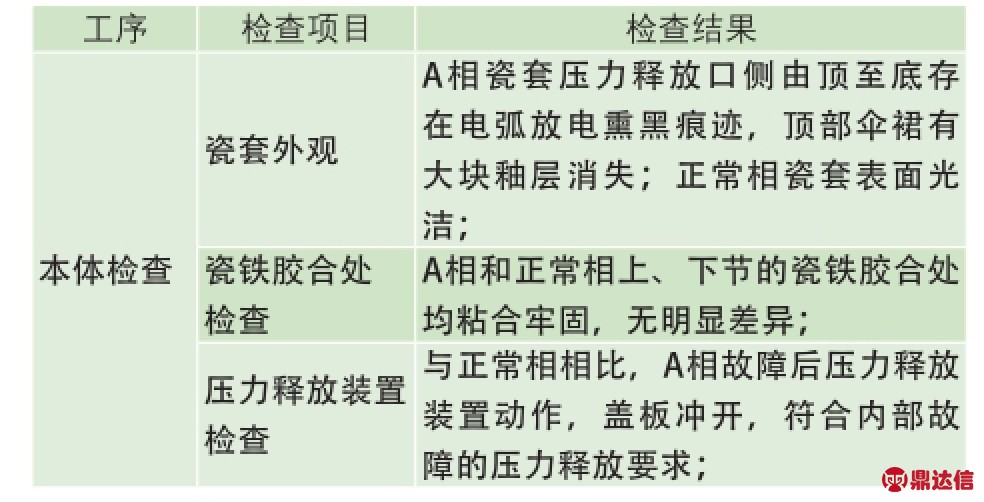
故障避雷器两端密封板密封圈、防水圈完好,具有较强弹性,无老化痕迹,密封性能良好;
故障避雷器隔弧筒内外表面均已熏黑;氧化锌电阻片柱结构完整,顶部碗状压片锈蚀严重;电阻片侧面已经完全熏黑,上下表面有明显受潮痕迹,为沿柱面闪络。
故障避雷器密封盖板上密封孔的螺栓突出于盖板边沿约5 mm(该孔为避雷器装配完成后抽气和充入氮气的通道,因而直接通向避雷器内部)。由于螺栓未完全拧入密封孔内,且密封胶覆盖不严。
密封孔内依次塞入了橡胶垫、铜片,最后拧入螺栓,其正常结构形式,橡胶垫的尖端应朝里;而故障避雷器则是将尖端朝外,在塞入过程中致使橡胶垫和铜片卡在孔中部的螺纹上,导致螺栓无法完全拧入,且密封胶覆盖不严。水分由此孔进入避雷器内,螺栓铜片等锈蚀严重,而正常避雷器螺栓则光亮如新。
3.2 试验检测
为判断避雷器内部是否存在受潮或氧化锌电阻片老化现象,在实验室对正常相避雷器进行直流参数测量,包括绝缘电阻、直流1 mA下的参考电压U1mA和0.75U1mA下的泄漏电流,试验数据见表3(A相避雷器因损坏无法测量),试验结果正常。
3.3 解体分析
为进一步分析避雷器故障原因,对A相(故障相)以及B、C相(正常相)避雷器进行了解体分析,相关分析如下:
故障避雷器两端防爆膜盖板外侧已经完全熏黑,内侧部分熏黑,无锈蚀痕迹;
故障避雷器两端防爆膜被冲破,压接部分均为完整圆环,未见明显松动、压接不到位情况;
表3 正常相避雷器试验结果
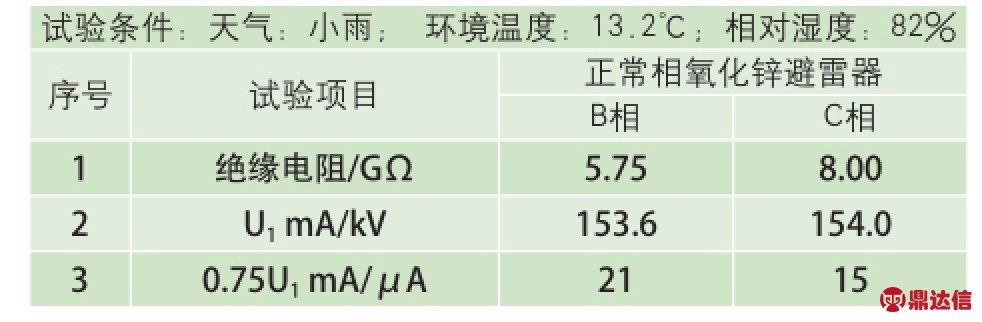
4 故障原因分析
根据上述故障现象、解体情况,分析本次避雷器故障的主要原因是:避雷器制造过程中,密封孔内的橡胶垫安装方向错误,螺栓无法拧入密封孔内,且密封胶覆盖不严,水气进入避雷器内部,导致电阻片柱受潮。继而引发避雷器内部阀柱沿面闪络,内部气压迅速膨胀,冲开防爆膜,压力释放装置动作,故障电流烧毁泄漏电流表。
5 结论及建议
此次避雷器故障的直接原因是:制造厂对密封板上的密封孔处理不当,橡胶垫安装方向错误,导致大量水分侵入避雷器内,电阻片柱受潮,引发沿面闪络。暴露的问题是:相关制造厂安装工艺控制不良。
建议避雷器制造厂在生产过程中加强工艺流程控制水平,严格做好装配工艺管理,确保所有出厂避雷器满足装配工艺要求。同时,在避雷器出厂前,做好避雷器密封试验。
建议运维单位结合停电,开展本型号避雷器密封孔的排查工作,发现问题及时更换。
建议运维单位加强避雷器的日常巡视,做好数据趋势分析。同时,在高低温、雨雪等恶劣天气前后加强红外精确测温,及早发现异常和缺陷。