摘要:本文从价值流的角度出发,对产品生产的信息流和实物流进行分析,找出影响生产周期的环节并对其进行相应的改善,从而减少不必要的浪费,缩短产品生产周期,提高库存周转率,提升企业运营效率。
关键词:库存周转率;价值流图;实物流;信息流
0 引言
随着现代制造技术的发展,市场竞争的加剧,注塑行业目前已是微利行业,同时企业为了及时满足顾客的需要,通常保持较高的库存量,这占用了企业大量的生产经营成本,企业为了更好的面对市场的竞争压力需提高库存周转率。价值流是从原材料到产品过程中按次序组合的所有活动。按照是否对顾客产生价值,这些活动可以分为非增值活动和增值活动。它是帮助企业分析整个价值流的一个强有力的工具,它可以使整个价值流(通常是纷乱复杂的)变为一张可视的价值流现状图,使得价值流中的问题显现出来,这样就可以应用各种精益技术减少不增值的活动[1]。
目前注塑行业在生产中的非增值活动占总生产活动的95%左右,本文运用价值流图技术着重对注塑加工行业进行实例研究,探讨VSM技术在注塑加工生产过程中的应用。针对提高库存周转率的问题,通过材料流和信息流来绘制注塑加工的价值流现状图,从理论和实践相结合的层面对整个制造流程进行整体的分析,并在此基础上,运用IE技术和方法,对注塑加工中的实物流和信息流加以优化和改进。
1 VSM(Value Stream Mapping)技术简介
价值流是指产品通过其生产过程的全部活动。它包括从概念设计、产品设计、过程设计直到投产的设计流和从原材料、制造过程直到产品交到顾客手中的生产流[2]。它的主要目标是通过绘制企业当前价值流图,将企业流程所有相关的实物流和信息流以图示的方式加以表达,帮助我们分析发现运营流程中潜在的、非增值的浪费活动,并通过IE技术减少或消除非增值的活动,如:运用流程分析与改善、柔性生产、作业测定等技术与方法来提高效率和快速反应能力,降低成本,提升综合竞争力。
由于生成NH3·H2O而没有离开反应体系致使溶液呈现碱性,从而使CO2也很难从溶液中逸出,造成NH3·H2O和CO2并存于同一体系中,使水解反应不能进行彻底而很快达到平衡,反应进行的程度很小,为此两者可以大量共存,这一点与和Al3+的反应不同。
VSM技术开展的基本步骤:①收集数据,绘制现状价值流图;②从现状图中识别浪费,确定改善点并绘制未来价值流图;③针对改善点,制定改善计划并实施;④持续改善并标准化作业流程,推广至其它产品。
2 实例研究
M公司是一家以家用电器为主要产品的注塑加工企业,公司生产长期受到制造周期较长,库存周转较低等问题的影响。经现场调查和数据记录显示,2011年其产品制造周期约为20天,库存周转率为月平均0.68次。由于制造周期长,库存周转率低,造成了巨大的资金占用。本文以M公司从接受订单到交货给客户为止为整个研究过程,改善实物流和信息流,提高库存周转率,降低成本。
假如我是水,遇到海洋生物搁浅沙滩,我会召集附近的兄弟们一起来帮忙,把搁浅的海洋生物送回大海,还要护送它们回到自己的族群。
2.1 现状调查,绘制价值流图 M公司主要涉及注塑,喷涂,部件加工等工艺。改善小组以A产品为改善切入点,对A产品从M公司接受客户订单到出货至客户整个流程进行跟踪和记录,绘制现状价值流图,如图1所示。
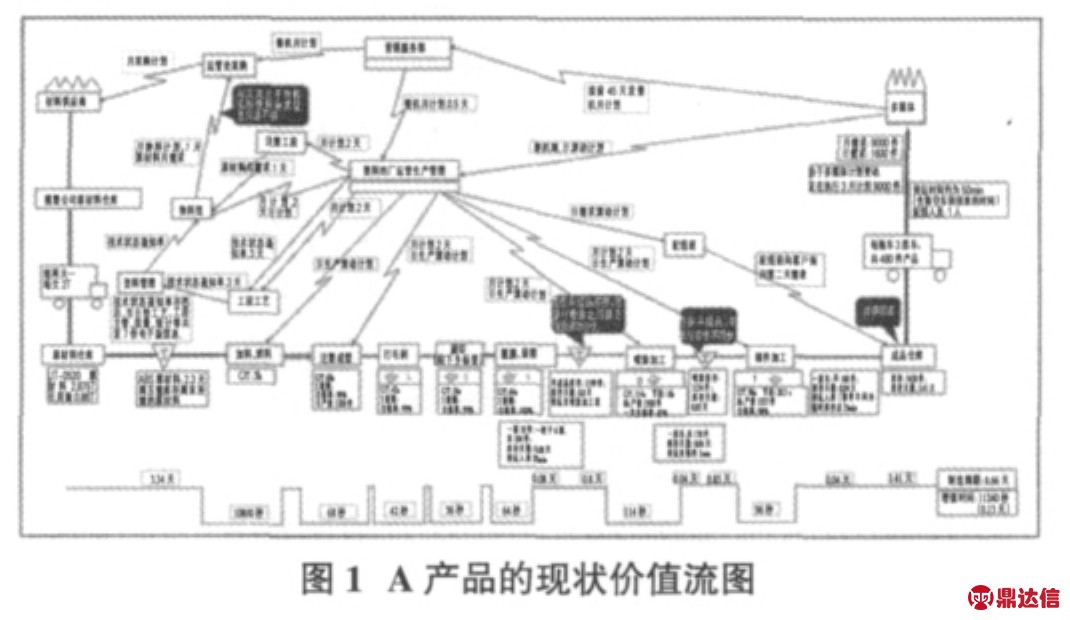
2.2 确定改善点并绘制未来价值流图 通过对现状价值流图分析,可知产品制造周期过长,约20天;原材料、半成品、成品库存较多,使库存周转率较低,据2011年数据显示,月库存周转率仅为:0.68(次/月),如表1所示。
对价值流图进一步分析,发现采购与物料计划之间信息传递不畅。因缺少物料使用的实时反馈,采购无法及时了解各生产厂实际物料使用情况,为避免断线,采购只有大量储备库存以防止缺料;其次,注塑、喷涂、部件加工各自形成孤岛作业,各工段只是生产产品而不考虑库存数量和交货时间,常常导致过量生产,库存积压;再加上各工段生产计划控制流程不规范,也无明确量化的控制指标,导致半成品及成品库存较高;最后,技术状态信息传递仍以纸张作业,速度较慢,大约需4天,拉长了制造周期,且每月需要耗用约600张纸张,形成浪费。综上所述,将以上几点列为改善点。绘制未来价值流图,如图2所示。
表1 2011年库存周转率(平均存货单位:万元)

月份 1 2 3 4 5 6 7 8 9 10 11 12平均存货周转率5787 0.74 5287 0.60 5652 0.56 6471 0.61 6757 0.70 6557 0.72 6293 0.69 6082 0.76 5869 0.68 5902 0.63 6532 0.70 7162 0.83
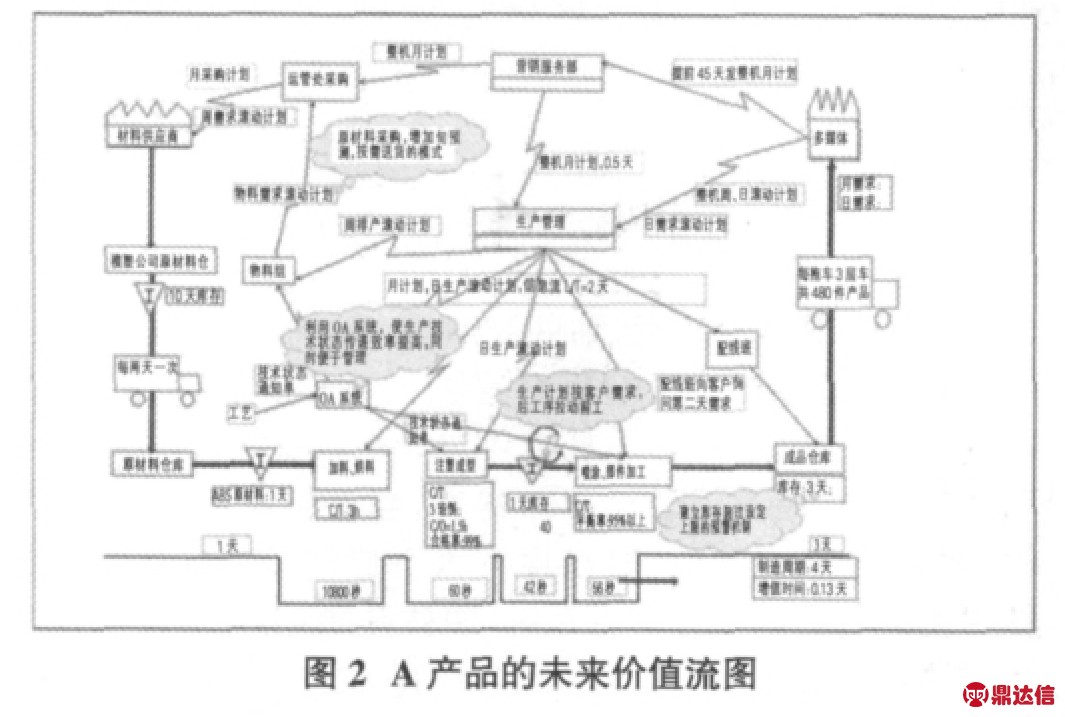
2.3 制定改善计划并实施 通过对M公司运营流程的调研,运用流程分析法、“5W1H”提问法、“ECRS”四大原则等方法及原理进行分析,并针对问题点进行了如下改善:
2.3.1 采购与物料计划人员信息传递改善:首先,编制《主要原材料交货周期信息表》,明确交货提前期,方便物料计划人员了解原料交货所需时间,有效防止断线;其次,制定《工程塑料控制管理办法》,进行权责划分,改善月需求计划传递流程,定制安全库存数量,增加旬滚动预测计划并传递至采购,采购以旬需求展开备料,如此使采购计划与生产计划匹配,防止原材料库存积压和产线断线;最后,通过月预测与实际用料对比,建立定期检讨机制,使各生产厂内原材料库存下降。
随着5G时代的来临,上网所需成本大大降低,同时网速大大增加。智能手机的硬件和软件都在不断更新升级,以此为基础,移动短视频的内容生产和消费就有了坚固的技术保证。
2.3.2 注塑、喷涂、部件过量生产改善:第一、采用拉动式生产方式,明确信息流传递流程。原流程是生产计划先给注塑,再由注塑传递给喷涂和部件,各工段几乎不考虑库存数量和库存天数,经常提前生产,应对客户计划变动的能力较低,导致库存较多。现采用拉动式生产方式,即生产计划先发给最末端的工段部件加工,部件根据自己的产能和交货时间计算出自己的交货提前期,以此推算出部件的原料需求时间,再将此时间发给前面的喷涂和注塑工段。各工段均根据自己的产能和交货时间推算出交货提前期,如此可有效避免提前生产,降低半成品库存和原材料库存。改善后各工段信息流传递如图3所示。
中国新生代欧美风儿童摄影师的杰出代表,对儿童摄影有独特而深刻的理解,作品风格多变,擅长简约、欧美、复古、唯美的摄影风格

第二,在可能的地方发展连续流:连续流的特点是在生产各工位间容易实现一个流生产,在制品的库存问题可以得到很好的控制[3]。A产品的整个制造流程为注塑成型后,在注塑工段完成打毛刺、覆膜,然后配送到后续工段进行喷涂加工和部件加工,再入成品库房,最后交与客户。现状实物流和信息流图如图4所示(实线为实物流,虚线为信息流)。
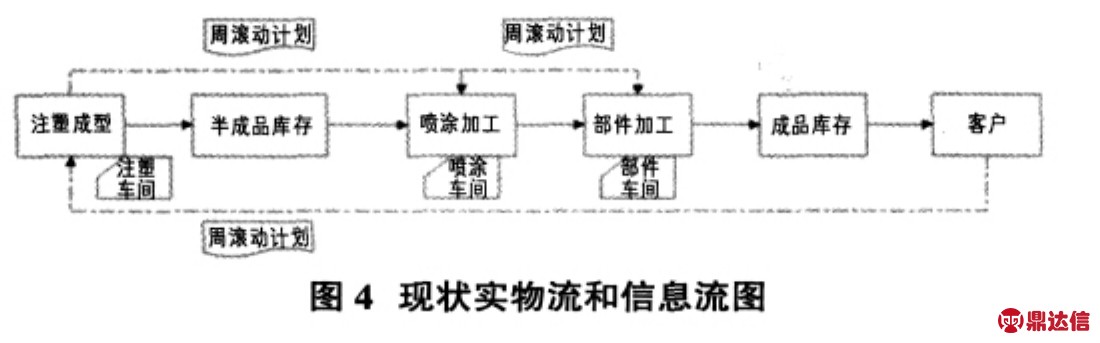
在不影响人均效率的前提下,根据各个工位的节拍将加工流程合并、重排,将部件加工前移至注塑车间,即注塑成型后的产品立即进行部件加工。改善后实物流和信息流如图5所示。
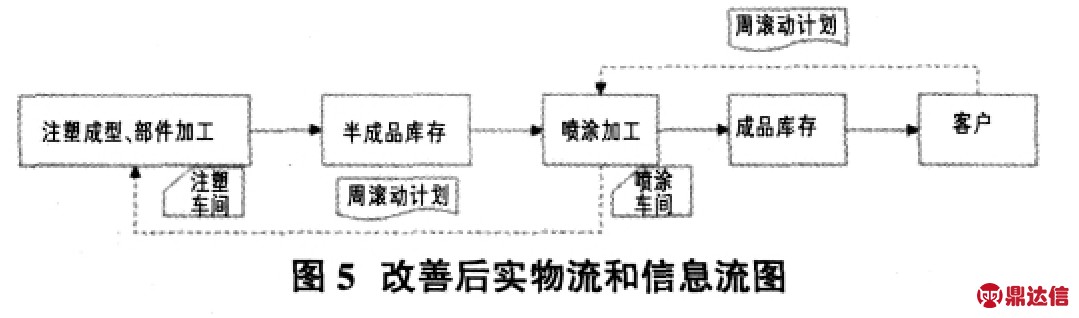
改善后,减少装箱和转运次数各一次,减少3个人力,提高了人均效率。方案的实施不会影响半成品的日产量,而成品的日产量略有下降,但其造成的负效益远远低于其他方面带来的正效益。改善前后对比如表2所示:
表2 改善前后数据对比
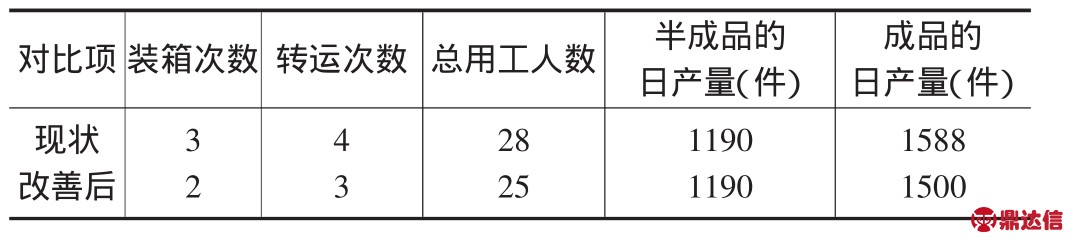
2.3.3 生产计划控制流程规范改善:编制《生产管理控制办法》,明确岗位职责,规范实物流和信息流传递流程,确定各工段生产提前期(或者前工段需完工日期)和库存上、下限公式,编制《库存分析报表》,明确超计划生产的数量。其中超计划生产数以生产技术状态中给出的后工序报废率(喷涂、部件和配送上线)作为参考,并在实际生产中,由生产计划人员根据《日清日结报表》中的实际报废数及时进行补充。《库存分析报表》格式如表3所示:
表3 库存分析报表格式
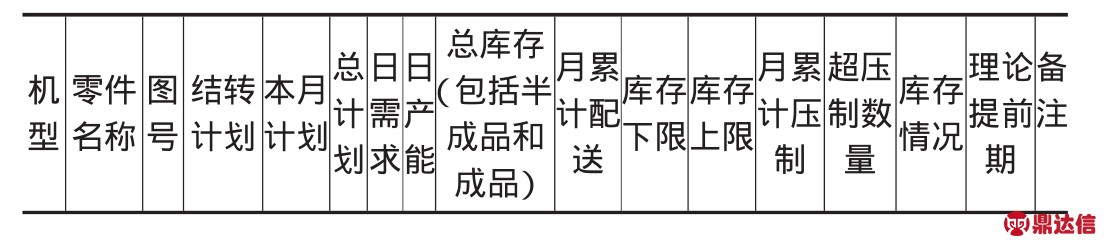
机型零件名称图号结转计划本月计划总计划日需求日产能总库存(包括半成品和成品)月累计配送库存下限库存上限月累计压制超压制数量库存情况理论提前期备注
2.3.4 技术状态传递信息改善:生产技术状态信息导入公司综合办公系统。工艺依要求填写技术状态,并在系统上记录各工艺完成时间。各需求部门在系统上查询相应技术状态资料,这样技术信息传递时间由4天变为1天,每月可节省约600张A4纸。
综合业务应用系统包括:防汛防旱智能决策支持系统、水资源信息管理系统、河道综合信息管理系统、排灌泵站信息管理系统、圩区排涝泵站集群管理系统、闸站自动控制管理系统、农业园区精准灌溉管理系统、局电子政务办公及移动政务系统。
2.4 持续改善并标准化作业流程,推广应用至其它产品 在个案改善的基础上,总结经验。通过PDCA(Plan,Do,Check,Action)循环对流程和表单进行持续改善,制定并实施《工程塑料控制管理办法》和《生产计划过程控制管理办法》等规范,编制和统一《原材料旬滚动预测报表》、《原材料月预测与实际需求统计表》、《主要原材料交货周期信息表》、《日清日结报表》、《生产技术状态信息表》、《成品及半成品库存分析表》等表单,并将其推广至公司其它大型系列产品。
3 结论
VSM(价值流图)技术的目的是提升整个公司的生产流程水平,进而提高库存周转率。本文通过对M公司从原材料采购到出货给客户整个运营流程进行分析,运用方法研究和时间研究来提高库存周转率。论文以流程改善为主线,技术改善为支撑,取得了很好的效果。后续工作将着手工程塑料预测和生产控制管理信息在PP/CO(Production Planning/Cost Object)系统上线,进而减少信息流传递时间,降低实物流库存,持续提升库存周转率。