摘 要:液压齿轮泵为液力自动变速器自动换挡系统和润滑冷却系统提供油液,是整机工作的保证,对其正确建模具有重要意义。以ZYBX4451型液力机械自动变速箱的设计为依托,该自动变速器内置一对外啮合液压齿轮泵,根据其结构特点、工作原理及性能特征,并通过对比分析普通外啮合齿轮泵和多齿轮泵的特性,搭建多齿轮泵的数学模型,对其进行流量特性分析。搭建试验台架,对齿轮泵性能进行试验研究,以验证理论分析的准确性。通过对比容积效率可知,所搭建数学模型的准确性,为此类变速箱齿轮泵的设计提供参考依据。
关键词:液力自动变速箱;齿轮泵;外啮合;容积效率;模型;试验
1 引言
液力自动变速箱作为汽车传动系统中重要的一环,起着改变发动机的输出扭矩以适应车辆行驶要求的重要机构。液压齿轮泵为液力自动变速器自动换挡系统和润滑冷却系统提供油液,是整机工作的保证[1]。液压齿轮泵维修操作方便、结构简单、占用空间小、质量轻等优点明显,所以它在液力自动变速箱及其他液压传动与控制技术中得到广泛应用。对液压齿轮泵进行建模分析,对其容积效率进行分析,使得齿轮泵能高效低耗工作,是研究人员重要的研究内容之一。文献[2]通过设计实验,测量了齿轮的端面间隙和齿轮泵的内侧板的油膜厚度。文献[3]针对齿轮泵的侧板及滑动轴承之间的润滑建立了二维雷诺方程并进行了研究,该流体类型为稳态不可压缩的流体。文献[4]对外啮合齿轮泵的相关试验、仿真以及数学建模,并对5种不同参数的齿轮泵进行了仿真分析和试验测试,并进行对比验证。
以ZYBX4451型液力机械自动变速箱的设计为依托,对其内置式齿轮泵进行结构分析和工作过程研究,根据外齿轮泵的工作原理,进行基本参数的确定,搭建其数学模型,分析其流量特性。搭建试验台架,用于液压泵的流量—压力特性、液压泵的流量—转速特性、液压泵的容积效率、液压泵的总效率。获取齿轮泵性能曲线图,对齿轮泵的性能进行评价分析,并对数学模型进行验证。
2 内置式齿轮泵结构
2.1 ZYBX4451型变速箱
“ZYBX4451”自动变速器主要由液力变矩器、缓速器、离合器、行星齿轮减速机构和液力控制系统组成。变速器二维图,如图1所示。该款变速器的最大优点是液压传动和行星齿轮变速机构。
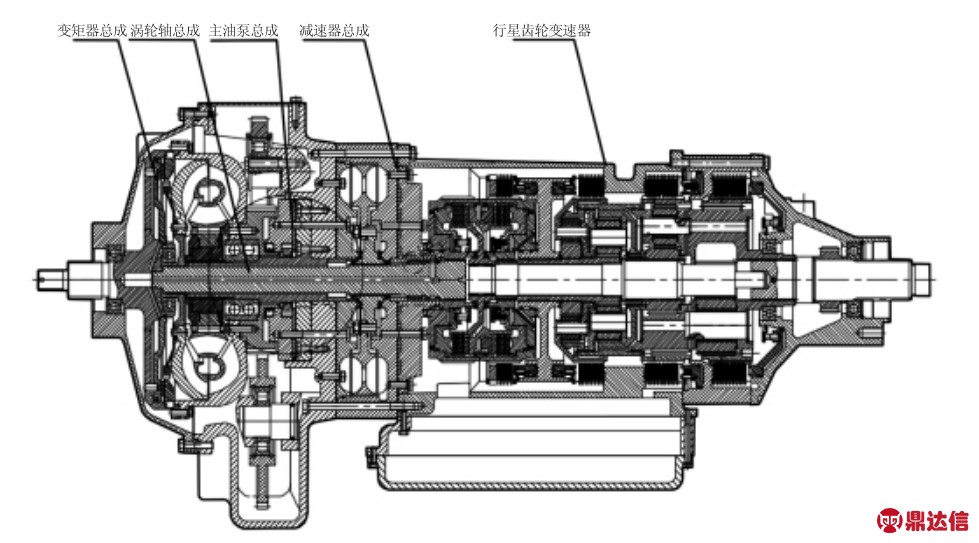
图1 液力机械自动变速箱三维模型
Fig.1 Hydraulic Automatic Transmission Three-Dimensional Model
2.2 齿轮泵结构组成
研究的齿轮泵为内置式齿轮泵,该款齿轮泵由主动齿轮和两个被动齿轮泵组成,该齿轮泵的结构,如图2所示。该齿轮泵盖上开有4个油口,2个进油口,2个出油口,在出油口处设置了卸荷槽。3个齿轮均是渐开线变位齿轮,保证了齿轮有较好的机械性能。大齿轮26个齿,小齿轮13个齿。变矩器泵轮旋转时,其后部轮毂驱动油泵主动齿轮,主动齿轮与被动齿轮总成啮合,当油泵工作时,油被吸进齿轮之间,将油液注入液压系统;回油泵用于带发动机驱动动力输出的变矩器,以便将动力输出机构的润滑油泵抽回油底壳[5]。
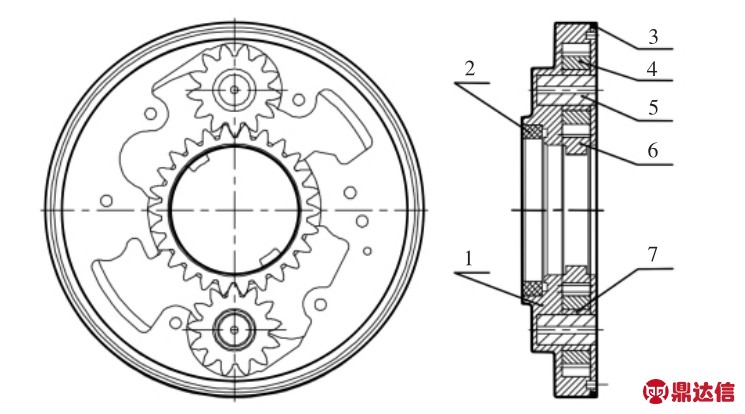
图2 齿轮泵
Fig.2 Gear Pump
1.齿轮泵壳体 2.3.密封圈 4.从动齿轮 5.从动齿轮轴 6.主动齿轮 7.轴承
3 齿轮泵数学模型
对于标准安装的外啮合齿轮泵的几何排量VB在理论上就等于直径为(z+2)m和(z-2)m的圆所围成的环形面积再乘以齿轮厚度B[6],即:

式中:m—齿轮模数,mm;Z—齿轮齿数;B—齿轮厚度,mm。
式中:dV—齿轮压油腔齿面扫过的容积;Ra—齿轮齿顶圆半径;Ra—齿轮瞬时啮合半径。

式中:N—从动轮数;z1—中心轮的齿数。
此处N取2,则其排量为上述的2倍,平均理论流量为:

式中:Z2—从动轮齿数;
n1—中心轮转速,r/min;
n2—从动轮转速,r/min。
其实际的输出流量QB为:

式中:ηv—多齿轮泵容积效率。
以上为对齿轮泵平均流量的分析,而对其影响最大的是泵的瞬时流量,直接对系统工作质量的好坏有重要影响。此值变化过大时,将会导致系统的压力脉动,造成单元平稳性下降,振动增加,产生气穴和气蚀,发出强烈的噪声,对系统产生破坏性影响[8]。对泵建模分析时,对瞬时流量特性进行分析,寻找脉动的主要因素,并作为建立数学模型的依据。齿轮泵工作示意图,如图3所示。

图3 齿轮泵工作示意图
Fig.3 Gear Pump Working Schematic Diagram
设主动齿轮1在dt时间内转过dφ1角度,相同时间被动齿轮2转过的为dφ2角度,由几何关系知:

式中:—齿轮的节圆半径;ω—齿轮的角速度。
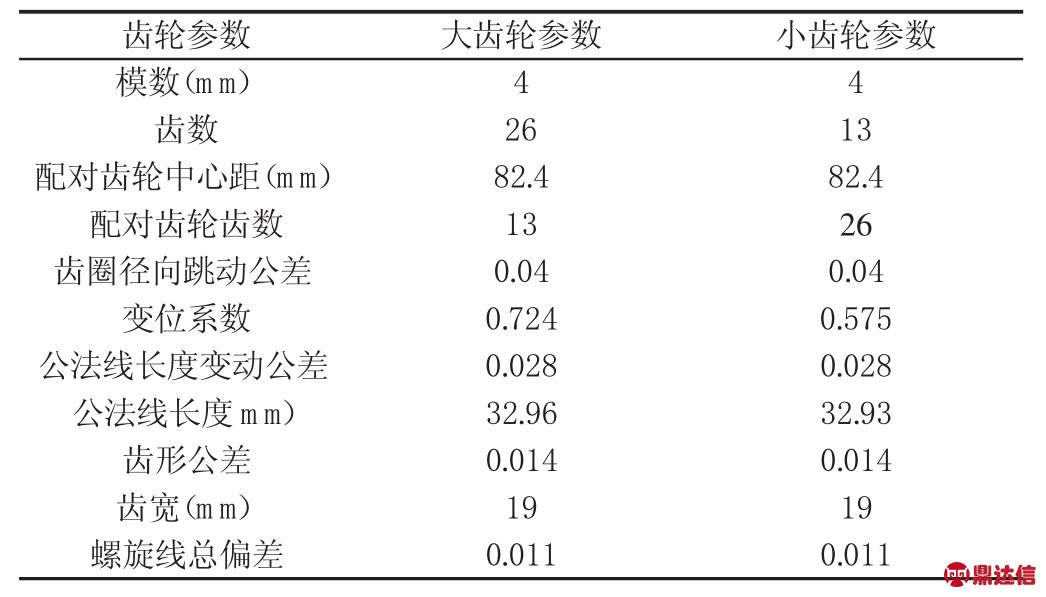
液压泵的容积效率:
则,压油腔排出的容积为:

故,压油腔排出的油液的瞬时流量:

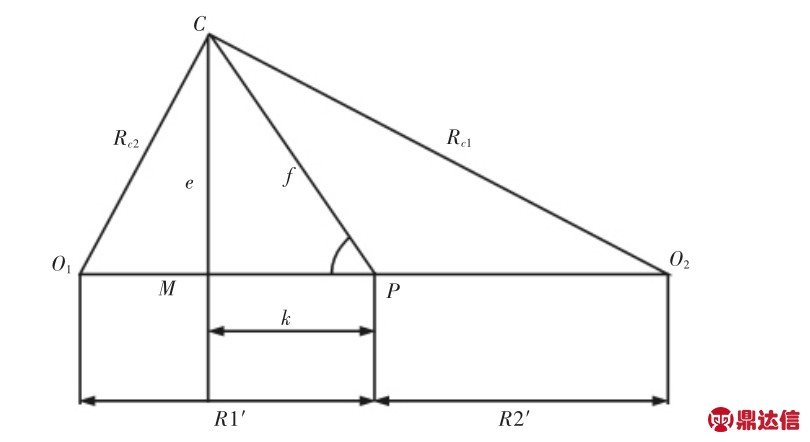
图4 啮合点与齿轮中心几何关系
Fig.4 Mesh Point and Center of Gear Geometry Relationship
在式(10)中,包含有Rc1、Rc2两自变量(未知量),如图4所示。C点为两啮合齿轮的啮合点;P点为齿廓接触点的公法线与连心线的交点,即节点;线段e代表啮合点C到齿轮的中心连线O1O2的垂直距离;线段k为啮合点C在齿轮的中心连线O1O2上到节点P的距离,通过几何关系得:

由几何关系可知:

由弧长公式、角速度公式可知:
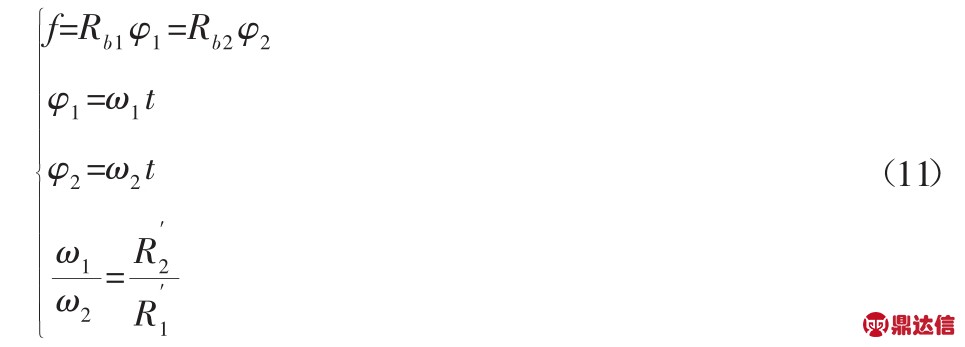
式中:Rb1、Rb2—主动轮、从动轮基圆半径;φ1、φ2—啮合点运动到节点的时刻,主从动轮转过的角度。
则瞬时流量为:

对于多齿轮泵,其几何排量为将中心轮旋转一周,其腔内密封工作容积的变化量[7]。多齿轮泵几何排量为:

式中:Qs—额定转速下的额定流量;Qk—额定转速下的空载流量;nk—空载转速;ns—实际转速。
液压泵的输入效率:

式中:M—在额定压力下,泵的输入扭矩;
n—在额定压力下,泵的转速。
液压泵的输出功率:

式中:P—在额定压力下,泵的输出压力;Q—在额定压力下,泵的流量。
液压泵的总效率为:

由以上分析可知,由于该齿轮泵是由两个外齿轮泵(子泵)构成,所以它的流量特性将取决于这两个齿轮泵的流量叠加。叠加后的瞬时流量特性与之前单个泵的特性基本相似,二者均呈现抛物线变化特性[9]。
所研究齿轮的相关参数,如表1所示。代入以上模型可得,泵的实际流量为117.95L/min,理论额定流量为148.9L/min,泵的额定容积效率为79.21%。
表1 齿轮泵参数列表
Tab.1 G ear Pum p Param et er Li st
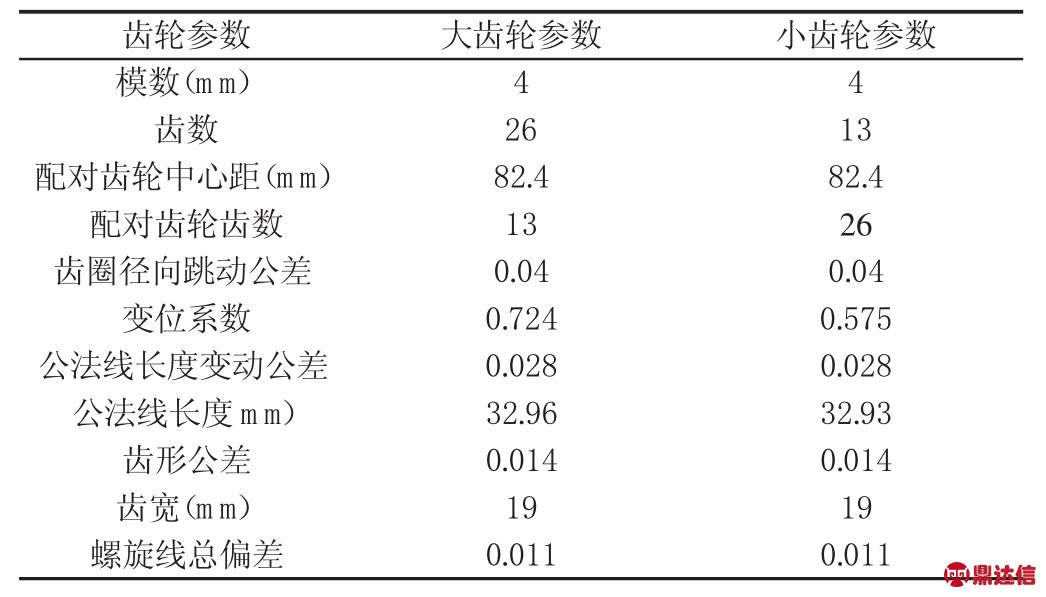
4 液压泵性能试验
4.1 性能试验台
本设计试验台的目的是用以测量齿轮容积效率。设计试验台,如图5所示。设计主要需要实验数据:液压泵的流量—压力特性、液压泵的流量—转速特性、液压泵的容积效率ηv、液压泵的总效率η。试验中采用节流阀调节作为液压泵不同负载。
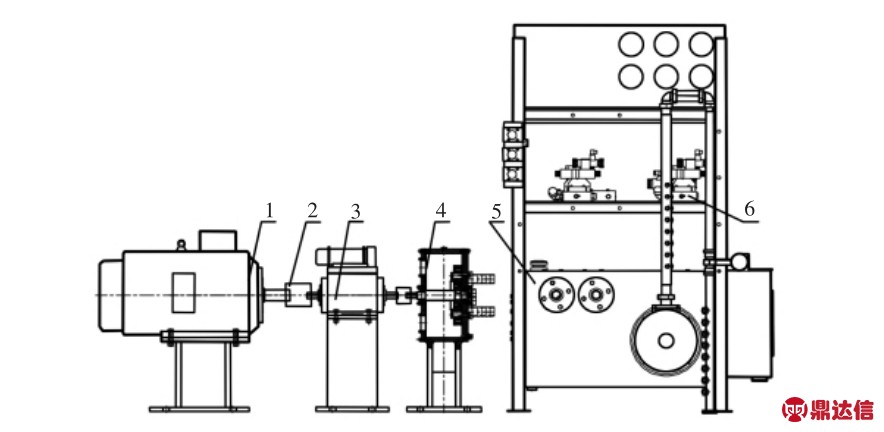
图5 台架试验整体布置图
Fig.5 Bench Test Plan As Whole
1.电动机 2.联轴器 3.扭矩传感器 4.齿轮泵外壳 5.油箱 6.阀块
试验采用用流量计测量流量;采用扭矩传感器测量;采用变频器测量转速。实验测得的是齿轮泵两个子泵的相关性能数据,齿轮泵整体性能数据需要加和处理[10]。
4.2 试验内容
(1)启动液压泵,关闭节流阀,将溢流阀的压力调至高于齿轮泵的额定压力的10%,安全阀压力5MPa。固定电动机转速n=1500(r/min)然后调节节流阀的开度,作为泵的不同负载(1MPa、1.2MPa、1.5MPa、2MPa、2.5MPa、3MPa、4MPa、5MPa),测出齿轮泵压力、流量及扭矩。
(2)启动液压泵,关闭节流阀,将溢流阀的压力调至高于泵额定压力的10%,安全阀压力5MPa。然后固定节流阀的开度,使齿轮泵的工作压力为2MPa。通过变频器调整电动机的转速,以控制泵达到不同的转速(600r/min、800r/min、1000r/min、1200r/min、1400r/min、1600r/min、1800r/min),对应测出转速、流量Q和扭矩M。
4.3 试验结果处理
液压齿轮泵性能参数,如表2、表3所示。曲线,如图6、图7所示。
表2 转速一定时的数据
Tab.2 D at a w i t h Speed Fi xed
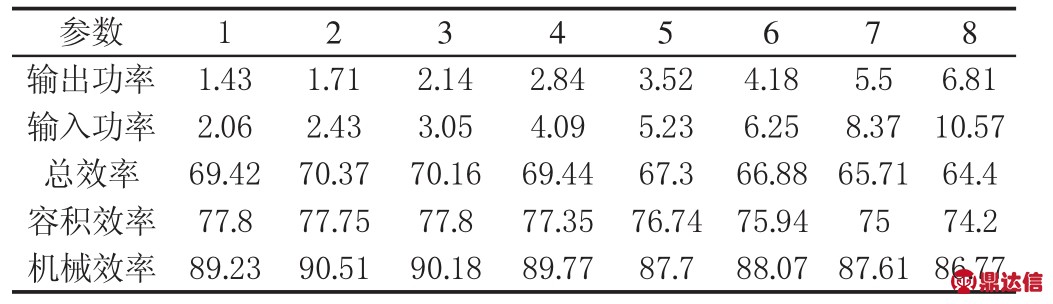

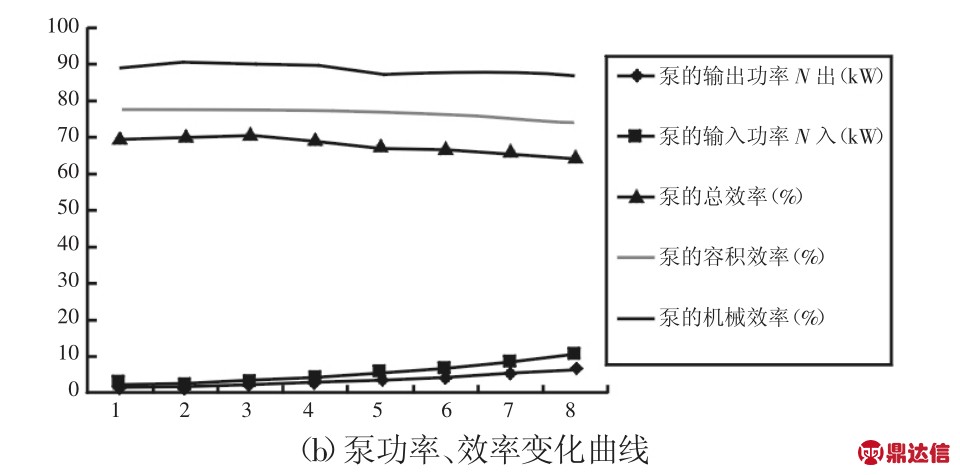
图6 随压力变化曲线(1500r/min)
Fig.6 Changing with Pressure Curve(1500r/min)
由表2和图6可知:在定转速下,齿轮泵的流量随着压力的增大而有小幅减小;而泵的输入扭矩却随着齿轮泵压力的增大而大幅增大;液压泵的容积效率随着泵的工作压力的升高而降低,这是因为:泵体为高速旋转零件,为保证其正常工作,在旋转体与非旋转体的接触面之间,如齿轮的外径、端面等与泵体、端盖等之间,必须有一定的间隙留存,这将导致,部分高压油液会经过通过之间的间隙,循环流回到低压区,由于结构间隙不可避免,因此,此部分压力损失也不可避免。随着油泵压力的升高,齿轮泵内泄漏增大,泵的出口流量就会降低,所以也将导致容积效率的降低。
表3 压力一定时的数据
Tab.3 D at a w i t h Speed Fi xed
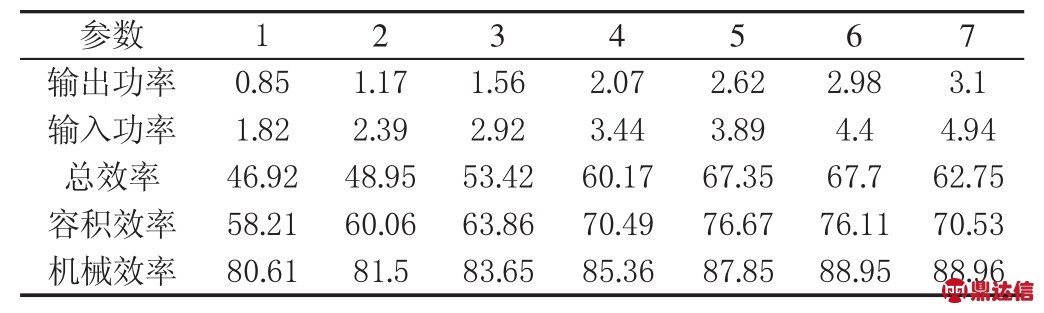
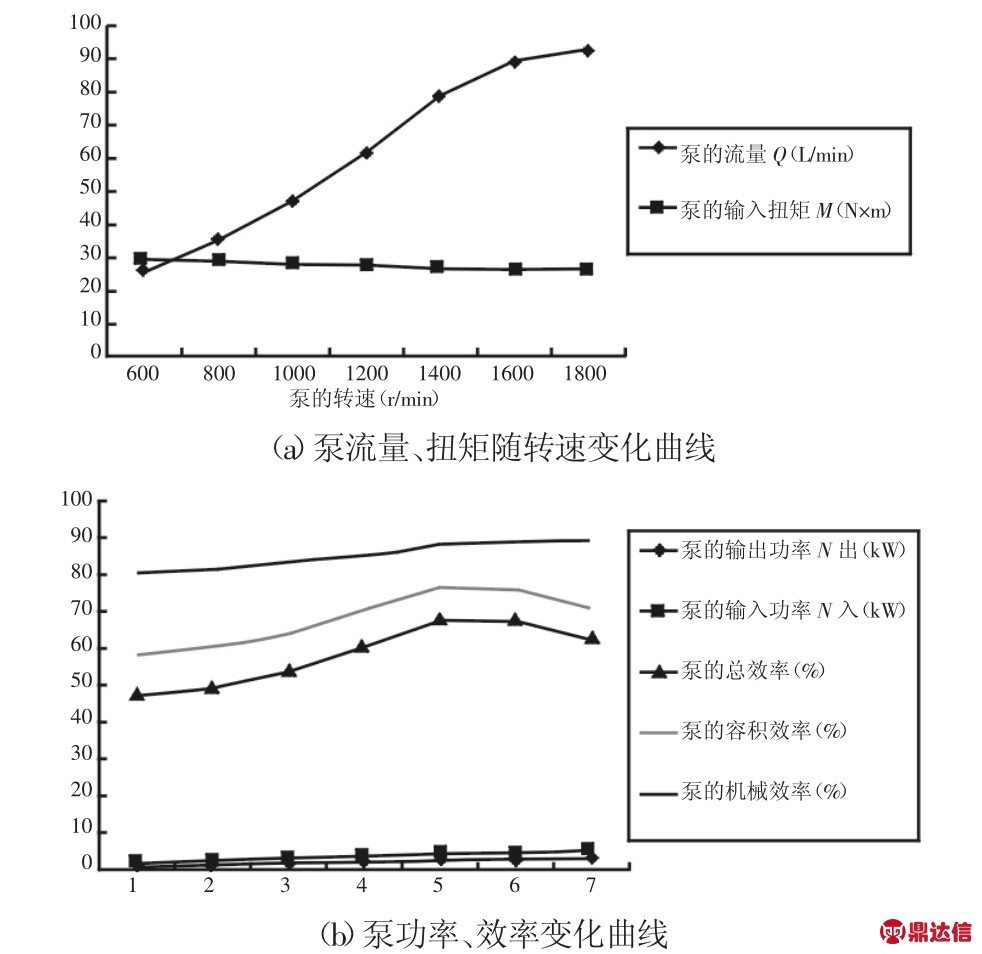
图7 随转速变化曲线(2MPa)
Fig.7 Changing with Speed Curve(2MPa)
由表3和图7可知:压力一定的条件下,齿轮泵容积效率先随着转速的升高而升高,但当齿轮泵的转速继续上升时,容积效率却降低了,主要原因是:外啮合齿轮泵的结构特点造成泵在高速运转时,液压油产生的离心力使其无法完全将泵体内齿槽的最大容积充满,在此情况下,将会造成外啮合齿轮泵的容积效率出现下降。随着工作转速的升高,将会在泵体内造成气蚀,从而使得泵体供油不足,流量浮动变化增大,噪声增加等。
由表2和表3数据对比及与数学模型求解对比可知,该齿轮泵的容积效率、齿轮泵总效率、机械效率相对较高,与理论分析结果及变化趋势基本相似,从而验证了数学模型的准确性与可靠性。
5 结论
根据液力自动变速箱内置齿轮泵的结构特点、工作原理及性能特征,建立多齿轮泵的数学分析模型,对其进行流量特性分析。该类泵由两个子泵有机构成,其吸、出油口相对泵体的中心线对称布置,因此,其中心轮径向液压力平衡;其流量为子系统叠加。基于数学模型,对多齿轮泵进行了流量、效率以及参数计算。在数学模型的基础上搭建了该多齿轮泵的试验台架。通过试验测量泵轮的工作压力、流量、转速、转矩等数据,对比泵轮的功率、总效率容积效率等,验证了数学模型的准确性和可靠性,为同类研究提供参考依据。