摘要:各主机厂在价格和行业竞争如此激烈的环境下,不仅对产品零件价格进行压缩,同时又对汽车内饰件品质有了更高的要求,汽车内饰件供应商迫切需要寻求新工艺或新技术来改变目前的困境。在这种环境下,笔者所在的公司从欧洲将最新气体辅助注塑工艺引入到汽车内饰件的车门拉手行业中。本文主要介绍气体辅助注塑工艺,以便帮助同行尽快了解和熟悉此种工艺,通过有效运用新工艺,使产品品质得到保证和工艺的推广,为公司和自己取得“双赢”。
关键词:气辅注塑,高压惰性气体,熔体,半射,满射回杆
0 引言
20世纪80年代,复杂的汽车注塑件(如汽车保险杠、仪表板、车门板、杂物箱甚至整个车身)因产品本身结构问题,制品壁太厚,加上塑料原料固有的收缩特性,总会在表面产生缩影和流痕等一系列问题,困挠着各大汽车厂商。本文具体介绍了气体辅助注塑成型工艺在汽车顶棚拉手中的应用,以及有效的问题解决方案。
青萝向来对自己的容貌自信,但当看到女子的那张脸时,仍不免惊叹世间竟有如此美人!她看起来比自己年长不了几岁,也就十七八岁的模样,肤色白皙,面容姣好灵透,带着一种不食人间烟火的纯净和圣洁。她的身体纵然沾染了血污,她的衣服纵然残破不堪,却也丝毫不能影响到她的圣洁和美好。
目前顶棚拉手本体的生产注塑工艺主要有以下4种,分别为普通注塑、普通注塑和组装、气体辅助注塑工艺以及微孔发泡注塑工艺。具体特征和使用情况如图1所示。本文主要具体介绍气体辅助注塑成型工艺,其由2部分构成,塑料熔体注射(传统注塑)和气体(一般采用氮气)注射成型。
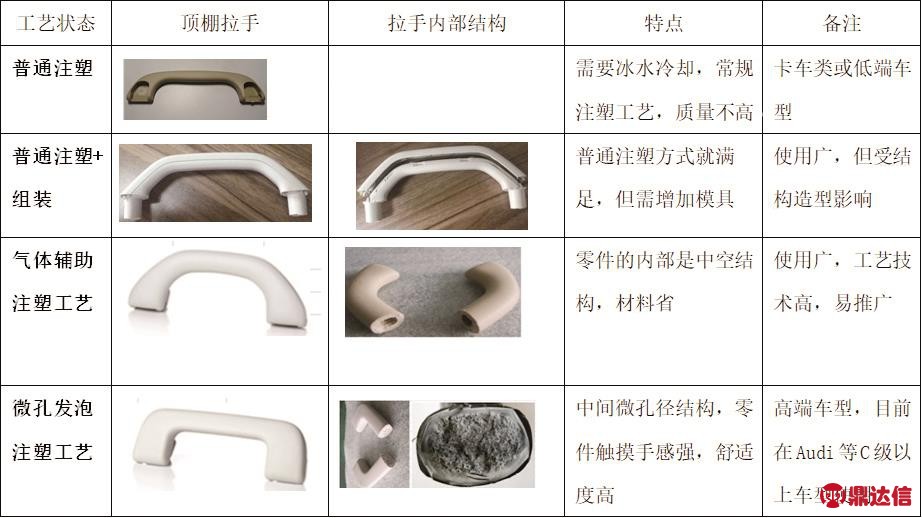
图1 目前注塑工艺的4种类型
1 气体辅助注塑成型的原理
气体辅助注射成型技术是利用高压惰性气体(一般采用氮气)在注塑件内部产生中空截面,并推动熔体完成充填过程,实现气体均匀保压,或者利用气体直接实现制件局部高压保压,消除制品成型缺陷的一项九十年代才开始进入实用阶段的塑料成型新技术。
气体辅助注射成型过程首先是向模具型腔内进行树脂的欠料注射,然后再把经过高压压缩的氮气导入熔融物料当中,气体沿着阻力最小方向流向制品的低压和易流动的高温区域。当气体在制品中流动时,它通过置换熔融物料而掏空厚壁截面。这些置换出来的物料充填制品的其余部分(如产品设计上的溢料槽)。
掘进机空间位姿监测主要监测掘进机截割头和机身空间位姿,构建的多传感器信息的煤矿悬臂式掘进机空间位姿监测系统方案如图1所示,系统主要由传感器检测系统、机载信号处理器和掘进机空间位姿监测上位软件3大部分组成,系统各个部分组成及功能如下:
2 气体辅助注塑工艺成型的方式
目前气体辅助注塑工艺主要有4种类型,分别为欠料注塑、满料注塑、回流到螺杆和带有往复式型芯的模具。因产品构造问题,本文只对前面3种工艺进行结合优化设计,并分别取名为半射和满射回杆(表1)。半射出气辅注塑成型过程如图2所示。满射出气辅注塑成型过程如图3所示。
表1 目前主要的2种气体辅助注塑工艺
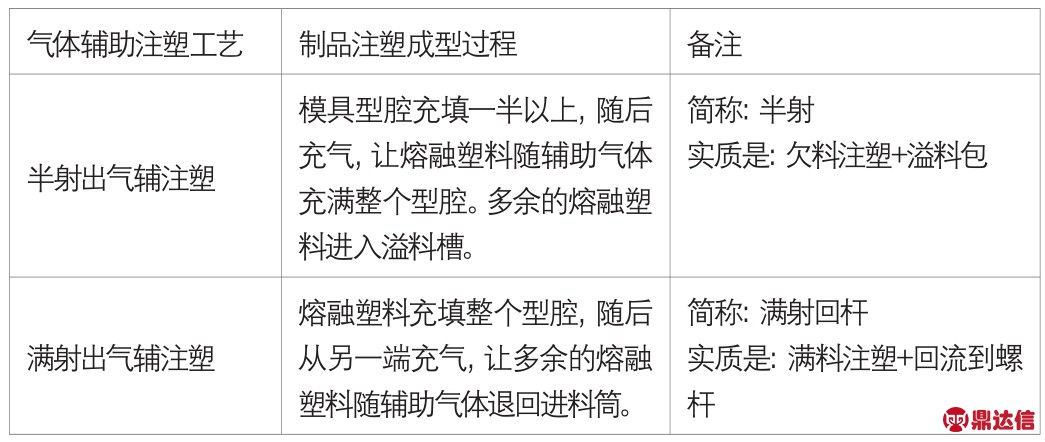
气体辅助注塑工艺 制品注塑成型过程 备注半射出气辅注塑模具型腔充填一半以上,随后充气,让熔融塑料随辅助气体充满整个型腔。多余的熔融塑料进入溢料槽。简称:半射实质是:欠料注塑+溢料包满射出气辅注塑熔融塑料充填整个型腔,随后从另一端充气,让多余的熔融塑料随辅助气体退回进料筒。简称:满射回杆实质是:满料注塑+回流到螺杆
3 气体辅助注塑成型的优点
气体辅助注塑成型工艺的优点是可以有效减少表面缩影,节省原材料的使用,增强尺寸稳定性,增加强度。而其他的优点还包括:低的注射压力使合模力要求降低,可以使用小吨位的机台;低的注射压力可以减少或消除制品飞边出现;成型周期缩短;降低了模腔内的压力,使模具的损耗减少,提高其工作寿命;减少射入点,气道可以取代热流道系统从而使模具成本降低[1]。
4 气体辅助注塑成型工艺模具设计要点
气体辅助注塑成型工艺模具在进行设计时,需要注意以下几方面:应选用流动性较好的塑胶,方便吹气时塑胶的流动;浇口应尽量选在产品的端部;半射出注塑成型方式吹气口,应选在靠近浇口的地方;如是一模多件,必须保证一件一条进气孔设计;吹气口必须在模具的下方,以防止因重力作用胶料堆积于模具下方,而造成胶厚不均匀;气辅模要求模温较高,一般都采用热流道,以及在动定模镶件时用热油加热,如果产品太长,还需要在动定模镶件时添加发热棒进行加热;气辅模流道和溢料槽的形状一般做成梯形。
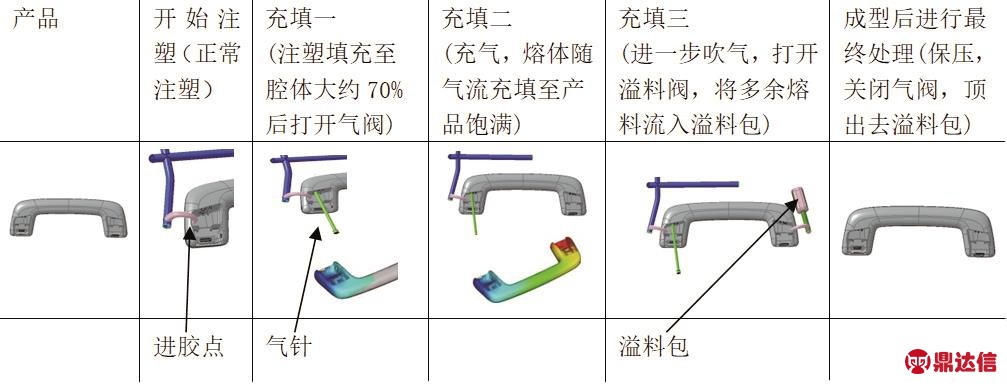
图2 半射出气辅注塑成型过程
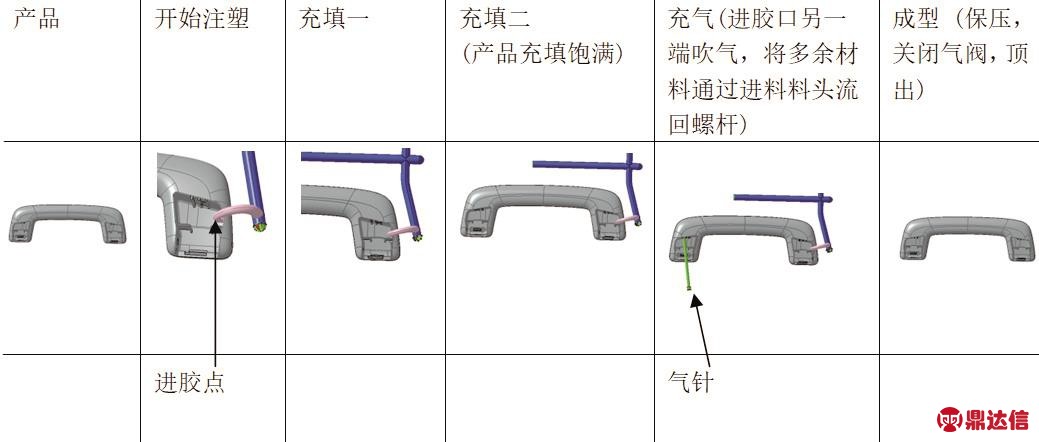
图3 满射出气辅注塑成型过程
5 部分案例的问题探讨
5.1 熔接线/痕
熔接线/痕是注塑成型(原理)工艺形成的溶接痕。其形成的原因是,由于进料端的温度可以保持不变,但是另一端以及早期进入的塑料,因温差问题出现冷却,导致不能充分与新进入的塑料进行有效混合,从而引起熔接线/痕。目前对于熔接线/痕,只能尽量缩少而不能完全消去(图4)。
此类问题可以通过以下方案进行改善:进料口位置偏移,让熔接线/痕转移非外观面内;通过提高模具型腔温度,使熔接线/痕偏淡、偏浅,改善目视效果;模具气辅方式调整,通过一端进料,另一端有溢料包方式,外观会相对改善,但损耗大;通过一侧进料,另一侧吹气,让多余的料反流到注塑机喷嘴,无损耗,但熔接线/痕也只能协助改善。
5.2 颜色/光泽
熔接线/痕工艺的问题,会导致拉手零件两端的颜色和光泽存在差异,建议通过以下方式进行改善。
我国奥数成绩举世第一,但是科学创造力却乏善可陈,研究表明,中美学生的差距不在于数学能力,而在于数学学习的方法,繁重的考试和复杂的题海战术让中国学生丧失了学习的兴趣,正如哈佛大学校徽所写,我们要有追求真理的热情。数学教育最怕的就是追求不必要的复杂性,创造脱离实际的问题,一味翻新花样为了难倒学生,这不符合高职学生的特点。同时,高数教学的另一个重大障碍,是缺乏数学的历史知识,没有数学文化和历史教育,学生就不能深刻理解数学的应用环境和时代背景。
(1)在工艺锁定情况下,通过零件的颜色的状态来定义来料色板的颜色,再推导塑料粒子的颜色状态。此方式要通过零件本身两端的平均颜色状态进行,即存在一侧颜色上差,另一侧颜色下差,通过平均值来弥补颜色状态满足。
1.加工产业链不完善,存在浪费现象。产业链不完善主要是指加工过程没有开发完全,与副产品间的联系有所缺乏,大部分的普通加工仅仅是针对小麦个体而言,并没有将它的所有价值尽可能的开发出来,由此造成了产业链不完全和浪费的发生。这种浪费既是经济上的浪费,也是资源上的浪费。所谓经济上的浪费,一方面是指传统的加工方式中需要损耗的成本过多,出现了一定的损失,另一方面则是指未开发完全价值中蕴含着那部分副产品有可能产生出的经济效益[1]。而资源上的浪费,则是指小麦资源未被开发完全的浪费,也是指部分小麦加工失败或者因受到加工技术的限制而未取得应有质量的浪费。
(2)零件皮纹有2种,分别为皮纹腐蚀和脉冲皮纹状态。建议通过脉冲皮纹来加工,其可以保证模具型腔材料的硬度,起放电加工方式会使模具型腔硬度在原基础上进一步提升,同时对颜色和光泽状态的稳定使用也有保证。如果使用皮纹腐蚀,其模具材料硬度不如脉冲皮纹,而且要不断进行消光调整,会模具重复拆卸,对模具装配精度影响大。
(3)通过对原材料本身的光泽控制。
5.3 其他方面的运用
在汽车配件方面使用气辅注塑方式,除了在顶棚拉手结构运用广泛,同时在部分零件上也可以通过气辅结构方式,来改善或解决部分零件本身设计问题引起的臂厚缩影问题。在零件臂厚位置增加气辅工艺的气针,利用在注塑过程中增加吹气来解决臂厚造成的缩影,有效降低零件成型要求工艺,比如门内拉手等。与普通的注塑成型相比,气体辅助注塑技术还有很多无可比拟的优点,它不仅仅可以降低塑料制品的制造成本,还可以提高零件本身的强度等性能。
该功能记录机械部件各种临界状态的参数。这些数据记录用于确定机械部件和液体的情况或状态,并提供其退化或故障之前的警告。
6 结束语
国外从上世纪90年代起,将气辅技术陆续应用于汽车、彩电、飞机及日用品等诸多领域。目前,美国和日本的汽车注塑件,已有80%采用气辅注塑成型,日本电视机行业64 cm以上的大屏幕彩电机壳,90%以上采用气辅注塑成型。然而此技术在我国起步较晚,基础较差,但放眼未来,该技术在注塑行业中的应用必将越来越广泛,有急迫的市场需求与重要的技术经济意义。
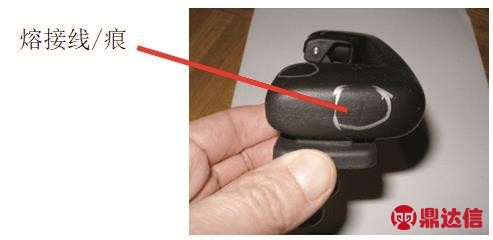
图4 熔接线痕