摘要:为了验证高清漏磁内检测技术对焊缝处裂纹型缺陷检测能力,对西气东输二线一处裂纹型缺陷管进行了牵拉试验研究。牵拉试验结果表明:在4 m/s牵拉速度内,裂纹型缺陷信号特征明显,数据分析时可进行缺陷特征识别。在4.61 m/s最大牵拉速度下,缺陷特征信号幅值最大衰减达77%,缺陷特征仍存在,但因信号平缓,识别较困难。对利用高清漏磁内检测技术检测焊缝缺陷进行了展望。
关键词:高清漏磁内检测器;螺旋焊缝;裂纹型缺陷;牵拉试验
0 引言
高清轴向漏磁内检测技术是目前国内采用的主流内检测技术[1-6]。SY/T6889-2012《管道内检测》[7]标准将轴向漏磁内检测技术定义为一种金属损失类缺陷检测技术,其主要检测管道金属损失,同时还可以检出环焊缝异常、狭窄的轴向外腐蚀及周向裂纹等裂纹型缺陷。
随着西气东输一线、二线、三线等高钢级、大口径、高压力输气管道投产运行,已发生多起焊缝失效案例[8-9]。内检测服务商漏磁内检测报告中焊缝异常缺陷的比例也在逐步升高,现有的漏磁内检测技术对焊缝缺陷、裂纹型缺陷的定性及尺寸量化尚不成熟。本文对现场发现的一处螺旋焊缝裂纹型缺陷进行了高清漏磁内检测器牵拉试验,对信号特征进行了分析,对检测器检测该类型缺陷能力进行了验证。
1 案例介绍
2015年5月20日至23日,中石油管道有限责任公司西部分公司对西气东输二线某处经内检测识别出的螺旋焊缝异常点进行开挖验证时,射线及TOFD超声检测结果表明该处存在裂纹型缺陷,缺陷位于顺气流9点20分部位,裂纹长度55 mm,裂纹自身高度无法确定。射线及TOFD超声无损检测结果见图1。
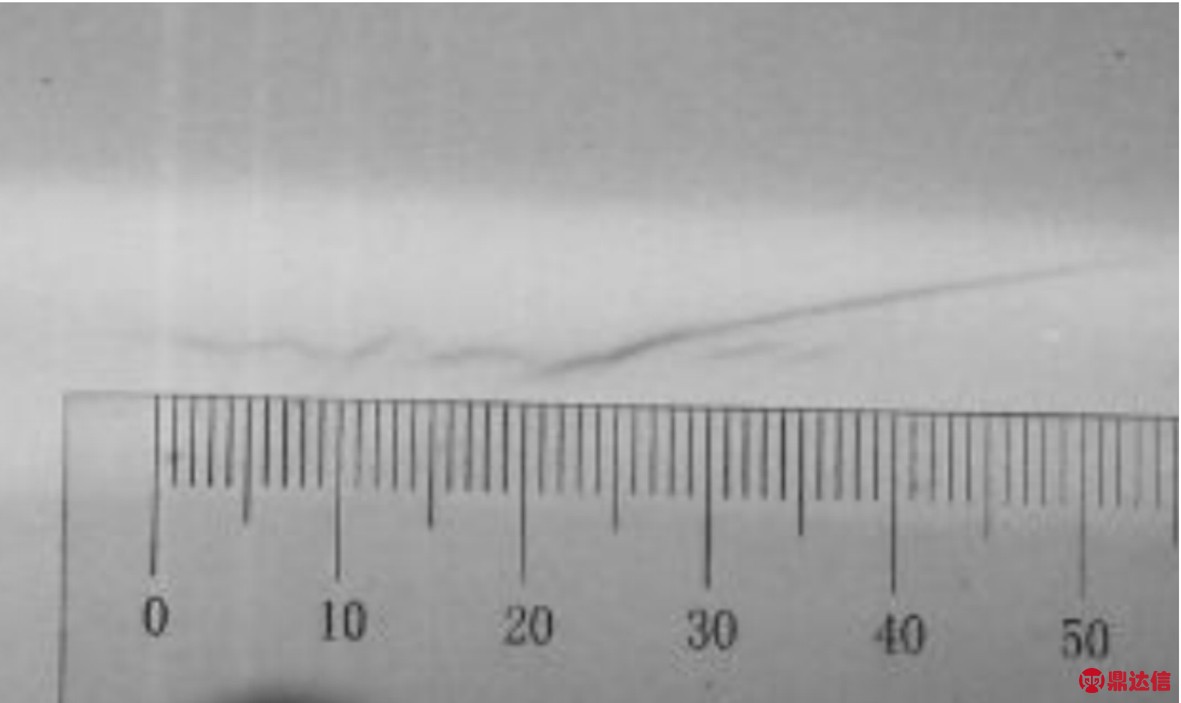
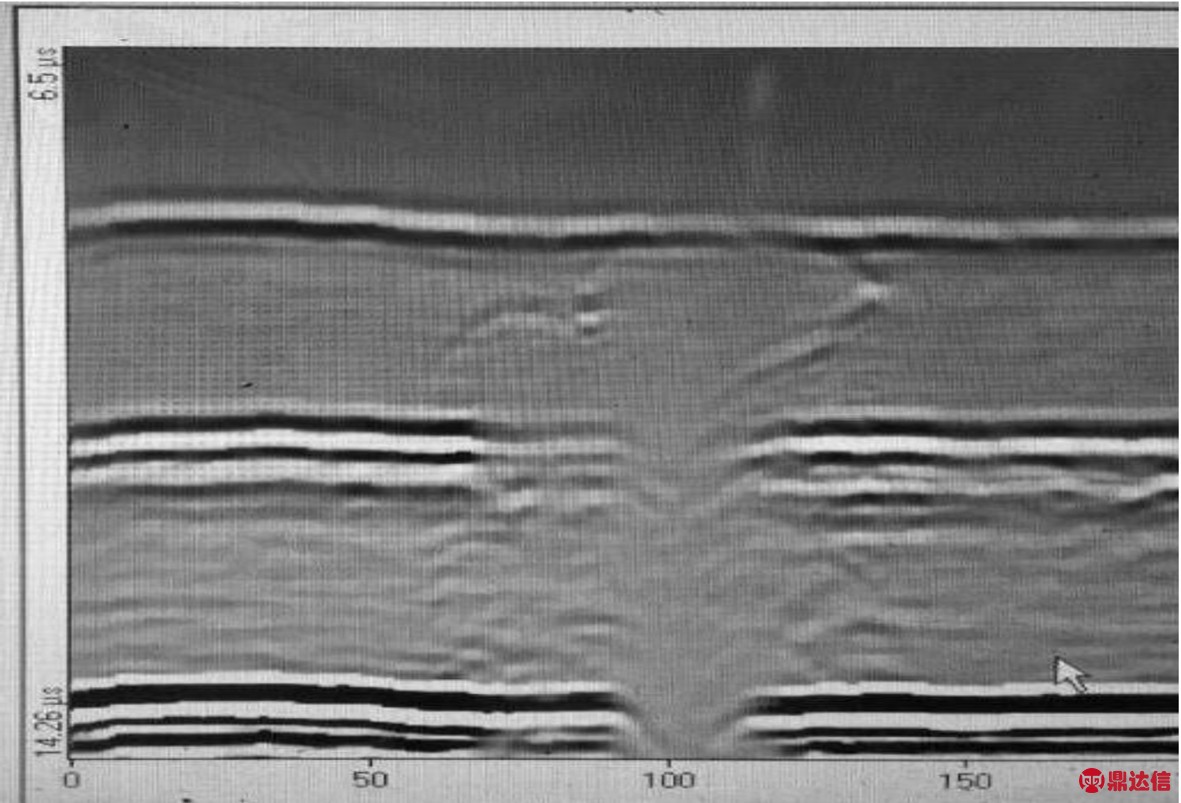
图1 射线及TOFD超声无损检测结果
发现该螺旋焊缝裂纹型缺陷的设备为Φ1219高清漏磁内检测器,其技术指标符合NACE International Publication 35100《In-Line Nondestructive Inspection of Pipelines》高清漏磁内检测器标准要求。高清漏磁内检测器实物图见图2。
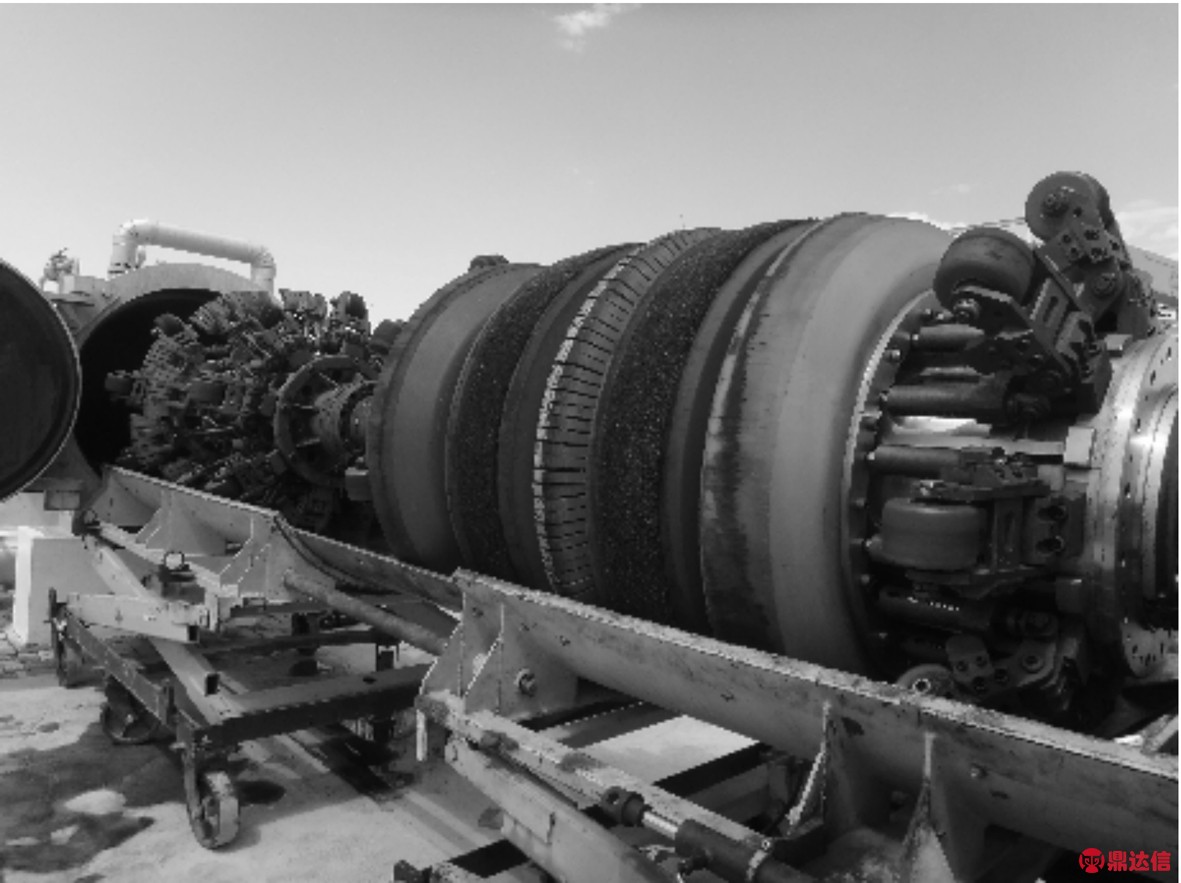
图2 高清漏磁内检测器实物图
2 牵拉试验设计
2.1 工艺设计
该牵拉系统工艺采用2台工程车通过牵引钢丝绳牵拉内检测器通过试验管道的方式。牵拉测试工艺流程图见图3。
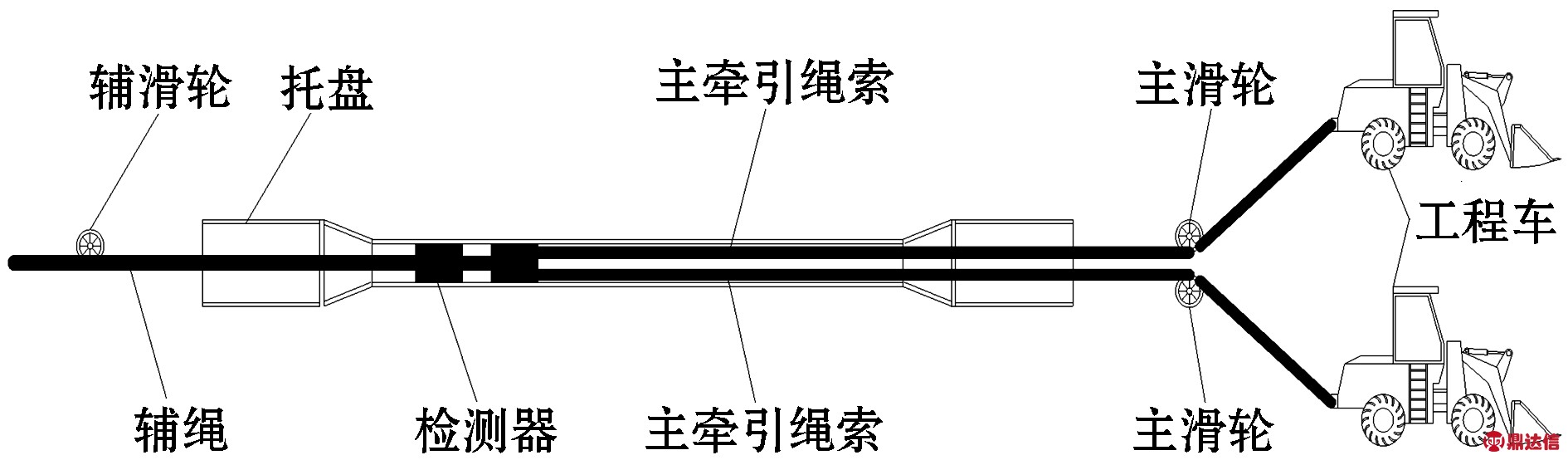
图3 牵拉测试工艺流程图
2.2 试验管道设计
牵拉试验管道由7根钢管组成,口径均为1 219 mm。漏磁内检测器质量为4.2 t,为了进行该螺旋焊缝裂纹型缺陷不同速度下缺陷特征研究,根据现场试验,布置试验管道如下:前5根为加速段,第6根为缺陷管,最后一根为减速段。试验管道设计图见图4。
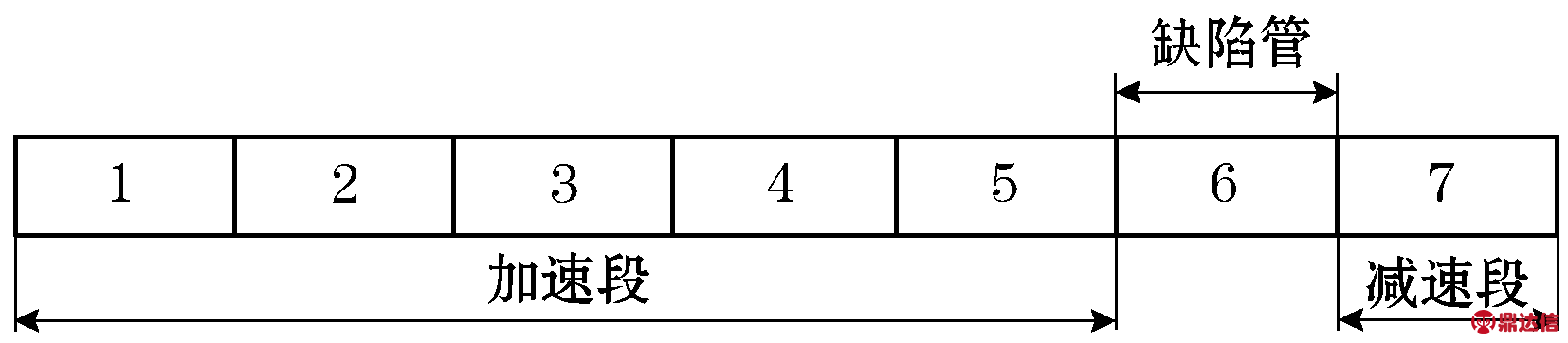
(a)设计示意图
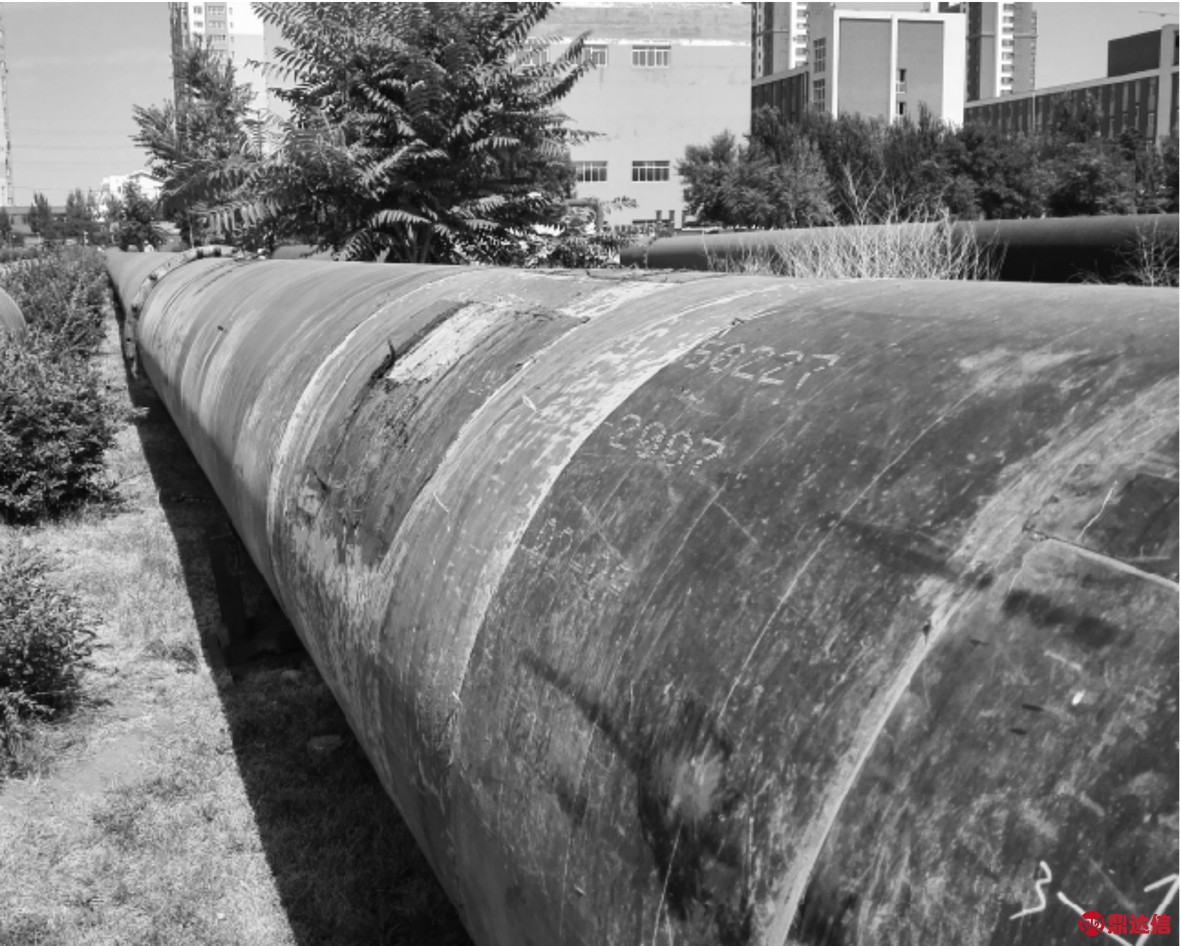
(b)设计实物图
图4 试验管道设计图
由于漏磁内检测器前节磁化节采用高磁能磁铁,对管壁吸附力强,经现场试验,1根钢管能满足最高牵拉速度下减速要求。缺陷管通过法兰及螺栓与上下游管节连接,其余管节焊接连接。
3 牵拉试验
3.1 试验结果
2016年7月20日至24日,采用工程车及Φ1219高清漏磁内检测器完成该螺旋焊缝缺陷一次牵拉试验。工程车为龙工50D装载机,额定功率162 kW。此次试验共牵拉8次,最高牵拉速度4.17 m/s。2016年8月4日,在拆除漏磁内检测器皮碗等附件给内检测器减重后,完成二次牵拉试验,最高牵拉速度4.61 m/s。表1为现场内检测及牵拉试验结果。
表1 现场内检测及牵拉试验结果
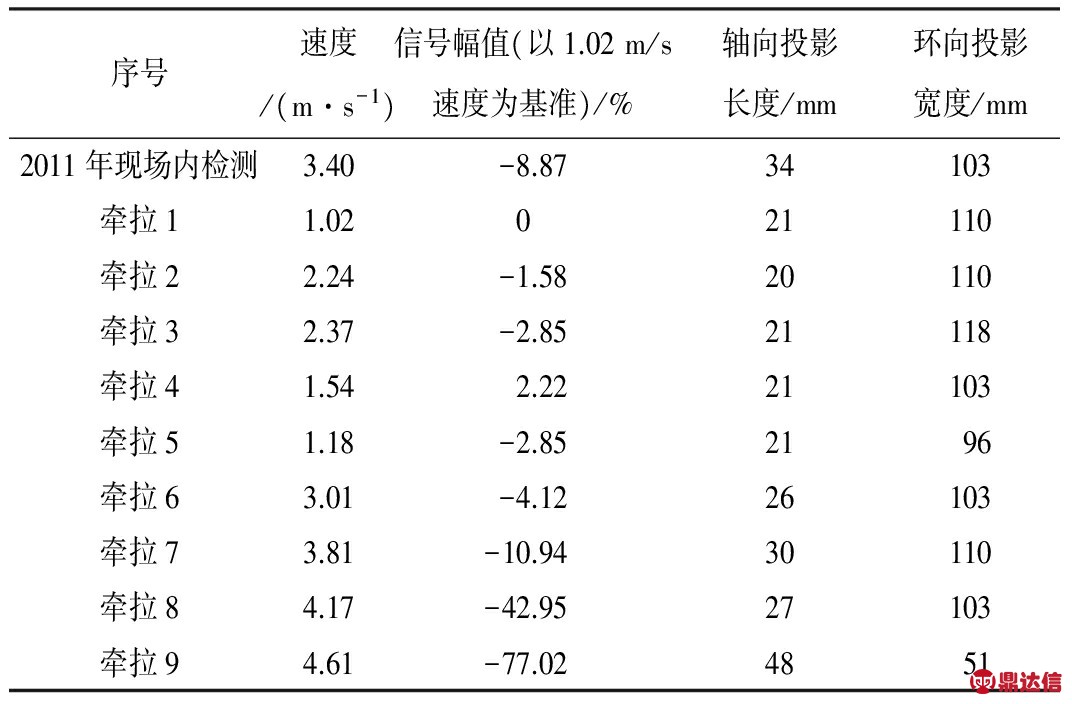
现场内检测及部分牵拉试验内检测信号图见图5,图中方框处为缺陷位置。
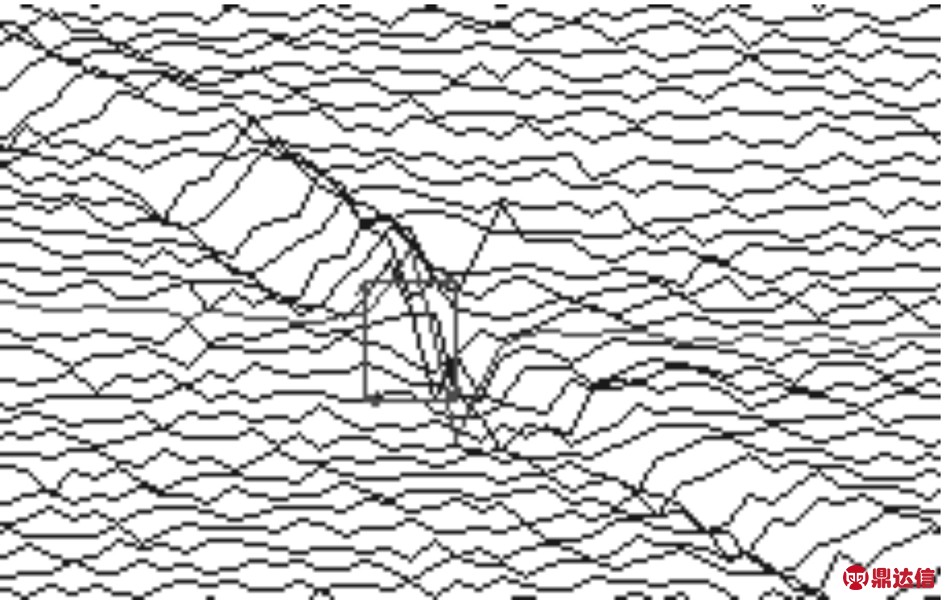
(a)2011年现场内检测
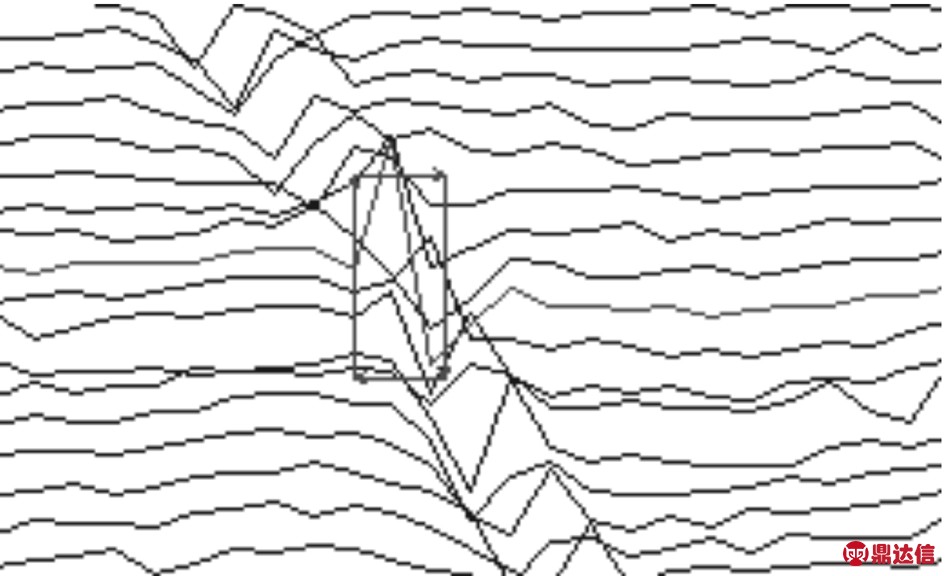
(b)1.02 m/s
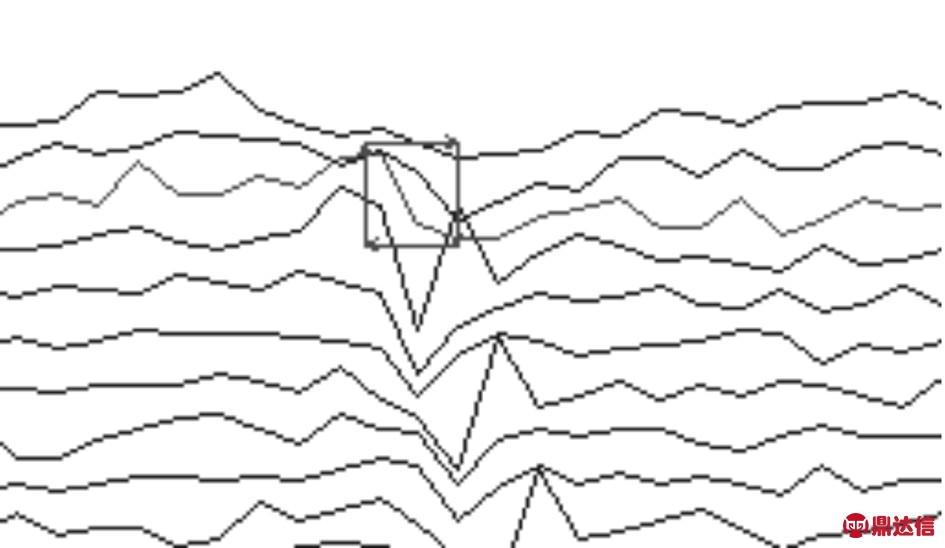
(c)4.61 m/s
图5 现场内检测及部分牵拉试验内检测信号图
3.2 试验结果分析
(1)在4 m/s牵拉速度内,裂纹型缺陷信号特征明显,数据分析时可进行缺陷特征识别(图5(a)、图5(b))。牵拉速度超过4 m/s后,缺陷特征仍存在,但因信号平缓,识别较困难(图5(c))。正常螺旋焊缝处漏磁信号具有先下后上的正弦信号特征,而螺旋焊缝裂纹型缺陷信号与其极性相反,信号特征为先上后下。
(2)由图6(a)可见:当牵拉速度在3.81 m/s时,此裂纹型缺陷特征信号幅值与最低牵拉速度1.02 m/s下幅值相比,最大衰减约11%。当牵拉速度超过4 m/s时,缺陷特征信号幅值急速衰减,当达到最高速度4.61 m/s时,最大衰减达77%。根据速度效应试验,可以得出结论:对于螺旋焊缝裂纹型缺陷,当内检测器运行速度在4 m/s以内时,可实现缺陷检测及识别;当速度超过4 m/s时,信号畸变,较难识别。
(3)由图6(b)、图6(c)可见:牵拉速度小于4 m/s时,裂纹型缺陷特征轴向投影长度、环向投影宽度变化不大。当牵拉速度达到4.61 m/s时,轴向投影长度变大,环向投影宽度变小。经分析是由于缺陷幅值信号衰减,导致信号平缓,识别出的尺寸变化导致。
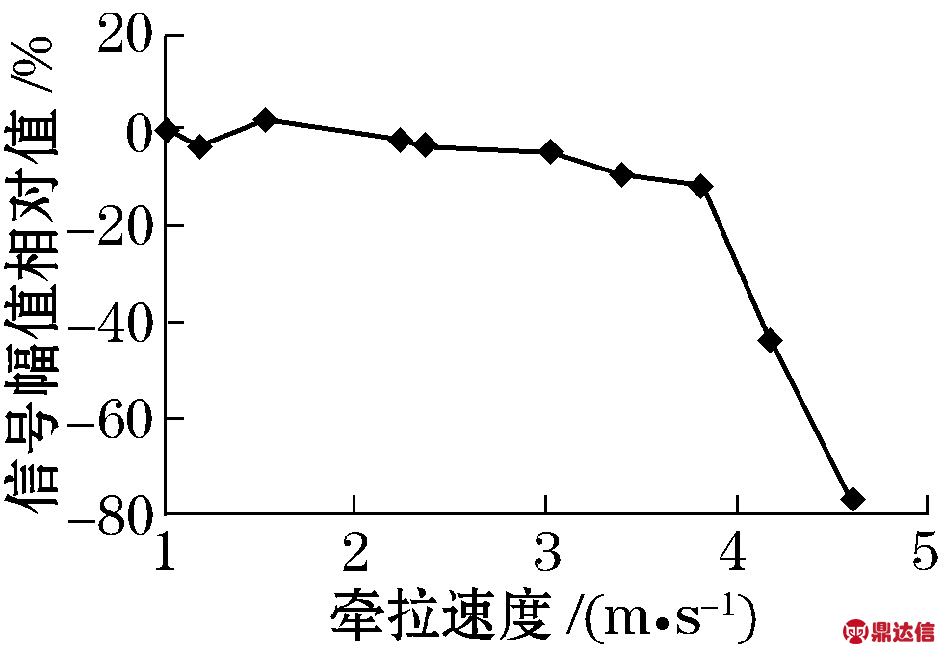
(a)信号幅值
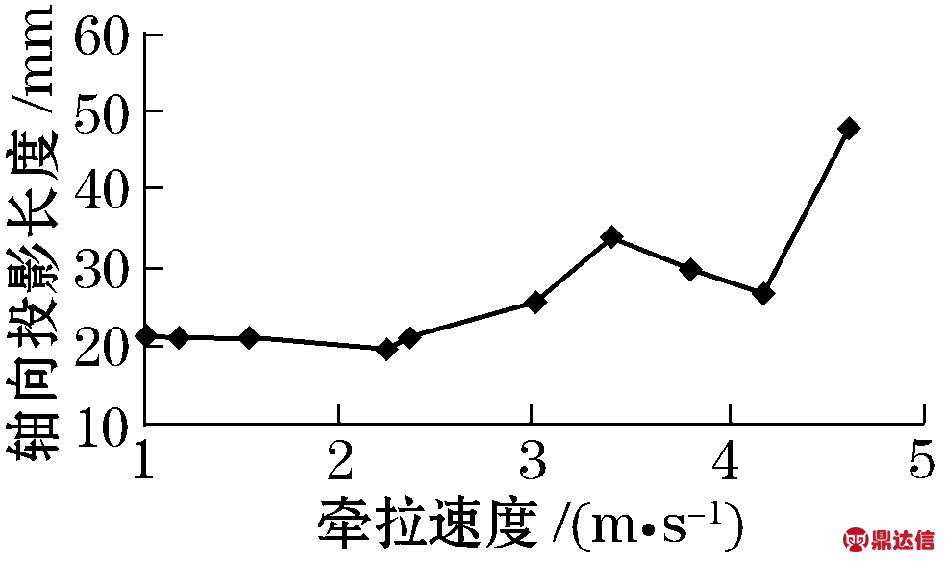
(b)信号轴向投影长度
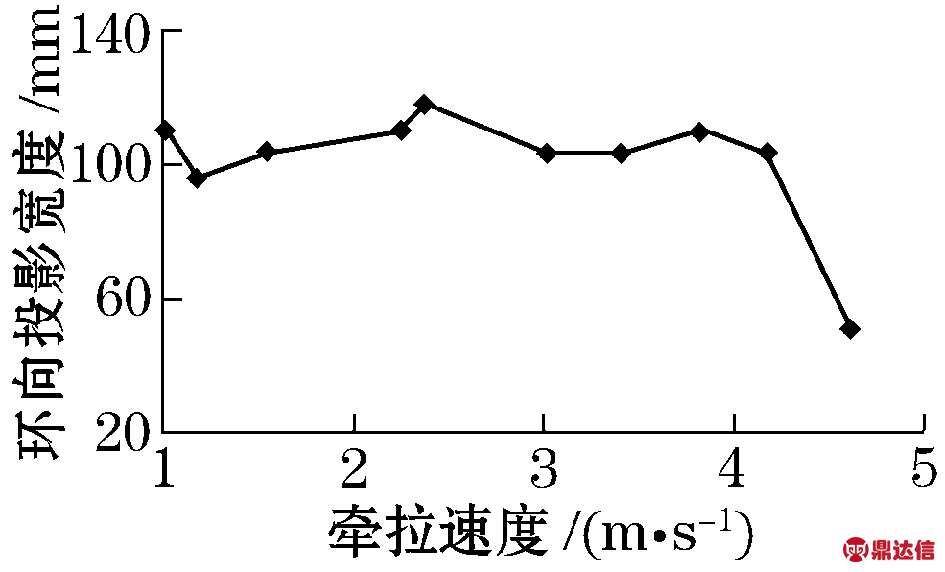
(c)信号环向投影宽度
图6 不同速度下信号特征变化图
4 缺陷失效分析
对该处螺旋焊缝裂纹型缺陷进行了静水压爆破试验及失效分析,根据断口形貌(图7),该处缺陷内表面长度45 mm,外表面长度15 mm,缺陷最长为64 mm;水压试验前裂纹最深已达到15 mm,水压爆破的断口深度为4 mm。
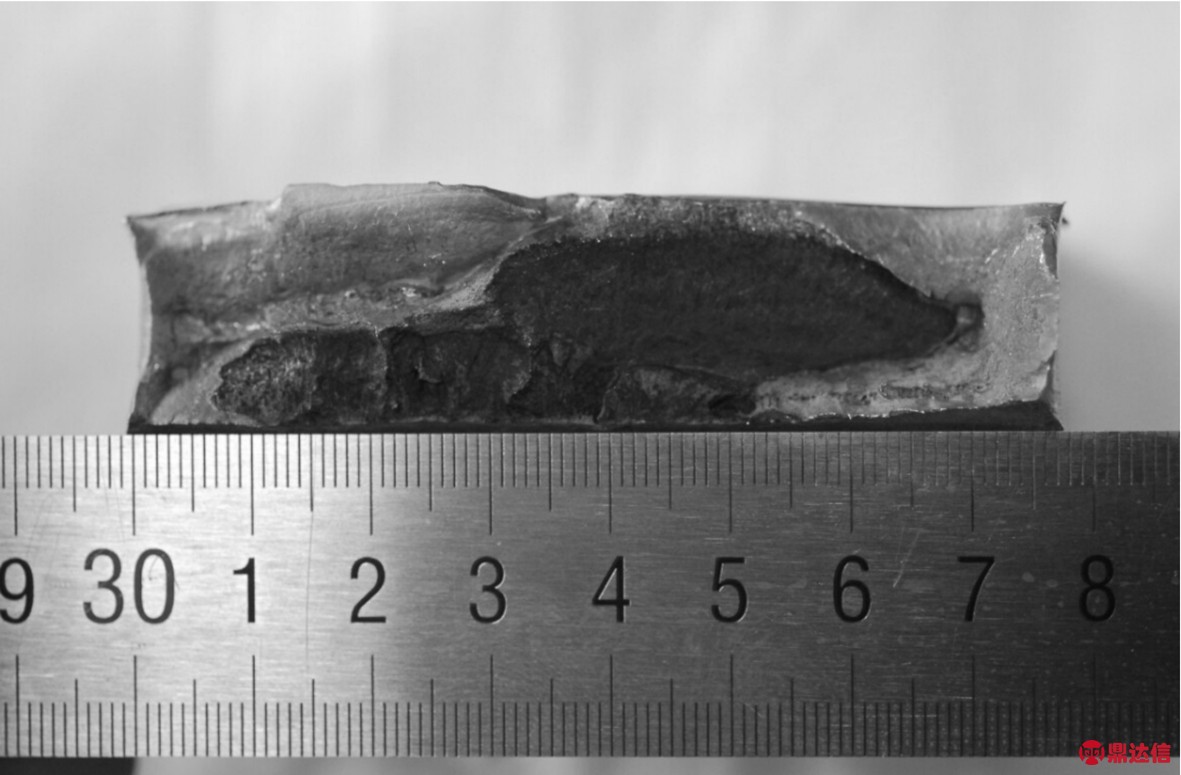
图7 断口形貌
根据牵拉试验数据,按照平均轴向投影长度27 mm,平均环向投影宽度101 mm计算,得到此裂纹型缺陷长度为104 mm,大于根据断口测量得到的最大缺陷长度(64 mm)。考虑是因为该处缺陷信号幅值较大,数据分析时识别出的环向投影长度过大造成的。
5 结论
(1)当牵拉速度在4 m/s以内时,裂纹型缺陷信号幅值有所衰减,最大衰减约11%。当牵拉速度超过4 m/s后,信号幅值急速衰减,最大衰减达77%。在内检测作业过程中,为获得高质量检测数据,需将内检测器运行速度控制在4 m/s以内。
(2)高清漏磁内检测器对螺旋焊缝裂纹型缺陷具有检测能力,牵拉速度在4 m/s以内时信号特征明显,但对于缺陷定性和定量还需进一步研究。
(3)牵拉试验是对内检测器检测能力进行验证,对缺陷特征进行建模,实现尺寸量化的有效手段。本文仅对该处螺旋焊缝裂纹型缺陷进行了牵拉研究。今后还应通过预制电火花加工的人工裂纹型缺陷及仿自然缺陷的焊缝缺陷,缺陷种类涵盖气孔、夹渣、错边、咬边、过度打磨、未焊满、未焊透、未融合、裂纹等,通过大量牵拉数据总结分析,进一步对利用高清或超高清漏磁内检测技术检测裂纹型缺陷的能力进行研究,解决长输油气管道焊缝缺陷内检测难题。