摘 要:牙刷柄橡胶热熔注射(后续简称“注胶”)是牙刷制造的重要工艺环节。市场现有注胶机械上下料仍然依靠人工,因为涉及封闭模具注胶工艺不易融入自动化线体中。现基于原有牙刷注胶单机,利用机器人实现一模多件牙刷同时上下料,从而大大提高了牙刷生产中此环节的效率。文中主要介绍牙刷注胶自动化的端拾器设计,供相关人员参考借鉴。
关键词:牙刷生产自动化;橡胶热熔注射;端拾器设计
牙刷是人们生活中必备的日用品,牙刷的制造生产已经日益趋近集中,是否拥有更高效的牙刷自动化生产线决定了企业的竞争力。牙刷制造工艺中主要包括注塑、注胶、植毛、磨毛等工艺环节,其中注胶是指在塑料牙刷柄中段(有时尾部)在模具内通过热熔橡胶的注射后冷却形成包裹在牙刷柄上用于防滑的橡胶层。现有常见的注胶机缺点包括:
1)依赖人工上下料速度慢;
2)摆放与模具整齐贴合较难;
3)开模中如出现粘连人工检查容错率低;
本设计旨在使用机械手带动端拾器实现注胶单机的辅助快速上下料,并准确检查缺料以提高牙刷自动化生产整体生产效率。
1 方案介绍
1.1 注胶工位整体设计
注胶机结构主要由机架、塑化注射单元、合模装置、控制系统、安全保护等组成。
牙刷注胶整体方案:考虑应用的工况、负载、节拍、自由度需求,选用六轴工业机器人,端拾器预估重量<8kg,综合上下料节拍考虑规格选用12kg六轴工业机器人。机器人利用端拾器从输送链上将注塑冷却剪切好的牙刷柄夹紧取走,整齐端正的将牙刷柄放入下模;上模合模,注射单元注射热熔橡胶;冷却,脱模;机器人下料把注胶好的牙刷柄放回输送带送往下一工位[1]。
1.2 端拾器设计技术难点预估
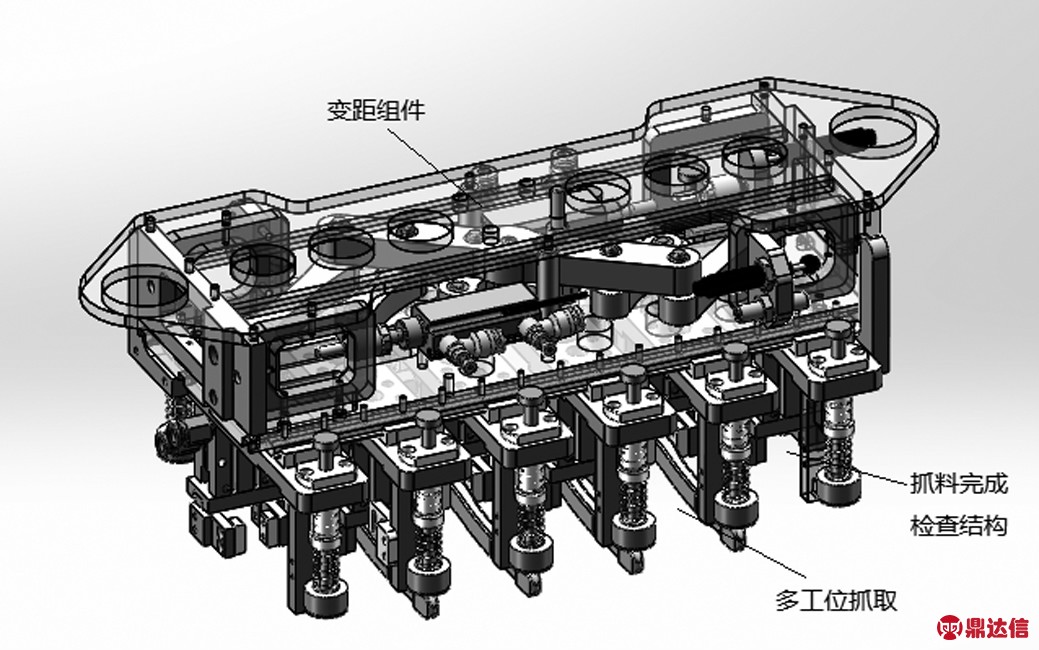
图1 端拾器总成
根据传统注胶工艺的经验和总体方案中的构想,端拾器设计可能需要匹配以下难点要求:
1)不同型号牙刷模具间距会不同,端拾器需具备调整距离的功能实现快速换型;
2)牙刷模具根据注胶机工作台的大小及参数调整因素一般为一出6~8支,端拾器需要实现多工位的同时夹取;
3)牙刷柄上料过程中需要保证端正平稳的放入模具内,除了机器人动作编程以外,结构上需要增加辅助单元[2]。
2 端拾器设计
2.1 抓取组件设计
气爪:单只牙刷抓取主要靠平行气爪从两侧平行夹住牙刷柄中端,从不同牙刷尺寸考虑,换型时均调整抓取组件气爪至牙刷柄线性尺寸中点;气爪抓取接触端有仿形块,换型是根据牙刷抓取点的截面尺寸仿形配合[3];
弹簧顶杆:前后对应配相同尺寸的弹簧顶杆,支撑板上装直线轴承,中心杆在直线轴承中可在机械限位范围内移动;弹簧杆末端为绝缘材料的柔性压块,压块上面到直线轴承间装一个圆柱压簧;弹簧顶杆作用是在端拾器下移到气爪夹取位置时,弹簧受压在牙刷柄前后两端施加两个反作用力,最终在气爪和两个弹簧顶杆间形成稳定悬臂;
在牙刷柄上料放进下模具的时候,气爪松开过程中,弹簧顶杆压住牙刷柄防止错位放置;
传感器检验:多工位抓取过程中,需要检验各抓取位确定有料(下料时确定是否全部抓走);采用触点开关判断,优点尺寸精巧、响应迅速、接触式不易受工况干扰;支架如图1,在触点开关支架末端设计一个缺口,配合气爪在左右方向上限位,防止牙刷柄旋转;当抓取位有料时,触点开关受力,反馈信号给控制系统;
抓取工位布局:足够对称的结构利用弹簧杆配合气爪让抓取和释放瞬间更平稳,上下料定位更准确,换型时候只需要更换气爪上的仿形块就可以实现快速换型[4]。
2.2 变距组件设计
端拾器支架:整个支架是由上下安装板和两个侧板固定完成的框架结构;上安装板是机器人执行端固定连接整个端拾器的,下安装板主要安装导轨直线单元。
多连杆变距机构:应用了一个平行连杆机构,中间为固定转轴固定在支架上,每个平行连杆轴连接对应一个单工位抓取组件,每个组件固定在滑块上,可在导轨上平行等距滑动;由两个变距气缸同时驱动最左右两端的连杆,连接杆转动实现变距;调节机械限位的位置,可控制距离,实际应用中抓取位间的平行距离等于模具中每模之间的距离。
变距组件整体:采用了平行连杆机构配合滑块导轨,可以通过调节机械限位迅速的实现抓取位之间的间距,从而使得端拾器可以配合各种不同的模具实现快速换型;前后作用的堆成结构保证了在气缸推力持续作用的过程中偏载的减少[5]。
3 结束语
从20世纪20年代自动化半自动化生产线引进以来,劳动高密集性产业生产成本大大减少。牙刷
产业作为人们生活中的必须品,每年在全世界有着非常多的需求量。各种机器人的应用在进入二十一世纪以来进入人们的视野以至在非常多的行业得到应用。工业机器人以非常高的灵活性远优于传统单机及生产线,而本文中主要介绍了一种用于牙刷注胶自动化的端拾器设计。能适用于不同型号的产品换型的能力在端拾器设计中是非常重要的;结构更合理的布局才能在机器人控制之前保证执行动作的稳定性。