在模具开发初期,冲压企业出于对产能、产品生命周期及模具成本等因素的考虑,会对新开发的冲压件产品的生产方式进行规划,如自制或委外、手动线或自动线生产等;模具开发人员会根据不同的要求,制订最为经济合理的模具开发方案,在模具选材、加工制造、废料排出、特殊处理等方面也就出现了很大的差别。因此在模具自动化改造过程中,需对存在的差异进行识别,逐一处理,方能保证模具改造的成功率。
明确改造对象
产品是生产过程的最终产物,在筛选哪些冲压件适合进行自动化改造时,需注意以下几点:
⑴产品工序数(除落料序外)需不大于冲压线压力机总数;
⑵为确保板料在延展过程中均匀变化,产品拉延序工艺补充部分周圈拉延深度需变化较小,不应存在一侧拉延深、一侧拉延浅的情况;
⑶产品拉延工序件拉延筋外坯料面需平整,无起皱现象;
⑷在批量生产过程中,拉延序不使用拉延剂等辅料;
⑸产品全序不存在卡模现象;
⑹批量生产后,拉延工序件上的冲击滑移线不划伤板料;
⑺单片废料对角线长度通常不超过400mm。
模具部分
拉延序凹模圆角状态
手动线拉延模工作部位材料多为MoCr合金(淬火硬度50HRC以上),大批量生产且无拉延剂辅助时,模具发热加剧,极易导致零件出现拉伤、开裂等质量缺陷,故需结合零件实际生产状态对模具进行表面镀铬处理。工作部位材料为Cr12MoV(淬火硬度58~62HRC)时,建议进行表面TD处理。
模具工作部位的材料多为铸件,存在砂眼等铸造缺陷。因手动线模具开发成本低于自动线模具,在满足使用的前提下,对铸件的质量要求亦较低,故在进行自动化改造时,需对拉延序凹模圆角状态进行检查;若砂眼较多,改造完成后将导致零件批量生产状态不稳定(经常出现拉伤、开裂等质量缺陷),且模具圆角处易掉碎屑。若砂眼较多,强行对模具进行表面处理(镀铬或TD),可能造成模具开裂或局部粉碎。
修边废料滑落
手动线模具在开发时不会着重考虑各序间的模具型面高度统一问题,对于废料滑落问题亦仅要求废料滑出模具,不强制要求滑入压机废料槽内;故在自动化改造时,需考虑在下模增加垫板,并结合废料滑出情况增加二级废料滑板,以便废料滑入压机废料槽内。
若废料在废料滑板上滑落速度较慢,导致与其他废料碰触出现卡料现象,可在废料滑板上铺一层MISUMI的滤油网板,加快废料滑落的速度。
由于自动线的生产节拍比手动线生产快,局部位置的废料在切断后因未及时滑落,在刃口上行时废料被向上带起,导致废料卡于模具内等现象;针对此问题,可在相应废料位置上模处,增加几个弹顶销,防止刃口向上带料。
端拾器吸盘位置的选择
自动线模具为确保吸盘在抓取零件时不压伤零件表面,通常会在吸盘对应的下模型面位置做符型,但从以下四点考虑,手动线模具改造时可不做符型:
⑴零件本体刚度较好,不易变形;
⑵吸盘抓取所选的位置多以平面为主,且分布均匀;
⑶选择尺寸合适的小型吸盘;
⑷吸盘抓取时选择对表面质量要求不高的位置。
自动化元器件的安装
⑴元器件的走线需避开废料通道,且不易被破坏;
⑵模具信号识别插头需置于模具内部且靠近压机插头位置;
⑶拉延序模具需安装板料投入检测开关(对角布置,尽量避免安装在模具后侧),上模对应位置需做避空;
⑷后序模具需安装接近开关,对角线布置,感应面尽量选择平面位置;
⑸模具信号识别插头的接线方式可按图1连接,其中模具号采用二进制规则进行编排;
⑹接近开关在选购时需注意用电方式(“交流”或“直流”)及供电电压,需与压机设备要求一致。
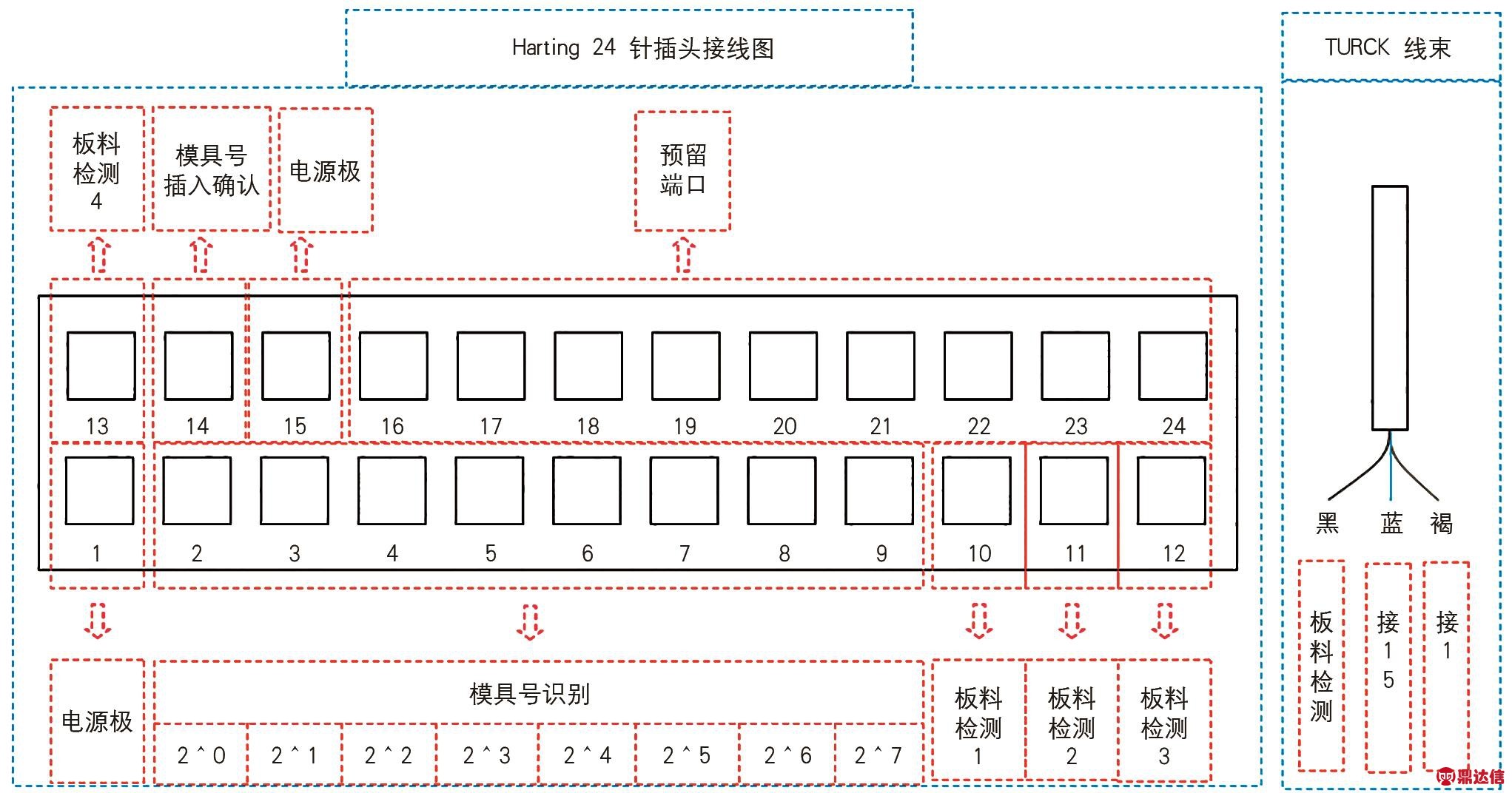
图1 模具信号识别插头的接线方式
压机部分
当自动冲压线设备数大于零件工序数(除落料序)时,需在最后一台或几台设备上安装空工位架,以便于零件在冲压线内正常流转,注意事项如下:
⑴空工位架上有可靠的零件符型面及定位系统;
⑵接近开关、信号插头等的布置与在模具上的要求一致;
⑶空工位架符型面的高度需与前一序模具型面高度基本保持一致;
⑷压机控制模式需调整为“空工位”,且设备参数中当前值与设定值需一致。
机械手端拾器部分
目前,行业内所使用端拾器品种繁多,均可满足正常生产需要,在选购时可整套选购,也可按照配件进行采购,但需注意以下事项:
⑴吸盘与吸盘连接件处的密封性;
⑵端拾器与机械手连接处插头的定位加工精度;
⑶零件尺寸较大,需选用重载端拾器;若考虑成本,可在端拾器上增加重量较轻的辅助连接杆,以提高端拾器整体强度;
⑷若不考虑对机械手进行改造,则端拾器吸盘总数最多不能超过机械手真空发生器的数量。
结束语
随着冲压行业的发展,为降低人工成本、提高生产效率,手动线生产改造为自动线生产的模式将被广泛采用,但为降低改造难度,建议在模具开发初期,在模具选材、加工处理、模具样式等要求上按照自动线模具要求进行开发。