摘 要:随着人类技术的快速发展,工业自动化的程度逐渐深入。厨电企业作为传统的制造行业,通过创新驱动、“机器换人”推动技术红利替代人口红利,是其经济继续保持增长的动力之源。介绍了ABB工业机器人的结构及特点,对ABB工业机器人在冲压自动化生产线的应用作深入介绍和分析。经过生产验证,将工业机器人引入到冲压自动化生产线上,是切合实际生产需求与发展的。
关键词:自动化;ABB工业机器人;冲压
0 引言
随着生活质量的提高,人们追求高品质生活的要求越来越高,厨房在家庭生活中的地位也就越来越高,高质量的厨房电器也是高品质生活质量的体现。不锈钢钣金冲压线就是厨电产品生产过程中的重要设备,其生产质量和效率将直接影响厨电产品的质量和生产效率。随着人们对厨电产品质量的要求越来越高以及产品生产的规模化,冲压生产领域ABB工业机器人冲压自动生产线[1]的应用,极大的提高了生产效率,保证的生产产品的质量。
1 ABB工业机器人的结构及特点
ABB是工业机器人的先行者以及世界领先的机器人制造厂商,致力于研发、生产机器人已有40多年的历史。ABB工业机器人主要由机器人主体和第5代控制系统柜(IRC5)两部分组成。机器人主体,具有和人手臂相似的动作功能,可在空间抓放物体或进行其他操作,由机械结构、驱动装置及传动装置组成;第5代控制系统柜(IRC5)是机器人的运动控制系统的集成柜,它控制实现机器人的运行。
1.1 ABB工业机器人的结构
1.1.1 机器人主体
ABB工业机器人是由六个转轴组成的机械设备,每个转轴可实现1个自由度。机器人六个转轴均由AC伺服电机驱动,每个电机后均有编码器和齿轮箱。受机械结构的限制,机器人各旋转关节一般不能实现3600转动,而是有一定的运动范围,各关节运动范围共同作用决定了机器人的运动范围,以ABB IRB4600 60kg/2.05m机器人为例,如图1所示。
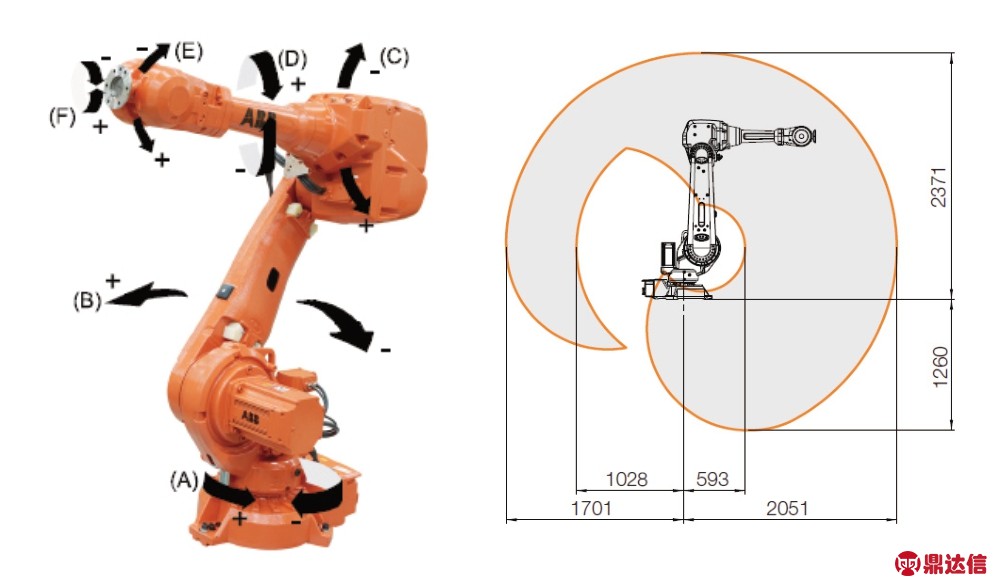
图1 ABB IRB4600 60kg/2.05m机器人主体及工作范围
1.1.2 第5代控制系统柜(IRC5)
ABB机器人第5代控制系统柜(IRC5)主要包括:计算机控制模块、轴计算机模块、驱动单元、输入/输出接口单元、示教单元等。计算机控制系统是机器人控制的核心,采用具有实时中断控制与多任务处理功能的专用计算机控制系统;伺服驱动系统在计算机控制系统的控制下,控制并驱动各关节伺服电机,实现机器人的运动控制:I/O接口通过硬线连接或总线的方式实现与外部控制系统或外部设备的通讯连接;示教器用于手动操作机器人动作,完成示教工作和参数设置、程序存取等系统基本操作。ABB第5代控制系统柜及伺服驱动逻辑图如图2所示。
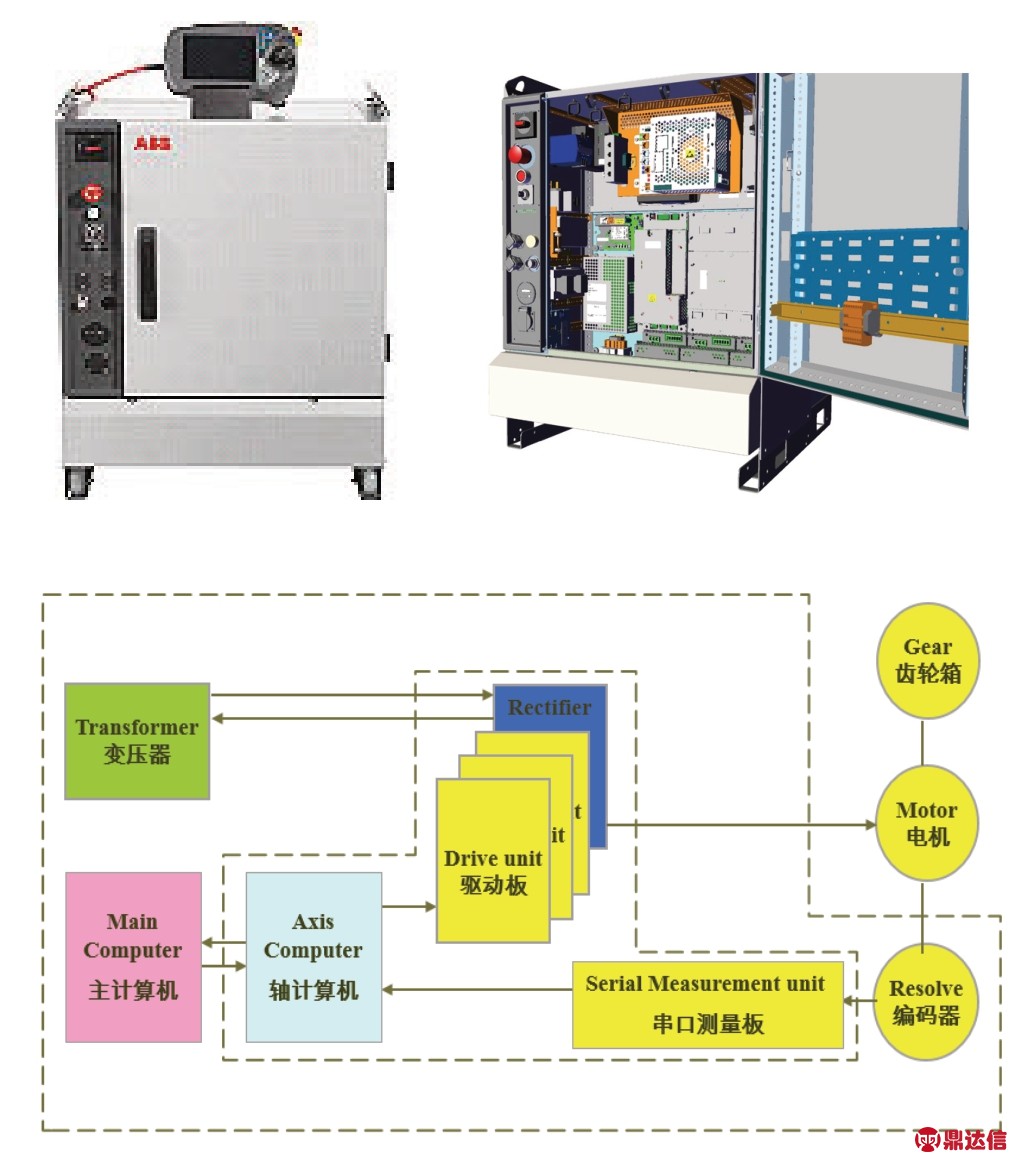
图2 ABB第5代控制系统柜及伺服驱动逻辑图
1.2 ABB工业机器人的特点
ABB工业机器人主要有以下特点:
1)具有各种不同负载和工作半径的型号,满足任何行业的需求;
2)具有不同的防护等级,适用于各种复杂的工作环境;
3)优化的机械设计,结构刚性好,强健可靠;
4)直观互动的彩色触摸屏,3D摇杆设计,灵活的定制应用功能,丰富的机器人选项,满足不同层次的客户需求;
5)领先的运动控制性能,强大的QuickMoveTM和TrueMoveTM功能,实现最高的运行速度和精度;
6)得力的SafeMove安全功能,实现机器人与操作员的协作互动,独有的Rapid程序语言,支持结构化编程,易学易用。
2 ABB工业机器人在冲压自动生产线的应用
ABB机器人[2]冲压自动化整线一般包含:压力机、线首拆垛系统、清洗机、涂油机、对中系统、上料机器人、压力机间传输机器人、线尾下料机器人、线末皮带机、线尾自动装箱系统以及换模系统等。下文以工厂的机器人冲压自动化生产线为例对其整体方案、电气控制和仿真模拟进行论述。
2.1 机器人冲压自动化方案整体设计
2.1.1 线首单元
1)拆垛设备
根据生产节拍和生产的连续性等要求,线首拆垛部分使用两个可移动式的拆垛小车,保证整线不停机生产。拆垛小车由电机或气缸驱动,具有到位停止限位开关,防止到位时工作台串动。拆垛小车上配置定位装置以便操作者方便地把托盘和料垛放到位。定位装置可以快速拆下并安装到其他位置以便适应不同大小的托盘。
拆垛台配备强力磁力分张系统,使上层坯料实现简便分离。每个小车配置磁力分张装置,可确保坯料完全分离。磁力分张装置固定在可旋转的伸缩臂上,伸缩臂安装于直线导轨上,直线导轨安装在工作台上,可实现上下,左右,前后六个方向的调节。生产转换期间可通过伸缩臂手动调整磁力装置的位置。
另外,拆垛小车上配置有末料检测装置。当拆垛台上垛料拆完后,机器人自动转向另一个拆垛台拆垛。此时,系统会发出声光报警提示操作人员进行垛料更换。操作人员按下按钮通知PLC,拆垛台移出工作区到达上料位置,操作者手动将磁力装置向后移动,借助叉车等工具更换垛料。
2)拆垛机器人通用端拾器
拆垛机器人配备通用端拾器[3],该端拾器能处理生产线上的各种板料。因此,它不需要更换端拾器。端拾器上的每个吸盘都可通过触摸屏进行可视化设定,将其设定为工作(用)或闲置(不用)模式,以适应不同的板料。该端拾器配备有一套双料检测器,以防止机器人抓起两张板料。如图3所示。
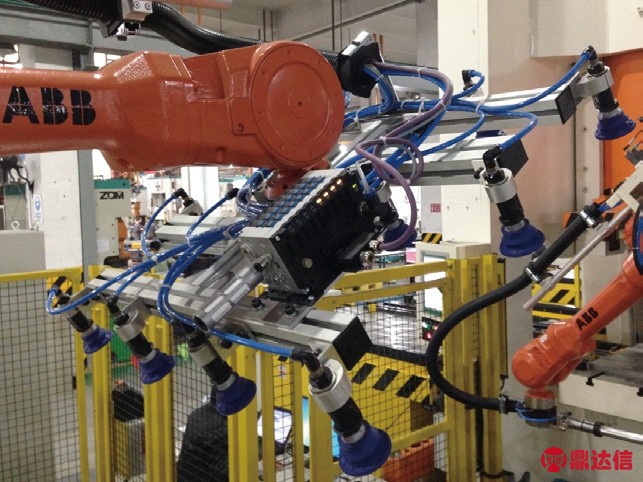
图3 拆垛机器人通用端拾器
3)涂油机
由于工厂的底盘件首工序需要涂油,以此来保证产品的拉延效果。所以线首配置一台涂油机。涂油机用于钢坯料表面涂敷深拉油。根据具体深拉工艺,按程序对机器中移动的坯料进行单面或双面涂油,也可选择全部表面或部分表面涂油。
表1 三种对中方式工作原理和特点

板料上的喷射图样和喷涂量可根据实际需要在触摸屏上自由选定。以实现喷油的准确性、灵活性以及多样性。油雾分离器通过通风机将夹杂在空气中的油雾吸出,然后油雾形成液体后经喷油型腔回流到储油箱内,保证现场干净,无油污。
4)对中方式
目前冲压生产线常用的对中方式有重力对中、机械对中以及视觉对中,其工作原理和特点如表1所示。
由于工厂的原坯料种类较多且形状都是规则的矩形,所以选择结构简单、好用的重力对中方式。对中台采用倾斜的重力滑台,对于规则的矩形板料,一般只需对中台的固定直角边就能实现板料的准确定位。
2.1.2 线间单元
线间单元除了按照合适的压机间距配备所需的机器人[4],最主要的是实现机器人端拾器的自动更换功能,简称ATC。端拾器的自动更换非常简便、快速,可以在120秒内完成。
每个机器人均会配备端拾器快换装置,从而实现机器人与端拾器主杆之间的自动连接。每个机器人单元配备2个端拾器主杆。当一个端拾器主杆带着端拾器的分枝在机器人进行生产的时候,工人可以对放在自动更换支架上的另一个端拾器主杆进行更换。端拾器支架安装在机器人后侧,用围栏将其和机器人隔开。工人只需要更换端拾器主杆,每个主杆有一个释放按钮,更换一个端拾器,非常方便快捷。它符合人体工学原理,且需要的存放空间非常小,如图4所示。根据产品的工艺特性,线间单元配备了翻转台、去毛刺专机、穿梭输送机、视觉检测等设备。
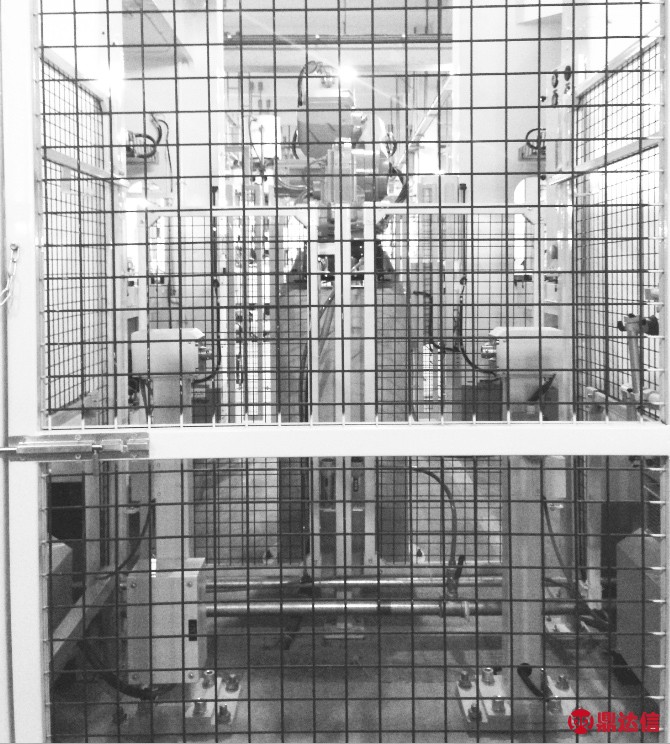
图4 线间机器人自动更换端拾器
2.1.3 线尾单元
线尾单元配备一个皮带机输出冲压成型的产品[5]。线尾皮带机为单幅皮带机,由一个带减速机的交流变频调速电机驱动,传输速度可以根据需要设定。皮带表面覆切割层,耐磨损。皮带机的尺寸满足产品的大小和整线生产速度,并且日常维护操作简单,备件更换也相当方便。如图5所示。
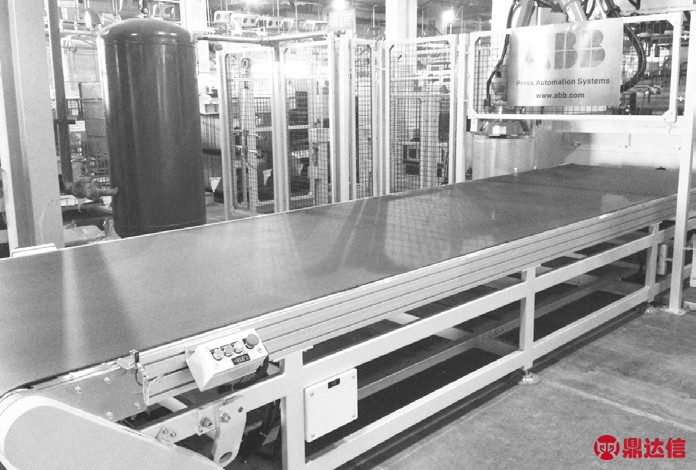
图5 线尾输出皮带机
2.2 机器人冲压自动化控制系统设计
ABB机器人冲压自动化整线控制系统主要包含:
1)整线控制及安全系统。
1)人机界面HMI。
3)ABB机器人冲压专用软件StampWare。
整线控制按照集中监控、分散控制的原则。在各控制部分控制系统中,采用设备层和管理控制层的典型控制模式[6],每个层次中使用不同的网络结构及软硬件配置,以实现各自不同的功能。
2.2.1 整线控制及安全系统
整线控制系统构架分为两层:控制层和设备层,设备层采用CC-link和Profibus总线通讯;管理控制层采用工业以太网通讯,如图6所示。
整线控制系统采用PLC,主PLC内安装有ABB冲压自动化专用控制和安全软件[7]。各种智能传感器和阀通过现场总线和相应的PLC或远程I/O单元进行通讯,包括现场操作站、现场设备检测单元(接近开关、光电开关等)、现场其他输入设备、现场执行机构(如变频器、电磁阀等)等。
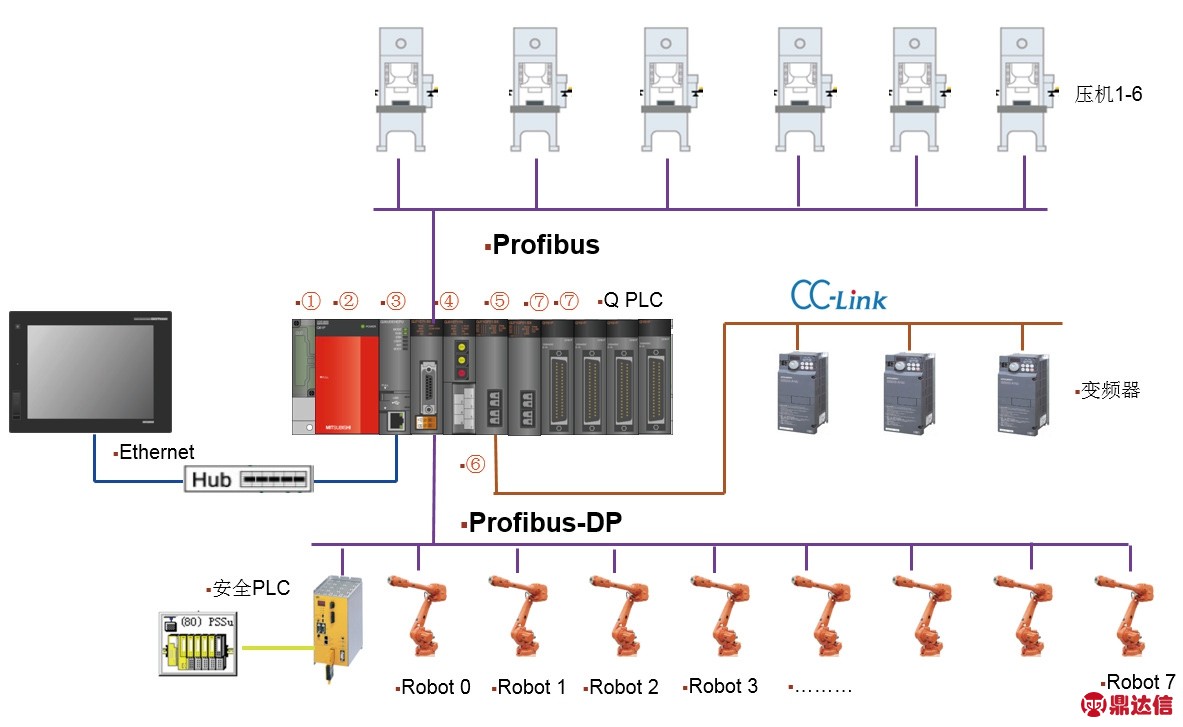
图6 整线控制系统架构图
整线安全系统采用德国安全控制器,并配置了完善的安全装置,实时监控各安全区域状况,及时发出声光报警信号或停机,与主PLC系统通讯采用现场总线方式。声光报警单元作为整线安全系统的辅助工具,能够在设备启停、设备故障、上下料故障以及各安全监控点报警等异常状况发生时及时通知操作人员处理。整个控制系统的所有紧急停止信号以及压机和机器人之间的安全连锁信号都连入安全系统中,通过PLC程序进行互锁控制,达到极高的安全等级,充分保证生产安全。
2.2.2 人机界面HMI
整个控制系统HMI采用触摸屏,采用工业以太网和主PLC进行通讯。HMI作为人机互动的界面,主要包括整线总览、操作提示、通用端拾器设置、配方管理、生产切换、诊断和服务等功能界面。操作人员可以通过HMI方便的操作、控制整个生产线,并实时监控生产线的生产状态,如图7所示。

图7 生产线HMI
2.2.3 ABB机器人冲压专用软件StampWare
StampWare是ABB开发的集成在机器人示教器上的冲压自动化软件,用于帮助操作者方便地操作管理机器人和冲压线。模块化的程序结构、编程向导和图形生产窗口,可以缩短培训时间,在安装、生产设置和机器人节拍优化期间,生产效率更高。它主要有两部分组成,StampWare人机界面和StampWare向导。StampWare人机界面将冲压生产线各种常用功能集成到操作面板上面,可以监控整条生产线及本单元状态。StampWare编程向导能够使操作者更容易学习并进行零件的编程,操作人员无需特别学习编程语言。StampWare编程向导包含了创建新零件程序的所有必要步骤,通过向导可视化界面的设定,新零件的编程工作能够非常快捷轻松地完成。
2.3 仿真模拟验证
2.3.1 ABB Robotstudio介绍
RobotStudio是ABB模拟与离线编程软件,作为FlexPendant的理想配套软件,Robotstudio拥有PC环境下的操作优势。它以ABB VirtualController为基础,与机器人在实际生产中运行的软件完全一致。因此,通过RobotStudio可执行十分逼真的模拟。在项目前期,通过RobotStudio进行仿真模拟,可以降低项目风险,提前预估生产线的节拍,使规划更加合理有效。
借助RobotStudio提供的各种工具,可在不影响生产的前提下执行培训、编程和优化等任务,提升机器人系统的盈利能力,并获得降低风险、投产迅速、换线快捷和提高生产效率等多种利益。
2.3.2 工厂仿真模拟验证
工厂冲压自动化项目是一条改造线[8],主要是生产家用燃气灶底盘件。此项目在前期规划时,难点主要有3点:1)底盘件生产工艺比较复杂,包括拉伸、去毛刺、翻转、穿梭机输送、人工装配支架等;2)1序油压机拉伸速度比较慢;3)整线生产节拍要求10s。
为了解决这些难点问题,降低整个项目的风险,ABB使用专用仿真软件对整个项目进行模拟验证,最终确认了生产线的整体布局,优化了每个机器人的运行轨迹,并得出生产线的节拍最快为9.6s/件,如图8所示。最终,此项目顺利完工并及时投入生产,生产线实际节拍最快可达到9.8s/件。

图8 工厂冲压项目模拟图
3 结语
本文介绍了ABB工业机器人的结构及特点,并对其在冲压自动化生产线的应用作深入介绍[9]和分析。随着冲压技术的不断深入发展,ABB工业机器人冲压自动线在厨电行业得到了广泛的应用,其代替了人工生产的重复性,在提高生产效率的同时极大的提高了产品的质量。目前,工厂工业机器人冲压自动生产线系统已投入运行,在获得了良好的经济效益的同时提高了产品的质量,对今后的新冲压生产线[10]的引进具有巨大的借鉴作用。