本文对重型车架总成外形特征及特点进行了介绍,研究出全新的车架总成制造技术,并成功应用于实际生产中,提升了重型车架总成的加工质量和技术水平,自动化程度得到了有效提高,达到了国内领先技术水平。
为满足国内外高端客户的市场需求,东风商用车公司近年开发了全新战略高端车型,打造东风超级重卡旗舰车型,力争成为国内重卡新标杆。
该重型车架总成采用全新设计,加工工艺复杂且质量要求严格,产品要求采用一次上线,同时对零部件制造智能化技术应用提出要求,考虑自动化设备的现场应用,鉴于此要求,传统制造技术已无法满足该车架总成生产需求,需开发新的制造技术手段实现该车架总成生产。
车架总成外形特征及特点
1.车架总成外形特征
车架总成为前宽后窄型车架,纵梁合件为主副梁结构(料厚匹配为8+4 mm),车架外宽前段由传统的940 mm增至1 080 mm,后段由传统的860 mm减至800 mm,发动机兜梁结构复杂,纵梁燕尾转嫁至尾横梁上,车架总成外形结构如图1所示。
2.车架总成特点
(1)发动机兜梁及尾横梁总成结构复杂,冲压成形难度大,总成装配孔位同轴度及开档尺寸精度均要求较高,三面结构的平衡轴横梁成形对于尺寸精度不易保证,平衡轴横梁与推力杆支座焊接,其左右装配螺纹孔位置精度高。

图1 车架总成结构

图2 车架总成加工工艺流程
(2)车架总成装配采用先涂装后装配,即纵梁、加强梁和横梁等零件先涂装,而后装配成车架总成。
车架总成制造工艺流程
该战略车型车架总成加工方案主要采取先涂装后装配,纵梁、加强梁和横梁先分别进行加工后涂装成油漆件,而后一次上车架装配线总拼装配成车架总成,由于在车架装配过程中,原有漆膜难以避免受到破坏,车架总成装配完成后,还需喷漆以保证最终涂装表面质量。主要工艺流程如图2所示。
车架总成制造技术的研究与应用
面对全新的车架总成产品结构和特点,制造技术人员通过前期对产品进行多轮研究论证,项目组联合厂家共同研发出全新冲压、焊接、涂装和装配等多项智能化制造技术并成功应用,以期实现车架总成加工制造,达到产品相关技术质量要求。
1.冲压技术
(1)冲压类主要涉及产品结构特征
横梁类产品主要为高强度钢板,抗拉强度σb在510~590 MPa范围内,结构复杂,形状较普通横梁差异大,料厚为7~8 mm,产品简图如图3所示。
(2)制造技术研究分析
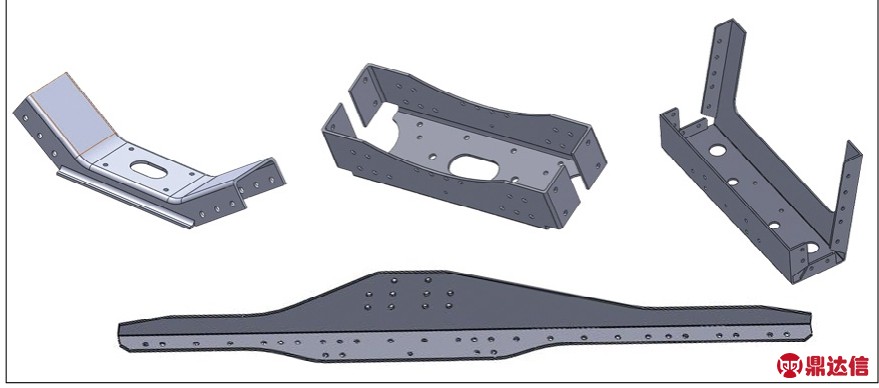
图3 横梁类产品(含L板)
由于传统横梁制造技术主要普遍采用1 250 t机械压力机以及相应的配套模具,结合人工上下料生产,传统大型L板采用钣金工艺实现,也采用人工上下料,存在诸多问题。项目组在充分了解国内外同行业冲压技术后,为保证高品质冲压件质量,通过合理选择大型油压机相关参数,确定采用大型2 500 t油压机进行生产,同时采用优化结构后的模具进行冲压(L板借用平板数控冲进行冲孔,保证孔位精度),采用智能化制造技术,即机器人自动上下料装置代替人工实现上下料自动化操作,应用视觉定位识别技术,研发出全新的机器人全自动冲压线。
(3)冲压自动化制造技术应用
该冲压技术属国内首创,总体方案采用中厚板冲压专用模具+中厚板成形油压机+机器人上下料装置+柔性化厚板专用端拾器组合,实现高端产品的厚板零件冲压,通过调整柔性化的油压机压力曲线,合理设计模具排废系统,选用适合中厚板抓取料的端拾器,优化自动化冲压程序,成功应用于实际生产。全自动冲压线总布置如图4所示。
该专用模具设计特殊废料滑板,保证废料自动滑落,模具上增加侧压装置,提高板料定位精度,修边冲孔时模具具备自动检测压双料功能,为保证冲压件表面质量,凹模采用铍铜合金,采用顶出器单独导向结构,避免铍铜合金磨损造成顶出器在模具中的晃动,提高成形件精度。
冲压设备选用2 500 t油压机,下死点可进行保压,工作压力和速度可在一定范围内调节,满足产品工艺需求。自动化传输系统主要采用智能化制造技术机器人上下料装置,由于油压机空间较大,产品结构差异大,冲压件工序多,本着传输系统自动化柔性化的要求,考虑采用机器人自动化传输系统。
柔性化厚板专用端拾器组合安装在机器人手臂末端第六轴,经过研究试验,对薄板冲压端拾器进行改进以适应厚板冲压,采用强力电磁吸盘和重量轻的铝型材组合成适应中厚板冲压用的端拾器,该结构柔性好,通过相关调节,以适应不同尺寸零件。
2.焊接技术
(1)焊接类涉及产品结构特征
焊接类产品主要为平衡轴横梁,横梁工艺合件(横梁与推力杆支座连接后的结构)由横梁和两个推力杆支座连接而成,横梁工艺合件如图5所示。
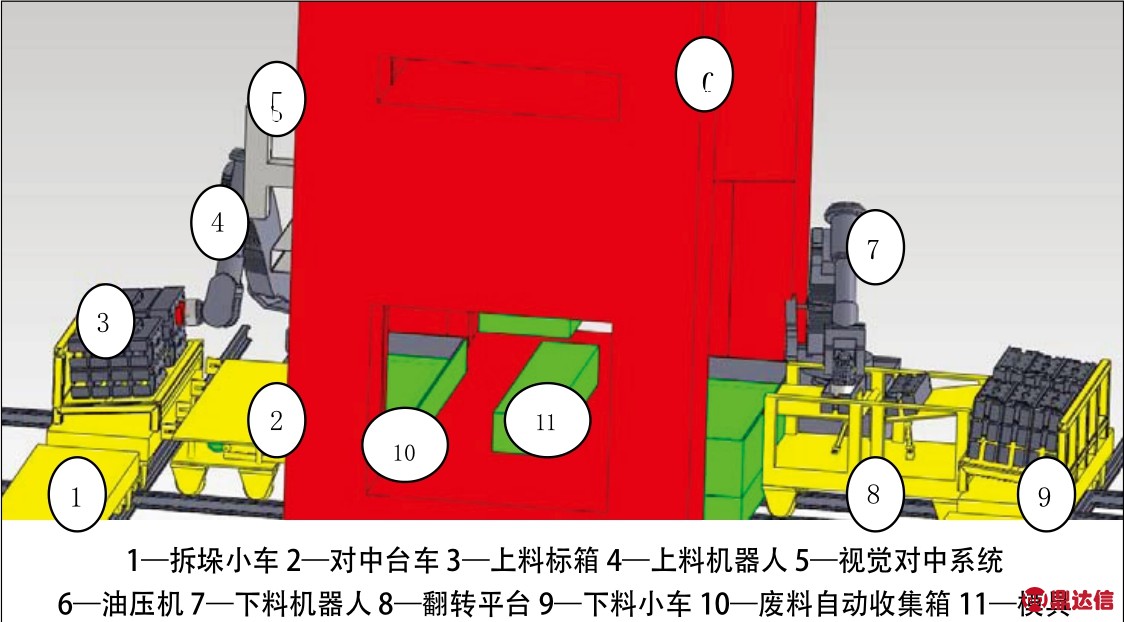
图4 全自动冲压线总布置
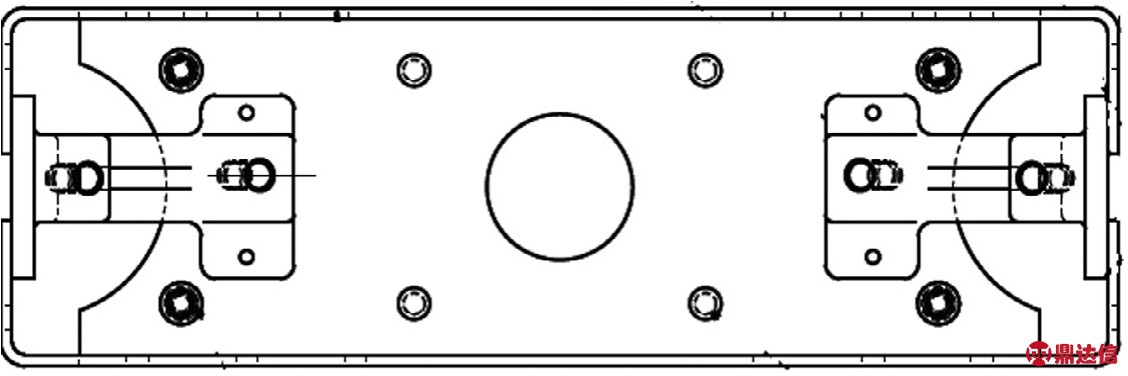
图5 横梁工艺合件
(2)制造技术研究分析
由于传统横梁焊接工艺为手工电弧焊,该工艺存在焊缝外观质量不稳定、差异性较大等问题。为适应全新重卡品质技术要求,需研发全新的焊接制造技术生产该横梁工艺合件,机器人焊接自动化技术作为成熟的生产手段已得到国内外普遍应用,机器人焊接可保证焊缝外观的质量稳定和一致性。通过优化机器人焊接方案,可提高单件工艺合件焊接节拍,大大降低员工劳动强度。鉴于横梁工艺合件内部空间较窄,以及此前并无类似产品焊接工艺参数参考,需设计制造专用焊枪集成于机器人,并需进行多轮焊接参数调试,以最终符合焊接工艺要求。
(3)焊接自动化制造技术应用
机器人弧焊设备系统主要由机器人弧焊系统、电气控制系统、焊接工装及设备、除尘系统和其他辅助设施组成。机器人弧焊系统包括特制焊枪、水冷设备、焊接电源、控制柜、送丝机构、示教器与机器人。机器人为六轴工业机器人,六自由度满足焊接柔性化要求,机器人具备示教编程、示教再现等功能,焊接电源具备与机器人控制柜通信功能。电气控制系统主要由机器人控制系统、PLC控制系统、变频器和伺服电动机等组成,PLC控制系统对回转工作台动作进行操作和控制,机器人依据PLC发出的信号对工件进行焊接。
3.涂装技术
(1)制造技术研究分析
由于车架总成采用先涂装后装配的方案(解决原有车架总成内部流黄水问题),纵梁、加强梁、横梁及小件需先进行涂装,而后在车架装配线进行整体装配,装配后再进行总成喷漆,以确保车架油漆表面质量。纵梁和加强梁可利用现有车架油漆线进行电泳涂装,但需配备专用油漆托架,考虑现有油漆线结构影响,横梁及小件借用外部资源进行涂装。车架总成装配后,在转运至喷漆过程中,由于车架总成前端大铸件尺寸较大,与下层车架严重干涉,还需配备专用车架总成垫块进行车架总成码放。
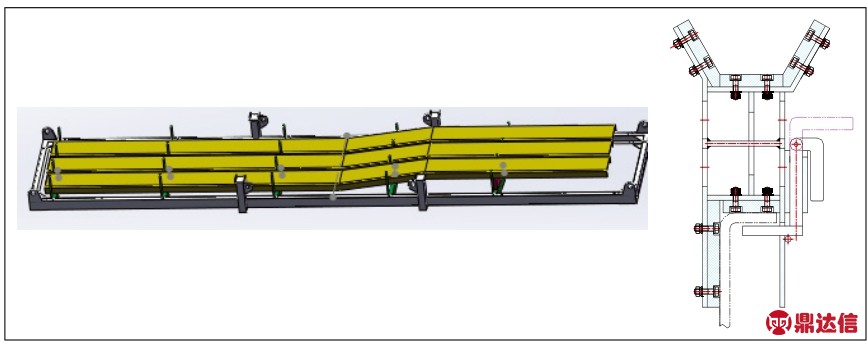
图6 油漆托架和总成垫块
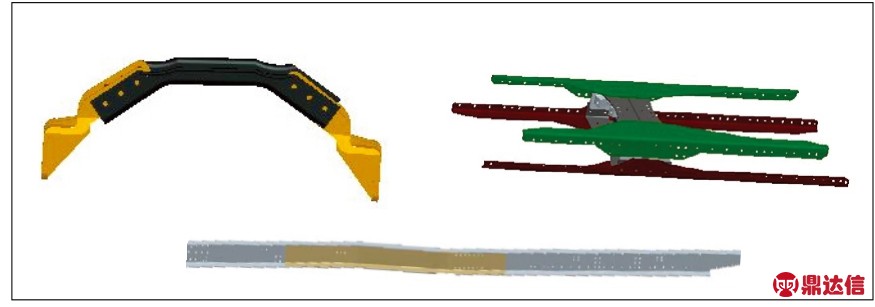
图7 装配类产品
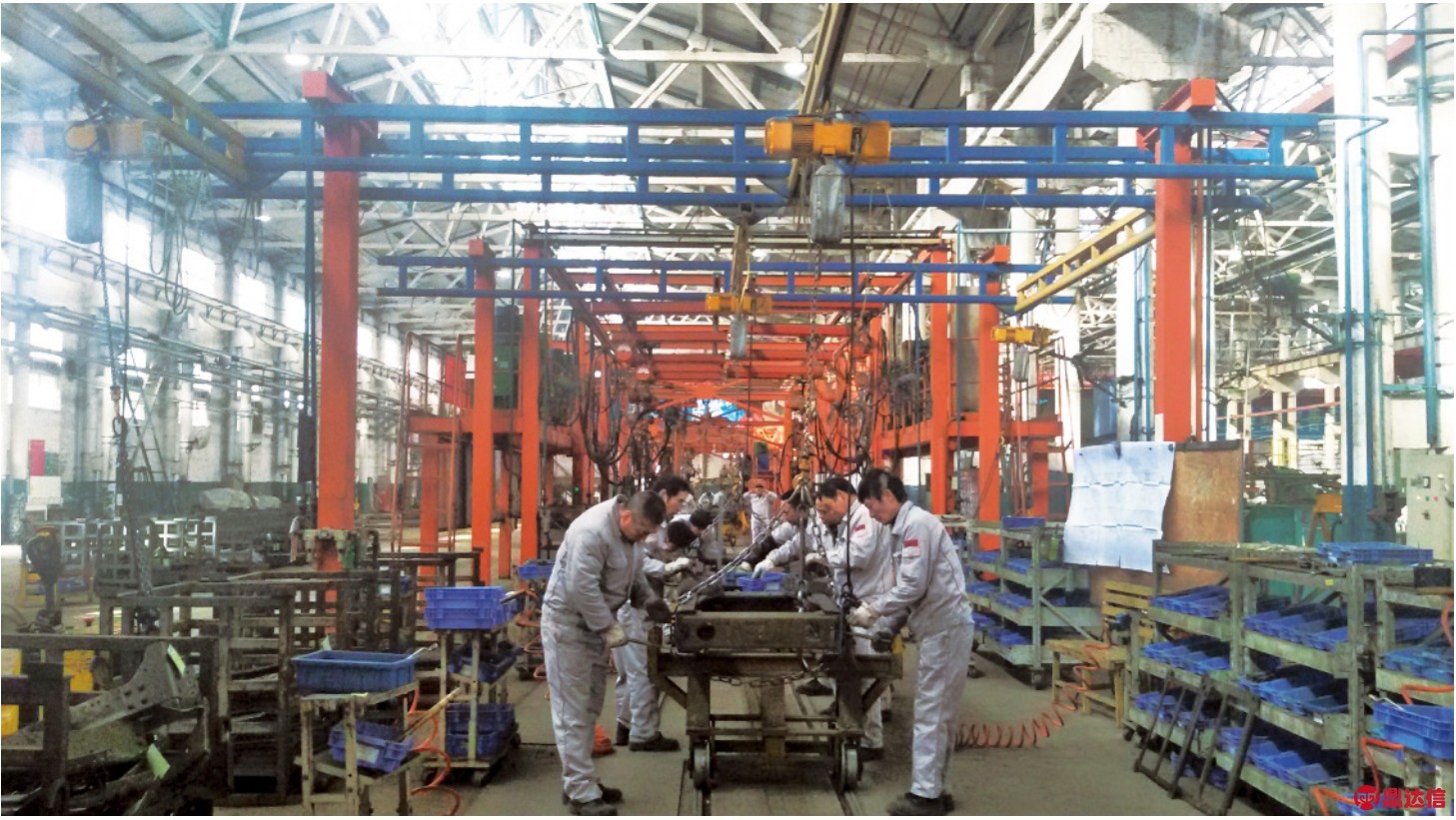
图8 全新试制装配线
(2)涂装技术介绍
油漆托架及总成垫块如图6所示。纵梁及加强梁成形后,被吊运至油漆托架进行摆放,单个托架可存放纵梁三根或加强梁六根,摆放后转运至车架油漆线,上线挂钩吊住托架的四个角,通过油漆下线后进行车架总成装配,装配后车架总成码放时,专用车架总成垫块置于车架总成前端,可避免前端大铸件相互干涉,码放后转运至喷漆线进行车架总成整体喷漆,保证最终油漆表面质量。
4.装配技术
(1)装配类涉及主要产品结构特征
装配类主要涉及相关横梁总成和车架总成装配,横梁总成零部件较多,结构复杂,较厚(7~8 mm)。产品简图如图7所示。
(2)制造技术研究分析
由于横梁总成装配结构复杂,且平衡轴横梁总成需实现一次上线,横梁总成需开发专用装配工装夹具,保证装配的重要尺寸精度和效率。根据产品设计要求,副梁需实现全孔,在主副梁镶合后,需采用螺栓预先固定主副梁相对位置,但是在车架总成装配后,主副梁孔位易产生双眼皮现象,影响装配质量,需对副梁孔进行相应工艺性更改(副梁孔径需加大1 mm,以消除主副梁双眼皮现象)。
(3)装配制造技术应用
试制装配线(见图8)采用全新制造技术设计改造,研究全新的纵梁上线技术和车架拼装技术,采用组合式KPK轨道、电葫芦及专用吊具相结合的方式,实现被吊零件在任意位置快速移动,铆接实现柔性化铆钳悬挂方式,车架总成依靠自动化RGV小车进行工位间转运,新增铆螺栓技术装备,配置多功能车架返修阵地。横梁装配设计全新专用工装夹具,主要采用气缸和定位销进行夹紧和定位,人工定位和气动夹紧相结合,严格保证横梁装配重要尺寸,夹具操作稳定不费力,平衡轴横梁夹具整体具备自动翻转功能,利于横梁整体装配,实现平衡轴横梁总成一次上线,同时配备吊装转运设备,减轻操作人员劳动强度。
关键设备及工装应用介绍
1. 2 500 t油压机
现有中厚板冲压设备,目前主要有大型偏心齿轮机械压力机、大型伺服压力机和油压机3类,机械压力机加工速度快,冲压行程固定,但价格较高,伺服压力机为世界顶级冲压设备,但国内只生产1 000 t以下的设备,大吨位需进口,价格昂贵,油压机工作压力和速度可以在一定范围内调节,在下死点油压机可以进行保压,且价格合适。综合上述分析,结合调研情况,针对横梁高精度要求,我们决定采用2 500 t油压机进行工件成形保压。
2 500 t油压机主要由机身、各种油缸、动力液压系统、电气控制系统、安全系统及其他辅助部件组成。机床结构先进、强度高且刚度好,配置适合厚板冲裁的低噪声冲裁缓冲装置,延长油压机使用寿命,具备保压功能,配置数控主滑块和液压垫,且主滑块工进速度可在8~50 mm/s范围内进行调节,根据模具特性优化工作台结构,保证整机框架结构最优。
2. 机器人焊接工装
为提高焊接质量,减轻员工劳动强度,研究采用机器人自动焊代替手工电弧焊,由于焊缝覆盖区域较小,因此选用ABB小型六轴工业机器人IRB1410,六轴式结合特制焊枪对横梁工艺合件进行全焊缝无死角焊接,六轴式机器人自由度高、运行轨迹精度高,可对横梁焊缝进行精确焊接。焊接电源选用松下YD-500GR3机器人焊接专用电源,焊接电源可与机器人控制器进行信号传递,实现自动化焊接。
3. RGV小车
试制装配线原有小车主要靠人力推动进行工位间转运,且车架产品结构变化,原有小车已无法适应新品装配,本着降低劳动强度、减少作业时间和提高装配效率的原则,经调研分析,自主开发自动化车架总成装配型RGV系统。该系统由一台RGV前端牵引车和一台无动力小车组成,拖动车架总成进行工序间自动化物流转运,RGV小车最大载重量达2 500 kg,可实现遥控自动和单机手动两种方式进行停止和运行,具备顺利转弯和定位功能,提高车架装配柔性化,提升作业效率。
4. 铆螺栓技术装备
根据车型设计要求,车架总成局部需采用铆螺栓制造技术,取代原有螺栓或铆钉连接。经技术研究,相比铆钉连接和高强度螺栓连接,铆螺栓技术具有装配效率高、防松脱效果好、质量检查方便和装配操作性优等特点,且已在国外知名重卡底盘使用多年,技术成熟。
铆螺栓装备主要由液压站、液压机构、枪头和切刀等组成,分为一拖三式和一拖一便携式,液压站提供铆接动力来源,枪头和切刀对铆螺栓进行铆接操作,螺栓由钉杆和套环组成,铆接后钉杆和套环形成无间隙配合,不会造成紧固件松动,且抗疲劳寿命长。
结语
东风商用车公司在不断开发全新战略车型的同时,也在积极提升整车加工质量,对于全新的产品结构和技术要求,工程技术人员需要在冲压、焊接、涂装和装配等制造技术应用中进行深入研讨,以国家工业4.0智能制造长远规划为奋斗目标,在新技术应用过程中,研讨智能制造技术。以机器人搬运、机器人自动化焊接和视觉智能定位系统等多项智能化制造技术与产品有机结合,提升东风商用车公司战略车型制造技术水平和质量。鉴于车架总成产品较重的特点,应用RGV自动化搬运装置系统等自动化技术,把员工从繁重的体力劳动中解放出来,减轻劳动强度,提高产品制造效率和加工质量,使各项技术达到国内领先水平。
随着东风商用车公司工业4.0智能制造工作要求提上日程,针对全新战略车型车架项目,智能化制造技术以及自动化技术的应用应逐步全面展开,降低人工成本,全面提升制造效率和质量,公司制造技术水平的提升,对于国内汽车智能制造技术的发展有一定的推动作用。