本文介绍了一汽解放汽车有限公司卡车厂薄板车间冲压自动化生产线机器人取料及上料的控制方式及压力机的安全角度设置,重点阐述了压力机与机器人之间的安全连锁、运行轨迹干涉情况,分析并阐述了自动化生产线机器人和压力机发生碰撞的原因及改进措施。
一汽解放汽车有限公司卡车厂薄板车间冲压生产线是卡车生产行业中应用较早的自动化生产线,该自动化生产线由上料系统(拆垛头、过渡皮带机、清洗机、涂油机、对中台、上料手)、5台压力机(首台2050t双动压力机、4台1000t单动压力机)以及6台4轴机器人组成。该冲压自动化生产线自建成以来,先后承担马自达6型轿车、红旗轿车、J5卡车、J6卡车等车型的大型外表面覆盖件及大型结构件的冲压任务。
该生产线在生产时,发生过多次机器人和压力机或模具相撞的事故,导致机器人端拾器变形、损坏,影响生产节拍。如何保证自动化生产线各个设备的安全运行,防止机器人和压力机、模具发生碰撞,是自动化生产线设备安全使用的一个重要课题。
冲压自动化生产线机器人的控制方式及设置
冲压自动化生产线有5个操作站分别控制6个机器人(R1和R2共用一个操作站,注:R1、R2分别代表1号机器人及2号机器人,下同)的角度设置及驱动、自动、循环等控制。角度设置包括前方压力机的偏置角度、当前角度,前方和后方压力机的安全位置角度,机器人取料角度等内容,如图1所示。
冲压自动化生产线操作站的参数设置主要考虑以下几点因素:
⑴机器人上料需要压力机满足连线、单次行程条件,压力机滑块位置在安全角度之上,并且后方机器人发出取料离开的信号或者后方机器人处于安全位置。
⑵机器人取料需要压力机满足连线、单次行程条件,压力机滑块位置在安全角度之上,并且前方机器人发出上料离开的信号或者前方机器人处于安全位置。
⑶通过总控室PLC、触摸屏、工控机、编码器、机器人控制柜,压力机控制柜对自动化生产线压力机及机器人进行动作控制及监控。
压力机与机器人之间安全连锁
压力机与机器人之间的安全连锁主要是机器人的取料、上料角度(压力机滑块角度)和机器人离开压力机的位置信号,机器人或者压力机的安全门、急停信号都会使相邻的压力机和机器人停止动作。
压力机与机器人运行轨迹干涉的原因分析及改进措施
图2所示为机器人取、送料轨迹。虽然压力机与机器人之间有安全连锁,但也常常会出现机器人和压力机发生轨迹干涉的情况,造成压力机或已安装的模具与机器人碰撞的故障。经分析,其原因主要有两个方面:第一是自动化生产线控制程序设计不严谨,其次为压力机运行状态不稳定。
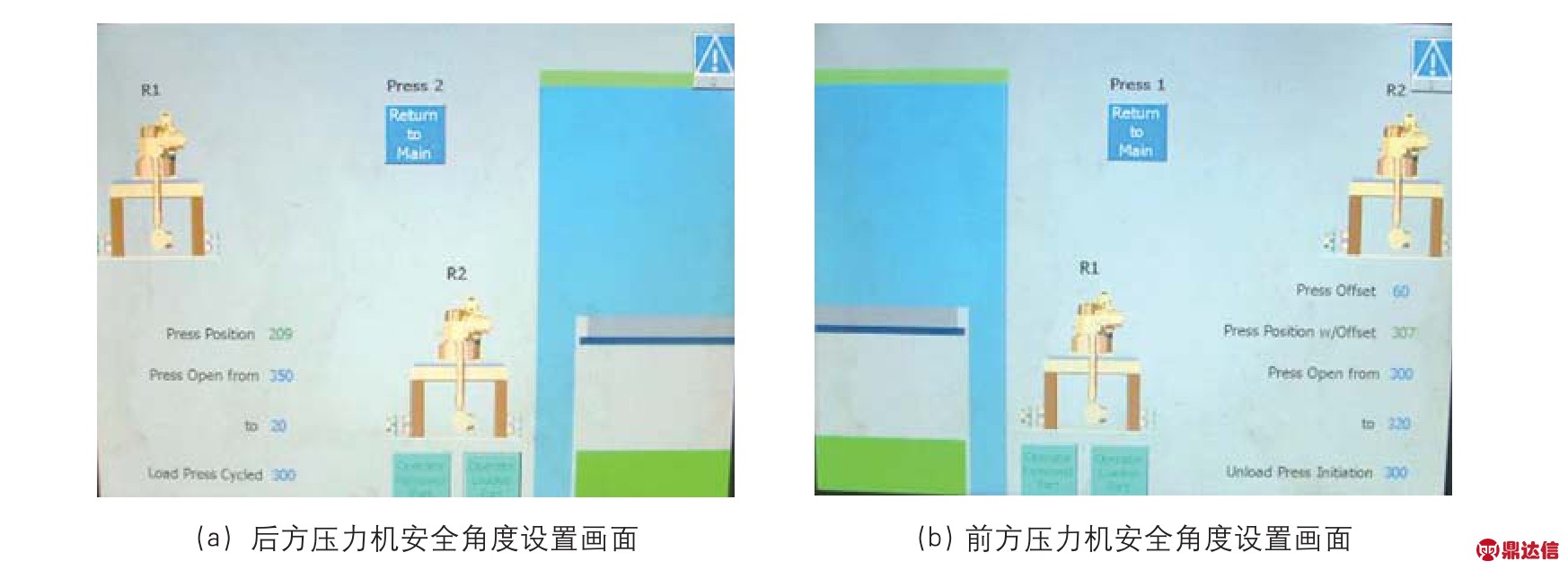
图1 操作站的设置
我们通过分析6次压力机与机器人运行时发生轨迹干涉并造成碰撞的事故案例,基本找到造成轨迹干涉的原因,并逐一制定措施进行了改进。
案例1
问题点:1000t压力机在回程(下死点到上死点)运行时,没到上死点却突然停止。机器人取件,导致机器人端拾器和压力机模具发生碰撞。
原因分析:⑴压力机停车角度在机器人允许取件的范围之内,所以机器人取件;⑵模具气夹夹紧信号丢失导致压力机行程停止。
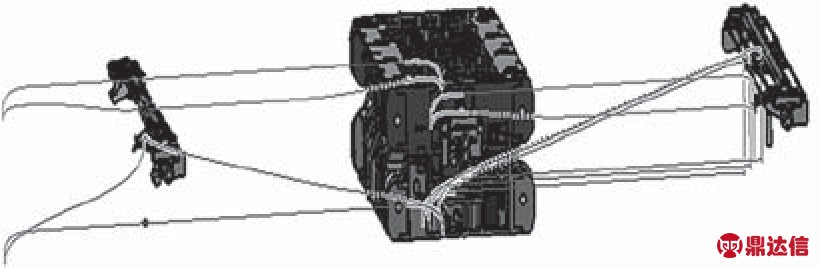
图2 机器人取、送料轨迹
改进措施:⑴取消模具气夹接近开关;⑵在压力机程序中删除模具夹紧连锁信号;⑶使用气夹安装模具时,操作者应先检查气夹是否夹紧到位。
案例2
问题点:压力机启动行程时,机器人取件,导致机器人端拾器和压力机模具发生碰撞,甚至端拾器被压在模具内。
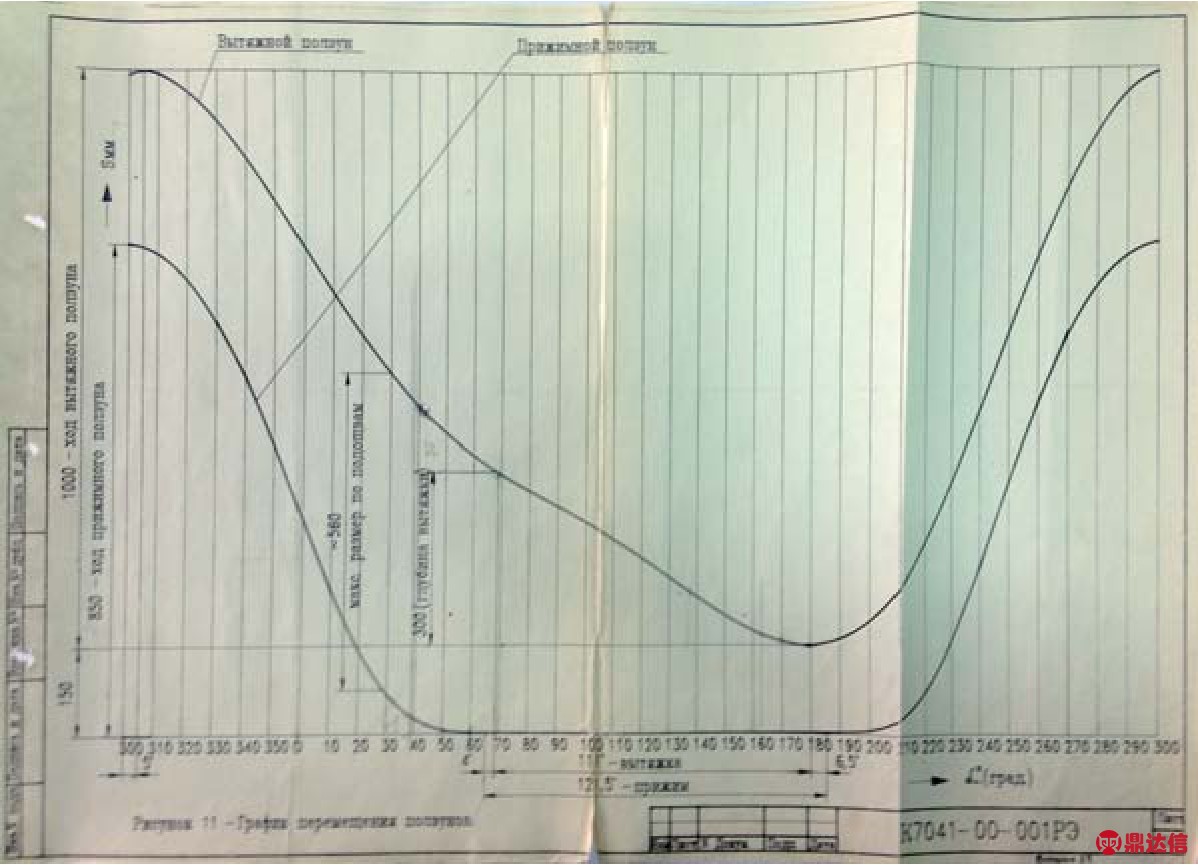
图3 内、外滑块角度曲线图
原因分析:机器人编码器内部联轴节紧固螺丝松动或螺纹损坏,传动轴与编码器连接轴不同步,导致机器人送件、取件角度发生改变,改变后的角度符合机器人取件角度。
改进措施:对机器人编码器内联轴节紧固螺丝采用防松胶粘接。
案例3
问题点:123-132号压力机连线生产时使用穿越模式,R4放件到压力机工作台过渡支架上离开,R5取件时,压力机开启行程,导致R5端拾器和压力机发生碰撞。
原因分析:⑴操作失误,压力机使用穿越模式时,不应该开启主电机,并且满足连线起动行程的条件;⑵自动化生产线程序设计不严谨。
改进措施:⑴修改自动化生产线总控室FC22、FC23、FC24、FC25程序;⑵在1000t压力机使用穿越模式时,防止自动起动压力机行程。
案例4
问题点:123-129(2050t)号压力机在起动行程时,R1取件,导致机器人端拾器和压力机模具发生碰撞。
原因分析:2050t压力机进行现场总线改造后,原压力机行程角度显示为外滑块,改为显示内滑块角度(图3),导致R1机器人取件角度发生很大的偏差。
改进措施:⑴修改自动化生产线总控室FC21、FC11程序;⑵设置R1操作站各个角度。
案例5
问题点:123-129(2050t)号压力机在开动行程时,R1取件,导致机器人端拾器和压力机模具发生碰撞。
原因分析:⑴操作失误,在操作站上强制R1取料;⑵平衡气缸压力设置和模具大小不匹配;⑶自动化生产线程序设计不严谨。
改进措施:修改自动化生产线总控室FC21程序。
案例6
问题点:1000t压力机在开启行程时,后面机器人取件,导致机器人端拾器和压力机模具发生碰撞。
原因分析:⑴操作失误,在操作站上强制机器人取料;⑵平衡气缸压力设置和模具大小不匹配;⑶自动化生产线程序设计不严谨。
改进措施:修改自动化生产线总控室FC22、FC23、FC24、FC25 程序。
效果验证
经过多次改进,避免了上述故障引起的冲压自动化生产线机器人和压力机发生碰撞,保护了机器人端拾器和模具的正常使用,也保证了自动化生产线生产的顺利进行。
结束语
此冲压自动化生产线自2003年投入生产以来,技术维修人员通过不断学习和摸索,目前已经能够独立解决自动化生产线出现的常见故障,并对自动化生产线软件也进行了一些小的改进,如防止自动化生产线机器人和压力机发生碰撞、翻译自动化生产线图纸、翻译自动化生产线上料系统及总控室操作站PLC程序注释、清洗机自动润滑程序改进等。这些工作不仅增加了我们对自动化生产线设备的了解程度,也提高了我们的维修技术水平。但是在自动化生产线提速方面还有一些问题没有得到解决,如在压力机没有停到上死点时,机器人提前进入模具内取件;机器人上料后没有完全离开压力机时,起动压力机行程。在以上情况下压力机和机器人没有安全连锁,这时如果压力机或机器人出现故障都会导致压力机和机器人发生碰撞等。
随着冲压设备新技术的不断应用,对设备管理人员的技术水平也提出了更高的要求,只有通过不断的学习,拓宽视野,提高自身的技术水平,才能为设备管理工作做出更大的贡献。