摘 要: 为明确西南管道3PE防腐蚀涂层(有孔和无孔)剥离的原因,通过现场调研初步明确了涂层剥离的主要原因,并通过电化学测试分析了破损涂层下涂层/金属界面上电解质的扩散过程,通过差示扫描量热法分析了剥离涂层和未剥离涂层的玻璃化转变温度。结果表明:当涂层发生破损时,电解质在涂层/金属界面上的扩散是引起涂层剥离的主要原因,其扩散过程分为腐蚀缝隙形成过程、氧浓差腐蚀过程和析氢腐蚀过程三个阶段;当涂层完好却发生大面积剥离时,这主要是由于环氧底层的玻璃化转变温度太低导致其与基体结合力不够引起的。
关键词: 3PE防腐蚀涂层;剥离;阴极保护;涂层/金属界面;玻璃化温度
防腐蚀涂层是保护埋地管道免遭外界腐蚀的第一道防线[1],其保护效果直接影响着阴极保护的工作效率。其防腐蚀作用主要表现在三个方面[2]:首先,防腐蚀涂层将金属管道与周围腐蚀性介质分开,防止电化学腐蚀反应的发生,并且能够减少大地中的杂散电流流入管道;其次,防腐蚀涂层减轻了在施工或者运行过程中管道受到的机械损伤以及应力集中问题;再次,防腐蚀涂层较高的电阻率使得阴保电流分布更加均匀,在相同阴保电流下能够保护更长的管道,降低了阴保电流损耗。
3PE防腐蚀涂层由底层环氧层、中间胶黏层和外层PE层构成。在管道运行过程中,3PE防腐蚀涂层在某些条件下总会发生阴极剥离现象,其主要分为剥离有孔状态和剥离无孔状态两种。发生阴极剥离的原因可能包含以下几个方面:1) 在管道施工或运行过程中,难免会发生防腐蚀涂层的局部破损,大地中的杂散电流从破损处流入管道,引起管地电位负向移动,发生析氢导致涂层进一步剥离,而电流从破损处流出时也会引起管道腐蚀,形成腐蚀缝隙,从而导致防腐蚀涂层的剥离[3]。2) 若管道最外层PE层发生破损,土壤中的水或电解质会进入内层环氧层,并通过扩散到达涂层/金属界面,发生电化学反应,产生的碱性环境和腐蚀产物的积聚会破坏涂层与金属之间的结合键,引起涂层剥离[4]。3) 特高压电力干扰以及其他条件引起的管道阴保电位剧烈震荡或大幅度偏移,会导致管道析氢,这也会引起防腐蚀涂层的剥离。4) 加工条件或加工参数不合适,同样会引起的防腐蚀涂层剥离。
从上述分析可以看出,引起3PE防腐蚀涂层剥离的原因有很多。因此,本工作针对某西南管道3PE防腐蚀涂层剥离的现状,通过现场实际调研得到管道阴保电位和防腐蚀涂层相关参数,然后通过在实验室测试涂层剥离过程中的电化学阻抗谱分析了破损涂层下涂层/金属界面上电解质的扩散过程,通过差示扫描量热法分析了剥离涂层和未剥离涂层的玻璃化温度,揭示引起管道防腐蚀涂层剥离的主要原因,阐释了防腐蚀涂层失效的主要过程。
1 试验
1.1 现场调研
针对某西南管道3PE防腐蚀涂层剥离现状,现场分别对涂层剥离点处管道的阴保电位、防腐蚀涂层参数、地形进行了测试及描述。防腐蚀涂层参数主要包括破损点数量(现场电火花检测)、损失尺寸(现场通过游标卡尺读取破损点的轴向和径向尺寸)和电阻率(现场采用电压降法测试)三个方面[5]。
1.2 电化学阻抗谱测试
电化学阻抗谱(EIS)测试在PARSTAT2273电化学工作站上进行,并采用三电极体系:辅助电极为铂电极,参比电极为饱和甘汞电极(SCE),工作电极为涂层存在破损点的X60钢,如图1所示[6]。工作电极加工过程:选取现场带有3PE防腐蚀涂层管段,切割成150 mm×150 mm×壁厚的试片,采用数字精雕机在试片涂层上制备缺陷孔(φ6.4 mm),以露出明显的金属基体为止,并将孔内涂层材料清理、修整;在试片底面打磨出两处金属光亮位置用于导线连接。试验溶液为3.5%(质量分数)的NaCl溶液,溶液高度为塑料圆筒高度的75%;通过恒电位仪实时监测将阴保电位控制在-1.0 V;电化学阻抗谱扫描范围为10 mHz~100 kHz;电化学阻抗谱处理采用系统自带的 ZSimpWin软件[7]。
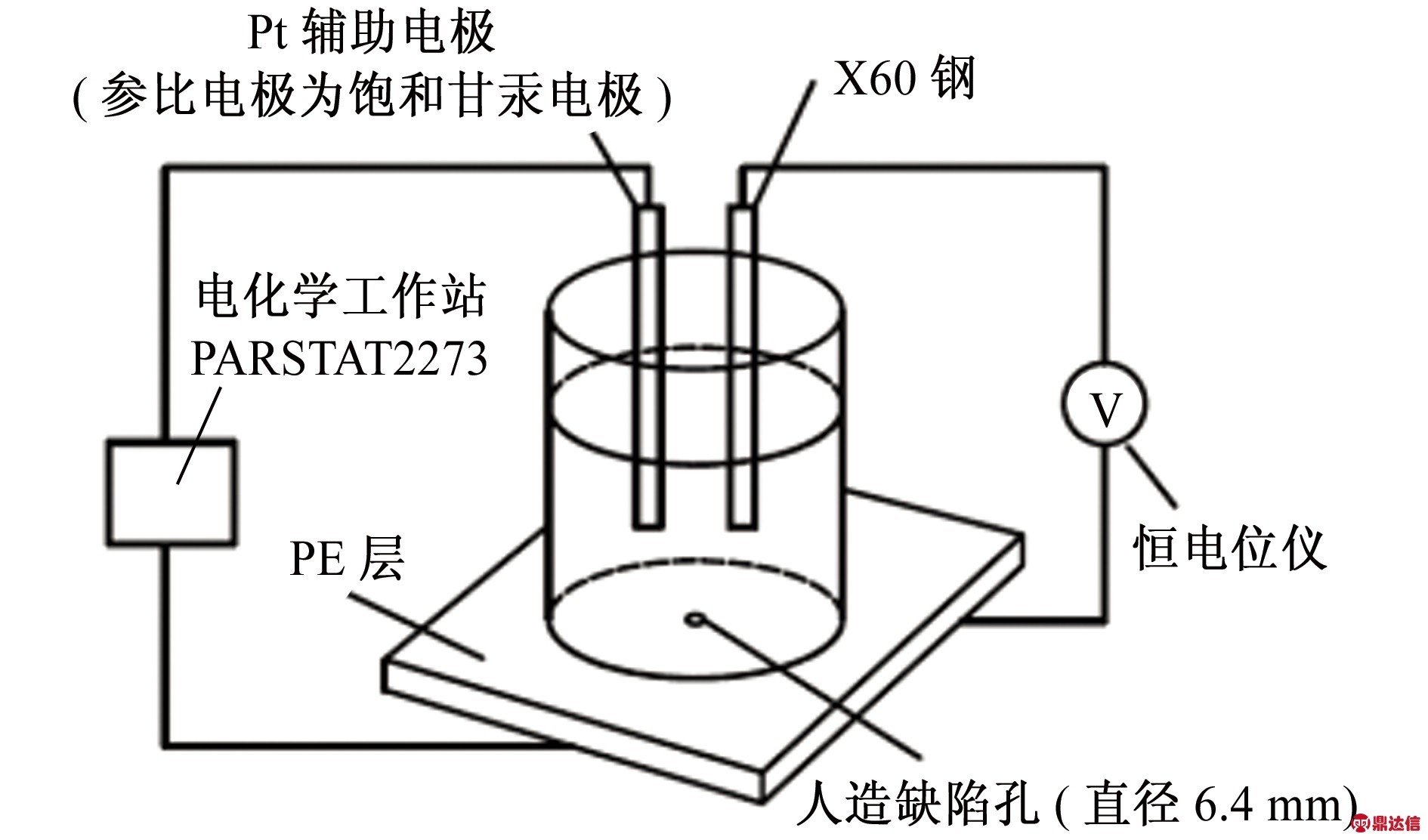
图1 阴极保护下涂层剥离过程中EIS测试的试验装置
Fig.1 Experimental device for EIS testing in coating
delamination under cathodic protection
1.3 差示扫描量热测试
3PE防腐蚀涂层中影响管道金属与防腐蚀涂层连接程度的是底层环氧层。环氧层以其较高的交联密度和与金属较好的连接程度而被广泛应用。其中反映环氧层性能的主要指标为其交联程度,可通过差示扫描量热法(DSC)来测试。因此,采用DSC分别对现场环氧层以及实验室单层环氧层的玻璃化转变温度进行测试。先取6~8 mg环氧层试样置于密闭铝箔中,在氮气环境中将试样加热至200 ℃,加热速率为10 ℃/min,通过差示扫描量热仪测DSC曲线。
2 结果与讨论
2.1 现场调研结果
从表1中数据可以看出,3PE防腐蚀涂层剥离点处管道的阴保电位为-1.36~-0.97V,基本满足阴极保护电位范围(-1.20~-0.85 V)的要求[8];但是无论是在平原还是山地,涂层均存在破损点,如图2所示,地下水的侵蚀、扩散是造成涂层剥离的原因之一;在第二个测试点处,防腐蚀涂层可徒手撕开,且已大面积脱落,这可能与涂层黏结不紧密、加工参数异常有关。因此,在现场测试的基础上,需对涂层与金属界面上的扩散过程以及现场环氧层的玻璃化转变温度进行测试,这对明确现场防腐蚀涂层发生剥离的原因有着十分重要的意义[9]。
表1 现场调研得剥离3PE防腐蚀涂层的相关参数
Tab. 1 Parameters of delaminated 3PE anti-corrosion coating obtained by field survey
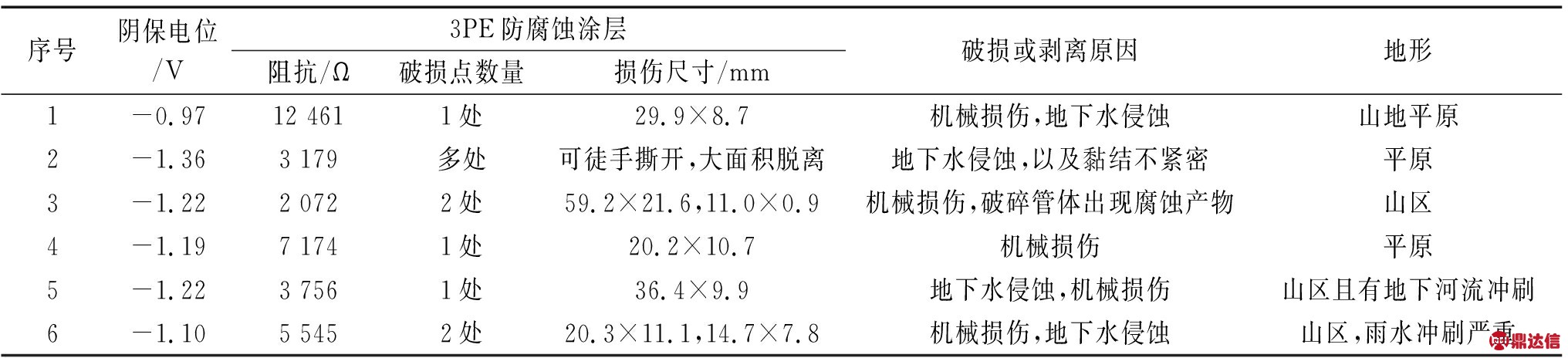
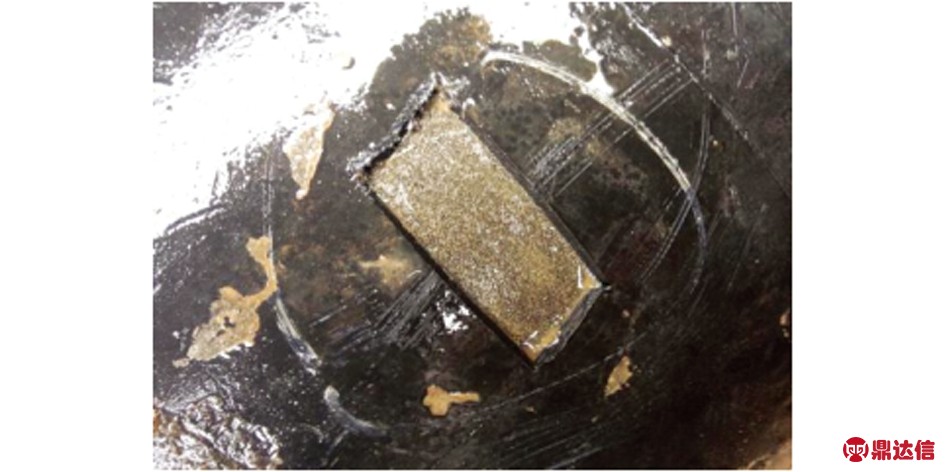
图2 现场3PE防腐蚀涂层剥离照片
Fig.2 Picture of delamination of 3PE anti-corrosion
coating in field
2.2 涂层/金属界面的扩散过程
电化学阻抗谱测试数据反映了在阴极保护条件下水在涂层/金属界面上的扩散和反应过程。图3为阴极保护下(-1.0 V)涂层存在破损点的X60钢在3.5% NaCl溶液中的Nyquist图,表2为电化学阻抗谱的拟合结果。在整个试验周期内,由于PE层本身的特性,不考虑水法向扩散对界面的影响,因此根据电化学阻抗谱及其拟合结果可以发现,整个反应过程(0~168 h)主要包含三个阶段。
第一阶段(0~72 h),当试验进行至24 h时,阻抗谱表现为1/4容抗弧与扩散阻抗相连,这表明此时电解质已经在界面上逐步发生扩散:在阴保电位的作用下,中性溶液中阴极主要发生吸氧反应,阳极为铁溶解反应,分别见式(1)和式(2);当试验进行到48 h时,整个过程依然是以扩散为主,没有形成明显的扩散通道/腐蚀缝隙,此时表现为涂层电容Cc增大,电阻降低,扩散阻抗表现为“不理想”(n≈0.75)的韦伯阻抗[10];当试验进行到72 h时,电化学阻抗谱依然存在扩散阻抗尾巴[11-12],但是容抗弧直径明显减小,此时涂层电容与扩散阻抗均明显增大,说明此时扩散通道/腐蚀缝隙正在逐渐形成,而电解质中的氧气也逐渐消耗殆尽[13-14],金属表面双电层逐渐形成。在这一过程中时间常数τ=Cc·Rc基本不变。
阴极反应:O2+2H2O+4e-4OH-
(1)
阳极反应:FeFe2++2e-
(2)
第二阶段(72~144 h),当试验进行到96 h时,此时扩散阻抗已经消失,阻抗谱基本表现为1/4容抗特征,随着反应的进行,腐蚀缝隙已经形成,由于缝隙内部为相对闭塞状态,外部氧气很难进入到缝内,因此形成了缝口富氧、缝内缺氧的氧浓差电池,此时缝内只发生金属的溶解和水解反应,见式(3);在接下来的36 h内,整个体系依然以氧浓差腐蚀机理为主。在这一过程中时间常数τ=Cc·Rc也基本保持不变。
Fe+2H2OFe(OH)2+2H++2e-
(3)
第三阶段(168 h),当试验进行到168 h时,阻抗谱表现出明显的韦伯扩散过程(n≈0.5),并且双电层电容明显增大:在过保护条件下,根据IR降理论[15-16],金属/涂层体系可能发生析氢反应,在金属表面形成氢吸附层,见式(4),表现为电荷转移电阻Rct减小,而双电层电容Cdl增大。
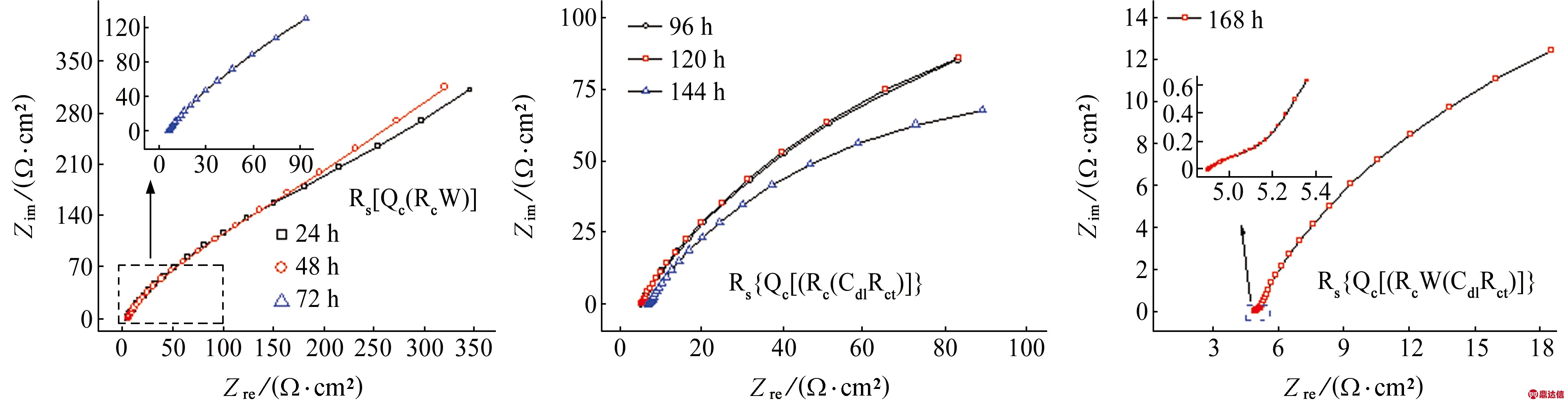
(a) 24~72 h(b) 96~144 h(c) 168 h
图3 不同测试时间时在阴极保护下(-1.0 V)涂层存在破损点的X60钢在3.5% NaCl溶液中的Nyquist图
Fig.3 Nyquist plots of X60 steel with damaged coating in 3.5% NaCl solution under cathodic protection (-1.0 V)
at different test time
表2 图3中电化学阻抗谱的拟合结果
Tab. 2 Fitted results of EIS in Fig.3
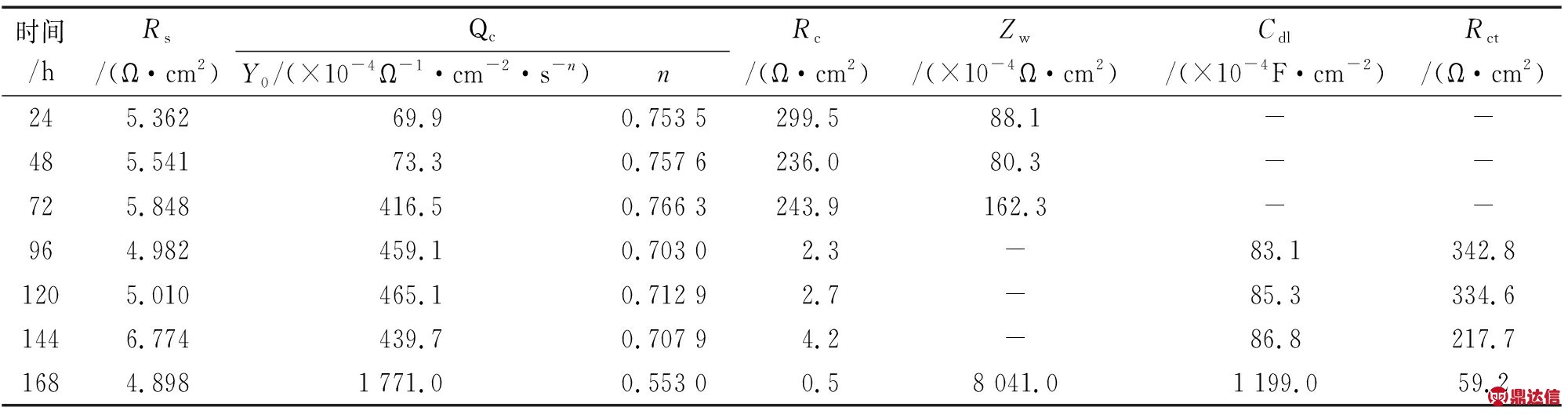
H2O+e-Had+OH-
(4)
因此,在阴极保护条件下,界面上的电化学反应(氧的去极化和金属失去电子)为“不理想”的韦伯扩散,使涂层逐渐发生剥离形成腐蚀缝隙;当腐蚀缝隙形成后,整个体系以缝内为阴极、缝外为阳极的氧浓差腐蚀为主,此时逐渐形成明显的双电层;当缝隙长度达到一定值时,在阴极保护条件下,金属可能发生析氢反应,形成氢吸附层,此时腐蚀缝隙前锋位置的物理结构(闭塞)和电化学反应条件(缺氧、存在水和阴极保护)与涂层界面反应相同,因此当水达到涂层/金属界面时,阴极过程以析氢反应为主[17],而阳极主要为金属失去电子变为金属阳离子,进而发生水解反应。
图4为不同测试时间时在阴极保护下(-1.0 V)涂层存在破损点的X60钢在3.5% NaCl溶液中的Bode图。根据相位角θ的测试数据可以发现,整个试验过程可以分为三个阶段。
在第一阶段(0~48 h),当频率f为0.5 Hz时,出现最大相位角θmax,约为55°,此时低频区域表现为“不理想”的电容特征,弥散系数n约为0.75,溶液向涂层/金属界面上的扩散已经发生,并且在存在破损点条件下,涂层的电容性质已经被打破,这也是导致在测试初期整个测试频率范围内相位角偏离90°的主要原因。
当试验进行到第二阶段(48~144 h)时,在72 h测试点处,最大相位角相比于48 h时的小幅增大,72 h时的Nyquist图仍然带有扩散阻抗的尾巴,但是体系的电容发生明显增大,此时腐蚀缝隙和双电层逐步形成。随着试验时间的延长,均在频率为0.07 Hz时出现最大相位角,且逐渐减小,这也意味着在这一阶段涂层/金属界面以腐蚀缝隙与形成双电层为主[18]。
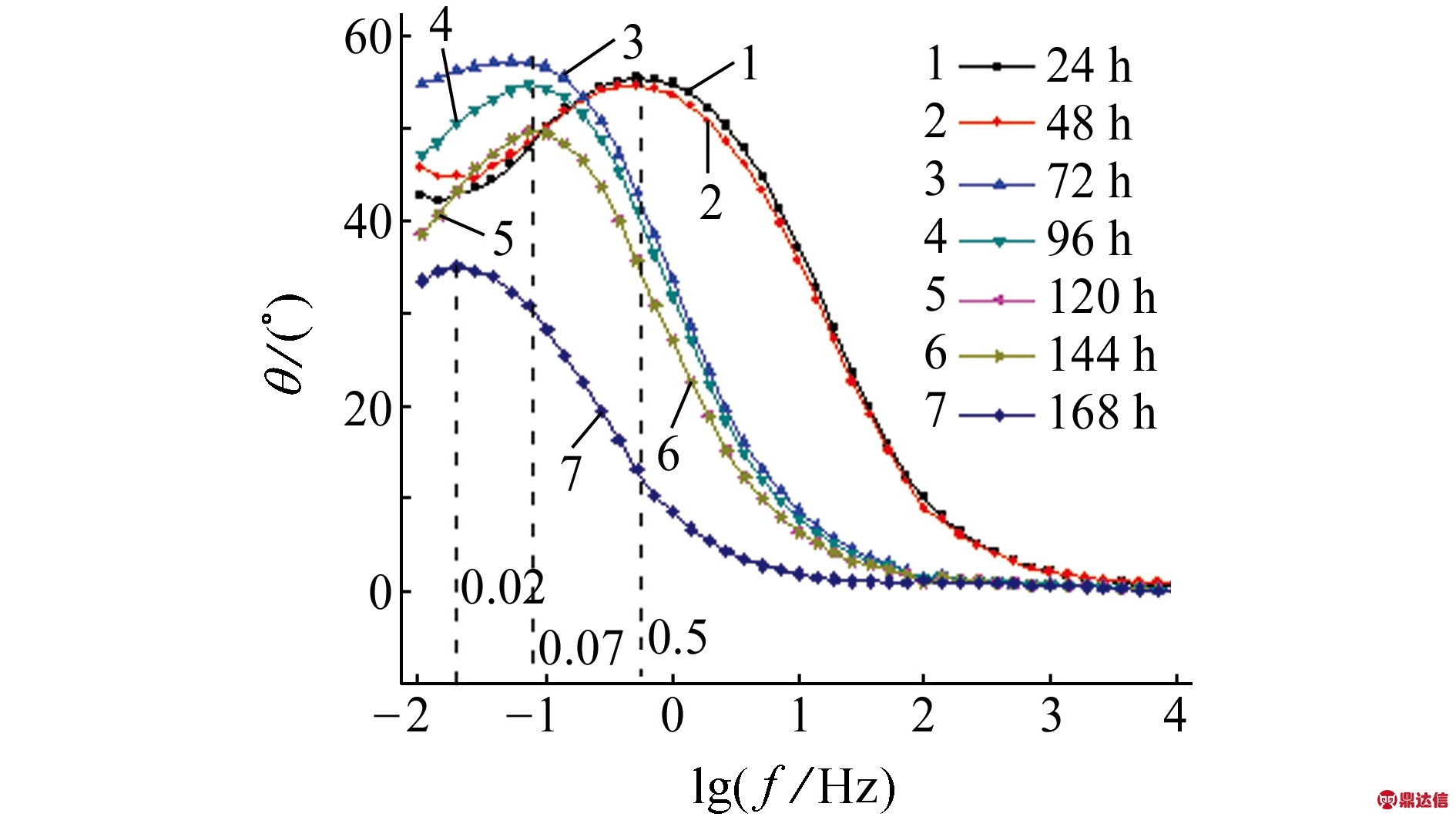
(a) lgf-θ
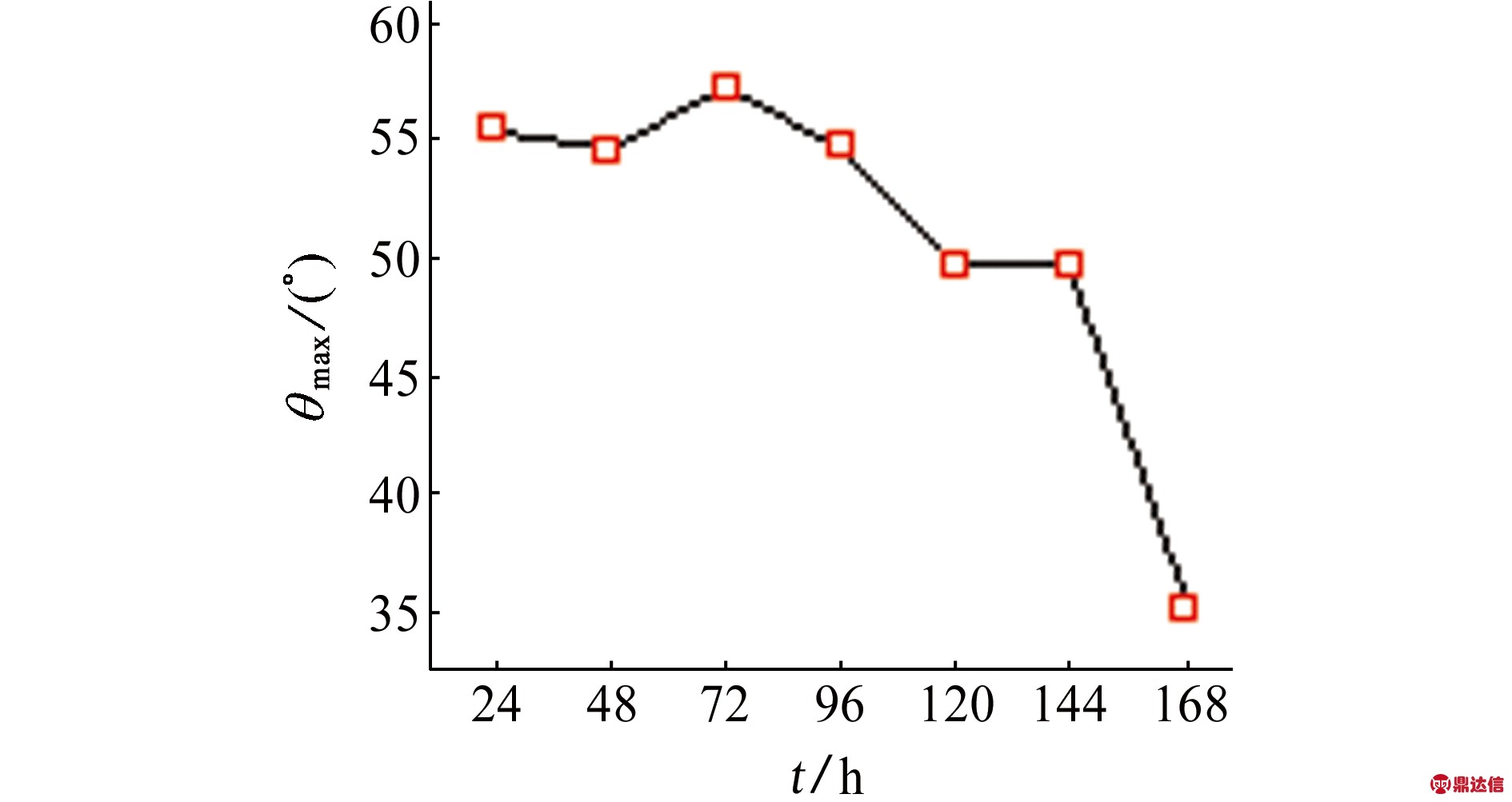
(b) θmax-t
图4 不同测试时间时在阴极保护下(-1.0 V)涂层存在
破损点的X60钢在3.5% NaCl溶液中的Bode图
Fig.4 Bode plots of X60 steel with damaged coating in
3.5% NaCl solution under cathodic protection (-1.0 V)
at different test time
在第三阶段(168 h),在频率为0.02 Hz时,最大相位角减小为35°,此时体系的阻抗特征从高频区转移到0.5 Hz附近的低频区,并且n约为0.5,这说明涂层/金属界面上的双电层已经形成并且逐渐向腐蚀缝隙内部延伸,整个体系由容性逐渐向阻性转变,物质转移过程逐渐取代电荷转移过程[19],因此在第三阶段,腐蚀缝隙和双电层都已经形成,在阴极保护条件下,缝隙内部以析氢反应为主。
2.3 环氧层的玻璃化转变温度
图5为在室温实验室测得的单层环氧层的玻璃化转变温度Tg随固化时间t的变化。结果表明,在室温环境中自然固化,随着固化时间的延长,单层环氧层的玻璃化转变温度快速升高,固化时间延长至4 d后,其玻璃化转变温度达100 ℃左右,在随后的3 d内缓慢升高,最终稳定于105 ℃,这表明环氧层已完全固化,涂层内部的交联程度较高[20-21],因此可以认为环氧层的玻璃化转变温度为105 ℃。
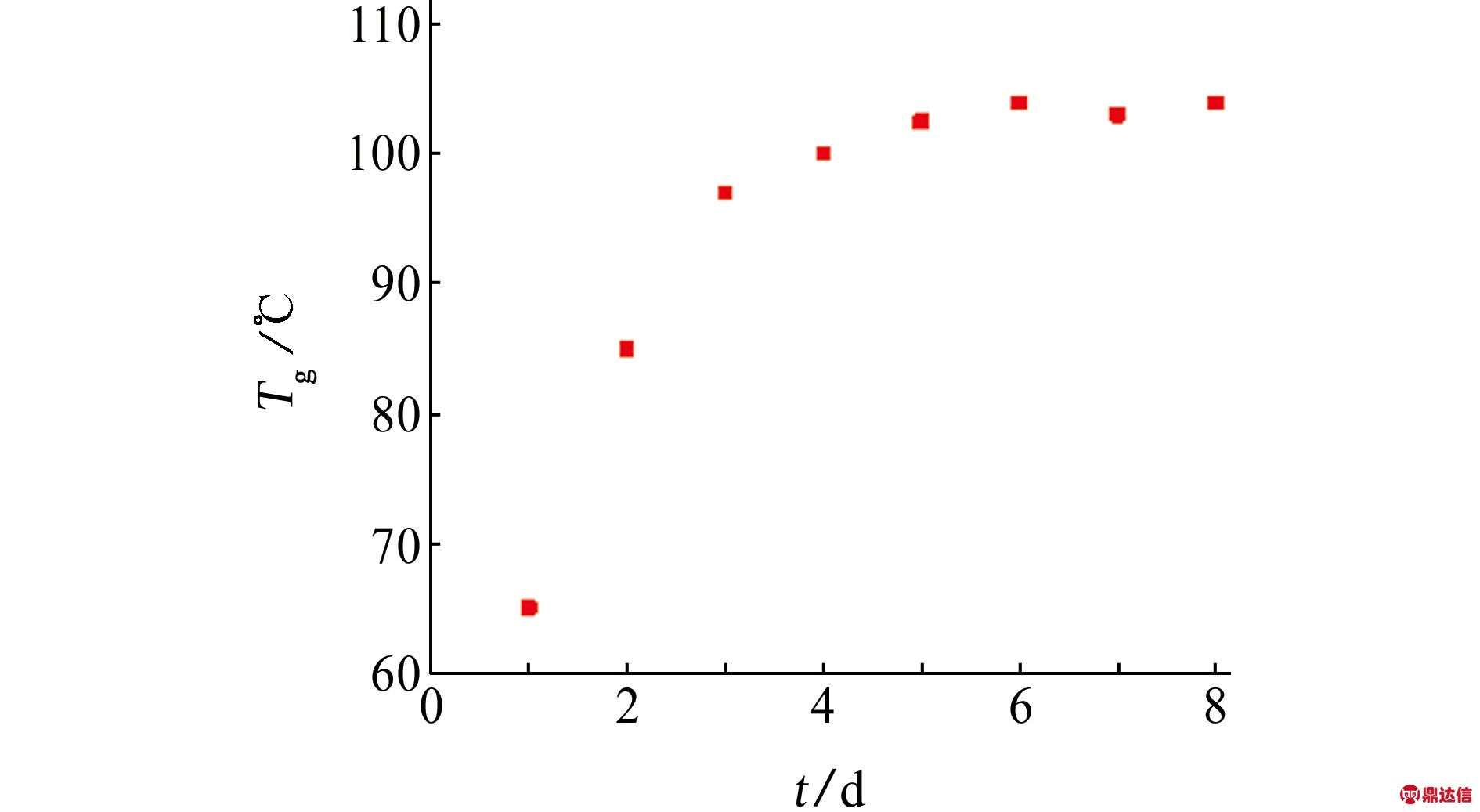
图5 单层环氧层的玻璃化温度随固化时间的变化
Fig.5 Relationship of glass transition temperature of
single epoxy coating and curing time
图6为现场未剥离涂层和剥离涂层中环氧层的DSC曲线。从图6中可以看出,未剥离环氧层的玻璃化转变温度为100 ℃,与实验室测试结果基本吻合,而剥离环氧层的玻璃化转变温度只有70 ℃,远小于实验室测试结果。大面积防腐蚀涂层可徒手撕掉,是因为其环氧底层的加工温度/固化时间不够,导致其环氧层内各物质间的交联密度不够,从而降低了环氧层与金属之间的结合力,最终导致涂层脱落。
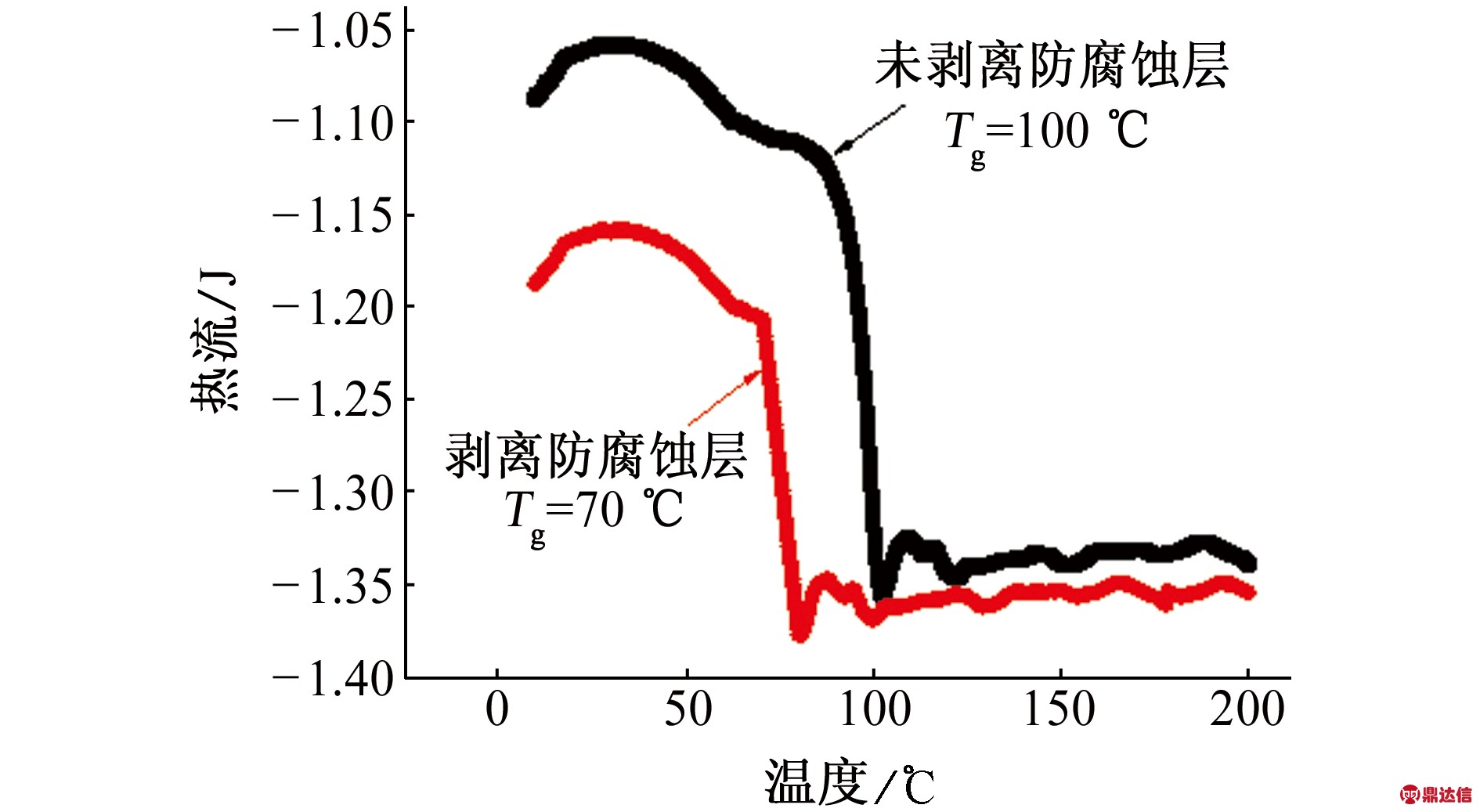
图6 现场未剥离涂层和剥离涂层的DSC曲线
Fig.6 DSC curves for coatings with and without
delamination in field
3 结论
(1) 当外力作用导致3PE防腐蚀涂层发生破损时,电解质在涂层/金属界面上的扩散是涂层发生剥离的主要原因。在阴极保护作用下,电解质在涂层/金属界面上的扩散主要分为三个过程:腐蚀缝隙形成过程、氧浓差腐蚀过程和析氢腐蚀过程。
(2) 当3PE防腐蚀涂层完好却发生大面积剥离时,其主要原因是加工温度/固化时间不够,导致其环氧层内各物质间的交联密度不够,从而降低了环氧层与金属之间的结合力,最终导致涂层脱落。