摘 要:为了研究盘形滚刀刀圈在轧制过程中的变形特点,提高盘形滚刀刀圈的综合性能,本文通过建立刀圈轧制成形的有限元分析模型,研究刀圈在轧制成形过程中等效应力场、等效应变场的演变规律和流线分布特点,并研究刀圈初始轧制温度、主辊摩擦因子和主辊转速对刀圈成形件质量的影响规律。利用D53K-800立式轧环机对刀圈进行轧制试验研究,并对轧制后的刀圈进行金属流线分析。刀圈轧制后金属流线沿其截面几何形状分布,流线光滑且封闭。结果表明:刀圈等效应变随温度变化不大,其值在1.93左右;主辊摩擦因子过大或过小,刀圈等效应变和应力的平均值和标准差均会增加;主辊转速为2.632 rad/s时等效应力的标准差最大。
关键词:全断面岩石掘进机; 滚刀刀圈; 轧制成形; 数值模拟; 试验研究; 金属流线; 有限元分析
全断面岩石掘进机(full-face rock tunnel boring machine,TBM)因其高效性和安全性已被广泛应用于地下建筑工程[1]。盘形滚刀作为其掘进过程中实现破碎剥离岩土、碴土过流、界面支护功能的关键部件[2],与岩石直接接触,受到强烈的冲击和突变载荷[3],容易出现磨损、崩刃、卷刃和断裂,大量失效无疑会增加停机和换刀次数,影响TBM的掘进效率,增加施工成本。刀圈的成形工艺很大程度上决定了其硬度、韧性等力学性能和使用性能。滚刀刀圈属于异形截面环件,相对于矩形截面、梯形截面等通用截面环件,异形截面环件的轧制成形工艺条件要求更高、更复杂。环件轧制是一种生产无缝环件的特种加工工艺[4]。针对环件轧制技术,国内外学者进行了大量的研究:Giorleo等[5]和Li等[6]建立了环件轧制的有限元模型,并通过实验和仿真对比分析了有限元模型的精度;丁敬国等[7]通过计算钢锭头尾展宽后的宽度差异,提出了钢锭的楔形轧制法;Qian等[8-9]对环件轧制中的轧辊尺寸和工艺参数进行了理论设计和实验验证;Anjami等[10]研究了轧辊尺寸对环件轧制过程的影响;李永堂等[11]通过理论分析和数值模拟,研究了42CrMo钢铸坯环件辗扩成形过程中变形工艺参数对金属变形和组织演变规律的影响;Parvizi[12]和Abrinia等[13]研究了摩擦因子、进给速度等工艺参数对工艺过程的影响并获得轧制力;Zhu等[14]、Kim等[15]和贺小明等[16]对环件轧制过程的有关工艺参数进行了优化;支颖等[17]提出了4种类型的变厚度轧制过渡区,并建立了4种类型过渡区曲线的数学模型。以上研究主要针对通用环形零件进行,针对盘形滚刀刀圈的成形工艺鲜有研究。本文以17 in(43.18 cm)滚刀刀圈为研究对象,对其轧制成形过程中的工艺参数进行设计,建立了刀圈轧制成形的有限元模型,分析了刀圈在轧制成形过程中的变形特点,研究了摩擦因子、始锻温度等工艺参数对刀圈成形件质量的影响,并进行了刀圈轧制成形和流线观察试验。
1 盘形滚刀刀圈轧制成形有限元模拟
1.1 刀圈轧制成形有限元模型建立
所选轧环机主辊转速为40 r/min,锥辊转速为9.6 r/min。结合毛坯和模具参数,芯辊进给的极限速度范围为1.08~2.84 mm/s[18],根据生产经验在该范围内取芯辊进给速度为1.3 mm/s。由环件轧制成形工艺毛坯设计公式,并结合17 in(43.18 cm)平底刀圈产品尺寸设计出毛坯尺寸,如图1所示。主辊尺寸为φ520 mm×φ760 mm×200 mm,芯辊尺寸为φ100 mm×160 mm。刀圈轧制成形的三维有限元模型包括刀圈毛坯、主辊、芯辊和锥辊,如图2所示。
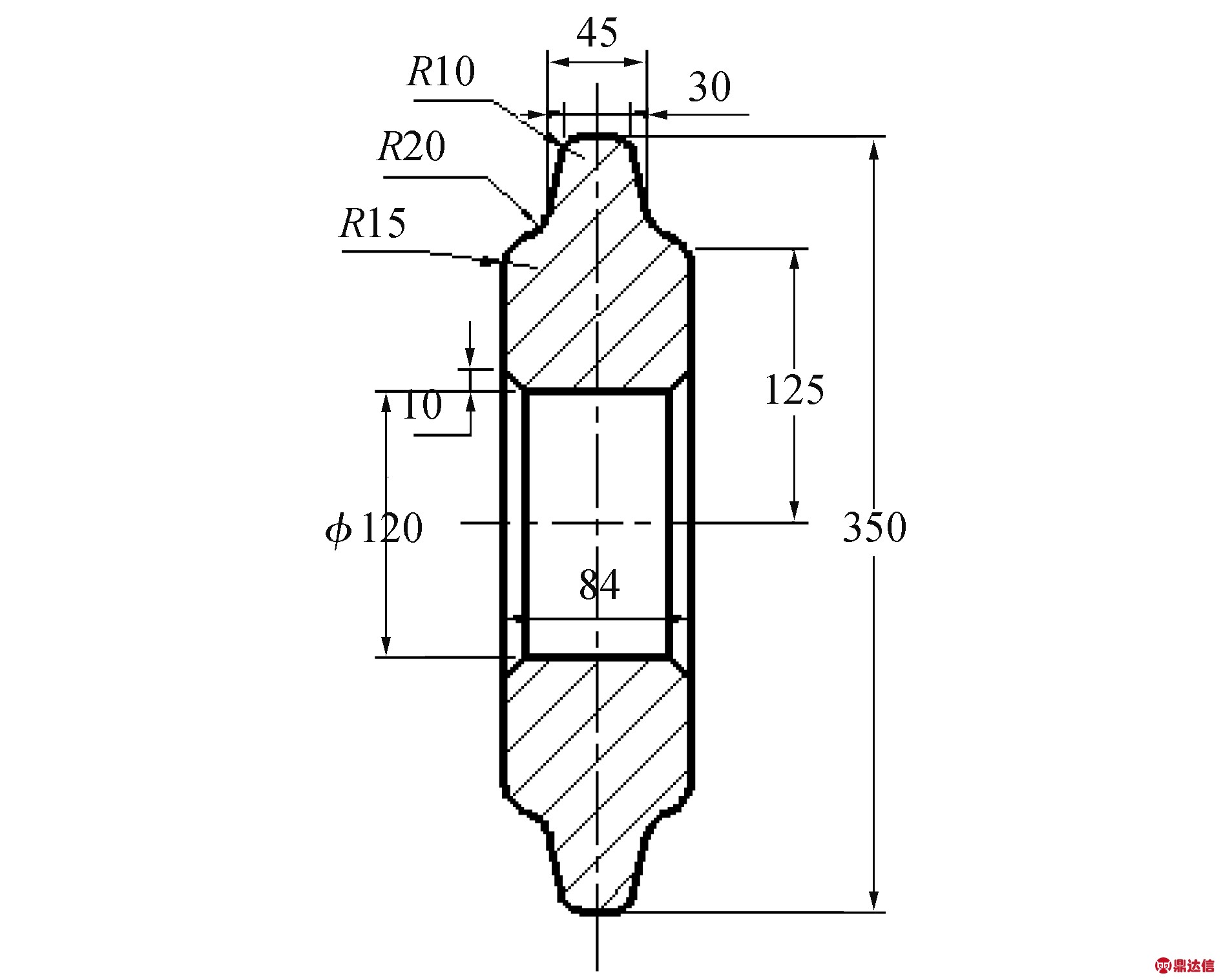
图1 刀圈毛坯和锻件尺寸
Fig.1 size of cutter ring blank and forging
采用Brick Mesh方式对刀圈进行网格划分,并采用自适应网格重划分技术处理网格畸变问题。刀圈材料为H13钢(4Cr5MoSiV1),在仿真中设置为塑性体,根据H13钢的标准锻造温度范围869 ℃~1 156 ℃,并结合实际生产,刀圈毛坯初始轧制温度设置为1 150 ℃。其余各模具为刚性体,预热温度设置为250 ℃,环境温度为20 ℃。接触摩擦形式采用Shear方式,毛坯与主辊、芯辊及锥辊的摩擦因子分别为0.7、0.5和0.3。毛坯与模具、空气的传热系数分别为11 N/(s·mm·℃)、 0.02 N/(s·mm·℃)。

图2 刀圈轧制有限元模型
Fig.2 Finite element model of cutter ring rolling
1.2 刀圈轧制成形有限元模拟结果
1.2.1 刀圈轧制成形过程等效应变分析
图3为刀圈轧制应变分布图。由图3(a)可知,刀圈应变百分比分布较均匀,大应变所占百分比极小,约16.7%。由图3(b)可知,轧制结束时,刀圈整体应变均匀,刀圈表面与模具接触轮廓区域应变较大,这是由于金属流动时与模具摩擦致使该处应变较刀圈其他部分大,刀圈内部基本无较大应变,这有利于晶粒的演变,可以获得较均匀的组织性能;图3(c)表明随着轧制的进行,各特征点应变值逐渐增大,刀圈芯部(P3)和刃部(P5)应变变化相对平稳,各特征点应变数值曲线较光滑;刀圈轧制结束时,各特征点的应变大小主要分布在0~1.22。应变反映了刀圈轧制组织晶粒变化,说明轧制过程中刀圈截面应变平稳,晶粒组织演变较均匀,刀圈轧制后可以获得良好的组织性能。
1.2.2 刀圈轧制成形过程等效应力分析
图4为刀圈轧制应力分布图。由图4(a)可知,应力值在约100 MPa的部位占了90%以上。由图4(b)可知,刀圈截面整体呈现由外表到内芯逐渐递减的趋势,内圈与刀刃部位应力较大,无明显的应力集中,反映了刀圈成型的均匀性。图4(c)可知,随着轧制进行,刀圈截面应力在初始阶段迅速上升,到稳定轧制阶段,应力变化较平稳,其大小在175 MPa左右,总体数值小于200 MPa,刀圈轧制结束时,其截面应力大小在100~160 MPa,轧制过程总体较平稳。刀圈与轧辊接触部位变形量较大,该处应力较大,反映刀圈外表面金属致密性好,预测金属流线密集,在一定程度上增加刀圈的耐磨性和抗冲击性能。毛坯充满型腔,说明毛坯和轧辊设计合理。
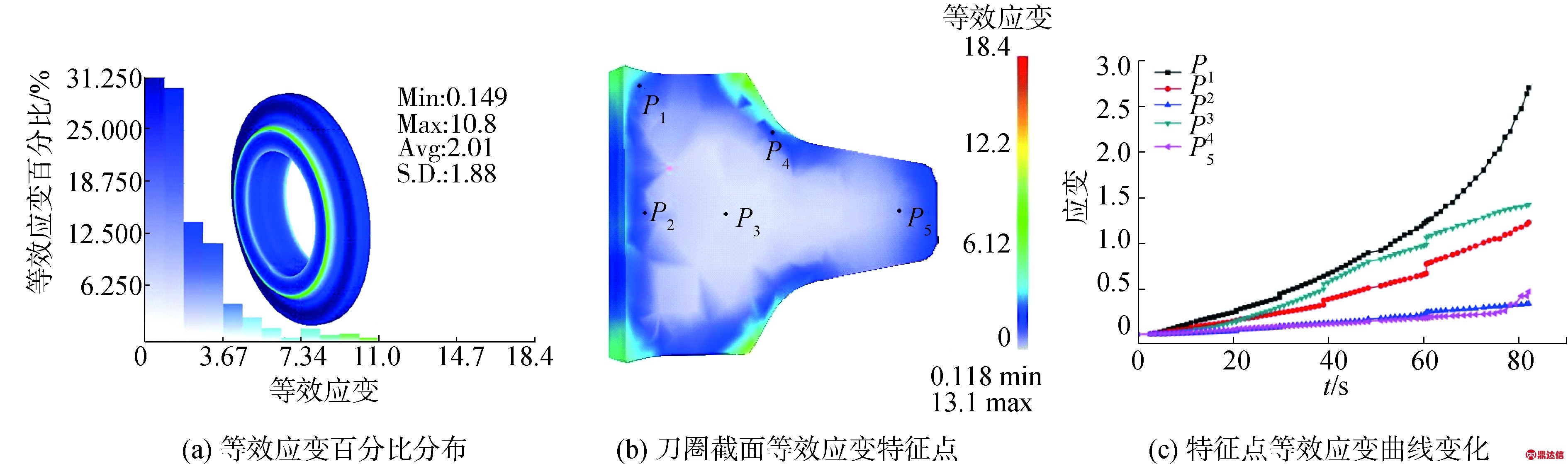
图3 刀圈轧制模拟应变结果
Fig.3 Simulation results of strain of the cutter ring rolling
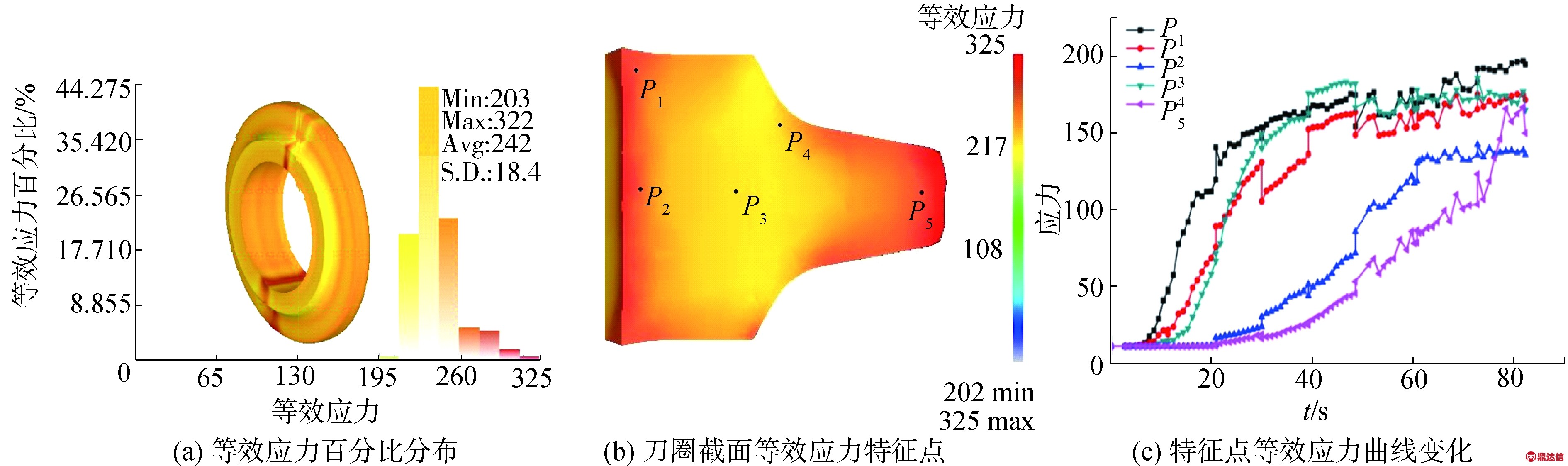
图4 刀圈轧制模拟应力结果
Fig.4 Simulation results of stress of the cutter ring rolling
1.2.3 刀圈轧制成形金属流线分析
流线是金属中的低熔点成分和带状组织偏析在轧制或挤压时沿主要变形方向伸展而形成的。图5为刀圈轧制成形后金属流线分布,纵横线交点连线表示该处金属流线,由图可知,轧制成形时,由于圆弧过渡处受到主辊的挤压作用,变形量较大,该区域流线分布相对较密集。刀圈芯部区域金属流线网格分布均匀,表明该区域变形量较小,且受力和变形均匀。刀圈金属流线整体沿近似截面几何形状分布,由于刀圈轧制成形连续局部变形的特点,金属变量较缓慢,流线分布均匀、封闭且光滑,没有出现乱流、回流、穿流等缺陷,使刀圈具有较好的力学性能和抗冲击疲劳强度。
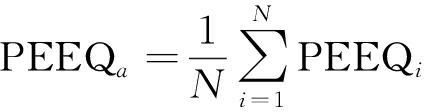
图5 刀圈流线分布
Fig.5 metal streamline distribution of cutter ring
2 工艺参数对刀圈成形质量的影响
2.1 评定指标
刀圈轧制成形质量可以采用其等效应力和应变的平均值及标准差来评定。对于成形件,成形过程坯料变形越均匀,局部变形差异越小,晶粒越均匀,组织应力越小,疲劳寿命越高。标准差能反映一个数据集的离散程度,可以衡量刀圈等效应变场、应力场分布的均匀程度,标准差越小,表明刀圈成形件等效应变和应力分布越均匀,成形件质量越好。其表达式分别为:

(1)

(2)
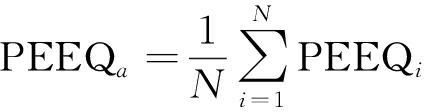
(3)
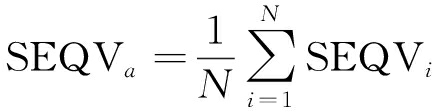
(4)
式中:SDP、SDS分别为等效应变和等效应力标准差;PEEQa、SEQVa别为所有节点的平均等效应变和平均等效应力;PEEQi、SEQVi分别为第i节点的等效应变和等效应力,N为节点总数。
2.2 初始轧制温度对刀圈成形件质量影响规律
H13钢标准锻造温度范围在869 ℃~1 156 ℃。考虑到毛坯与模具之间的传热影响,仿真取值时适当提高温度范围,故选择刀圈始锻温度分别为1 050 ℃、1 100 ℃、1 150 ℃和1 200 ℃进行刀圈轧制仿真。图6为初始轧制温度对刀圈轧制成形刀圈质量的影响规律,由图6可知,刀圈成形件等效应变平均值在初始轧制温度为1 100 ℃时较大,随着初始轧制温度升高,等效应变平均值降低;等效应变的标准差随初始轧制温度变化不大,其值在1.93左右。刀圈成形件等效应力的平均值和标准差随初始轧制温度的升高而降低,即在轧制温度范围内,初始轧制温度越高,刀圈等效应力分布越均匀。轧制温度对成形力和金属充型能力有很大影响,随着轧制温度的升高,金属材料塑性增加,变形抗力降低,高温使材料的塑性越来越好,材料变形也越均匀。轧制温度过低时,金属流动能力差,易导致成形力大和靠模后金属填充不足等缺陷。

图6 初始轧制温度对刀圈成形质量的影响
Fig.6 The influence of the initial rolling temperature on the forming quality
2.3 主辊摩擦因子对刀圈成形件质量影响规律
选取主辊摩擦因子分别为0.55、0.70、0.85和1.00进行仿真研究。图7为主辊摩擦因子对刀圈成形质量的影响规律,通过图7的曲线综合分析可知:刀圈在轧制过程中,摩擦因子过大或过小,刀圈等效应变和应力的平均值均较大。刀圈等效应变的标准差随主辊摩擦因子的增大变化不大,其值在1.97左右,表明在不同的摩擦因子下,刀圈变形都比较均匀。刀圈等效应力标准差随不同摩擦因子的变化规律与其平均值变化一致,即摩擦因子过大或过小时,其标准差均较大,表明该条件下刀圈变形不均匀。这是因为摩擦因子过大,在刀圈轧制后期,毛坯与模具接触区域变大,该区域金属流动困难,模膛充型越来越困难,应力呈不稳定波动,易出现充不足等缺陷。摩擦因子过小时,可能由于轧制过程持续时间较短暂,而轧制力较大,导致金属变形量较大,变形不均匀性增加。
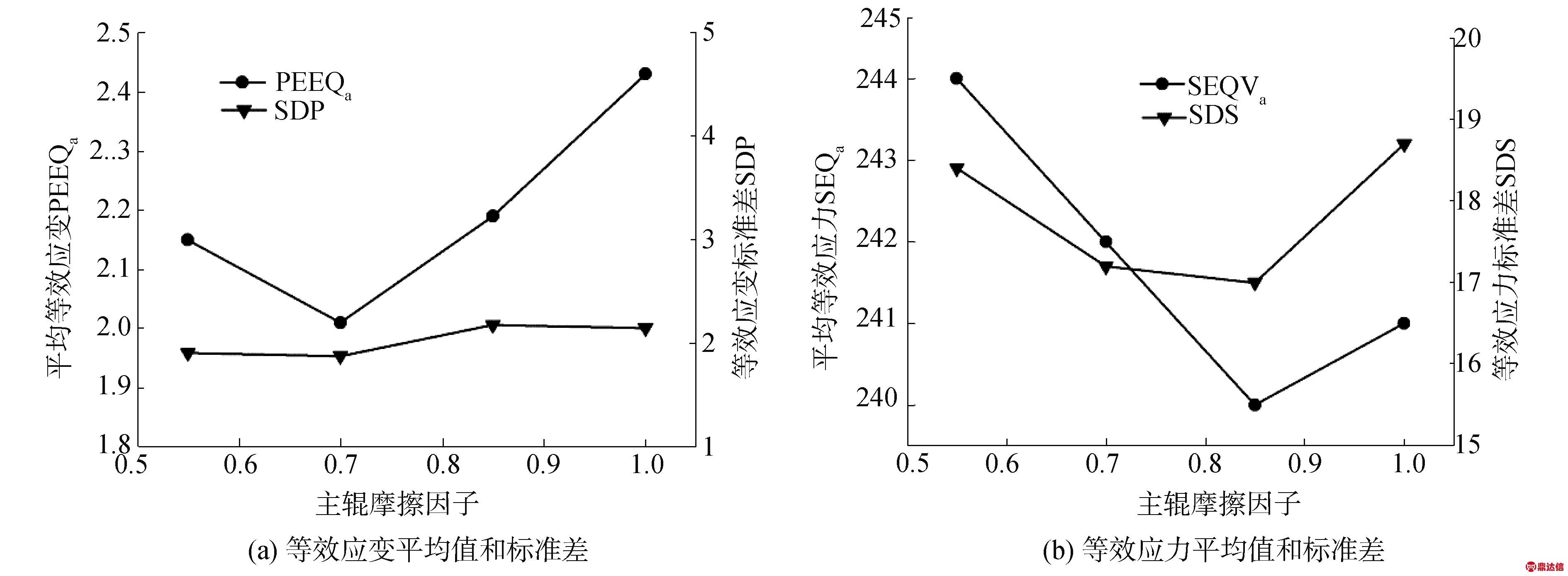
图7 主辊摩擦因子对刀圈成形质量的影响
Fig.7 The influence of the main roller friction factor on the forming quality
2.4 主辊转速对刀圈成形件质量影响规律
在滚刀刀圈轧制成形建模确定的工艺参数基础上,选择主辊转速分别为1.842、2.632、3.421、4.211 rad/s进行刀圈轧制工艺仿真。图8为主辊转速对刀圈成形质量的影响规律,由图8可知:刀圈成形件等效应变的平均值和标准差随着主辊转速的增大而增大,即刀圈变形量增大,变形的不均匀性也增大;刀圈等效应力的平均值在主辊转速为2.632 rad/s时达到最大,此后,随着主辊转速的增大,应力平均值减小;应力标准差与平均值变化规律一致,即在主辊转速为2.632 rad/s时应力的不均匀性达到最大。主辊转速影响刀圈轧制成形的稳定性,主辊速度过大,毛坯咬入孔型困难,轧制时间长;主辊转速过小,毛坯易卡入孔型或者形成多边形缺陷,所以主辊转速的选取对轧制成形有很大影响。
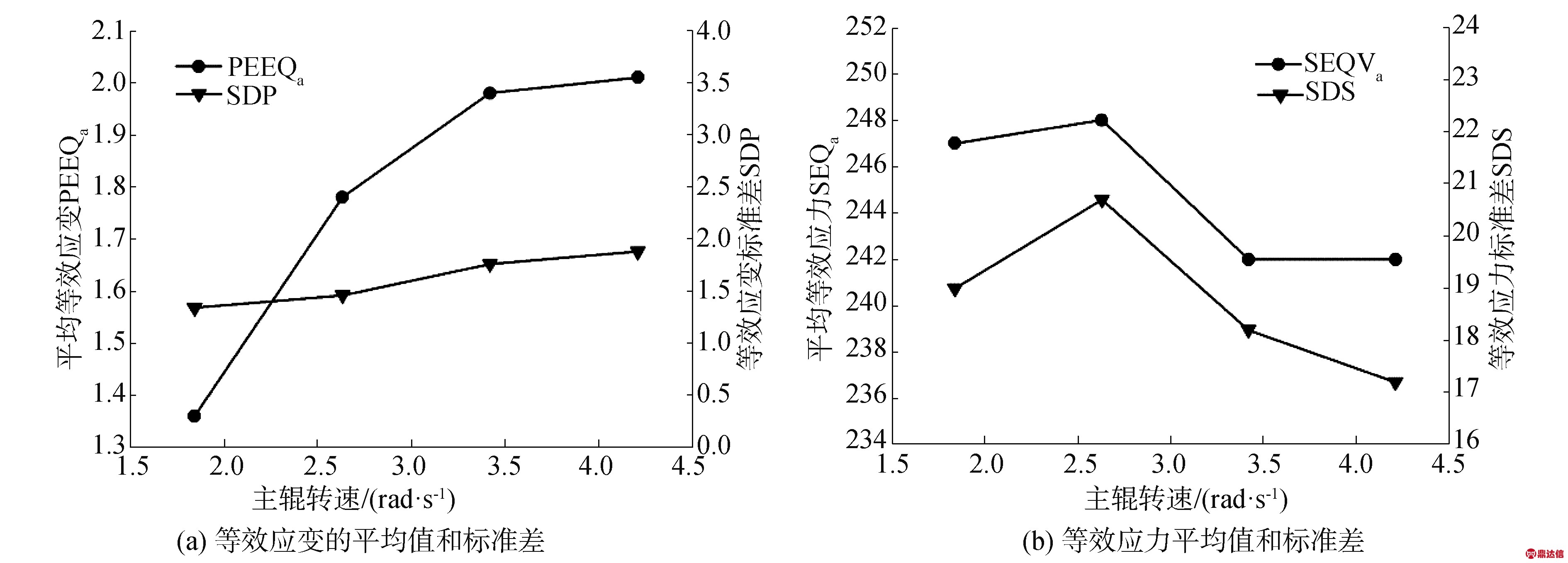
图8 主辊转速对刀圈成形质量的影响
Fig.8 The influence of the main roll rotationalspeed on the forming quality
3 试验研究
为了验证刀圈轧制过程有限元模型的可靠性,对17 in(43.81 cm)H13钢滚刀刀圈进行轧制成形试验。实验设备为D53 K-800立式轧环机,轧制环件最大高度300 mm,轧制环件外径尺寸350~800 mm,轧制线速度1.3 m/s。刀圈轧制成形件以及尺寸测量过程如图9所示,由图9(a)可以看出,刀圈成形件无裂纹、翘曲、折叠等明显的缺陷,与主辊的孔型贴合较好,充型比较充分。待轧制后的刀圈成形件冷却后,用TEMO TMME20-10200B电子数显游标卡尺测量其内径、外径和内圈高度,分别在成形件外圈、内圈和内圈端面每90°处测量并取其平均值,与数值模拟值进行比较,如表1所示。由表1可以看出,制试验值与数值模拟得到的刀圈内径、外径和高度比较其误差分别为4.8%、1.5%和8.2%。在实际轧制成形生产刀圈时,内径端面会保留较大的机加工余量,而模拟仿真时,由于锥辊的运动较为复杂,采用了简化的方式处理,故该尺寸轧制试验值与数值模拟值存在一定误差。各误差值均在9%以内。
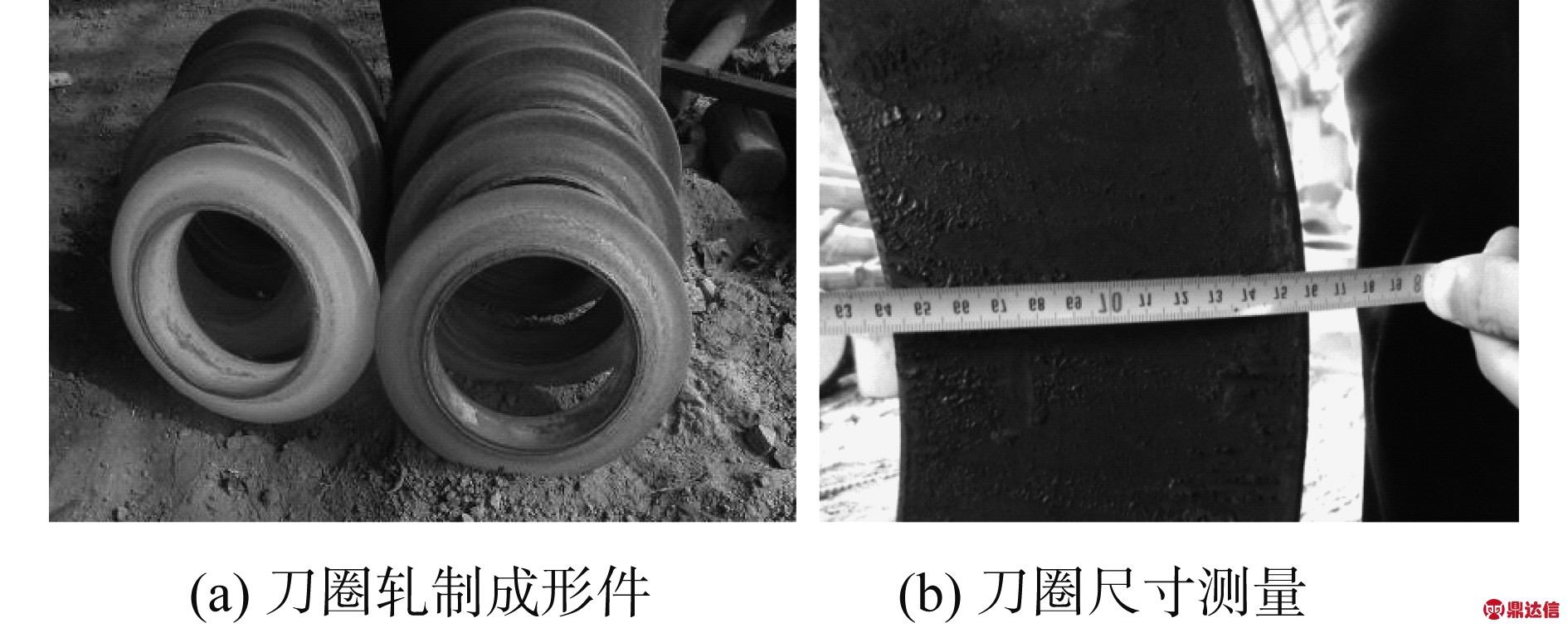
图9 刀圈轧制试验
Fig.9 Cutter ring rolling test
将上述轧制后的刀圈进行取样,图10为刀圈试样取样位置,对试样进行处理后观察其截面流线。图11为刀圈截面刀刃受力情况和流线分布图。由图可知,刀圈金属流线与刀圈几何形状相似,刀圈刃部流线封闭且光滑,这与模拟得到的流线分布一致。流线分布对金属受力特征和疲劳破坏影响很大,且流线在零件表面露头的地方在微观上是缺陷源,易形成应力集中,是疲劳断裂时最初裂纹最易出现的地方。刀圈金属流线沿截面几何形状分布的特征使其在承受外力作用时拥有更好的受力特征和抗疲劳破坏性能。
表1 数值模拟和轧制试验刀圈尺寸比较
Table 1 Cutter ring size comparison of numerical simulation and rolling testmm
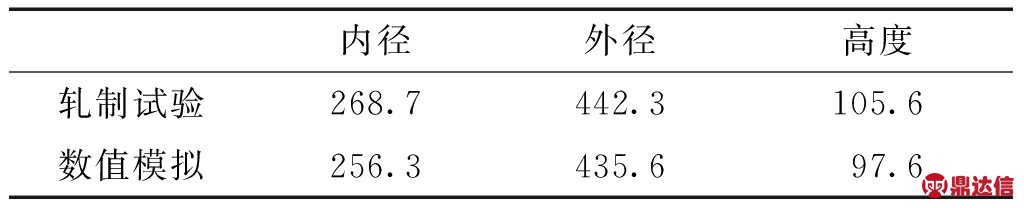
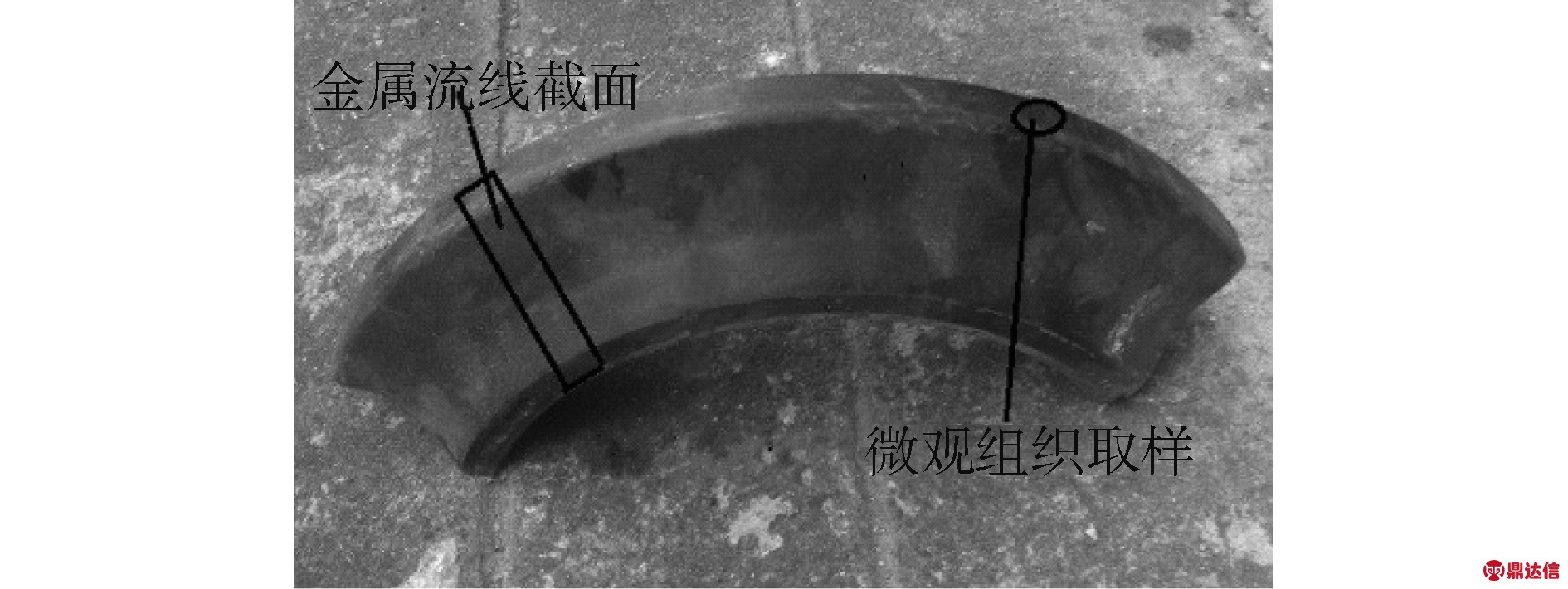
图10 刀圈试样取样位置
Fig.10 Sampling position of cutter ring specimen
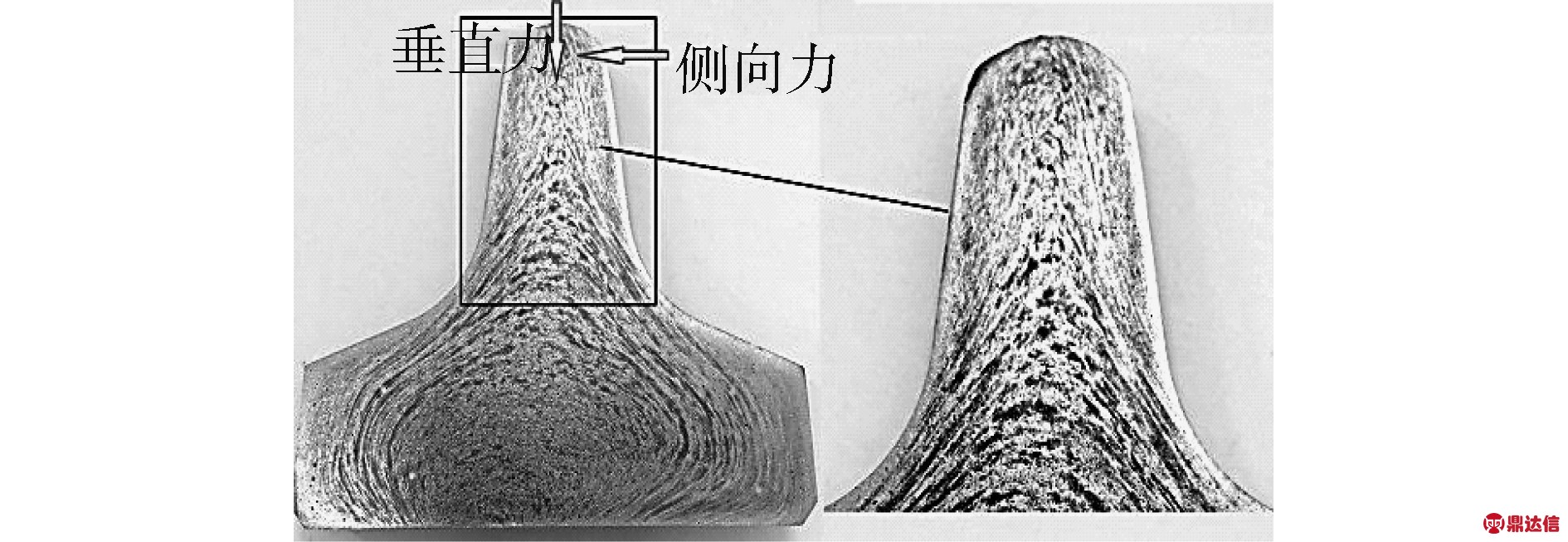
图11 刀圈受力和流线分布
Fig.11 Stress and streamline shape of cutter ring
4 结论
1)轧制成形过程中,刀圈截面应变大小分布在0~1.22,变化平稳,能获得良好组织性能。随着轧制进行,刀圈应力先迅速上升,此后稳定在175 MPa左右。轧制结束后,刀圈截面应力大部分在100~160 MPa。轧制后刀圈金属流线光滑,沿刀圈截面几何形状分布均匀。
2)刀圈等效应变标准差随温度变化不大,等效应力随着初始轧制温度升高而减小,分布越均匀;主辊摩擦因子过大或过小,刀圈等效应变和应力的平均值和标准差均会增加,即变形不均匀性增加;刀圈等效应变的平均值和标准差随主辊转速增加而增大,主辊转速为2.632 rad/s时应力的标准差达到最大。
3)通过刀圈轧制试验,得到模拟和试验结果刀圈尺寸最大误差为8.2%;通过金属流线观察得到轧制刀圈流线沿刀圈截面几何形状分布,光滑且封闭,具有良好的受力特征和抗疲劳破坏性能。