摘要:采用INSTRON准静态压缩试验机和分离式霍普金森压杆装置,研究固溶态AM80镁合金在室温准静态和冲击载荷下的变形行为及组织演变。准静态载荷下, 流变应力随应变率(3×10-5~4×10-1 s-1)的升高逐渐降低,表现为负应变率敏感性;冲击载荷下,流变应力随应变率(7.00×102~5.20×103 s-1)的升高而升高,呈现出明显的正应变率敏感性。冲击载荷下AM80镁合金的变形机制以基面滑移和孪生为主,大量细小致密的形变孪生以及适量非基面滑移的启动是AM80镁合金在冲击载荷下流变应力明显高于准静态载荷的重要原因。此外,随应变率的升高,AM80镁合金变形的均匀性明显增强,当应变速率升至3.65×103 s-1时,冲击变形所引起的局部绝热温升软化大于应变硬化与应变速率硬化的总和,部分晶粒产生了明显的动态回复,使得孪晶密度和变形均匀性反而降低。
关键词:AM80镁合金;高速冲击;应变率敏感性;Johnson-Cook本构方程;形变孪生
镁合金的密度低、比强度和比弹性模量高,且具有良好的阻尼减震和高效的吸能特性,是装甲、航空航天和交通运输等领域实现轻量化最理想的结构材料之一。目前,关于镁合金的相关研究主要集中在较低应变率下的变形行为、变形机制、强化与失效机理[1-5]。众所周知,镁合金结构件在服役过程中不可避免地要承受加载速率较高的爆炸、冲击等载荷[6-7]。在轻量化的推动下,镁合金零部件在武器装备、航空航天和汽车等领域中的应用越来越多,使得其在高速冲击载荷下的应力响应行为、变形机制与失效机理越来越受关注。随加载应变率的升高,AZ31镁合金的断裂机制由准静态压缩时的准解理断裂转变为高速冲击时的韧性断裂[8-9],且其在高速冲击载荷下的屈服强度、抗拉强度和形变吸能等均表现出一定的正应变率效应,显微裂纹扩展也由沿晶逐渐演变为穿晶[10-11]。AZ31镁合金沿其法向受高速冲击时,其屈服强度、应变硬化率和塑性具有较明显的正应变率效应,而沿横向和扎制方向高速冲击时的应变率效应则不明显。郭鹏程等[12]、Mukai等[13]研究了AZ31B镁合金在4.96×102~2.12×103 s-1应变率范围内的室温变形行为与加载应变率的相关性,发现该合金的流变应力不具有应变率效应,但其变形显微组织却对加载应变率较敏感。较低加载应变率下AZ31B镁合金的变形主要以孪生的方式进行,而在高应变率载荷下除孪生外,还激活了较多的柱面与锥面滑移。此外,Yokoyama[7]通过研究AZ31、AZ61和ZK60变形镁合金的冲击拉伸行为及夏比冲击功与高应变率吸能的关系,发现这3种镁合金的拉伸强度及形变吸能性均随应变率的升高而提高,且当应变率为1×103~2×103 s-1时,三者均表现出明显的各向异性。虽然对准静态载荷下镁合金的力学响应行为及显微组织演变已进行了系统的研究,并且近年来有关高速冲击载荷下的相关研究也越来越多[7-9,13-17],但镁合金在准静态与高速冲击载荷下的力学响应及组织演变的研究报道较少。本文中,基于AM80镁合金,通过准静态和高速冲击压缩,研究镁合金在室温下的力学响应行为及显微组织演变,探讨其在不同载荷作用下的变形机制。
1 实验方法
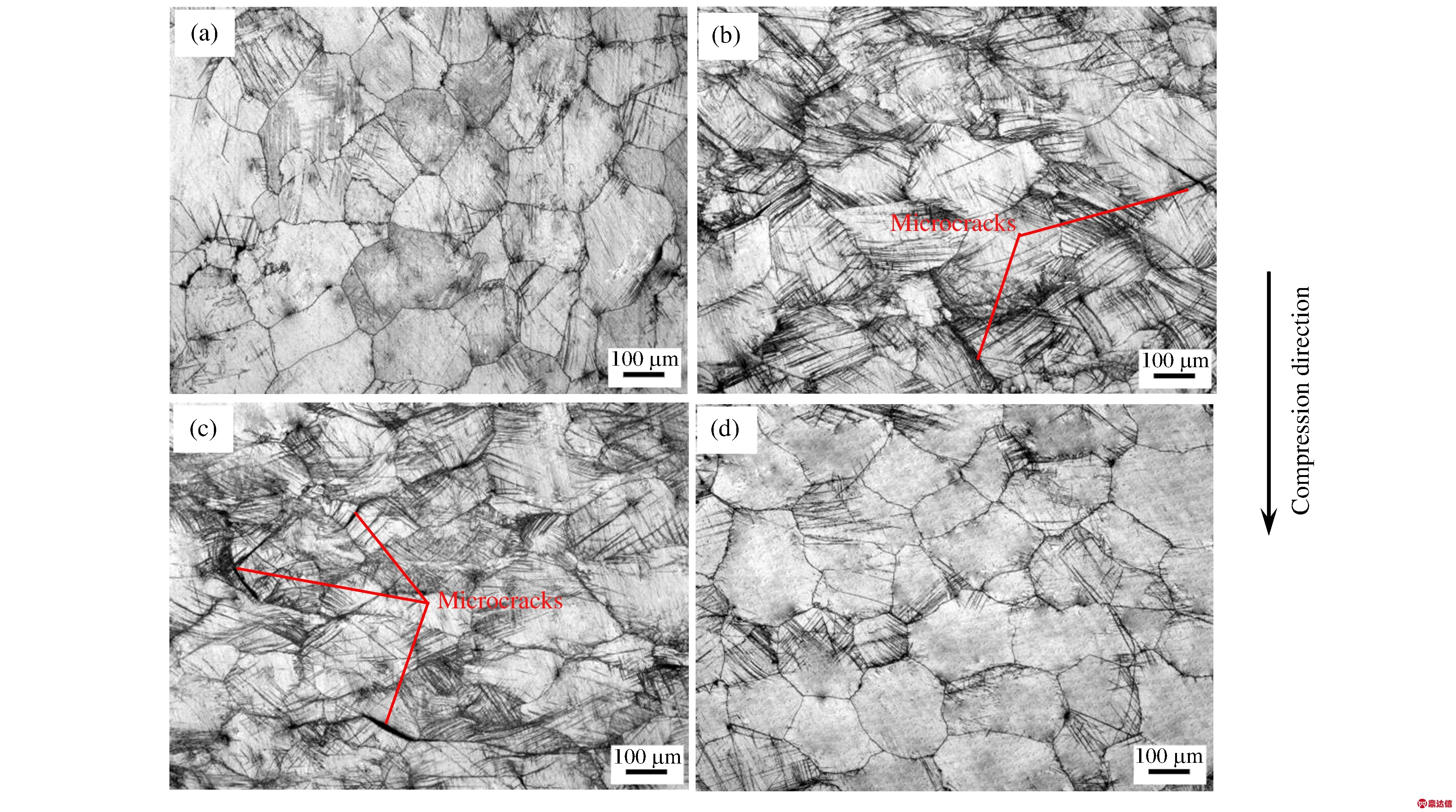
图1 试样在圆柱形铸锭中的相对位置
Fig.1 Relative position of samples in the cylindrical ingot
配制实验用AM80镁合金的原料为:镁(纯度99.98%)、铝(纯度99.6%)、电解锰(纯度95%)。依次将镁、铝和电解锰加至熔炼炉中,待熔炼充分后在720 ℃下浇铸到事先预热至250 ℃的圆柱形金属模中,模具尺寸为∅90 mm×500 mm。AM80镁合金主要化学成分的质量分数:Al,8.0%;Mn,0.1%;Mg,91.9%。采用到温入炉的方式,将镁合金铸锭放至450 ℃的箱式电阻炉中固溶处理16 h,然后取出在室温下进行空冷。最后,将固溶处理后的合金切割成圆柱形压缩试样,准静态和高速冲击压缩试样尺寸分别为∅10 mm×15 mm和∅8 mm×4 mm,试样在圆柱形铸锭中的相对位置如图1所示。
准静态压缩实验采用INSTRON压缩试验机,加载应变率分别为3×10-5、1×10-3、4×10-1 s-1;高速冲击压缩实验采用分离式霍普金森压杆(split Hopkinson pressure bar,SHPB),加载应变率分别为7.00×102、1.10×103、2.15×103 、2.75×103、3.65×103和5.20×103 s-1,SHPB装置的主要组成如图2所示。所有实验均在室温下进行,相同应变率下的应力应变数据取3次有效实验的均值。在试样圆柱形端面涂适量润滑剂,以减小压缩变形时试样和压头间的摩擦。采用内径为12 mm、外径为20 mm、高为2.9 mm的超高强度钢环进行冲击,以获得应变(ε)为0.28的变形试样。为防止试样在冲击过程中与超高强钢环接触,采用内、外径分别为8和12 mm,高度约为2.9 mm的软质海绵填充至试样与金属环中间。实验时先将软质海绵环放置在金属环中,并保持一端的端面齐平,然后将试样放置在内径与试样外径一致的软质海绵环中。通过圆柱面中心沿轴向切取显微组织观测试样,经打磨、抛光和腐蚀后,采用蔡司Axiovert 40 MAT倒置光学显微镜(optical microscope,OM)进行观察。
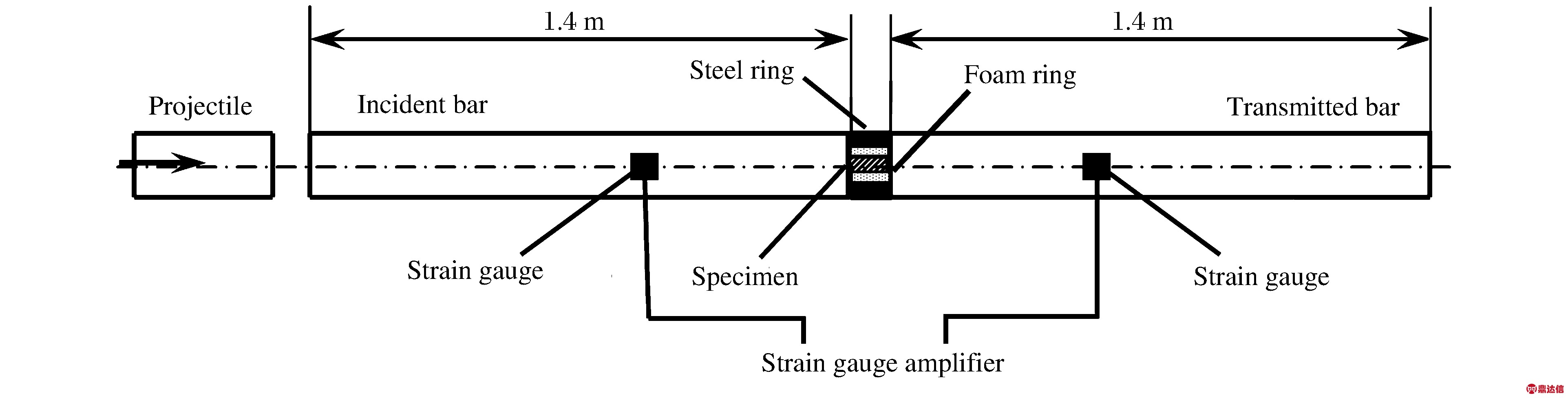
图2 SHPB装置示意图
Fig.2 Schematic of SHPB apparatus
2 实验结果及分析
2.1 准静态和高速冲击载荷下的应力响应行为
图3为AM80镁合金在准静态和高速冲击载荷下的真应力-真应变曲线。可见,AM80镁合金在准静态和高速冲击载荷下的流变应力均具有较明显的应变率效应。对比图3(a)和(b)可知,AM80镁合金在准静态和冲击载荷下的流变应力响应差异明显,冲击载荷下合金的流变应力明显高于其在准静态载荷下的。准静态压缩下,AM80镁合金的屈服强度对应变率不敏感但当变形进行至中高应变(ε≥0.08)时,其流变应力反而随加载速率的升高逐渐降低,即AM80镁合金具有一定的负应变率敏感性。Zhao等[18]的研究表明,镁合金在准静态载荷下的负应变率敏感性与其动态应变时效有关。应变率越低,溶质原子扩散得越充分,对位错的钉扎效果越好,因此其流变应力越高。与准静态压缩下不同,合金在冲击载荷下的流变应力均随应变率的升高而增大,表现出明显的正应变率敏感性。高速冲击载荷下,当应变率低于2.75×103 s-1时,合金在整个变形过程中均表现为应变硬化;当应变率为2.75×103 s-1时,合金应变硬化至其极限强度后,由于应变硬化与局部温升软化达到平衡,应力不再升高;当应变率高于2.75 ×103 s-1时,合金应变硬化后呈现出明显的软化特征,这是由于合金在高速冲击载荷下的变形后期产生了明显的局部绝热温升软化效应,使得合金的变形抗力反而逐渐降低。同时,合金在高速冲击载荷下的局部绝热温升软化随加载应变率的升高而增强,因此合金流变应力的降幅逐渐增大。由图3(b)可知,合金流变应力在应变为0.03时的升高速率明显增高,这是因为孪晶在该应变时开始产生[19],导致合金应变硬化能力迅速增强所致。
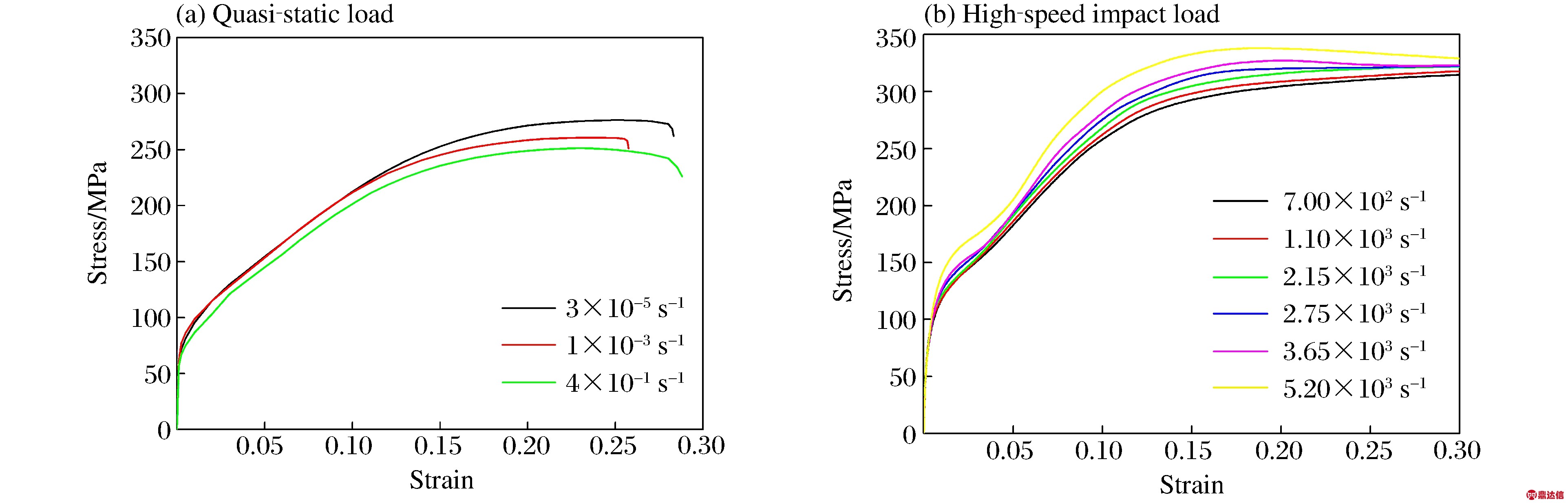
图3 AM80镁合金在准静态和高速冲击载荷下的真应力-真应变曲线
Fig.3 True stress-true strain curves of AM80 magnesium alloy at quasi-static and high-speed impact loads
通过特定应变(ε=0.05,0.10,0.15)下的加载速率-真应力曲线分析AM80镁合金的应变率敏感性,结果如图5所示。3个特定应变下的真应力均与应变率成线性关系,当真应变由0.05增大至0.10时,曲线斜率明显增大,而当真应变继续增大至0.15时其斜率不再增大。表明AM80镁合金在高速冲击载荷下的应变率敏感性随加载应变的增大,表现为先增强后减弱。
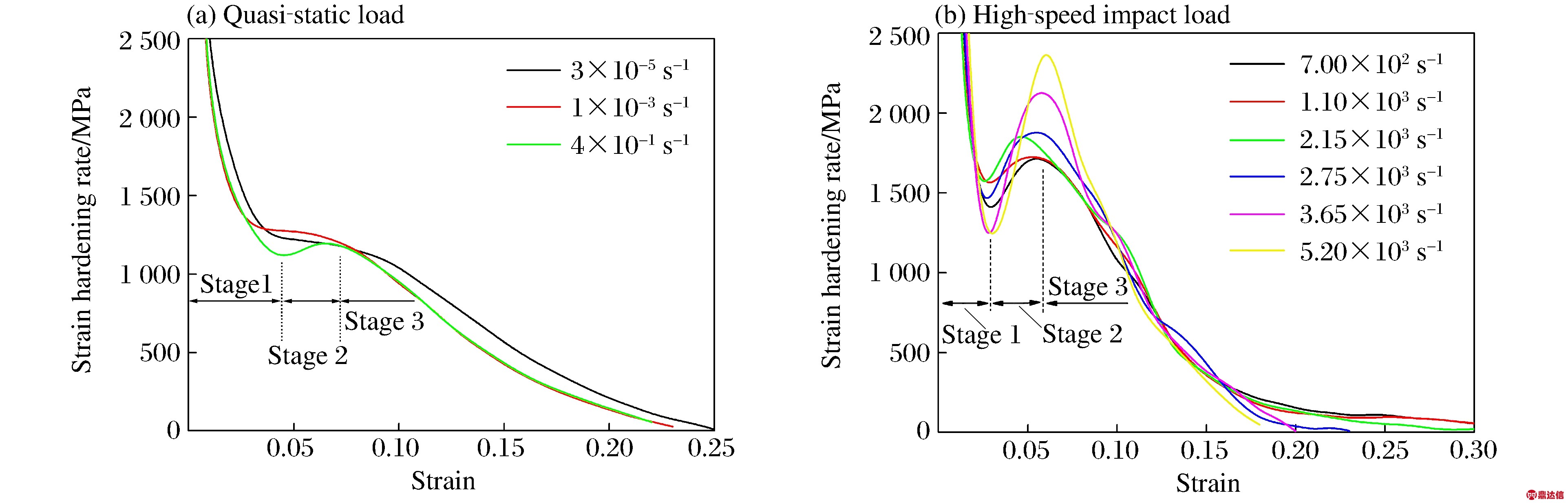
图4 准静态和高速冲击载荷下AM80镁合金的应变硬化率曲线
Fig.4 Strain hardening rate curves of AM80 magnesium alloy at quasi-static and high-speed impact loads
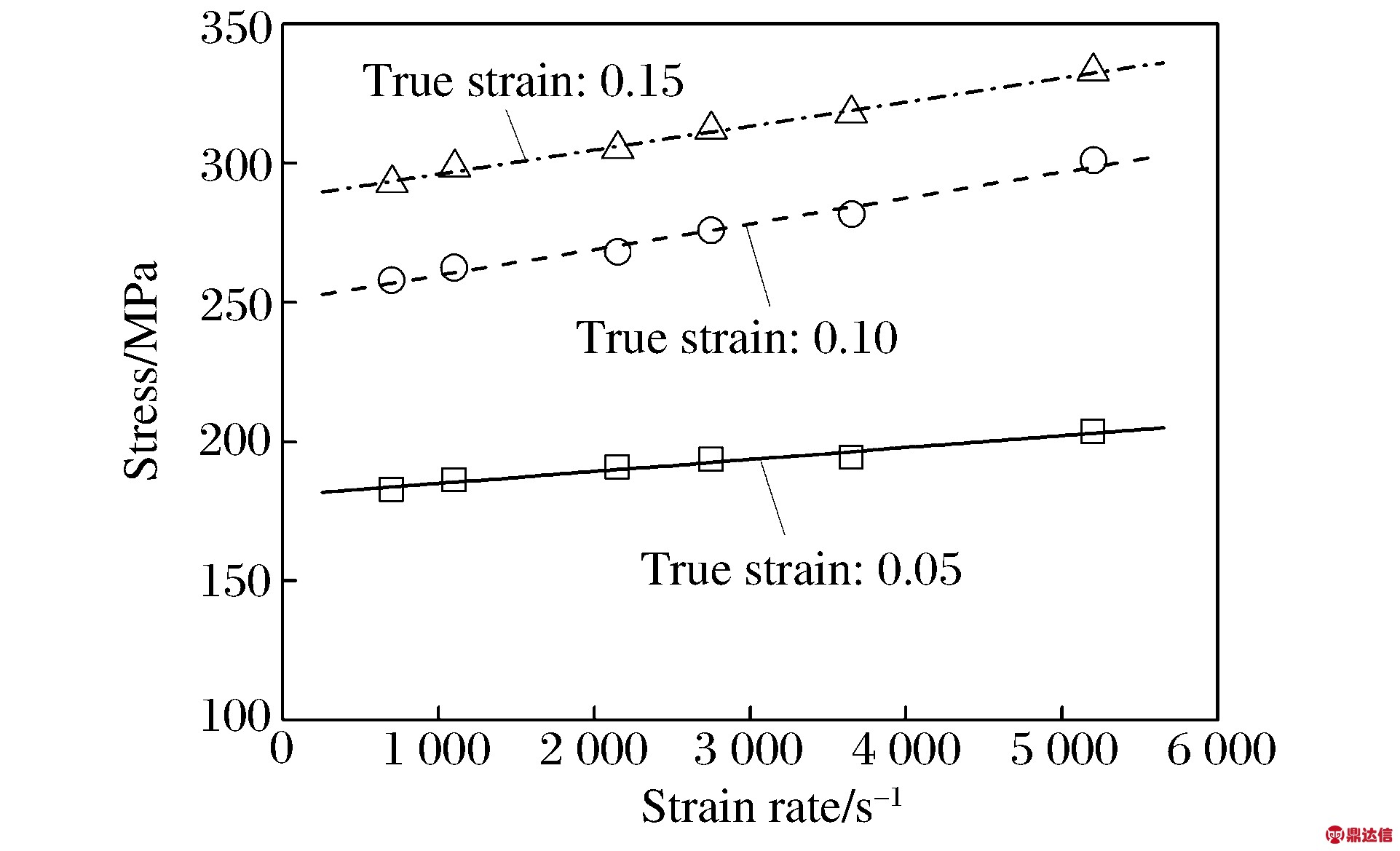
图5 特定应变下真应力与应变率的关系曲线
Fig.5 True stress as a function of strain rate at specified stains
图9和10是AM80镁合金试样在准静态载荷下分别以3×10-5 和4×10-1 s-1的应变率压裂后的OM显微图,压缩方向如图中箭头所示,图(a)、(b)、(c)和(d)在试样截面上的位置如图8所示。由图可知,4个特定位置的形变孪晶密度、间距以及与压缩轴的夹角均存在一定差异:位置c处的孪晶密度最高,位置b处的孪晶密度高于位置a处的孪晶密度,位置d处的孪晶密度最低;间距正好相反;而孪晶与压缩轴的夹角则与形变孪晶密度一致。特定位置处所呈现出的不同显微组织特征表明AM80镁合金在准静态载荷下的变形均匀性较低。仔细观察还发现,两应变率下位置b和c处的晶粒内还产生了显微裂纹。这些裂纹均在孪晶与晶界的交叉处形核,并沿孪生方向扩展直至贯穿整个晶粒,与Xie等[23]的研究结果一致。裂纹的萌生有利于应力的释放,且还影响主裂纹的扩展[23]。对比图9和10可知,随应变率的升高,相同位置处的晶粒内所产生的形变孪晶密度增大,间距减小,即形变孪生在准静态载荷下具有一定的正应变率敏感性。此外,4个位置处的孪生演变并不相同,位置a、b和c处晶粒内的形变孪晶显著增加,特别是位置a处,而位置d处晶粒内的形变孪晶密度变化较小。
为了更好地表征AM80镁合金的应变率敏感性,对其应变率敏感指数m [21]进行分析,其表达式为:和σ1为相同应变下应变率分别为
和
时的压缩应力,求得特定应变(ε=0.05,0.10,0.15)下合金的应变率敏感性指数m分别为0.004 2、0.009 2和0.008 0。可知,铸态AM80镁合金在准静态载荷作用下的应变率敏感性不明显,而在动态冲击载荷作用下则具有较强的正应变率敏感性。
2.2 本构拟合
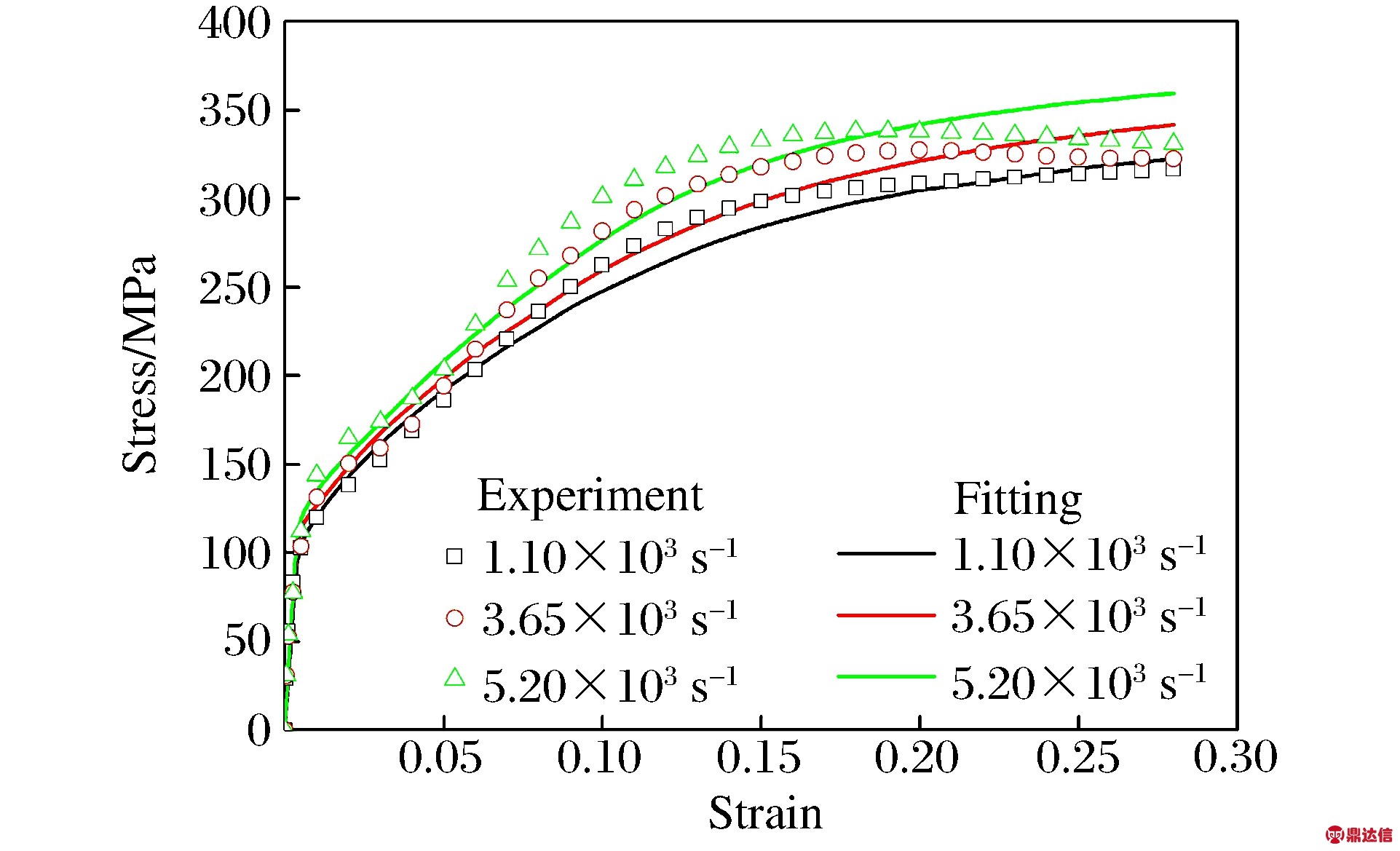
图6 高速冲击实验与J-C本构拟合真应力-真应变曲线
Fig.6 True stress-true strain curves of high-speed impact and J-C constitutive fitting results
众所周知,绝大多数金属材料在爆炸、冲击等高应变率下的流变应力不仅具有明显的应变率敏感性,且其变形过程近似为一个绝热的过程,流变应力还表现出明显的温度效应。镁合金作为实现武器装备、航空航天和汽车等轻量化最理想的结构材料之一,其动态应力响应行为及绝热温升效应越来越受青睐。综合考虑了材料应变率效应和温度效应的Johnson-Cook (J-C)本构模型,不仅结构形式简单,求解便捷,而且还能够较准确地预测材料在不同温度和应变率下的流变应力响应行为,是目前大型商业软件中应用最普遍的动态力学本构方程。J-C本构方程由3部分组成,分别为应变函数、应变率函数和温度函数,其表达式如下:

式中:σ为材料的流变应力;ε为瞬时塑性应变;为加载应变率;
为准静态载荷下的参考应变率;T、Tr和Tm分别是应变为ε时的变形温度、参考变形温度和材料的熔化温度;A、B、C、n和m是J-C本构方程需要求解的5个参数,分别为参考变形温度下的初始屈服应力、应变硬化系数、应变率系数、应变硬化指数和热软化指数。
AM80镁合金在冲击载荷下的应力响应行为采用J-C本构方程来表征,并忽略温度对应力响应行为的影响。本构方程中的参数C为常数,为提高拟合精度,取这与文献[22]中C为
的指数不同,本文采用
的多项式对C进行拟合。拟合求解时首先确定参数A、B和n。选取
为准静态参考应变率,求得本构方程中的参数
镁合金的J-C本构方程为:

高速冲击载荷下AM80镁合金的真应力-真应变曲线和修正后的本构方程结果如图6所示。两者的吻合度较高,实验屈服应力比本构拟合的约低5%。
2.3 显微组织演变
图7为AM80镁合金未变形状态的OM组织,表明AM80镁合金固溶处理后晶粒呈等轴状,且晶粒内不存在孪晶。为了更好地研究AM80镁合金在准静态与冲击载荷下应力响应行为的显著差异,本文中选取压缩变形后特定位置的显微组织进行对比分析,取样位置如图8所示。
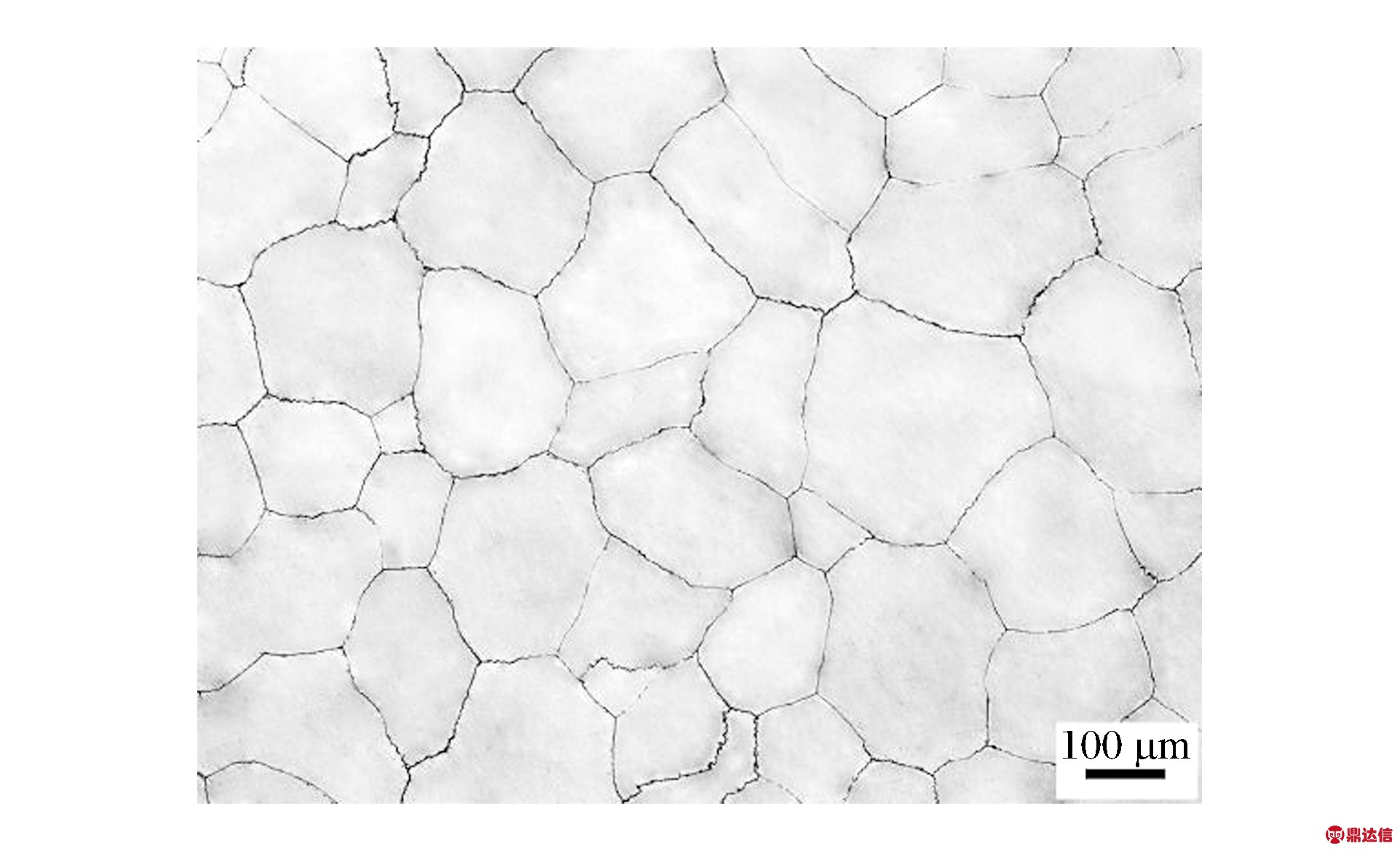
图7 实验用未变形AM80镁合金的金相图
Fig.7 OM image of undeformed AM80 alloy used in experiment
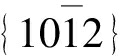
图8 显微观测点在压缩试样中的相对位置
Fig.8 Relative positions for microstructure observation in compression sample
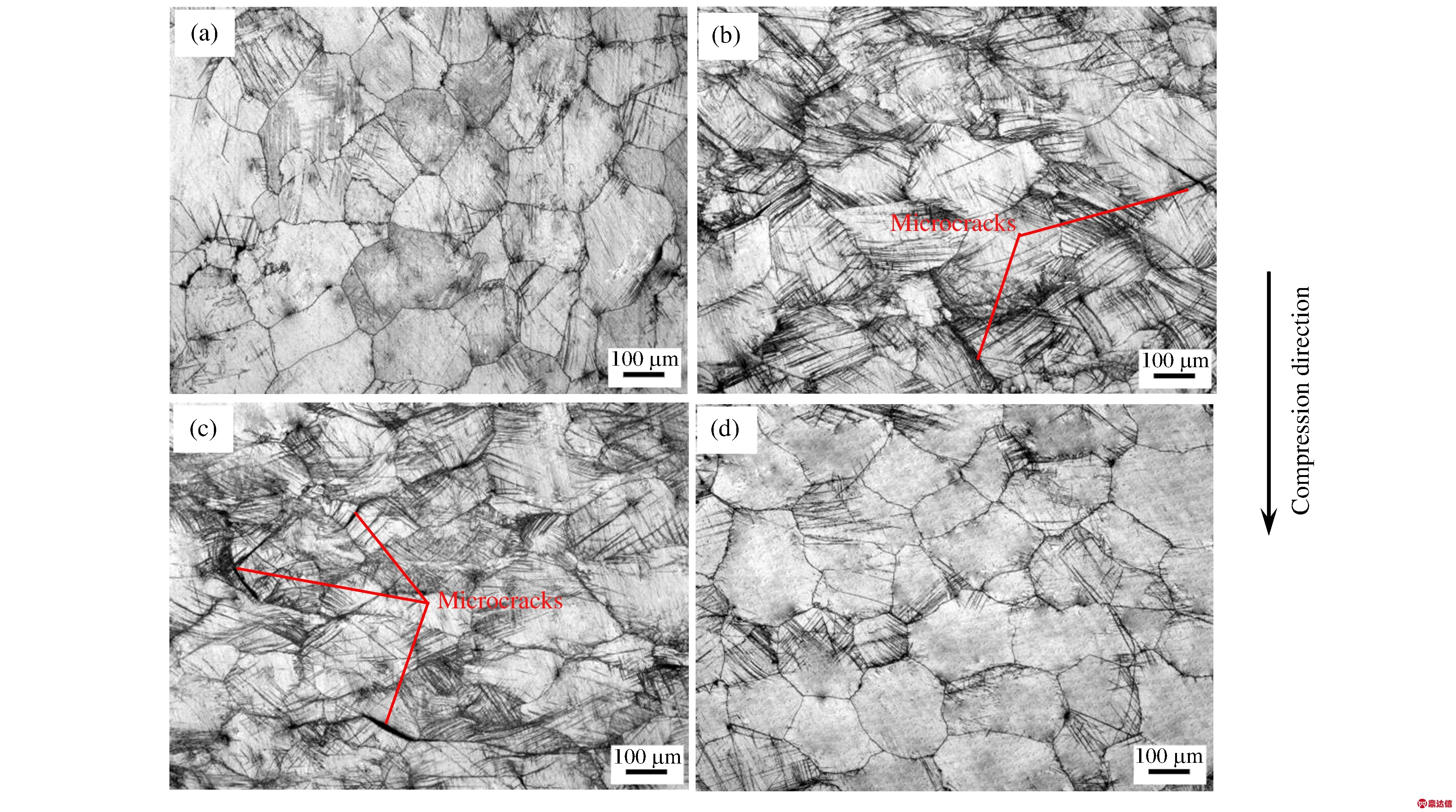
图9 应变率为3×10-5 s-1时压裂后的金相图
Fig.9 OM images of the fractured sample at 3×10-5 s-1 strain rate
图4为AM80镁合金在准静态和高速冲击载荷下应变硬化率(dσ/dε)与真应变(ε)的关系曲线。可见,AM80镁合金在准静态与高速冲击载荷下的应变硬化行为的差异明显,高速冲击载荷下的应变硬化率比准静态加载时的明显要高。此外,不同应变率载荷作用下合金的应变硬化率均由3个阶段组成。准静态载荷下,应变硬化率在第1阶段表现为急剧下降。随应变的增大逐渐进入稳定阶段,即第2阶段。此时应变硬化率基本不变或缓慢升高,这主要是由于形变孪晶的产生所致[20]。这种应变硬化率随真应变的增大基本维持恒定的趋势一直保持到ε=0.07。随应变的继续增大,合金的应变硬化率迅速降低,即进入第3阶段。这是因为随应变的继续增大,形变孪晶的增加速率逐渐降低,不足以维持其高的应变硬化率[17]。合金在高速冲击载荷下的应变硬化行为同样可分为3个阶段,但与准静态的相比,其变化规律明显不同。高速冲击载荷下的应变硬化率在第3阶段的下降速度较快。这是因为随应变的增大,镁合金中的孪生不断被消耗,其孪生速率在变形中后期反而降低,所产生的孪生硬化以及应变硬化已全被绝热温升软化所抵消,绝热温升软化是该阶段的主要变形特征;此外,高速冲击载荷下第2阶段的应变硬化率表现为随真应变的增大迅速升高。研究表明镁合金的形变孪生对应变率极其敏感,特别是拉伸孪晶随应变率的升高,孪生速率显著升高[17]。正是由于孪生的正应变率敏感性,使得冲击载荷下第2阶段的应变硬化率不仅明显高于准静态载荷下的,且随应变的增大迅速升高。
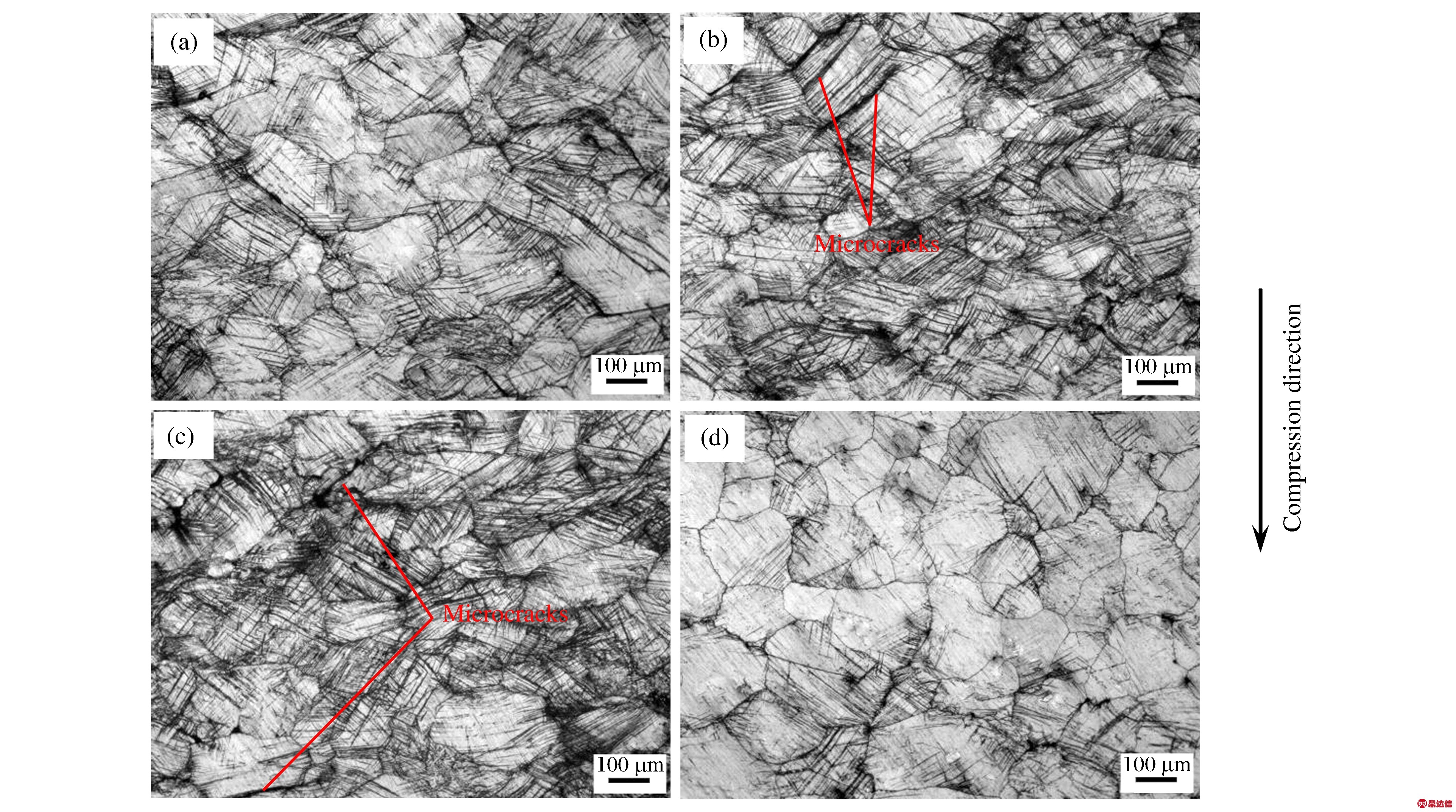
图10 应变率为4×10-1 s-1时试样压裂后的金相图
Fig.10 OM images of the fractured sample at 4×10-1 s-1 strain rate

图11 试样在2.15×103 s-1的应变率下压缩至0.28应变后的金相图
Fig.11 OM images of the fractured sample with compressive strain of 0.28 at 2.15×103 s-1 strain rate
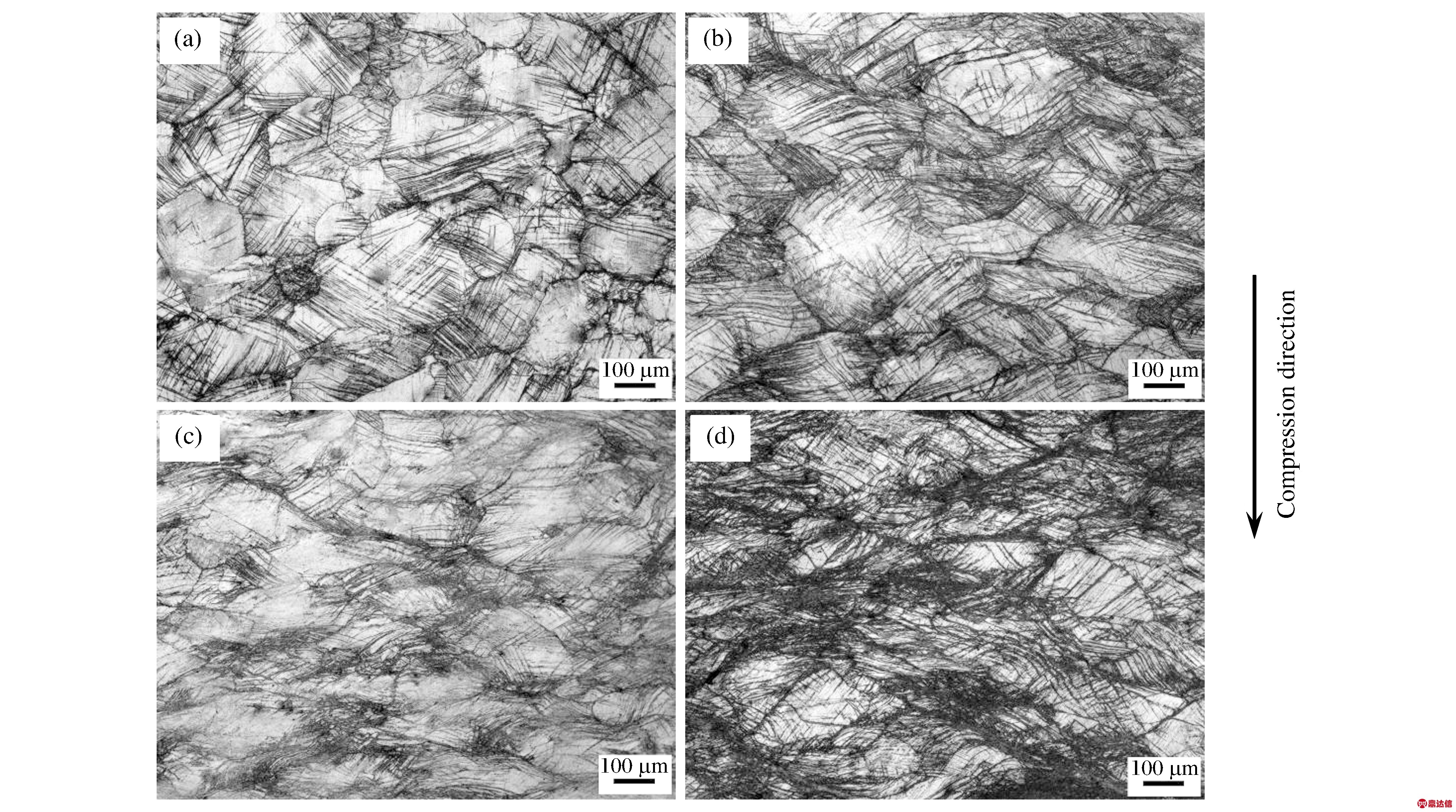
图12 试样在3.65×103 s-1的应变率下压缩至0.28应变后的金相图
Fig.12 OM images of the fractured sample with compressive strain of 0.28 at 3.65×103 s-1 strain rate
AM80镁合金试样在冲击载荷下以2.15×103和3.65×103 s-1的应变率压缩至应变为0.28后的金相显微组织分别如图11和12所示,压缩方向如图中箭头所示,图(a)、(b)、(c)和(d)在试样截面上的位置同样如图8所示。可知,冲击载荷下AM80镁合金变形的均匀性较准静态明显增强,4个特定位置晶粒内的形变孪晶密度、间距以及与压缩轴夹角之间的差异较准静态载荷下的均显著减小。与准静态相比,冲击载荷下各位置处的形变孪晶与压缩轴的夹角均更大。以2.15×103 s-1的应变率加载时,位置b处的孪晶密度最高,位置c处的孪晶密度高于位置d处的孪晶密度,位置a处的孪晶密度最低,且位置b和c处的晶粒内产生了明显的显微裂纹。这些显微裂纹均在晶界与孪晶交叉处形核,然后沿孪晶扩展。位置c处的裂纹沿孪晶不断扩展,直至贯穿多个晶粒,其扩展过程中由于部分孪晶方向与最高切应力方向不一致,裂纹出现一定偏折,如图11(c)所示。在3.65×103 s-1的应变率下,位置d处的孪晶密度最高,位置b处的孪晶密度高于位置a处的孪晶密度,位置c处的孪晶密度最低,与2.15×103 s-1应变率下的不同,该应变率下在4个特定位置处均未观察到明显的显微裂纹。此外,该应变率下位置c处的形变孪晶密度明显降低,这主要是由于当应变率由2.15×103 s-1升高至3.65×103 s-1时,局部绝热温升使得该区域内的晶粒产生了明显的动态回复[2],这也是导致高应变下本构拟合与实验结果差异较大的主要原因。
3 讨 论
面滑移和孪生相协调是镁合金的主要塑性变形机制。与准静态压缩相比,高速冲击压缩时AM80镁合金的流变应力明显要高,这取决于合金在准静态和高速冲击载荷下的变形机制。AM80镁合金在准静态压缩时的塑性变形机制为基面滑移主导的滑移与孪生相协调。此时,只有当晶粒取向不利于滑移时才会产生孪生,使得原为硬取向的晶粒通过形变孪生转变成软取向,从而继续滑移,形变孪生主要起协调各晶粒间变形的作用。随应变的增大,软取向晶粒逐渐被消耗而转变为硬取向,使得位错迅速增殖,导致其在晶界和孪晶界等处塞积所产生的应力集中程度增强,从而促进形变孪生的形核和扩展。由于准静态载荷下孪生只起协调变形的作用,因此其孪晶密度相对较低,且较厚,其显微结构特征主要表现为高密度位错[25]。冲击载荷下,由于变形时间极短,基面滑移不足以满足其变形要求,需要启动大量的形变孪生。此外,柱面滑移与锥面滑移也开始启动以协调变形。AM80镁合金在室温高速冲击载荷下的变形机制是以基面滑移和孪生为主、非基面滑移为辅。由于拉伸孪生具有较强的正应变率效应,使得合金在冲击载荷下的孪生形核率显著升高。Yang等[26]的研究表明,镁合金在高速冲击载荷下的显微组织主要表现为高密度位错和大量细小致密的形变孪晶。众所周知,室温下镁合金基面滑移所需的临界应力最低,
拉伸孪生次之,而<a>棱柱面滑移的临界切应力比基面滑移高一个数量级。由此可知,冲击载荷下所产生的大量形变孪晶,以及适量的非基面滑移是其流变应力明显高于准静态载荷的根本原因。
随应变率的升高,合金的变形均匀性提高,当应变率升高至3.65×103 s-1后,合金的变形均匀性反而降低(图9~12),这主要是由于不同应变率下合金的协调变形能力不同所致。室温低应变率载荷下,合金变形主要是通过基面滑移的方式进行,孪生只起协调变形的作用。低应变率下的孪晶密度较低,且较厚,对变形所起到的协调作用不明显[23],因此其变形均匀性相对较低。镁合金中形变孪生的正应变率效应,使得形变孪晶密度随加载应变率的升高而升高,因此高速冲击载荷下AM80镁合金的协调变形能力较强,其变形均匀性提高。特别是当准静态载荷转变为高速冲击载荷后,大量形变孪晶的产生使得合金的协调变形能力得到了极大的提高,因此其变形均匀性显著提高,如图11所示。当应变率升高至3.65×103 s-1后,形变所引起的局部绝热温升使得位置c处的晶粒产生了明显的动态回复,位错和孪晶密度降低[24],导致合金在该应变率下的变形均匀性反而降低,如图12所示。这主要是由于合金在该应变率下高速冲击变形时所产生的局部绝热温升增大,所引起的动态回复软化大于应变硬化与应变率硬化的总和,因此AM80镁合金的流变应力在变形后期反而随应变的增大逐渐降低,如图4所示。
AM80镁合金应变硬化率在变形各阶段呈现出明显不同的特征,特别是第2阶段合金在准静态与冲击载荷下所表现出的应变硬化行为差异明显,这主要是由于不同载荷作用下的变形机制不同所致。室温下镁合金的变形机制主要为滑移和孪生,准静态载荷作用下变形以滑移为主,高速冲击载荷作用下则是孪生占主导[17]。准静态压缩时,合金在第2阶段的应变硬化率随加载应变率的升高,由缓慢降低转变成逐渐上升,其峰值随应变率的升高而增大。与准静态相比,高速冲击载荷下的应变硬化率表现为迅速上升,这是因为准静态载荷作用下合金的变形是以基面滑移为主,孪生为辅,而高应变率载荷下的变形机制则是孪生占主导。由于拉伸孪晶具有明显的正应变率敏感性,冲击载荷下所产生的大量细小致密形变孪晶能有效地提高合金的应变硬化能力。另外,高应变率下非基面滑移的启动也在一定程度上提高了合金的应变硬化率。
4 结 论
(1)AM80镁合金在准静态与高速冲击载荷下表现出完全不同的流变应力响应行为。准静态压缩时为负应变率敏感性,高速冲击压缩时则为正应变率敏感性。(2)高速冲击载荷下AM80镁合金的变形机制是孪生主导的基面滑移与孪生相协调。大量细小致密的形变孪生,以及适量非基面滑移的启动是冲击载荷下合金的流变应力明显高于准静态载荷的根本原因。(3)合金的变形均匀性随应变率的升高而提高。当应变率升高至3.65×103 s-1后,局部绝热温升使得部分晶粒产生了明显的动态回复,位错和孪晶密度降低,其变形均匀性也随之降低。3.65×103 s-1应变率下的变形后期局部绝热温升所引起的动态回复软化大于应变硬化与应变率硬化的总和,使得其流变应力反而降低。