摘要:为满足油雾净化设备技术提升的迫切需求,运用COMSOL Multiphysics 软件进行多物理场耦合数值仿真和实验验证,以实现油雾净化设备的结构优化。结果表明:油滴雾粒的去除效率随极板上电压的增高呈现递增关系,直至效率接近于1;电场风速增大使油滴在通道内的停留时间减少,向极板的偏移量减小,在风速超过3.5m/s 时,效率急速下降;油滴的分级去除效率随着其粒径的增加而增大,且较小粒径的油滴因其曳力占总受力的比例大而受风速的影响更加明显;经结构优化后的设备效率提高12.6%,体积减小21%,且经实验验证数值模拟具有准确性和可靠性,可为产品优化提供理论依据。
关键词:油雾雾粒;数值仿真;停留时间;分级效率
在车、铣、钻、磨等金属加工过程中,高速、超高速数控机床在工作时会产生大量的切削热,而用以润滑和冷却的切削液在加工过程中极易汽化,形成大量的油雾颗粒[1]。这些油雾含有多种有毒成分,危害车间工人的身体健康并有致癌致畸作用[2],且油雾悬浮在车间中,附着在机床外表面及换热器上,会增加热阻,降低设备的使用寿命,长期积累会使车间里的电气系统和机床电路系统出现故障[3]。
为了减少油雾的污染和危害,保护车间工人的职业安全与健康,提高车间的空气质量与设备使用寿命,净化及回收利用工业油雾,开发更高效的油雾废气净化装置已经成为精密机械加工、国家节能减排及全球绿色制造战略的必然要求。
而静电式油雾净化器是解决油雾问题十分有效、使用率高的设备。因此,为了满足现有油雾净化设备技术提升的迫切需求,对油雾颗粒的收集机理进行数值研究,具有重要的指导意义。
本文以某型号静电式油雾净化器为模型,通过研究油雾颗粒的运动轨迹及电场强度、气流风速、油滴粒径对净化效率的影响,完成结构参数优化和匹配,并对优化结果进行实验验证。
1 数学模型
1.1 电场
净化器电场由外加静电场和空间电荷形成的电场两部分构成,电场分布特性满足泊松方程和电流连续性方程[4]:
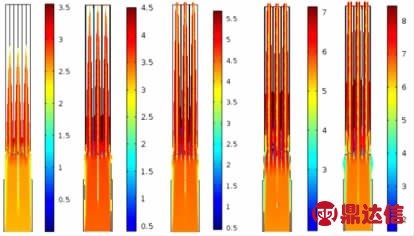
式中:V—电势(V);ε0—真空介电常数(C/(V·m)),一般取 8.85×10-12;ρV—空间电荷密度(C/m3)。

式中:μi—离子迁移率(m2/(V·s)),一般取2.1×10-4;E—电场强度(V/m);μ—气流速度矢量(m/s);D—离子扩散系数(m2/s),一般取5.3×10-5。
根据电荷守恒定律有:

其中,μiEρV 表示电荷传导项,这是在单级电荷漂移区对电荷起主导作用的项;μρV表示对流项,是空气流动对空间电荷的作用项;D▽ρV 表示扩散项,即空间电荷自身的热运动项。
将式(2)代入式(3),可得到:

由于电晕放电产生的离子速度比空气速度快两个数量级,即μiE≫u。因此,可以忽略空气速度对电流密度的影响[5],式(4)可简化为:

式(1)和式(5)构成了电场的基本方程组,采用离散化耦合求解[6]的方式进行静电场和空间电荷电场的计算。
1.2 流场
净化器内流场可以假设流体为不可压缩流体,流场的控制方程采用雷诺平均方程 [7](Reynoldsaveraged Navier-Stokes,RANs 法)。在湍动能 k 方程的基础上,引进ε(湍动耗散率)方程,建立标准 k-ε 方程模型。
质量守恒方程:

动量守恒方程:

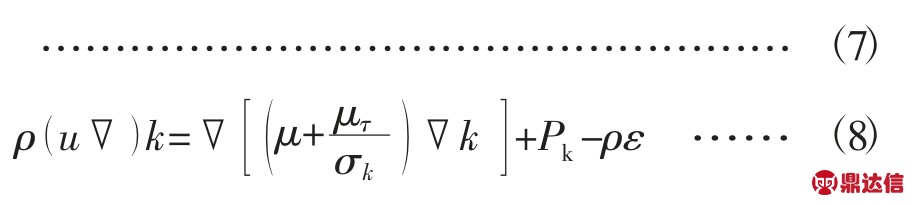
湍动耗散率ε 方程:
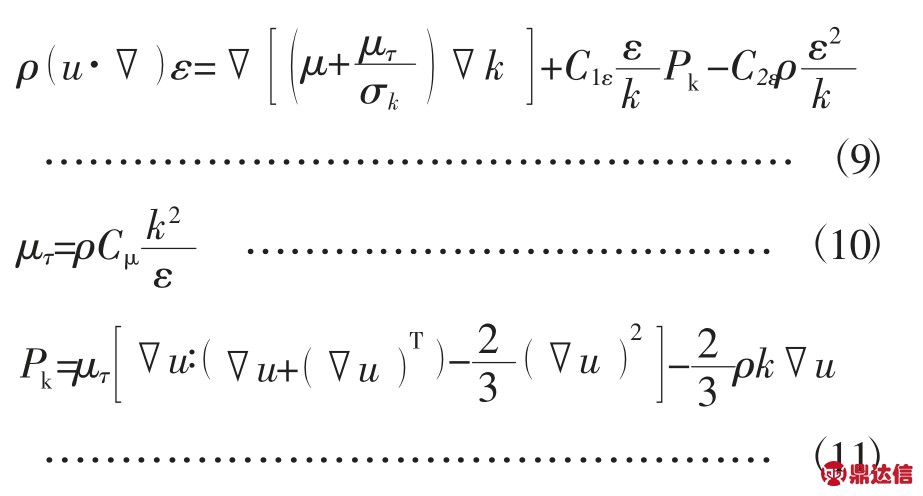
式中:u—速度场(m/s);P—压力(Pa);ρ—空气密度(kg/m3);I—单位矩阵;F—电场力附加项(N);Pk—湍动能每单位耗散净产出;μτ—湍流粘性系数(kg/(m·s));C,μ,σ—相关系数。
计算所使用各参数见表1:
表1 湍流参数表

1.3 颗粒动力场
分析油雾颗粒的运动轨迹,需要建立颗粒的运动方程。由于对净化器进行二维模拟,忽略颗粒在竖直方向受到的重力与浮力,因此用来考量的作用力有颗粒荷电产生的库仑力及对流产生的曳力。

式中:mP—油滴粒子质量(kg);FD—油滴所受曳力(N);FE—油滴所受电场力(N)。
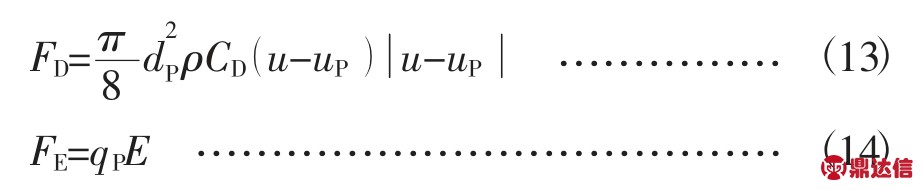
式中:dp—油滴直径(m);CD—流体阻力系数,是粉尘雷诺数ReP 的函数,对介于斯托克斯定律作用范围内的球形粉尘:
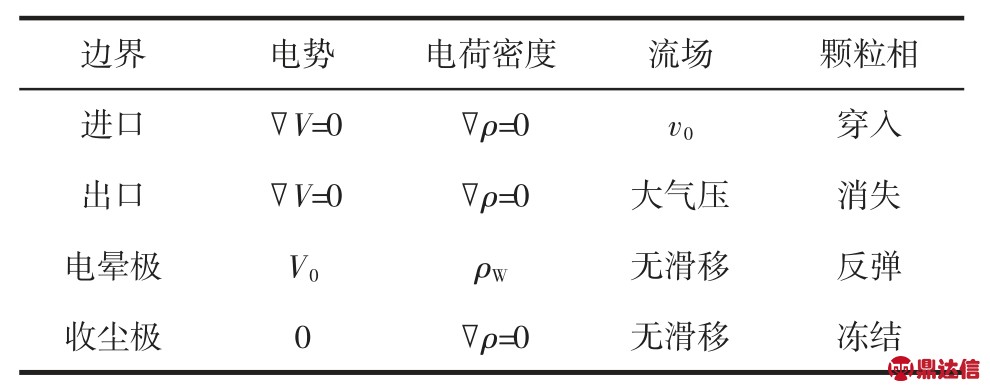
式中:qP—油滴荷电量(C);由于油滴直径在1 μm 左右,主要考虑场致荷电 [8],且为了简化考虑,取油滴的饱和荷电量:

式中:ε0—真空介电常数,取 8.854×10-12C/(V·m);εr—电介质的相对介电常数。
2 数值计算与实验模型
2.1 边界条件
模型的边界条件包括进口条件、出口条件及壁面条件等,采用速度入口,压力出口,壁面条件为壁函数的形式,笔者给出各边界条件(见表2)。
表2 边界条件
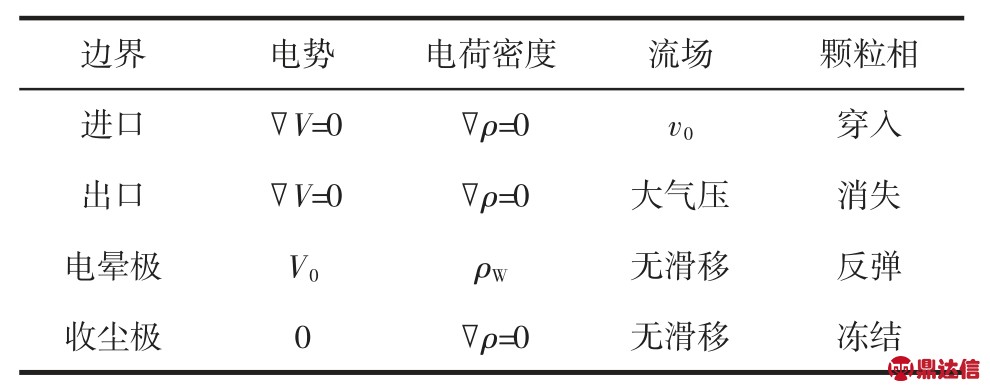
表2 中的ρW 可以根据Peek 定律来确定:

式中:s—相邻极线间间距的1/2(m);jP—极板的电流密度(A/m2);f—电晕线粗糙度因子;δ—气体相对密度,ri—电晕区半径(m)。
其中的 P0=1.01×105 Pa,T0=293 K; McDonald[9]等许多学者在模拟时均假设电晕区厚度为零,对于电晕区半径ri,近似取电晕线半径r0 进行的计算。而实际上电晕区半径要比电晕线半径要大,Conbine[10]给出如下经验公式:

2.2 模拟模型与数值计算
笔者以采用静电式油雾净化器的部分电离和收集芯段为研究模型,电极丝布置在电离芯段的中央,其上被加载直流高压电,电离芯片接地,收集芯片相间地加载直流高压电和接地。
利用COMSOL 软件计算双高压电源下油雾颗粒在净化器内的运动轨迹,涉及多物理场耦合分析:首先计算得到静电场分布,随后计算整体的流场分布,之后将流场速度与对流扩散相相互耦合,在此基础上计算整个空间内的离子浓度在稳态情况下的分布。再将结果代入粒子荷电方程中,计算不同粒径粒子的荷电量,最终使用粒子追踪模块获得粒子在上述条件下的运动轨迹。
2.3 实验模型
该实验系统主要由油雾净化器、进风管、出风管、采样器、热线风速仪、油雾发生器、高压电源、风机组成,在进风管及出风管上的测试孔测定风速及粉尘浓度(见图1)。
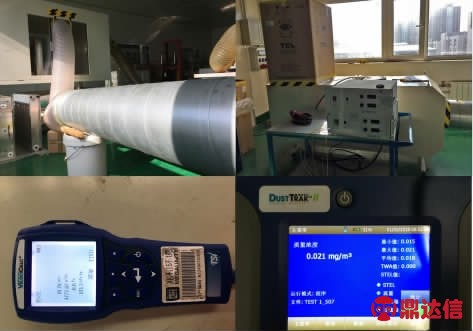
图1 实验系统图
3 结果与分析
3.1 电场强度的影响
通过实验,笔者得到电晕极电压为11.5 kV,入口风速为4.5 m/s,极板电压分别为3.5 kV、4.5 kV、5.5 kV、6.5 kV、7.5 kV 时净化器通道内的油雾运动轨迹(见图2)。
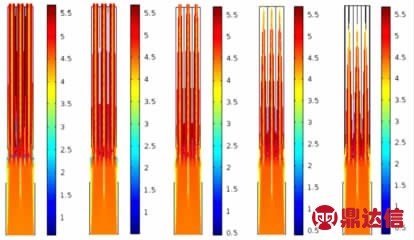
图2 不同电压下的颗粒轨迹
可以看出,油雾颗粒进入电离通道荷电后,在电场力的作用下逐渐偏移至极板表面而被捕获,且接地的极板上收集的颗粒明显多于接电的极板。随着极板电压的增加,油雾颗粒向极板的驱进速度和偏移量随之增大,极板电压在6.5 kV 时,油雾颗粒完全被极板捕集。
考虑到设备经济性和电压稳定性,该静电式油雾净化器的加载电压选择为11.5 kV/5.8 kV。
3.2 气流风速的影响
通过实验得到电晕极电压为11.5 kV,极板电压为5.8 kV,入口风速分别为2.5 m/s、3.5 m/s、4.5 m/s、5.5 m/s、6.5 m/s 时净化器通道内的油雾运动轨迹(见图3)。
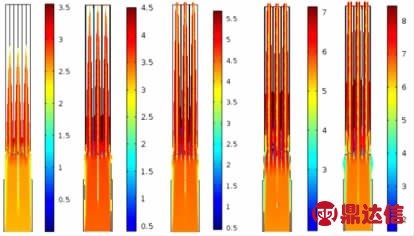
图3 不同风速下的颗粒轨迹
可以看出,随着气流风速的增大,油雾的停留时间减小,更多的颗粒来不及荷电或运动到极板表面就被气流带出电场通道,风速小于3.5 m/s 时,油雾颗粒几乎可以全部被捕集。
3.3 油雾粒径的影响
粒径是影响油雾脱除效率的重要因素,颗粒所受曳力及电场力均和粒径的大小有关,通过实验得到不同风速下油雾颗粒的分级脱除效率(见图4)。所处理油雾的粒径范围在0.1~2.5 μm 之间,其中1 μm 粒径的油雾颗粒占61.1%,小于0.5 μm 的油雾颗粒占8.9%。
可见,随着粒径的增加,分级效率也在逐渐增加,且较小粒径的油雾受风速的影响更加明显。即使当风速达到6.5 m/s,对于粒径大于2 μm 的油雾颗粒的脱除效率仍可接近97%。这是因为虽然电场力和曳力主导着颗粒的运动,但随着粒径的减小,曳力占颗粒总受力的比例增加:对于0.1 μm的油雾颗粒,在293 K 温度下其所受曳力可占总受力的94%左右,所以气流速度对其作用明显;而对于粒径大于2 μm 的油雾颗粒,受曳力和电场力的作用相当,在足够大的电场强度下,其效率的改变不大。
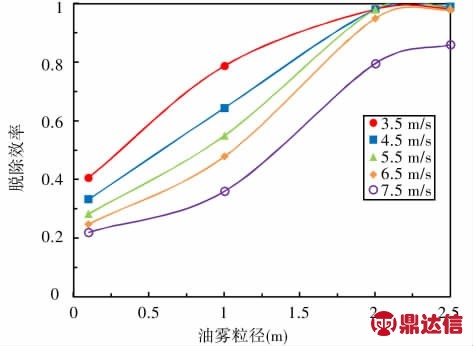
图4 不同风速下的分级效率
3.4 结构优化
笔者在保证相同收尘面积和气体流量的前提下,收尘极板数量保持不变,减小极板间距,并模拟其净化效率。
通过实验得到电压为11.5 kV/6 kV,电场风速为4.5 m/s,不同极板间距下模拟得到的净化效率曲线(见图5)。
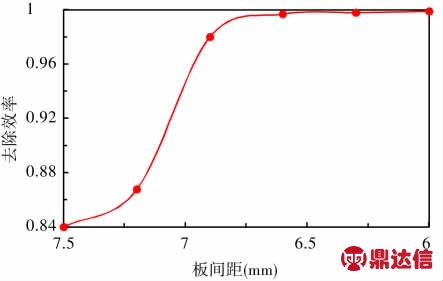
图5 不同极板间距下的净化效率
可以看出,在相同电场强度下,随着极板间距的减小,效率呈增加趋势,在间距为6.9 mm 时,增加斜率变缓,因此考虑到风速增加引起的湍动能和涡流大小的增加及设备运行的稳定性,选定6.9 mm 为最优极板间距。
通过实验测试对比原有设备和经过优化设备在电压11.5 kV/6 kV,不同电场风速下的油雾净化效率(见图6)。
可见,结构优化后设备效率明显提高,并未随风速的增加呈现明显下降趋势。结构优化后,相同风量下运行时效率提升12.6%,而设备体积减小21%,具有使用价值。原设备在风速为4.5 m/s,极板间距为7.5 mm 时的净化效率为86%;结构优化后极板间距为6.9 mm 时的净化效率接近于1。
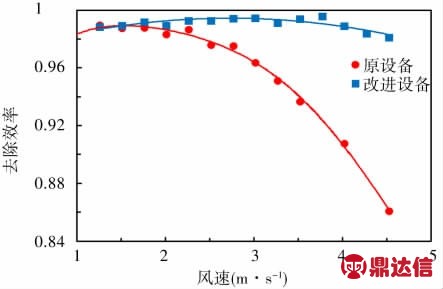
图6 不同风速下的净化效率
4 结 语
笔者以工业用静电式油雾净化器为例,用COMSOL Multiphysics 数值仿真软件对电场、流场和颗粒运动场耦合下的多物理场模型进行了数值仿真和实验验证。得到主要结论如下:
(1)随着极板电压的增高,油滴向极板的驱进速度和偏移量增加,去除效率也随之增加,当电压达到6.5 kV 时,油滴颗粒可以完全被极板捕集。
(2)随着入口流速增大,油雾在通道内的停留时间减少,向极板的偏移距离减小,在风速超过3.5 m/s 时,效率急速下降。
(3)随着油雾粒径的增加,其分级效率也在逐渐增加,且较小粒径的油雾因其曳力占总受力的比例大而受风速的影响更加明显。
(4)经结构优化后的设备效率提高12.6%,体积减小21%。
实验结果证明本文所述的数值模拟方法结果可靠,可以用于净化器结构参数和运行参数的优化及新产品研发。