摘要:针对煤直接液化反应器中的结焦问题,建立了多相流模型模拟了反应器内循环杯局部气-油煤浆两相的流动行为,得到了相含率等流体力学参数的空间分布情况。模拟结果表明,气液分离导致的泡沫聚并破碎以及雾沫夹带是形成结渣/结焦的主要原因。模拟研究了循环杯内堵塞程度与下降管中气含率的关系,表明随堵塞程度的提高,下降管中的气含率从0增加到34%,从而造成循环泵抽空。基于对结焦原因的分析,提出了优化的循环杯结构并进行了模拟分析。结果表明,改进后的循环杯结构可以有效强化气液分离,在极限条件下下降管中的气含率为14%,可以保证装置的稳定运行,为工业装置的改造提供了参考。
关键词:煤直接液化;强制循环悬浮床;多相流;模拟
引 言
神华煤直接液化示范工程于 2008年建成并投入运行,是世界上首套百万吨级煤直接液化工业装置。装置采用两个串联的强制内循环悬浮床反应器,具有反应器内温度控制容易、液相利用率高、可有效防止矿物质沉积的特点,日处理煤6000 t,是世界上最大的加氢反应器[1,2]。作为工业装置的核心设备,煤直接液化反应器是装置长周期稳定运行的关键因素。反应器内发生物料结焦堵塞造成循环泵抽空是影响反应器稳定运转的重要原因,而循环杯是最容易产生结焦的位置[3]。存在流动死区造成煤浆的长期滞留、局部供氢不足以及煤浆被溅射到气室壁面都可能成为结焦的原因[4]。
目前对于煤直接液化过程的研究开展了大量的研究工作,如物料及产品物性研究(油煤浆的黏度[5]、液化油及溶剂油的组成[6-7]等),不同煤种的液化特性、液化机理和动力学[8-10],液化残渣的组成、萃取分离及加工利用技术开发[11-13]等方面。对于煤直接液化反应器的研究相对较少,且主要集中于工业应用。吴秀章等[14]介绍了强制内循环反应器在煤直接液化工艺中从小试到中试和工业装置的应用,并和鼓泡床反应器进行了比较。杜海胜等[15]对影响煤直接液化反应器性能的因素进行了分析,提出了优化的操作控制措施。任相坤等[16]开展了强制内循环煤直接液化反应器流动性能的冷模与热模实验,考察了反应器内的固含率、气含率、压降、流速及气速等参数的分布情况。徐建伟等[17]研究了水-空气-煤粉体系的冷模实验装置中相含率的轴向分布规律。对于鼓泡床形式的液化反应器,Ishibashi等[18]研究了150 t·d-1的直接液化示范装置中鼓泡床反应器内气含率随气速、温度和压力的变化规律;李红星等[19]研究了空气-水-玻璃珠体系的连续内环流三相反应器的流动特性。在先前研究者的工作中,由于直接液化反应条件苛刻,因此冷模实验和实际工况相比物性与流动参数的对应存在困难;热模实验中由于装置的限制,对于循环杯等局部流场变化较大区域的测量存在困难。考虑到反应器的放大效应,现有的实验测量数据得到的规律只能作为工业反应器的参考。随着计算机硬件的快速发展,数值模拟研究可以发挥更重要的作用,为研究多相流流体力学提供了有力的工具[20-21]。由于计算量的限制,目前的数值模拟工作主要针对中试反应器且内构件进行了简化。
本文应用双流体模型,研究了煤直接液化工业反应器中气-油煤浆两相的流动行为,得到了循环杯局部的相含率、气速、液速等参数的分布情况,分析流场的空间分布对结焦形成的影响;在对目前循环杯可能存在的问题分析的基础上,提出了结构优化方案并进行了模拟以强化气浆两相分离,为缓解反应器的结焦问题提供了理论支持。
1 数学模型和模拟设置
1.1 数学模型
假设溶剂油和煤粉为混合均匀的浆液,采用欧拉-欧拉方法描述反应器中的气浆两相流动,并选用基于连续介质的双流体模型,具体控制方程如下。
流体连续性方程

流体动量守恒方程

式中,α为体积分数,下角标k为不同相,ρ为密度,t为时间,u为速度矢量,p为压力,g为重力加速度,μeff为有效黏度,M为相间作用力。
气-液两相之间存在着若干种相间作用力,如曳力、升力、虚拟质量力以及湍流扩散力等。其中曳力的影响占主导地位[22],Laborde-Boutet等[23]通过数值分析得出曳力值远大于(100倍以上)其他相间作用力。模型中主要考虑曳力,其形式为

式中,下角标l为液相、g为气相,Cd为曳力系数,db为气泡直径。
曳力系数表达式为

式中,Cd0为单气泡标准曳力系数,ω为气泡群的曳力校正因子,指数因子n取1[24],气泡直径采用式(5)[25]。单气泡相间曳力采用Tomiyma模型[26],该模型已经得到了研究者的广泛验证[27-29]。
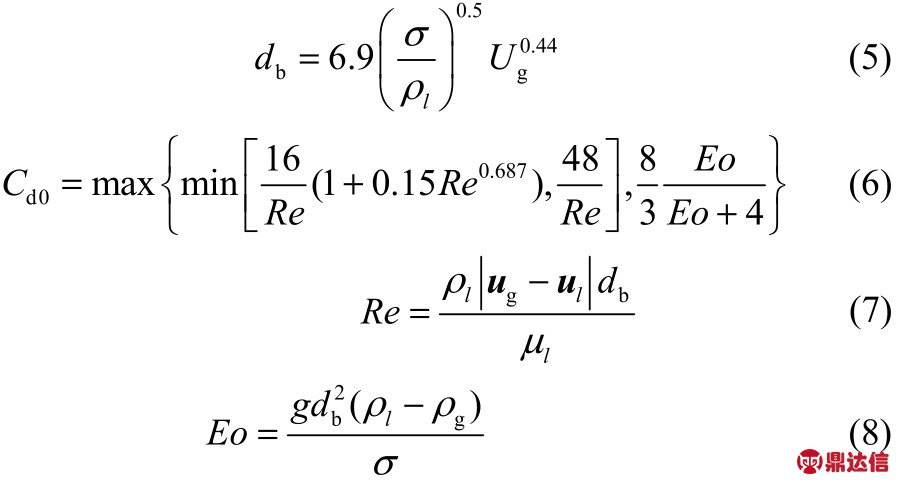
式中,σ为表面张力,Ug为表观气速,Re为Reynolds数,Eo为 Eötvös数。
气液两相流动处于湍流状态,采用 k-ε模型求解。
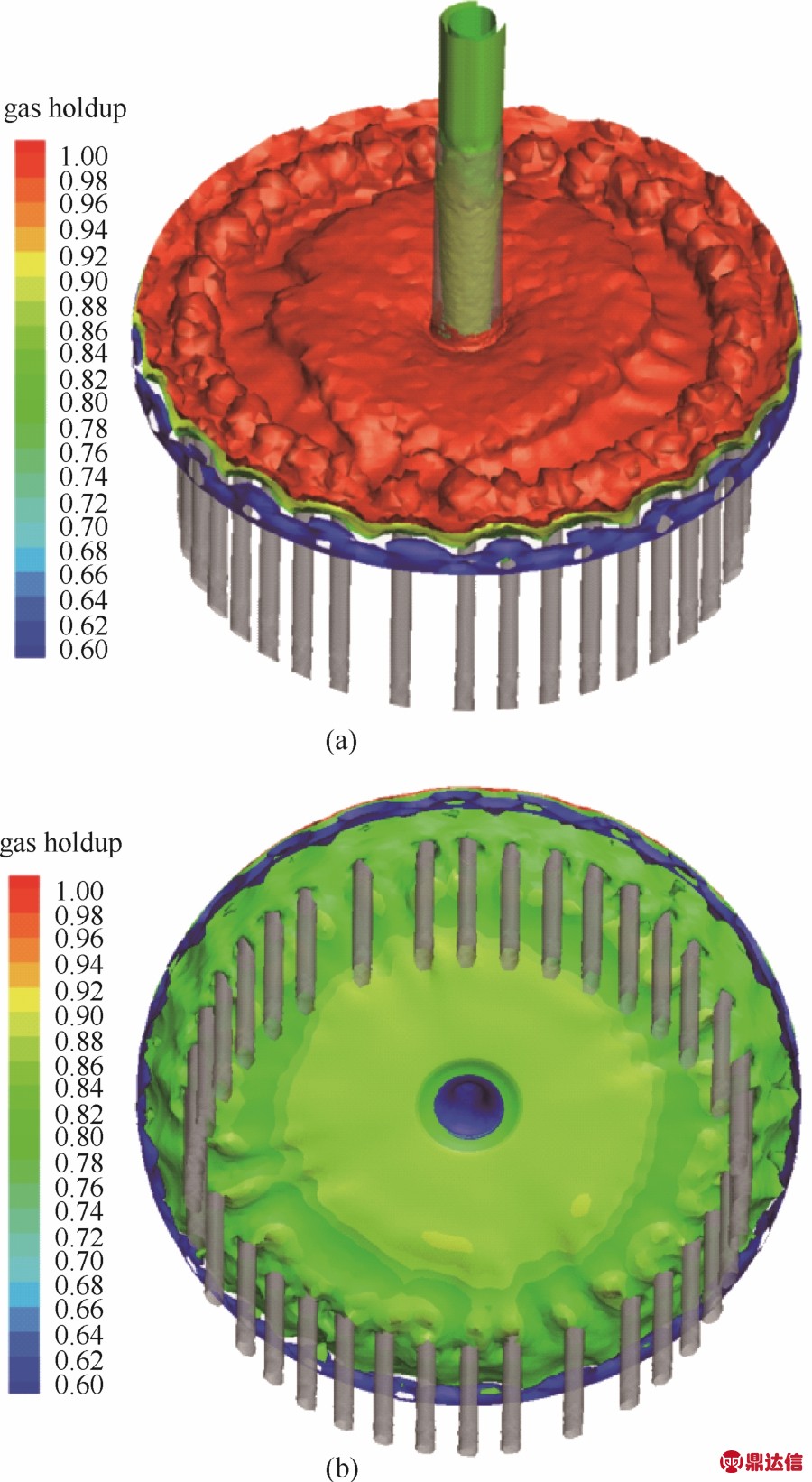
式中,k为湍流动能,ε为湍流动能耗散率,G为湍流动能产生项。
1.2 模拟参数
本文研究对象为工业规模的强制循环悬浮床煤直接液化反应器,主要针对循环杯的局部结构进行了三维模拟。气相为以氢气为主的混合气,液相为油煤浆。气液两相从底部均匀进料,向上运动经过循环杯,通过循环杯和反应器壳体间的环隙以及循环杯内部的升气管加速向上运动,在循环杯上方气相和浆液相在惯性和重力的作用下分离后,气相夹带部分液相从上部的出口管离开反应器,其余大部分液相在循环泵的抽吸作用下从循环杯内部经下降管离开反应器。计算构体如图1所示,图1(a)为整体结构,图1(b)为循环杯的局部结构。具体计算参数设置如表1所示。
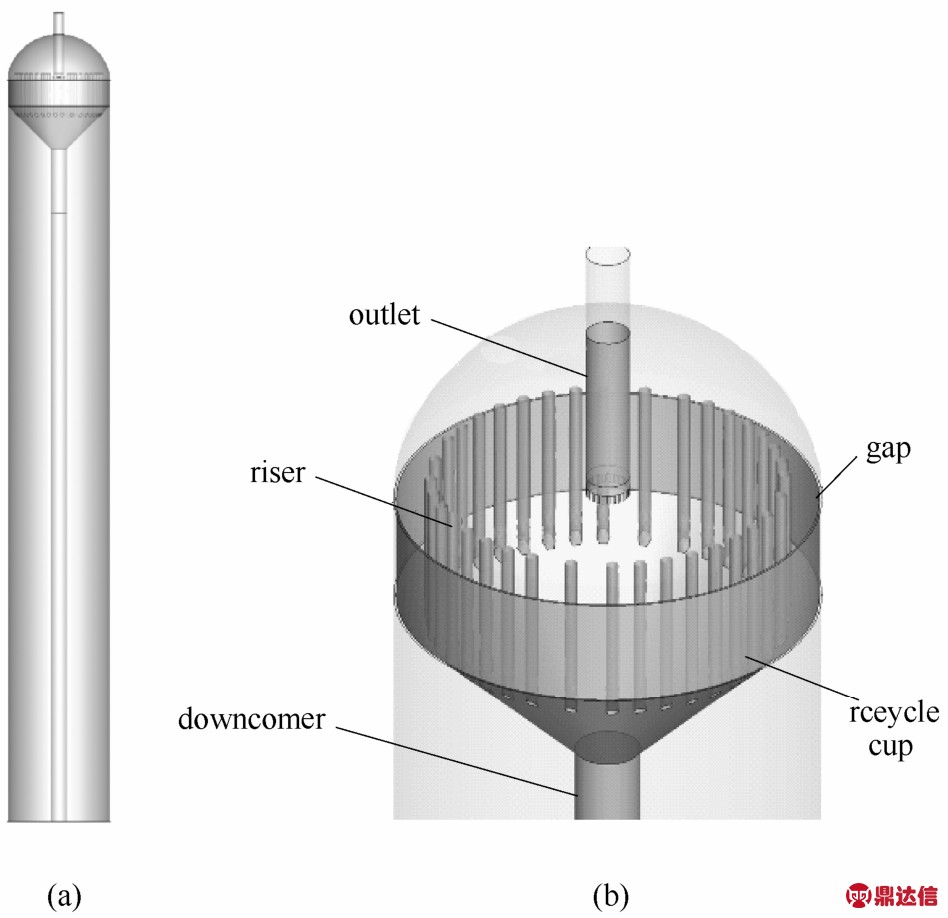
图1 反应器的计算构体
Fig.1 Schematic diagram of structure of reactor
1.3 边界条件和数值方法
模拟采用商业软件 ANSYS 14.0进行方程求解。初始计算区域中充满液相,两相的入口边界条件为速度入口,出口管采用压力出口边界条件,循环管出口条件为固定质量流量条件以保证循环量稳定,壁面为无滑移边界条件。
表1 几何参数和操作参数设置
Table 1 Geometric and operating parameters
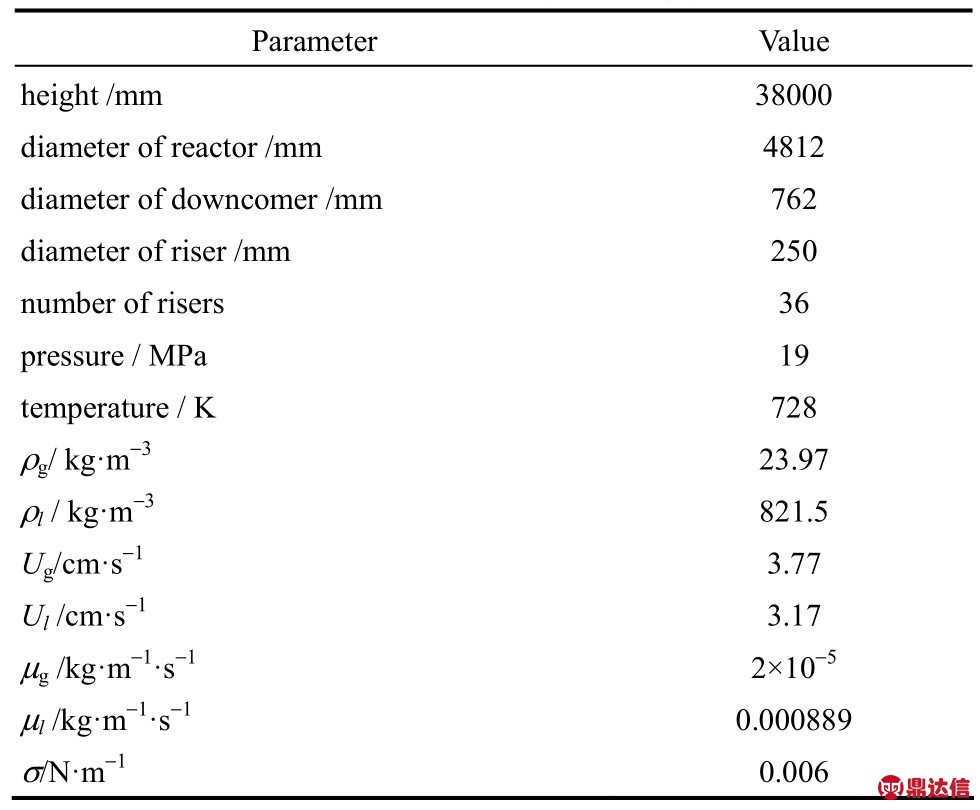
方程求解中压力-速度的耦合采用 Phase Coupled SIMPLE算法,质量守恒与动量守恒方程均采用二阶离散方式,时间步长设置为5×10-4s,模拟时间为4400 s,其中后2000 s用于数据统计。经过计算网格无关性验证后选取的计算网格数为240万个。
2 模拟结果和讨论
气含率总体分布和径向及轴向气含率分布的模拟结果如图2所示。由图2(a)可知,反应器内主体平均气含率为0.20,与工业反应器实测值一致;气液相经过循环杯时流通面积减小,气液相加速运动的同时气含率增大,经过循环杯分离后在循环杯上方形成气液混合区,混合区上方形成气室。不同高度处气含率的径向分布如图2(b)所示,循环杯上方的气含率分布界面则清晰地展示了循环杯对气液相分离的效果,循环杯上方基本为气相,中心处出口管内气体夹带部分液相离开;循环杯的圆柱体部分,在循环杯和反应器壁面的环隙间气含率为0.55,升气管内的气含率为0.42,说明气相在环隙和升气管中并不是均匀分配,而是更倾向于从环隙中上升;循环杯的圆锥体部分,在壁面附近形成了气含率略高的气垫层,其余区域气含率分布较为均匀;位置更低的反应器主体部分,气含率分布较为均匀,下降管中基本无气体,说明气液分离效果较好。反应器中心剖面上不同径向位置的气含率轴向分布如图2(c)所示,在反应器中心处气含率分布的模拟结果表明,在循环杯上端以下主要为液相,其以上气含率逐渐增加;在径向距中心1 m处,在循环杯的下方气含率基本稳定,在接近循环杯外壁面处有气垫层,气含率从0.20增大到0.36;循环杯内基本无气体,气含率接近于 0;在循环杯的上沿附近气含率从0迅速增加到1,其间气液分离层高度约0.5m;在径向距中心2 m处,在循环杯的下方气含率基本稳定,在接近循环杯外壁面处有气垫层,气含率从0.20增大到0.45,然后升气管内气含率基本稳定在0.44,其上部气室内气含率迅速增大至1。
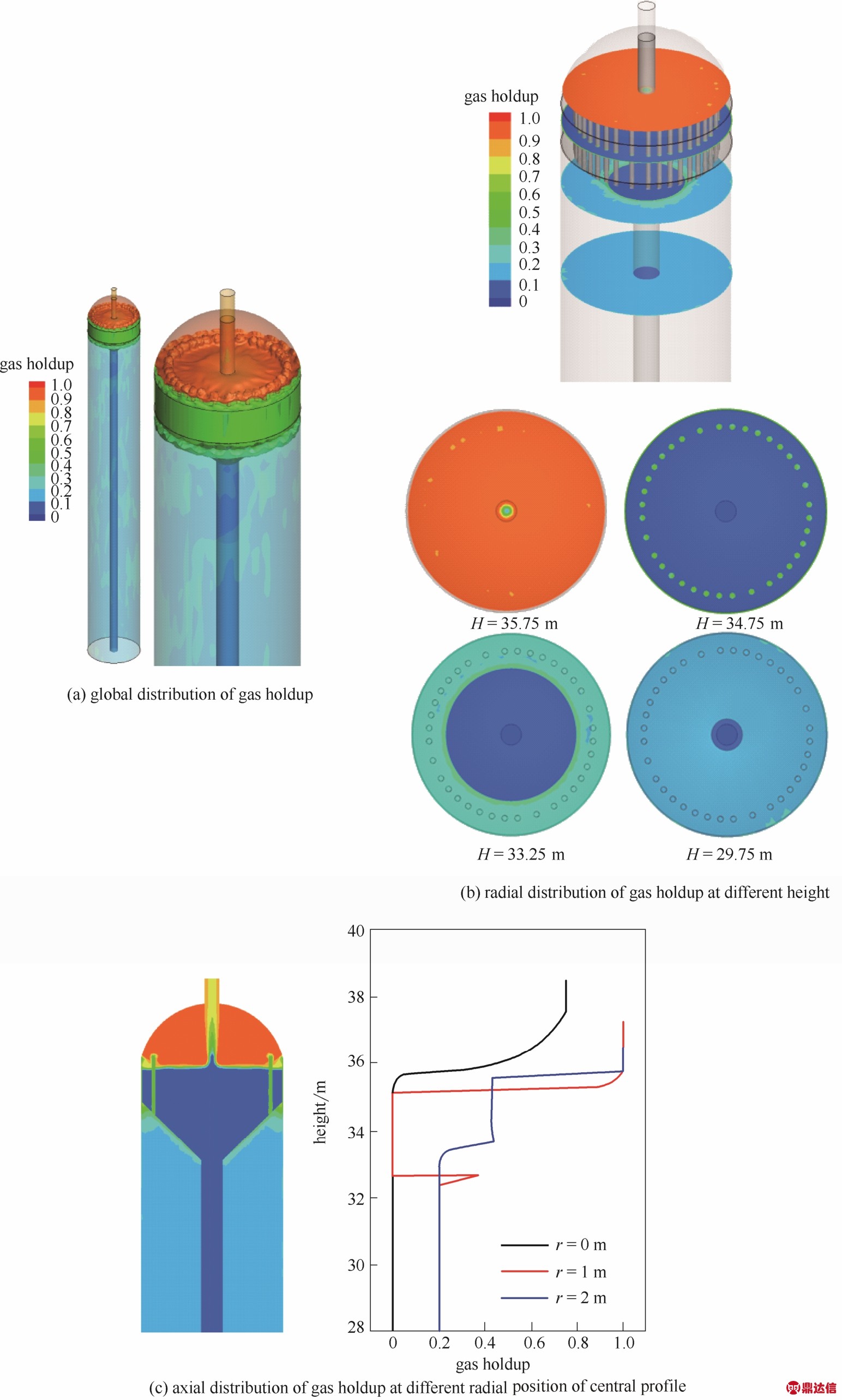
图2 气含率分布模拟结果
Fig.2 Simulation results of gas holdup distribution
图3为上述的气室、液相区和气液分离区的分布情况。同时模拟结果表明循环杯上方的气相流场存在环流,主要由于气液相加速通过循环杯后向上的速度较大,而出口为低压区,在压力梯度和惯性的共同作用下形成了环流。在气速较大的情况下则容易形成雾沫夹带。气液分离层中气含率较高的部分其性质更类似于泡沫,同时气液分离是动态过程,因此气液分离层的界面处于剧烈的变化过程。如图4(a)所示,气液分离界面的动态变化过程反映了泡沫的聚并破碎,形成了类似于煮粥的现象;图4(b)则展示了出口管对气液混合相的卷吸作用。图5展示了在气液分离区上方出口管附近存在浆液含量极低的区域,结合图3所示的气相环流,说明在出口管中下部附近存在雾沫夹带情况,工厂实际检修时该位置存在较明显的沉积情况。
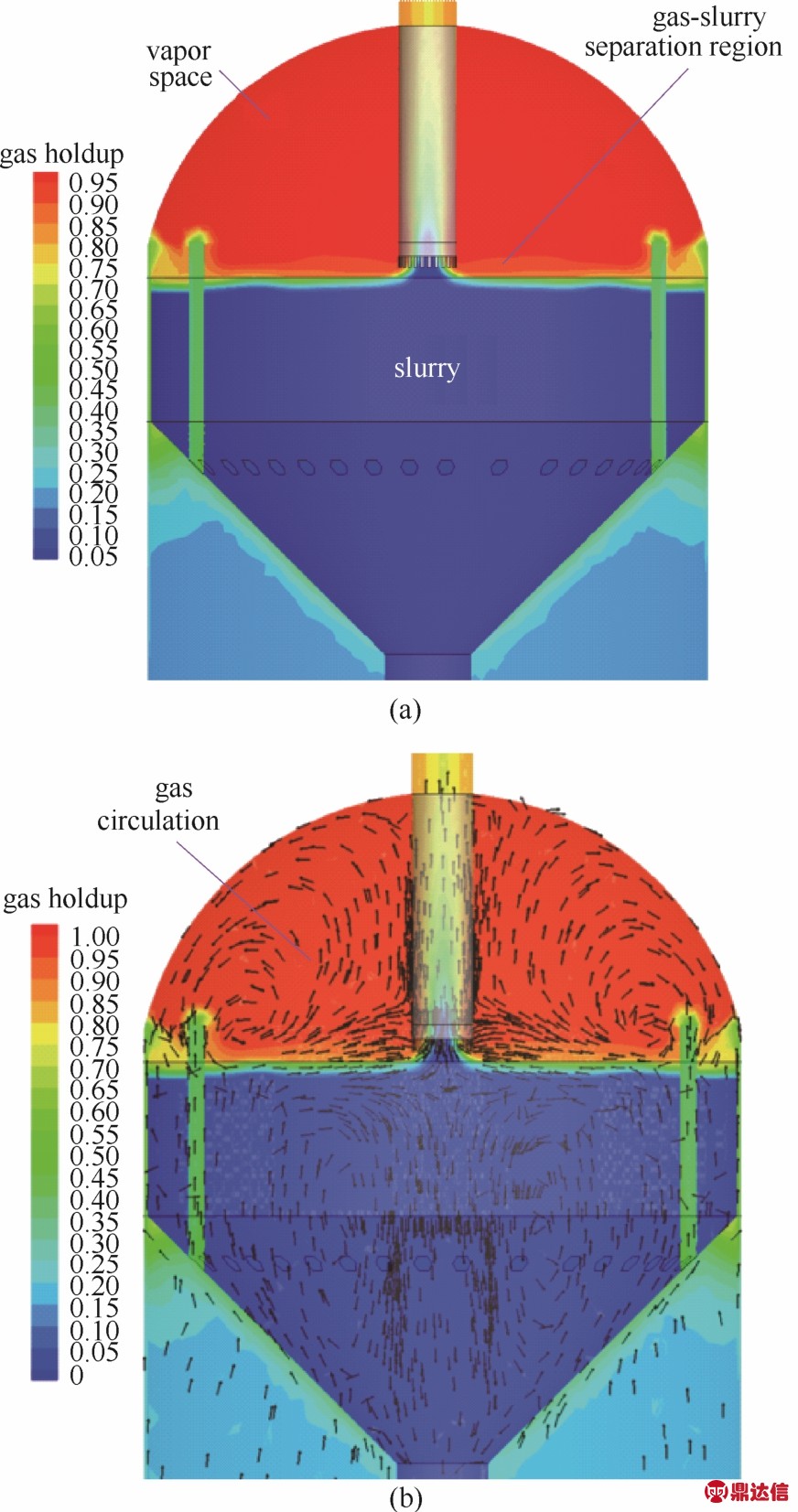
图3 气相流场分布的模拟结果
Fig.3 Simulation results of flow field of gas phase
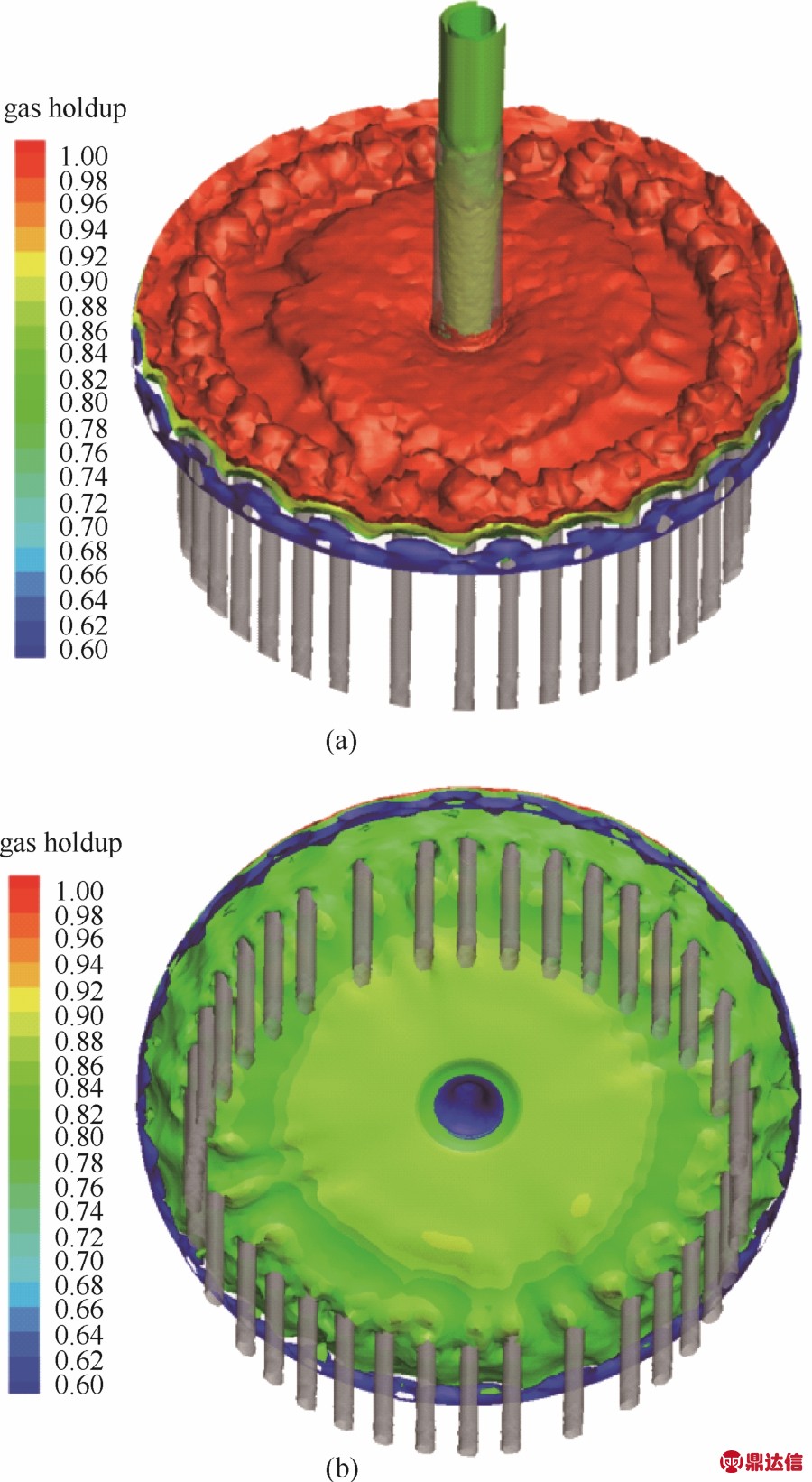
图4 气液分离界面的模拟结果
Fig.4 Simulation results of gas-liquid separation interface
模拟结果表明循环杯中形成堵塞的原因有:①由于气液分离过程中泡沫的聚并破碎造成泡沫层中的少量浆液被溅射到反应器壁面,在高温且缺少流体冲刷的条件下浆液中的煤粉及矿物质沉积在壁面形成结渣,而自由基及沥青烯等重组分则形成结焦;② 雾沫夹带则会将微量的浆液液滴沉积在更高的位置,如出口管壁面以及封头的穹顶等,造成反应器顶部的结渣或结焦;③ 由于缺少流体冲刷且供氢不足,结渣/结焦会不断长大,并掉落至循环杯内,部分从下降管中循环,部分则在循环杯累积,形成不同程度的堵塞。随运行时间的延长,堵塞情况则会越来越严重,直至停工。
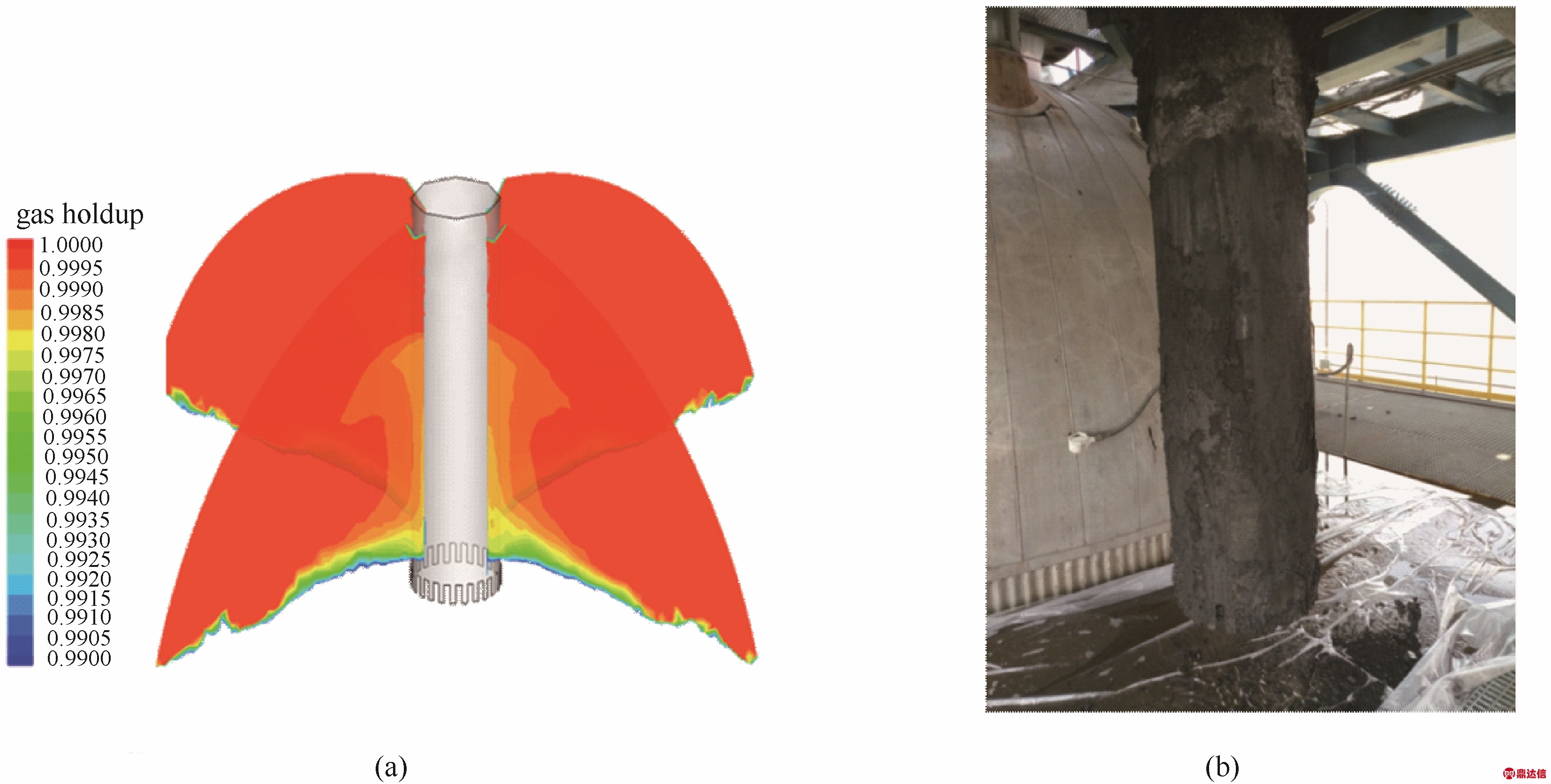
图5 雾沫夹带的模拟结果及实际情况
Fig.5 Simulation results of entrainment and practical case
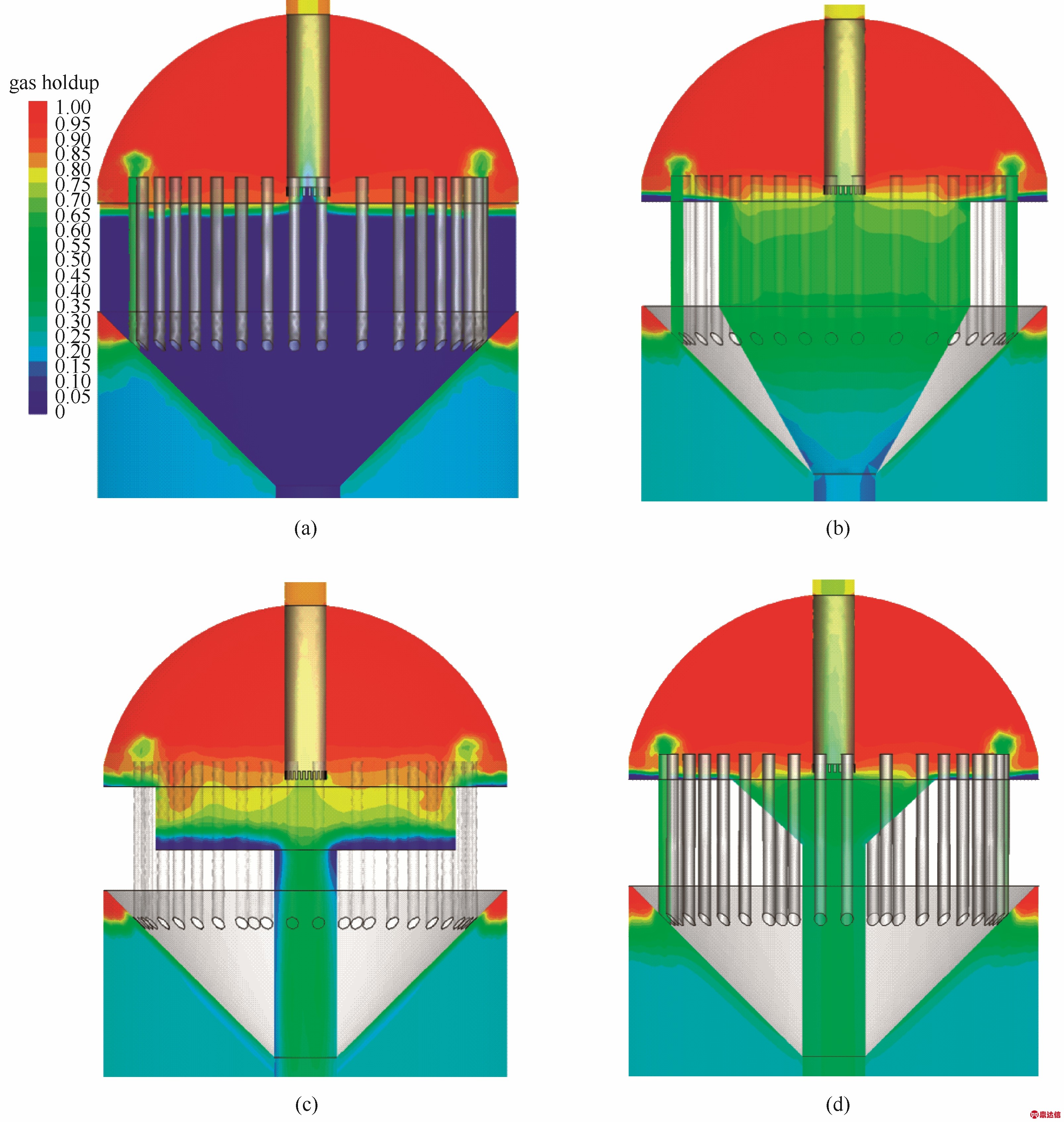
图6 不同堵塞程度工况的气含率模拟结果
Fig.6 Simulation results of gas holdup under different blocking conditions
基于以上分析,考虑到循环杯内的局部堵塞程度随运转时间的延长而增加,本文对循环杯内不同堵塞程度的影响进行了模拟。局部堵塞可能存在两种形式:① 在反应器壳体壁面形成沉积层从而结焦/结渣,并不断长大并脱落形成堵塞(即被堵塞的区域主要沿径向变厚,同时结焦脱落沿轴向沉积);②反应后的灰分及大颗粒煤粉、大块结渣等在循环杯底部累积形成堵塞(即被堵塞的区域主要沿轴向累积,同时壁面沿径向存在结焦)。4种工况及模拟结果分别如图6所示,图6(a)为环隙堵塞,图6(b)为循环杯内主要沿径向堵塞,图6(c)为循环杯内主要沿轴向堵塞,图6(d)为循环杯内严重堵塞。图中白色区域为假设的发生堵塞区域,无流体存在。如图6(a)所示,环隙堵塞时气液相进一步向上加速,升气管上方的射流高度增加,同时气液分离层厚度增加,循环杯内可以保持较好的气液分离效果;同时在集液杯堵塞处下方形成新的小气室。如图 6(b)所示,堵塞逐步积累后,气液分离效果变差,循环杯内气液无法有效分离,部分气体被夹带至下降管中,下降管中平均气含率为15%,同时升气管处于泡沫层中有可能成为新的结焦点。如图6(c)所示,在轴向上堵塞程度很高时,循环杯内处于泡沫层的状态且泡沫层厚度迅速增加,泡沫层的聚并破碎会加速壁面附近的结渣/结焦;大量气体进入下降管,下降管中平均气含率达到24%。如图6(d)所示,发生严重堵塞时,循环杯的分离功能基本失效,下降管中的气含率为34%,会造成循环泵抽空,从而装置被迫停工。工业反应器检修时的实际堵塞情况也介于图 6(c)、(d)之间,也说明了模拟结果的合理性。
3 循环杯结构优化分析
通过上述对结焦原因的分析,对循环杯的结构进行了优化以减轻反应器内的结焦。从减少泡沫层和结焦点的角度出发,提出了如图7所示的新型循环杯结构并进行了模拟验证分析。新的结构中取消了升气管,而流体的流通面积保持不变。
循环杯结构改进前后的气液分离效果的对比如图8所示。由图8(a)、(b)的对比可以看出结构改进后气液分离效果变化的总体情况,气液混合相的射流高度降低,气液分离层厚度减小同时泡沫减少,循环杯下方的气含率基本不变。由图8(c)、(d)的对比可以看出,结构改进后,由于泡沫层的减少,即泡沫的数量减少同时聚并破碎频率降低,从而气液分离界面更为平滑。由图 8(e)、(f)的对比可以看出,结构改进后,由于气液分离效果的强化,雾沫夹带现象也得到有效抑制。因此,模拟结果展示了改进后的循环杯结构可以更有效地将气液相分离。

图7 改进的循环杯结构
Fig.7 Revised structure of circulation cup
为了研究循环杯内严重堵塞时改进结构的效果,对循环杯内严重堵塞且环隙堵塞一半的工况进行了模拟。模拟结果如图9所示,在循环杯内严重堵塞的情况下改进后的结构依然可以保持较好的气液分离效果,气液分离层厚度较小且气液界面较平稳;在环隙的堵塞部分与未堵塞部分的交界处局部有明显的流体波动,剧烈的流体冲刷可以防止堵塞的进一步扩大。下降管中平均气含率为13%,可以保证循环泵维持工作。因此模拟结果也展示了改进后的循环杯结构可以在极限条件下更有效地将气液相分离,保证装置的稳定运行。
4 结 论
本文采用双流体模型研究了煤直接液化反应器内气液两相的流动结构。模拟结果表明气液分离导致的泡沫聚并破碎以及雾沫夹带是形成结渣/结焦的主要原因。模拟研究了循环杯内堵塞程度和下降管中的气含率的关系,随堵塞程度的提高,下降管中的气含率从0增加到34%,最终造成循环泵抽空。基于对结焦原因的分析提出了优化的循环杯结构并进行了模拟分析。模拟结果表明改进后的循环杯结构可以有效地强化气液分离,保证装置的稳定运行。本文建立了煤直接液化反应器的多相流模型并进行了数值模拟研究,模拟结果可以为工业装置的改造提供参考。
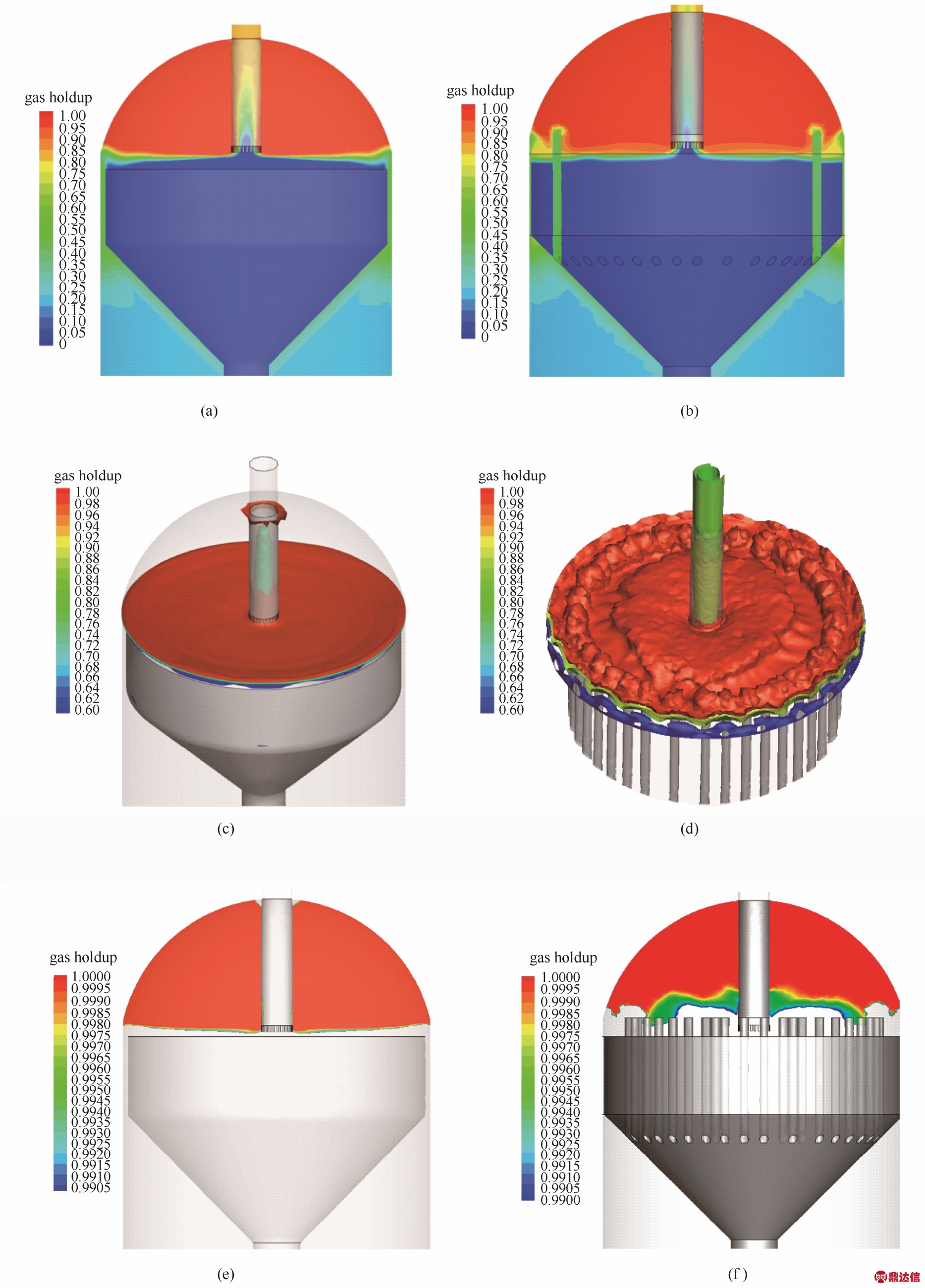
图8 结构改进前后气液分离效果的模拟结果对比
Fig.8 Comparison of gas-liquid separation effect between revised and original structure
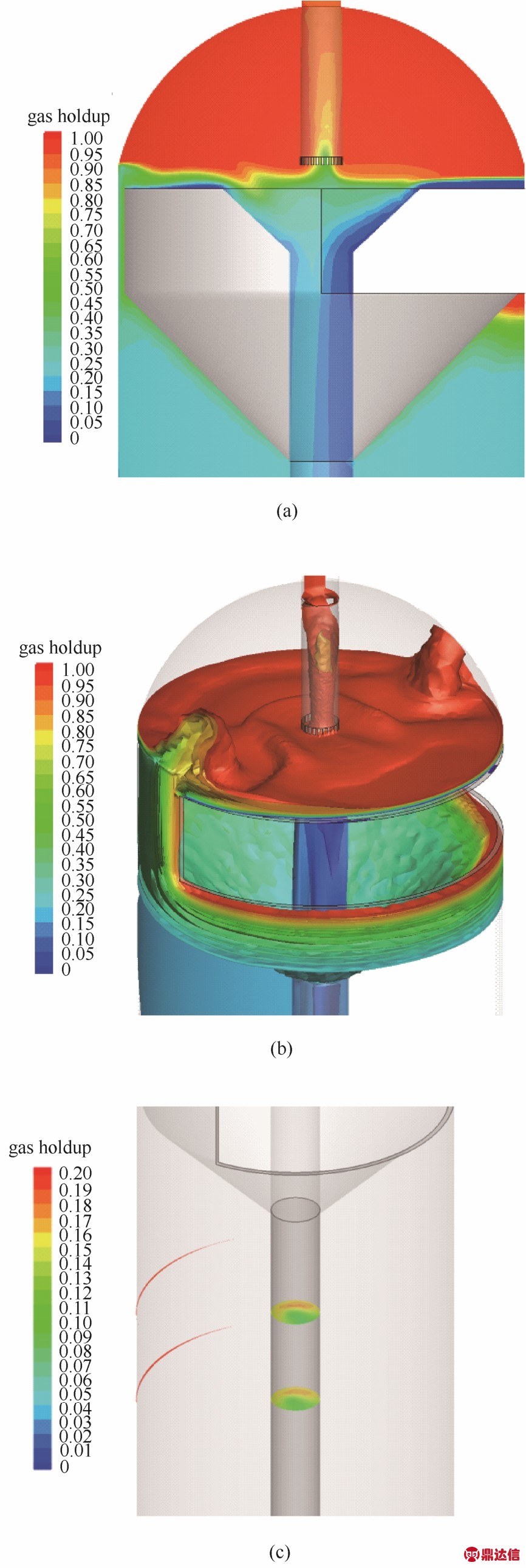
图9 结构改进后极限工况下气液分离效果的模拟
Fig.9 Simulation results of gas-liquid separation effect of revised structure under serious blocking
由于煤直接液化反应体系的复杂性,为了更准确地模拟反应器内多相流的特性,需要进一步对相间作用即曳力模型开展研究。在多气泡体系中,需要对单气泡曳力系数经验关联式进行修正,在修正过程中存在一些经验修正因子[30]。Yang等[31-33]提出了气液体系的多尺度模型,消除了对经验修正因子的依赖,并扩展应用于气液固三相体系,实现了对环流反应器的模拟。未来结合多尺度模型,有望进一步提高模拟精度,为煤直接液化工业反应器的优化提供支持。