摘要以一个典型汽车零部件机加工车间为对象,调研了其生产工艺,分析了油雾散发的基本原理。为了监测车间内空气中油雾浓度动态水平,开发了油雾在线监测系统,对车间内油雾浓度进行了连续观测,分析了典型位置油雾浓度与区域设备的关系,并调研了车间内设备油雾净化器安装情况,测试了油雾净化器的风量与出口浓度。结果表明:在生产期间车间呼吸区的油雾浓度显著高于美国国家职业安全与健康研究所(NIOSH)推荐的油雾接触限值(0.5 mg/m3);油雾排放源头控制至关重要,在过滤、离心和静电等多种净化设备中,静电净化设备出口浓度最低,并能维持较高的风量。
关键词工业车间 油雾 浓度 监测 净化
0 引言
室内空气中的颗粒物会对人体健康造成危害[1],治理室内空气中颗粒物污染已经成为全世界的共识。民用建筑室内颗粒物主要来自于室外大气[2-3]与厨房[4],其控制理论与方法已有丰富的研究成果[5],近年来民用建筑室内颗粒物控制进步显著。而工业建筑则不同,以机加工车间为例,其室内污染物主要来自机加工工艺使用的切削液(其中零部件精加工应用最广泛的切削液为乳化液(含有矿物油、防锈添加剂等)[6],主要用途是冷却与润滑),在使用中切削液经历与高速旋转的刀具激烈撞击和高温蒸发等过程,会不断产生油雾颗粒物[7],颗粒物浓度远超一般民用建筑室内空气颗粒物浓度,其粒径主要在2.5 μm以下[8],可以沉积到人体肺部[1],严重威胁工作人员健康[9]。
1996年,美国学者针对某滚珠轴承生产厂进行了调查,该厂厂房内油雾浓度高达0.65 mg/m3,导致4%接触油雾的工人患上了哮喘病,远超没有与油雾接触的工人的患病比例[10]。2013年,瑞典研究者对来自25家工厂的总共超过1 500名工人的调查表明,超过70%的人反映存在油雾引起的身体问题[12]。由于我国职业健康工作仍处于起步阶段,国内还未见公开报道的专门针对油雾的职业病调查数据,但工业车间的油雾污染形势却很不乐观,2003年在26家金属加工企业的43个车间进行的油雾浓度抽样调查发现,超过37%的车间油雾浓度超过1 mg/m3[7],另外,根据国家统计局发布的2015年数据,仅以零部件精加工为主的设备制造、汽车制造业的从业人数就超过1 000万人,因此工业车间油雾污染物的控制意义重大。室内空气污染物的控制方法主要包括源头控制、通风控制与净化控制,各种方法在民用建筑均有良好的表现[5],而工业车间由于环境的复杂性,虽然工业通风方法不断发展[12-14],但工业车间的通风净化仍然面临挑战[15]。此外,工业车间内油雾浓度的监测也很重要,对于内部空间大、油雾颗粒浓度高的工业车间,采用APS,OPC和DUSTTRAK这类体积大、成本高的标准颗粒物测量仪器,难以对车间油雾浓度实现长期的、多测点的动态监测。近年来,传感器、数字电子学和无线通信技术领域的进步促进了一种新的空气污染监测模式的出现[16],通过便携式低成本传感器网络系统,该监测模式可以对空气污染物实现高时空分辨率的监测[17]。
本文选择某汽车零部件加工车间作为研究对象,进行了以下研究工作:1) 调研了该车间的主要生产设备和工艺,测量了每台设备开门和关门情况下油雾颗粒物的浓度,确定了该车间内生成油雾的主要污染设备和工艺;2) 开发了油雾在线监测系统,通过连续观测车间内的油雾浓度,监测了油雾浓度的动态水平,并分析了典型位置油雾浓度与区域设备的关系;3) 调研了车间内设备加装油雾净化器后的油雾浓度情况,测试了油雾净化器的排风量、出口浓度和被净化设备的开门浓度,用以评估净化器的净化效果。
1 车间设备与工艺
1.1车间主要设备
该汽车零部件加工厂长306 m、宽90 m、高8 m,主要生产差速器、传动轴、等速万向节和盘式制动器等产品,包括球形壳、保持架、三销轴、滚子、轴等多种零部件及相应部件的组装。由于生产品种多、产量大,车间内部设备布置很紧凑,且每个零件的生产过程都需要经过加工、倒角、去毛刺、淬火、回火、研磨及多次清洗,不同类型的设备在生产线中的布置十分复杂,以球形壳的加工为例,图1给出了生产工艺流程。
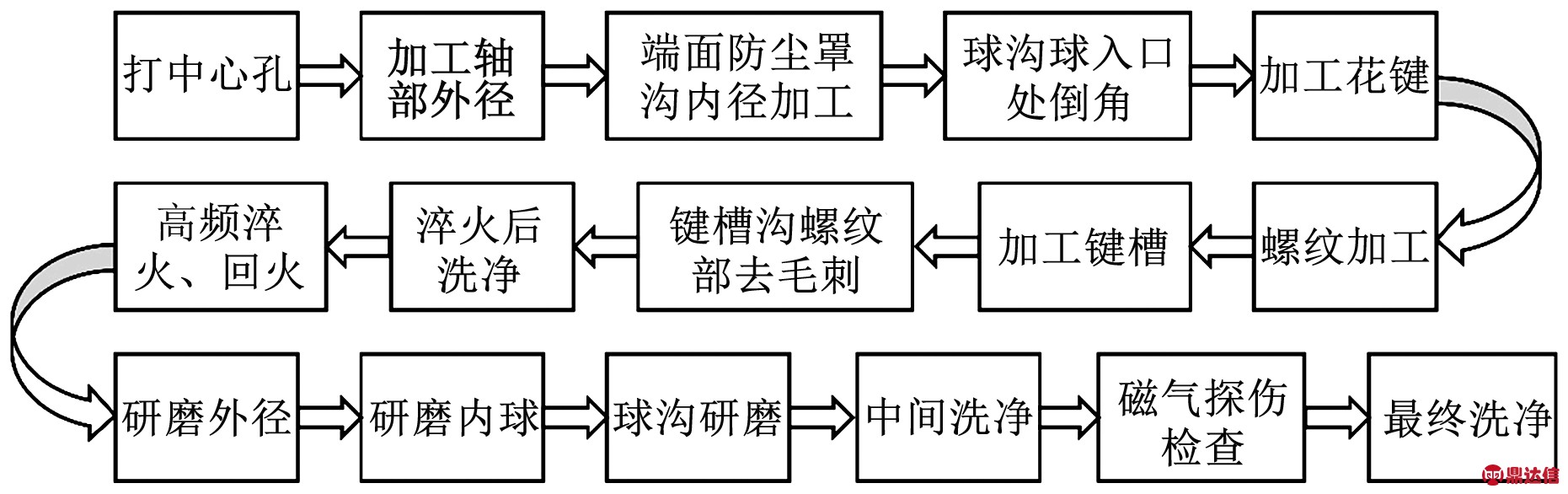
图1 球形壳加工生产工艺流程
为了更好地评估车间内的油雾污染与净化情况,对车间内的设备与工艺类型及加工液使用情况进行了详细调查,结果见表1。
该车间内共有520台机加工设备,分20种设备类型,主要有数控车床、数控外圆磨床、低压清洗机及数控加工中心设备。
1.2车间主要工艺与油雾的产生
该车间内用于生产的主要工艺有研磨、车削、铣削和拉削。在生产过程中,砂轮和刀具与工件的高速相对运动会产生大量的摩擦热[18],为了冷却、清洗、润滑和保护刀具及工件,会使用相应的金属切削液[19]。由表1可知,该车间使用的金属切削液主要为体积分数3%~5%的乳化液与体积分数5%~10%的半合成切削液。由于切削液与工件的撞击作用、工件旋转产生的离心力作用及切削液的蒸发和冷凝作用,车间内会形成油雾[20]。此外,高频淬火和清洗过程中使用的淬火液和清洗液也会受高温影响蒸发生成油雾。机加工过程中油雾的产生机理见图2。
2 车间油雾监测
2.1单台设备油雾浓度测定
由于该车间工人工作时需要正对机加工设备进行取、放工件等操作,因此研究时不仅对车间内整体油雾浓度进行了检测,还逐台测量了不同设备工作时的油雾浓度,包括操作门开启时和关闭时的油雾浓度,测量了安装油雾净化器的设备净化器出口处的油雾浓度与风量。测量仪器为某品牌A4-CG颗粒物传感器,测量原理为激光光散射法,测量的粒径范围为0.3~2.5 μm,测量使用的传感器由使用称重法测量颗粒物质量浓度的某公司TSP颗粒物切割器进行校准。测量单台机加工设备的关门油雾浓度时,将传感器靠近设备门,连续读取数据,得到油雾颗粒浓度的平均值;测量单台机加工设备的开门油雾浓度时,传感器放在同一位置,连续读取数据,得到油雾颗粒浓度的平均值。
表1 设备与工艺类型及加工液使用情况
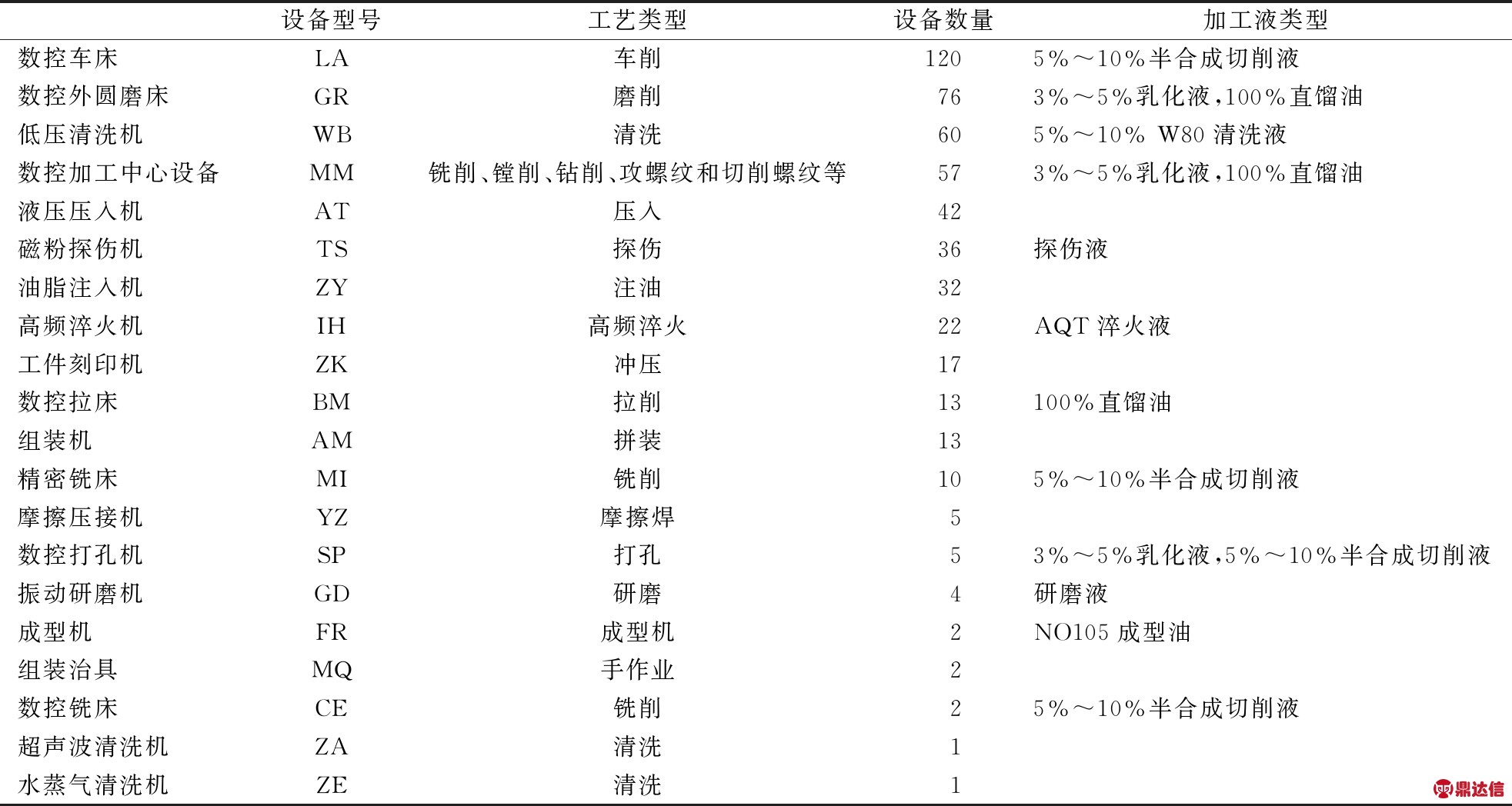
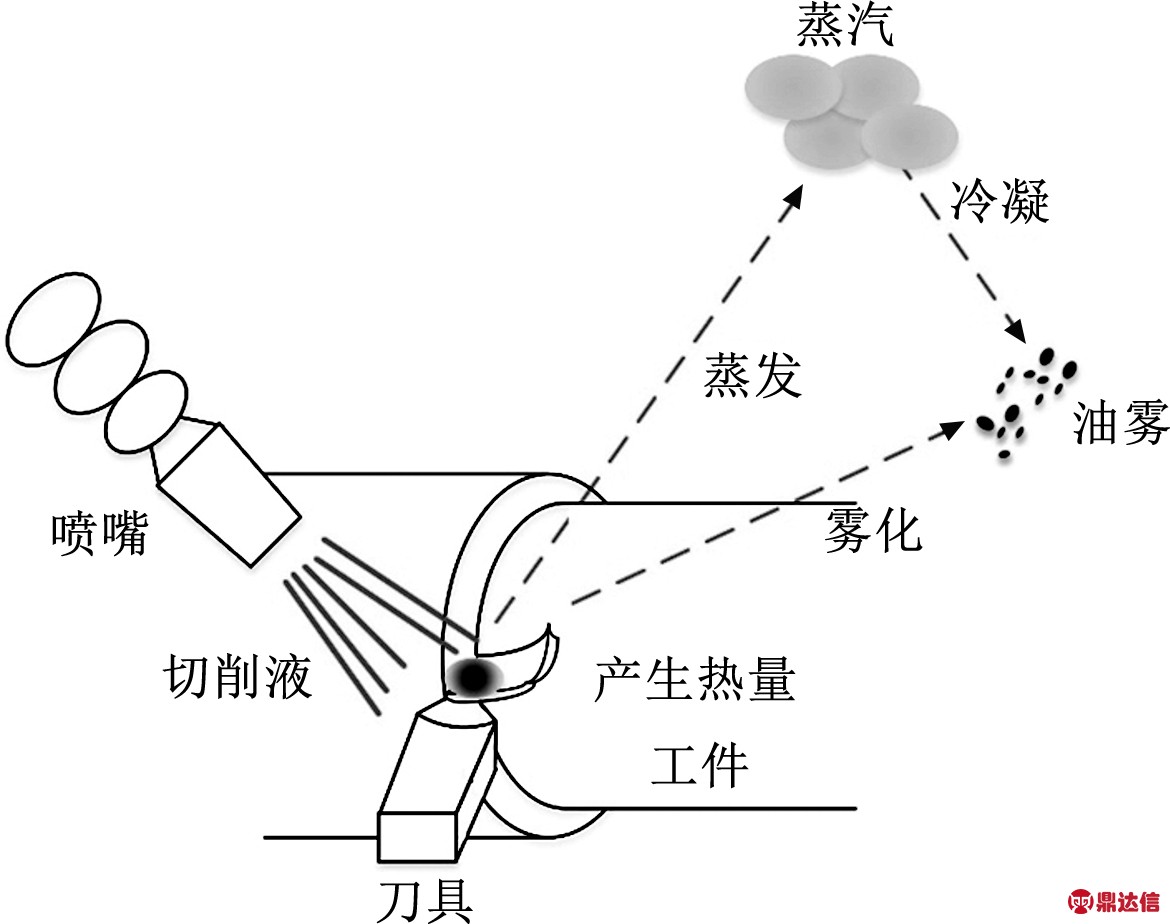
图2 机加工过程中油雾的产生机理[21]
本次共测量了包含17种类型的426台设备,图3给出了不同类型设备开、关门时的油雾浓度平均值。
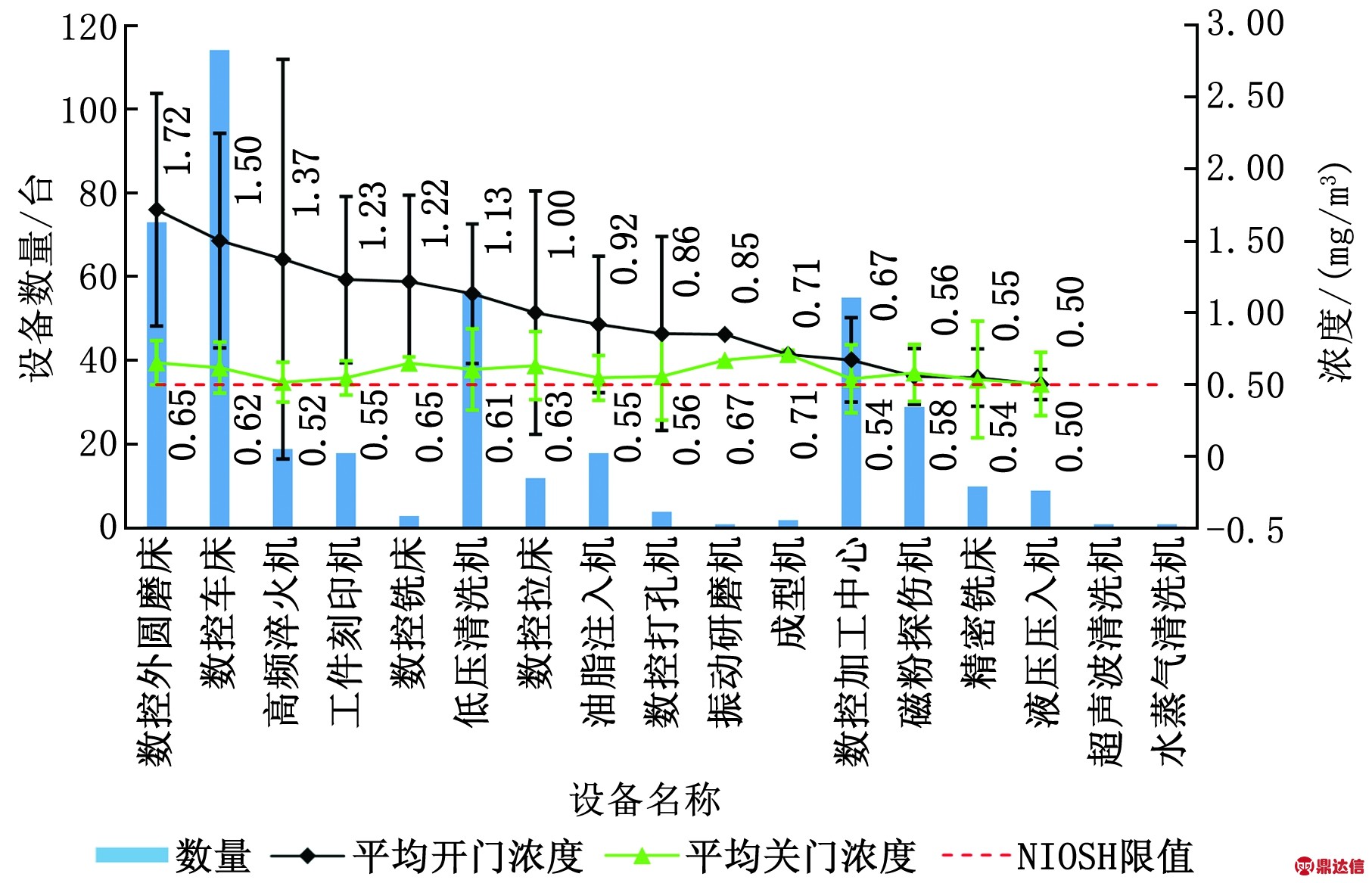
图3 不同类型设备开、关门时的平均油雾浓度
美国国家职业安全与健康研究所(NIOSH)推荐的油雾接触限值为0.5 mg/m3[22],日本职业健康协会规定的油雾控制限值为3 mg/m3[23]。该工厂设备的操作门开启时,共有195台设备的油雾浓度大于0.5 mg/m3,5台设备的油雾浓度大于3 mg/m3,分别占调查总数的45.8%和1.2%;操作门关闭时,共有147台设备的油雾浓度大于0.5 mg/m3,占调查总数的34.5%。由图3可知,车削、磨削、高频淬火、低压清洗和铣削等生产过程产生的油雾浓度较高,且数控车床、数控外圆磨床、高频淬火机、低压清洗机和数控加工中心设备的数量较多,共占调查设备总数的74.4%,是该工厂的主要污染设备。
2.2在线监测系统
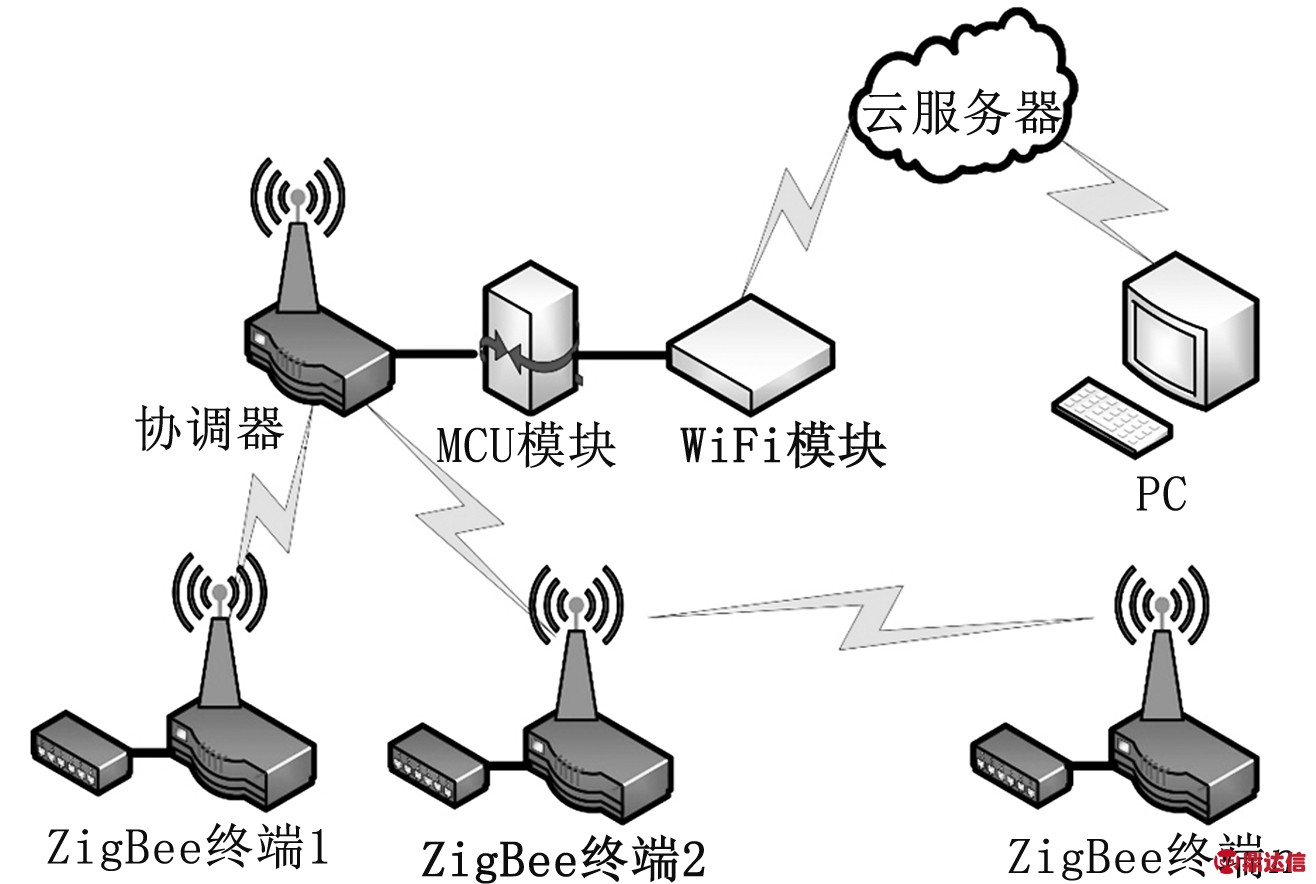
图4 监控系统结构
为了实现工厂油雾的实时监测,开发了一种基于ZigBee的无线传感器网络监测系统,该系统结构如图4所示,整个系统包括若干ZigBee终端、ZigBee路由器、协调器、MCU模块、无线模块、云服务器及PC端。
2.3车间油雾动态监测
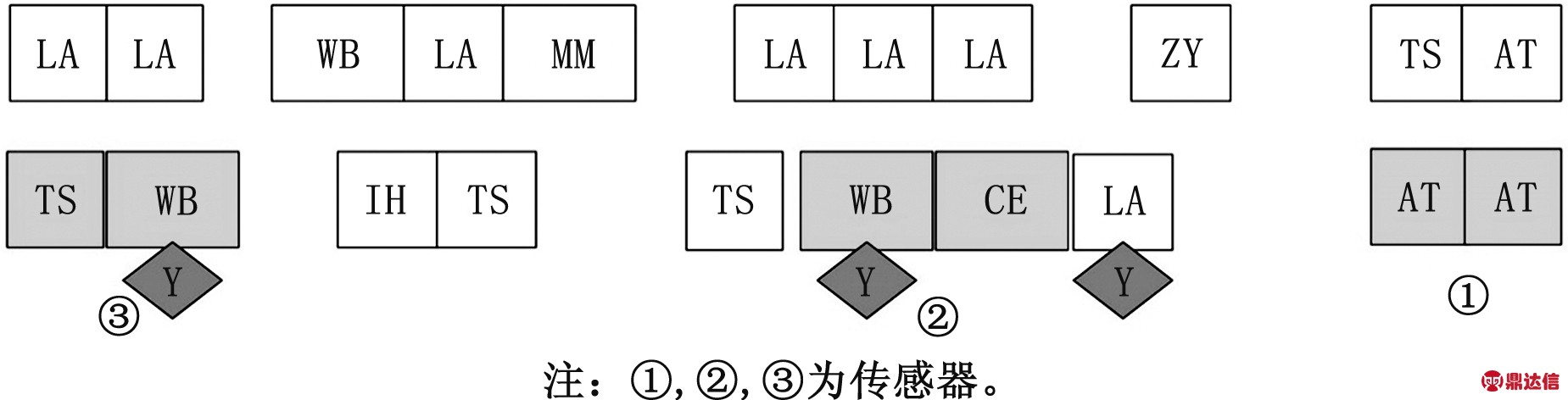
图5 传感器平面布置
在2018-07-16—2018-08-10期间对车间油雾浓度进行了动态监测,3个传感器的平面布置如图5所示,其中Y表示相应设备配置的净化器。图5中3台净化器为同一品牌同种型号,均为上出风;3个传感器安装在厂房同一列的支撑柱上,高度为1.5 m,处于车间工人的呼吸区,①号传感器安装在2台液压压入机附近,②号传感器安装在低压清洗机和数控铣床中间靠后,③号传感器安装在低压清洗机和磁粉探伤机中间,②号、③号传感器距离就近的净化器的垂直距离均为1.2 m。为了能在海量的传感器监测数据中提取准确、有价值的信息给使用者,需要对数据进行深入分析,科学、高效地对数据进行处理。目前常用的传感器数据处理方法有:使用盲源分离和独立成分分析方法改善传感器的稳定性;使用粒子群优化算法选择最小二乘支持向量回归的惩罚因子和核函数参数,建立最优的传感器回归模型;使用小波分析和小波熵等方法对传感器测试信号进行特征提取,以抑制噪声的影响。本文通过综述现有传感器数据处理方法,针对实际工厂测试环境,依据拉依达准则[24]对测试数据进行分析。
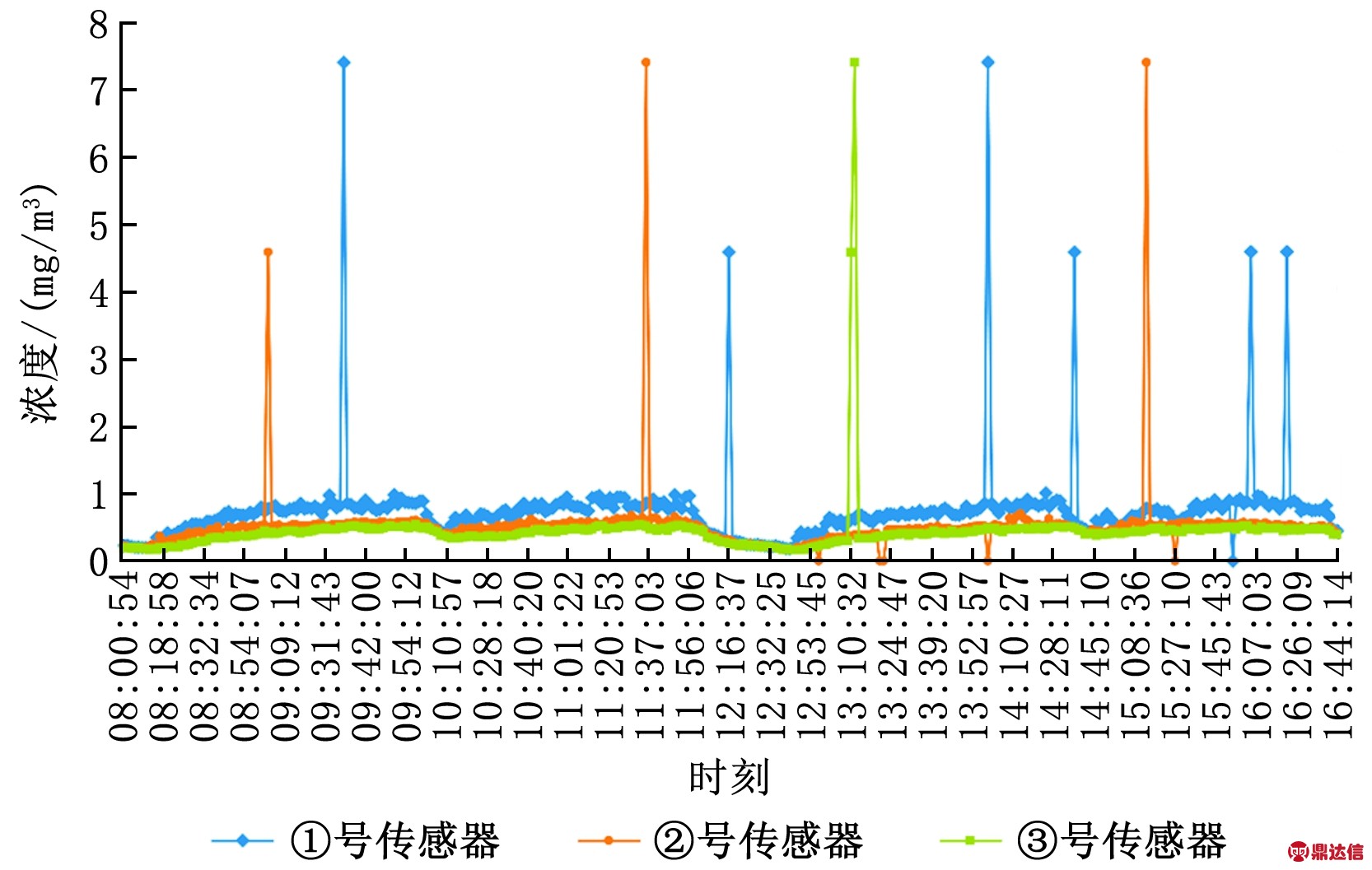
图6 2018-08-09车间油雾浓度动态监测结果
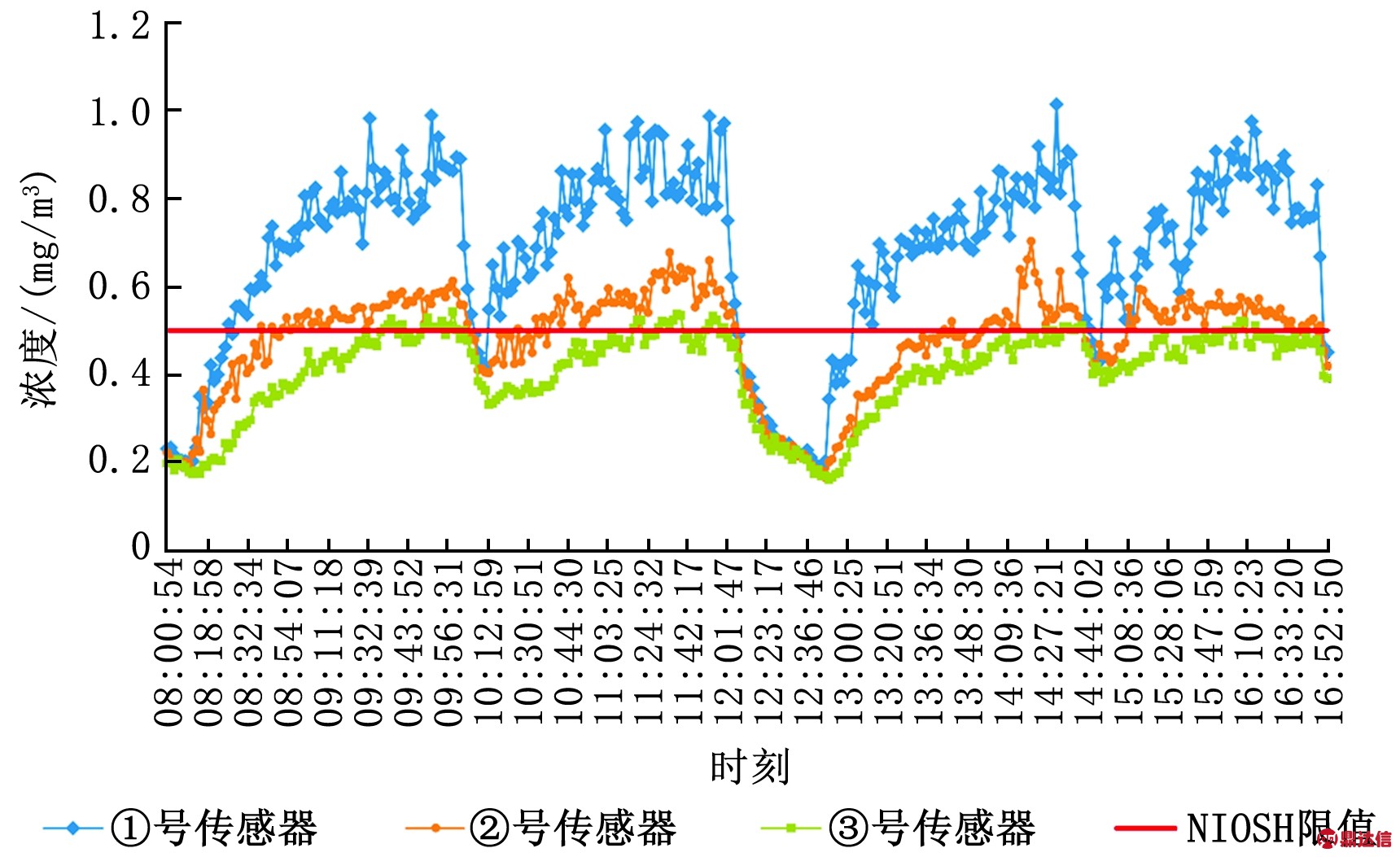
图7 处理后的油雾浓度动态监测结果
图6给出了2018年8月9日08:00(上班时刻)—17:00(下班时刻)期间3个传感器的实时监测值。从图6可以看出,有异常数据出现。采用拉依达准则算法对测试数据进行处理,剔除异常数据,最终整理出的结果如图7所示。以下分析基于清洗后的数据。
从图7可以看出:浓度波动有3个下降时间段,分别为10:00—10:10,12:00—13:00,14:30—14:40,这是由于这3个时间段为休息时间,设备不生产,但车间内的排风系统仍继续运行,车间内油雾得到稀释和扩散,因此3个测点测得的油雾浓度均出现快速衰减,并且设备停止加工的时间越长,3个测点衰减后的浓度越一致,尤其在12:00—13:00这一时间段,3个传感器监测得到的浓度值几乎重合;设备重新开始生产后,3个测点的油雾浓度均开始上升,约1.5 h后油雾产生量与排风系统排出的油雾量达到平衡,3个测点的油雾浓度上升缓慢,接近稳定状态。
另外,①号传感器测出的浓度要比②号和③号传感器的监测值高,这是由于②号和③号传感器附近的设备配备了净化器,而①号传感器附近的液压压入机未安装净化器。对比②号和③号传感器采集的数据,浓度变化趋势几乎一致,而②号传感器测出的浓度略高于③号,这是由于数控铣床生产中所产生的油雾浓度要高于磁粉探伤机,这与图3单台设备测量结果一致。
对比图7中美国国家职业安全与健康研究所(NIOSH)给出的油雾接触限值0.5 mg/m3[22],①号、②号和③号传感器监测到的油雾浓度值超出限值的时间分别为7.35,5.31,1.21 h。由此可知,净化器的使用能够大大降低油雾的污染程度,不同工艺所产生的油雾浓度有较大的差异。
3 车间净化设备现状评估
针对早期工厂油雾污染严重的问题,该车间已安装了116台、9种类型净化器用于降低空气中油雾浓度,笔者对这些净化设备的相关信息进行了调查,结果如表2所示。不同净化器的净化能力相差较大,原因有2个:一是不同品牌净化器的配置不同,主要体现在风量和净化原理上;二是部分净化器由于维护不及时,内部产生阻塞,降低了净化效果,造成即使是同一品牌的净化器,净化能力也存在不同。
表2 车间内油雾净化器调查结果
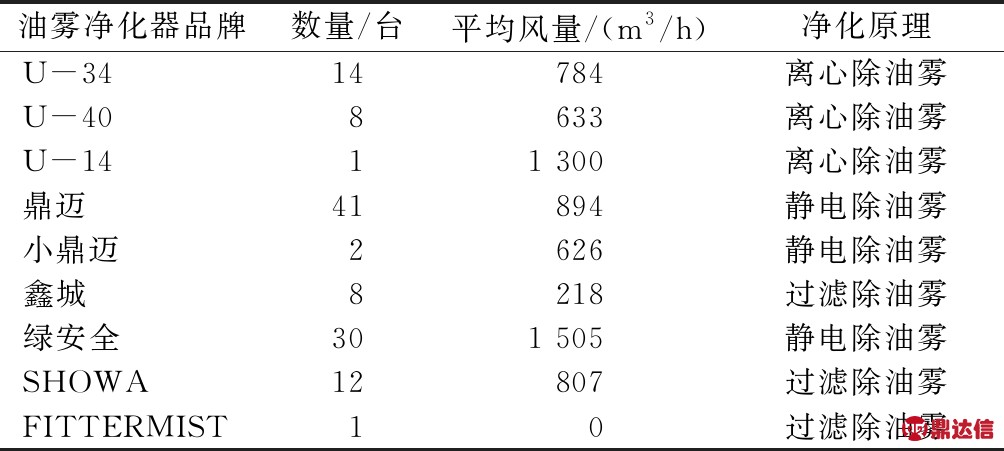
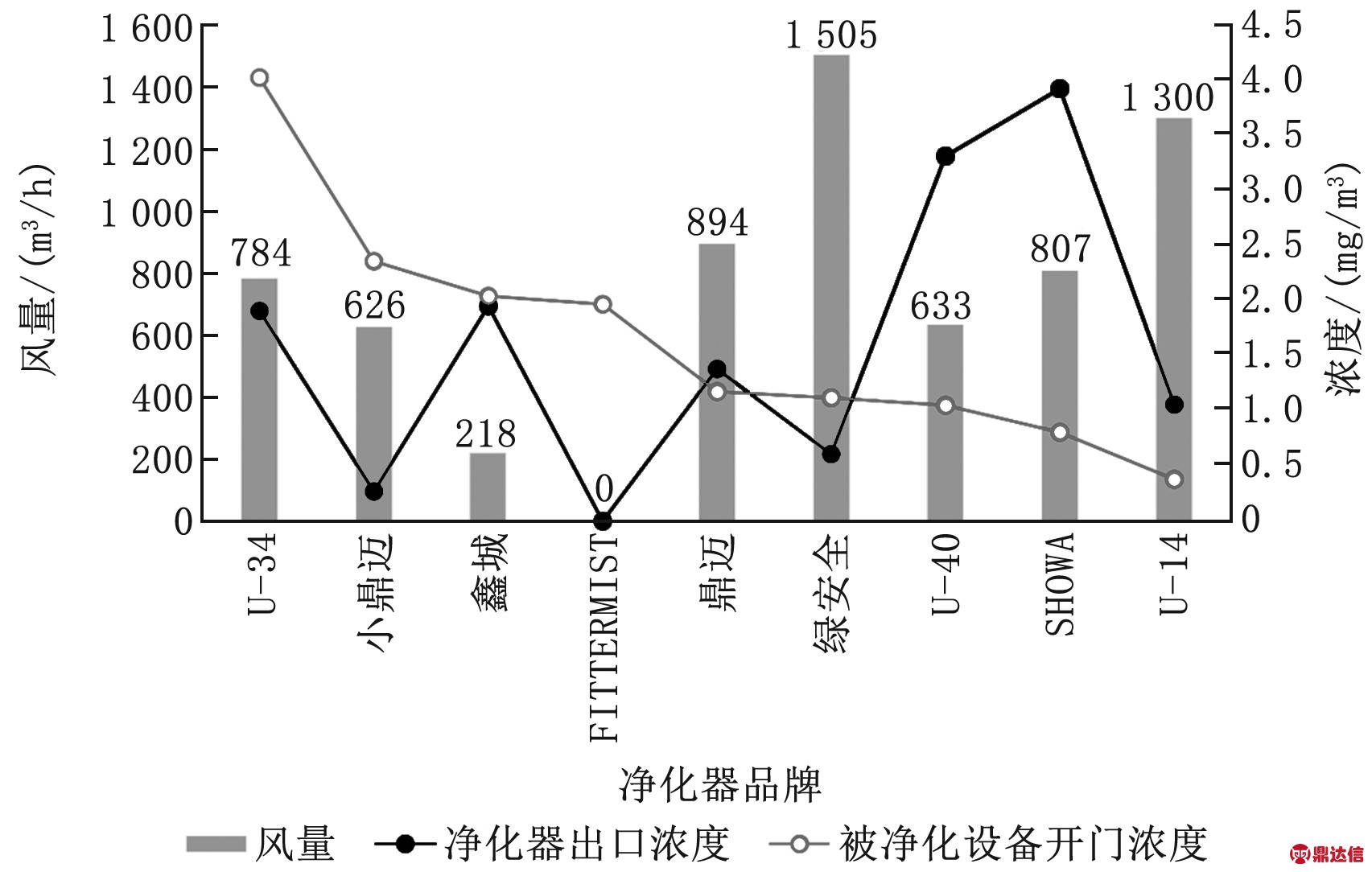
图8 不同净化器的效果评估
为了评估净化器的净化效果,对净化器的出口浓度和被净化设备开门浓度进行了测量,结果如图8所示。净化器的净化效果主要采用3个指标进行评估:一是风量,二是出口浓度,三是被净化设备开门浓度。风量大、出口浓度高或者风量小、出口浓度低均说明净化器的净化效果不好。从图8可以看出:品牌为绿安全的净化器风量大、出口浓度低、被净化设备开门浓度低,因此净化效果最好;U-14和鼎迈的风量较大、出口浓度较低、被净化设备出口浓度较低,故净化效果较好;小鼎迈、U-40和SHOWA的净化器净化效果次之;其他净化器净化效果较差。整体来看,虽然部分净化器净化效果较好,但从数量和净化器维护两方面分析,该车间目前装配的净化器未能对车间整体完成有效净化,车间内污染仍然很严重。
4 结论
1) 车削、磨削、高频淬火、低压清洗和铣削等工艺产生的油雾浓度较高,且数控车床、数控外圆磨床、高频淬火机、低压清洗机和数控加工中心设备数量较多,共占调查设备总数的74.4%,是该工厂的主要污染设备。
2) 开发的基于ZigBee的无线传感器网络监测系统能够准确、连续地监测车间油雾浓度,并且能够实现数据的实时可视化。
3) 对车间3个典型位置进行油雾动态监测的结果显示:设备是否生产是影响车间油雾浓度最主要的因素,设备停工则污染源消失,车间油雾浓度迅速衰减,设备运行则污染源出现,车间油雾浓度开始升高;车间内油雾浓度分布不均,净化器所在区域油雾浓度较低,低油雾散发的设备附近油雾浓度较低;在9 h的生产时间内,3个测点区域的油雾浓度值超出NIOSH推荐的油雾接触限值0.5 mg/m3的时间分别为7.35,5.31,1.21 h。
4) 对车间现有净化器进行了效果评估,发现在多种净化设备中,静电净化设备净化效果最好,在保持较低的出口油雾浓度前提下能维持较高的排风量。