摘要:基于隔水管挠性接头的使用工况和功能特点,分析了隔水管挠性接头的试验内容与试验原理,设计了隔水管挠性接头试验装置。该试验装置包括3种类型的试验工装,分别用于水压试验、弯曲循环试验和载荷试验。重点介绍了弯曲循环试验工装和载荷试验工装的结构原理与使用方法。该试验装置可用于模拟隔水管挠性接头在海洋的工况并试验与研究,试验数据与结果可为现场使用提供参考依据。
关键词:隔水管;挠性接头;试验装置;设计
挠性接头是保障海洋石油钻井隔水管系统正常工作的重要设备之一,主要安装在隔水管底部,允许在隔水管和BOP组之间存在角度偏差,从而减少隔水管上的弯曲力矩,如图1。我国在该设备的研究和开发方面起步较晚,且远落后于发达国家。为了推动海洋石油装备的国产化,宝鸡石油机械有限责任公司目前已经设计完成了一种FJ-E25S型隔水管挠性接头(以下简称挠性接头),该挠性接头内部设有挠性元件,可适应任意方向的偏摆,具有承载能力强,结构简单紧凑,抗弯曲能力强等特点[1-5]。
笔者针对该挠性接头实际工况和结构特点,设计了简单、有效、经济的试验装置,用于挠性接头的试验与研究,确保其在深水海洋环境下的安全性和可靠性。
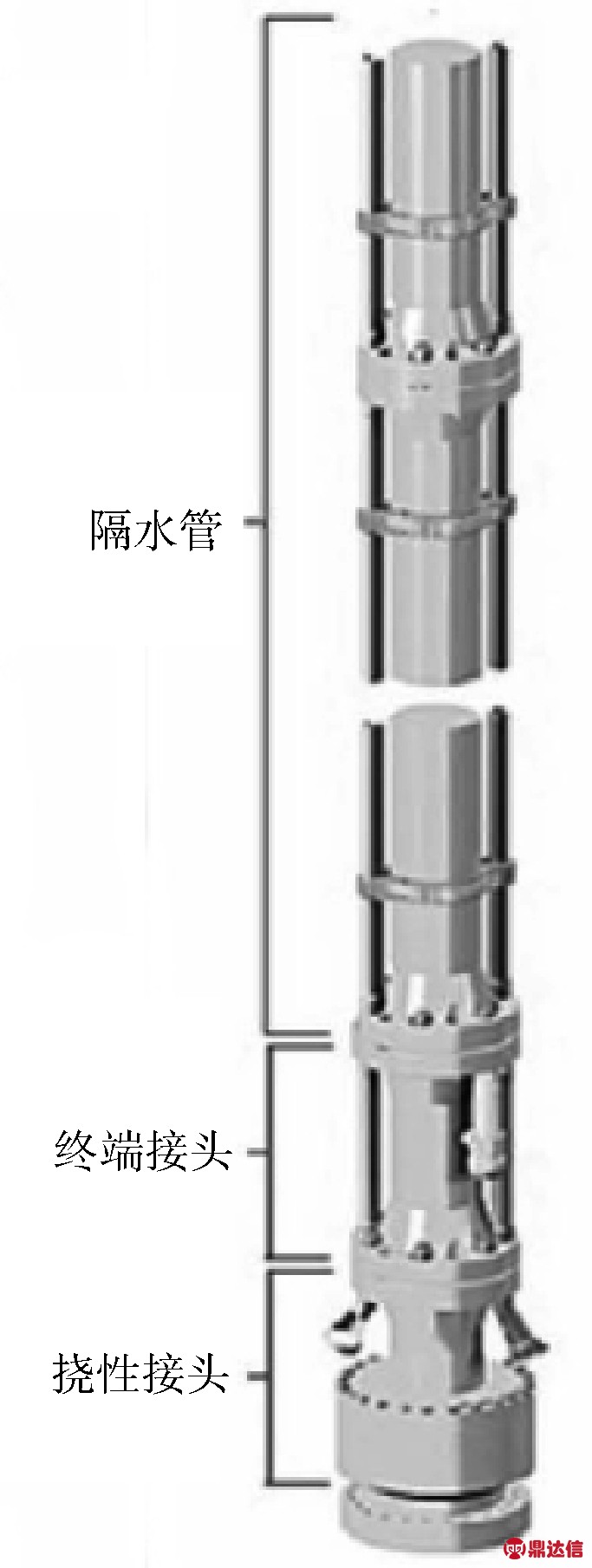
图1 挠性接头工作位置
1 试验要求
由于挠性接头是重要钻井通道,工作在海底,在波浪作用下,除发生周期性的前后左右摇摆外,还产生随波浪上下升沉运动。这些运动将影响隔水管系统稳定性及井口装置安全性,甚至带来灾难性后果[6-11]。因此,挠性接头应进行静水压试验、弯曲循环试验和在弯曲工况下的载荷试验等。该挠性接头适用于E级隔水管系统,工作水深1 500 m,工作压力17.24 MPa,工作载荷为4 448 kN;许用挠性角度为±10°;挠性接头上下端均采用标准法兰连接。
2 试验原理分析
根据上述的试验要求,为了达到预期的试验目的,挠性接头试验装置至少应具备3种类型的试验工装,分别满足挠性接头的水压试验、弯曲循环试验和载荷试验。
2.1 水压试验
水压试验包括静水压强度试验和静水压密封试验,试验压力分别25.86 MPa和17.24 MPa。由于挠性接头上下法兰均按照标准和规范进行设计,因此试验工装也参照标准设计即可,本文将不再阐述。
2.2 弯曲循环试验
弯曲循环试验用于模拟隔水管系统在海洋工况下受到洋流、波浪等作用,发生前后左右摇摆,造成挠性接头中挠性连接件产生循环弯曲偏摆的现象。因此,相关标准规定,在1个挠曲平面内,在最大挠性角的±50%处,即±5°处,弯曲循环试验次数不得低于100 000次,如图2。
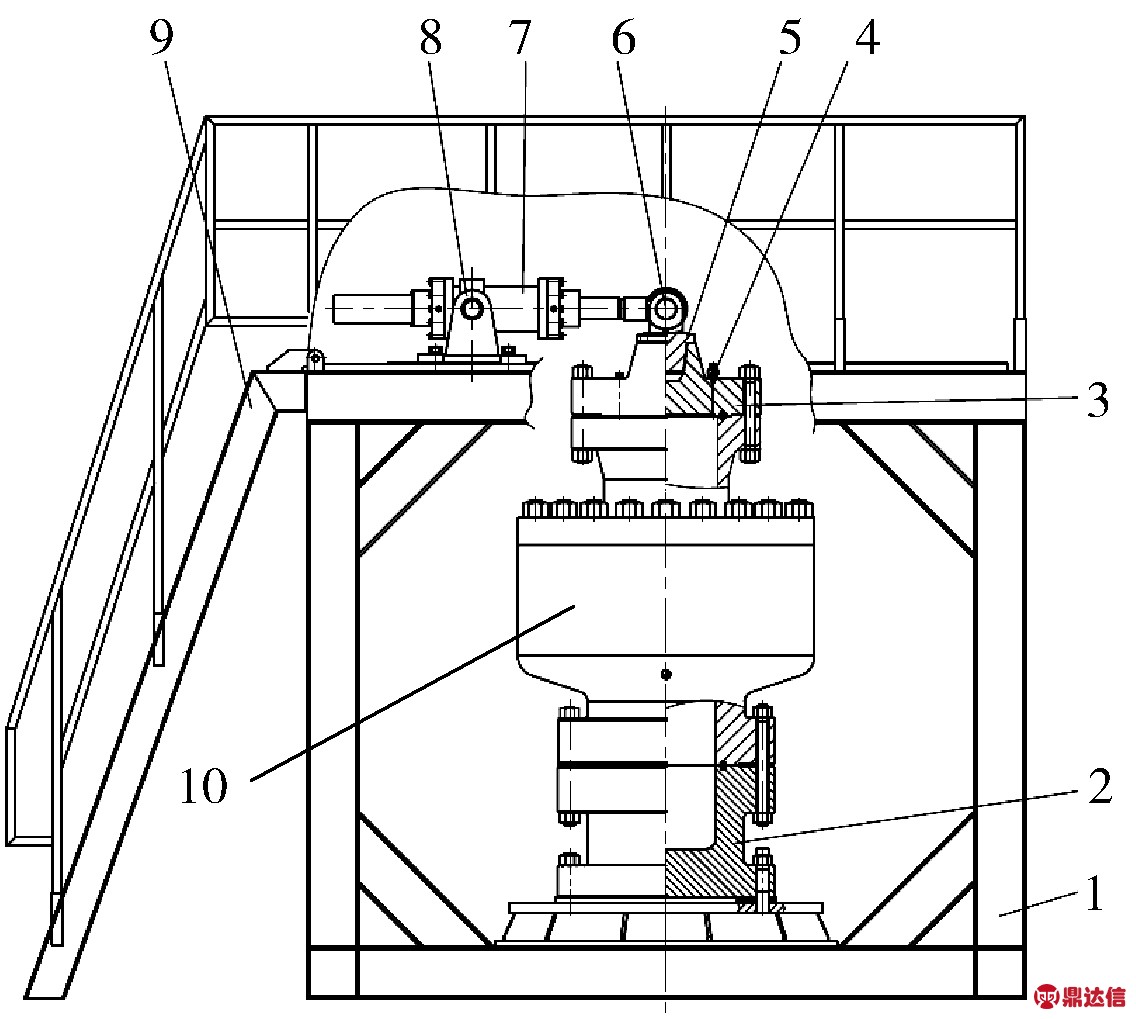
图2 弯曲循环试验原理
2.3 载荷试验
载荷试验用于检测挠性接头承受综合性外力的性能,是模拟隔水管系统在海洋钻井工况下,受到拉伸载荷并伴随弯曲偏摆的试验与研究。由于海洋工况的不确定性,会造成隔水管系统发生不同方向和不同角度的偏摆。试验时,挠性连接件可能会沿圆周任意方向偏摆,偏摆角度为0~10°,试验最大载荷为2倍工装载荷,即8 896 kN。如图3。
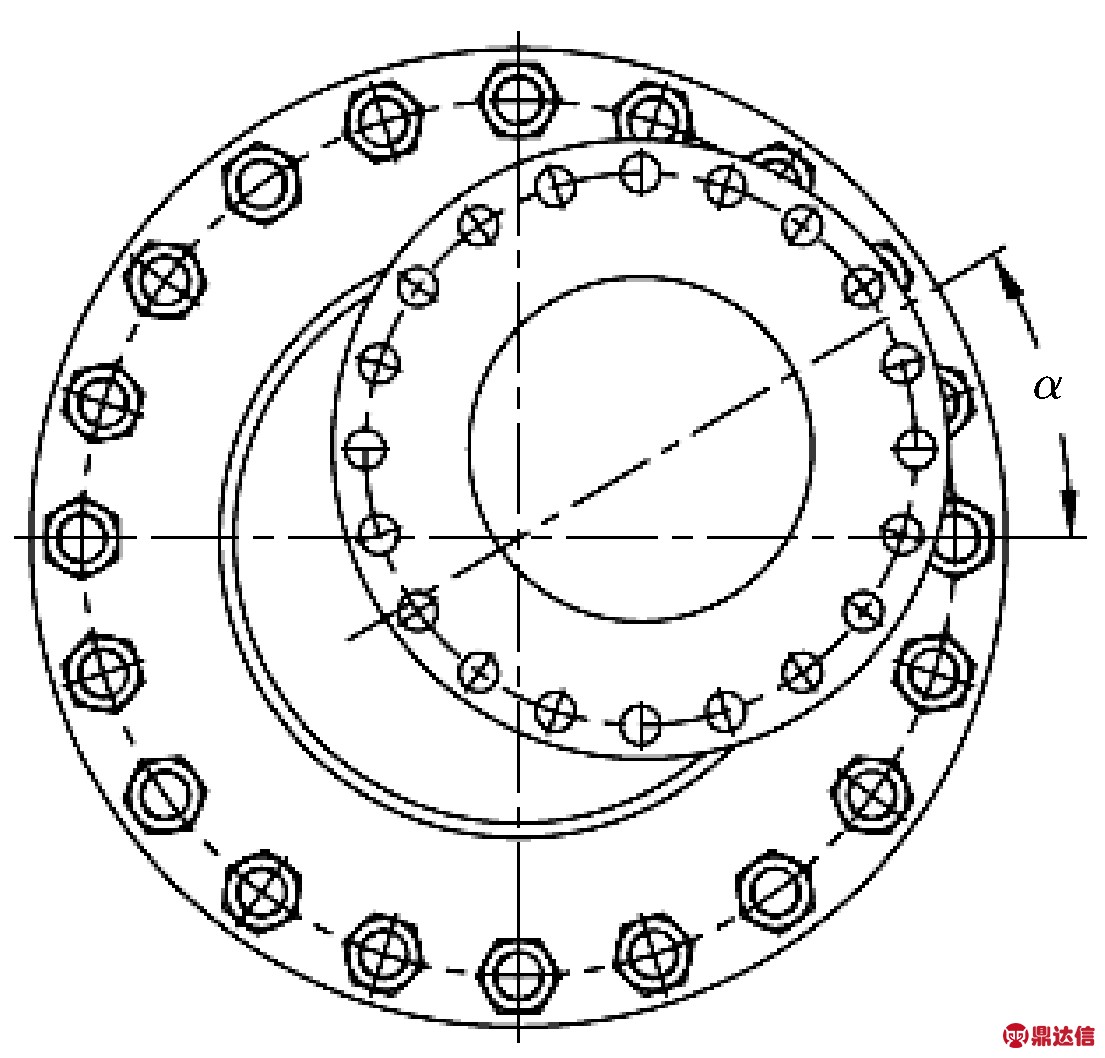
a 挠性连接件偏摆方向
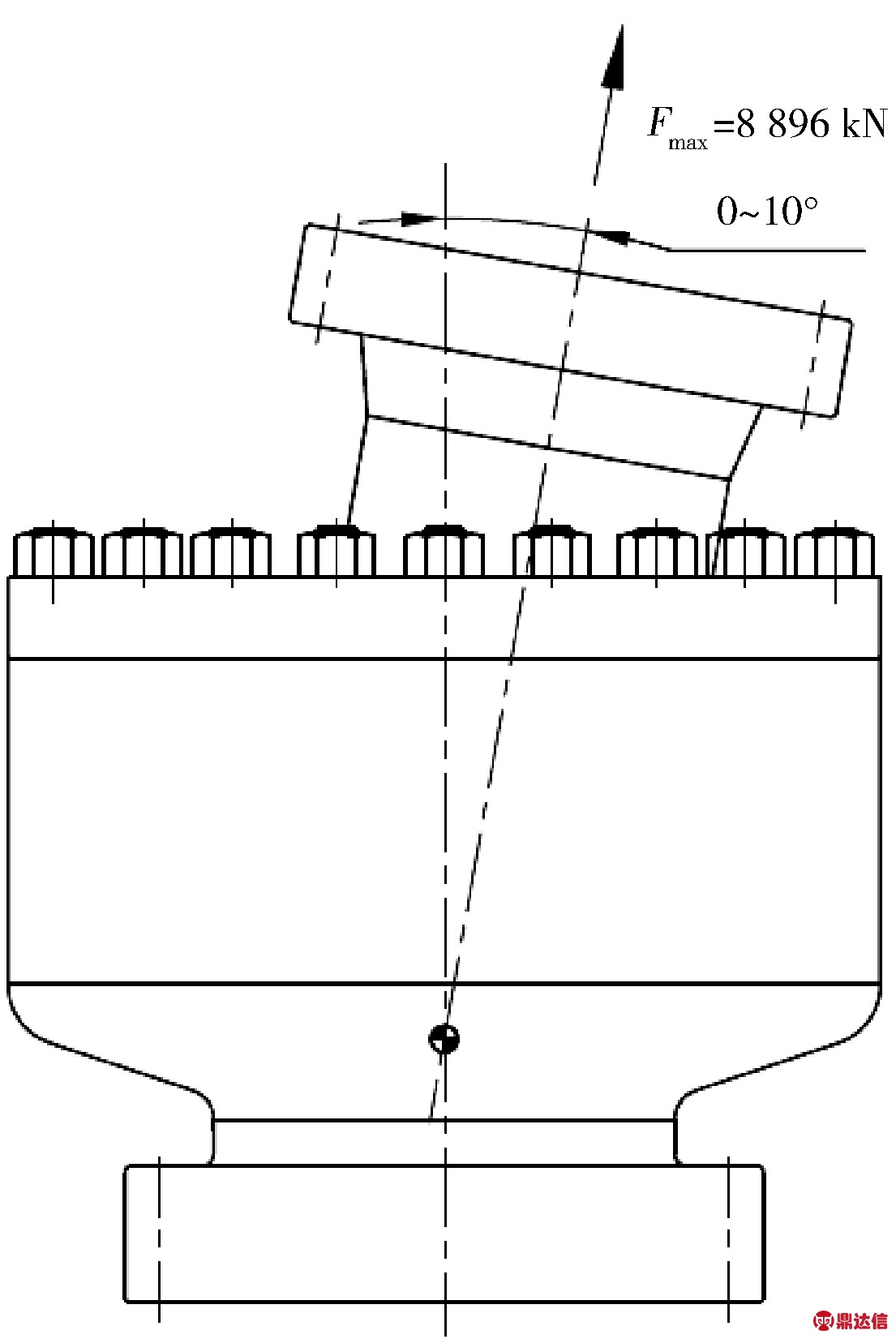
b 挠性连接件偏摆角度及载荷
图3 载荷试验原理
3 弯曲循环试验工装设计
弯曲循环试验工装包括安装连接机构、水压试验机构和弯曲加载机构。如图4。
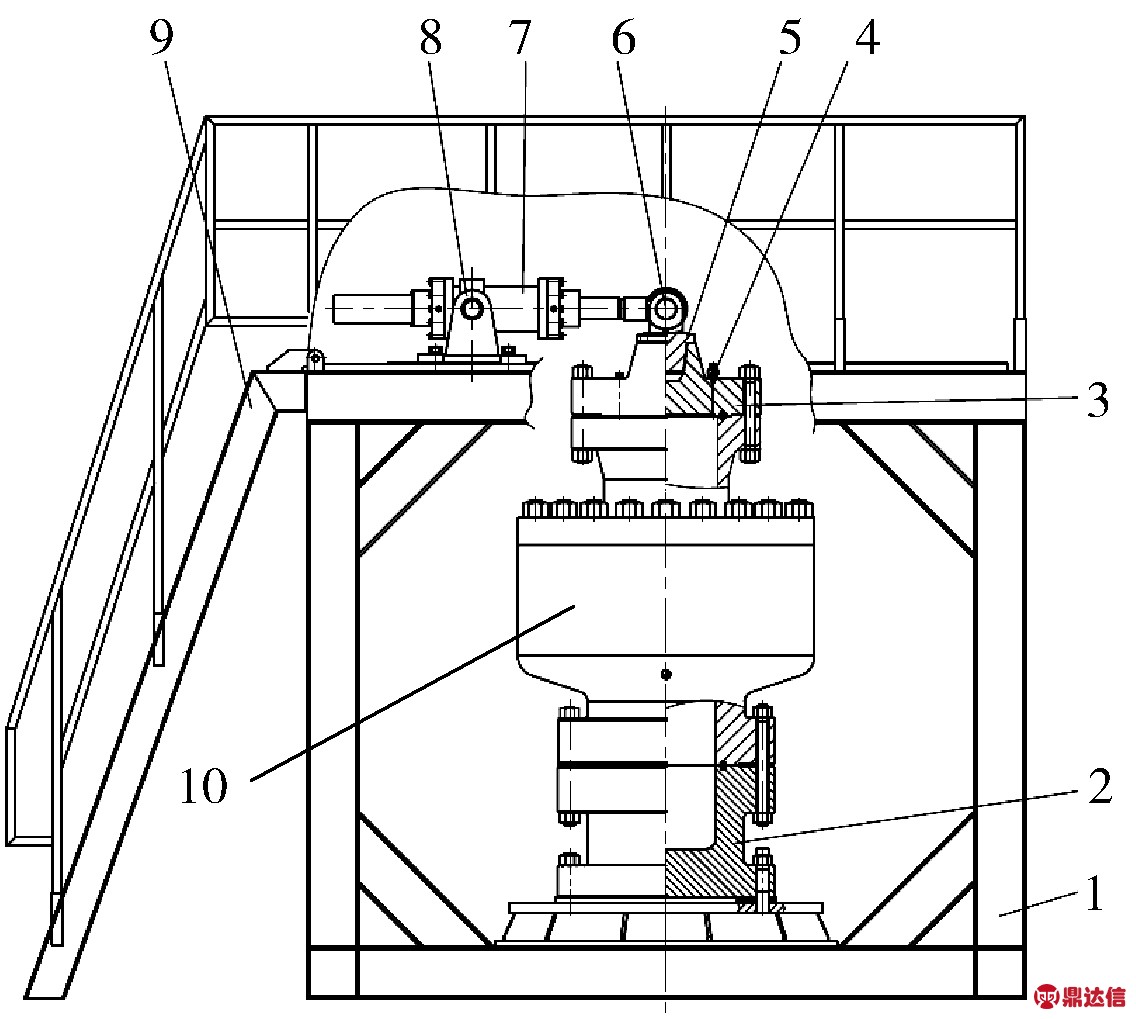
1—试验台架;2—下法兰;3—上法兰;4—水压接头;5—弯矩销;6—连接销轴;7—液压缸及液控系统;8—铰支座;9—斜梯;10—挠性接头。
图4 弯曲循环试验工装
3.1 安装连接机构
安装连接机构包括试验台架和斜梯,主要用于挠性接头、油缸等的安装、固定与连接。
3.2 水压加载机构
水压加载机构包括下法兰、上法兰和水压接头,其目的是做为一种技术手段来观察和检测挠性接头因循环弯曲载荷而造成各零部件的磨损、破坏或疲劳等现象。具体操作是:试验时,往挠性接头内腔泵入工作液,达到要求的试验内压时,开启液压缸带动挠性连接件做弯曲循环运动。如果挠性接头发生磨损、破坏或疲劳等现象,会直接造成压力下降或压力泄漏,实现实时检测挠性接头的工作性能的目的;也可快速、直接找出试验失败的原因,为设计改进和提高提供依据。
另外,该水压试验机构的上、下法兰还兼顾其他试验的结构与功能,可以直接用于挠性接头的水压试验和载荷试验,避免重复设计、制造。如图5~6所示。

图5 上法兰
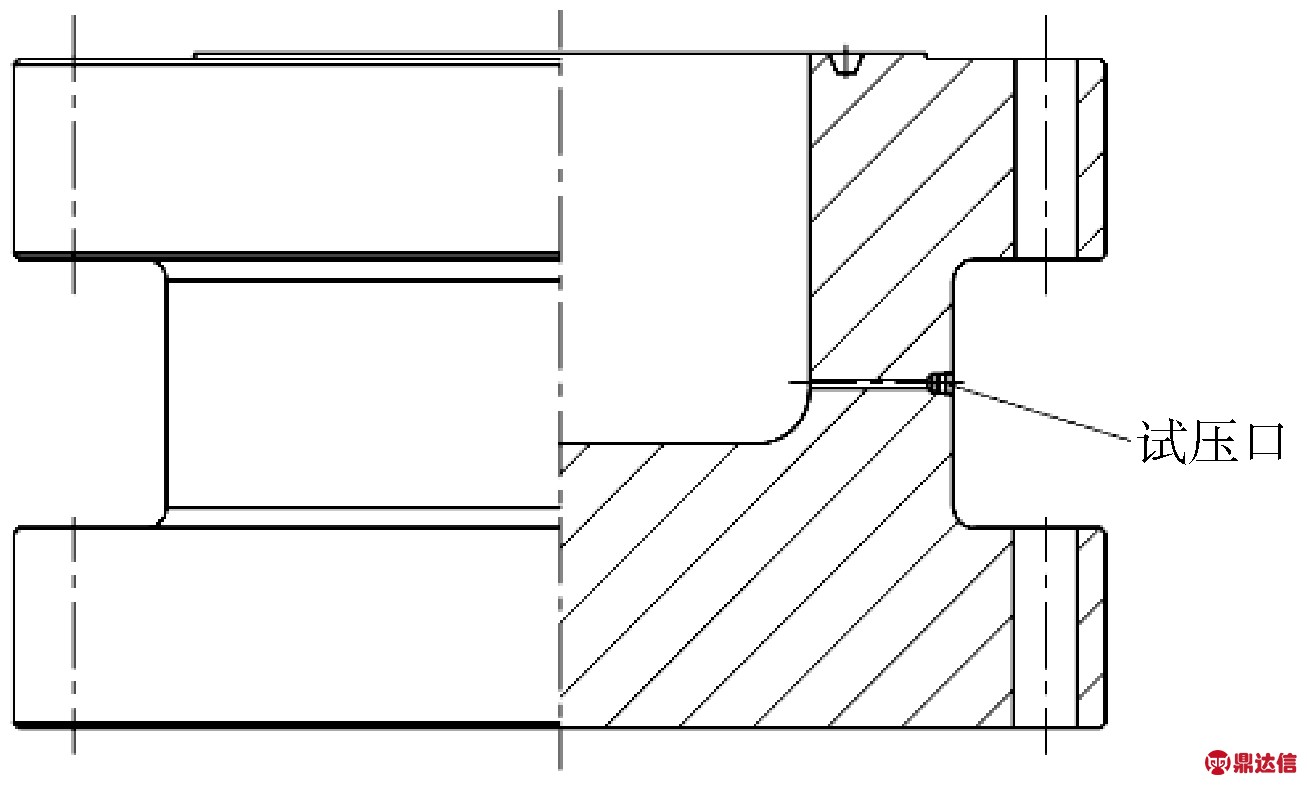
图6 下法兰
3.3 弯曲加载机构
弯曲加载机构包括弯矩销、连接销轴、液压缸液控系统和铰支座,主要功能是为挠性接头施加循环弯曲载荷。
液压缸为双出杆结构,液压缸额定压力31.5 MPa、油缸内径160 mm、活塞直径100 mm、行程380 mm,液压缸内腔两端设有缓冲结构,外部中段设有旋转轴,活塞端部为球铰耳环,如图7。

图7 液压缸结构
液压系统主回路设计除了要保证挠性连接件在液压缸的带动下做循环运动外,还要统计计算挠性连接件的循环次数;另外,液压主回路中还设有蓄能器,蓄能器增加了液压系统油压的稳定性,也削弱了往复运动带来的液压振动。图8为液压系统主回路原理图。
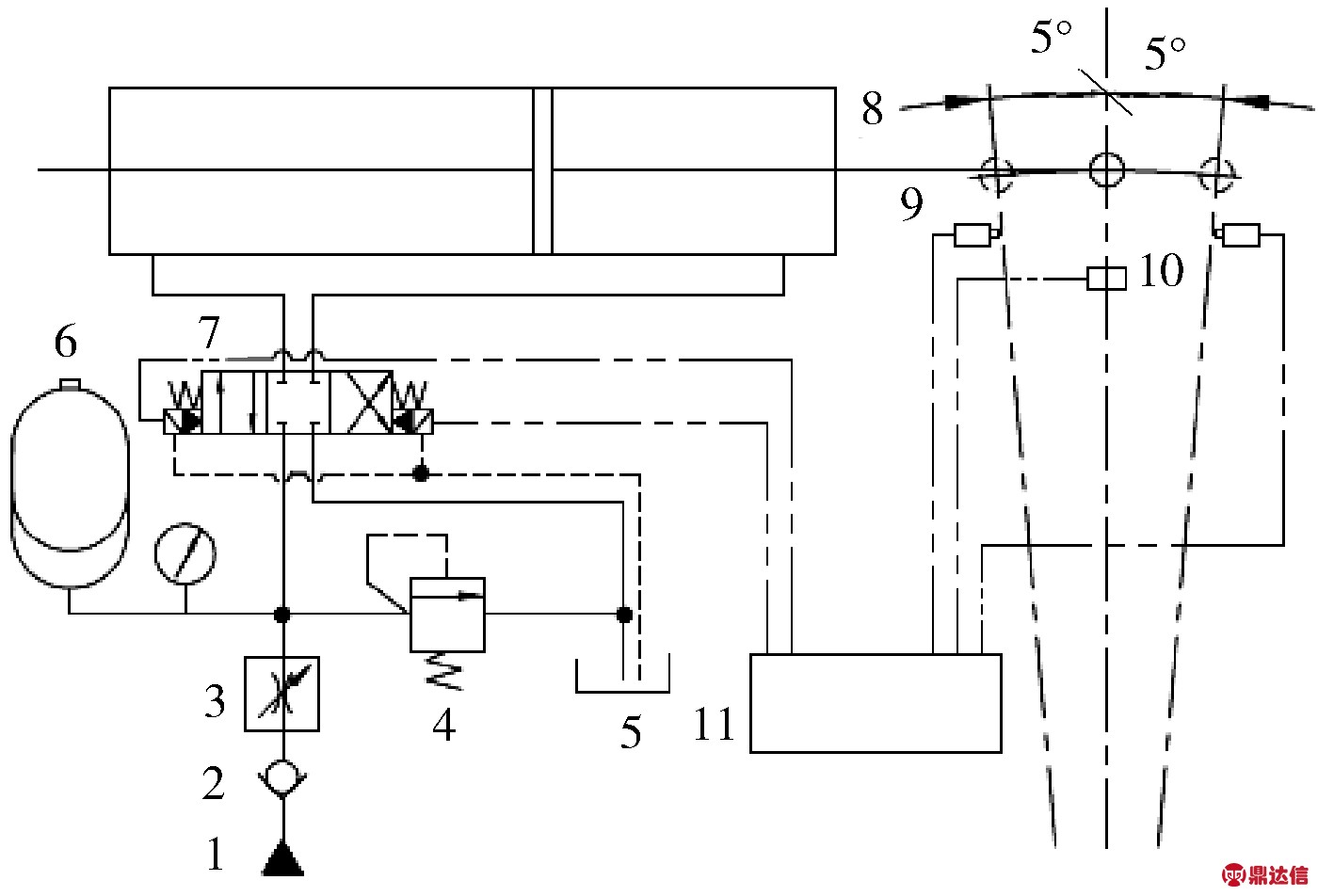
1—液压油源;2—单向阀;3—节流阀;4—溢流阀;5—油箱;6—蓄能器;7—电液换向阀;8—液压缸;9—限位开关;10—计数器;11—操作控制台。
图8 液压系统主回路原理
4 载荷试验工装设计
载荷试验除了尽可能模拟实际工况外,同时还应结合现有的工艺试验装备条件,因此,本试验设定了3种试验状态,即挠性连接件偏摆0°、5°和10°的载荷试验。
4.1 偏摆0°的载荷试验工装
偏摆0°的载荷试验与常规载荷试验并无实质差别,按通常的试验方法进行安装、连接、加载即可完成试验。如图9。
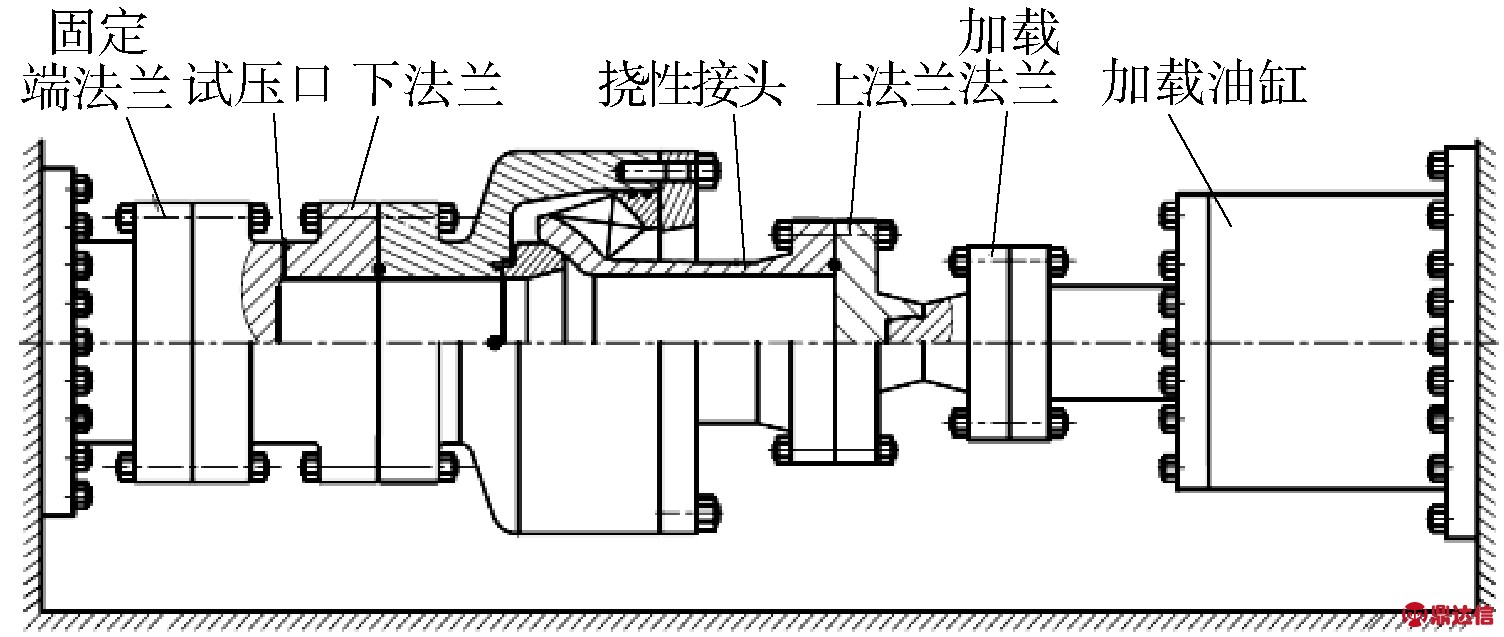
图9 偏摆0°载荷试验工装
4.2 偏摆5°和10°的载荷试验工装
由于现有的工艺试验装备其加载端与固定端在同一中心线,无法进行倾斜加载,因此须对其结构进行更改,更改内容包括:更换固定端法兰和增加偏摆油缸。如图10所示。
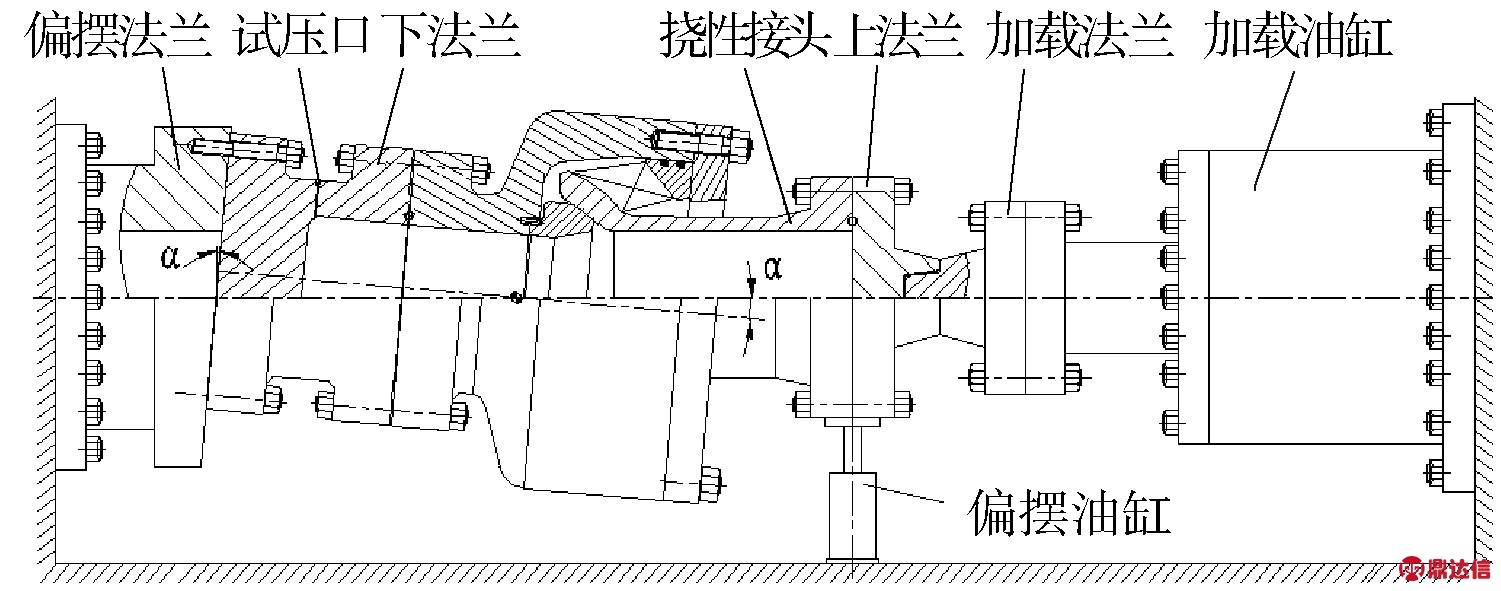
图10 偏摆5°或10°的载荷试验工装
重新设计了固定端法兰,其目的是模拟挠性接头在不同偏摆角度下试验。固定端法兰包括5°偏摆法兰和10°偏摆法兰,并且将连接方式更改为沉孔螺栓结构,螺纹沉孔垂直于偏摆面。如图11所示。
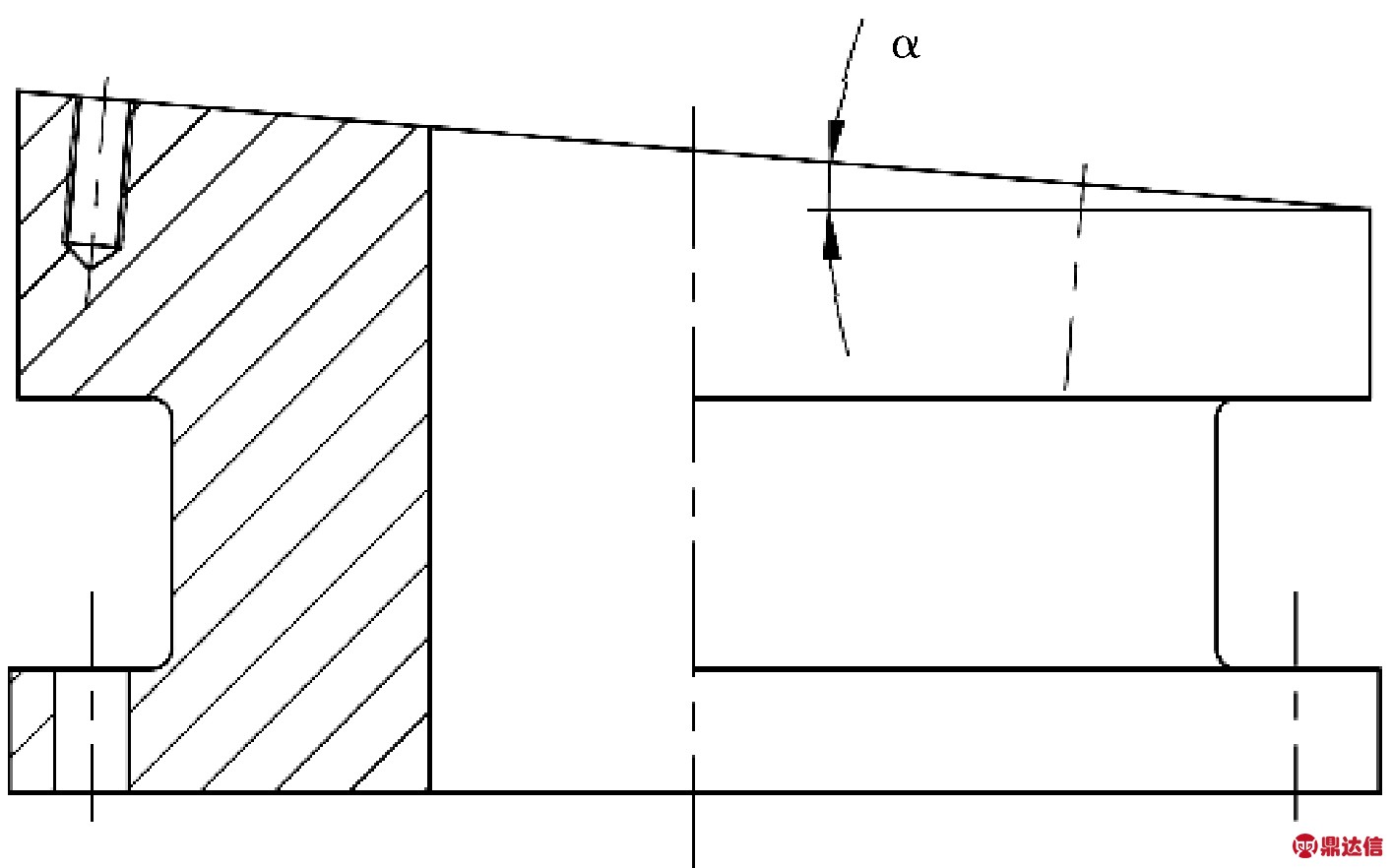
图11 偏摆法兰
4.3 试验操作步骤
以偏摆10°的载荷试验为例进行说明。
第1步,将挠性接头上端与上法兰、加载法兰连接,下端与下法兰连接,组成载荷试验组件。
第2步,将载荷试验组件下端与10°偏摆法兰连接;此时启动偏摆油缸,对挠性连接件施加弯曲载荷,使其偏摆到水平位置,即偏摆10°;然后载荷试验组件再与加载油缸连接,使其到达试验状态。
第3步,启动加载油缸,逐级加载至试验载荷;此时,再注入内压,检测挠性接头是否异常。试验完成后,卸载、泄压。
第4步,将载荷试验组件分别与10°偏摆法兰和加载油缸脱离。
第5步,将载荷试验组件沿周向旋转一个螺栓孔的角度;然后再按照第2步~第5步的次序进行试验,直到完成整个圆周方向的载荷试验。
按上述试验方法,即可完成偏摆5°或其他偏摆状态小的载荷试验;该试验工装和试验方法可部分实现挠性接头在不同方向和不同角度的偏摆载荷试验。
5 结论
1) 挠性接头试验装置可实现挠性接头的水压试验、弯曲循环试验和载荷试验。
2) 弯曲循环试验工装中液压缸采用了双出杆结构和机械缓冲结构,保证了试验的匀速和平稳;该工装中液压控制系统同样具备稳压和减震功能,同时还兼顾试验循环次数的统计;该试验进行时,增加了水压检测手段,可实时检测挠性接头的试验状况。
3) 载荷试验工装利用了现有的工艺试验装备进行改进与提升,同时增加了偏摆法兰和偏摆油缸,可部分实现挠性接头在不同偏摆方向和不同偏摆角度下的载荷试验;试验数据和结果可为现场使用提供参考依据。
4) 上、下法兰通用性强,同时满足水压试验、弯曲循环试验和载荷试验的要求和应用,避免重复设计、制造。
5) 挠性接头试验装置设计简单、可靠,可用于隔水管挠性接头的试验与研究。