摘 要:根据管接头零件的结构特点,并结合数控车床上分度卡盘的应用情况,研发出可实现无偏心管接头和具有偏心结构管接头零件的高效装夹、自动转位加工技术及相应转位夹具。其转位夹具具有快速设计制造、通用性强、结构简单及使用方便等特点;通过数控自动转位高效加工彻底解决了管接头零件因种类多、数量大,模锻件不易装夹定位等造成的生产加工瓶颈问题,降低了操作者的劳动强度,提高了零件加工质量,为企业柔性生产线的构造打下了良好的基础。
关键词:管接头;车床夹具;旋转定位;夹具设计
管接头是航空液压、燃油、环控等多个系统的主要管路连接件,在液压、气压、油路等管路中,起到改变管路方向,传递液压油、燃油等介质,对液压燃油、空气等介质起到分流、合流、限流等作用。因工作区域广泛,导致其结构形式多种多样,如图1所示,按管嘴数量可分为两通、三通、四通和五通管接头,按结构形式可分为无偏心管接头、偏心结构管接头。
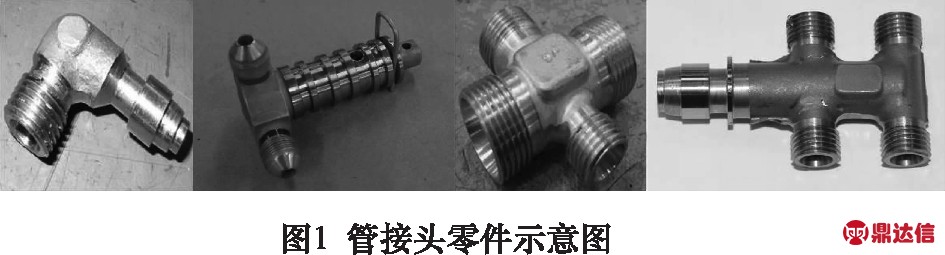
管接头零件因结构特点多为锻造毛坯加工,导致其定位基准差,且加工部位不在同一方向导致装夹次数多。传统的加工方法为普通车床加组合夹具或简易夹具的形式,如图2所示,每加工一侧管嘴结构,均需要一套组合夹具[1],因夹具种类多、体积大导致装卸不方便,且普通车床转速低导致零件表面不够光滑。后续已通过改变卡爪结构,优化为数控车床加自制简易夹具的形式,如图3所示,零件加工表面质量问题得以大幅改善。但随着飞机产量的大幅提升,生产周期的缩短,以数控车床加自制简易夹具逐次加工单一管嘴的方法已不能满足当前的生产需要,急需一种更为高效的加工技术来解决因装夹次数多导致加工效率低、零件互换性差的问题。本文基于分度卡盘的应用对管接头零件在数控车床上的快速装夹、自动转位夹具进行研究与设计,实现了管接头零件在数控车床上的高效高质量加工。
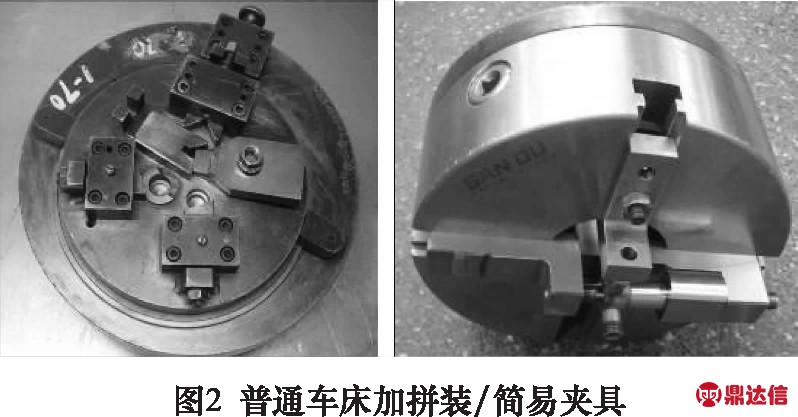
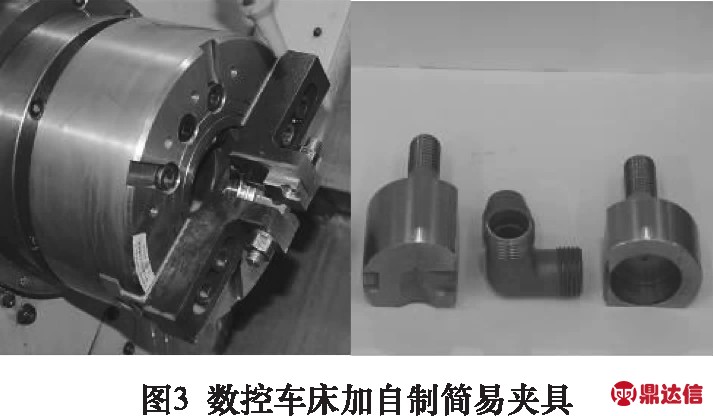
1 管接头自动转位加工技术分析
通过图1可以看出,管接头零件的加工部位基本为管嘴及内孔,其外部中心处扳手台及相邻管径为非加工区域,可用于零件定位装夹[2];采用二爪或四爪卡盘,通过夹具对非加工管径进行装夹定位加工,加工完一侧管嘴后,改变夹具在卡盘上的装夹角度,实现其余管嘴的加工,夹具装夹及零件加工次数仍取决于管嘴的数量,零件整体加工效率不高。
分度卡盘是一种改变零件装夹角度很实用的结构,通过对零件加工步骤及分度卡盘的分析,设计出了一套数控车床自转位加工的机构,如图4所示;将分度卡盘通过不锈钢导油管、内六角螺钉等与机床主轴连接,卡盘压爪通过自动转位夹具固定零件,机床主轴中心线与管嘴一轴线重合[3],夹具旋转轴线即为管嘴轴线所在平面上各轴线交点的垂线,如图5所示。通过集成改装,卡盘压爪借助尾座的M指令来实现转位功能,例如转位90°的指令为:
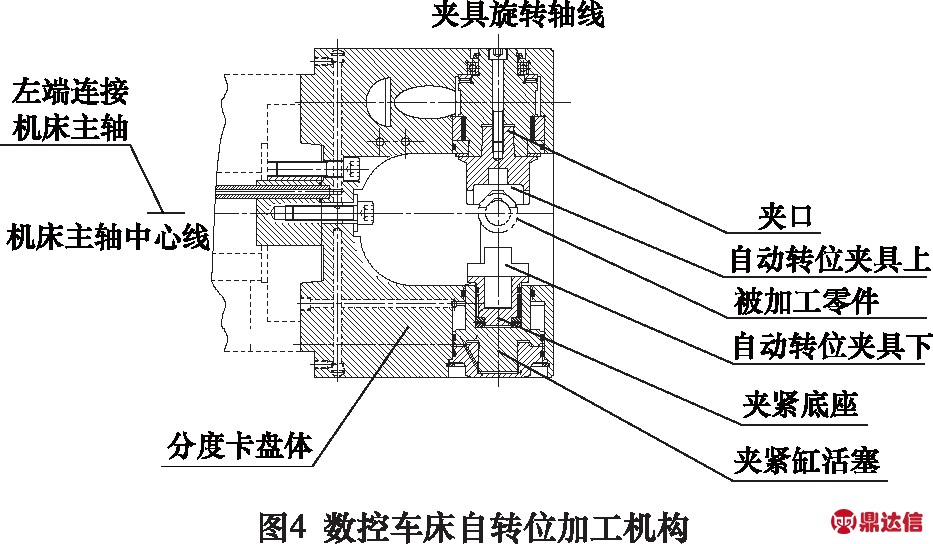
G0 Z___(退刀)
G0 X___(退刀)
M85(夹爪转位45°,机床PLC设定延时2 s后再转45°)
G0 Z___ X___(进刀)

加工时,将被加工零件放置于自动转位夹具中间,自动转位夹具在机床液压系统控制下自动向机床主轴中心线方向收紧,实现自动夹紧、快速定位功能。完成一侧管嘴的加工内容后,夹紧活塞在机床液压系统控制下,沿着夹具旋转轴线转动,驱动夹紧底座、夹口及自动转位夹具旋转,被加工零件随着自动转位夹具一同旋转,实现被加工零件自动转位功能,随即可进行另一侧管嘴的加工。自动转位夹具旋转过程中,夹具与零件之间的位置关系未发生变化,因此无需再次对刀、测量等操作,重复定位精度由机床底座自身决定,加工质量稳定。通过此技术即可实现管接头零件一次装夹,自动转位加工多侧管嘴,大幅提高零件加工效率,减小因多次装夹误差导致的管嘴轴线偏差。
2 自动转位夹具设计应用
2.1 无偏心管接头自动转位夹具
为实现管接头零件在数控车床上的自动转位加工,转位夹具必须具有自动定位、夹紧及转位功能[4]。针对无偏心结构的管接头零件,以如图6所示的异型管接头为例,进行零件工艺流程分析及转位夹具设计。
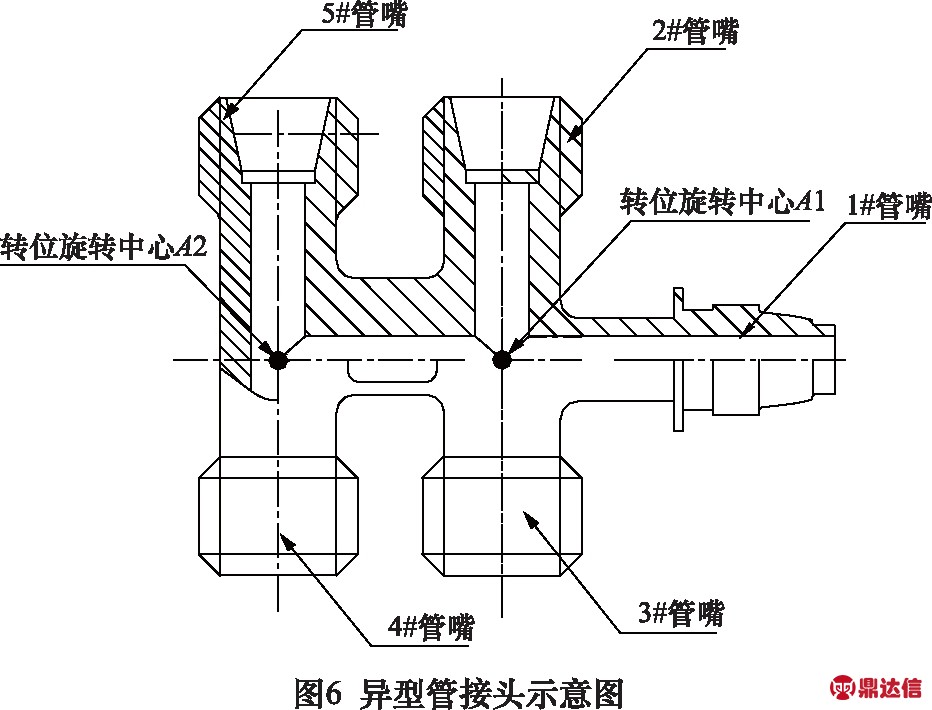
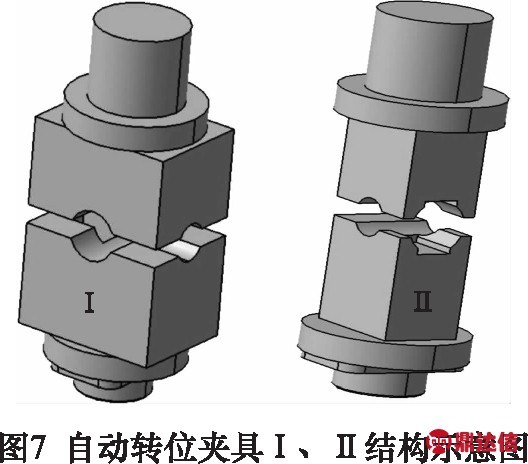
该零件共有1#~5#五个管嘴,按传统加工方式需要进行5次装夹定位加工;通过管接头自动转位加工技术分析,我们得知通过寻找零件的转位旋转中心A1、A2,并设计对应的自动转位夹具Ⅰ、Ⅱ,如图7所示,使零件装夹在自动转位夹具上时,夹具旋转轴线穿过零件转位旋转中心,即可实现一次装夹,相应管嘴转位连续加工[5]。
通过总结自动转位夹具设计制造、使用的经验,形成了一套设计该夹具的通用表格图册。其中L1、L2为夹具外形尺寸,L3、L4为扳手台避让孔尺寸,L3、L4一般比扳手扁对应尺寸大0.3~0.6 mm,L1、L2与L3、L4之间的差值为夹具装夹接触面宽度,以单边装夹接触宽度3~5 mm最优;D1、D2、D3及D4分别为对应接触管径的尺寸,其公差在(+0.2/+0.1) mm,既能保证重复装夹定位的一致性,又能保证零件压紧时自动定心;δ为两夹具夹紧时的工作间隙,但最小应大于2 mm,以便于夹紧[6]。根据实际零件的管嘴数量及角度,自行调整夹具开口的数量与方向,即可实现自动转位夹具的快速设计。夹具材料方面常采用45#钢,热处理为淬火+回火,表面处理为化学氧化。
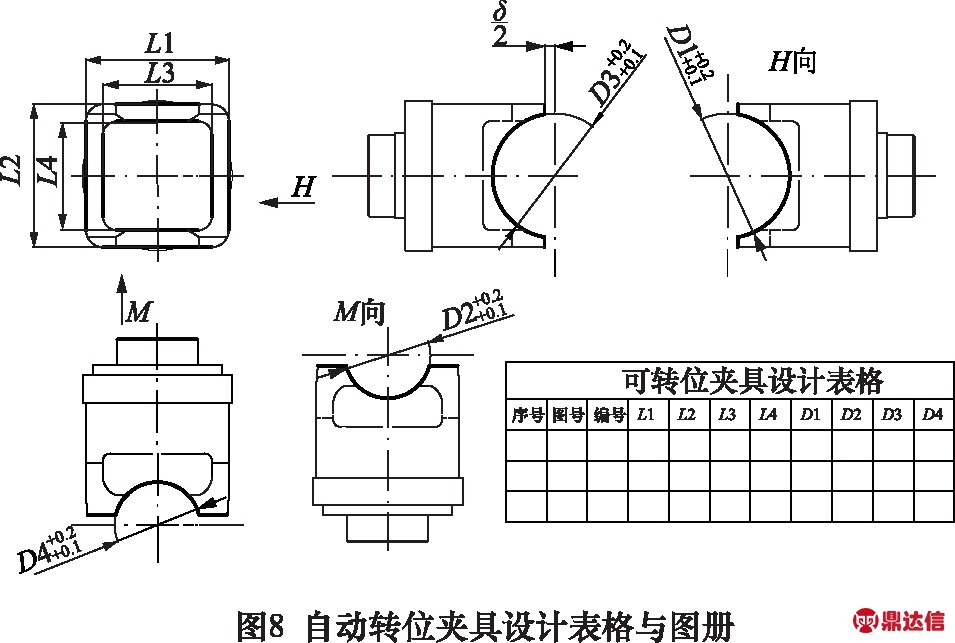
上述异型管接头零件优化后的数控加工方式如表1所示,两次装夹即可实现5个管嘴的加工,累计完成一个零件的加工只需近25 min,大幅减少了操作人员更换定位夹具、对刀的工作量,相比传统加工模式,总体加工时间缩短了3倍;5次装夹定位变成2次,有效解决了因锻造毛坯不易装夹,多次装夹导致管嘴轴线存在偏差、零件互换性差的问题。
2.2 偏心结构管接头自动转位夹具
具有偏心结构的典型零件为转动接头,如图9所示;转动接头是航空飞机液压系统中重要的管路连接件,是实现飞机起落架收放功能的重要部件之一,其零件主体轴线与一管嘴轴线存在偏心距S,且不同部位的该类零件偏心距存在一定差异,针对此类零件的自动转位夹具设计,重点在夹具偏心距的调节。
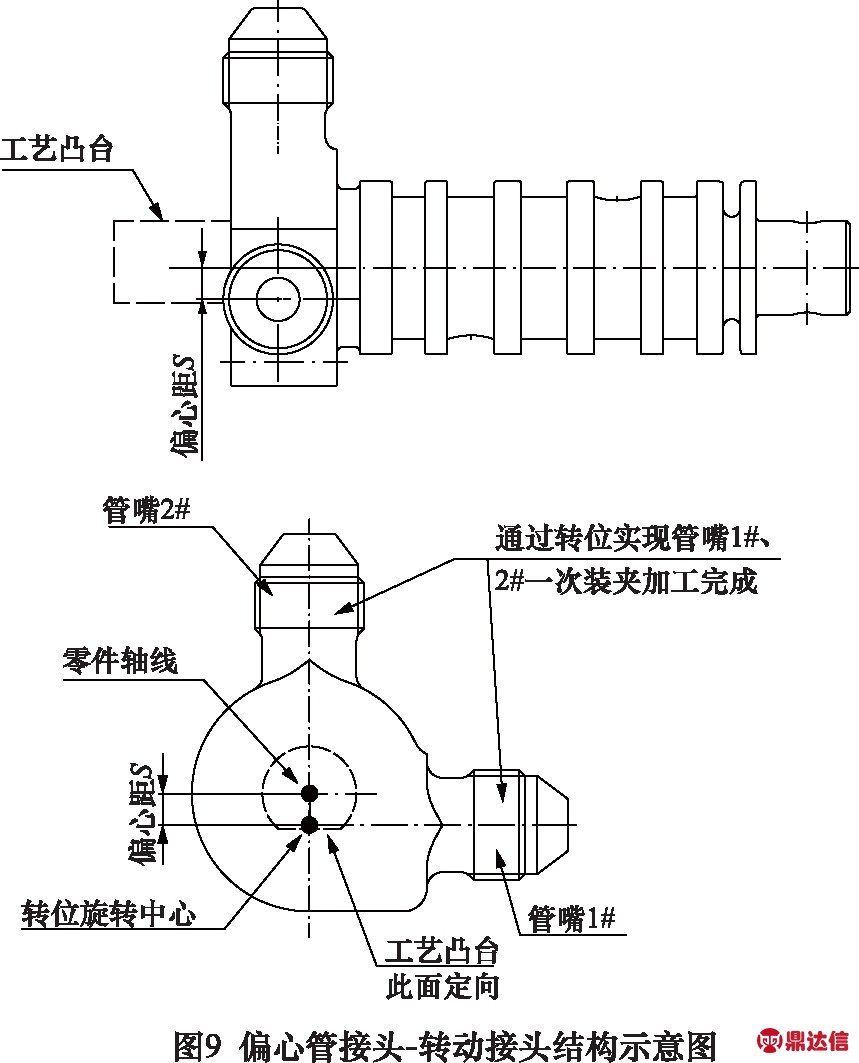
通过设计一套偏心距可调的转位夹具,如图10所示,包括基体、定向螺栓、T型滑块、调节底座、固定螺钉和定位销;转动接头零件通过此夹具在分度卡盘上的装夹方式如图11所示;零件工艺凸台上的定位面与管嘴一轴线平行,定向螺栓利用此定位面,实现零件在夹具上的快速定向,装夹后管嘴轴线与主轴的中心线满足重合度的要求[7]。夹具与加工零件具有相同的偏心距S,夹具转位旋转轴线通过两管嘴轴线交点,在装夹加工完管嘴1#后,夹具自动转位90°,直接进行管嘴2#的加工。
针对具有不同偏心距的零件,根据调节底座与基体上的刻度线,通过T型滑槽结构滑动对夹具偏心距进行调节;基体和调节底座上均开有4个常用偏心距快速定位孔,通过插入定位销,对调节底座进行快速定位,拧紧固定螺钉后,拔出定位销,即可实现常用偏心距的快速调节。
此偏心距可调转位夹具的设计应用,实现了单一偏心零件多管嘴的一次装夹定位,自动转位加工多个管嘴,同时实现了多个偏心距不同的转动接头零件共用一套夹具;减少夹具数量,降低夹具订制费用的同时,提高了管接头零件的加工效率,减少了零件装夹次数,避免了反复装夹公差累计导致零件超差。
表1 管接头自动转位加工步骤
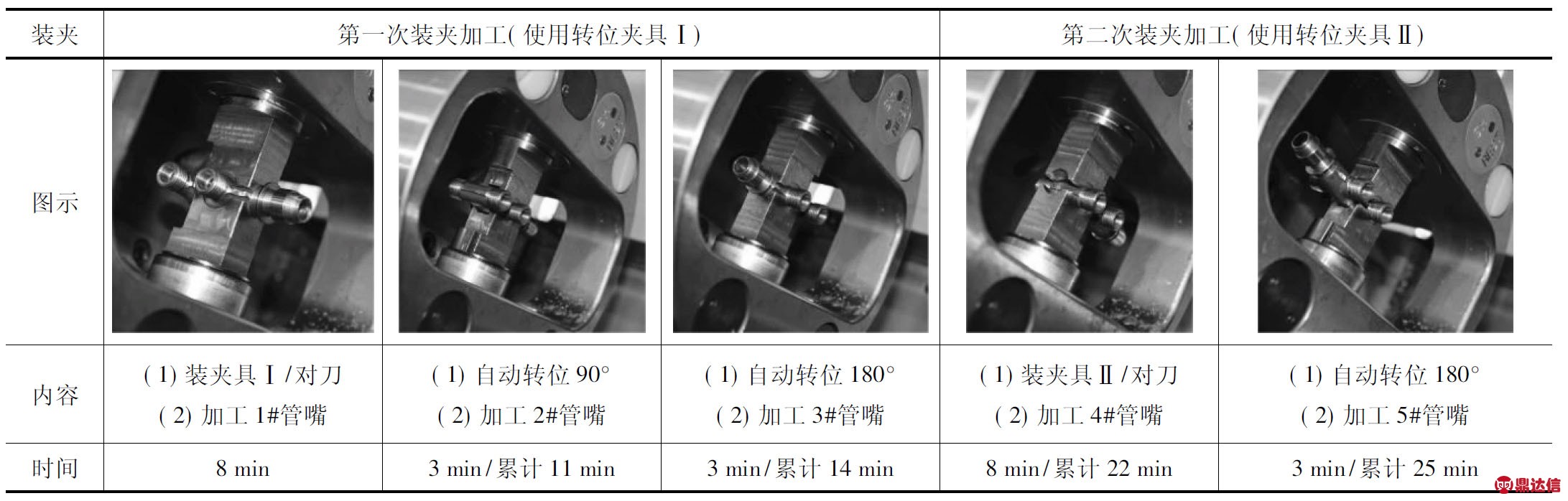
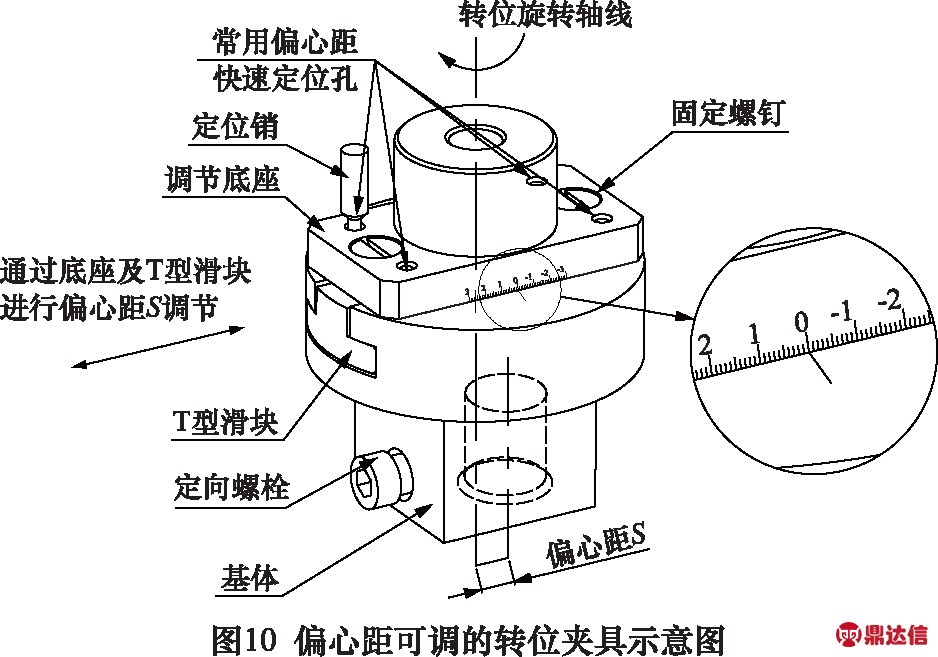
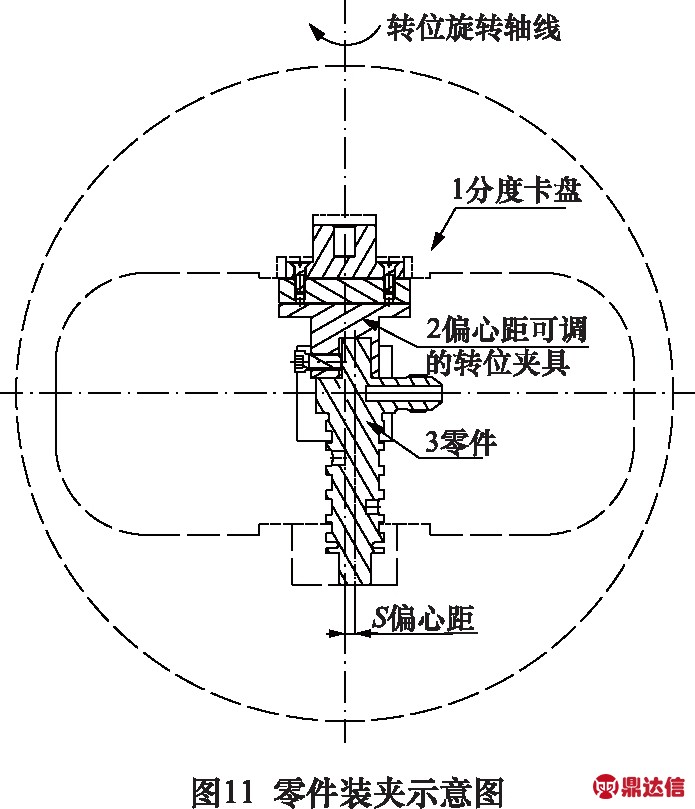
3 结语
根据管接头零件的结构特点,并结合数控车床上分度卡盘的应用情况,设计研发出了两套结构新颖、运行可靠自动转位加工机构,实现了无偏心管接头和具有偏心结构的转动接头的高效装夹定位与加工,彻底解决了管接头零件因种类多、数量大及锻造毛坯不易装夹定位造成的生产加工瓶颈问题,拓展了数控车床应用范围的同时,为企业柔性生产的构造打下了良好的基础,也对结构复杂的回转体零件加工起到一定的借鉴作用。
实践证明:自动转位夹具具有快速设计制造、通用性强、结构简单、使用方便的特点;转位加工技术实现了管接头零件自动转位连续加工,保证加工质量,提高效率,降低了操作者的劳动强度[8]。