摘要:挠性接头刚性差,在微细磨削加工中易变形,其精度难以控制.为了提高挠性接头的工作性能,重点研究了挠性接头细颈的磨削工艺参数及其表面质量.基于磨削加工、弹塑性力学和有限元法等理论,利用ABAQUS模拟单颗磨粒微细磨削高弹性合金钢,分析磨削工艺参数对磨削力、热的影响规律,并用专业金属切削软件Advantedge对残余应力进行仿真,研究工艺参数对残余应力的影响规律,为进一步提高细颈的磨削质量及挠性接头角刚度的稳定性奠定基础.研究结果表明,提高砂轮线速度,可以大大减小磨削过程对工件表面的热作用宽度和深度,有利于减小热损伤和提高表面质量.
关键词:挠性接头; 微细磨削; 仿真; 残余应力
挠性接头是挠性陀螺仪组成挠性支撑的关键部件,其制造精度直接影响陀螺仪性能的好坏[1].挠性接头关键部位是由2个直径为1~3 mm的微小孔形成厚度仅为45m的细颈,其尺寸精度要求在±1
m内.磨孔是其精加工工序,对零件的表面质量和使用性能至关重要.挠性接头材料为高弹性合金钢3J33,其具有较高的弹性模量和高的抗拉强度及低导热性,是典型的难加工材料.
由于惯性导航技术的保密与封锁性,现有文献都局限于对挠性接头细颈工艺方法的研究,而鲜有3J33材料磨削工艺参数对磨削力、热及其对加工质量的作用机制的研究报导.文献[2]对一体式挠性接头制造工艺技术进行了全面分析.文献[3]对挠性接头制造关键技术及措施和研磨必要性进行了探讨.文献[4]对挠性陀螺关键部件挠性接头的结构和工艺做了较为详细的综述,并指出细颈一般采用精密镗床镗孔或磨床磨孔.在难加工材料的磨削仿真中,文献[5]采用有限元方法研究了GH4169高温合金、TC4钛合金磨屑形成过程,以及磨削速度对磨屑形态、磨削力和磨削温度的影响.文献[6]利用ANSYS/LS-DYNA模拟单颗磨粒磨削光学玻璃的动态过程,分析了磨削深度、高的砂轮线速度及其综合作用情况对光学玻璃延性磨削的影响,揭示了光学玻璃的高速延性磨削机理.然而这些模型中都忽略了单颗磨粒的最大未变形厚度,且现有文献对其他难加工材料如钛合金、陶瓷、高温合金的磨削研究较多,而对于超高强度钢的磨削仿真甚至残余应力研究几乎空白.
工件材料、砂轮速度、工件速度等实际磨削条件对材料的弹塑性变形及磨削机理等具有重要影响.认识单颗磨粒的磨削作用是考察复杂磨削过程及其作用的重要方法[7].本文基于有限元仿真技术,开展微细磨削工艺参数对磨削力、热及其对残余应力作用机制的研究,为一体式挠性接头的高质量制造提供工艺参数优化设计的理论依据.
1 单颗磨粒微细磨削仿真模型的构建
ABAQUS分析软件具有优秀的网格细分技术,并可以设置刀具旋转,但它对残余应力仿真计算的应用技术尚不够成熟.Advantedge是专业的残余应力分析软件,但在二维仿真中不能设置刀具旋转运动.故采用ABAQUS建立单颗磨粒仿真模型,研究CBN(cubic boron nitride)磨粒在不同磨削参数下的力热作用机制.采用Advantedge建立基于单颗磨粒的残余应力仿真模型,分析不同工艺参数对残余应力的作用机制,为实际生产加工工艺参数的选择提供科学依据,从而提高加工质量和效率.
磨削是大量磨粒同时与被加工材料相互作用并完成材料去除的过程,磨削表面的形成机理非常复杂.因此,可将复杂磨削过程简化为单颗磨粒磨削的二维仿真模型,不仅模型简单、计算量小,而且能够观察到材料的塑性流动和应力变化规律.
1.1 微细磨削仿真几何运动模型
在单颗磨粒的仿真研究中,由于微孔磨削转速极高(可达120 000 r/min),磨削深度微米级,单颗磨粒在工件上的作用时间极短(< 1E-5 s),因此,可把内孔磨削简化成平面磨削.微孔直径φ3 mm,采用φ2.4 mm的CBN小砂轮磨削.单颗磨粒统一假设成理想锥体,顶锥角为106°,磨粒高度为50m,刃弧半径为5
m.单颗磨粒未变形厚度agmax计算公式[8]如式(1)所示.
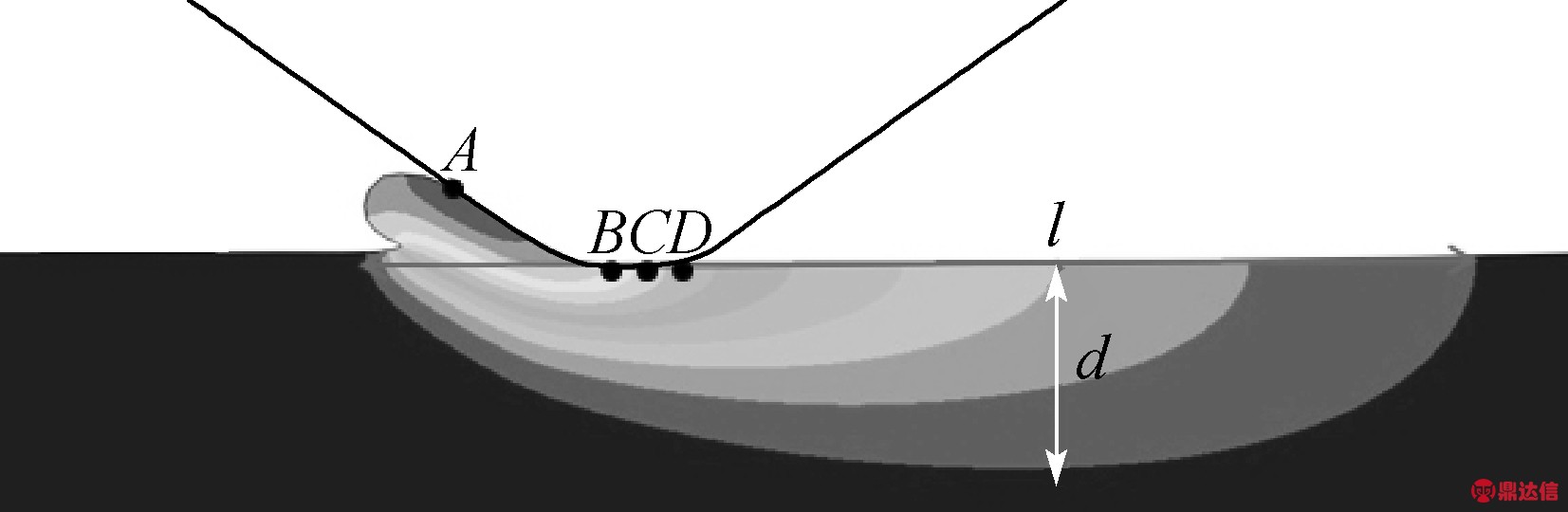
(1)
其中:vs为砂轮线速度;vw为工件线速度;Nd为砂轮动态有效磨刃数;θ为磨粒顶锥半角;ap为切深;ds为砂轮直径;dw为工件直径.
基于ABAQUS软件平台建立单颗磨粒磨削动态行为的二维仿真模型,单颗磨粒以一定的线速度围绕砂轮中心旋转,如图1所示,其中:Rs为砂轮半径,L和b分别为工件模型的长度和宽度.工件速度相对于磨粒速度而言很小,可使工件固定不动,从而实现了切削厚度从零增加至agmax.改变砂轮速度和最大未变形厚度可得到相应的力、热演变规律.
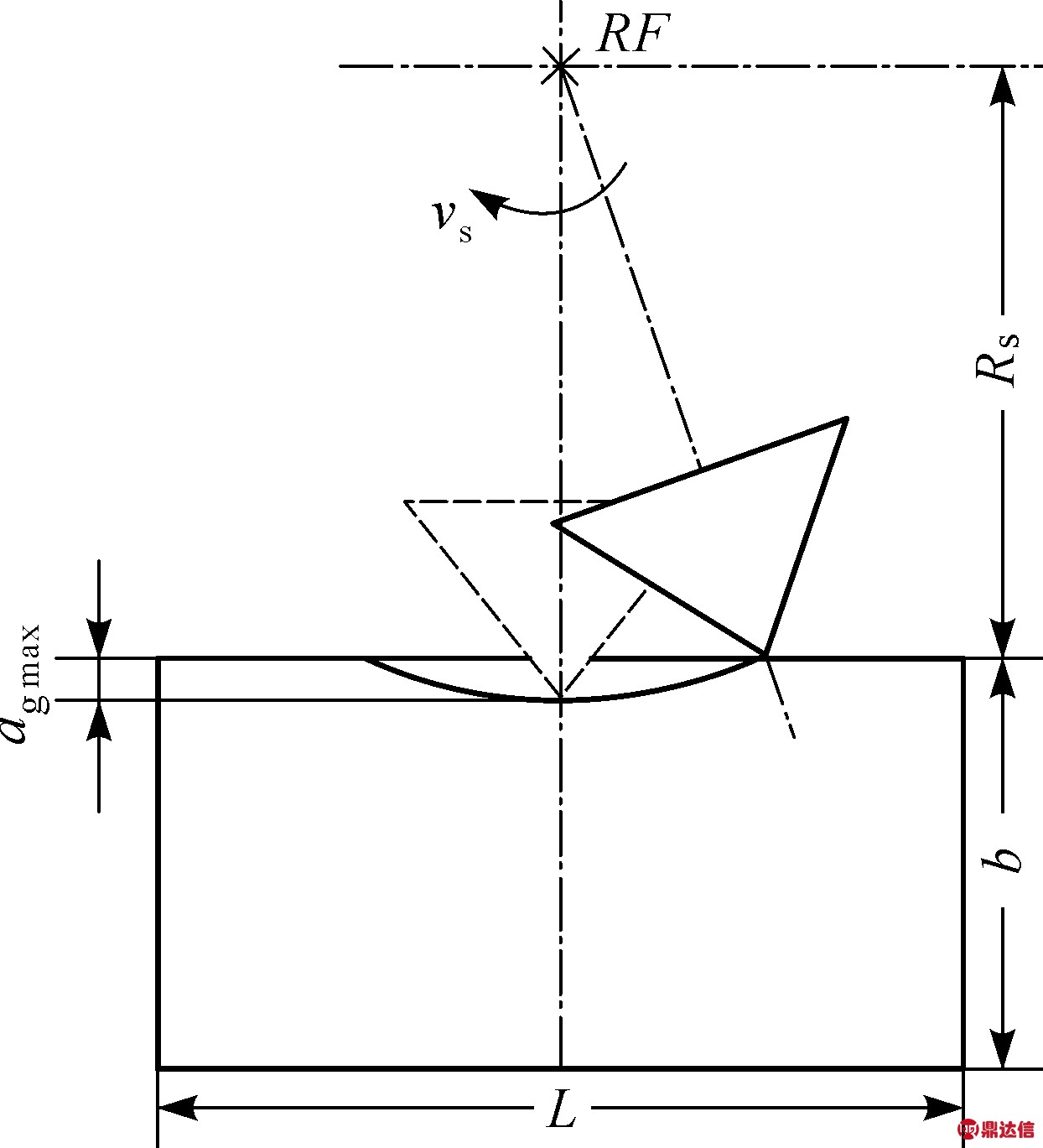
图1 单颗磨粒磨削过程示意图
Fig.1 Single grain grinding process diagram
基于Advantedge软件平台的二维正交微切削模块,构建单颗磨粒磨削高弹性合金的仿真模型,如图2(a)所示,单颗磨粒磨削过后自动冷却工件至室温,可查看工件残余应力值及其分布状态,如图2(b)所示.通过改变不同砂轮线速度和切深可得到残余应力分布规律.
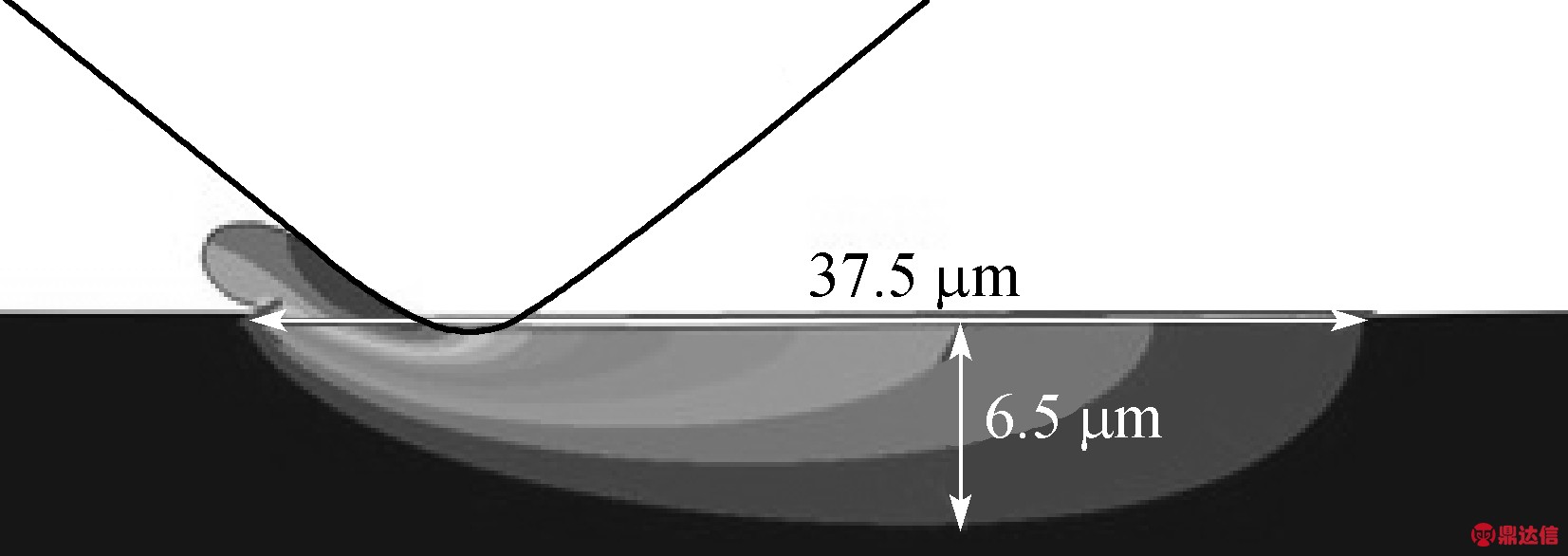
图2 磨削残余应力仿真模型
Fig.2 Grinding residual stress simulation model
1.2 磨削工艺参数组合方案
由于工件固定不动,只考虑砂轮速度vs和未变形厚度agmax改变,假定工件转速恒定(nw=100 r/min),工件线速度为0.016 m/s.仿真研究中取切深为1~10m.为了优选高速电主轴的工作转速,仿真研究中选取砂轮转速为20 000~200 000 r/min,Φ2.4 mm的砂轮直径,砂轮线速度为2.5~25 m/s.仿真选择的磨削参数如表1所示,以考察磨削后的残余应力与材料去除率
.
的计算如式(2)所示.
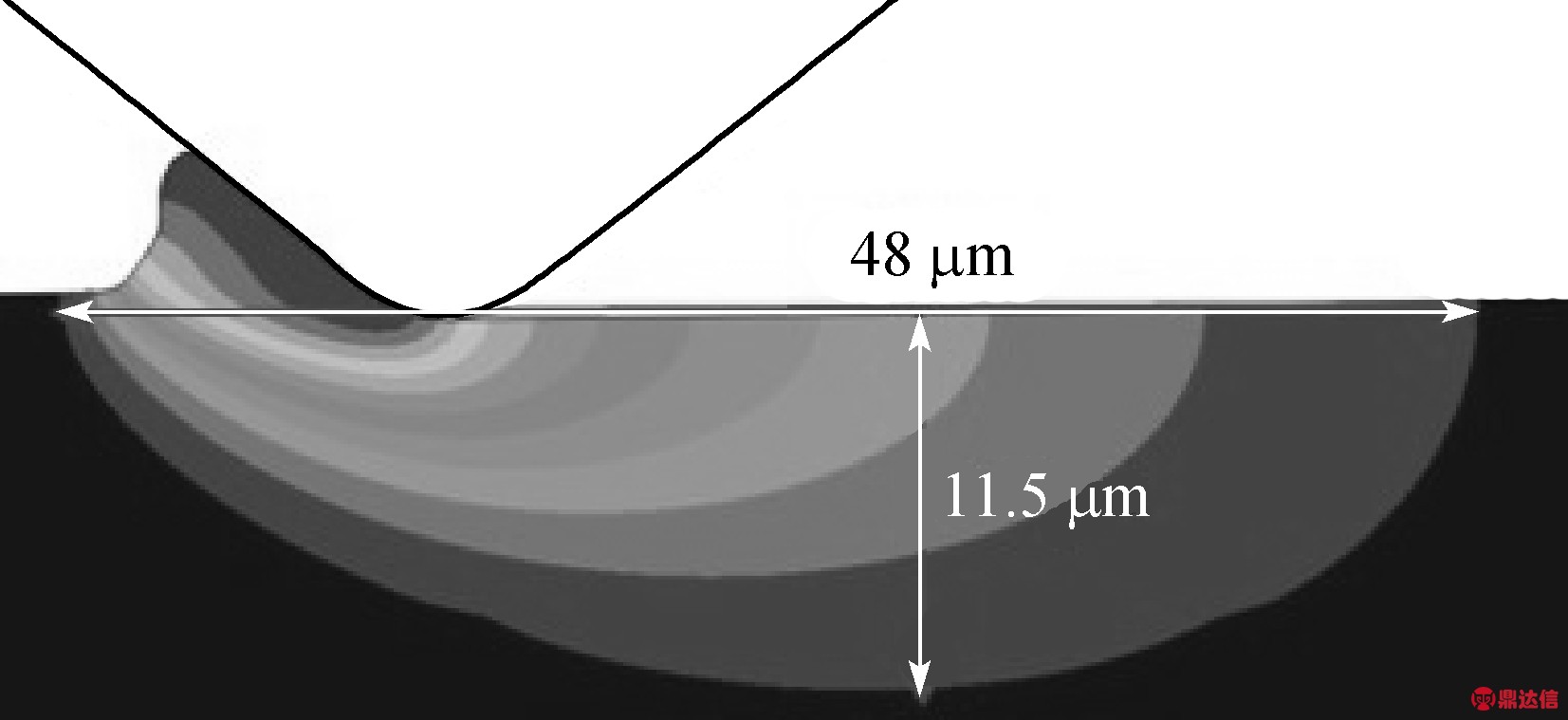
(2)
表1 磨削工艺参数
Table 1 The grinding process parameters
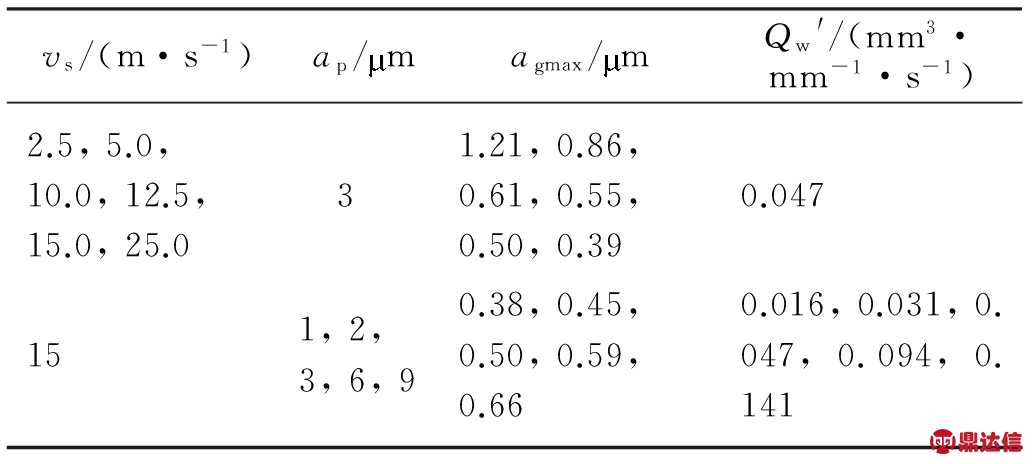
1.3 材料本构模型的建立
惯性导航关键件挠性接头的材料为高弹性合金3J33,是马氏体时效钢.Ni18-250是一种超高强度钢.由两者材料成分(如表2)与物理性能(如表3)对比可知[9-11],两者同属马氏体时效钢,成分性能相似,相对误差足够小,因此,仿真研究中,采用Ni18-250本构模型代替3J33.磨粒视为刚体,材料为CBN,其物理性能参数如表4所示.
表2 3J33与Ni18-250成分对比
Table 2 Composition comparison between 3J33 and Ni18-250 %
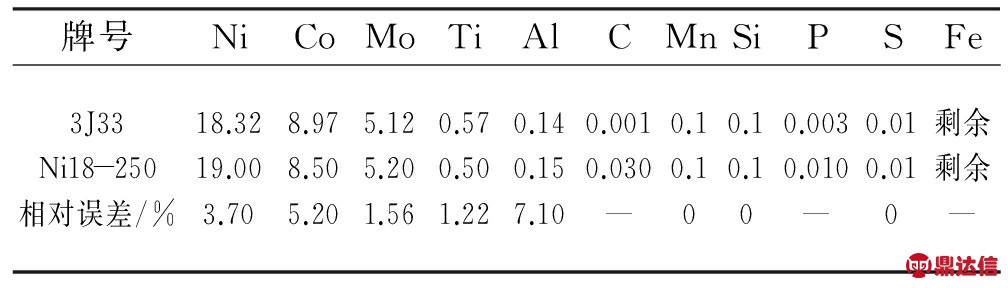
表3 3J33与Ni18-250物理性能对比
Table 3 Physics performance comparison between 3J33 and Ni18-250
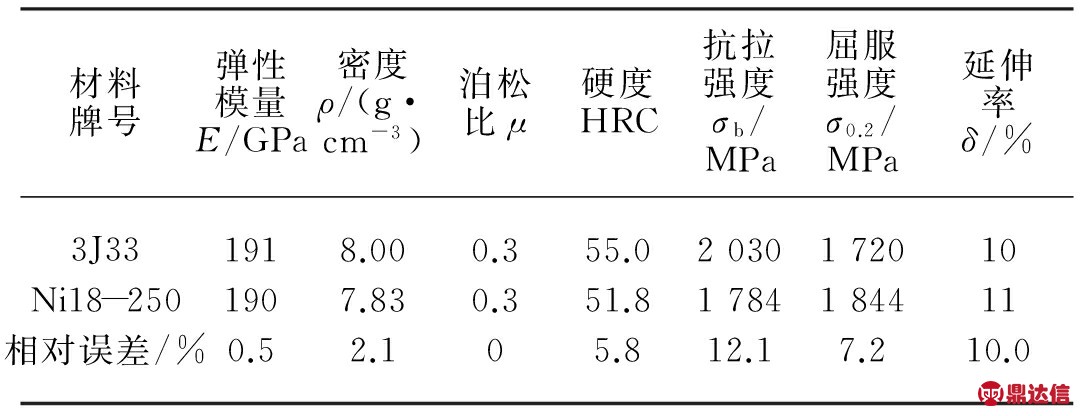
表4 工件与磨粒材料物理性能参数表
Table 4 Physical performance parameters of workpiece and grinding grain

在模拟磨削时,应使用能真实反映应变、应变率、温度对材料流动应力影响的本构方程.考虑各种因素对工件材料硬化应力的影响,应用Johnson-cook模型,认为材料在高应变率下表现为应变硬化、应变率强化和热软化效应.Johnson-cook数学表达式如式(3)所示.
(3)
式中:σ为屈服应力;C1,C2,C3和m为相关系数;n为材料硬化系数;ε为等效应变;为应变率;
为相对塑性应变率;T为温度;T0为环境温度;Tm为熔化温度.仿真中所需的JC本构模型参数[12]如表5所示.
表5 Ni18-250JC模型参数
Table 5 Ni18-250JC model parameters
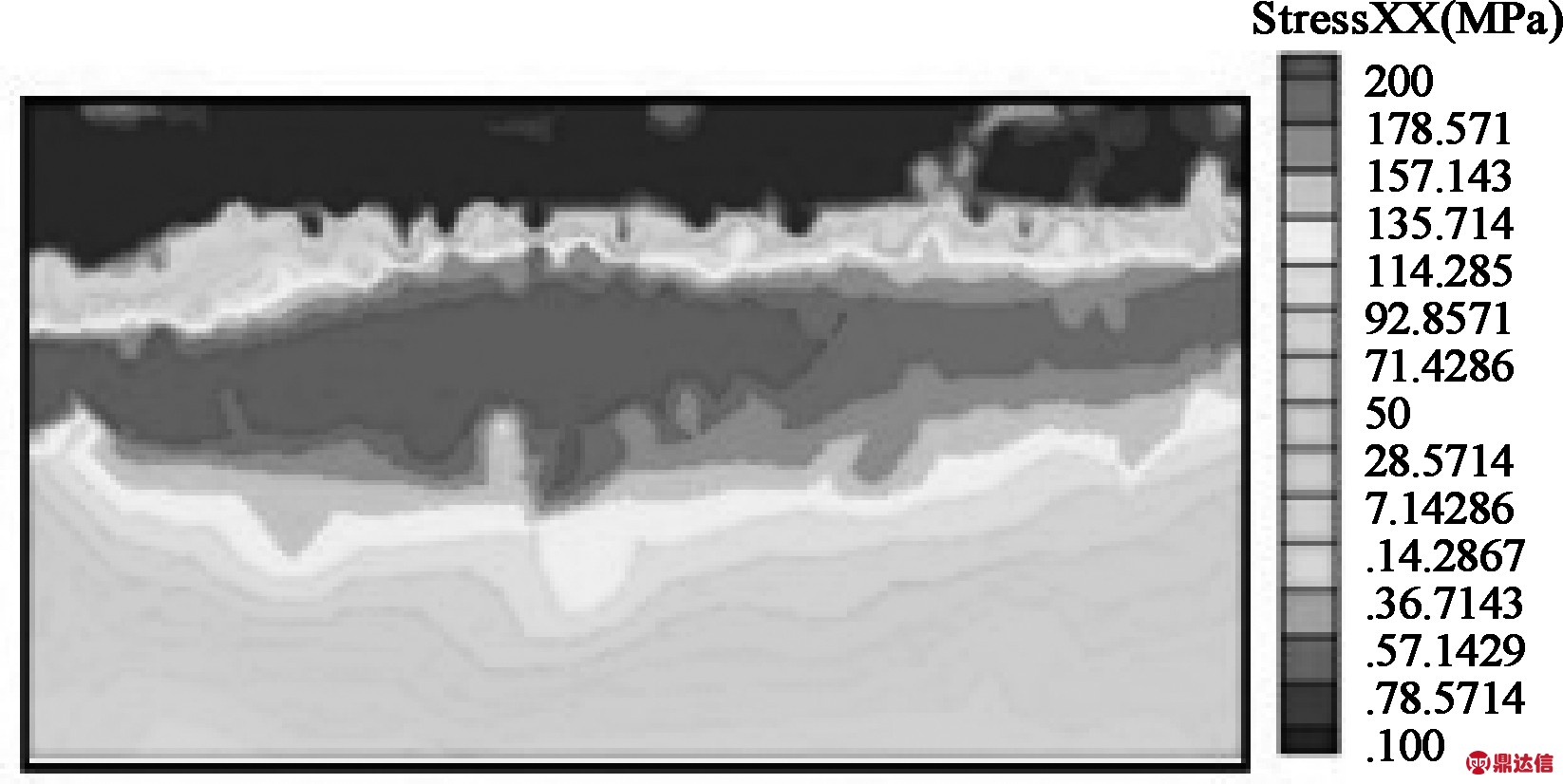
1.4 网格划分
磨粒相对于工件的刚性很大,本文把磨粒设置为刚性体,故无需对磨粒进行网格划分.工件的网格划分如图3所示.在距离工件上表面10m层深处加密网格,采用双精度偏离撒种方式布置种子数,在磨削区域最小单位尺寸设置为0.1
m.其余地方设置全局均匀种子,单元尺寸为0.002 mm.网格单元类型为CPE4RT,是四节点耦合平面应变单元,双线性位移,缩减积分,为了避免网格畸形沙漏现象,施加虚拟刚度以限制沙漏模式扩展.为了防止不合格单元形状,在单颗磨粒磨削模拟过程中加入ALE(arbitrary Lagrange-euler)自适应网格控制.
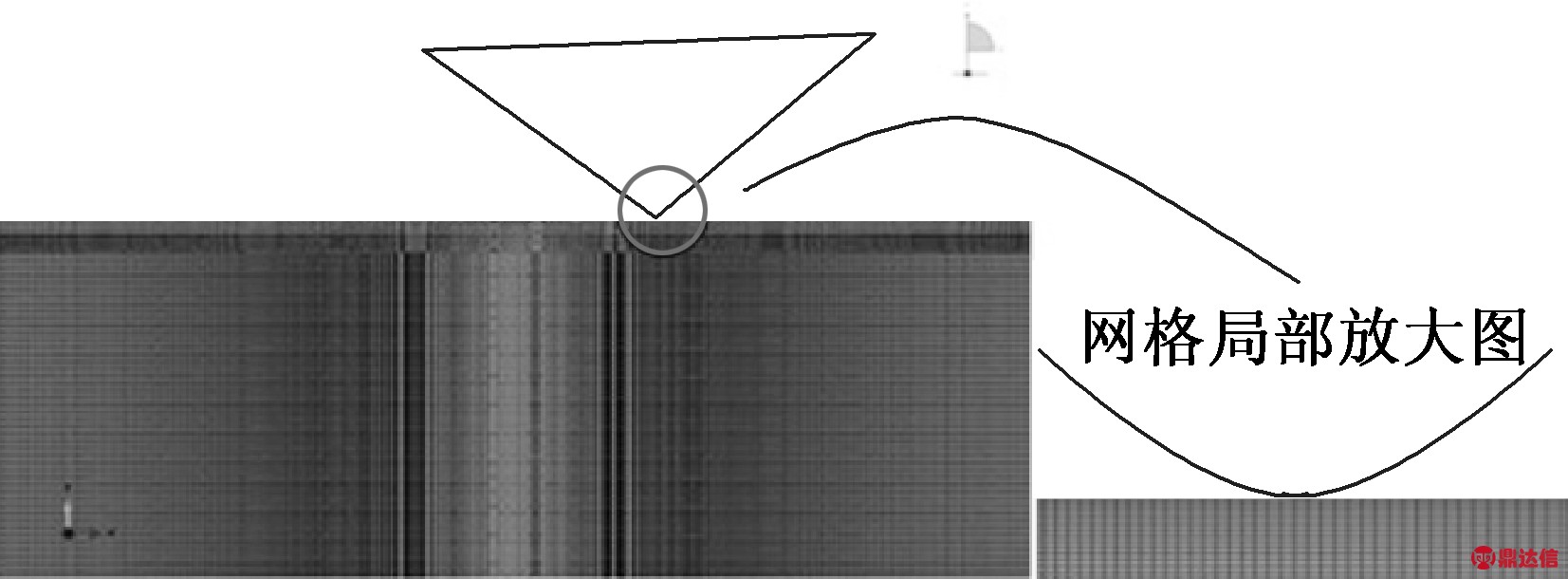
图3 工件网格的划分
Fig.3 Workpiece meshing
2 微细磨削仿真结果分析
通过微细磨削仿真,研究不同工艺参数组合对磨削力和热的影响,进而探讨力、热对工件表面质量完整性的影响.由于挠性接头细颈的尺寸精度及使用性能要求极高,应以零件的表面质量及磨削精度为主要考虑因素,在质量精度范围内提高加工效率,在现有条件下进行工艺参数优化,为实际加工提供理论支撑.
2.1 磨削工艺参数对磨削力、热影响机制
在磨削弧区分别取工件上磨屑(A)、刀尖(B)、远离刀尖1~2m(C,D)处的温度,如图4所示.由图4可知,温度沿着切削方向逐步升高,原因是在刀具前方的材料受到刀具剧烈挤压、摩擦、剪切作用,使得温度迅速升高集中在磨屑上;随着刀尖的远离,工件表面受到外界空气的冷却和热量传递作用使得温度逐步下降.磨削热有一定的热作用影响区域,热作用宽度l表现为磨削过的工件表面至磨屑根部处的位置,热作用深度d主要受材料内部的热传递系数及工件表面温度的影响.从温度分布来看,在未加入任何冷却液的情况下(干磨),磨削高弹性合金产生的热量多且导热系数低,工件表面温度可达400~500 ℃,容易引起工件烧伤氧化、产生的热应力引起磨削裂纹等.故在微细磨削时需要严格控制温度分布,采用一定的冷却方式降低磨削热,以保证工件表面质量.
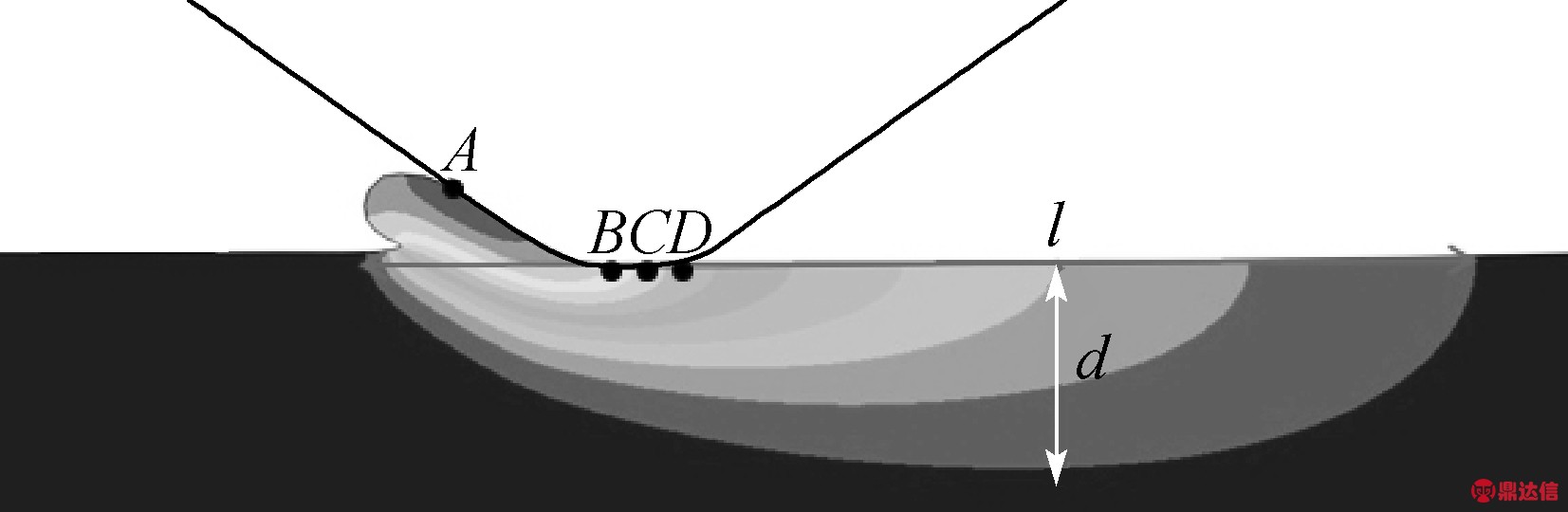
图4 磨削温度取点示意图
Fig.4 Grinding temperature access point diagram
当工件线速度(vw=0.016 m/s)、切深(ap=3m)不变时,即材料去除率不变,法向和切向磨削力(Fn和Ft)随着砂轮转速的增大而非线性降低;而磨削热随着砂轮线速度的增大而增大,但增大幅度有所减缓,如图5所示.由图5可知,砂轮线速度从15 m/s(ns=120 000 r/min)提高至25 m/s(ns=200 000 r/min)时,磨削力减小28%,工件表面温度升高5.14%.说明当砂轮转速超过15 m/s时,磨削力却有较大的下降幅度,工件表面温度(tB、tC、tD)上升缓慢,甚至具有下降趋势.但是,由于速度过高会引起振动,刀具磨损,导致工件表面质量下降,因此,需要进行全面的综合考虑.当材料去除率一定时,为了减小切削力和磨削热对薄壁件变形的影响,应该在合理的速度范围内选取较高的砂轮速度,获得更小的切削力,使力引起的变形减小,工件表面质量精度提高.

(a) 磨削力
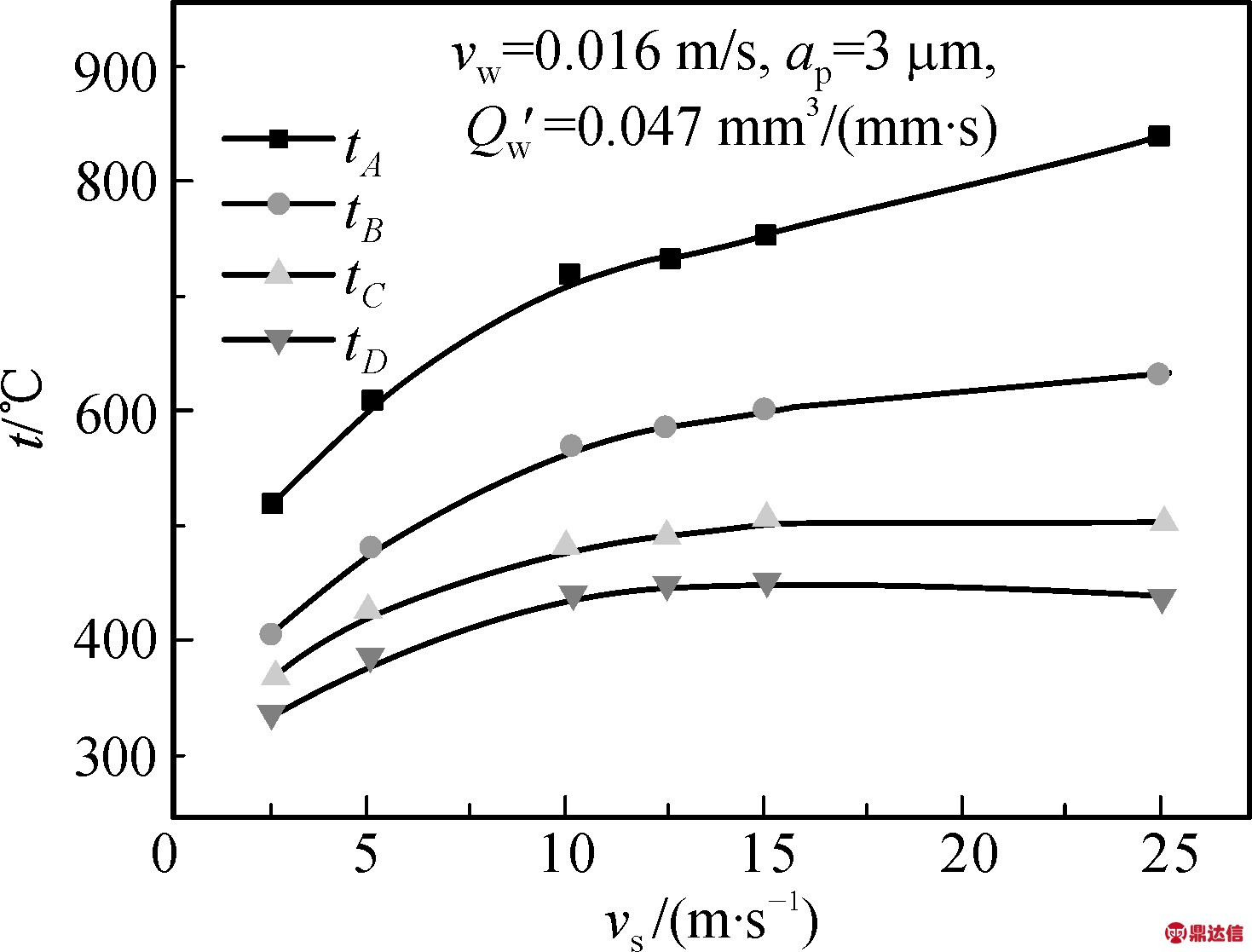
(b) 工件表面温度
图5 砂轮线速度对磨削力与工件表面温度的影响
Fig.5 Influence of wheel speed on grinding force and workpiece surface temperature
当砂轮线速度(vs=15 m/s)、工件线速度(vw=0.016 m/s)不变时,提高切深可有效提高金属去除率,如图6所示.由图6可知,切深ap由1m提高至3
m,磨削力增大6.4%,磨削热升高7.49%,agmax增加0.32倍(根据式(1)),但材料去除率
增加至3倍(根据式(2)).说明在微细磨削中提高切深可以大大提高材料去除率,但由于单颗磨粒最大未变形厚度agmax增幅不大,磨削力和热的增幅也不明显,有利于控制残余应力等表面质量.因此,在工件线速度与砂轮转速一定时,在工件所允许的力、热范围内可适当提高切深(3~6
m),从而提高金属去除率,实现加工精度范围内的高效磨削.
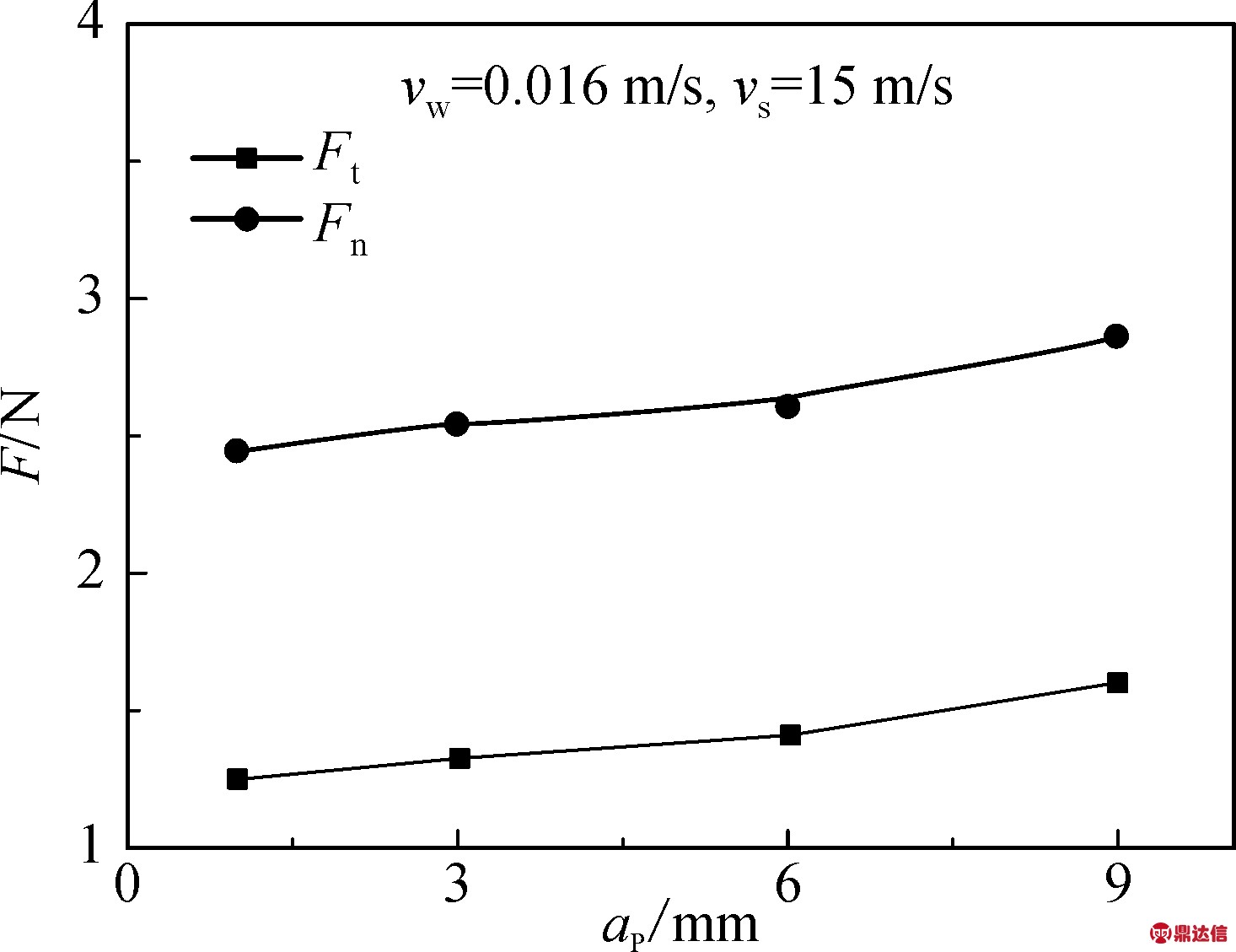
(a) 磨削力
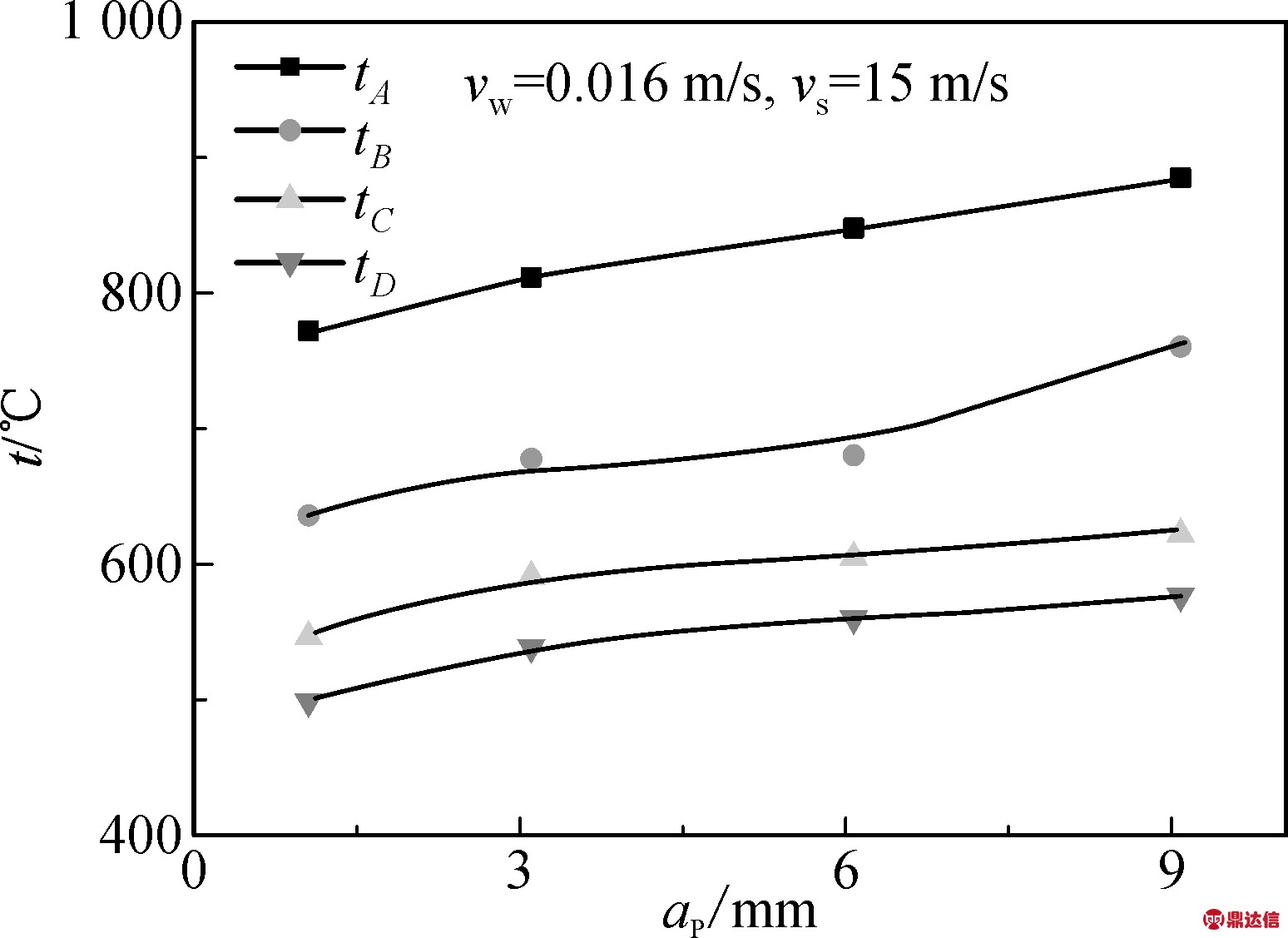
(b) 工件表面温度
图6 磨削切深对磨削力和工件表面温度的影响
Fig.6 Influence of cutting depth on grinding force and workpiece surface temperature
磨削热对磨削弧区的热作用影响如图7所示.当切深不变、砂轮线速度提高5倍时,如图7(a)与7(b),热作用宽度降低50.00%,热作用深度降低64.35%,说明砂轮线速度越高,磨削弧长越短,工件与磨粒作用时间越短,大量的磨削热集中在工件表层,热量来不及向下传导,故作用深度大大减小;当砂轮线速度不变,切深提高6倍,如图7(c)与7(d),热作用宽度增加33.45%,热作用深度增加23.33%.说明提高砂轮线速度有利于减小磨削热对工件表面的损伤,工艺参数优化设计时,应优先选择高的砂轮转速(80 000~120 000 r/min),再适当提高磨削切深(3~6m),从而提高磨削质量和磨削效率.
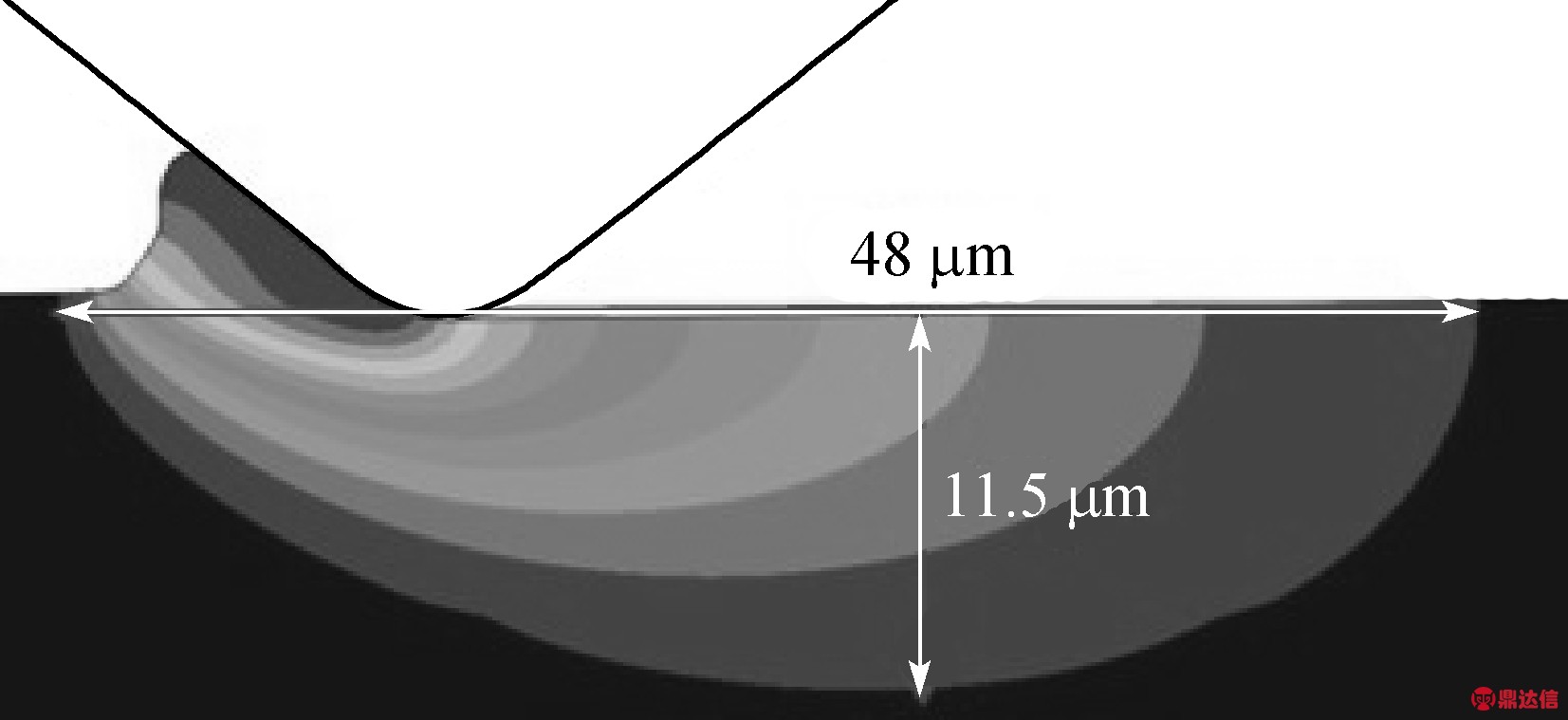
(a)vs=5 m/s,ap=3m
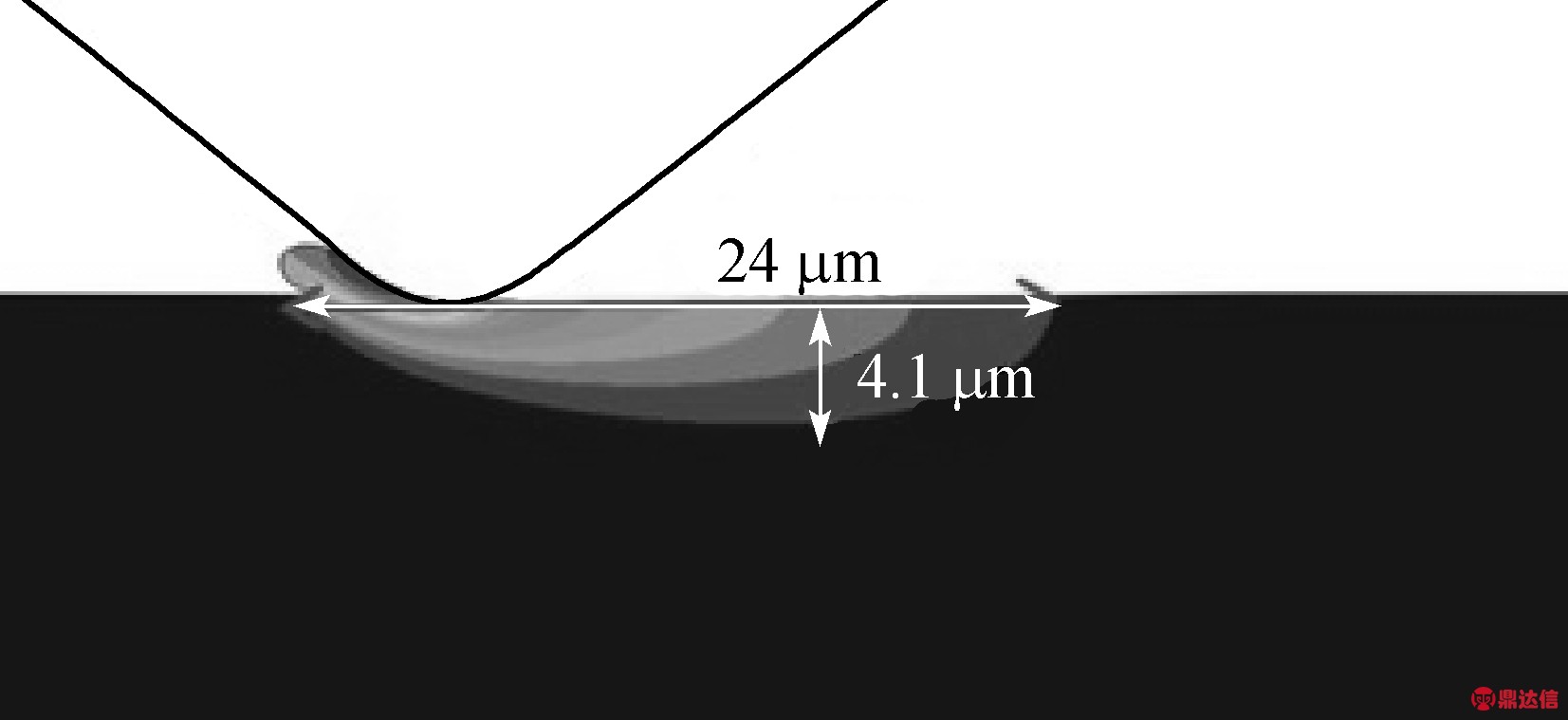
(b)vs=25 m/s,ap=3m
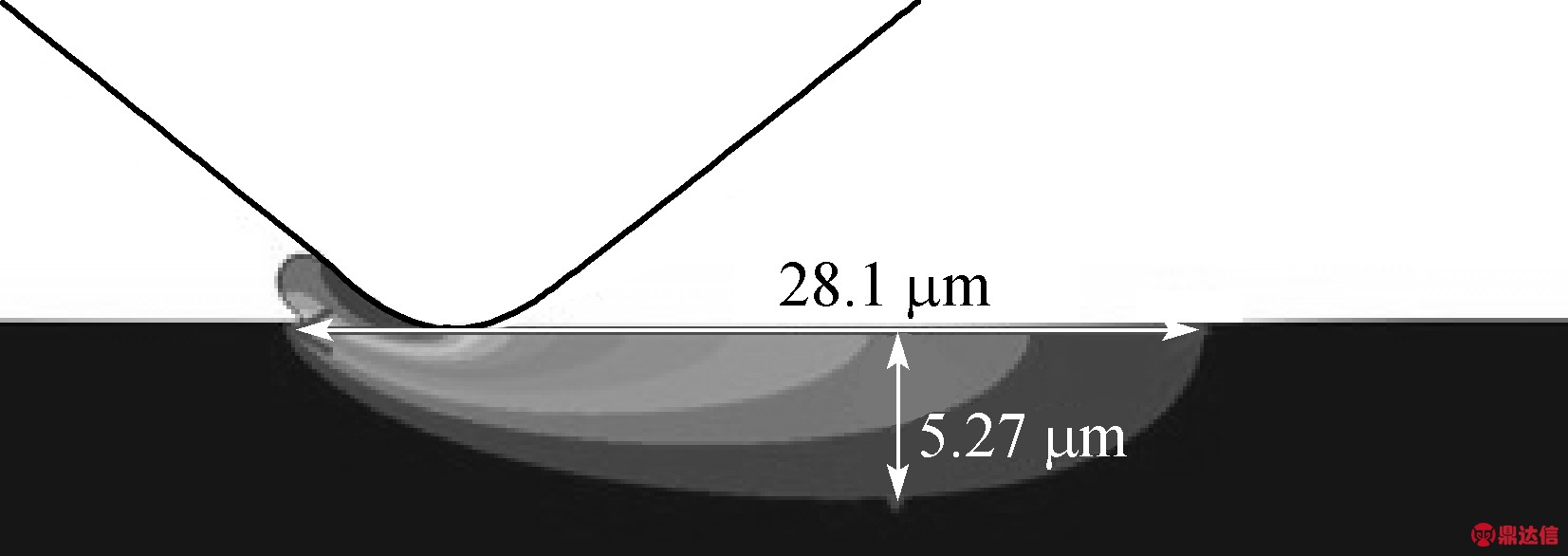
(c)vs=15 m/s,ap=1m
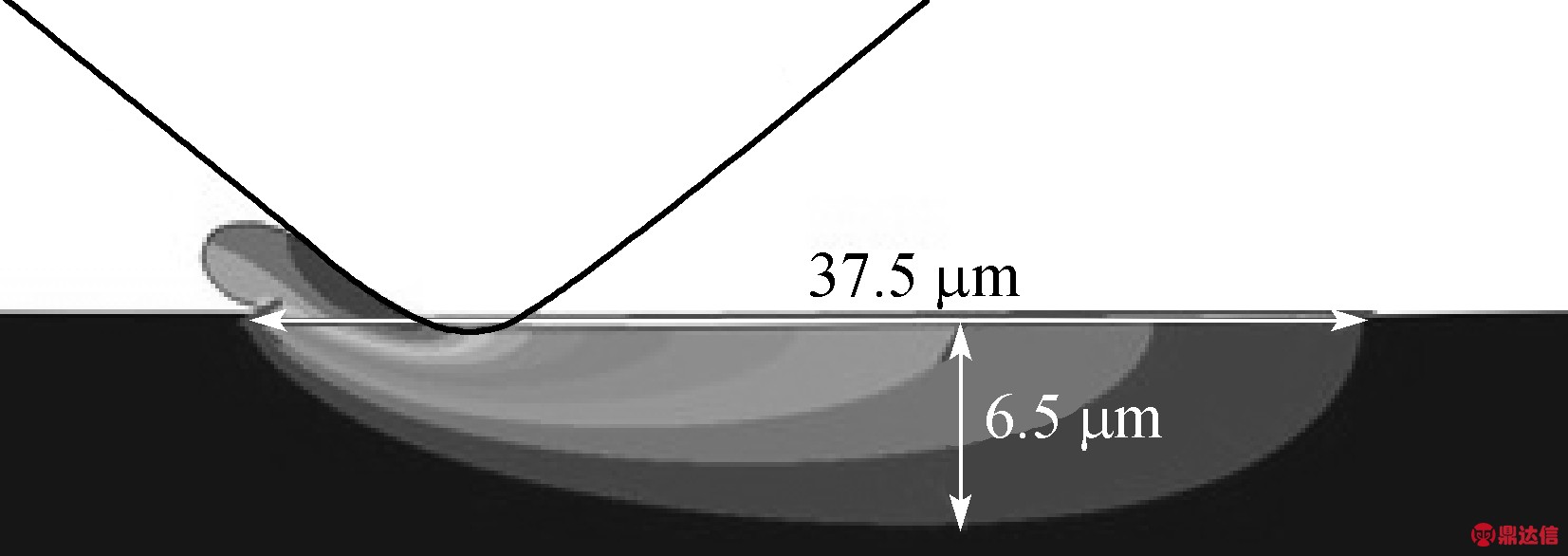
(d)vs=15 m/s,ap=6m
图7 工件磨削表面的热分布云图
Fig.7 Thermal distribution diagram of workpiece grinding surface
2.2 磨削工艺参数对残余应力的影响机制
磨削残余应力是工件表面质量的重要指标,直接影响接头的变形及质量稳定性,研究工艺参数引起的残余应力分布规律,可以为优化工艺参数的选择提供理论依据.残余应力分布如图8所示.由图8可知,微细磨削的表面残余应力为压应力(-150~-400 MPa),亚表层应力为拉应力(150~300 MPa),说明机械效应起主导作用,热效应引起的拉应力不足以逆转机械效应引起的压应力.当切深不变时(图8(a)),从磨粒对工件表面的机械作用力角度来分析,当砂轮线速度提高,磨削力下降,使得表面残余压应力值和亚表层拉应力值减小;从磨削热作用区域来分析,砂轮线速度提高,虽然工件表面温度有所提高,但磨削热作用深度减小,导致拉应力分布层深度减小,综合结果为应力极差值降低,工件表面质量稳定.同理,当砂轮线速度不变时(图8(b)),切深越大残余压应力与拉应力层越深,应力极差越大,质量越不稳定.
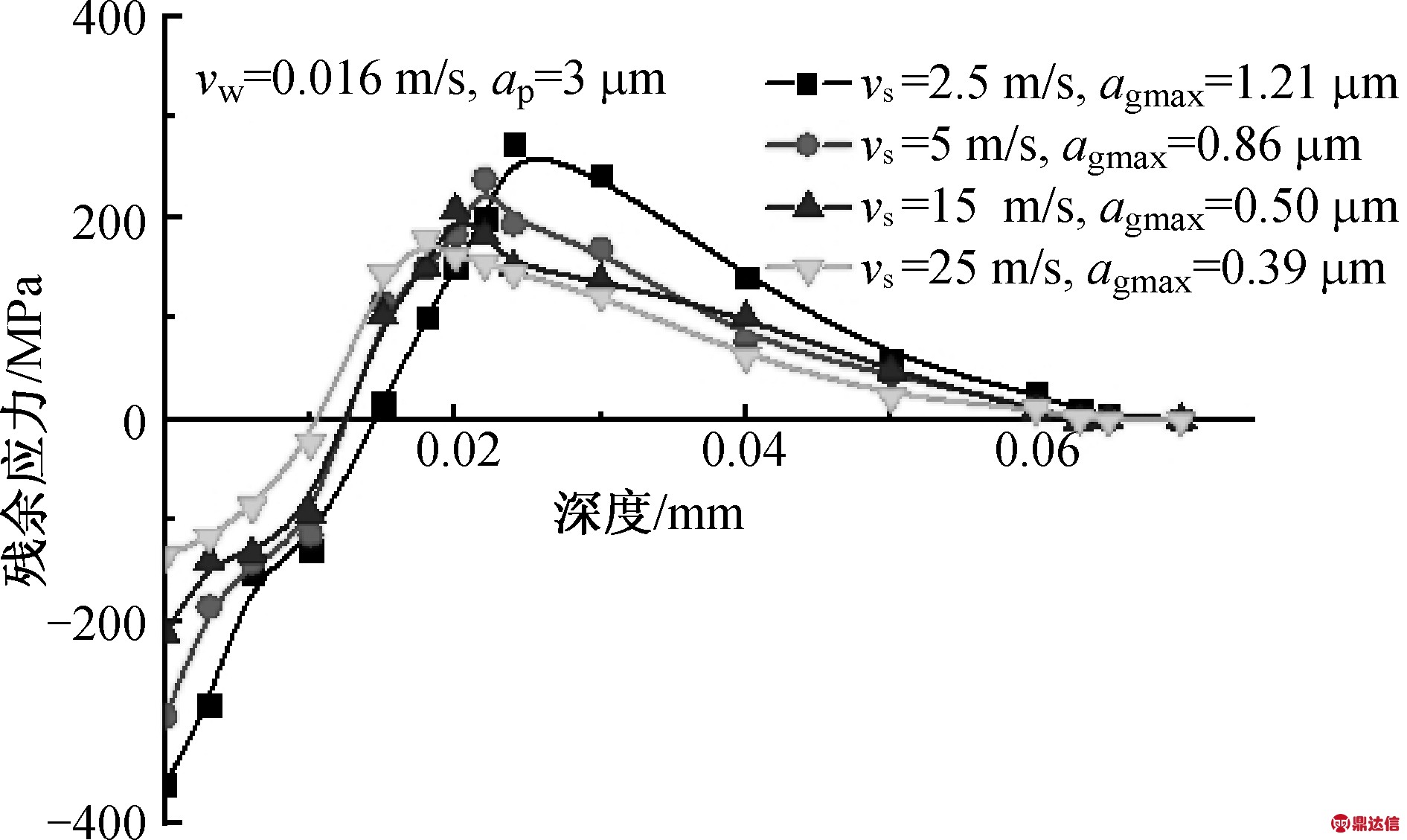
(a) 砂轮线速度(ap=3m)
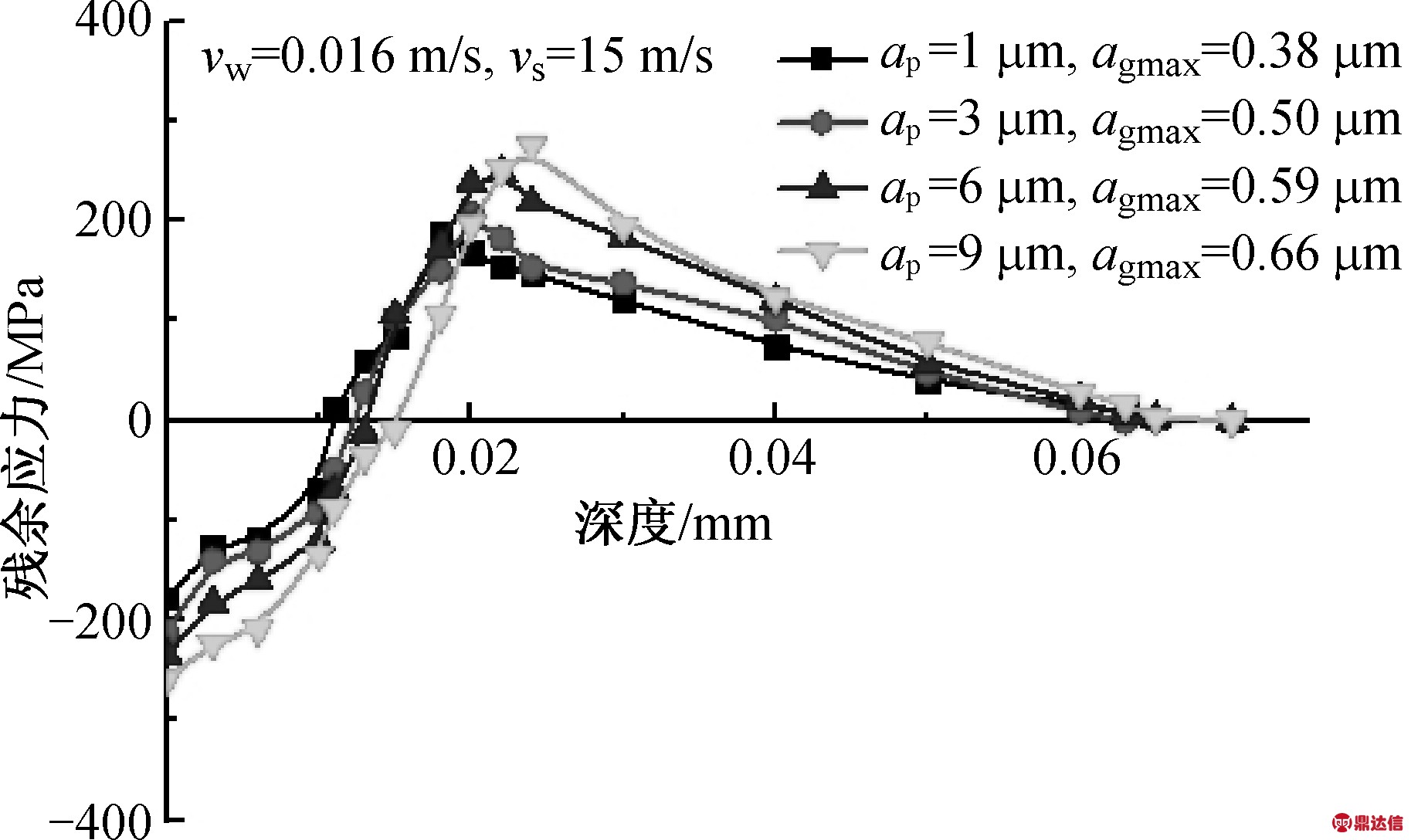
(b) 磨削深度(vs=15 m/s)
图8 磨削工艺参数对残余应力的作用
Fig.8 Grinding process parameters’ effect on residual stress
不同磨削参数下的残余应力分布云图如图9所示.由图9可知,由于最大未变形厚度的变化不及切深变化快,残余应力对砂轮速度比切深更敏感.在实际加工中,为了保证零件的质量稳定性,在合理的范围内应首选高砂轮转速(80 000 ~120 000 r/min),再适当提高切深(3~6m),使工件残余应力值越靠近平衡线,则引起的变形量会减小,提高了零件的加工精度.例如在现有主轴条件下,若选择vs=15 m/s(ns=120 000 r/min),ap=3
m进行磨削,比ap=1
m时应力极差只增加了12.6%,而加工效率却提高了3倍,这样既可保证残余应力极差小,又能保证加工效率的提高.
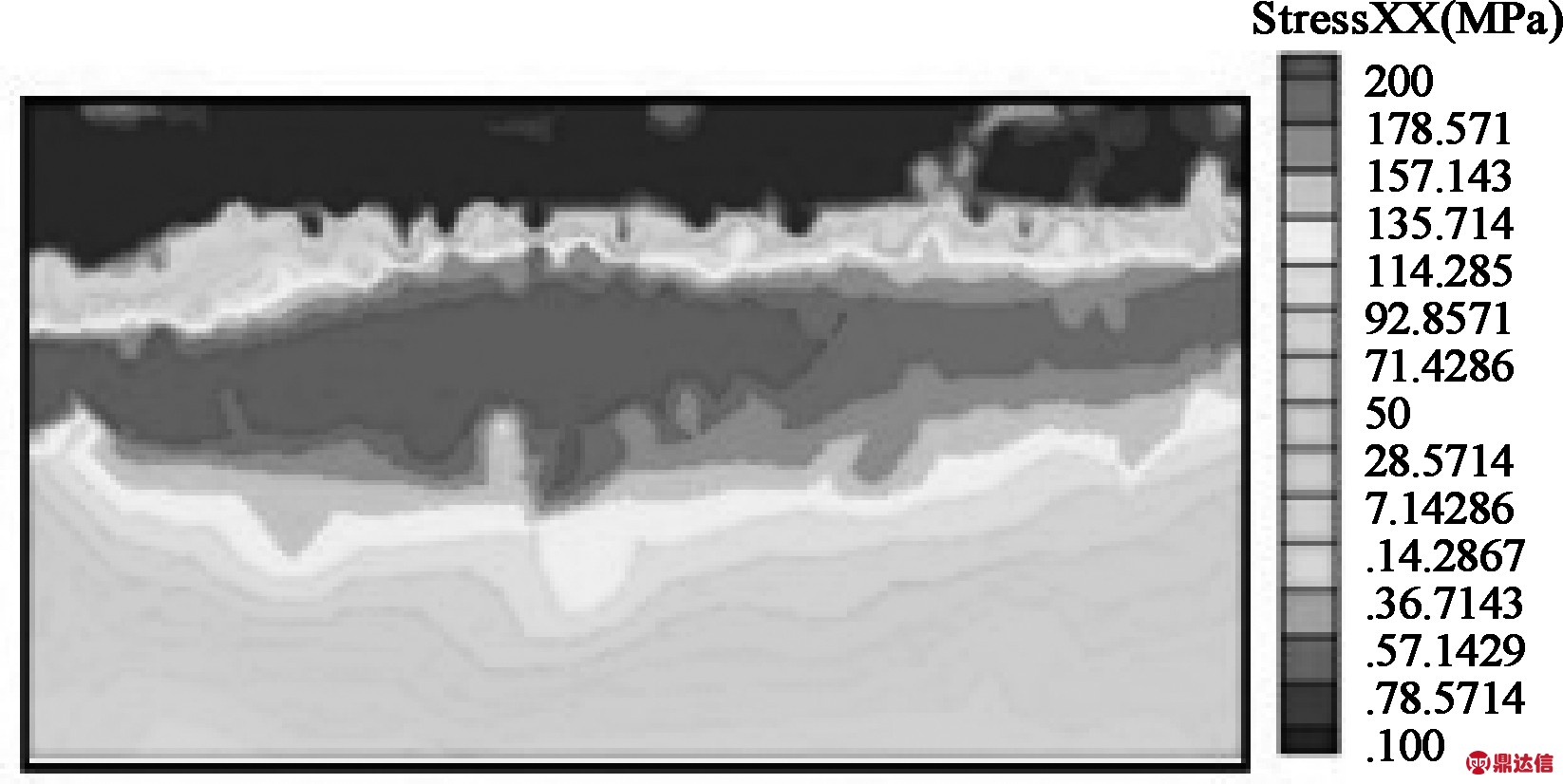
(a)vs=5 m/s,ap=3m
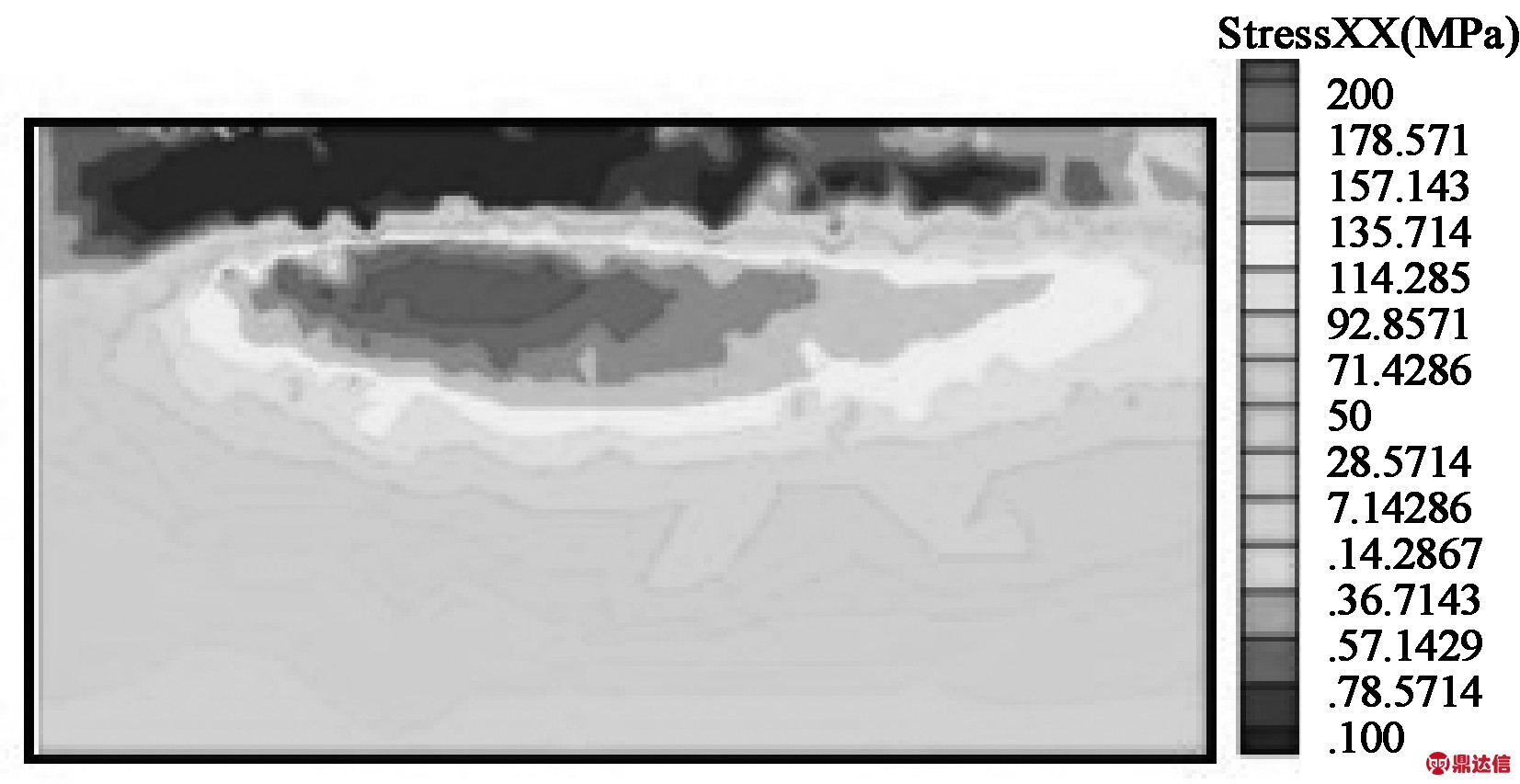
(b)vs=25 m/s,ap=3m
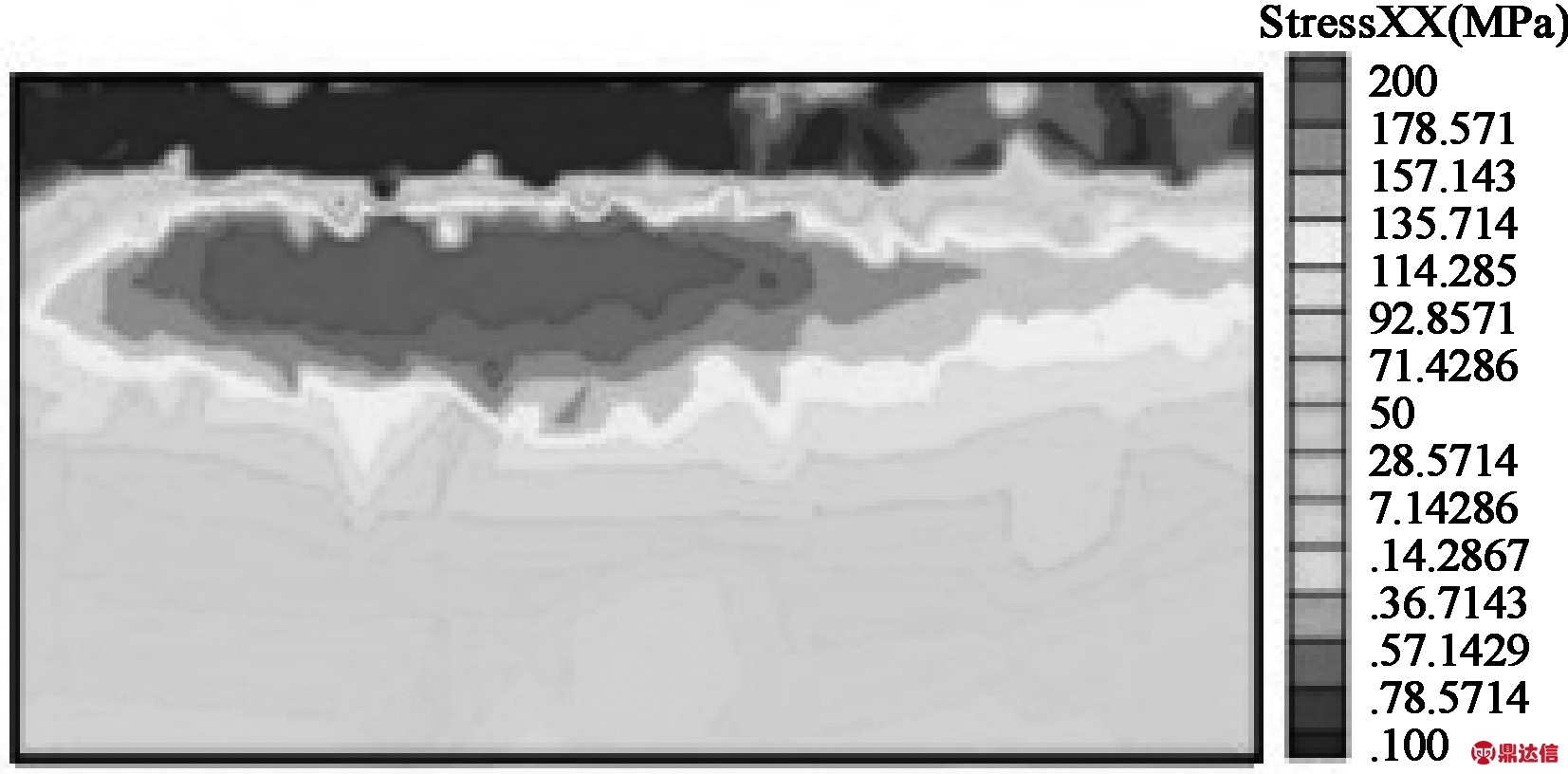
(c)vs=15 m/s,ap=1m
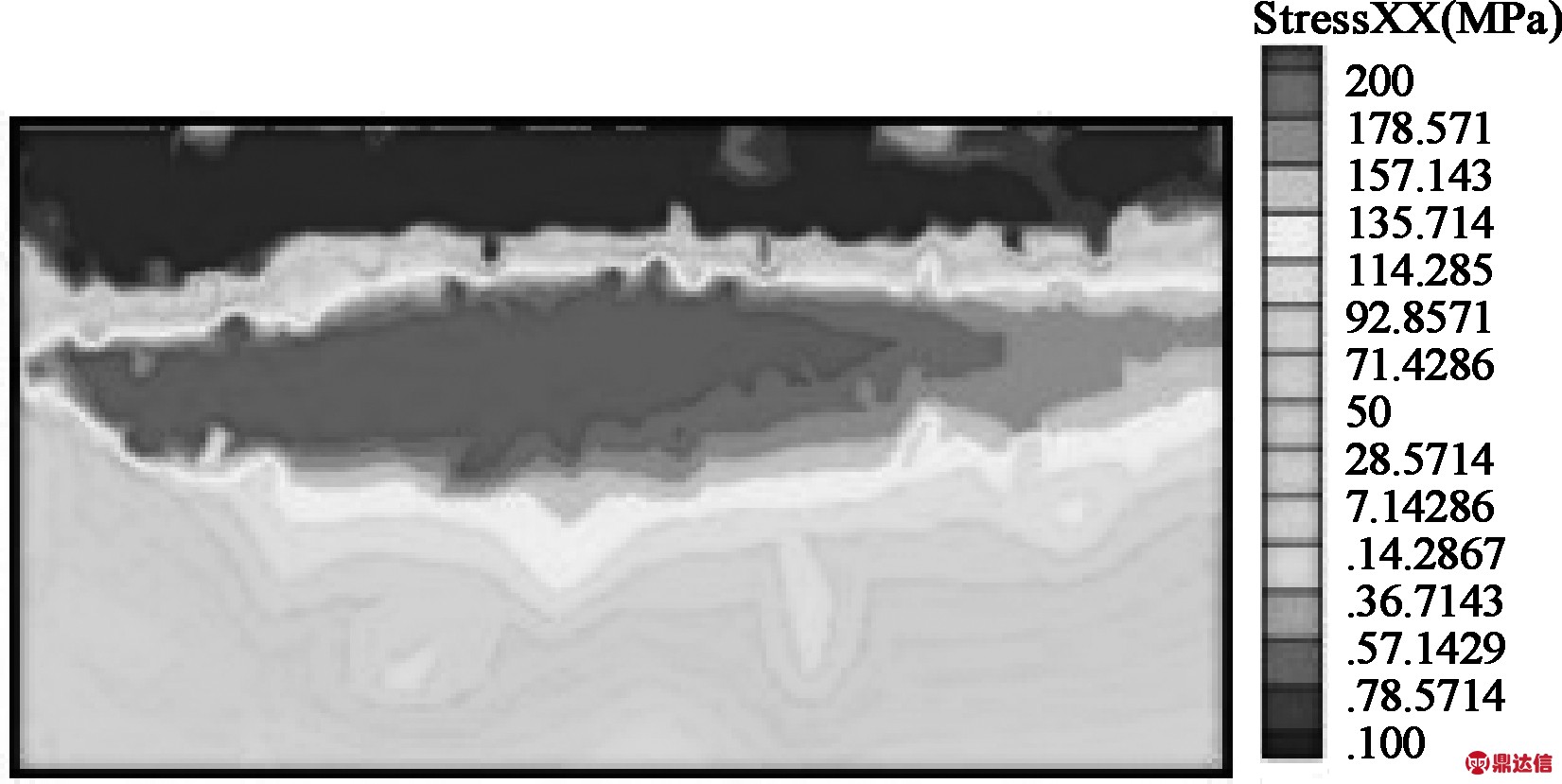
(d)vs=15 m/s,ap=6m
图9 不同磨削参数下的残余应力分布云图
Fig.9 Residual stress distribution diagram under different grinding parameters
但考虑到vs=15 m/s(ns=120 000 r/min)为主轴极限速度,可能会引起主轴负荷过大,寿命有所降低.当vs=12.5 m/s时,与vs=15 m/s相比磨削力增加程度在14%以内,磨削热变化幅度不明显,导致压应力增加的程度大于拉应力,最终使得应力极差值增大9.8%.这虽然对于细颈的变形具有一定的影响,但若采用极限转速,主轴跳动量大同样对零件变形有影响,综合考虑下在零件所允许变形范围内可采用vs=12.5 m/s(ns=100 000 r/min)进行加工.
3 结 语
本文针对挠性接头细颈易变形、内表面加工散热条件差等薄弱环节,研究了磨削参数对磨削力和工件表面温度的作用机制,探索了磨削参数对残余应力影响.结果表明,可以依据零件质量要求和材料去除率目标,进行磨削工艺参数的优化设计,其主要策略与结论如下所述.
(1) 在磨削深度一定,材料去除率一定时,提高砂轮线速度不仅降低磨削力,还降低热作用区域,使得磨削残余应力极差变小,易于减少零件的加工变形.
(2) 在砂轮线速度一定,在保证工件质量的前提下,适当提高磨削深度,可以大大提高材料去除率.
(3) 提高砂轮线速度,可以大大减小磨削过程对工件表面的热作用宽度和深度,有利于减小热损伤和提高表面质量.因此,工艺参数设计时,应优先选择高的砂轮线速度,再适当提高磨削切深,以实现产品质量与生产效率的完美统一.