摘 要:根据丁腈橡胶在变压器中的使用环境,设计了四种条件下(70 ℃热空气、70 ℃热空气压缩、70 ℃热油、70 ℃热油压缩)的老化实验。结果表明,四种条件下,随着老化时间的延长,断裂伸长率及抗压缩永久变形能力持续下降;拉伸强度在老化初期会有小幅下降,然后持续上升,到某一时间开始下降,有油条件下会更早出现转折,同时在老化初期硬度会有小幅降低,但整体的硬度变化趋势是上升的。油介质中老化的橡胶,表现出相对较低的硬度及断裂伸长率、较高的压缩永久变形率,和前中期相对较高的拉伸强度。压缩应力的存在,使得橡胶材料表现出更低的拉伸强度、硬度及断裂伸长率。四种条件下的老化过程中玻璃化转变温度均有所上升。丁腈橡胶的老化是以分子链交联反应为主的,油和压缩应力使丁腈橡胶的各项性能表现出不同的变化趋势,对橡胶寿命的预测要根据其实际工况下的性能变化规律及具体性能需求选择合适的指标。
关键词:丁腈橡胶;热氧老化;热油;压缩
丁腈橡胶(NBR)由于其优异的耐油性、耐磨性及物理力学性能而被广泛应用于油介质密封领域[1]。但是,由于丁腈橡胶主链中含有双键,其耐热老化、耐候性及化学稳定性等较差,在变压器等充油设备长期运行过程中,出现由于其老化导致的漏油缺陷较为严重,影响了电力设备的安全稳定运行。因此,研究丁腈橡胶在变压器运行工况下的老化行为非常必要。
国内外学者对丁腈橡胶老化机理及性能演变规律的研究众多[2-8]。熊英等[6]研究了丁腈橡胶在应力和高温作用下的老化现象,发现不同形式的应力作用对丁腈橡胶的性能和储存寿命影响很大;郑亮[7]研究了原油对丁腈橡胶密封件性能的影响,发现丁腈橡胶在原油中的老化以分子链交联反应为主,老化具有温度敏感性,高含水率的原油对丁腈橡胶密封件的性能存在极大的负面影响;Zhao等[8]研究了丁腈橡胶在高温作用下分别在空气与氮气氛围中老化过程中的连续应力松弛特征,发现只有在空气中才会出现应力增加“反弹”现象,这是因为丁腈橡胶热氧老化交联反应大于断链反应所致。但这些或是仅进行单一因素下的加速老化实验,或是仅考察有限的性能指标,而作为常用的耐油型密封橡胶,丁腈橡胶在实际使用过程中受到诸多因素(热、氧、光、油介质、应力等)的共同作用,其老化机理及不同性能的演变规律都是有所不同的。
本文根据丁腈橡胶在变压器中的实际运行工况,设计了四种条件下的老化实验,分析对比了在这四种条件的多项性能变化规律及老化机理。
1 实验部分
1.1 材料与仪器
丁腈混炼胶;25#变压器油。
ZG-50型平板硫化机;DHG-9030(A)型鼓风干燥箱;AGS-J型万能材料试验机;邵氏硬度计;DSC822E型差示扫描量热仪。
1.2 实验方法
丁腈混炼胶用平板硫化机进行硫化,硫化条件为175 ℃×10 MPa×10 min。硫化成型的试片尺寸140 mm×140 mm×2 mm。用橡胶冲片机裁成Ⅱ型哑铃试样(用于测量拉伸强度及断裂伸长率);2 cm×2 cm正方形试样(用于测量硬度及压缩永久变形率变化)。
考虑到丁腈橡胶的实际使用温度与加速老化的需要,实验温度选择70 ℃,实验分为四个部分同时进行:①70 ℃热空气老化:将试样直接置于70 ℃的烘箱中进行老化;②70 ℃热空气压缩老化:将试样放入夹具中,拧紧夹具,保证试样25%的压缩率,置于70 ℃的烘箱中进行老化;③70 ℃热油老化:将试样浸入装有25#变压器油的不锈钢容器中,盖好盖子,置于70 ℃的烘箱中进行老化;④70 ℃热油压缩老化:将试样放入夹具中,拧紧夹具,保证试样25%的压缩率,然后整体浸入装有变压器油的不锈钢容器中,盖好盖子,置于70 ℃的烘箱中进行老化。分别在老化后的第2,4,7,14,21,28,35,42,56…d取样测试。
1.3 性能测试
1.3.1 拉伸强度与断裂伸长率测定 按照GB/T 528—2009《硫化橡胶或热塑性橡胶拉伸应力应变性能的测定》测定,拉伸速度500 mm/min。
1.3.2 硬度性能测试 按GB/T 531.1—2008《硫化橡胶或热塑性橡胶压入硬度试验方法第一部分:邵氏硬度计法(邵尔硬度)》测定。
1.3.3 压缩永久变形率测定 按GB/T 7759—1996《硫化橡胶、热塑性橡胶常温、高温和低温下压缩永久变形测定》执行(采用叠加试样)。
1.4 Tg测试
采用扫描量热仪对不同老化阶段的丁腈橡胶试样进行测试,气氛为氮气,升温速率为10 ℃/min。
2 结果与讨论
2.1 70 ℃不同条件下老化时间对丁腈橡胶硬度的影响
选取2015年1月—2017年12月年我院收治的60例病情好转的2型糖尿病患者作为研究对象。将其随机分成观察组和对照组。观察组30例进行延续性护理,对照组30例进行常规护理,两组患者均进行为期3个月的相应护理。观察组中,男性患者12例,女性患者18例,平均年龄为(59.8±3.9)岁。本组患者的病程在1~16年,平均病程为(4.7±0.8)年。对照组中,男性患者17例,女性患者13例,平均年龄为(60.5±4.3)岁。本组患者的病程在1~17年,平均病程为(4.9±0.6)年。两组患者病情等一般资料比较,差异无统计学意义(P>0.05),具有可比性。
图1反映了丁腈橡胶在70 ℃不同老化条件下硬度随时间的变化情况。
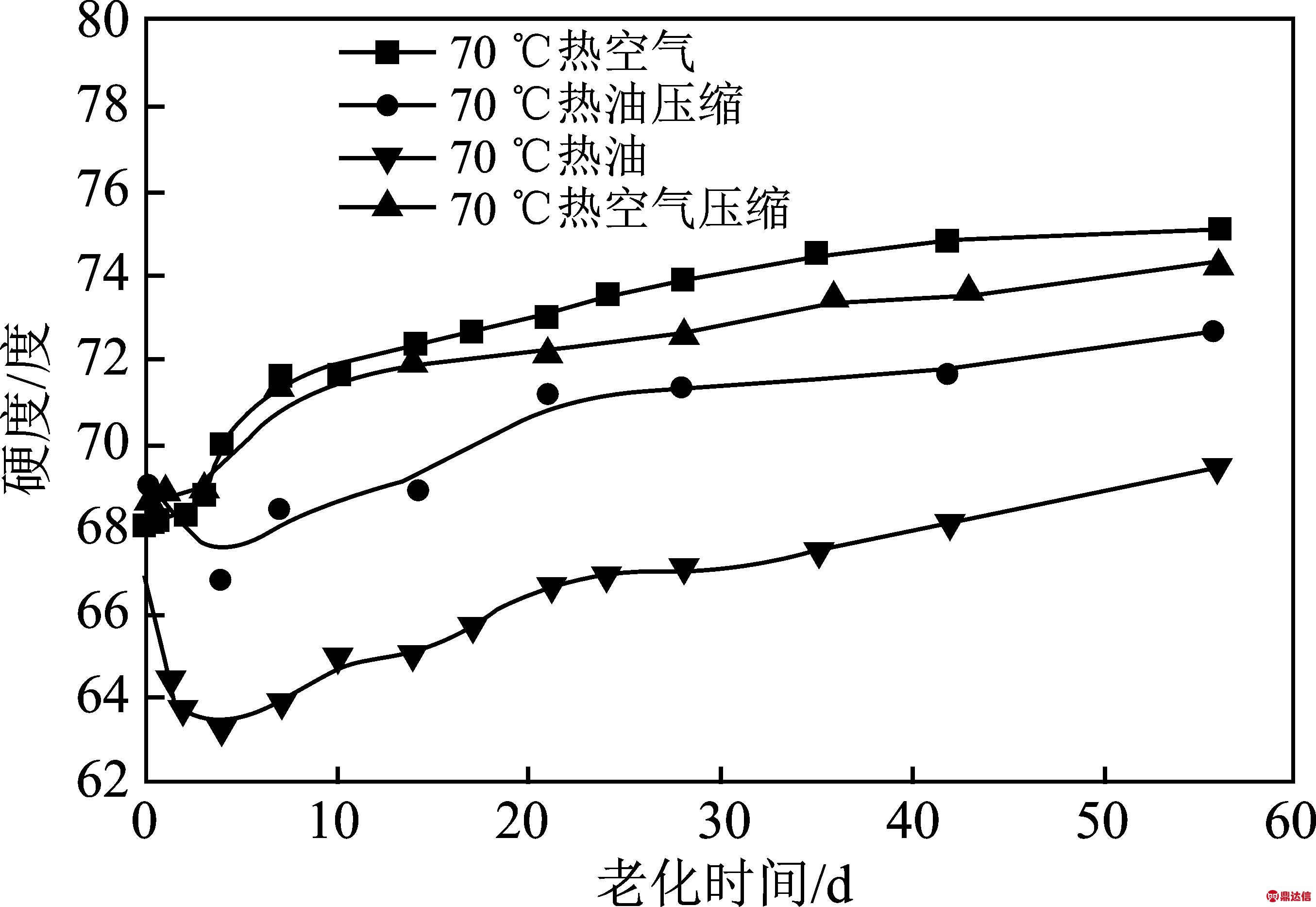
图1 70 ℃四种条件下丁腈橡胶硬度变化
Fig.1 Hardness of NBR during 70 ℃ ageing under four conditions
由图1可知,70 ℃热空气条件与70 ℃热空气压缩条件下呈现出相似的硬度变化趋势,在老化的前几天(0~4 d)硬度变化幅度较小,随着老化时间的增加,硬度逐渐增加,且在(4~10 d)硬度增加速度较快,然后随着老化时间的延长,硬度的增加速度逐渐减缓。同时,从第10 d开始,70 ℃热空气压缩条件下相比于70 ℃热空气条件下,丁腈橡胶的硬度整体偏低。
丁腈橡胶中存在不饱和的碳碳双键,在高温和氧作用下,容易造成橡胶分子链反应生成自由基,使得橡胶分子主链断裂,导致硬度下降。同时,在自由基的作用下,新的交联反应继续进行,交联密度的增加带来了橡胶硬度的增加。橡胶的老化是分子链的断裂和交联反应共同作用的结果[5]。橡胶硬度随老化时间的增加而持续增加,说明丁腈橡胶的老化是以交联反应为主的。施加的压缩应力大大约束了分子链的各种松弛行为,降低了分子链的断裂活化能,从而使分子链更易发生断裂,产生更多的自由基,链降解反应加剧[6],导致压缩状态下丁腈橡胶表现出相对较低的硬度。
70 ℃热油条件与70 ℃热油压缩条件下丁腈橡胶的硬度变化趋势也基本一致,均表现为在老化初期(0~5 d)硬度迅速下降(由68.5度分别降至63.2度与66.8度),然后随着老化时间的推移,丁腈橡胶的硬度开始逐渐上升,且上升速率逐渐减缓。在老化的中后期(5~56 d)这两种条件下丁腈橡胶的硬度变化情况基本一致,但70 ℃热油条件下丁腈橡胶的硬度整体上低于70 ℃热油压缩条件下的硬度。同时,在整个老化阶段有油条件(70 ℃热油与70 ℃热油压缩)下丁腈橡胶的硬度均低于无油条件(70 ℃热空气与70 ℃热空气压缩)下丁腈橡胶的硬度。
当橡胶材料浸泡于油介质中时会吸入油分子,由于溶胀作用,使橡胶的体积胀大,弹性减小,橡胶变软,也就是硬度下降。当试样受到压缩应力作用时,虽然压缩应力使橡胶硬度降低,但显然,变压器油对橡胶的溶胀作用对橡胶的硬度影响更大,橡胶安装在夹具中减少了油的吸入,所以热油压缩条件下,硬度下降较慢。达到溶胀平衡后(第4 d),橡胶的硬度随着老化时间的延长逐渐开始增加。
2.2 70 ℃不同条件下老化时间对丁腈橡胶拉伸强度与断裂伸长率的影响
图2表示丁腈橡胶在这四种条件下断裂伸长率随时间的变化情况。
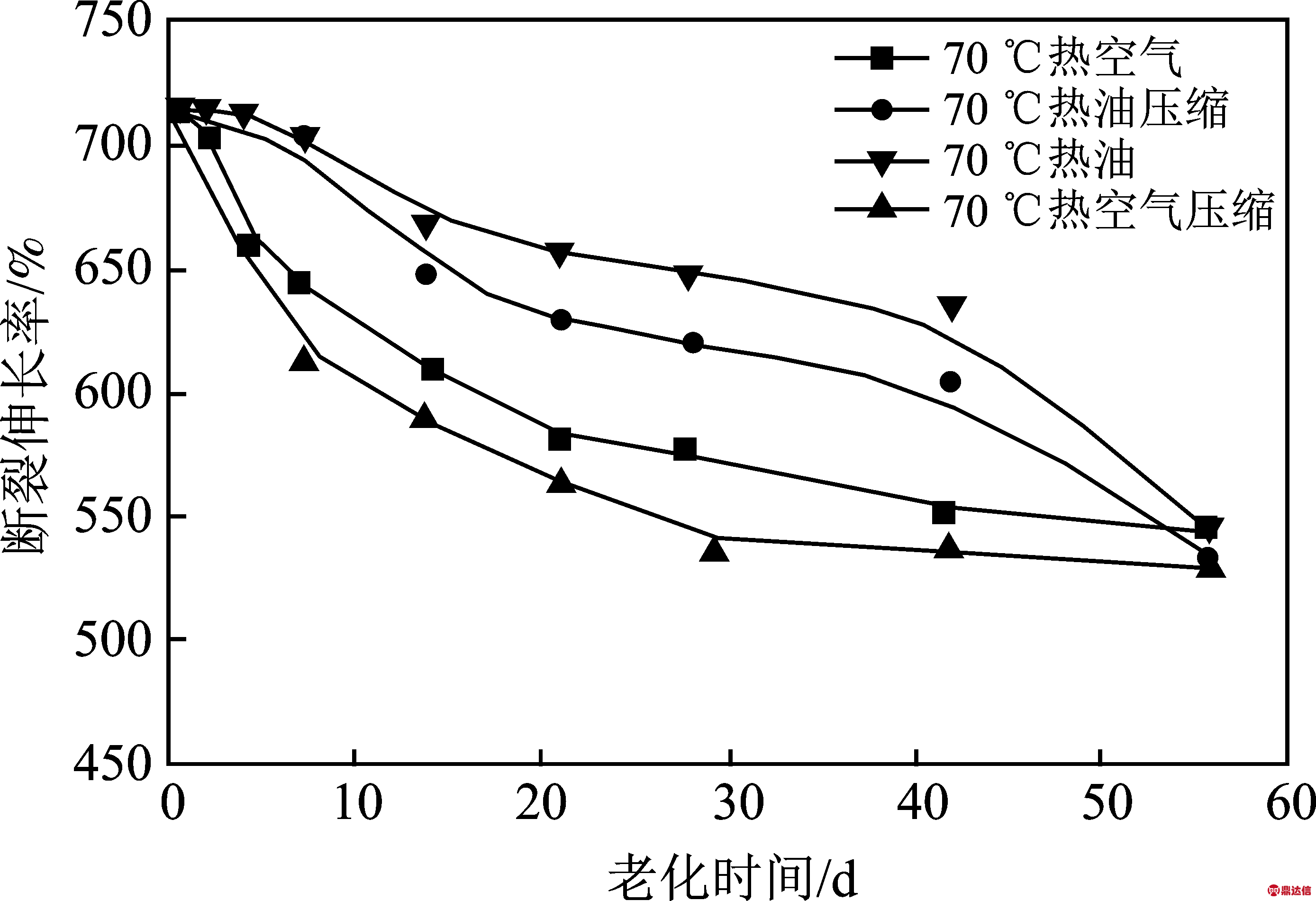
图2 70 ℃四种条件下丁腈橡胶断裂伸长率变化
Fig.2 Tensile strength of NBR during 70 ℃ ageing under four conditions
由图2可知,无油条件下,丁腈橡胶断裂伸长率表现出相同的变化趋势,均是随老化时间的延长逐渐降低,且降低速度逐渐减缓;而有油条件下的变化有所不同,在35 d前断裂伸长率表现出与无油条件相同的趋势,然后又开始以较快的速度降低,到第56 d断裂伸长率基本上与无油条件下相同,且在第56 d前断裂伸长率都保持70 ℃热油>70 ℃热油压缩>70 ℃热空气>70 ℃热空气压缩。
丁腈橡胶浸泡在变压器油中隔绝了空气,在一定程度上抑制了橡胶的热氧老化断链反应,所以有油条件下的断裂伸长率普遍高于无油条件,但在高温的作用下交联反应速度加快,过多的交联点导致橡胶的断裂伸长率急剧降低。
老化过程中,施加的压缩应力作用一方面使分子链发生取向,约束了分子链的松弛行为,另一方面加速了分子链断链反应速率。所以,在整个老化阶段,压缩条件下的断裂伸长率均低于未压缩条件。
图3反应了丁腈橡胶这四种条件下拉伸强度随时间的变化规律。
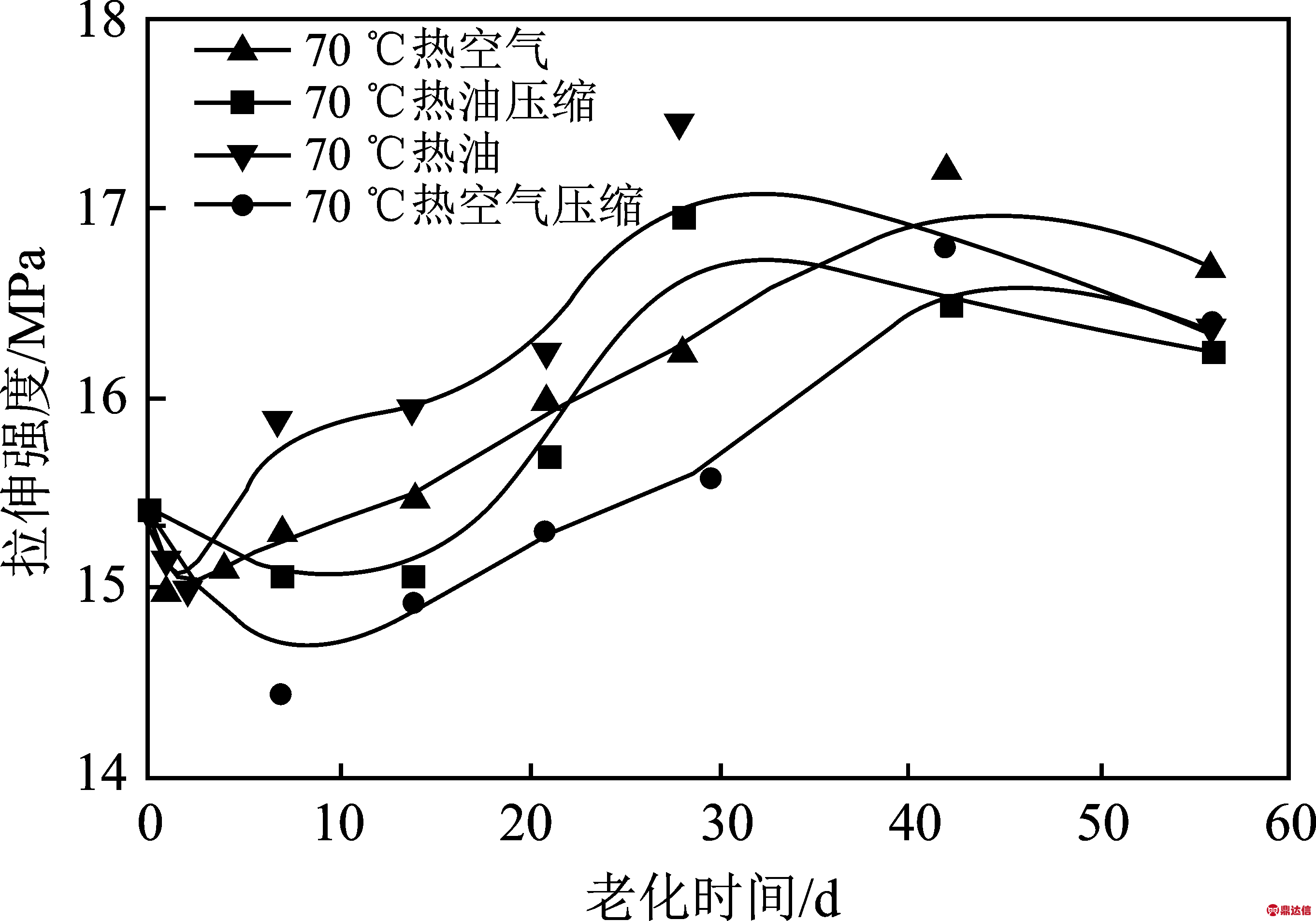
图3 70 ℃四种条件下丁腈橡胶拉伸强度变化
Fig.3 Elongation at break of NBR during 70 ℃ ageing under four conditions
由图3可知,四种条件下丁腈橡胶的拉伸强度都是呈现出先下降然后上升最后又下降的趋势,但具体来说又有一些区别。压缩状态下(70 ℃热空气压缩与70 ℃热油压缩)在老化的前几天(0~7 d)拉伸强度先降低(分别降至14.43 MPa与15.04 MPa)然后逐渐上升,分别到第42 d与第28 d上升到最大值(16.8 MPa、16.9 MPa),然后逐渐下降。而未压缩状态下(70 ℃热空气与70 ℃热油),拉伸强度在老化初期(0~4 d)有小幅度下降(分别降至15 MPa与15.22 MPa)然后保持上升状态,分别在第42 d与第28 d上升到最大值(17.2 MPa、17.47 MPa),然后逐渐下降。
有油条件(70 ℃热油与70 ℃热油压缩)下拉伸强度变化的转折点(到达最大值的时间)基本相同(第28 d),无油条件(70 ℃热空气与70 ℃热空气压缩)下,拉伸强度变化的转折点也基本相同(第42 d)。
拉伸强度的变化反应橡胶在老化过程中交联和断链共同作用的结果,老化初期,随着交联密度的增加,分子链间相对滑移的难度也逐渐增加,提高了丁腈橡胶的抗拉伸能力,导致拉伸强度上升。但随着老化的继续进行,过多的交联点反而不利于其抵抗拉伸[9],加上热氧老化导致橡胶内部分子链断链反应的加剧,拉伸强度逐渐降低。
当橡胶浸泡在变压器油中时,由于隔绝了空气,抑制了橡胶的断链反应,在高温作用下,分子链的交联反应速率有所增加,导致在有油条件下交联密度增加更快,从而使拉伸强度增加更快,且出现转折的时间更早。在老化的后期表现出比无油条件下更低的拉伸强度。这与前面断裂伸长率的变化规律是相吻合的。
四种条件下老化初期拉伸强度均出现不同程度的下降现象,结合之前提到的硬度在这段时间变化也较为缓慢,说明该丁腈橡胶在老化初期断链反应较为明显。同时,施加的压缩应力一方面使分子链发生取向,约束了分子链的松弛行为,另一方面加速了橡胶的断链反应,故在老化初期,四种条件下的丁腈橡胶拉伸强度出现不同程度降低现象,而压缩状态下该现象更为明显,且在老化的中后期拉伸强度均低于未压缩条件下。
2.3 70 ℃不同条件下老化对丁腈橡胶压缩永久变形率的影响
图4反映了丁腈橡胶在70 ℃不同老化条件下压缩永久变形率随时间的变化情况。
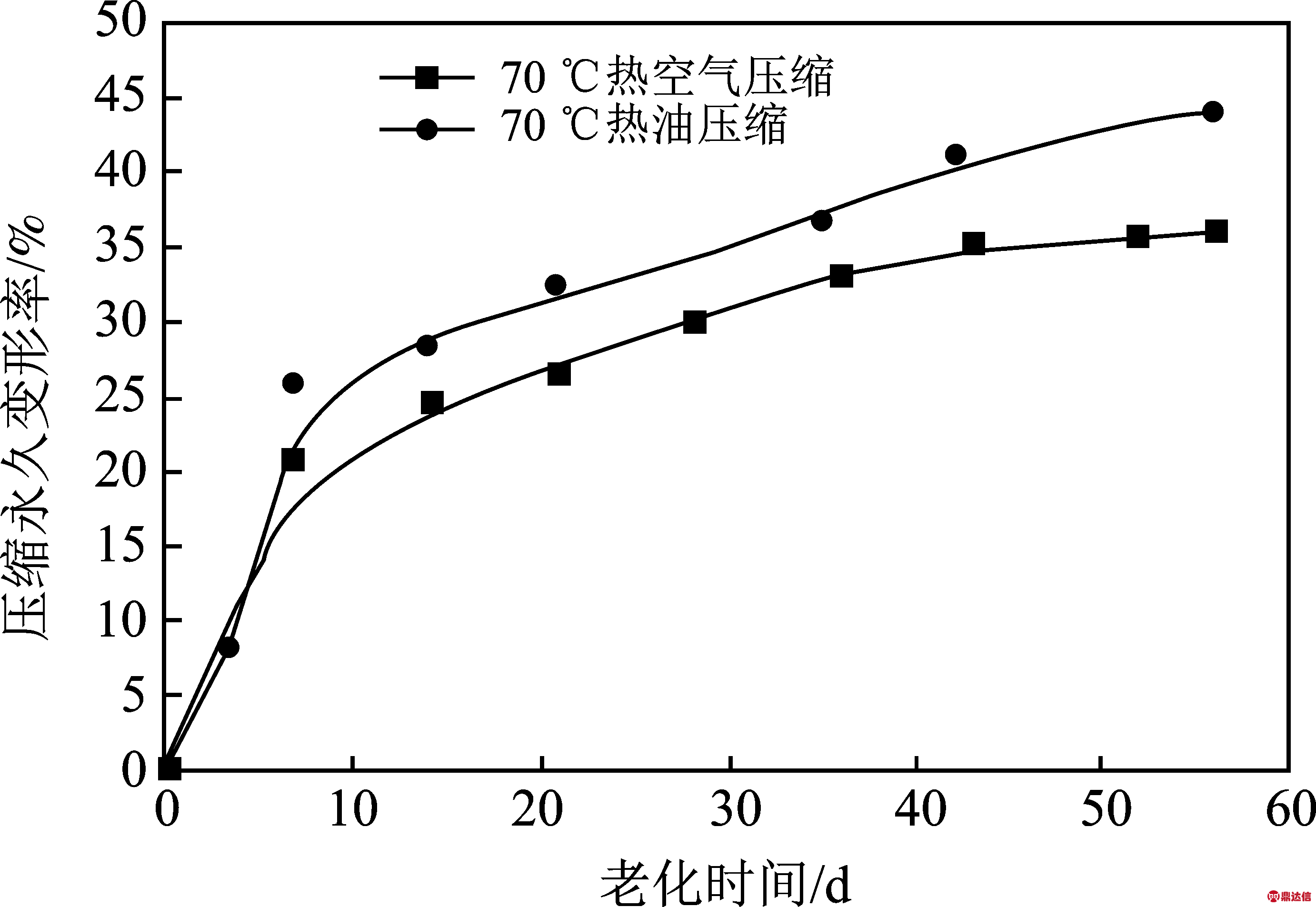
图4 70 ℃有油与无油条件下丁腈橡胶压缩永久变形率变化
Fig.4 Compression set of NBR durin 70 ℃ ageing in oil and in air
由图4可知,70 ℃热油压缩条件与70 ℃热空气压缩条件下,丁腈橡胶的压缩永久变形率变化趋势基本相同,都是在老化初期(0~10 d)压缩永久变形率迅速增加(分别增加至25%、20%),然后在接下来的时间里(10~56 d)随着老化时间的延长,压缩永久变形率逐渐增加,但增加速率逐渐变缓。两种条件下,丁腈橡胶的压缩永久变形率在前7 d基本保持一致,从第7 d开始,70 ℃热油压缩条件下的压缩永久变形率在接下来的老化时间内整体上均高于70 ℃热空气压缩条件下的压缩永久变形率。
产生这种差异的原因是,溶胀作用降低了丁腈橡胶交联网络结构的致密性,使分子链的自由度增加,弹性降低,压缩力消失后恢复到原来状态的能力也随之降低。
2.4 Tg分析
表1为四种条件下老化28 d和56 d丁腈橡胶的Tg变化。
表1 70 ℃四种条件下丁腈橡胶Tg随老化时间的变化
Table 1 Tg of NBR during 70 ℃ ageing under four conditions
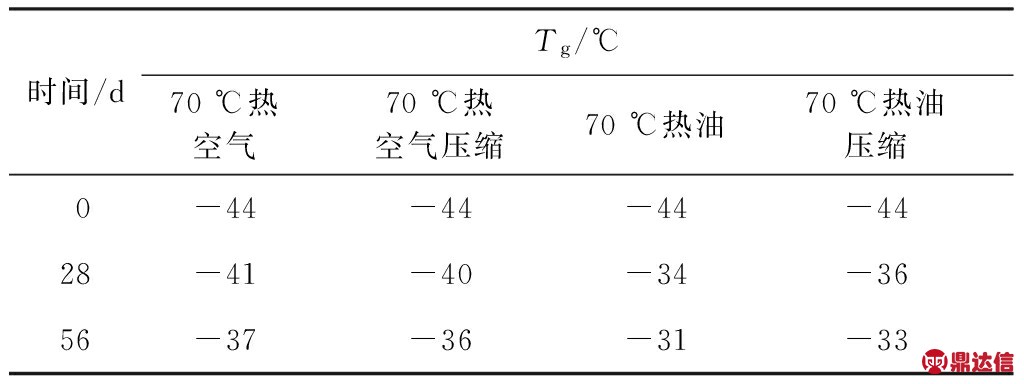
由表1可知,未老化的丁腈橡胶Tg最低,随着老化的进行,Tg都在增加。这是因为橡胶的老化是分子链断链反应与交联反应共同作用的结果,占优势的交联反应对分子链的运动起约束作用,从而使Tg逐渐增加。
另外,不同条件下Tg的变化速度是不同的。有油条件下,Tg增加迅速,到第56 d分别增加至-31 ℃(热油未压缩)和-33 ℃(热油压缩),而无油条件下,Tg仅增加至-37 ℃(热空气未压缩)与-36 ℃(热空气压缩)。这是因为随着老化的持续进行,变压器油进入橡胶后,分子链间的自由空间被油分子所挤占,分子链段之间的相对运动趋势减弱,导致Tg偏大[10]。
热空气压缩条件下的Tg变化要大于未压缩条件,这是因为施加的压缩应力挤出了橡胶分子链的“自由体积”,从而导致Tg偏大;而在有油条件下,热油压缩条件丁腈橡胶的Tg反而低于热油条件下的Tg,这是因为压缩应力减少了油的浸入,使得变压器油对丁腈橡胶Tg的影响相对偏小,虽然压缩应力会导致Tg偏大,但显然油对Tg的影响更大,结果就是热油压缩条件下的Tg变化要小于热油未压缩条件下。
3 结论
橡胶各项性能的总体变化趋势说明该丁腈橡胶的老化是以分子链间交联反应为主,但在老化初期断链反应占有较大比重。压缩应力与油介质同时存在时,对橡胶的性能影响是复杂的,一方面施加的压缩应力会加速橡胶内部分子链的断链反应;另一方面减少了橡胶分子链的活动空间,阻碍了油的浸入,降低了溶胀作用对橡胶性能的影响。丁腈橡胶浸泡在变压器油中由于隔绝了空气,降低了热氧老化断链反应的速率,但在高温作用下,交联反应速率相对无油条件下有所增加。到老化后期,急剧增加的交联点会使这些性能迅速降低。
不同外界条件下,丁腈橡胶的性能变化趋势是不尽相同的,所以对丁腈橡胶寿命的预测要综合橡胶在模拟工作环境下的性能变化趋势与性能需求选择合适的性能指标。