摘 要:导光板模具是加工导光板的核心部件,微结构阵列孔的加工精度对导光板模具至关重要。通过精密撞点机床在导光板模具钢上加工微结构阵列孔和在白光干涉仪下检测微结构阵列孔的孔径和圆心距,分析检测数据找出影响导光板模具微结构阵列孔的加工精度的因素。利用激光干涉仪的线性测长模块验证精密撞点机床的定位和重复定位对微结构阵列孔的中心距的影响,利用激光干涉仪的动态测量模块验证微振动对导光板模具加工的影响。通过实验,找出影响导光板模具微结构阵列孔的加工精度因素并提出提高加工精度的方法。
关键词:导光板;微结构阵列孔;加工;检测
1 引言
导光板在智能手机背光模组中起着关键的作用,其将LED点光源转化成面光源[1-3]。导光板的加工精度和质量将直接影响智能手机显示屏的显示效果。导光板快速和高效的加工主要通过导光板模具复制加工,因此导光板模具的加工精度将直接决定导光板的质量[5]。导光板模具微结构阵列孔的加工属于精密加工,其对加工环境有严格的要求,同时导光板模具微结构阵列孔的加工和检测密不可分,高精度的加工设备离不开高精度的检测仪器,因为通过对工件的检测才能得出加工的精度和分析影响加工的因素。本研究中,导光板模具通过精密撞点机加工,其加工精度通过高精度白光干涉仪检测验证[3]。导光板模具上加工的微结构阵列孔孔径约为38μm,其加工过程难控制,对其精度影响的因素也很多,如加工机床的微振动、机床的定位精度、导光板模具在调节平台上的斜度等[5]。通过高精度白光干涉仪对加工的导光板模具微结构阵列孔进行孔径和孔心距的检测,并对检测结果分析,研究对加工精度影响的因素,最终实现提高加工精度的目标,从而复制加工出高精度和高质量的导光板。
2 导光板模具微结构阵列孔的加工
精密撞点机是三轴精密机床,X轴和Y轴为行程300mm的高精度线性导轨并由直线电机驱动,Z轴上装有精密手动调节运动平台,其上装有柔性铰链刀架,刀架上装有金刚石撞点刀具,如图1所示。压电陶瓷驱动撞点刀具,且其最大运动行程为40μm。导光板模具是一种模具钢,其规格为135mm*75mm*20mm,如图2所示。可利用精密撞点机床在模具钢上加工出各种规则和不规则形状的微结构阵列孔[5]。
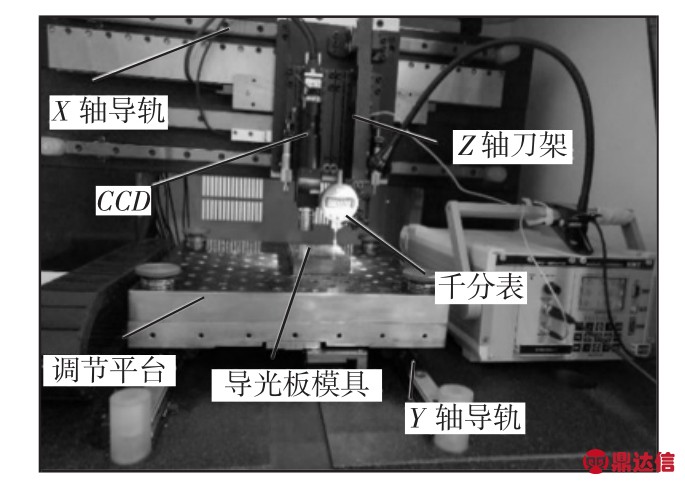
图1 精密撞点机导光板模具调平
Fig.1 Leveling of Guide Plate Mold on Precision Hitting Machine
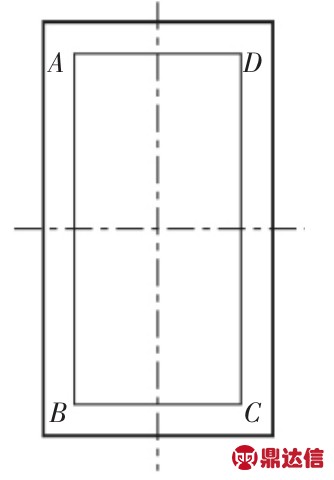
图2 导光板模具
Fig.2 Light Guide Plate
导光板模具放在机床调节平台上,要求斜度调节满足在2μm内。因为在导光板模具上加工的微结构孔,孔径和深度都特别小,一般不会超过50μm。如果斜度调节达不到要求,会出现微结构阵列孔孔径超差。更严重的情况,若导光板模具上某点太高可能撞刀并损毁刀具,某点太低刀具Z向进给接触不到导光板模具加工面,加工不出微结构阵列孔,所以如果斜度调节误差不在2μm内,将直接影响导光板模具的加工精度。如图1和图2所示,在调平时,高精度千分表吸附在机床Z轴上接触在导光板模具A点,机床Y轴负向运动,千分表探针接触在导光板模具B点,机床X轴正向运动,探针从导光板模具B点运动到C点,Y轴正向运动探针从C点运动到D点,X轴负向运动探针从D点运动到A点。在机床X、Y轴的联动下带动千分表在导光板模具上从AB-C-D-A走一个循环,高精度千分表显示调节平台和导光板模具的综合高度。在调节导光板模具加工平台时,以A点为基准,调节B点处的调节平台手拧装置使B点导光板模具局部升高或者降低;以B点为基准,调节C点处的调节平台手拧装置使C点导光板模具局部升高或者降低。以此类推,前点为基准,调节其随后点处的平台调节手拧装置,调节经过A-B-C-D-A的一个循环后,如若不满足误差在2μm内的要求则继续多次重复调节。
导光板模具斜度调平之后,拆卸下高精度千分表,即可进行对刀加工。通过改变加工程序中压电陶瓷脉冲的输入数值控制微结构撞点的孔径大小,在控制程序中设定微结构孔径大小为38μm、水平方向(X向)和竖直方向(Y向)孔中心距均为100μm。
3 导光板模具微结构阵列孔的检测
本次检测采用的布鲁克Contour GT-X5型号白光干涉仪[4],因受白光干涉仪镜头视野的影响,只能测量6个微结构阵列孔和其X向、Y向的孔心距,但对这些孔径和孔心距多次测量求均值也能较好反映机床加工导光板模具微结构阵列孔的加工精度。为欲在白光干涉仪下测出微结构阵列孔的理论数据,即阵列孔径D1-D6、水平方向的孔心距X1-X4、竖直方向的孔心距Y1-Y3,如图3所示。
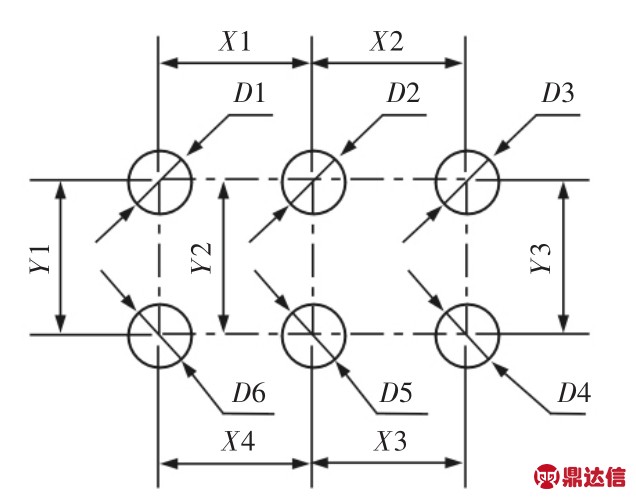
图3 导光板模具理论测量数据
Fig.3 Theoretical Measurement Data of Light Guide Plate Mold
3.1 微结构阵列孔径的测量
白光干涉仪下的微结构孔径测量,如图4(a)所示。从X向(水平方向)和Y向(竖直方向)测量的R和M之间的距离就是导光板模具上微结构孔径,如图4(b)所示。测量的X向孔径37.6108μm,测量的Y向孔径37.3020μm,如图4(c)所示。如表1中,从三次测量的结果中可知6个微结构孔(D1-D6)孔径大小,并分别对其求平均值得出微结构孔平均孔径。
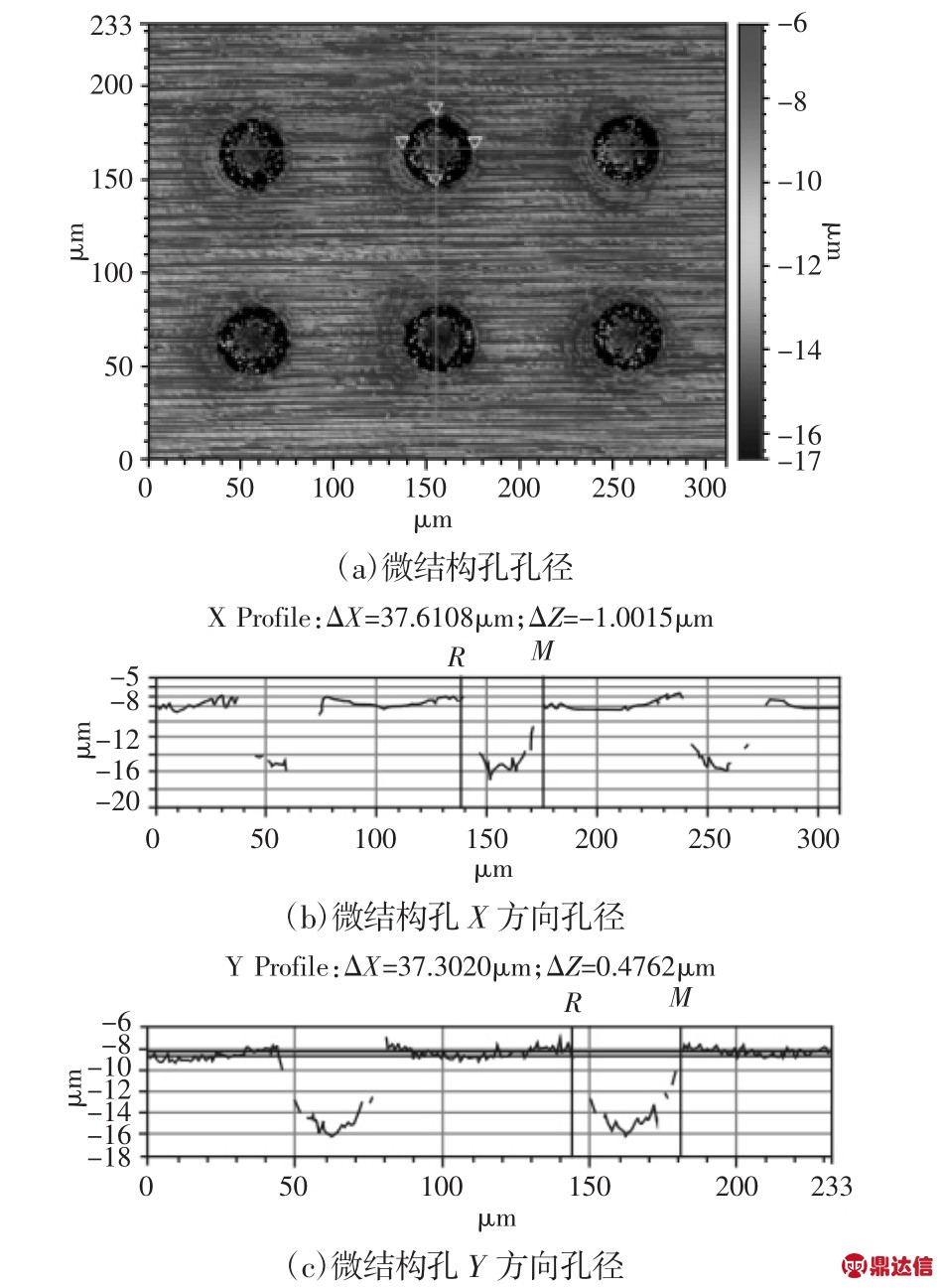
图4 微结构阵列孔孔径测量
Fig.4 Diameter Measurement of Microstructure Array Holes
表1 微结构阵列孔径测量数据
Tab.1 Measurement Data of Diameter of Microstructure Array Holes
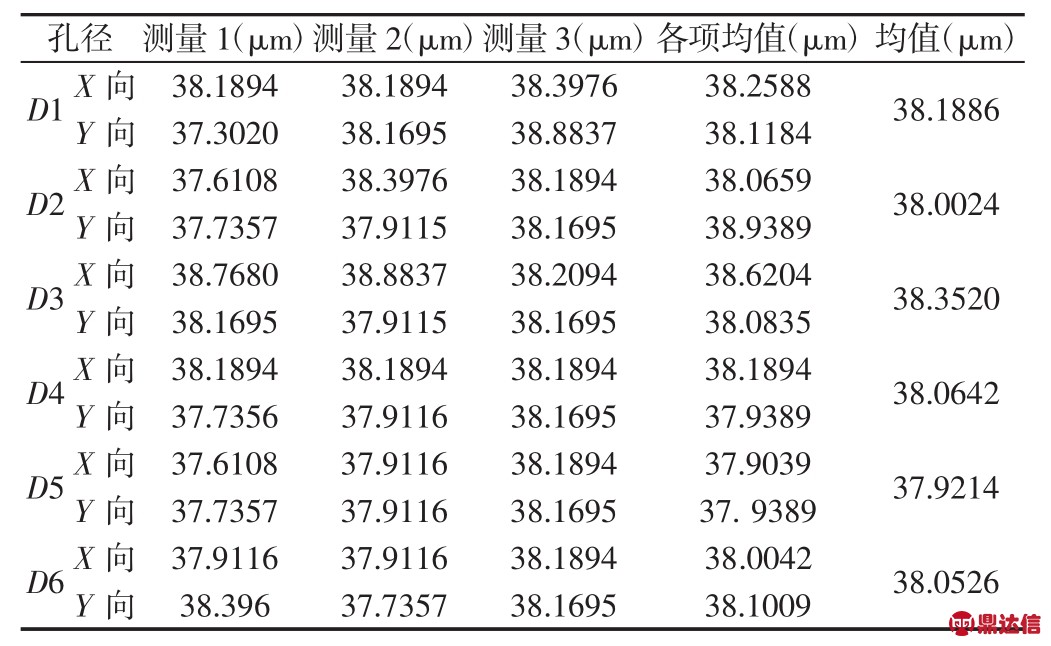
理论上微结构孔径为38μm,但在白光干涉仪的实际测量中微结构阵列孔孔径最大值为38.3520μm,最小值为37.9214μm,满足加工精度在0.5μm内的要求。虽然满足要求,但仍要研究在微结构阵列孔加工过程中引起误差的因素。通过多次实验和分析,机床的微振动和导光板模具在调节平台上的斜度是微结构阵列孔径误差的两大主要因素,后续实验进行了验证。
3.2 微结构阵列孔心距的测量
如图5所示,图5(a)中显示分别从X向(水平方向)和Y向(竖直方向)测量的微结构阵列孔的孔心距X1和Y1,R和M之间的距离就是导光板模具上微结构孔的孔心距,图5(b)中测量的X向圆心距X1为100.1254μm,图5(c)中测量的Y向圆心距Y1为100.2096μm。如表2中,从三次测量的结果中可知6个微结构孔的水平方向孔心距X1~X4,竖直方向的孔心距Y1~Y3,分别对其求均值得水平方向和竖直方向的孔心距。
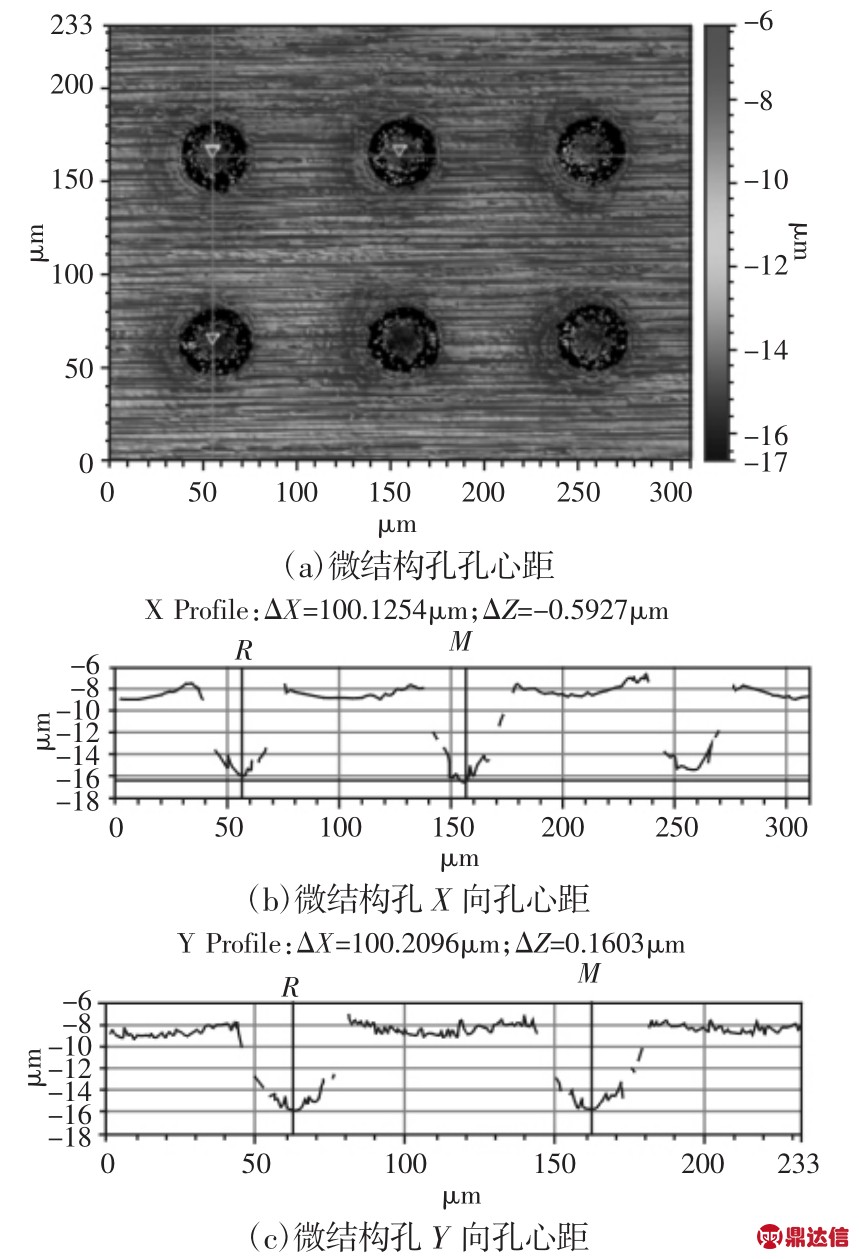
图5 微结构阵列孔心距测量
Fig.5 Measurement of Center Distance of Microstructure Array Holes
表2 微结构阵列孔心距测量数据
Tab.2 Measurement Data of Center Distance of Microstructural Array Holes
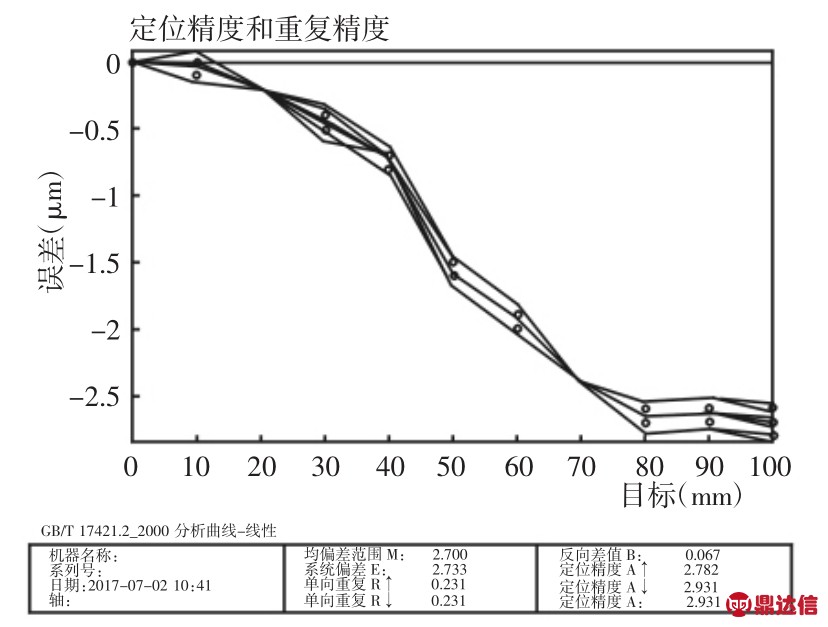
理论上微结构孔心距为100μm,但在白光干涉仪下的实际测量中微结构阵列孔心距最大值为100.6812μm,最小值为100.1102μm,因要求的孔心距精度在0.5μm内,通过多次实验验证机床导轨定位精度不满足要求,引起微结构阵列孔心距的误差偏大,后续实验进行了验证。
4 机床定位精度对微结构阵列孔心距的影响
实验采用的雷尼绍XL-80激光干涉仪,其即可以通过线性测长模块测机床导轨的定位精度和重复定位精度也可以通过动态测量模块测量机床的微振动。在机床的调节平台上固定反光镜并使其随机床Y轴导轨移动,干涉镜放在大理石平台上保持静止不动[7],如图6所示。将激光干涉仪三角支架升至所需高度,镭射头放置在支架上,调节光路至镭射头五颗灯全亮状态,打开机床上位机,运行运动程序,打开激光干涉仪软件线性测长模块进行定位精度和重复定位精度的测量。经激光干涉仪对机床Y轴的多次测量,如图7所示。从其软件中经过数据分析得出Y轴的定位精度为2.931μm和重复定位精度为0.231μm。因机床的定位精度是衡量机床轴运动精度的关键指标,由Y轴定位精度数据可知,机床的Y轴定位精度远大于白光干涉仪下测的Y轴方向上孔心距精度。因此机床导轨的定位精度不够高引起导光板模具微结构阵列孔中心距误差偏大。造成机床定位精度不高一般是导轨本身的结构设计或控制系统调试补偿不理想两方面的原因。为解决此问题,我们利用激光干涉仪对导轨进行定位精度多次误差补偿,使机床导轨的定位精度和重复定位精度提高至满足加工要求。
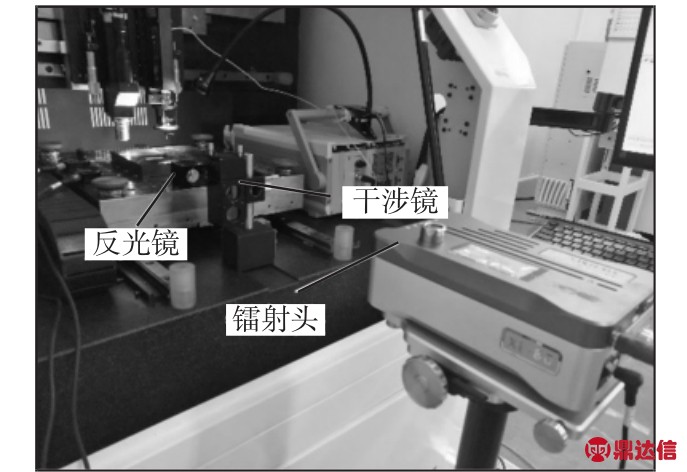
图6 定位精度测量和动态测量
Fig.6 Positioning Accuracy Measurement and Dynamic Measurement
5 微振动对导光板模具加工的影响
微振动一般指低频振动,机床振动不可避免,微振动更是不可避免[9]。尽管精密机床经过隔振处理,但在加工过程中,机床微振动对加工精度的影响还是很大,将直接影响导光板模具微结构阵列孔径误差。在测试振动时,光路调节,如图6所示。但机床Y轴导轨保持不动。经过激光干涉仪的动态测量模块分别测量了10Hz、25Hz、50Hz、100Hz、250Hz、500Hz、1KHz等不同频率下的振动位移图,在动态测量模块中设置预触发时间5s和触发后时间30s,经过不同频率下多次测量数据对比,随着频率的增大,振动位移(幅值)有降低的趋势,验证了低频振动对机床加工精度的影响。通过不同频率下的振动位移数据对比,振动位移最大值在10Hz左右,通过图8可知,机床在没有加工只打开控制系统的条件下,软件设置触发后,20.4s出现振动最大值0.2078μm,22.9s时出现振动位移最小值-0.8259μm。通过图9可知,机床在加工条件下,在27.8s时出现振动位移最大值1.2574μm,在7.5s时得到振动位移最小值(-0.1249)μm。通过多次对比发现导光板模具加工的过程中,微振动的振动位移加大,但因加工的微结构阵列孔径较小,因此对导光板模具微结构阵列孔径精度会有影响,应严格控制机床的微振动。
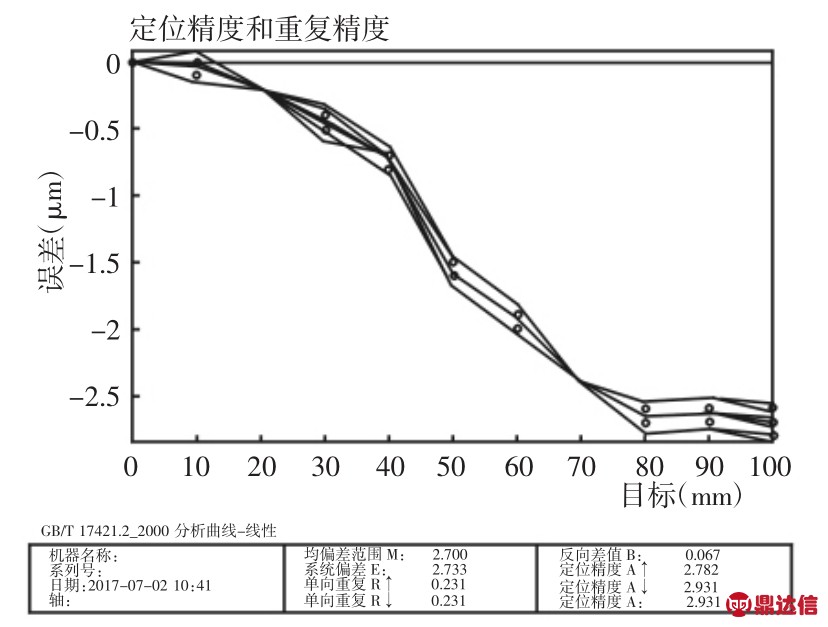
图7 Y轴定位精度测量数据
Fig.7 Positioning Accuracy Measurement Data of Y Axis
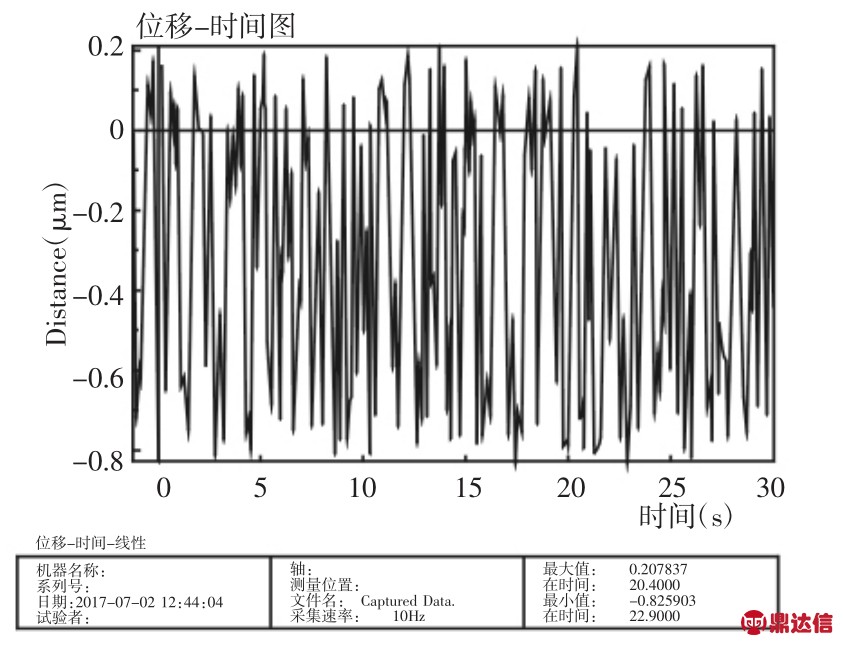
图8 机床加工前加工平台的振动
Fig.8 The Vibration of Processing Platform before Machining
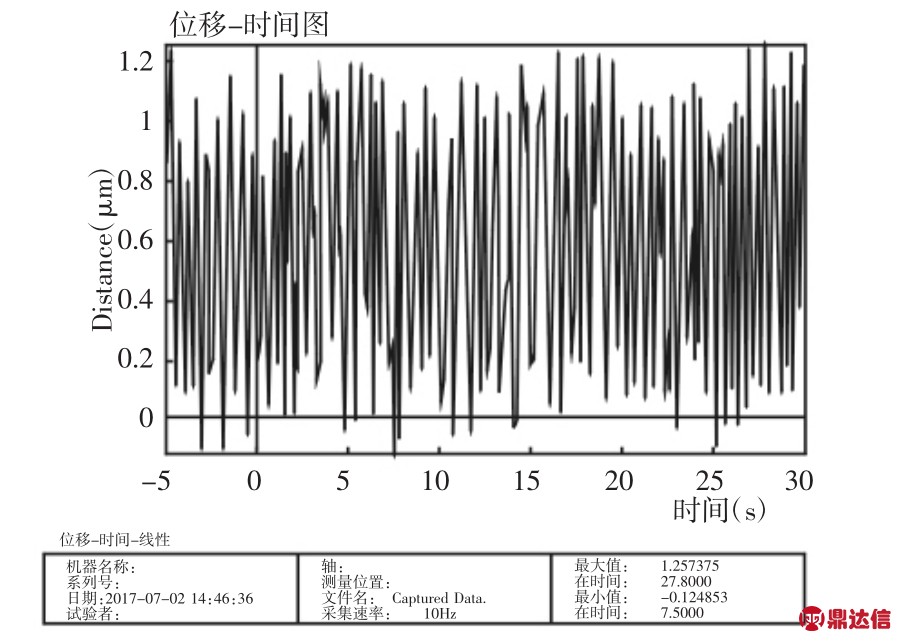
图9 机床加工中加工平台的振动
Fig.9 The Vibration of Processing Platform when Machining
精密机床的本体结构设计中,将控制系统集成在大理石台下的支架中且大理石台没有气浮隔振系统,数控系统开机后对加工平台有明显的微振动影响,同时Z轴上的柔性铰链刀架在快速加工时也会产生微振动。
6 结论
通过精密撞点机加工导光板模具微结构阵列孔和在白光干涉仪下测量微结构阵列孔径、X向和Y向孔心距得出:(1)经过白光干涉仪检测,导光板模具微结构阵列孔径加工精度满足小于0.5μm误差范围内,但通过激光干涉仪的动态测量模块实验验证微振动对机床的加工精度有一定的影响,因导光板模具上微结构阵列孔径仅38μm,微结构阵列孔径易受机床的低频振动和环境噪音的影响。(2)Y轴上加工平台上导光板模具斜度的调节也是加工过程中的一个难点,受导光板模具钢加工精度和Y轴上调节平台结构限制,现有条件下导光板模具斜度误差只能调节在2μm范围内,如若能调成更高的精度,也会避免导光板模具在加工过程中出现加工的孔径超差现象。(3)经过白光干涉仪检测,导光板模具微结构孔的孔心距误差相对较大,出现这种情况微振动、机床的定位精度等都会对其造成影响,更重要的是机床的定位精度,但机床的本体结构设计已完成,无法更好优化机床结构的前提下,提高定位精度只能从数控系统中利用激光干涉仪多次进行定位精度和重复定位精度误差补偿,来达到提高导光板模具微结构阵列孔心距精度的要求。