摘 要:目前盾构管片模具主要采用传统的人工和激光跟踪测量技术进行检测,存在检测点位少,精度低等缺点,不能很好地指导管片模具的修复工作,直接影响到管片尺寸的生产精度,易造成盾构隧道管片破损、开裂及渗漏水等现象,为后期的运营埋下了安全隐患。宁波市轨道交通利用三维激光扫描技术对管片模具进行检测,通过理论分析、现场试验及数据分析,确定了点云数据的拼接方式、扫描分辨率、基准模型及模型对齐的方式,成功克服了现有的管片模具检测中存在的测量点位少、精度低等缺点,实现了对管片模具的全方位检测,大大提高了管片模具的检测精度。同时在参考现有规范及经验的基础上,制定出了盾构管片模具三维激光扫描检测标准,很好地指导了管片模具的修复工作,提高了盾构管片尺寸的生产精度,确保盾构隧道的施工质量。
关键词:盾构管片;模具;三维激光检测;点云数据;对齐方式;3D色谱偏差图;检测标准
引言
管片模具作为盾构管片生产的载体,其尺寸精度直接决定管片生产的尺寸精度[1],而提高管片尺寸的生产精度是减少成型隧道管片破损、渗漏等病害的前提。目前盾构管片模具检测主要有传统的人工检测和激光跟踪测量两种方法。传统的人工检测是利用千分尺、高度尺、样规在管片模具的特定位置分别对其内腔的宽度、高度、弧长进行检测[2],其缺陷是测量点位少,只能靠有限的几个点位来判断模具的整体变形情况,精度无法得到保证,且宽度和弧长的检测结果也只能反映出两侧模、端模之间的相对变形,无法直观地表达模具各个型面的绝对变形情况,不能很好地指导模具修复工作,直接影响到盾构管片尺寸的生产精度。激光跟踪测量系统是建立在激光干涉长度测量和角度精密测量基础上的极坐标测量系统,通过跟踪仪实时跟踪带有棱镜的跟踪球来确定跟踪球所在点的坐标。红外跟踪测量技术在进行管片模具检测时,其检测点位虽比传统的人工检测点位多,但仍不足以覆盖整个面,仅测出了各个型面的边线,然后通过边线拟合出整个面,仍然无法得出各个型面的变形情况。
由于三维激光扫描技术突破了传统的单点测量方法,为快速建立物体的三维影像模型提供了一种全新的技术手段,且三维激光扫描技术具有快速性、不接触性、实时、高密度、高精度,数字化、自动化等特性,已被广泛应用在测绘工程、结构测量、古建筑保护、灾害评估、机械设计与制造、数字城市等方面[3-20]。宁波市轨道交通首次将三维激光扫描技术引进到管片模具检测当中,成功地克服了现有的模具检测中存在的测量点位少、精度低等缺点,实现了对管片模具的全方位检测,大大提高了管片模具的检测精度,确保了管片尺寸的生产精度,同时也延长了模具的使用寿命,取得了良好的经济效益与社会效益。
1 工程概述
宁波市轨道交通盾构隧道采用带凹凸榫槽的通用环管片,管片外径6 200 mm,内径5 500 mm,环宽1 200 mm,每环由6块管片构成,其中含标准块3块(B1、B2、B3),三块夹角均为67.5°,邻接块2块(L1、L2),两块夹角均为68.75°,封顶块1块(K),夹角为20°,管片楔形角为20′37.59″,楔形量为37.2 mm,封顶块中间位置为管片环宽度最小处,宽度为1 181.4 mm;中间标准块(B3)的中间位置为管片环宽度最大处,宽度为1 218.6 mm。在管片拼装过程中,带凹凸榫槽的通用环管片对管片尺寸的精度要求比较高,不然很容易出现破损、开裂及渗漏,因此应加强对管片模具进行检测,提高其检测精度,以达到提高管片尺寸精度的目的。
2 三维激光检测关键技术
2.1 设备的选型
目前三维激光扫描仪根据不同行业、不同领域的应用需求不同,其种类比较多,三维激光扫描系统按照载体的不同,又可分为机载式、车载式、轨道式和便携移动型(有手持式,背包式,推车式)等;按激光发射器测距原理分为脉冲测距式、相位干涉式、立体相机和机构化光源技术(三角测量)等。
盾构管片是在生产车间进行生产,因其模具一般都比较笨重,最大一块模具(B3块)质量达5 t,尺寸为4 000 mm×1 600 mm×1 400 mm,内腔深度350 mm,所以模具检测场地一般就近选择在管片生产车间内,同时模具的检测精度要求非常高,达到0.1 mm级,因此在综合考虑管片模具的检测精度、尺寸大小、检测空间及检测环境等,最终选用MetraSCAN750TM手持式三维激光扫描仪。MetraSCAN750TM手持式三维激光扫描仪自带校准功能,包括C-Track(跟踪器)、MetraSCAN 3D(扫描仪)、C-Track校准棒、MetraSCAN 3D校准板、磁力定位标靶(贴片式定位标靶)、笔记本电脑及相关软件等,其中MetraSCAN 3D(扫描仪)配有一部635 nm的红色线激光闪光灯,C-Track(跟踪器)配有两个工业相机。见图1。
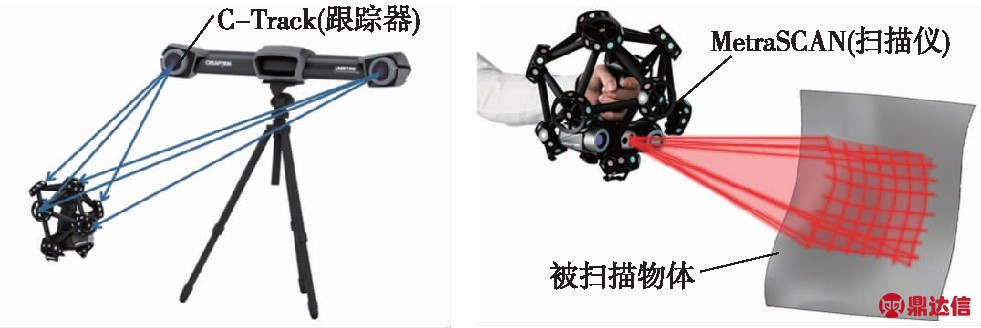
图1 MetraSCAN750TM三维扫描仪
MetraSCAN750TM手持式三维激光扫描仪主要参数如表1所示。
表1 MetraSCAN750TM三维扫描仪主要设备参数
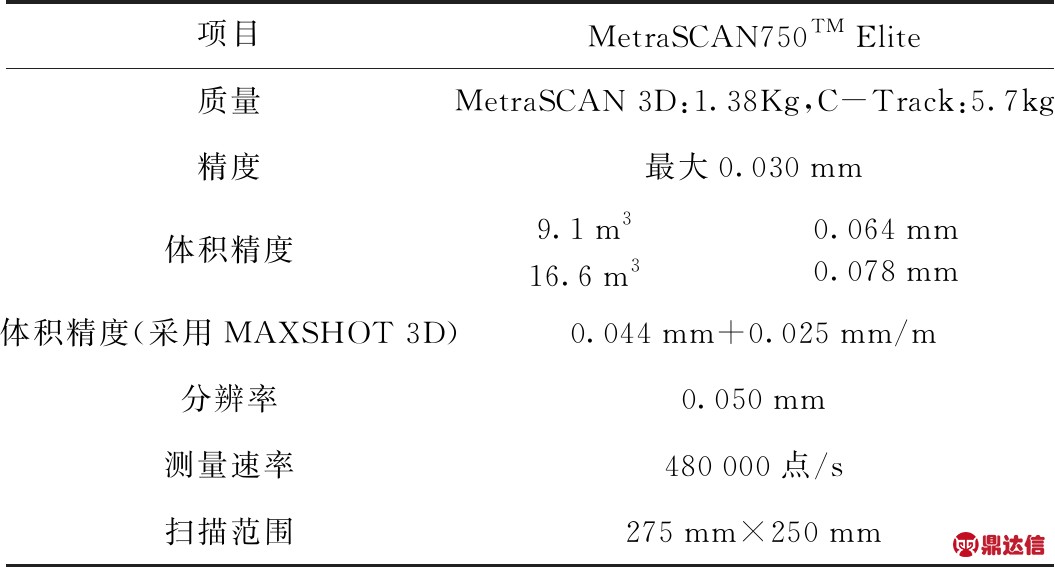
工作时将激光线照射到物体上,两个相机来捕捉这一瞬间的三维扫描数据,由于物体表面的曲率不同,光线照射在物体上会发生反射和折射,然后这些信息会通过第三方软件转换为3D图像。同时使用反光型定位标靶,与扫描软件配合使用,支持摄影测量和自校准技术。摄像头探测到的定位标点图案和扫描仪相同,通过三角测量,配套软件能够确定扫描仪(在空间中)的位置。
2.2 点云数据的拼接
三维激光扫描仪每个测站扫描的数据都是独立的自由坐标系统,数据处理时必须要将多次(测站)扫描得到的点云数据合并到一个统一坐标系进行拼接处理。目前点云拼接方式主要有双站方式、全局方式和绝对方式3种,其中双站方式和全局方式属于相对定位,测站间或区段间的衔接需要有搭接区域,如果测站或区段过多,存在着较大的误差传递,适合于中、小范围的扫描;绝对方式属于绝对定位,需提前布设导线网和调和高程控制网,测站间不需要搭接,适合于大、中范围的扫描。
C-track(跟踪器)跟踪检测的范围为1.5~4.2 m,管片模具平均长度约为3.4 m,其中最大一块长度为4 m。虽然都在检测范围之内,但由于各块模具中间弧度落差较大,C-track(跟踪器)检测视角受到干扰,无法一次捕捉到管片模具上所有的定位标靶。因此,需通过两次设站分别对定位标靶进行捕捉。由于只有两个测站,不存在误差传递的影响因素,采用双站方式实现对点云数据的拼接,同时通过增加搭接处标靶数量来提高点云拼接的精度,搭接标靶数量不少于4个。
2.3 扫描分辨率的选取
扫描的分辨率指扫描的点采样间隔,反映了对物体扫描的精细程度。扫描分辨率越高,扫描的测点越密集,物体被扫描得越精细,精度也就越高,但所需扫描时间也越长。因此管片模具三维激光扫描分辨率的选取应综合考虑扫描精度、作业效率等因素,现场采用1 mm。
2.4 基准模型及对齐方式的选择
模具检测时,需将每次扫描的三维模型同基准模型进行对比,其偏差值即为模具的变形值,所以基准模型及对齐方式选择是否合适将直接决定着检测结果的精度。
基准模型选取有两种,一为模具加工时的设计模型,如图2所示;二为进场验收合格后第一次扫描得到的模型,如图3所示。模型对齐也有两种,一种为特征对齐,利用特征的点、线、圆、面、球、圆柱、圆锥等进行点与点重合、线与线共线、矢量平行/同向/重合、平面共面等;另一种为最佳拟合,利用检测模型质心、最小惯性主轴,完成基准模型与检测模型的质心、最小惯性主轴的重合,达到曲面匹配的目的。
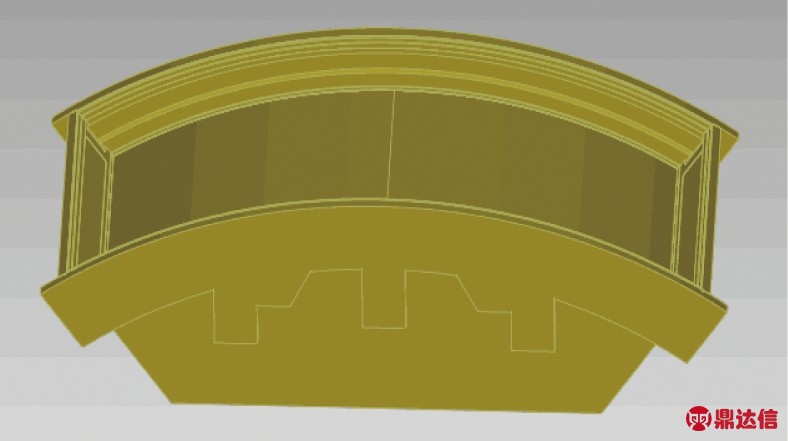
图2 设计模型
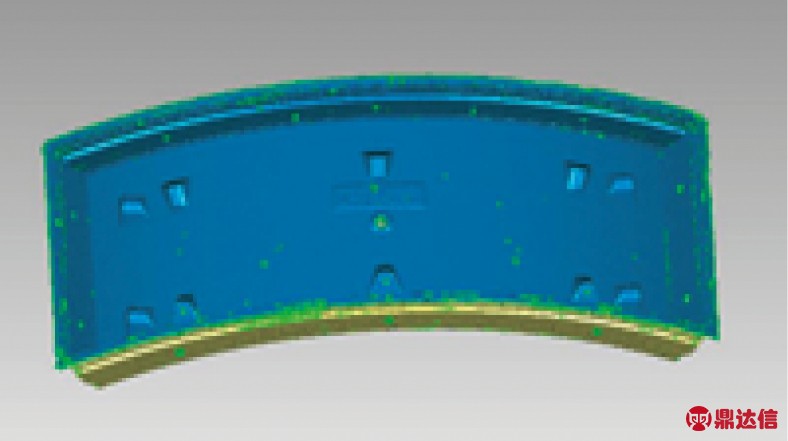
图3 扫描模型
(1)采用特征对齐进行拟合
在采用设计模型作为基准模型进行特征拟合对齐时,如图4所示,坐标系Y方向可以使用两块侧模作为约束,X方向可以使用两个端模作为约束,Z方向只能使用底模拟合的圆柱作为约束,但是使用曲面拟合圆柱的效果很差,拟合出来的圆柱直径D为5 480.860 6 mm,如图5所示,而管片内径只有5 500 mm,两者相差达到了20 mm,将拟合出的圆柱进行对齐时误差太大,显然无法满足检测精度要求。采用进场验收合格后第一次扫描得到的模型作为基准模型进行特征拟合对齐,同样存在底面拟合圆柱精度不足的问题。
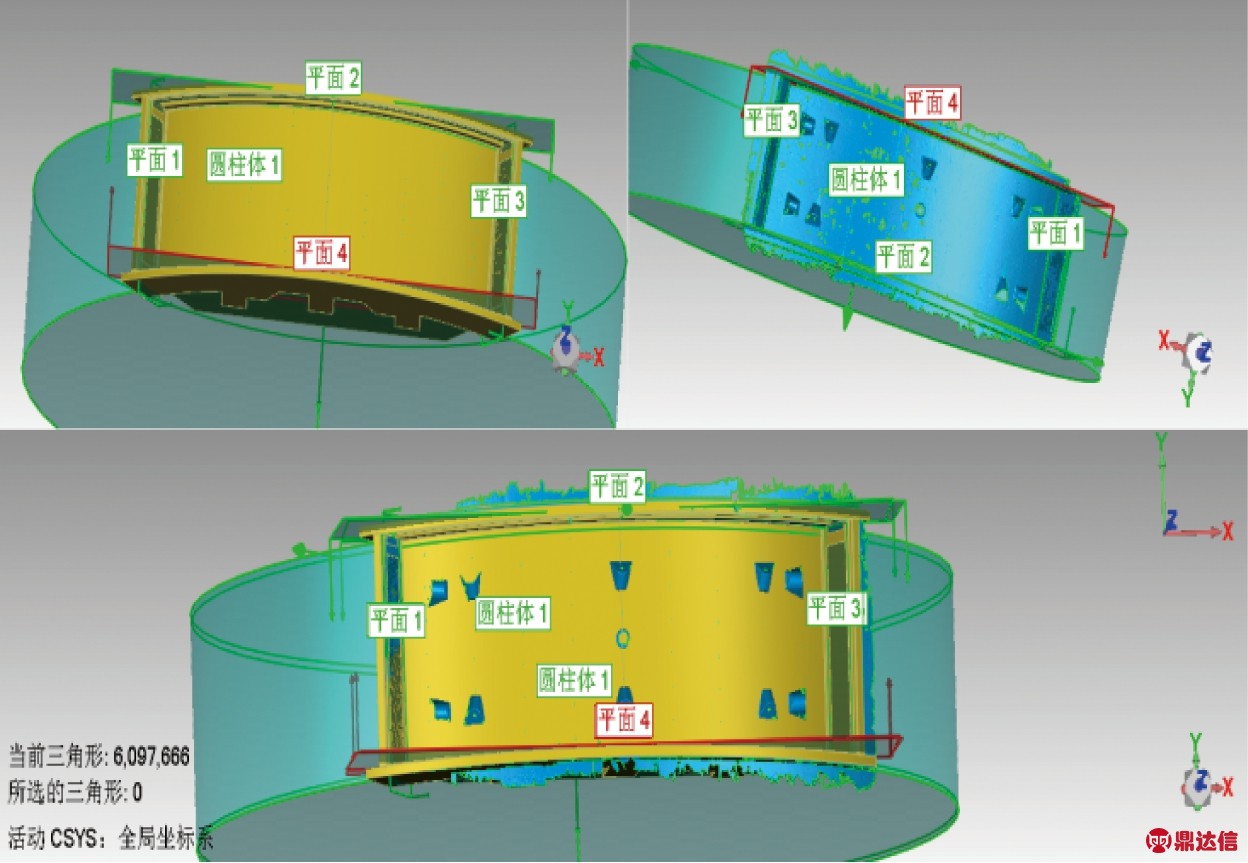
图4 设计模型作为基准模型特征拟合对齐
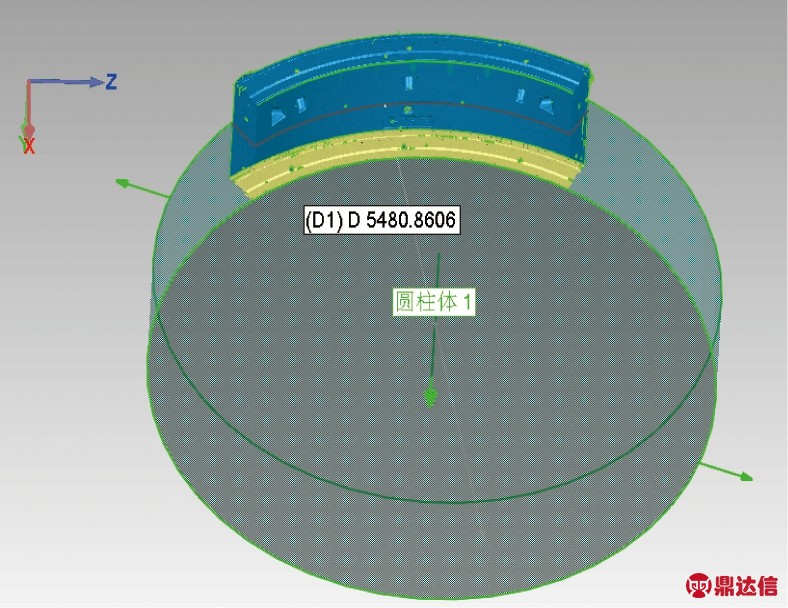
图5 扫描模型底面拟合圆柱
(2)采用最佳拟合进行对齐
如采用设计模型作为基准模型进行最佳拟合对齐时,由于设计模型没有手孔盒,实测模型有手孔盒,对齐结果会受到手孔盒的影响,造成拟合误差较大;如采用进场验收合格后第一次扫描得到的模型作为基准模型,则不受手孔盒的影响,为了验证其对齐精度,现场进行了两次试验:一次假设模具没有变形,另一次假设模具已经变形。
①假设模具没有变形
现场对同一块模具连续进行两次扫描,将两次扫描结果采用最佳拟合方式进行对齐,其3D色谱偏差如图6所示,其差值为仪器测量误差及最佳拟合对齐误差之和,而仪器的空间精度已知,由此可以计算最佳拟合对齐的误差。
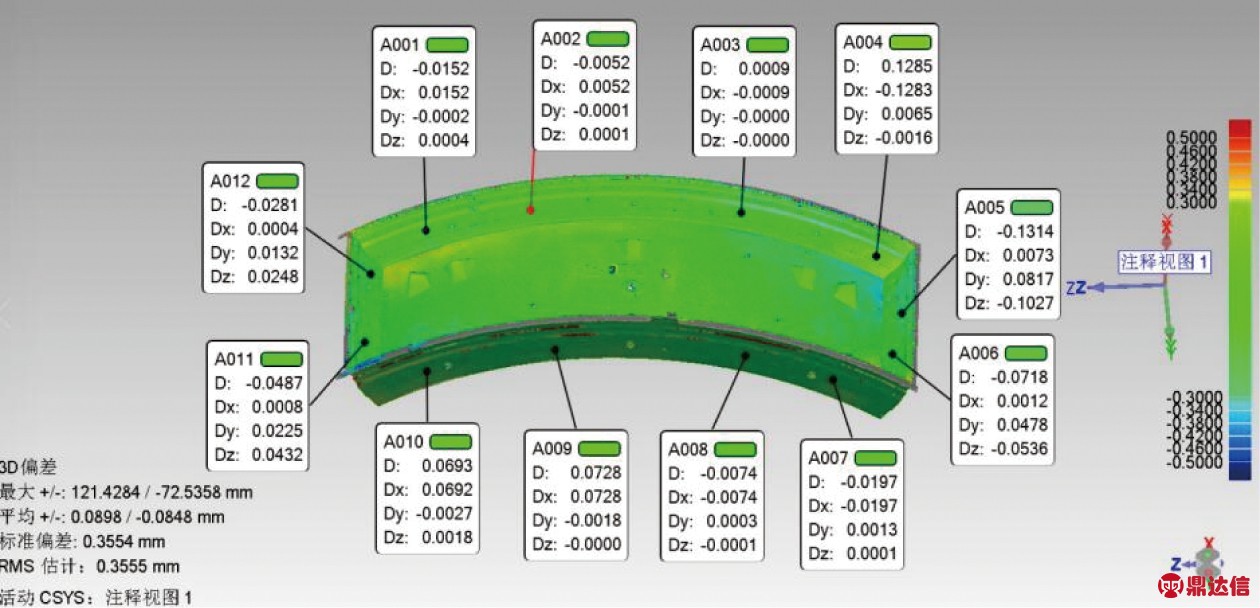
图6 两次扫描3D色谱偏差
从两次扫描结果对比看,其差值均在0.13 mm之内,而设备标称体积精度为0.044 mm+0.025 mm/m,模具长度约为3.4 m,扫描结果理论测量精度为0.129 mm,则最佳拟合对齐精度在0.01 mm数量级,满足管片模具检测精度要求。
②假设模具已经变形
现场对一块管片模具进行两次扫描检测,第一次扫描完成后将模具两块侧模轻微打开,再进行第二次扫描,在两次扫描前分别用传统检测方法内径千分尺(精度0.02 mm)对模具的宽度进行测量(传统检测方法中只有宽度测量相对精确),通过传统检测方法两次测量的宽度差值可以看出模具前后的变形情况,再将两次扫描检测结果进行对齐,其3D色谱偏差如图7所示。其差值减去模具变形的数值后,即为仪器测量误差及最佳拟合对齐误差之和,由此可以计算在管片模具发生变形后最佳拟合对齐的精度是否会受影响。
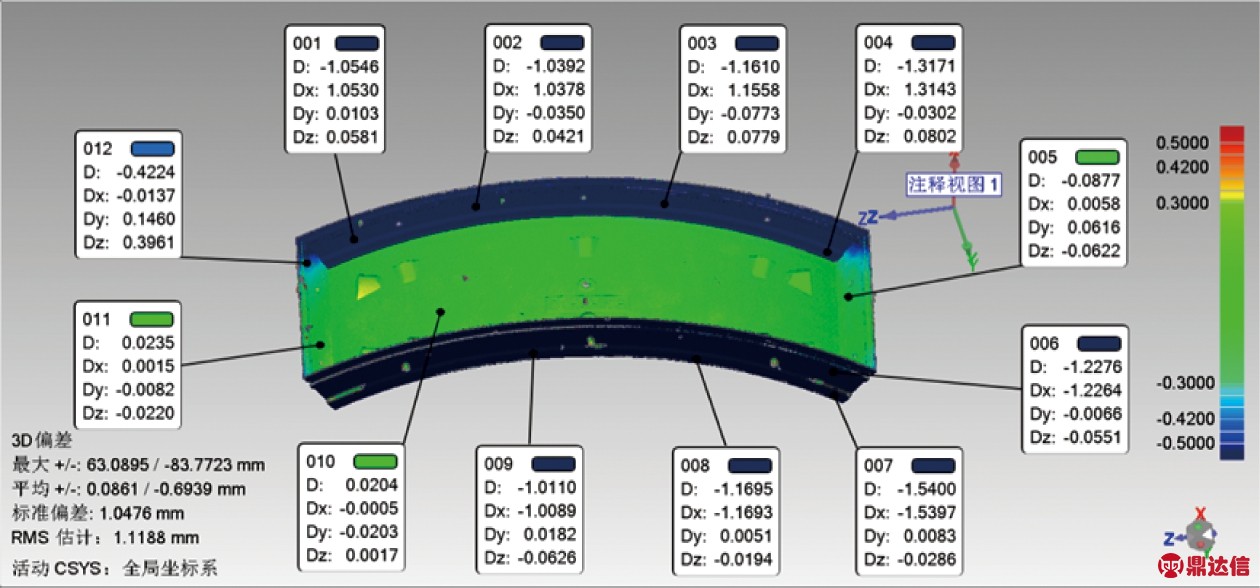
图7 两次扫描3D色谱偏差
现场内径千分尺测量点位对应图7中的002-009、003-008处,其两次差值分别为-2.15,-2.38 mm;现场两次扫描结果对比,测点002与008偏差之和为-2.04 mm,测点003与008偏差之和为-2.33 mm,采用两种检测方法的结果差值在0.15 mm之内。因设备标称体积精度为0.044 mm+0.025 mm/m,模具长度约为3.4 m,扫描结果理论测量精度为0.129 mm,则最佳拟合对齐精度在0.01 mm数量级,满足管片模具检测精度要求。
因此在管片模具三维激光扫描时,选用进场验收合格后第一次扫描得到的模型作为基准模型,选用最佳拟合方式对模型进行对齐。
2.5 检测标准的制定
(1)现有的检测标准
现有规范中对盾构管片模具及管片尺寸的偏差允许值如表2、表3所示。
表2 管片模具的偏差允许值
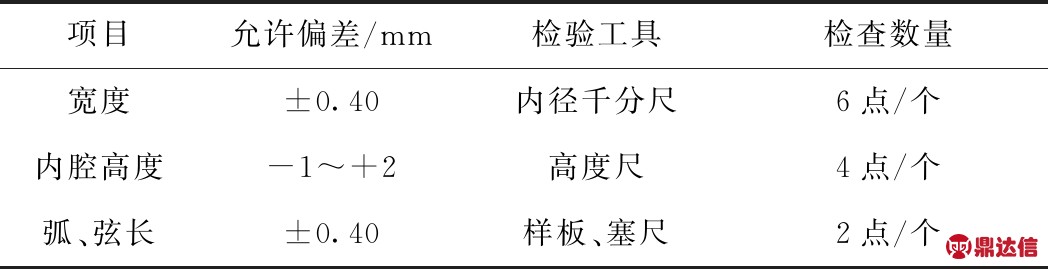
表3 管片的偏差允许值
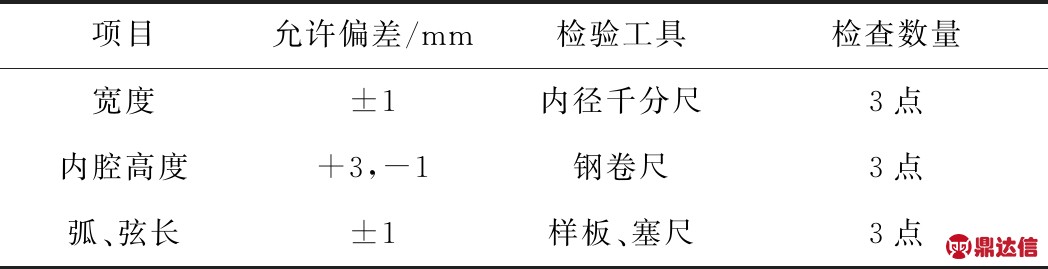
现有的检测标准与传统的检测手段是相对应的,仅是一个相对变化量,而不是绝对变化量,当发生两块侧模或端模向同一个方向变形时,有可能出现模具实际变形已经很大,但检测的结果是合格的现象。在实际工程建设中,部分城市建设单位对管片生产厂家提出了更高要求,如宁波轨道交通对管片模具偏差允许值要求如表4所示。
表4 宁波轨道交通管片模具的偏差允许值
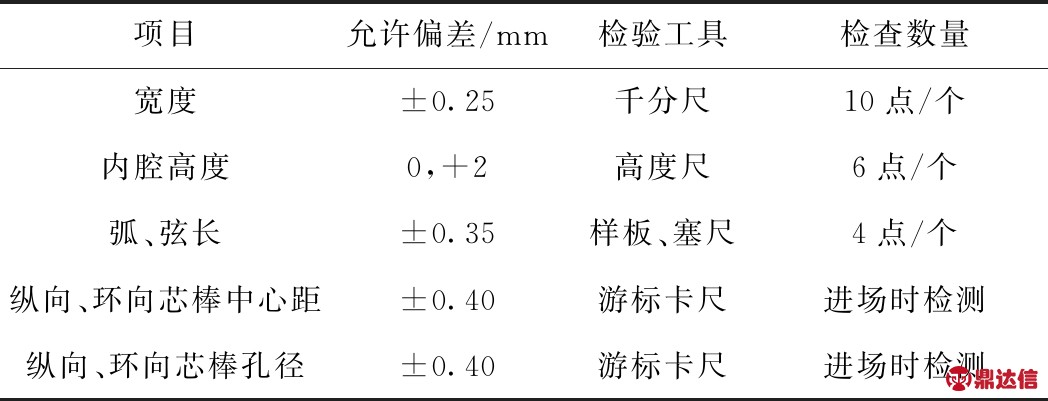
(2)管片模具三维激光扫描检测标准的制定及修复
管片模具三维激光扫描仪检测结果可以准确显示两块侧(端)模的变形方向和变形量,以此结果来指导管片模具修复时,修复结果能够精确控制,进而准确控制管片尺寸偏差。因此,在确定管片模具三维激光扫描检测结果判定标准时,可以综合考虑现有规范中管片模具、管片尺寸的偏差允许值及管片模具偏差值对管片模具修复的影响程度来制定。
结合试验确定的三维激光扫描仪测量精度、自动拟合对齐精度及现场实际情况确定管片模具三维激光扫描检测结果判定标准如表5所示。若实测偏差小于偏差值1,则可以继续生产;实测偏差值大于偏差1但是小于偏差2,该钢模需在生产线上进行必要的维修保养;若实测偏差大于偏差值2,则必须撤下生产线进行修复,并在修复完成后重新进行检测,检测合格后方可用于生产。
表5 管片模具三维激光扫描检测结果判定标准
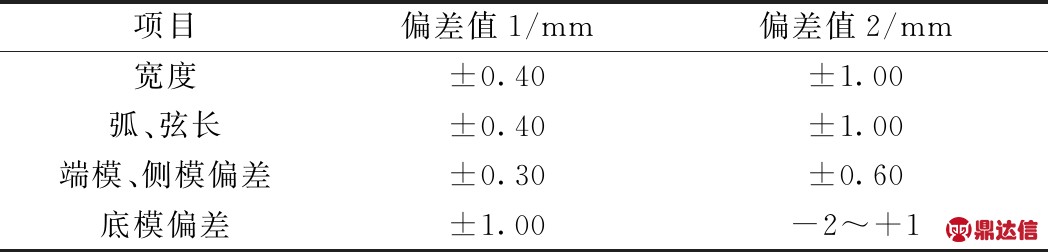
3 结论与建议
(1)利用三维激光扫描技术对管片模具进行检测,成功地实现了管片模具变形的可视化表达,解决了传统人工检测方法中检测点位少、精度低,弧长和宽度只能检测绝对变形的缺点,提高了管片模具的检测精度。
(2)通过试验验证了采用第一次扫描结果作为基准模型、最佳拟合作为对齐方式的数据处理方法的可行性,为管片模具三维激光扫描检测提供了理论支撑。
(3)在参考现有规范及经验的基础上,结合三维激光扫描技术的特点,制定出了三维激光扫描检测标准,使管片模具修复更准确,更有针对性,且节省了修复时间,提高了经济效益。
(4)管片模具三维激光扫描检测时,应将模具内腔清理干净,合模时应严格按照相关要求进行操作。
(5)三维激光扫描仪对外部条件要求相对较高,检测过程中应避免温差过大。